Alcoa стремится к совершенству в области надежности
Если вы не переносите жару, вам лучше не искать работу на предприятии Alcoa Primary Metals в южной Индиане.
Огнедышащие электролизеры и тигли, заполненные расплавленным металлом, могут повысить температуру окружающей среды производственного цеха почти до трехзначного числа. Тепло заметно излучается от оборудования. По щекам и спине рабочих текут ручейки пота. Необходимы частые перерывы на воду и Gatorade.
Это физически сложная среда, но реальное тепло, указанное в первом абзаце, больше связано с положением этого конкретного завода в алюминиевой промышленности. Это предприятие, являющееся частью крупного Warrick Operations компании Alcoa, было построено в конце 1950-х годов, и в начале 1960-х годов начали производить необработанный алюминий для листовой промышленности.
Это старый завод в отрасли, чувствительной к возрасту и технологиям. В 1980 году в Америке работало 33 плавильных завода. Сегодня их насчитывается 13. Всего 6 процентов мировых алюминиевых мощностей будет произведено в этом году на плавильных заводах, которым более 50 лет. Часы идут.
К этому состоянию добавьте следующее:
-
25 процентов сотрудников завода в настоящее время имеют право на пенсию по возрасту или выслуге лет;
-
заработная плата на предприятии - одна из самых высоких в отрасли; и,
-
Несколько лет назад затраты на техническое обслуживание этого завода на метрическую тонну произведенного алюминия были вторыми по величине в глобальной системе Alcoa.
Вы чувствуете жар? Каждый работник на этом заводе делает. Но вместо того, чтобы ждать гибели, которая казалась неизбежной, обслуживающий и эксплуатационный персонал выступил вперед и принял меры.
«Мы должны все устроить, если мы хотим поддерживать этот уровень жизни и поддерживать этот завод», - говорит менеджер по плавильному производству Alcoa Business System Марк Кенейп. «Это новая реальность. Тебе просто нужно смириться с этим ».
Все начинается с взгляда в зеркало.
«Нашей задачей было и остается конкурентоспособность по ценам, несмотря на наш преклонный возраст», - говорит Кенейп. «Мы больше не находимся на переднем крае возрастной кривой. У нас должен быть горизонт от 15 до 20 лет, чтобы привлечь капитал в Alcoa. Если это от 25 до 30 лет, это было бы здорово. Для этого мы должны постоянно доказывать, что мы бережливое, конкурентоспособное, стабильное и эффективное предприятие ».
Это не среда для слабых. Но за упорный труд и настойчивость можно получить множество наград.
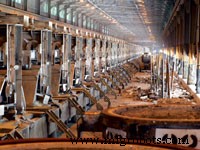
Тайм-аут вызова
Усилия по поддержанию присутствия Alcoa Primary Metals в производственном сообществе южной Индианы начались на корпоративном уровне.
В 1997 году генеральный директор Alcoa Ален Белда начал внедрять принципы производственной системы Toyota (TPS) в 250 офисов своей компании по всему миру.
Менеджер по производству алюминия Родни Каннингем (слева), координатор процессов Ларри Йорк и старший штатный инженер-технолог Брайан Ауди стоит внутри пустующего резервуара для глинозема на территории Warrick Operations компании Alcoa. На заводе традиционно использовались четыре таких резервуара в качестве сборных емкостей для глинозема, ключевого ингредиента в процессе плавки алюминия. Благодаря инициативе бережливого производства и критическому мышлению завод сократился до двух резервуаров, что позволило компании сэкономить значительную сумму денег.
TPS - это философия бережливого производства, основанная на производстве «точно в срок», устранении отходов и быстром решении проблем. Однако при внедрении системы металлургический завод в Индиане сделал важное открытие.
«TPS, Flow и Lean не работают, если у вас нестабильное, непредсказуемое оборудование», - говорит Кенейп.
Эффективное, оптимизированное и рентабельное обслуживание оборудования и надежность оборудования должны быть на первом месте.
Чтобы проиллюстрировать свою точку зрения, Кенейп предлагает диаграмму, которая называется «айсберг технического обслуживания». Выше воды указаны прямые затраты на техническое обслуживание, связанные с материалами, рабочей силой, сверхурочными, контрактными услугами, а также накладными расходами и льготами. Под поверхностью скрываются косвенные расходы, связанные с простоями, настройкой и запуском, невыполненными графиками, избыточными запасами, кризисным управлением, экстренными закупками и общим волновым влиянием на производство.
«Непрямые компоненты являются заложниками нестабильного оборудования и производственных процессов», - говорит он.
Все эти отходы склеивают систему и приводят к увеличению затрат на эксплуатацию и техническое обслуживание.
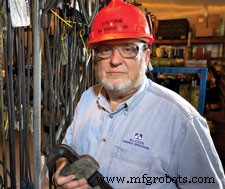
В 2002 году общие затраты на техническое обслуживание этого плавильного завода превысили 35 миллионов долларов. Его «болезненно высокий» коэффициент затрат на техническое обслуживание, превышающий 137 долларов США на каждую метрическую тонну произведенного алюминия (см. «Только факты» для годового тоннажа), поставил его вторым после последнего среди плавильных заводов Alcoa во всем мире. В 2002 году средний мировой показатель составлял 90 долларов за тонну.
У этого завода Алкоа и его руководителей было два варианта.
«Директор завода Ройс Хос сказал, что мы собираемся снизить наши затраты. Это был не вариант оставаться на месте. Это должно было случиться », - говорит Кенейп. «Мы могли бы сделать это с умом или недальновидно. Когда ты становишься близоруким, это страшные дни. Трудно привлечь капитал на завод, чтобы выполнить то, что нужно сделать, когда вы просто откладываете техническое обслуживание. Такой подход никому не нравится. Это побуждает людей искать что-то лучшее ».
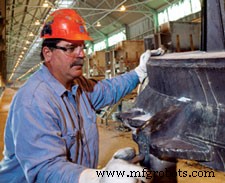
Ловля волн
Если вы еще не догадались, завод Alcoa выбрал разумный подход для снижения затрат на техническое обслуживание. Руководители технического обслуживания объединились с консультантами из Life Cycle Engineering (LCE) и Ron Moore Group в начале 2003 года, чтобы создать подход под названием «Процесс повышения надежности», который был развернут тремя «волнами». Этот процесс основан на убеждении, что между техническим обслуживанием и эксплуатацией обязательно наличие формализованного, четко определенного партнерства. В рамках этого партнерства компания владеет оборудованием и в первую очередь заинтересована в надежности. Техническое обслуживание - это равноправный партнер, стремящийся предоставить своевременные и эффективные методы, навыки, знания и поддержку.
«Это большое изменение», - говорит инженер по надежности Джозеф Моц. «Раньше это была обособленная среда, в которую постоянно указывали пальцем».
Расплавленный металл разливается из тигля
в отделении слитков завод Алкоа.
Некоторые примеры:
Оператор заметил потенциальную проблему. Никакого исправления не было запланировано и сделано. Машина сломалась. Кто был виноват?
Или техническое обслуживание потребовалось для двухчасового профилактического обслуживания. Находясь в машине, он обнаружил дополнительные проблемы и закончил работу PM через восемь часов, что повлияло на производительность. Кто был виноват?
В этих случаях ответом было и техническое обслуживание, и эксплуатация.
«Мы должны были понять, что мы все в одной команде, - говорит Моц. «Мы все здесь, чтобы производить алюминий. Если мы пойдем в разные стороны и не будем работать вместе, процесс не сработает ».
Волна 1 в трехволновом подходе началась в июне 2003 года.
«Волной 1 был Рон Мур», - говорит Кенейп. «Мы пригласили его поговорить с ключевыми руководителями завода. Он бросил вызов старым парадигмам. «Вам нужно больше придерживаться философии владельца активов». «Вы тратите деньги зря». Он встряхивает вещи и открывает глаза ».
Волна 2 прибыла в августе с полной оценкой качества надежности, проведенной LCE. В течение двухнедельного периода компания провела продолжительные интервью с 90 сотрудниками по эксплуатации и техническому обслуживанию (почасовая и с зарплатой), а также с диспетчером завода.
Информация привела к:
-
финансовый анализ с подробным описанием оценочной стоимости устранения пробелов в достижении совершенства в надежности по сравнению со стоимостью внедрения (представленной в виде расчета рентабельности инвестиций);
- предварительный генеральный план, в котором излагаются процессы и методологии, необходимые для устранения пробелов.
«Мы хотели посмотреть на наше текущее состояние и определить целевое состояние», - говорит Кенейп. «Разрыв между этими двумя вещами - ваша боль или выгода. Стоит ли прилагать усилия для преодоления разрыва? Мы должны были доказать это высшему руководству. Нам нужно было доказать, что вложение денег в старый завод имеет смысл.
«Учитывая все факты, было разумно как можно скорее получить одобрение денег, чтобы продолжить».
Волна 3 началась в сентябре. Руководители по эксплуатации и техническому обслуживанию:
-
реализовал генеральный план
-
обучил всех сотрудников их новым ролям и обязанностям, связанным с повышением надежности оборудования
-
провели семинары по правильным методам повышения надежности
-
установленные определенные процессы и эффективные показатели прогресса
«Это непросто. Ничего подобного », - говорит Родни Каннингем, руководитель производственного цеха. «Но если у вас есть обязательства руководства и партнерство между техническим обслуживанием и производством, ваши шансы на успех увеличиваются. Без этих вещей у вас ничего не получится ».
Поднимая планку
Установление определений в различных областях помогло вызвать улучшения. Основное внимание было уделено определению «что возможно?» и «что такое прогресс?»
Ответ пришел в том, что общая эффективность оборудования (OEE) была признана ключевым показателем для всего предприятия. OEE отслеживает источники операционных потерь, включая доступность, производительность и качество оборудования, и выражается в процентах от оптимальной производительности.
«Это в основном определяется некоторыми прошлыми лучшими показателями», - сказал менеджер по производству электродов Том Свобода. «Вы видели, как это произошло. Это не было выдумкой или гипотезой. Независимо от того, работало ли оборудование в этом месяце необычно или вы действительно были на вершине процесса, это произошло. Вопрос в том, если вы делали это в течение одного периода времени, почему вы не можете делать это все время? »
Используя спортивную аналогию, чтобы проиллюстрировать важность 100-процентного OEE, если прыгун в высоту обычно прыгает на 6 футов 6 дюймов, но устанавливает личный рекорд в 7 футов, что конкретно привело к этой пиковой 100-процентной производительности. Он тренировался по-другому? Изменил ли он диету перед соревнованиями? Он носил другую обувь? Он буквально поднял планку. Чему можно научиться и что можно делать, чтобы снова и снова достигать этой отметки?
Техническое обслуживание и операции работали вместе, чтобы определить максимальную производительность для функций завода (например, сборка анода), процессов (выгрузка руды), результатов (лом) и отдельных единиц оборудования (кольцевая печь). При сборе этой информации было определено, что в результате достижения целей OEE можно было сэкономить 8,3 миллиона долларов в год.
На основе исходной информации были определены текущие состояния и установлены целевые условия. Мероприятия - рабочие проекты с использованием инструментов бережливого производства, таких как кайдзен и непрерывное совершенствование, - имели место. Прогресс был измерен и проанализирован. И были рассчитаны ощутимые выгоды.
В 2004 году усовершенствования на 2,4 миллиона долларов были связаны с прибылью от OEE.
Более глубокий анализ и принятие мер также привели к снижению затрат на техническое обслуживание плавильного завода. В первый год после начала реализации инициативы по обеспечению надежности расходы упали на 1,9 миллиона долларов с базового показателя в 32 миллиона долларов до 30,1 миллиона долларов. В 2004 году эта цифра упала еще на 700 000 долларов. Соотношение затрат на техническое обслуживание на метрическую тонну произведенной продукции также снизилось до 109 долларов в 2004 году.
План «Запланировано»
Также были предприняты серьезные усилия для более точного определения элементов обслуживания. В частности, в этой управляемой оператором системе надежности «как планируется работа?» и «как выполняется работа?»
«Оглядываясь назад, мы обманывали себя, полагая, что мы здоровы, - говорит менеджер по техническому обслуживанию Дэнни Рейес. «Многие из наших старых показателей были недоступны. Мы думали, что наш «процент запланированных и запланированных работ» был на уровне 85 процентов, а наш «процент завершения PM» был на уровне 90 процентов ».
LCE сообщила предприятию, что использовала неправильные определения.
«Процент запланированных и запланированных работ» на самом деле был просто «процентным планом». Планирование было очень ограниченным, - говорит Рейес. «Это было соблюдение графика. Вероятно, 10 процентов этих работ были запланированы ».
Суть проблемы заключалась в соотношении личного состава ремесленников (140) и планировщиков (четыре) 35:1.
«Это работало не очень хорошо, - говорит специалист по планированию технического обслуживания Ларри МакКуббинс. «Времени на планирование было очень мало. Вы стали планировщиком, и не очень хорошо умеете делать это ».
Реактивная среда процветает в этой настройке. «Мы использовали« подход к обслуживанию дома », - говорит Кенейп. «Вот так мы с вами занимаемся проектами субботним утром. Это действительно незапланировано и неэффективно ».
С тех пор на заводе были добавлены три планировщика, всего семь, что обеспечило более управляемое соотношение 20:1.
«Это позволяет этим ребятам наладить, организовать работу, спланировать ее, согласовать ее с производственными центрами, убедиться, что все детали есть, убедиться, что оборудование вышло из строя и есть время», - говорит суперинтендант по техническому обслуживанию плавки. Скотт Деон.
Другие ключи к лучшему планированию:
-
Официальный документ теперь описывает компоненты запланированной работы (см. Врезку на странице 14). «Четыре бедных планировщика, которые у нас были, пытались сделать все по-другому, - говорит Деон. «Этот новый формат теперь стандартизирует порядок выполнения работы».
-
Планировщики теперь используют формальную безопасную зону для набора рабочих мест. В прошлом необходимые детали и материалы отправлялись на стройплощадку по частям. Куча может лежать неделями, пока не будут доставлены все предметы. Во время ожидания нередко было перемещать, терять или использовать детали или инструменты для другой работы.
«Когда планировщик планирует работу, он заказывает все материалы и доставляет их сюда. , - говорит МакКуббинс. «Когда все для работы здесь, мы собираем его на одном или двух поддонах. Затем ремесленники привозят его на стройплощадку и выполняют работу ». -
Эффективное общение.
«Раньше я думал, что знаю, чего хотят люди. Этот процесс научил меня тому, что я этого не делал, - говорит МакКуббинс. «Я не знала, чего они хотят и что им подходит. Раньше я планировал работу и не задавал вопросов ».
Деон добавляет:« Благодаря разделению ответственности с производством мы теперь знаем, какая работа будет первой. Человек, владеющий оборудованием, должен знать, что является наиболее важным. Раньше я не думаю, что мы гадали. Но были ли мы на 100 процентов? Наверное, нет ». -
Целенаправленные и эффективные еженедельные встречи.
«Собственники активов председательствуют на собраниях, а планировщики / составители графиков технического обслуживания - координаторы», - говорит Кенейп. «Если это совещание по планированию, мы обсуждаем, как мы собираемся это сделать. Если это плановая встреча, мы ее устанавливаем ».
Также в отношении того, как выполняется работа, завод предпринял шаги по документированию истории оборудования и стандартизации инструкций по обслуживанию.
«Раньше можно было получить записи, но потом документация прекратилась», - говорит инженер-энергетик выпрямительной станции Дэн Декастра. «Итак, мы создали место на сервере и начали документировать. Для этой станции мы составили список «плохих парней». Мы выбрали серьезные проблемы и начали с них. Теперь вы можете вернуться в 2001 год и увидеть историю воздушных переключателей, контактов, трансформаторов и салазок ».
Джонатан Фултон, инженер по надежности, добавляет:«Возможно, треть нашего обслуживающего персонала могла бы выйти на пенсию завтра, если бы захотела. Это огромная потенциальная опасность для нас. К тому же со стороны сложно получить качественного мастера. Чтобы решить эту проблему, мы стандартизируем рабочие процессы и разрабатываем историю оборудования. Таким образом мы можем быстро научить людей с техническими знаниями ».
Примечания для детской кроватки
Последний пример улучшения - это то, как предприятие лучше определило, кто покупает продукты для технического обслуживания и как деньги тратятся на инструменты и расходные материалы.
В прошлом различный обслуживающий персонал на плавильном заводе покупал ручные инструменты, электроинструменты, средства безопасности, чистящие средства, погрузочно-разгрузочные средства и сотню других необходимых предметов. Приобретенные продукты размещались в децентрализованных ящиках для инструментов по всему объекту и во множестве неофициальных мест хранения (шкафчики, сундуки и закутки).
«По мере расширения завода увеличивались площади. У них была небольшая группа, и кто-то делал заказы, и они складывали свои запасы тут и там, - говорит главный механик Дик Дэй. «Мы тратили большие деньги, пытаясь прокормить эти детские кроватки. Им не удалось. Люди покупали вещи, но это было недоступно ».
Если механику нужен был какой-то конкретный инструмент, он охотился за ним. Это было где-то поблизости. Если не мог найти, то заказывал. Купленный инструмент может исчезнуть раньше, чем достанется ему. Это привело к расточительным и избыточным расходам.
Чтобы решить эту проблему, была построена централизованная детская кроватка, и все дополнительные детские кроватки и места для детских комнат были перенесены в эту охраняемую, огороженную зону.
Пришли никчемные.
«Мы поняли, что у нас много устаревшего оборудования - что-то для части оборудования, которое мы, возможно, сняли 10 лет назад», - говорит Кенейп.
И вот пришло ценное.
«Это было потрясающе - все, что получилось из дерева. Кто-то принес шкаф с насосами и домкратами на сумму более 38 000 долларов, - говорит Дэй, который стал главным помощником центральной кроватки. «Мы начали использовать то, что у нас было. По некоторым материалам нам не пришлось ничего заказывать в течение года ».
Сегодня Day несет ответственность за покупку этих продуктов, связанных с техническим обслуживанием. Он получает покупки, хранит их и распределяет по мере необходимости.
«Мы знаем, что у нас есть и где это находится», - говорит он.
Дэй также создал систему минимума / максимума для различных продуктов и предпринял усилия по стандартизации торговых марок электроинструментов и сварочных материалов.
«Что касается электроинструментов, мы в основном стандартизировали их на DeWalt, и мы серьезно вникаем в их аккумуляторные инструменты», - говорит он. «Что касается сварочных материалов, мы стандартизировали наши пистолеты для подачи проволоки и запасные части для них».
Он делает домашнее задание и находит инновационные способы сократить расходы.
Вот несколько примеров:
Перчатки :«Раньше мы покупали марку перчаток с ярлычком по цене 12 долларов за пару. Это то, что «должны были иметь все», - говорит он. «Вы можете купить такие же перчатки с небольшой резинкой по цене 2,67 доллара за пару. Людям они нравились ».
Гидравлическое масло :«Мы купили его галлонами по 8 долларов за штуку. Покупая его оптом, мы теперь экономим 3 доллара на галлон. Я наливаю масло в многоразовые кувшины по 57 центов за штуку ».
Ацетиленовый шланг :«Раньше покупали расфасованным в катушку. Теперь мы покупаем его на 500-футовом рулоне и отрезаем то, что нужно человеку. Мы экономим 25 процентов ».
Дэй говорит, что это все здравый смысл.
«Я смотрю на это как на свои деньги», - говорит он. «Если это мой бизнес, я бы руководил им так».
Заставить их потеть
Благодаря упорному труду, партнерству, ответственности и новаторскому мышлению этот плавильный завод Alcoa стал более стабильным, экономичным, предсказуемым, надежным и конкурентоспособным по цене.
Выгоды от затрат на OEE с начала года до настоящего времени составили 4,4 миллиона долларов в годовом исчислении по сравнению с базовым показателем 2003 года.
Расходы на техническое обслуживание с начала года до даты составили 27,1 млн долларов в годовом исчислении и на 4,9 млн долларов меньше базового показателя 2003 года.
Затраты на техническое обслуживание во втором квартале 2005 года составили 96 долларов за метрическую тонну произведенной продукции, а в ближайшем будущем планируется достичь 87 долларов.
Последующая оценка LCE поместила завод в категорию «упреждающих условий», и сейчас ведутся работы по его повышению до категории «безупречность».
Есть оптимизм и импульс.
«Когда меня наняли 15 лет назад, мы сказали:« У нас старые технологии. Мы не можем конкурировать с некоторыми из более современных объектов », - говорит Фултон. «Для меня награда в том, что мы соревнуемся и работаем с большей эффективностью. Мы производим больше продукции с помощью наших 40- или 50-летних технологий, чем на объектах, построенных 10 или 20 лет назад ».
Хотя это растение никогда не уйдет полностью, оно делает все, что в его силах, чтобы попотеть конкурентам.
Каковы характеристики запланированной работы?
-
Для работы существует точная оценка времени, так что у руководителя будет разумное ожидание того, когда он или она сможет назначить задачу.
-
Имеется точная оценка необходимых ресурсов в виде личного состава, запасных частей, инструментов, вспомогательного оборудования и т. Д.
-
Получена вся необходимая информация (чертежи, разрешения, безопасность и т. Д.)
-
Устанавливаются последовательность этапов работы, процедуры и инструкции для выполнения работы.
-
Все необходимые детали и материалы укомплектованы.
-
В качестве встроенной проверки для обеспечения качественной запланированной работы периодически обсуждайте характер работы с руководителем и / или мастером, назначенным для выполнения работы. Убедитесь, что имеется полное представление об объеме работ и комплектность рабочего пакета.
Техническое обслуживание и ремонт оборудования
- Что такое культура надежности?
- Какова роль инженера по надежности?
- Революция надежности Whirlpool
- Лучшие показатели обслуживания и надежности
- Ключ № 1 к успеху надежности
- Как совершенство надежности увеличивает преимущества бережливого производства?
- Надежность, ориентированная на семью
- Управление цепочкой поставок:выходя за рамки совершенства надежности
- Почему высокая надежность необходима для безопасности
- Надежность - зеленая инициатива