Получение нанокомпозитов Cu @ C типа желток-оболочка в качестве высокоэффективных катализаторов окислительного карбонилирования метанола в диметилкарбонат
Аннотация
Был разработан простой способ изготовления композитов желток-оболочка с настраиваемыми медными ядрами, заключенными в полые углеродные сферы (Cu @ C) со средним диаметром около 210 нм и размером полости около 80 нм. Во время пиролиза ограниченное нанопространство полой полости гарантирует, что процесс зарождения и роста нанокристаллов Cu происходит исключительно внутри полостей. Размер сердечников Cu можно легко регулировать от 30 до 55 нм, варьируя концентрацию соли меди. За счет преднамеренного создания пористости оболочки посредством химической активации КОН при оптимизированном массовом соотношении КОН / HCS 1/4 каталитические характеристики окислительного карбонилирования метанола в диметилкарбонат (ДМК) активированного образца значительно улучшаются с TOF до 8,6 ч −1 при конверсии метанола 17,1%. Катализатор с активированной оболочкой из желтка демонстрирует многообещающие каталитические свойства, включая возможность повторного использования с небольшой потерей каталитической активности и незначительным выщелачиванием активированных компонентов даже после семи циклов рециркуляции, что способствует тщательному внедрению экологически чистого производства экологически чистого химического вещества DMC.
Фон
Диметилкарбонат (ДМК) привлек большое внимание как широко используемый строительный блок из-за его превосходной биоразлагаемости (например, низкой биоаккумуляции и стойкости) и низкой токсичности [1]. Потенциальные промышленные применения DMC охватывают многие области, такие как неядовитые растворители, альтернативные заменители фосгена, топливные добавки и промежуточные продукты для синтеза поликарбонатов и изоцианатов [2,3,4,5]. С учетом различных методов синтеза DMC, окислительное карбонилирование метанола (MeOH) с использованием CO, O 2 , и MeOH в качестве сырья представляет собой один из предложенных благоприятных процессов из-за высокой степени использования источника углерода и экологических преимуществ. Катализаторы, используемые в этой реакции, в основном можно разделить на два типа:хлорсодержащие катализаторы и бесхлорные катализаторы. Поскольку существуют некоторые проблемы, такие как серьезные коррозионные проблемы, ухудшение качества продукта и дезактивация катализатора, которые возникают из-за потери хлора из хлорсодержащих катализаторов, катализаторы, не содержащие хлора, были тщательно изучены [6, 7]. Медь или оксид меди, нанесенные на активированный уголь (AC), показали многообещающую каталитическую активность для синтеза DMC [8,9,10], и исследователи предположили, что Cu является активным центром этой реакции [10,11,12,13]. Однако дезактивацию нанесенных медных катализаторов обычно связывают с агломерацией частиц меди, потерей активных частиц и изменением химического состояния меди, среди которых первое является более серьезным. Чтобы преодолеть такие недостатки, разработка и изготовление наночастиц, инкапсулированных в защитную оболочку, выгодно для усиления каталитической активности и стабильности реакционных центров при окислительном карбонилировании метанола до DMC с технологической точки зрения.
Вдоль этой линии наноструктуры желточной оболочки (YSNs) или нанокомпозиты типа rattle, в которых основные наночастицы (NP) инкапсулированы внешним слоем с межузельным свободным пространством между ними, были особенно популярны из-за их уникальных иерархических / многоуровневых наноструктур. , а также сопутствующие оптические и электрические свойства и большой потенциал каталитического применения [14]. Защитная оболочка в YSN может эффективно поддерживать стабильность основного элемента даже в суровых условиях и в достаточной степени обнажать его активную поверхность [15]. Предполагается, что замкнутое пустое пространство будет полезно для химического хранения, компартментации и ограничения взаимодействий хозяин-гость и, что более важно, обеспечит уникальную среду для создания согласованных действий между ядром и проницаемой оболочкой [16]. Эти замечательные текстурные характеристики позволяют YSN функционировать как многообещающий кандидат для удовлетворения таких требований, как стабильность к спеканию и возможность повторного использования для приложений в катализе. Среди них наноструктуры желток-углеродная оболочка сразу же привлекли значительный интерес благодаря собственной проводимости, а также превосходной химической и термической стабильности углеродного покрытия [17,18,19,20,21].
Недавно Лю и его сотрудники сообщили о получении полых сфер посредством сборки, индуцированной слабым кислотно-основным взаимодействием, с использованием олеиновой кислоты, мягкой матрицы и функциональной дигидроксибензойной кислоты (DA) в качестве предшественника [22]. Здесь мы расширяем их работу, чтобы разработать легкость для YSN с настраиваемым размером ядра Cu, инкапсулированным внутри полых углеродных сфер (HCS) (Cu @ C), используя стратегию «корабль в бутылке». Пористость оболочки гетерогенных катализаторов Cu @ C можно регулировать активацией КОН, а также исследовать ее влияние на каталитические характеристики и стабильность при синтезе ДМК.
Методы
Химические вещества
2,4-Дигидроксибензойная кислота (DA) была получена от J&K Scientific Ltd. Олеиновая кислота, раствор аммиака (25%), формальдегид, нитрат меди (Cu (NO 3 ) 2 · 3H 2 О), гидроксид калия (КОН) и метанол (МеОН) были получены от Sinopharm Chemical Reagent Co. Ltd. Все химические вещества были аналитической чистоты и использовались без какой-либо дополнительной очистки. Во всех экспериментах использовалась деионизированная вода, полученная из системы Milli-Q (Millipore, Bedford, MA). О 2 (> 99,99%) и CO (> 99,99%) были поставлены компанией Beijing ZG Special Gases Science &Technology Co. Ltd.
Синтез полых углеродных сфер (HCS)
Полые полимерные сферы (HPS) с полой сердцевиной и полимерной оболочкой сначала были приготовлены с использованием олеиновой кислоты в качестве мягкой матрицы и фенольной смолы в качестве предшественника углерода в соответствии с процедурой, описанной Lu et al. [22]. В типичной процедуре 2,5 ммоль 2,4-дигидроксибензойной кислоты и 7,5 ммоль формальдегида растворяли в 95 мл деионизированной воды. 5 мл водного раствора, содержащего 56 мкл олеиновой кислоты и 180 мкл раствора аммиака (25%), добавляли к приготовленному выше раствору при 30 ° C и медленном перемешивании в течение 30 мин. Затем смесь переносили в автоклав, подвергнутый гидротермальному старению в течение 4 ч при 140 ° C. После центрифугирования, промывания деионизированной водой и этанолом, высушивания при 50 ° C в течение ночи и затем пиролиза при 700 ° C в течение 2 часов в токе азота получали HCS.
Синтез нанокомпозитных материалов Cu @ C
Обычно 0,3 г свежеприготовленных HCS сначала диспергировали в 30 мл раствора нитрата меди с различным диапазоном концентраций от 0,03 до 0,24 М. Затем смесь переносили в автоклав для гидротермальной пропитки при 100 ° C в течение 10 минут. час Полученный пропитанный образец, обозначенный как HCS-Cu 2+ , был получен тем же способом, что и HPS. После прокаливания при 400 ° C в течение 2 часов в атмосфере H 2 / N 2 (10% / 90%), наконец, были получены нанокомпозиты «желток-оболочка» Cu @ C-X (X =0,03, 0,06, 0,12, 0,24).
Синтез катализатора Cu @ A-HCS со сферой из активированного угля KOH в качестве носителя
Предпринята попытка обработки HCS KOH с целью изменения характеристик углеродного носителя и дальнейшего воздействия на характеристики Cu-катализатора. Обычно 0,3 г HCS физически смешивали с 0,15 г КОН в отсутствие воды. После предварительной обработки образец нагревали в потоке азота 80 мл / мин со скоростью нарастания 10 ° C / мин до 700 ° C в течение 2 ч, а затем охлаждали до комнатной температуры. Уголь, подвергнутый последующей обработке КОН, многократно промывали разбавленной HCl, а затем дистиллированной водой до тех пор, пока не перестанут обнаруживаться ионы хлора (AgNO 3 контрольная работа). После сушки при 60 ° C в течение ночи во время гидротермальной пропитки использовали 0,12 М раствор нитрата меди, а другие процедуры были идентичны процедурам для Cu@C-0,12, в результате получили модифицированные образцы, обозначенные как Cu @ A-HCS.
Каталитические характеристики Cu @ C-X (X =0,03, 0,06, 0,12, 0,24) и Cu @ A-HCS
Окислительное карбонилирование метанола проводили в автоклаве из нержавеющей стали объемом 25 мл, футерованном тефлоном и снабженном магнитной мешалкой. В типичном эксперименте 0,2 г катализатора и 10 мл метанола загружали в автоклав, который затем плотно закрывали, трижды продували CO и затем повышали давление до 3,0 МПа с помощью CO и O 2 (P CO :P O2 =2:1) при комнатной температуре. Реакция протекала при 120 ° C при непрерывном перемешивании со скоростью 750 об / мин в течение 1,5 часов. После реакции реактор охлаждали до комнатной температуры и сбрасывали давление. Катализаторы отделяли фильтрованием. Концентрации продуктов в фильтрате определяли методом газовой хроматографии (ГХ) с использованием детектора FID. Возможность повторного использования использованного катализатора была изучена путем проведения серии последовательных прогонов.
Основная реакция окислительного карбонилирования метанола до диметилкарбоната показана ниже:
2 канала 3 ОН + 1/2 СО + О 2 =(Канал 3 O) 2 CO + H 2 О.
Концентрация меди, конверсия MeOH (C MeOH ), Селективность DMC (S DMC ) и частота оборота (TOF) рассчитывались по следующим уравнениям:
Концентрация меди (C Cu , ммоль / г) =содержание Cu (мас.%) / 63,55 × 1000.
Превращение МеОН (C MeOH ,%) =прореагировавший метанол / введенный метанол × 100%.
Избирательность DMC (S DMC ,%) =2 полученный ДМК / прореагировавший метанол × 100%.
Частота оборота =произведенный DMC / (молярное количество меди × время реакции).
Характеристика
Картины дифракции рентгеновских лучей (XRD) записывали на дифрактометре Rigaku D-Max 2500 с использованием Cu K α излучение ( λ =0,154 нм) при 40 кВ и 100 мА, со скоростью сканирования 4 ° мин −1 при 2 θ от 5 ° до 85 °. Анализ с помощью просвечивающей электронной микроскопии (ПЭМ) проводили на просвечивающем электронном микроскопе с полевой эмиссией JEM 2100F (JEOL, Токио, Япония), работающем при 200 кэВ. Образцы ПЭМ были приготовлены путем погружения сеток Cu с покрытием C в этанольные растворы образцов и сушки при комнатной температуре. Термогравиметрический (ТГ) анализ проводился на термогравиметрическом анализаторе STA 449 F3 Jupiter (NETZSCH) с N 2 или расход воздуха 50 мл / мин. Площадь поверхности и объем пор определяли по изотермам адсорбции азота при 77 К с использованием анализатора площади поверхности 3H-2000PS2 (Beishide). Удельные площади поверхности Брунауэра-Эмметта-Теллера (БЭТ) были рассчитаны с использованием данных адсорбции в диапазоне относительных давлений P / P 0 =0,04–0,3. Кривые распределения пор мезопор по размерам рассчитывались методом BJH (Barrett-Joyner-Halenda) по адсорбционной ветви. Общий объем пор был оценен по количеству азота, адсорбированного при относительном давлении ( P / P 0 ) 0,99. Содержание меди определяют растворением катализатора в смеси сильных кислот с последующим анализом атомно-адсорбционной спектрометрии (AAS) с использованием оборудования SpectrAA-220 AAS. Анализ продукта реакции проводили методом газовой хроматографии (ГХ; Agilent 6890) с использованием детектора FID.
Результаты и обсуждение
Параметры текстуры и термическая стабильность предварительно подготовленной опоры
Площадь поверхности по БЭТ и объем пор образцов, участвующих в различных стадиях приготовления, сведены в Таблицу 1. Как видно на рис. 1а и в таблице 1, полученный ГЭС имеет низкие площади поверхности по БЭТ (~ 23 м 2 г −1 ). Таким образом, введение предшественников катализаторов с помощью обычного метода пропитки вряд ли возможно. Таким образом, мы используем процесс гидротермальной пропитки для улучшения диффузионной способности, так что прекурсор меди может быть успешно втянут в полость HPS. Площадь поверхности по БЭТ HPS и HPS-Cu изменена с 23 до 15 м 2 г −1 заверил заявление. Кроме того, изображения ПЭМ на рис. 2 дополнительно подтверждают наличие наночастиц Cu, образованных исключительно в пределах углеродной оболочки.
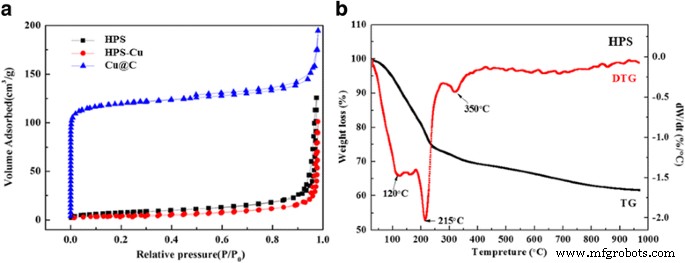
а N 2 изотерма адсорбции-десорбции продуктов, полученных после каждой стадии:HPS, HPS-Cu 2+ , и Cu @ C. б Профили ТГ-ДТГ ГЭС
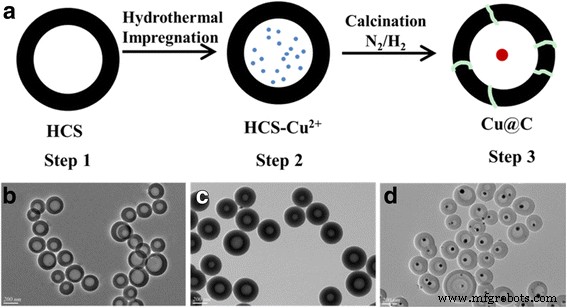
а Схематическое изображение синтеза нанокомпозитов Cu @ C в условиях гидротермальной пропитки. ПЭМ-изображения продуктов, полученные после каждого шага: b HCS, c HCS-Cu 2+ , и d Cu @ C
Процесс карбонизации HPS исследуется TG. На рисунке 1b показан результат TG-DTG в N 2 . . На протяжении всего этого интервала основная потеря HPS происходит около 215 ° C и завершается около 350 ° C. Это можно объяснить разложением олеиновой кислоты, внедренной внутри ГПС, и карбонизацией полимерного каркаса [22]. Таким образом, по сравнению с кривыми ТГ катализаторов Cu @ C (см. Рис. 5b), чтобы обеспечить полную карбонизацию HPS и предотвратить агрегацию наночастиц Cu, оптимальная температура приготовления была определена в 400 ° C.
Структурные свойства нанокомпозитов Cu @ C
В качестве примера взят нанокомпозит «желточная оболочка» [email protected], процедура синтеза для получения структур «желточная оболочка» с наночастицами Cu, инкапсулированными углеродной оболочкой, в соответствии со стратегией «корабль в бутылке», проиллюстрирована на рис. 2а. На рис. 2b, c показаны типичные ПЭМ-изображения конечного продукта, полученные на каждом этапе. Как видно, успешно синтезированы ГТС с однородным размером около 210 нм (рис. 2б). В процессе гидротермальной пропитки не наблюдается очевидной разницы между HCS и HCS-Cu 2+ . (Рис. 2в). Однако после прокаливания морфология полости сохраняется, но можно наблюдать НЧ Cu из-за разложения солей меди. Наконец, достигается структура Cu @ C со структурой желточной оболочки (рис. 2d) с диаметром ~ 200 нм и размером полости ~ 80 нм. Просвечивающая электронная микроскопия высокого разрешения (HRTEM) (рис. 3b) показывает, что частицы ядра имеют пространство 0,18 нм, индексируемое по плоскости Cu (2 0 0). Это согласуется с результатами XRD (рис. 3c), где дифракционные пики при 2 θ =43,3 °, 50,4 ° и 74,1 ° стали наблюдаемыми, поскольку Cu 2+ виды на предшественнике (HCS-Cu 2+ ) восстанавливаются до металла Cu в восстановительной атмосфере, соответствующей конкретным (1 1 1), (2 0 0) и (2 2 0) кристаллическим плоскостям Cu, соответственно, что основано на карте JCPDS 04-0836. . N 2 Изотерма адсорбции-десорбции полученного [email protected] представляет собой изотерму типа I, демонстрируя наличие обильных микропор на углеродных оболочках [email protected] (рис. 3d). Этот образец имеет площадь поверхности по БЭТ 365 м 2 / г с объемом пор 0,23 см 3 /г. Низкая удельная поверхность вместе с узкой микропористостью обычно указывается в качестве основных недостатков, ограничивающих возможности их применения, которые будут рассмотрены ниже. Подробные параметры текстуры образцов приведены в Таблице 2.
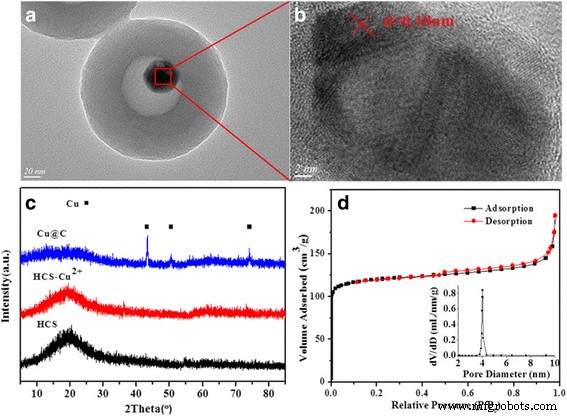
а , b ПЭМ-изображения медной жилы в [email protected]. c Рентгенограммы продуктов, полученных после каждого этапа:HCS, HCS-Cu 2+ и [email protected]. г N 2 Изотерма адсорбции-десорбции и распределение пор по размерам Cu@C-0,12
Механический путь образования одиночных наночастиц Cu внутри углеродной оболочки можно объяснить ограниченным процессом зарождения и роста. В процессе пиролиза многие начальные крошечные ядра CuO сформировались и полностью распределились внутри полой полости из-за разложения включенной Cu (NO 3 ) 2 молекулы. Когда восстановитель H 2 диффундирует в полость, образующиеся ядра CuO далее восстанавливаются до металлических ядер Cu, которые имеют тенденцию мигрировать и агрегировать с образованием более крупных частиц. Когда образуются более крупные, оставшиеся ядра Cu в полости будут последовательно поглощаться поверхностью предварительно сформированных частиц, что приводит к росту нанокристаллов Cu. Подобный механизм также был предложен в другом месте [23]. Основываясь на процессе зародышеобразования и роста, можно сделать вывод, что размер полученного ядра Cu можно контролировать, регулируя количество прекурсора соли меди, размещенного в замкнутой полости.
Контроль размера Cu Core
Изменяя Cu (NO 3 ) 2 с концентрацией от 0,03 до 0,24 М была получена серия нанокомпозитов с оболочкой из желтка, обозначенных как Cu @ C-X (X =0,03, 0,06, 0,12, 0,24). Морфологию и размер продуктов исследовали с помощью просвечивающей электронной микроскопии. Как видно на рис. 4a – d, почти все полые наносферы состоят из одной частицы внутри. Однако размер ядра Cu образующихся наносфер увеличивается с 30 ± 1,3 до 55 ± 2,5 нм (рис. 4e – h) с увеличением Cu (NO 3 ) 2 концентрации, определяемые из изображений ПЭМ с учетом не менее 150 частиц. Примечательно, что часть полых углеродных сфер (HCS) сосуществует с YSN для низкого содержания Cu (NO 3 ) 2 концентрации (рис. 4а). Кроме того, несколько небольших наночастиц Cu, декорированных на внешней поверхности углеродной оболочки (рис. 4d), могут быть вызваны разложением и агрегацией остаточной Cu (NO 3 ) 2 вне оболочки.
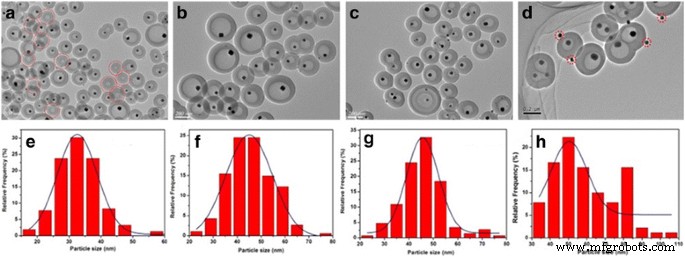
ПЭМ-изображения и соответствующие гистограммы распределения наночастиц Cu по размерам в образцах: a , e [email protected], b , f [email protected], c , г [email protected] и d , ч [email protected]
На рис. 5а показаны дифрактограммы свежеприготовленного Cu @ C-X (X =0,03, 0,06, 0,12, 0,24). Все образцы имеют три типичных пика отражения, привязанных к кристаллам Cu (карта JCPDS № 04-0836). По мере увеличения концентрации соли меди дифракционные пики становятся намного сильнее и резче, а размер НЧ Cu увеличивается с 26,6 до 52,2 нм с помощью уравнения Шеррера, основанного на самом сильном пике на диаграммах, что хорошо согласуется с результатами ПЭМ. . Кроме того, ТГ-анализ был проведен для определения содержания Cu в наносферах на рис. 5b. Предполагая, что остатки полностью состоят из CuO, рассчитанные количества загрузки Cu для Cu @ CX (X =0,03, 0,06, 0,12, 0,24) составляют приблизительно 5,9, 7,5, 8,0 и 9,9 мас.% Соответственно, что идентично значения, определенные на основе анализа AAS.
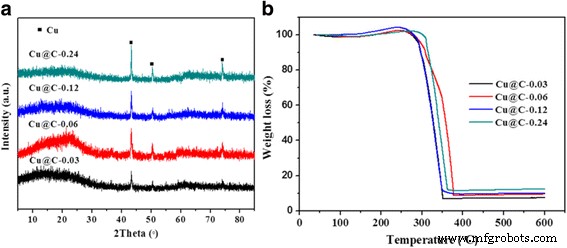
а Диаграммы XRD и b Кривые ТГ образцов:[email protected], [email protected], [email protected], [email protected]
Каталитическая эффективность Cu @ C-X (X =0,03, 0,06, 0,12, 0,24)
Свежеприготовленный катализатор Cu @ C испытывали на жидкофазное окислительное карбонилирование метанола до DMC (таблица 2). Неожиданно, хотя катализатор Cu@C-0,12 был лучше других, он дал только крайне неэффективную конверсию метанола 0,82%. Низкая каталитическая активность может быть связана с отсутствием достаточной пористости и большим объемом пор в оболочке. Насколько нам известно, поры, расположенные на оболочке, действуют как каналы, соединяющие пустоту сфер с внешней средой [24]. Хотя толщина оболочки Cu@C-0,12 составляет ~ 15 нм, отсутствие достаточной пористости (структурный объем пор 0,23 см 3 / г с низкой удельной поверхностью 365 м 2 / g) ограничивает количество молекул реагента для диффузии в полости и дальнейшего контакта с скрытым активным компонентом ядер Cu. Таким образом, очень важно создать большую пористость в оболочках для облегчения массопереноса. Как известно, активация КОН - это хорошо зарекомендовавший себя метод регулирования пористости углеродных материалов [25,26,27]. С помощью этого метода в углерод можно ввести микропоры и мезопоры, а также значительно увеличить удельную поверхность и объем пор [28]. Во время процедуры активации количество КОН обычно считается критическим фактором, влияющим на пористую структуру; таким образом, были сделаны различные массовые отношения КОН / HCS для оптимизации активированного Cu@C-0,12.
Физико-химические свойства Cu @ A-HCS
ПЭМ-изображение (рис. 6a) показывает, что активированный образец Cu @ A-HCS сохраняет сферическую морфологию при более низком массовом соотношении KOH / HCS (1/4), но частично или сильно травлен с массовым отношением KOH / HCS выше 1 / 2 (См. Дополнительную информацию на рис. 2a, b). Этот результат хорошо согласуется с предыдущими сообщениями о том, что чрезмерное количество КОН приведет к большему выгоранию углерода и разрушит морфологию [29]. Интересно, что для нанокомпозитов Cu @ A-HCS после активации высокодисперсные частицы меди преимущественно внедряются в оболочку полых сфер, которые сосуществуют с несколькими, заключенными в полости. По сравнению с [email protected], НЧ Cu, вставленные в оболочку, демонстрируют относительно меньший размер частиц с центром на 18 ± 2 нм (рис. 6b), поскольку матрица оболочки препятствует росту небольших кластеров Cu. Наличие белых точек на оболочке свидетельствует о существовании неупорядоченных микроспор. На рисунке 6c показан N 2 изотермы -адсорбции-десорбции Cu @ C-HCS, которые демонстрируют характерные кривые IV типа, связанные с особенностями мезопор, показывая, что активированные образцы обладают иерархически микро- / мезопористыми структурами. Также можно обнаружить, что после активации КОН при 700 ° C в течение 2 часов площадь поверхности A-HCS увеличилась с 471 до 989 м 2 / г, даже больше, чем у активированного угля (812 м 2 / г), и объем микропор (V mic ), объем мезопор (V mes ), а общий объем (V T ) тоже увеличилось, но соотношение V mic в V T имеет тенденцию к уменьшению. Этот результат указывает на то, что после активации КОН создается больше мезопор, что, возможно, связано с расширением микропор или созданием мезопор в присутствии КОН [30]. Типичная большая площадь поверхности и развитая пористость катализаторов Cu @ A-HCS способствуют диспергированию активной фазы на носителе, гарантируют быстрый перенос вещества между ограниченным катализатором и внешней средой (реагентами) и повышают его устойчивость к спеканию. при высокой загрузке металла [31]. Как подтверждается диаграммой XRD на фиг. 6d Cu @ A-HCS, все пики можно без сомнения индексировать как кубическую Cu (JCPDS 04-0836); Между тем уширение характерных пиков означает образование НЧ Cu малого размера. Фактически, средний размер наночастиц Cu в Cu @ A-HCS оценивается в 15 нм в соответствии с уравнением Шеррера, что согласуется с результатом, полученным с помощью ПЭМ. Как и ожидалось, катализаторы Cu @ A-HCS с 11 мас.% Cu, определенные методом AAS, были получены с использованием того же метода, выше, чем Cu@C-0,12. Что еще более важно, во время процесса активации кислородсодержащие функциональные группы, возможно, возникшие в результате активации КОН, неизбежно вводятся в HCS [27]. В целом, образование поверхностных групп, увеличение площади поверхности и объема пор синергетически приводит к высокому диспергированию наночастиц Cu, что способствует усилению каталитической активности [32,33,34]. Подробные текстурные свойства приведены в таблице 3.
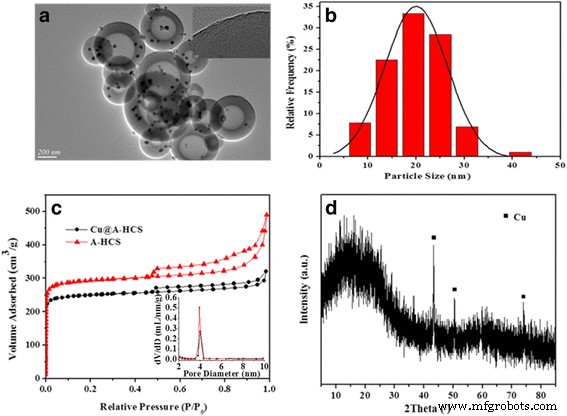
а ПЭМ-изображение Cu @ A-HCS и b соответствующий размер частиц Cu. c N 2 изотермы адсорбции-десорбции и распределения пор по размерам A-HCS и Cu @ A-HCS. г Картины XRD катализатора Cu @ A-HCS
Каталитические характеристики Cu @ A-HCS
Каталитические характеристики A-HCS и Cu @ A-HCS суммированы в таблице 4. Как показано в таблице 4, ясно, что носитель A-HCS не проявлял каталитической активности при синтезе DMC. Как и ожидалось, каталитические свойства активированного образца резко улучшились по сравнению с неактивированным. Примечательно, что по сравнению с 2,04 ч −1 и 4,38% для Cu@C-0,12, начальная активность Cu @ A-HCS демонстрирует почти четырехкратное увеличение времени пролета на 8,6 ч -1 сопровождается соответственно резким увеличением содержания C MeOH 17,1% соответственно при тех же условиях. Эти замечательные результаты являются разумными, если учесть, что увеличение площади поверхности и объема пор углеродных оболочек может положительно адсорбировать больше молекул реагентов из основного раствора, значительно ускорить диффузию по каналам и обогатить их в пустом пространстве катализаторы, что приводит к более высокой концентрации реагентов для доступного ограниченного катализа. Катализатор с достаточно долгим сроком службы имеет решающее значение для его применения в промышленности. В качестве катализатора выбран активированный образец Cu @ A-HCS с многообещающей активностью для испытания на долговечность в системе периодического действия, описанной выше. Гетерогенные катализаторы часто страдают от снижения активности из-за обширного выщелачивания активных металлических частиц во время реакций [35]. Не менее важна устойчивость к коалесценции катализатора на основе нанокристаллов [36]. В нашем случае, как показано в Таблице 3, восстановленный катализатор Cu @ A-HCS (отделенный фильтрацией) сохраняет гораздо более высокую каталитическую активность, чем CuCl, даже после семи прогонов (записи 2-8) и среднего выщелачивания Cu, которое составляет активный компонент катализатора составляет около 0,004%, оставаясь почти таким же, как свежий. Между тем, кристаллическая структура и морфология катализаторов практически не изменились после последовательных циклов (дополнительный файл 1:Рисунок S2). По-видимому, наличие пористой углеродной оболочки достаточно для стабилизации активных металлических частиц, предотвращая их агрегацию и выщелачивание; в то же время оболочки достаточно проницаемы, так что каталитические поверхности остаются доступными и выгодными для реагентов и продуктов [12]. Следовательно, катализаторы YSN представляют собой эффективные и некоррозионные каталитические системы, в которых наночастицы Cu в качестве материалов ядра, инкапсулированные в полости HCS, образуют реактивные центры, а пористая углеродная оболочка предотвращает агрегацию и выщелачивание ядра в условиях реакции.
Выводы
Таким образом, мы представили простую стратегию «корабль в бутылке» для изготовления наноструктур желток-углеродная оболочка, состоящая из наночастиц Cu с заданным размером в узких распределениях путем регулирования концентрации солей меди. Как было продемонстрировано, каталитические свойства этой системы типа погремушки при окислительном карбонилировании метанола до ДМК сильно зависят от пористости. Активированный образец с чрезвычайно большой площадью поверхности позволяет создавать высокоэффективные ограниченные нанореакторы для каталитических реакций со значительно более высокой конверсией (17,1%) и TOF (8,6 ч −1 ), длительный срок службы и незначительное выщелачивание в каждом цикле, что, несомненно, обеспечивает чистое производство экологически чистого химического вещества DMC. Более того, метод синтеза, описанный в этой статье, может открыть новые возможности для получения наноструктур из желточной оболочки с различным составом, заключенных в углеродную оболочку.
Наноматериалы
- Нанокупы могут отклонять свет
- Простой синтез гетероструктурированных WS2 / Bi2MoO6 как высокоэффективных фотокатализаторов, управляемых видим…
- Новые нанокомпозиты полистирола с полианилином, легированным лаурилсерной кислотой
- Высокопроизводительное производство качественных нановолокон с использованием модифицированного электрос…
- Видимые световые фотокаталитические характеристики нанокомпозитов ZnO / g-C3N4, легированных азотом
- Изготовление и определение характеристик нового композитного катализатора из углеродного нановолокна Tio2 дл…
- Магнитные поли (N-изопропилакриламид) нанокомпозиты:влияние метода получения на антибактериальные свойства
- Изготовление, характеристика и цитотоксичность сферических конъюгированных наночастиц карбоната кальция, п…
- Изготовление и характеристики высокоэффективного поглощения электромагнитных волн структурированных нано…
- Изготовление и характеристика ZnO Nano-Clips с помощью процесса, опосредованного полиолом