Изготовление и определение характеристик нового композитного катализатора из углеродного нановолокна Tio2 для анодного катализатора для топливных элементов с прямым метанолом с помощью метода электроспиннинга
Аннотация
Платина (Pt) - это обычный катализатор, используемый в топливных элементах с прямым метанолом (DMFC). Однако Pt может привести к отравлению катализатора углеродистыми частицами, что снижает эффективность DMFC. Таким образом, данное исследование сосредоточено на изготовлении нового композита TiO 2 . носитель анодного катализатора из углеродного нановолокна для топливных элементов с прямым метанолом (ДМТЭ) методом электроспиннинга. Расстояние между наконечником и коллектором (DTC) и скорость потока были исследованы как параметры, влияющие на электроформование. Чтобы убедиться, что изготовлен лучший каталитический материал, нановолокно прошло несколько характеристик и электрохимических испытаний, включая FTIR, XRD, FESEM, TEM и циклическую вольтамперометрию. Результаты показывают, что D18, изготовленный с расходом 0,1 млч -1 и DTC 18 см - это ультратонкое нановолокно с наименьшим средним диаметром 136,73 ± 39,56 нм. Он показал наивысшую активность катализатора и значение электрохимической активной поверхности как 274,72 мА · мг -1 . и 226,75м 2 г −1 PtRu , соответственно, по сравнению с другими образцами.
Фон
Топливный элемент с прямым метанолом (DMFC) - одна из будущих систем производства энергии из возобновляемых источников, и она очень безвредна для окружающей среды. Система вырабатывает электроэнергию, используя жидкое топливо (метанол) напрямую, без каких-либо дополнительных устройств или процессов сгорания. Преимуществами DMFC являются их простота, высокая удельная энергия, низкая рабочая температура и легкий запуск с мгновенной дозаправкой [1]. Однако системы DMFC по-прежнему страдают от нескольких ограничений, таких как отравление катализатора и медленная кинетика реакции, что приводит к тому, что система имеет низкие характеристики и выходную мощность [2]. Оба эти ограничения связаны с катализатором и материалом, используемым в этой системе.
Платина (Pt) - обычный катализатор, используемый в DMFC. Однако Pt может привести к отравлению катализатора углеродистыми частицами, что снижает эффективность DMFC. Позже для увеличения скорости реакции вводят платину-рутений (PtRu), но кинетический параметр катализатора по-прежнему остается одной из основных проблем в DMFC. Таким образом, изменение этого биметаллического катализатора начинает применяться в области катализатора DMFC. Один из наиболее привлекательных подходов среди исследователей - введение оксида металла и наноматериалов в качестве побочного компонента катализатора. Диоксид титана (TiO 2 ) представляет собой оксид металла, который привлекает много внимания со стороны разработчиков. TiO 2 обладает различными полезными свойствами, не токсичен, негорюч и обладает высокой устойчивостью к коррозии [1], может повышать электрохимическую и термическую стабильность [3], а также влиять на электронные свойства и бифункциональный механизм композитных катализаторов [4]. Ито и др. [5] разработан PtRu / TiO 2 -встроенное углеродное нановолокно (CNF) (PtRu / TECNF), и Ercelik et al. [6] представили PtRu / C-TiO 2 в качестве электрокатализатора в приложении DMFC, и результат показывает, что производительность этого нового композитного электрокатализатора выше, чем у катализатора PtRu.
Наноматериал - одна из нанотехнологий, которые нашли широкое применение, включая преобразование энергии. В области преобразования энергии существует множество типов наноматериалов, которые представляют собой нановолокна, нанотрубки, нанопроволоки, наностержни и другие. Этот материал становится основным объектом исследования энергетических материалов из-за уменьшения размеров до нанометрового масштаба, что может повлиять на многие элементарные этапы, включая перенос заряда и молекулярную перестройку, а также на свойства поверхности для обеспечения высоких межфазных объемных фракций и повышенной скорости реакции [ 7]. В этом исследовании основное внимание уделяется структурам нановолокон для обоих материалов:TiO 2 . оксид металла и углерод. Это связано с особыми свойствами нановолокон, которые могут обеспечивать высокое соотношение поверхность / объем и удлинение [7], высокую электропроводность, хорошую механическую прочность и однородную дисперсию катализатора, что может повысить электрокаталитическую активность [8].
Нановолокна могут быть получены с помощью нескольких процессов, включая выдувание из расплава, межфазную полимеризацию, электроспиннинг и осаждение полимера, вызванное антирастворителем [9]. В последнее время электроспиннинг стал основным выбором исследователей из-за огромных преимуществ создания ультратонких структур из нановолокон. Электроспиннинг - это уникальный процесс формирования волокон субмикронного диаметра (в диапазоне от нанометров до микрометров) с использованием растворов на основе полимеров или плавления под действием электростатических сил [10]. Электропрядение состоит из трех основных компонентов:источника высокого напряжения (несколько десятков кВ), фильеры (шприц с иглой) и заземленного коллектора (например, пластины или вращающегося коллектора) [11, 12]. Рисунок 1 иллюстрирует общий процесс и установку для процесса электропрядения. Поэтому электроспиннинг популярен благодаря своей простой процедуре, универсальности, высокой производительности, эффективности и более экономичному процессу [7, 13].
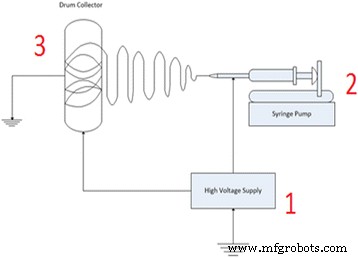
Установка электропрядения для всех основных компонентов
Этот процесс имеет несколько параметров, которые можно настроить для получения оптимальных структур нановолокон, будь то диаметр или морфология поверхности, а влияющие параметры различны для каждого материала. Параметры можно разделить на три основные категории:параметры раствора, окружающей среды и процесса. В этом исследовании основное внимание уделяется параметрам процесса, а скорость потока раствора и расстояние между кончиком иглы и коллектором (DTC) были выбраны в качестве основных влияющих параметров для получения наименьшего диаметра. Это связано с небольшим объемом исследований, посвященных этим параметрам [14], хотя они рассматривались как основные переменные для получения ультратонких нановолокон [15,16,17,18].
Таким образом, в данном исследовании представлен композит TiO 2 углеродное нановолокно в качестве носителя катализатора на анодном электроде. Ожидается, что эта комбинация композита увеличит электрокаталитическую активность и снизит отравление катализатора, чтобы повысить общие характеристики DMFC. Основными целями этого исследования являются изготовление нановолокон наименьшего возможного диаметра для увеличения площади поверхности и обеспечения более активного пятна для каталитической реакции и улучшения характеристик DMFC. Производство нановолокон включает несколько этапов, включая процессы золь-гель, электроспиннинга, стабилизации и карбонизации. Для получения нановолокон наименьшего диаметра параметры электропрядения, такие как скорость потока и DTC, взяты в качестве основных переменных в данном исследовании. Подготовленные нановолокна характеризуются инфракрасной спектроскопией с преобразованием Фурье (FTIR), дифракцией рентгеновских лучей (XRD) и сканирующей электронной микроскопией (FESEM). Все носители катализаторов с разными параметрами электропрядения нанесены на PtRu (PtRu / TiO 2 -CNF) и оценивается с помощью анализа электрохимической активной поверхности (ECSA) и циклической вольтамперометрии (CV) для оценки производительности и определения их потенциала в качестве носителей катализатора в DMFC. Результаты экспериментов показывают влияние параметров электропрядения на диаметр нановолокна, а также их потенциал в приложениях DMFC.
Методы / экспериментальные
Материалы
Были получены поли (винилацетат) (PVAc, Mw =500 000), диметилформамид (DMF, 99,8%), изопропоксид титана (TiPP, содержание 97%), уксусная кислота (99,7%) и прекурсор Ru (содержание 45–55%). от Sigma-Aldrich Co., Ltd., а предшественник Pt (содержание 40%) и этанол (99,8%) были получены от Merck, Германия и R&M Chemical Reagents, соответственно. Все химические вещества использовались без дополнительной очистки. Основное устройство, электропрядильная машина, имеет марку Nfiber N1000, Progene Link Sdn. Bhd., И ультразвуковая клеточная дробилка INS-650Y от INS Equipments Trading Co., Ltd., Китай.
Подготовка TiO 2 -CNF нановолокна
Золь-гель метод начинается с приготовления раствора полимера, в котором ПВС (11,5 мас.%) В качестве источника углерода растворяли в растворителе, ДМФ. Раствор полимера перемешивали при 60 ° C в течение 1 ч, а затем перемешивали в течение ночи при комнатной температуре. TiO 2 предшественник, TiPP и раствор полимера смешивали в соотношении 1:1, и к раствору полимера добавляли небольшое количество уксусной кислоты и этанола. Смесь гомогенизировали с помощью ультразвуковой дробилки клеток в течение 60 с. Затем раствор переносили в шприц для инъекций в установке электропрядения из нановолокна. Приложенное напряжение составляло 16 кВ, а расход и DTC регулировались в диапазоне 0,1–0,9 мл / ч -1 . и 14–18 см. Скорость потока была установлена на 0,1, 0,5 , и 0,9 млч -1 , обозначенные F0.1, F0.5 и F0.9 соответственно. Образцы со значениями DTC 14, 16 и 18 см обозначены D14, D16 и D18 соответственно. Изготовленное нановолокно выдерживали в течение 5 часов при комнатной температуре перед стабилизацией в течение 8 часов при 130 ° C. Стабилизированное нановолокно карбонизировали при 600 ° C в течение 2 часов в атмосфере азота с использованием трубчатой печи, а затем измельчали ступкой и пестиком в течение 5 минут перед дальнейшим использованием в этом исследовании. Массовая нагрузка для всех образцов одинакова и составляет 6,67 мг / с -1 . .
Отложение катализатора
TiO 2 Нановолокна -CNF добавляли в смесь изопропилового спирта (IPA) и деионизированной воды (деионизированная вода) и обрабатывали ультразвуком в ультразвуковой ванне в течение 20 мин. Предшественник платино-рутениевого катализатора (20 мас.% При соотношении 1:1) смешивали с раствором и перемешивали в течение 20 мин. Затем pH смешанного раствора доводили раствором NaOH до pH 8. Температуру повышали до 80 ° C и добавляли 25 мл 0,2 M NaBH 4 добавляли по каплям в смешанный раствор. Раствор перемешивали еще 1 час. Затем смесь охлаждали, фильтровали и многократно промывали. Порошок катализатора сушили при 120 ° C в течение 3 часов и, наконец, измельчали с помощью ступки и пестика, чтобы получить мелкодисперсный порошок катализатора, который был готов к использованию в эксплуатационных испытаниях.
Характеристика катализатора
Химическое соединение в носителе катализатора идентифицировали с помощью инфракрасной спектроскопии с преобразованием Фурье (FTIR, PerkinElmer), а для анализа структуры и кристаллической структуры образцов использовали дифракцию рентгеновских лучей (XRD, D8 Advance / Bruker AXS, Германия). Морфологию и распределение образцов по размерам анализировали с помощью автоэмиссионной сканирующей электронной микроскопии (FESEM, SUPRA 55VP). Просвечивающая электронная микроскопия (ТЕМ, Tecnai G2 F20 X-Twin) использовалась для наблюдения за подробной структурой и распределением элементов нановолокон.
Оценка электрохимических измерений
Характеристики были измерены для всех катализаторов, изготовленных с разными параметрами. Катализатор PtRu был нанесен на TiO 2 -CNF-носитель катализатора для оценки электрохимическими измерениями. Эти измерения были получены с использованием системы трехэлектродных ячеек, в которой используется циклическая вольтамперометрия (CV) для изучения активности катализатора в реакции окисления метанола (MOR) с использованием электрохимической рабочей станции Autolab. Система трехэлектродных ячеек работала при комнатной температуре и включала в себя Pt, серебро / хлорид серебра (Ag / AgCl) и стеклоуглеродный электрод (GCE, диаметр 3 мм) в качестве противодействующего, контрольного и рабочего электрода. Перед началом измерения GCE был очищен глиноземом и полировальной бумагой, несколько раз начертил округлый узор, напоминающий число «восемь». Затем GCE промывали деионизированной водой и обрабатывали ультразвуком в течение 30 с перед использованием. Каталитические чернила для GCE были приготовлены диспергированием 15 мг катализатора в смеси 400 мкл деионизированной воды, 400 мкл IPA и 125 мкл раствора нафиона (5 мас.%) В течение 30 мин. Затем 2,5 мкл каталитических чернил наносили на GCE с помощью микропипетки и сушили в течение 1 часа при комнатной температуре, а затем нагревали при 80 ° C в течение еще 30 минут. Электролит представлял собой раствор 0,5 М H 2 . SO 4 в 2 М метаноле, и через него в течение 20 минут барботировали газообразный азот для удаления кислорода. Измерение CV проводилось в диапазоне потенциалов - 0,1–1,1 В относительно Ag / AgCl при скорости сканирования 50 мВ / с -1 .
Результаты и обсуждение
Структурная характеристика
Влияние скорости потока
ИК-Фурье спектроскопия была выполнена на TiO 2 -Образцы CNF для определения присутствующих химических соединений. ИК-спектры образцов, полученных при различных расходах, показаны на рис. 2. Спектры выявили сигналы химической связи, характерные для TiO 2 и углерод. Средний и широкий пики на 3200–3600 см −1 представляют собой функциональные группы O-H, в то время как резкая и сильная полоса поглощения C =O располагалась в области 1550–1850 см −1 [19]. Пики алканов (группы C-H) слабые и широкие и расположены в области 1300–1450 см −1 . . Однако группы C-C предположительно появляются при очень низких волновых числах, ниже 500 см −1 . [19] и не присутствуют в спектрах из-за небольшого диапазона волновых чисел (4000 см −1 <Волновое число> 50 см −1 ) производят по спектру. Средние и резкие полосы в области 650–900 см −1 принадлежат к группам Ti-O, как предполагают Ding et al. [20]. В ИК-спектрах присутствуют все функциональные группы в TiO 2 -Образцы CNF. Все образцы имеют одинаковые волновые числа и пики, что указывает на то, что скорость потока раствора полимера во время электропрядения не влияет на химические соединения в образце.
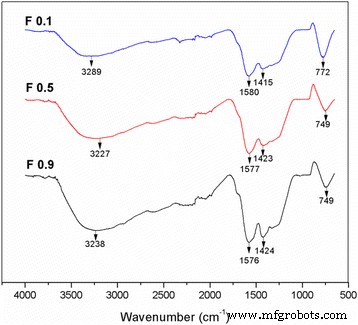
ИК-спектры TiO 2 -Образец CNF с различным параметром расхода в диапазоне от 650 до 4000 см −1 волновое число
TiO 2 -Образцы УНФ, изготовленные при расходах 0,1, 0,5 , и 0,9 млч -1 обозначаются F0.1, F0.5 и F0.9 соответственно. На рисунке 3 показаны дифрактограммы TiO 2 . -CNF-носители катализатора, изготовленные с различными скоростями потока. На рис. 3а показан отдельный образец носителя катализатора, представляющий собой образец F0.1, для просмотра крупным планом рентгенограммы со всем материалом пика в TiO 2 . -CNF, в то время как на рис. 3b показан весь рассматриваемый образец расхода. Существование TiO 2 и углерод в образце. TiO 2 состоит из двух структур, анатаза и рутила, потому что температура карбонизации преобразует небольшое количество анатаза TiO 2 в рутиловый TiO 2 . Пики дифракции для анатаза TiO 2 равны 25 ° (101), 38 ° (112), 48 ° (200), 53,9 ° (105), 62 ° (213) и 68 ° (116), а для рутила TiO 2 равны 27 ° (110), 36 ° (101), 41 ° (111) и 54 ° (211). Источник углерода обозначен несколькими дифракционными пиками, в том числе при 30 ° (110) и 55 ° (211). Анатаз и рутил TiO 2 образовывал тетрагональную структуру, тогда как углерод имел гранецентрированную кубическую кристаллографическую структуру.
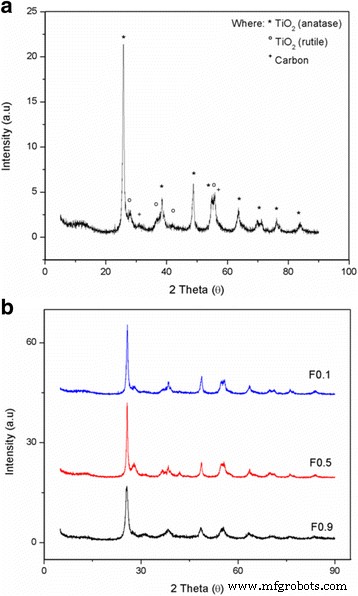
Рентгенограммы a индивидуальный TiO 2 -CNF образец и b образец с разным расходом
Было обнаружено, что скорость потока в методе электропрядения влияет на диаметр нановолокна, который был рассчитан с использованием анализа FESEM. Изображение FESEM представлено на рис. 4, тогда как результаты распределения по размерам и диаметру показаны на рис. 5 и в таблице 1. Изображение подтверждает, что структура нановолокон сформировалась при всех исследованных расходах. Нановолокна F0.1 показали гладкую морфологию из-за более низкой скорости потока, что дает достаточно времени для испарения растворителя, помогая создать гладкую структуру. Средний диаметр нановолокна по результатам 100 измерений составляет 161,18 ± 26,08 нм, что является наименьшим диаметром среди образцов, полученных при различных скоростях потока. Однако изображение F0.5, полученное методом FESEM, показывает образование плоских лент на нановолокнах из-за отсутствия испарения из сердцевины, т. Е. Растворитель захватывается сердцевиной и диффундирует в окружающую атмосферу, вызывая структуру плоских лент [ 21]. F0.9 показывает больше шероховатых нановолокон с неоднородными диаметрами и несколько бусинок, сформированных по морфологии нановолокон. Это происходит, когда скорость потока намного превышает оптимальное значение, что сокращает время сушки до того, как волокно достигнет коллектора. Средние диаметры нановолокон F0,5 и F0,9 были выше, чем у F0,1, которые составили 220,28 ± 38,01 и 286,33 ± 50,83 нм соответственно. Изображение FESEM показывает, что диаметр нановолокон увеличивается с увеличением скорости потока во время электропрядения. F0.1 с расходом 0,1 млч -1 , был использован для дальнейшего анализа влияния DTC на диаметр нановолокна.
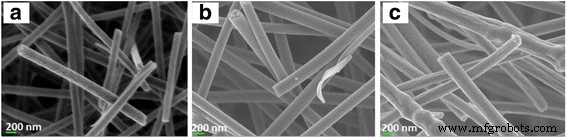
FESEM изображение a TiO 2 -CNF (F0.1), b TiO 2 -CNF (F0.5) и c TiO 2 -CNF (F0.9) при увеличении × 30 000
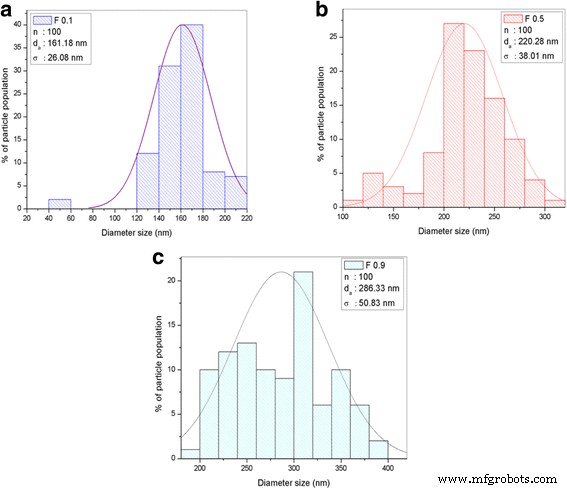
Данные гистограммы распределения диаметров по размерам с параметром n, d a , а σ. а TiO 2 -CNF (F0.1). б TiO 2 -CNF (F0.5). c TiO 2 -CNF (F0.9)
Влияние расстояния между наконечником и коллектором
Синтезированный TiO 2 Носители катализатора -CNF были проанализированы с помощью FTIR для оценки химической связи в образцах, и ИК-спектры образцов проиллюстрированы на фиг. 6. ИК-спектры показывают три образца с различными параметрами DTC после процесса карбонизации. Все синтезированные образцы демонстрируют наличие связи O-Ti-O и карбонатных ионов, при этом пики и волновые числа в спектрах находятся в том же диапазоне, что и в образцах F0.1, F0.5 и F0.9 в предыдущий раздел. Волновые числа были достаточно близки, чтобы указать на схожесть образцов, включая образцы, полученные при разных скоростях потока на рис. 2. Однако образец D14 показывает наличие нового пика около 2300–2400 см -1 , которые указывают на валентные колебания N-H. Этот пик можно классифицировать как пик солей третичного амина, где связь N-H является слабой и не имеет практического значения, которым можно пренебречь [19]. Наличие этой связи может быть связано с неполным удалением соединения растворителя в процессе карбонизации. Это наблюдение показывает, что параметры электропрядения, такие как скорость потока и DTC, не влияют на химическое связывание в образцах.
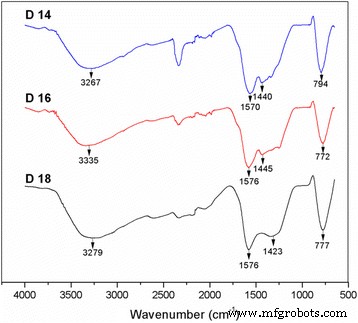
ИК-спектр TiO 2 -Образец CNF с другим параметром DTC в диапазоне от 650 до 4000 см −1 волновое число
Кристалличность TiO 2 Носители катализатора -CNF были проанализированы. Диаграммы XRD показаны на рис. 7a для отдельного образца и на рис. 7b для DTC. Отдельный образец на рис. 7a показывает крупный план XRD для DTC 18, чтобы увидеть пик существования для всего задействованного материала. Материалы, входящие в состав носителя катализатора, TiO 2 и углерод, как показано, присутствуют в каждом образце. Пики дифракции исследовали в диапазоне 2θ от 5 ° до 90 °, а пики при 31 ° (110) и 55 ° (211) указывают на то, что углерод с кристаллографической структурой FCC присутствует в носителе катализатора. Острый дифракционный пик при 25 ° (101) был приписан TiO 2 в форме анатаза, и есть несколько других пиков для анатаза TiO 2 , в том числе на 38 ° (004), 48 ° (200), 53 ° (105), 55 ° (211), 63 ° (204) и 69 ° (116). Остальные четыре дифракционных пика при 27 ° (110), 36 ° (101), 41 ° (111) и 54 ° (211) принадлежат рутиловому TiO 2 . И анатаз, и рутил TiO 2 имеют тетрагональную кристаллографическую структуру.
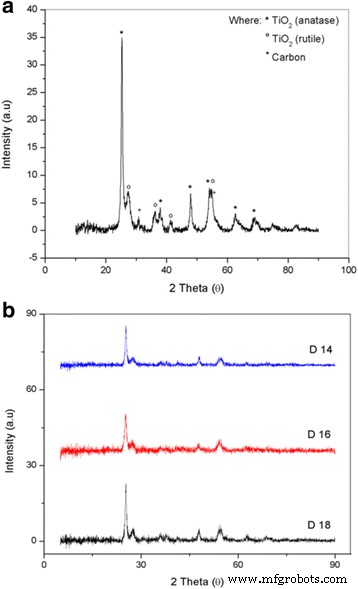
Рентгенограммы a индивидуальный TiO 2 -CNF образец и b другой образец кода неисправности
TiO 2 Нановолокна -CNF были изготовлены методом электроспиннинга с различными значениями DTC, обозначенными D14, D16 и D18. DTC варьировался до 14, 16 и 18 см. Диаметр нановолокна был рассчитан с использованием анализа FESEM. На рисунке 8 показаны изображения FESEM образцов с различными значениями DTC при увеличении × 30 000. Влияние изменения DTC на диаметр нановолокон было оценено с использованием распределения частиц по размерам (диаметра), как показано на фиг.9, и значения приведены в таблице 2. Распределение диаметров включает несколько параметров, n (наночастица население), d a (средний арифметический размер частиц) и σ (стандартное отклонение) [22].
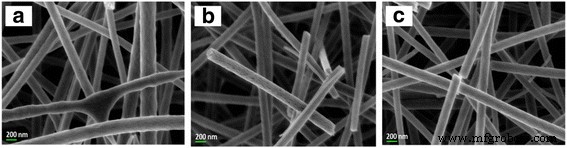
FESEM изображение a TiO 2 -CNF (D14), b TiO 2 -CNF (D16) и c TiO 2 -CNF (D18) при увеличении × 30 000
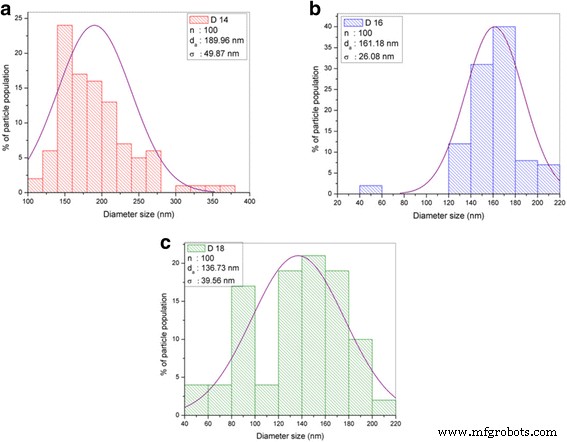
Данные гистограммы распределения диаметров по размерам с параметром n, d a , а σ. а TiO 2 -CNF (D14). б TiO 2 -CNF (D16). c TiO 2 -CNF (D18)
Наименьший средний диаметр составил 136,73 ± 39,56 нм (90–170 нм), принадлежащий D18, за ним следовали D16 и D14 с диаметрами 161,18 ± 26,08 и 189,96 ± 49,87 нм, соответственно. Чем больше расстояние между наконечником и коллектором, тем меньше диаметр нановолокна. Такое поведение обусловлено временем осаждения и интервалом нестабильности взбивания во время процесса электропрядения. Чем больше расстояние, тем больше время осаждения, и в течение этого периода возникает явление нестабильности взбивания, также известное как механизм утонения и расщепления. Это явление возникает из-за взаимодействия заряженных ионов с электрическим полем [17]. Когда электрическая сила, приложенная к наконечнику сопла, достигает критического значения, сильно заряженная плотность и вязкоупругая сила разделяют струи на более мелкие струи, создавая путь изгиба, намотки и спирали к коллектору. Когда DTC длиннее, многократно происходит разделение струи, в результате чего получаются ультратонкие волокна и волокна меньшего диаметра. Следовательно, наименьший диаметр принадлежит образцу D18 с расходом 0,1 мл / ч −1 . и код неисправности 18:
Диаметр изготавливаемых нановолокон, TiO 2 -CNF, сравнивается с предыдущим исследованием диаметра нановолокон для TiO 2 . нановолокон на основе, и это сравнение показано в таблице 3. Результаты показывают, что TiO 2 -CNF имеет наименьший диаметр нановолокна - 136,73 ± 39,56 нм. Это связано с оптимальным параметром, используемым при методе электропрядения; который имеет низкий расход и высокое значение кода неисправности. Таким образом, при меньшем расходе и более высоком значении DTC получается меньший диаметр нановолокна. Это показывает, что параметры электроспиннинга в наибольшей степени влияют на диаметр нановолокна. Несмотря на то, что более продолжительный код неисправности и меньшая скорость потока предпочтительны, существуют оптимальные значения для этих параметров, поскольку эти параметры могут привести к потере веса. Это происходит из-за чрезмерного испарения, при котором нановолокно формируется до того, как достигнет коллектора, что позволяет нановолокну свободно перемещаться в нежелательные области.
Проба D18 с расходом 0,1 млч -1 и DTC, равный 18, был выбран для анализа ПЭМ, чтобы изучить морфологию и получить размер диаметра. ПЭМ-изображение и элементарное отображение TiO 2 Носитель катализатора -CNF показан на фиг.10. Изображение ПЭМ показывает, что TiO 2 -CNF дает гладкое и шелковистое нановолокно диаметром 135,38 нм. Диаметр находится в том же диапазоне (90–170 нм), что и полученный с помощью анализа FESEM. Картирование используется для изучения распределения TiO 2 и углерод на нановолокне. Результаты показывают, что TiO 2 и углерод, образованный равномерно в структуре нановолокон, благодаря однородному распределению раствора полимера и TiO 2 прекурсор в золь-гель методе. Это отображение также показывает расположение материалов, в которых TiO 2 и углерод расположены по всей поверхности нановолокна, что способствует созданию активных реакционных зон во время катализа. Ожидается, что другие образцы нановолокон будут иметь такое же равномерное распределение TiO 2 и углерод. Размер частиц TiO 2 и углерод в образцах нановолокон и их влияние на MOR обсуждается в следующем разделе.
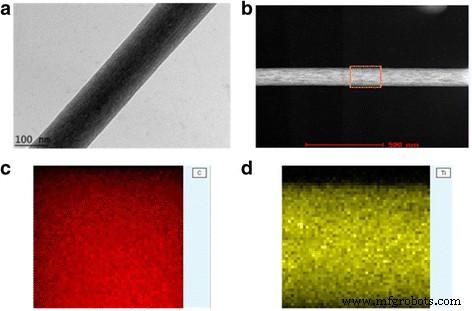
TiO 2 -CNF-носитель катализатора a Изображение ПЭМ (масштаб 100 нм), b Изображение ПЭМ для TiO 2 и отображение нановолокон C, c отображение для нановолокна C и d отображение для TiO 2 нановолокно
Электрохимическая характеристика реакции окисления метанола
Электрохимическая характеристика включает три основных этапа:определение электрохимической активности, электрокаталитических характеристик и долговременной стабильности и долговечности. Электрохимическая активность и электрокаталитические характеристики были проанализированы методом CV с использованием трехэлектродной системы для получения качественной и количественной информации об участвующей реакции [23]. На рис. 11а, б показано ПЭМ-изображение катализатора PtRu, нанесенного на поверхность TiO 2 F0.1 и D18. -CNF поддерживает соответственно. Катализатор PtRu был равномерно распределен на поверхности нановолокон как в F0.1, так и в D18. На рисунке 11c показана рентгенограмма D18 PtRu / TiO 2 . -CNF, тогда как в таблице 4 приведены данные для диаметра нановолокон, полученные с помощью FESEM, и размер кристаллитов частиц в образцах, полученные с помощью XRD. Таблица 4 показывает, что образцы серии F (F0.1, F0.5 и F0.9) с добавленным катализатором имеют TiO 2 (анатаз) размер кристаллитов приблизительно от 20 до 22 нм. Изменение диаметра нановолокна мало влияет на размер кристаллитов TiO 2 . , в то время как размер кристаллитов углерода изменяется по мере увеличения диаметра нановолокна с 15,9 нм в F0,1 до 25,8 нм в F0,9. Размер кристаллитов Pt также имеет тенденцию к увеличению с увеличением размера кристаллитов углерода. Размер кристаллитов Pt, нанесенного на F0.1, F0.5 и F0.9, составляет 5,67, 8,04 и 9,75 нм соответственно. Изменения размера кристаллитов Pt обусловлены поверхностными свойствами нановолокна. В таблице 4 также показан размер кристаллитов PtRu, нанесенного на образцы серии D. Диаметр нановолокна уменьшается от D14 до D16 до D18. В отличие от образцов серии F размер кристаллитов TiO 2 (анатаз) в образцах серии D уменьшается с уменьшением диаметра нановолокна. TiO 2 размер кристаллитов составляет 23,40, 21,50 и 18,60 нм для D14, D16 и D18 соответственно. Размер кристаллитов углерода и Pt также уменьшается с уменьшением диаметра нановолокна. Размер кристаллитов углерода уменьшается с 17,3 нм в D14 до 14,4 нм в D18, в то время как размер кристаллитов Pt, нанесенных на D14, D16 и D18, составляет 5,44, 5,67 и 4,64 нм соответственно. Исходя из этих данных, изменение размеров кристаллитов TiO 2 и углерод в нановолокне приводят к изменениям поверхностных свойств нановолокна, что приводит к изменению размера кристаллитов частиц Pt, осажденных на поверхности нановолокна.
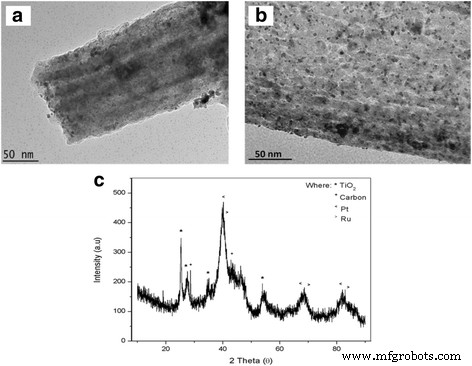
Изображение PtRu, нанесенного на TiO 2 -CNF а ПЭМ изображение PtRu / TiO 2 -CNF в F0.1, b ПЭМ изображение PtRu / TiO 2 -CNF в D18 и c Рентгенограмма PtRu / TiO 2 -CNF D18
На рисунке 12 показаны CV-профили PtRu / TiO 2 . -Электрокатализаторы из CNF с различными носителями катализатора в 0,5 M H 2 SO 4 решение. Кривая CV для F0.1, F0.5 и F0.9 показана на Рис. 12a, а D14, D16 и D18 показаны на Рис. 12b. Адсорбция-десорбция водорода платиной происходит в диапазоне от –0,2 до 0,1 В по сравнению с Ag / AgCl. Массовая нагрузка для всех электрокатализаторов в этом профиле такая же, как 0,57 мг / см −2 . . PtRu / TiO 2 -CNF supported on D18 exhibits a steep current peak for hydrogen adsorption in comparison in the other D series samples, while F0.1 has a steep peak in comparison with the F series samples. The peak indicates that the active surface area on the PtRu/TiO2 -CNF electrocatalyst and the ECSA can be calculated from the equation:ECSA = Q /(Γ .W Pt ). Where, Q is the integral of the hydrogen adsorption area, Γ is the constant for the charge required to reduce the proton monolayer on the Pt (2.1 CmPt −2 ), and W Pt is the mass loading of Pt. Table 5 shows the ECSA of all the catalyst samples in units of m 2 г −1 with mass loadings according to the mass of PtRu. From Table 5, the ECSA for PtRu supported on F0.1, F0.5, and F0.9 is 131.29, 65.05, and 25.03 m 2 г −1 , соответственно. The ECSA value decreases with increasing Pt crystallite size in the catalyst samples. The catalyst supported on D14, D16, and D18 has an ECSA value of 21.48, 131.29, and 226.75 m 2 г −1 , соответственно. As shown previously, the value of the Pt crystallite size in the D series samples decreases from D14 to D18, and thus, the ECSA increases according to Pt crystallite size. Smaller size particles lead to an increase in the active surface area of the catalyst. Overall, the electrospinning parameters clearly show big influence towards the diameter and surface properties (surface morphology) of nanofibers.
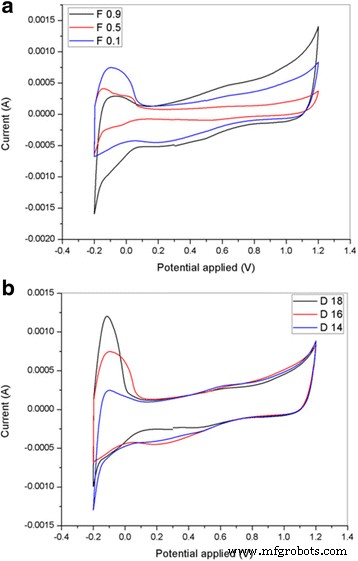
Cyclic voltammetry profiles of the PtRu/TiO2 -CNF with a different flow rate, F0.1, F0.5, F0.9, and b different DTC, D14, D16, and D18, in 0.5 M H2 SO 4 solution at the scan rate of 50 mVs −1
The electrocatalytic performance of PtRu supported on the different F and D series nanofibers is tabulated and plotted in Table 5 and Fig. 13. The CV curve was measured in 2 M methanol and 0.5 M H2 SO 4 solution saturated with N2 gas at room temperature. The mass loading for all the electrocatalyst is the same which is 0.57 mgcm −2 . Figure 13 shows multiple CV curves over a potential range of − 0.1 to 1.1 V vs. Ag/AgCl. Figure 13a shows the CV graphs for PtRu supported on the F series nanofiber samples. As the diameter of the nanofiber decreases from sample F0.9 to F0.1, the current density in MOR increases, and the oxidation peak and onset potential of MOR shift towards positive values. On the other hand, in the D series nanofiber samples, the oxidation peak potential of the catalyst supported on D14, D16, and D18 is 0.754, 0.771, and 0.732 V (vs. Ag/AgCl), respectively. There is no pattern in the oxidation peak potential in the D series samples, and the onset potential is almost the same for each sample, at 0.36 V vs. Ag/AgCl. However, the peak current density at the oxidation peak potential of MOR increases in accordance to the catalyst support on D14, D16, and D18. The peak current density for D14, D16, and D18 is 201.45, 249.58, and 274.72 mAmg −1 PtRu , соответственно. It can be clearly seen that the increase in the current density matches the patterns in the diameter, from FESEM analysis, and ECSA value. This shows that a smaller diameter size produces high surface area and increases the number of active sites on the electrocatalyst surface. The higher peak current for the composite electrocatalyst may result from the supporting material (TiO2 -CNF), where changes in the structure and the combination of materials can be very effective in producing positive effects on the metal-support interaction [5, 24].
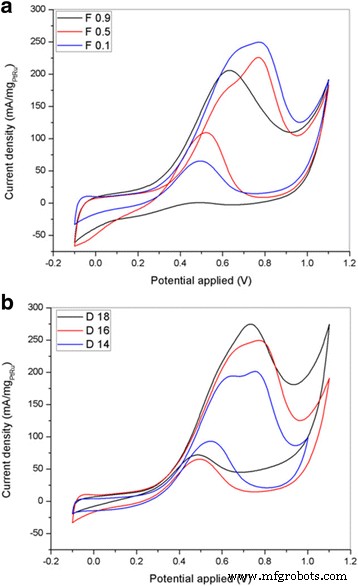
Cyclic voltammograms for PtRu/TiO2 -CNF with different a flow rate and b DTC of the catalyst support in 2 M methanol and 0.5 M H2 SO 4 at the scan rate of 50 mVs −1
The reverse scan in the CV curve shows a small oxidation peak at a potential of approximately 0.49–0.55 V vs. Ag/AgCl. This second oxidation peak appeared due to the incomplete removal of oxidized carbonaceous species in the forward scan [25]. However, the ratio between the forward (If ) and reversed (Ib ) oxidation peak for PtRu/TiO2 -CNF (D18) exceeded 3.8, which means that the electrocatalyst has high tolerance towards carbonaceous species, reducing the potential for catalyst poisoning. This result shows that the combination of metal oxide and carbon nanofibers has a good potential for use in fuel cell applications.
Conclusion
TiO 2 -CNF nanofibers can be fabricated via electrospinning, which is the main technique, and several other methods. The nanofibers are influenced by the flow rate and the DTC, which were examined as electrospinning process parameters, with three different samples for each parameter, denoted F0.1, F0.5, F0.9, D14, D16, and D18. The results showed that the TiO2 -CNF (D18) sample produced the smallest average diameter of 136.73 ± 39.56 nm. TiO 2 -CNF was mixed with PtRu to form the composite catalyst, and its CV performance was examined. The current density of the PtRu/TiO2 -CNF (D18) sample is 1.4 times higher than that of PtRu/TiO2 -CNF (D14), while the ECSA of PtRu/TiO2 -CNF (D18) is 10 times higher than that of the other samples. Thus, the flow rate and DTC highly affect the diameter, morphology, and performance of the nanofibers. The nanofiber performance increased with decreasing nanofiber diameter, which shows the capability of the composite nanofiber catalyst to be an upcoming anode catalyst for DMFCs.
Наноматериалы
- Метод изготовления искусственных молекул получил приз за лучший плакат
- Графен и полимерные композиты для суперконденсаторов:обзор
- Проектирование чистых и композитных углеродных нанотрубок с помощью порозиметрических характеристик
- Повышенная производительность нового анодного катализатора PdAu / VGCNF для электроокисления в глицериновом топ…
- Изготовление, характеристика и цитотоксичность сферических конъюгированных наночастиц карбоната кальция, п…
- Аэрогель / серный композит с активированным углем с полианилиновым покрытием для высокопроизводительных лит…
- Изготовление и характеристика ZnO Nano-Clips с помощью процесса, опосредованного полиолом
- Поддержка новых анодных катализаторов для топливных элементов с прямым метанолом:характеристики и характер…
- Простой метод загрузки наночастиц CeO2 на массивы анодных нанотрубок TiO2
- Катализаторы на основе платины на различных углеродных носителях и проводящих полимерах для применения в то…