Изготовление наноразмерных ямок с высокой производительностью на полимерной тонкой пленке с использованием литографии с динамической вспашкой на основе AFM
Аннотация
Мы показываем, что метод динамической вспахивающей литографии (DPL) на основе атомно-силового микроскопа (АСМ) может быть использован для изготовления ямок нанометрового размера с высокой производительностью. Метод основан на царапании с относительно большой скоростью по поверхности образца в режиме постукивания, который отвечает за расстояние разделения соседних ямок. Испытания на царапание проводятся на тонкой пленке из полиметилметакрилата (ПММА) с использованием алмазоподобного углеродного покрытия. Результаты показывают, что 100 мкм / с является критическим значением скорости царапания. Когда скорость царапания превышает 100 мкм / с, могут образовываться ямочные структуры. Напротив, наноканавки могут формироваться на скоростях, меньших критического значения. Из-за сложности разрыва молекулярной цепи стеклообразного полимера с приложенной высокочастотной нагрузкой и низкоэнергетического рассеяния при одном взаимодействии иглы и образца, для достижения одной ямки требуется 65–80 проникновений. Далее детально анализируется процесс формирования котлована, включающий три фазы:упругую деформацию, пластическую деформацию и преодоление отвала. В частности, с помощью предложенного метода можно получить 4800–5800 ямок за 1 с. Представлены как эксперименты, так и теоретический анализ, которые полностью определяют потенциал этого предложенного метода для эффективного изготовления ям.
Фон
Недавнее и быстрое развитие нанотехнологий привлекло все большее внимание к применению наноструктур в различных областях, таких как наноэлектромеханические системы, наносенсоры и нанофотоника. В частности, наноточки, определяемые как одномерные наноструктуры, широко используются в областях хранения и получения квантовых точек с высокой плотностью [1]. Однако эффективное изготовление наноточек по-прежнему сталкивается с огромными проблемами. Многие ученые предложили различные методы изготовления наноточек на самых разных материалах. Среди них метод химического синтеза широко используется для получения наноточек для большинства устройств обнаружения свойств и наноразмерных устройств [2]. Однако с помощью этого метода сложно определить размеры и пространственное распределение наноточек. Это приводит к тому, что для определения местоположения и манипуляций в последующих процессах требуется больше усилий. Таким образом, многие ученые посвятили ресурсы исследованию более контролируемых методов получения структур наноточек с размерами в несколько нанометров, таких как литография сфокусированным ионным пучком [3], электронно-лучевая литография [4] и литография наноимпринтов [5]. Однако сложность, строгие экологические требования и / или высокая стоимость сильно затрудняют применение этих методов.
Поскольку атомно-силовой микроскоп (АСМ) был изобретен в 1986 году, он широко используется в качестве высокоточного профилографа поверхности [6]. Когда сила взаимодействия между наконечником АСМ и образцом увеличивается до относительно большого значения, такого как несколько сотен наноньютонов или даже несколько сотен микроньютонов, материал образца может быть удален острым наконечником пластически, подобно небольшому режущему инструменту [7 ]. Химическая и тепловая энергия также была введена в систему AFM посредством местного окисления [8] или нагрева образца [9], чтобы облегчить удаление материалов образца. Это, таким образом, приводит к появлению некоторых новых производственных методов, расширяющих сферу применения существующих методов нанолитографии на основе иглы AFM (TBN). Среди всех методов TBN подход механического удаления является самым простым и гибким [10]. Этот метод состоит в первую очередь из вдавливания и последующего царапания на различных материалах, при этом взаимодействие зонд-материал сильно зависит от типа материала, такого как металлы [11], полупроводники [12, 13] и полимеры [14]. Путем точного управления взаимодействием зонда и материала на наноразмерных масштабах были успешно созданы сложные и высокоточные наноструктуры, такие как наноточки, наноканавки и даже трехмерные наноструктуры. В частности, некоторые ученые выполнили процессы наноиндентирования на поверхности полупроводниковых материалов на основе иглы АСМ для получения структур наноточек [15,16]. В их исследованиях было установлено, что кристаллические дефекты, вызванные наноиндентированием, являются центрами зарождения наноструктур InAs. Однако относительно большая твердость полупроводниковых материалов может привести к серьезному износу наконечника. Таким образом, некоторые исследователи предложили проводить процесс наноиндентирования на более мягких материалах, таких как полимерный тонкопленочный резист, чтобы сначала изготовить структуры из наноточек. Эти структуры наноточек затем могут быть перенесены на полупроводниковые материалы с помощью процессов реактивного ионного травления (RIE) или мокрого травления [17]. Из-за его низкой твердости и сверхтонкой толщины слой резиста может быть пронизан при относительно небольшой нормальной нагрузке. Некоторые ученые предложили двухэтапный подход царапания для получения массивов наноточек на поверхности поликарбоната [18]. Этот метод основан на ряби материалов, образованных процессом царапания с постоянной силой на игле АСМ. Однако расстояние между соседними наноточками зависит только от геометрии наконечника АСМ, и механизм образования наноточек остается неясным.
С другой стороны, низкая производительность является критическим фактором, препятствующим развитию методов нанопроизводства на основе наконечников АСМ. Было продемонстрировано, что процесс наноиндентирования на основе иглы АСМ требует много времени для получения крупномасштабных структур наноточек [19]. Чтобы решить эту проблему, Vettiger et al. представила концепцию «Многоножки», в которой используются большие массивы микрокантилеверов, работающих параллельно, для достижения сверхвысокой плотности обработки [20]. Учитывая серьезный износ наконечника после царапания на большой площади, некоторые ученые предложили новый режим прерывистого контакта для уменьшения силы взаимодействия между наконечником и образцом, тем самым уменьшая износ наконечника [21, 22]. Однако для больших массивов микрокантилеверов, используемых в этом подходе, требуются сложные процессы проектирования и производства, и требуется утомительный процесс регулировки положения всех наконечников на одном зонде, чтобы гарантировать контакт с образцом. Поэтому некоторые исследователи модифицировали коммерческую систему AFM, включая аппаратное и программное обеспечение, чтобы обеспечить возможность высокоскоростной обработки [23,24,25]. В этих методах использовались наконечники с одной консолью. Однако с помощью этих подходов можно эффективно изготовить только наноканавки, а царапание на больших скоростях также может привести к серьезному износу наконечника. В дополнение к статической обработке с помощью наконечника AFM, динамическая литография вспашки (DPL) на основе наконечника AFM также в последнее время привлекает все больше и больше внимания; этот процесс проводится в постукивающем режиме системы АСМ. При увеличении амплитуды возбуждения кантилевера наконечник АСМ может проникать в поверхность образца для достижения процесса обработки [26,27,28]. Из-за прерывистого контакта между зондом и образцом в подходе DPL износ зонда может быть уменьшен, аналогично методам, предложенным в работах [1,92]. [21, 22]. Глубина обработки, полученная методом DPL, обычно составляет порядка нескольких нанометров, что подходит для изготовления наноструктур на тонкой пленке, такой как полимерный тонкопленочный резист и двумерные материалы [29]. Более того, в методе DPL кантилевер иглы АСМ можно было заставить колебаться с частотой в несколько тысяч герц, что привело бы к многократному взаимодействию иглы с поверхностью образца за короткий период. Таким образом, метод DPL может быть потенциальным подходом к эффективному созданию структур наноразмерных ямок на поверхности тонкопленочного образца.
В этом исследовании представлен метод нанолитографии с быстрым сканированием (FSN), основанный на подходе к изготовлению DPL и с использованием коммерческой системы AFM. На рисунке 1а показана схема процесса наноцарапания с алмазоподобным углеродным покрытием наконечника, которая иллюстрирует вид наконечника в контакте с тонкой пленкой полиметилметакрилата (ПММА) на кремниевой подложке. Кантилевер приводится в движение около своей резонансной частоты для создания прерывистого контакта между зондом и поверхностью образца. Амплитуда возбуждения наконечника поддерживается на постоянном уровне системой управления (AM-AFM). Модуль Nanoman, установленный в системе AFM, используется для всего процесса обработки, а направление царапания выбирается параллельно длинной оси кантилевера. Исследовано влияние скорости царапания на обработанные наноструктуры. Кроме того, исследуется механизм образования ямочной структуры.
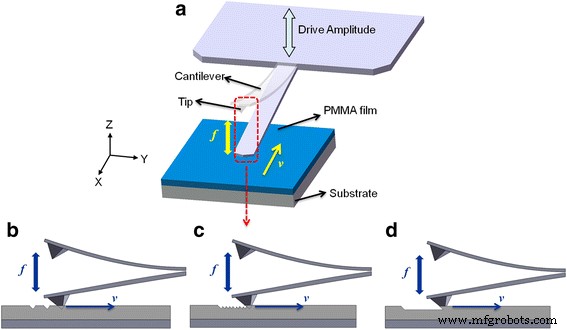
а Схема процесса штриховки на поверхности пленки ПММА методом FSN. Кантилевер колеблется на своей резонансной частоте f в вертикальном направлении. Скорость царапанья v изменяется в направлении быстрого сканирования. Показаны различные диапазоны скорости царапания: b высокая скорость царапания, c средняя скорость царапания и d низкая скорость царапания
Методы
Концентрация раствора ПММА составляет 1,25 мас.%, Полученного растворением порошка ПММА с молекулярной массой Mw =120 000 в хлорбензоле. Пленки ПММА получают путем центрифугирования раствора на куске подложки из монокристаллического кремния, которую очищают последовательными ультразвуковыми ваннами в ацетоне и спирте в течение примерно 10 мин. В экспериментах по созданию пленок толщиной в несколько десятков нанометров скорость вращения выбрана равной 6000 об / мин. После нанесения покрытия пленки из ПММА подвергаются дополнительному отжигу при 125 ° C, что близко к температуре стеклования ПММА, в течение 30 минут.
Эксперименты проводятся на коммерческом АСМ (Dimension Icon; Bruker Corporation, США). Силиконовый наконечник выбирается с номинальной жесткостью пружины 42 Н / м и резонансной частотой 320 кГц, предоставленной производителем (TESPD; Bruker Corporation, США). Сторона наконечника кантилевера закалена алмазоподобным углеродным покрытием (DLC) для увеличения срока службы наконечника. Измерение наноструктур на поверхности ПММА установлено в режиме постукивания с частотой сканирования 1 Гц и линией сканирования 256. При использовании другого зонда необходимо настроить консольную систему. В этом исследовании точка настройки настроена на 300 мВ. Изображения обрабатываются уплощением первого порядка с использованием программного обеспечения Nanoscope Analysis, предоставленного компанией Bruker.
Оборудованный модуль Nanoman в системе AFM используется для процесса царапания в этом исследовании, который широко применяется для проектирования траектории иглы для получения желаемых структур, таких как прямоугольники или круги, на поверхности образца. Чтобы изменить поверхность, значение амплитуды возбуждения наконечника следует увеличить до V . w (запись), где взаимодействие между иглой и пленкой ПММА стимулируется, чтобы игла проникала через поверхность образца. После процесса царапания значение амплитуды возбуждения наконечника немедленно понижается до V . r (чтение) без изменения кантилевера. Доказано, что по сравнению со статической литографией вспашки износ наконечника при DPL очень мал, и, таким образом, им можно пренебречь. Избегая замены зонда и поиска местоположения наноструктуры, этот метод визуализации на месте может повысить эффективность процесса царапания. Все эксперименты проводятся при комнатной температуре.
Результаты и обсуждение
Учитывая ограничение скорости AFM PZT, в экспериментальных испытаниях выбираются скорости царапания в диапазоне от 0,1 до 1000 мкм / с. На рисунке 1 показана схема процесса наномеханической обработки, включая три диапазона скоростей. При царапании с относительно большой скоростью (около нескольких сотен микрометров в секунду) могут образовываться отдельные ямки, как показано на рис. 1b. Когда скорость царапания снижается до среднего значения (около 100 мкм / с), ямки могут перекрываться друг с другом, как показано на рис. 1c. Как показано на рис. 1d, когда скорость царапания достигает относительно небольшого значения (десятки микрометров в секунду), ямки могут трансформироваться в наноканавки. Этот результат показывает, что расстояние между двумя изготовленными ямками зависит от скорости царапания, которая имеет большое влияние на изготовленные наноструктуры.
В данном исследовании выбраны четыре типичных направления царапания, как показано на рис. 2а. V 1 и V 3 представляют собой царапины по длинной оси кантилевера; V 2 и V 4 определяются как царапины, перпендикулярные длинной оси кантилевера. Траектории острия получаются путем управления AFM PZT. На рисунке 3 показаны АСМ-изображения квадратных наноструктур, изготовленных с различными скоростями царапания, и соответствующие поперечные сечения наноструктур, поцарапанных с направлением V 1 , при резонансной частоте кантилевера 380 кГц. При относительно большой скорости царапания 200 мкм / с могут образовываться сплошные ямки, как показано на рис. 3а. Для четырех направлений царапания, установленных заранее, ямки будут образовываться сразу же, намного меньше, чем за 1 с, даже если скорость царапания ускользнет в точке поворота в двух направлениях. При средней скорости царапания (100 мкм / с) на траектории обработки не может быть обнаружено явных ямок, и образуются флуктуирующие наноструктуры, как показано на рис. 3b. На пересечении двух соседних дорожек царапания можно наблюдать только одну ямку с гораздо большей глубиной, что можно объяснить следующим образом. В течение периода преобразования между двумя соседними дорожками царапания скорость царапания должна снизиться до 0, и острие может вдавливаться в поверхность образца больше раз, чем в случае царапания, что может быть возможной причиной создания большей глубины. ямы. Скорость царапания 100 мкм / с может считаться критическим значением для изготовления сплошных ямок на тонкой пленке из ПММА. На рис. 3с показаны обработанные наноканавки со скоростью царапания 50 мкм / с. Из поперечного сечения обработанной наноканавки можно заметить, что дно наноканавки является относительно плоским, и может быть сформирована очевидная глубина наноканавки. Более того, как показано на рис. 3, поскольку наконечник проталкивает пленку из ПММА, во время царапины не образуются сколы, и могут образовываться только скопления на одной или обеих сторонах канавки. Кроме того, профили разных сторон полученных наноструктур несовместимы при царапании с разных направлений, что аналогично результатам статической литографии с асимметричным острием. Для других материалов резиста, таких как СУ-8 или полистирол (ПС), пороговые значения скорости царапания будут отличаться от таковых для пленки ПММА из-за другого модуля релаксации напряжений. Однако их пороговые значения могут быть получены путем эксперимента по царапанию, следуя тому же подходу, что и в этом исследовании.
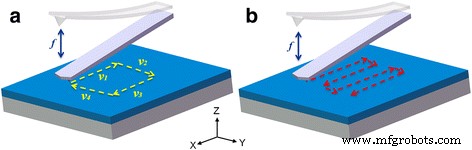
а Четыре типичных направления царапания ( V 1 , V 2 , V 3 , и V 4 ) выбраны для изготовления наночастиц в этом исследовании. б Траектория наконечника с подачей для шаблонов большой площади
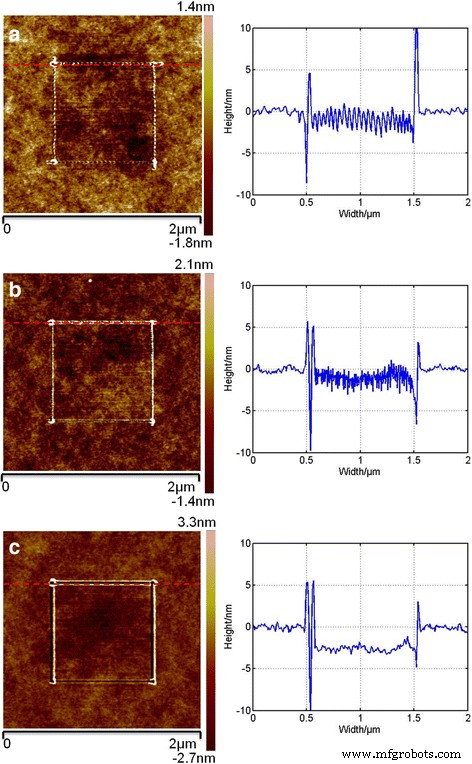
АСМ-изображения трех видов наноструктур и их поперечного сечения со скоростью царапания a 200 мкм / с, b 100 мкм / с и c 50 мкм / с
При скорости царапания менее 100 мкм / с можно получить наноканавки хорошего качества. На рис. 4 показана взаимосвязь между глубиной обработки наноканавки и скоростью царапания с различными направлениями царапания, показанными на рис. 2а. Для каждой наноканавки экспериментальная глубина рассчитывается как среднее из пяти значений глубины в пяти различных местах. Расстояния царапания для всех направлений царапания одинаковы - в данном исследовании 1 мкм. Можно заметить, что глубина обработки уменьшается с увеличением скорости царапания для всех направлений царапания. Одну из возможных причин можно объяснить следующим образом. Для расстояния царапания 1 мкм, выбранного в данном исследовании, количество операций прессования при скоростях царапания 100 мкм / с и 1 мкм / с будет 3870 и 387000 соответственно. При том же расстоянии царапания большое количество операций прессования наконечником AFM может привести к относительно большому проценту перекрытия между соседними операциями прессования, что может привести к большей глубине обработки наноканавки. Кроме того, как показано на рис. 4, глубина наноканавок, поцарапанных во всех направлениях, одинакова, когда скорость царапания меньше 5 мкм / с, в то время как глубина наноканавок, обработанных в направлении V 3 становится намного меньше, чем глубина обработки, полученная в других направлениях со скоростью царапания более 5 мкм / с. Кроме того, полосы погрешностей обработанной глубины, полученные в направлении V 3 намного больше, когда скорость царапания меньше 5 мкм / с, чем для других. Одну из возможных причин можно объяснить следующим образом. Геометрический зонд АСМ, используемый в этом исследовании, является несимметричным, и наклон зонда, вызванный типичным наклоном кантилевера в 12 °, используемый для обеспечения того, чтобы только игла АСМ касалась поверхности образца, может привести к разнице в площади контакта. между зондом и поверхностью образца с разными направлениями царапания. Для скорости царапания менее 5 мкм / с площадь перекрытия смежных операций прессования очень велика. Таким образом, площадь контакта между зондом и поверхностью образца также чрезвычайно велика. Таким образом, влиянием направления царапания на глубину обработки можно пренебречь. Тем не менее, нарост, образующийся вдоль поверхности наконечника, также зависит от направления царапания, что аналогично процессу статического царапания. Следовательно, наложение не может формироваться стабильно в V 3 направление царапания. Вставленные рисунки на рис. 4a, b представляют собой поперечные сечения типичных наноканавок, обработанных со скоростями царапания 0,5 и 50 мкм / с соответственно. Из поперечного сечения наноканавки, обработанной со скоростью царапания 0,5 мкм / с, нижняя часть наноканавки колеблется при царапании в V 3 направление, что может привести к относительно большой полосе погрешности для глубины обработки. При царапании со скоростью более 5 мкм / с площадь перекрытия с соседними операциями прессования становится небольшой. Таким образом, направление царапания играет важную роль, что может привести к относительно небольшой глубине обработки, полученной в V 3 направление царапания.
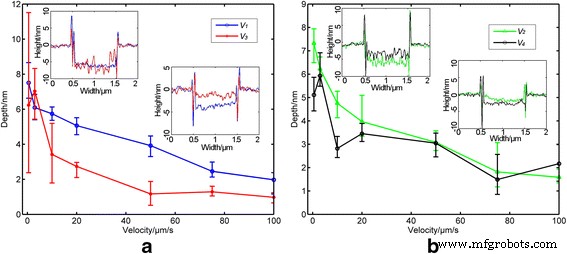
Зависимость глубины канавки от скорости царапания в типичных направлениях царапания: а V 1 и V 3 , параллельно длинной оси кантилевера; б V 2 и V 4 , перпендикулярно длинной оси кантилевера. На вставках показано поперечное сечение наноканавок для скоростей царапания 0,5 и 50 мкм / с
Тонкая пленка из ПММА представляет собой вязкоупругий материал, зависящий от времени. Таким образом, периодическая нагрузка, прикладываемая наконечником АСМ, может влиять на модуль Юнга образца. Общее представление для модуля релаксации напряжений G определяется как G 1 и G 2 [30]:
$$ G \ left (\ omega \ right) ={G} _1 \ left (\ omega \ right) + {iG} _2 \ left (\ omega \ right) $$ (1) $$ {G} _1 \ left (\ omega \ right) =\ left [{G} _r \ right] + {\ int} _ {- \ infty} ^ {+ \ infty} \ frac {H \ left (\ tau \ right) {\ omega} ^ 2 {\ tau} ^ 2} {1 + {\ omega} ^ 2 {\ tau} ^ 2} d \ left (\ ln \ tau \ right) $$ (2) $$ {G} _2 \ left ( \ omega \ right) ={\ int} _ {- \ infty} ^ {+ \ infty} \ frac {H \ left (\ tau \ right) \ omega \ tau} {1 + {\ omega} ^ 2 {\ tau} ^ 2} d \ left (\ ln \ tau \ right) $$ (3)где G r постоянная и ω связано с частотой. H ( τ ) представляет собой спектр времен релаксации, вносимый в релаксацию напряжения, который связан с временами релаксации между ln τ и ln τ + d (ln τ ). Когда частота возбуждения установлена на значение, близкое к резонансной частоте кантилевера, которое составляет 387 кГц, модуль может достигать высокого значения. Согласно расчету с использованием упомянутых выше уравнений, тонкая пленка ПММА представляет собой стеклянное состояние с приложенной высокочастотной нагрузкой [30]. Поскольку режим нарезания резьбы используется во всем процессе обработки, сила взаимодействия и рассеяние энергии между зондом АСМ и поверхностью образца во время процесса царапания относительно невелики, и даже амплитуда возбуждения V w / V r установлен на относительно высокое значение, в диапазоне от 10 до 20. В этих условиях обработки из-за стеклоподобных свойств тонкой пленки из ПММА и относительно небольшой нагрузки, приложенной наконечником АСМ, цепи между молекулами полимера не могут быть повреждены. сломанную и пластическую деформацию трудно вызвать для изменения поверхности образца за один цикл операции прессования. Однако наконечник имеет достаточную энергию (> 1 ~ 2 эВ), чтобы сделать это в течение первых 20–30 раз прессования [27]. Таким образом, цепные связи между молекулами полимера могут быть разорваны, чтобы вызвать пластическую деформацию на поверхности тонкой пленки.
Расстояние между соседними операциями прессования является критическим параметром, который связан со скоростью царапания и частотой колебаний наконечника. Расстояние одной линии приямка ( L ) можно получить, используя время, затраченное на одну линию пита ( t ) умноженное на скорость царапанья ( v ). Общее количество колебаний наконечника АСМ на одной пит-линии ( N ) можно рассчитать, используя частоту колебаний кантилевера ( f ) умноженное на время ( t ). Таким образом, расстояние между соседними операциями прессования ( D ) можно получить по формуле. 4.
$$ D =\ frac {L} {N} =\ frac {v} {f} $$ (4)Собственная частота колебаний кантилевера, выбранного в данном исследовании, составляет примерно 387 кГц. Частота возбуждения системы AFM выбрана близкой к этому значению. Как упоминалось выше, скорость царапания следует выбирать в диапазоне от 200 до 900 мкм / с, чтобы гарантировать образование ямок. Таким образом, расстояние между соседними операциями прессования ( D e ) в процессе царапания можно рассчитать в диапазоне от 0,52 до 2,33 нм, который обозначен красной кривой на рис. 5а. Синяя кривая на рис. 5a представляет соотношение между расстоянием между соседними углублениями ( D ), полученной из экспериментов, и скорости царапанья. Вставленные изображения АСМ получены для ямок, обработанных с тремя типичными скоростями царапания:400, 600 и 800 мкм / с. Следовательно, количество операций прессования для одного карьера можно рассчитать как отношение D к D e показано на рис. 5b. Предполагая, что скорость царапания является постоянной величиной, 4800–5800 ямок может быть образовано на тонкой пленке ПММА за 1 с, если рассчитать по длине царапания ( L ) и расстояние между ними ( D ). Из рис. 5b можно увидеть, что количество операций прессования для образования одной ямы увеличивается с увеличением скорости царапания и в основном находится в диапазоне от 65 до 80. Учитывая, что ровная местность между двумя ямками почти равна размерам питтингов, требуется всего около 32–40 операций прессования, чтобы разорвать полимерные цепи и вызвать пластическую деформацию поверхности образца, что согласуется с выводом Капеллы [27]. Кроме того, можно сделать вывод, что полимерные цепи легче разорвать при царапании с относительно небольшой скоростью. В этом исследовании жесткость пружины кантилевера идентична. Для изготовления ямок можно использовать более жесткий кантилевер, что приводит к большей прилагаемой силе и более высокой резонансной частоте. Если к поверхности образца приложено большее усилие, подвод энергии увеличивается в каждом цикле. Таким образом, большее рассеивание энергии способствует деформации пленки ПММА. Таким образом, можно создать одну яму с уменьшенными циклами. Однако, если резонансная частота колебательной системы увеличивается, цикл операции прессования между поверхностью образца и зондом увеличивается. Кроме того, рассеяние энергии будет увеличиваться за один цикл из-за уменьшения точки схватывания в экспериментах. Критическая скорость может определяться значением уставки. Основываясь на приведенном выше обсуждении, на пороговое значение скорости может влиять приложенная сила, резонансная частота консольной системы и точка установки, которая будет в центре внимания будущих исследований.
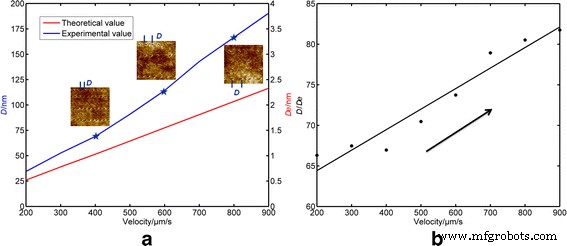
а Вариант D и D e со скоростью царапания (200–900 мкм / с); на вставках показаны результаты изготовления для различных скоростей царапания. б Соотношение D к D e
На рис. 6 показан процесс формирования ямы, включающий три фазы:упругую деформацию, пластическую деформацию и преодоление нагромождения. Согласно приведенному выше обсуждению, во время царапания наконечника на расстоянии от рис. 6а, б количество операций прессования недостаточно велико для разрыва полимерных цепей тонкой пленки ПММА и возникновения пластической деформации поверхности образца. Показано, что осциллирующий наконечник проникает в образец полимера постепенно в течение первых 40–50 операций [27]. По сравнению с процессом индентирования в работе Ref. [27], нажатие с боковой скоростью могло создать расстояние между двумя соседними проходками. Однако расстояние между двумя соседними проникновениями (в диапазоне от 0,52 до 2,33 нм) намного меньше, чем радиус острия АСМ (примерно 15 нм). Таким образом, ситуация в данном исследовании аналогична случаю процесса вдавливания. Из-за отсутствия накопления энергии во время начальных 30–40 проникновений явной пластической деформации в зоне обработки не наблюдается. Этот результат указывает на то, что доминирующим механизмом диссипации энергии является упругая деформация на первой стадии царапания. Таким образом, острие АСМ скользит в постоянном контакте с поверхностью образца в течение периода времени между рис. 6a, b. Когда количество проникновений, выполненных наконечником АСМ, достигает критического значения (40 раз в данном исследовании), полимерные цепи начинают разрываться и происходит пластическая деформация, как показано на рис. 6c. В то же время на поверхности взаимодействия между передней поверхностью наконечника АСМ и материалом образца возникнет нормальное напряжение и напряжение сдвига; таким образом, может образоваться наложение перед передней поверхностью наконечника АСМ. Произойдет деформация (Δ), связанная с боковым движением наконечника против скопления. Это приведет к возникновению напряжения внутри полимерной пленки, которое может быть снято при распространении трещины [31]. Скорость выделения энергии деформации V s можно описать как:[32].
$$ {V} _s =E \ frac {h} {2} {\ left (\ frac {\ varDelta} {L} \ right)} ^ 2 $$ (5)где E - модуль Юнга полимерного материала и L - длина внутреннего дефекта. h представляет собой общую глубину проникновения до свободной поверхности образца. Член поверхностной энергии W контролирует внутренний дефектный процесс, равный скорости выделения энергии деформации через термодинамическое равновесие. Член поверхностной энергии зависит от скорости распространения внутреннего дефекта ( v L ), который дается [33].
$$ W ={W} _0 \ left (1+ \ alpha {v} _L ^ n \ right) $$ (6)где v L равно d L / d t и α - постоянная величина, относящаяся к материалу образца. нет также является параметром, связанным с материалом. Тангенциальная сила, приложенная к вершине наконечника, может быть создана за счет упругой энергии, накопленной в полимерной подложке, что может быть выражено как [32]:
$$ {F} _t =\ frac {Eah} {2} \ frac {\ varDelta} {L} $$ (7)где a представляет собой радиус области контакта между зондом и образцом. Поскольку жесткость зонда намного превышает жесткость образца, материал может быть удален из сформированного отверстия [31]. Однако Миндлин определил критическое значение силы, которое могло привести к скольжению иглы по поверхности подложки [34]. Критическая касательная сила ( F tc ) для скользящего движения можно определить как функцию силы сцепления и нормальной нагрузки, выраженную как [35,36,37,38]:
$$ {F} _ {tc} =\ mu \ left (P + 3 \ pi RW + \ sqrt {6 \ pi RW P + {\ left (3 \ pi RW \ right)} ^ 2} \ right) $$ ( 8)где μ коэффициент трения. P является нормальным, а R представляет собой радиус острия АСМ. Когда F t достигает критического значения F tc наконечник АСМ будет скользить по скоплению материала вместо того, чтобы выталкивать материал из отверстия, образованного наконечником. Контакт размыкается в каждом цикле, и, таким образом, скольжение может происходить легче в каждом цикле в режиме нарезания резьбы. Хотя точка установки не близка к 100% уменьшения колебаний наконечника, период времени контакта может иметь место в течение одного цикла, и стержень может происходить в течение этого периода времени.
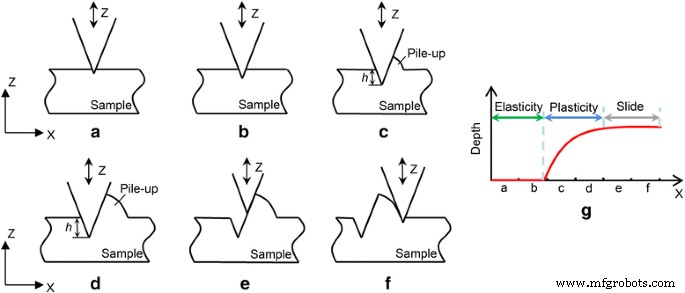
Схема формирования ямы с a , b стадия эластичности, c , d стадия пластичности, е , f этап слайда и g диаграмма предшествования формирования карьера
Как показано на рис. 6d, в этом исследовании глубина, на которую зонд АСМ проникает в поверхность образца, становится больше из-за уменьшения площади контакта зонд-образец, когда игла АСМ движется с поперечной скоростью. Высота наложения также увеличена. Это может способствовать уравновешиванию нормальной нагрузки, прикладываемой наконечником АСМ. В то же время касательная сила, приложенная к вершине острия, описанная в формуле. 7 также можно было увеличить. With an increasing penetration depth, the tangential force could reach the critical value F tc given in Eq. 8. The AFM tip starts to slide on the formed pile-up without modifying the material. Because of the characteristics of the tracking sample surface of the AFM system, the AFM tip would rise to climb over the pile-up, as shown in Fig. 6e. After the AFM tip moved over the pile-up, one pit could be achieved and another pit would be fabricated by repeating the above steps. The corresponding deformation mechanism of each stage of pit formation can be found in Fig. 6g.
According to the previous experimental results, the scratching velocity should be set to larger than 100 μm/s. As shown in Fig. 2b, scratching directions V 1 и V 3 are selected and a feed perpendicular to the scratching direction is conducted to achieve pit arrays with a large dimension of 5 μm. Figure 7a shows the pit arrays obtained with a scratching velocity of 400 μm/s. Figure 7b, c shows the local and 3D AFM images of the machined pits, respectively. Because the scratching velocity slows down to 0 near the transition point of two different scratching directions, the depths of the first and last pits of one horizontal scratching path are much larger than the pits in the middle. One possible reason is explained above. As shown in Fig. 7b, c, the pits in the middle of the scratching path are distributed evenly, which may result from the constant velocity. Moreover, it can be observed from the cross-section of the pits shown in Fig. 7d that the depths of the pits are approximately 2.5 nm. In addition, because of the opposite scratching directions of the adjacent paths, the geometries of the pits in adjacent lines are different. As shown in Fig. 8a, with a scratching velocity of 200 μm/s, the spacing distance between the adjacent pits is relatively small and the geometries of the pits are close to circular. From the fast Fourier transform (FFT) image of the pits, high-density pits can be obtained with a scratching velocity of 200 μm/s. When scratching with a velocity of 900 μm/s, as shown in Fig. 8b, the spacing distance is nearly 100 nm and differences between pits obtained with different scratching directions can be clearly observed. Also from the FFT image of the pits, with a scratching velocity of 900 μm/s, only low-density pits can be achieved.
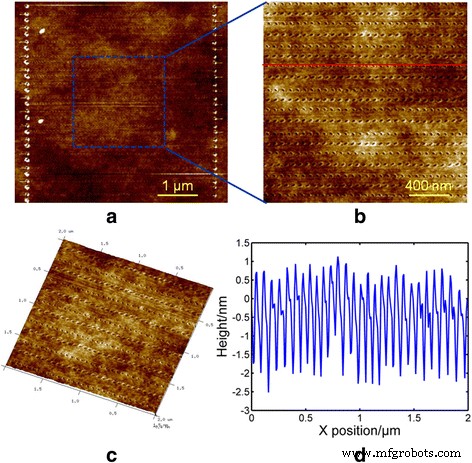
AFM images of an array of pits with a scratching velocity of 400 μm/s, a a dimension of 5 μm, b a portion of a with a dimension of 2 μm, c a 3D AFM image of b , и d a cross-section of pits for the red line in b
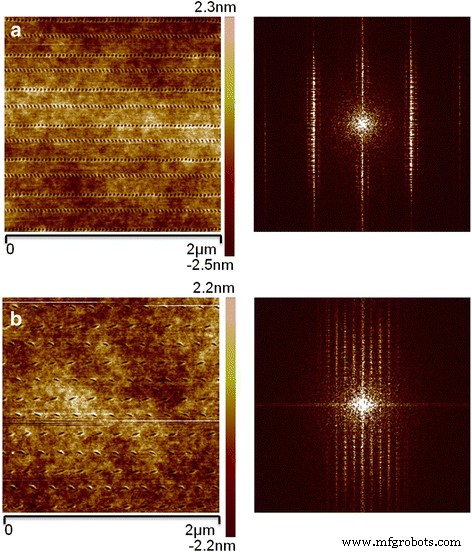
AFM image of pit arrary with a dimension of 2 μm and FFT image of the morphology. The scratching velocities are a 200 μm/s and b 900 μm/s
Выводы
To improve the fabrication efficiency with the tip-based DPL method, a scratching velocity that ranges from 0.1 to 1000 μm/s is investigated and demonstrated based on the commercial AFM tapping mode. In the present study, results demonstrate that 100 μm/s is the critical value of the scratching velocity for the formation of pits. Nanogrooves with a pile-up can be obtained with scratching velocities less than the critical value. With scratching velocities greater than 5 μm/s, the machined depths are consistent in all typical directions except the V 3 direction, in which the machined depth becomes much smaller. In contrast, the depth is independent of the scratching direction. Separate pits can be generated with scratching velocities larger than the critical value of 100 μm/s. The total number of fabricated pits can reach nearly 4800–5800 in 1 s, when the scratching velocity is a constant value ranging from 200 to 900 μm/s. According to the stress relaxation modulus theory, the polymer surface is in the condition of a glass state when applying a high-frequency load. The energy applied on the sample surface is not large enough to break PMMA molecular chains during one penetration of the AFM tip. To form one pit, 65 to 80 penetrations are required. For the initial stage of penetration, elastic deformation is the dominant material removal mechanism. When the number of penetrations reaches 40 times, the polymer chains start to break and plastic deformation occurs. With increasing penetration depth, the height of the material accumulated beside the machined pit becomes larger, which will lead to an increase in the tangential force applied on the tip apex. This is the possible reason for the AFM tip sliding over the pile-up, after which one pit is created. Finally, pit arrays with dimensions of 5 μm, spacing distance of 70 nm, and machined depth of 2.5 nm are achieved successfully. FFT images are used to reveal the relationship between the density of pits and the scratching velocity.
Наноматериалы
- Пионеры AFM отмечены премией Кавли
- Пакетное производство широкополосных металлических плоских микролинз и их матриц, сочетающих самосборку на…
- Изготовление упорядоченного наноразмерного рисунка с использованием триблочного сополимера ABC с солью в тол…
- Высокопроизводительное производство качественных нановолокон с использованием модифицированного электрос…
- Изготовление схем оптической коммутации из структурных цветных микроволокон
- Одношаговая дифракционная литография на основе маски для изготовления трехмерных подвесных конструкций
- Безрезисторный источник опорного напряжения в наномасштабе с низким энергопотреблением и высоким PSRR
- Ge pMOSFET с высокой подвижностью и пассивированием аморфным Si:влияние ориентации поверхности
- Производство полидиметилсилоксановых наножидкостных чипов с помощью процесса наномоллирования на основе н…
- Стабильные полимерные чернила с высокой проводимостью