Интервью с экспертом:главный инженер Oerlikon в AM, Мэтью Донован, о 3D-печати для аэрокосмической промышленности
Oerlikon, глобальная технологическая и инженерная группа, обслуживает некоторые из наиболее важных с точки зрения безопасности отраслей, включая аэрокосмическую и оборонную. . Все чаще аддитивное производство становится ключевой частью ее предложений:в начале этого года компания открыла в США центр инноваций и производство передовых компонентов стоимостью 55 миллионов долларов.
В экспертном интервью на этой неделе мы сядем за стол с Мэтью Донованом, главным инженером по аддитивному производству компании Oerlikon, чтобы обсудить, как компания продолжает развивать комплексное производственное предприятие AM и захватывающие тенденции в области AM обратите внимание на стандарты и почему они имеют решающее значение для будущего отрасли.
Не могли бы вы рассказать мне об Oerlikon?
Oerlikon - глобальная компания и лидер в производстве как поверхностных решений, так и искусственных волокон. Компания Oerlikon AM, входящая в сегмент поверхностных решений, предлагает решения для аддитивного производства, от металлических порошков до прототипирования и серийного производства.
Как вы впервые начали заниматься аддитивным производством?
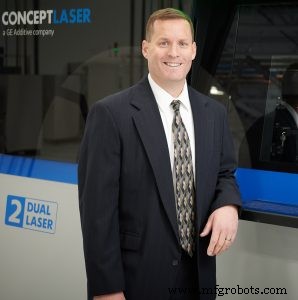
Мой опыт работы в авиакосмической сфере. До прихода в Oerlikon я последние 20 лет работал, в основном, над газотурбинными двигателями, компонентами горячей секции и компонентами секции сгорания.
У меня есть опыт работы с системами подачи топлива, в основном для аэрокосмических газотурбинных двигателей, но также и с промышленными газовыми турбинами и установками для риформинга топливных элементов. Я также работал над различными исследованиями и разработками с НАСА и другими компаниями. Итак, у меня есть опыт работы с высокопрочными, жаропрочными материалами для очень сложных условий.
Я начинал как инженер-технолог, изучая все тонкости производства и сборки деталей и тратя их время в качестве инженера по качеству, проводящего полевые исследования тех же компонентов.
Я начал работать в сфере передового производства в 2006 году. Я начал сталкиваться с сложными геометрическими формами и компонентами, которые мы не могли изготовить при традиционном производстве.
В то время я работал с Morris Technologies над металлическими компонентами, напечатанными на 3D-принтере. Мы начали разработку компонентов для топливных форсунок с использованием аддитивного производства.
За эти годы я разработал несколько компонентов, используя аддитивное производство. Я работал в United Technologies, помогая всему предприятию в разработке и внедрении технологий AM, в основном уделяя особое внимание аппаратному обеспечению для летной сертификации.
Когда мы работали над внедрением этих компонентов, одним из основных пробелов, которые я обнаружил, было полное отсутствие стандартов на то, как производить детали и как их сертифицировать.
Большая часть затрат, связанных с аэрокосмической отраслью, связана не только с самими компонентами, но и с сертификацией. Мы должны обеспечить полную отслеживаемость каждого компонента, который мы производим. Разработка стандартов того, как мы это делаем, и внедрение этого для аддитивов было довольно сложной задачей.
Я начал работать над стандартами AM с ASTM F42 примерно в 2009 году. Я помогал разработать некоторые стандарты, а затем работал в нескольких комитетах. Я был соавтором руководства по проектированию лазерной наплавки металлического порошка, ISO ASTM 52911, ISO / TC 261 и ASTM F42.
Благодаря этой работе с United Technologies, работая со множеством талантливых людей и имея доступ к ряду отличных ресурсов, мы смогли придумывать различные инновации и разработать действительно передовые продукты для AM. слой металлического порошка.
Какова ваша роль в Oerlikon?
Я начал работать в Oerlikon в 2017 году и сейчас занимаю должность главного инженера AM. Моя роль была в значительной степени сосредоточена на внедрении и развитии готовых к производству технологий металла AM.
Мы начинали как новое подразделение Surface Solutions Group. Мы построили новый завод в Хантерсвилле, Северная Каролина, в который переехали чуть меньше года назад.
Это предприятие площадью 120 000 квадратных футов, на котором в настоящее время эксплуатируется 18 систем металлического порошкового покрытия. На месте у нас есть возможности горячего изостатического прессования (горячего изостатического прессования) и вакуумной печи, а также пост-обработка, обработка порошка и контроль.
Цель заключалась в том, чтобы создать на этом предприятии настоящий непрерывный производственный процесс AM с контролем каждого аспекта цепочки поставок, чтобы мы могли обеспечить отслеживаемость для наших клиентов.
Моя роль в этом заключалась в основном в сертификации машин. Я тесно сотрудничаю с производителями оборудования для установки и аттестации наших машин, а затем получаю сертификаты на их возможности и совместимость с компонентами на разных машинах.
После этого мы сможем понять возможности станка, допуски и точность отдельного станка, чтобы обеспечить геометрический допуск компонента AM и различия между нашими станками, а затем настроить их, чтобы мы могли доставить один и тот же продукт на нескольких машинах.
Стандартизация была действительно важной темой для разговоров, особенно в таких отраслях, как аэрокосмическая. Как все развивались за то время, пока вы работали в отрасли, и каков текущий статус стандартизации AM?
Произошло несколько очень хороших событий.
Нам нужны стандарты, особенно в аэрокосмической отрасли, но также и в других критически важных для безопасности областях, таких как медицина, атомная энергия и энергетика. Ключевым моментом в стандартах является то, что они позволяют всем говорить на одном языке и понимать, на что способен продукт.
Из-за отсутствия стандартов все эффективно строили детали и выполняли свою работу часто очень похожими способами, но не одинаково. Они говорили на разных языках. Очень часто люди используют разные термины для обозначения одного и того же процесса или ссылаются на один и тот же термин, имея в виду радикально разные процессы.
Разработка стандартов позволяет вам говорить на одном языке со всеми и понимать, что вы имеете в виду, говоря, скажем, о повышении квалификации, сырье или уровне квалификации машины.
В аэрокосмической отрасли, если у вас нет стандарта, по которому вы можете сертифицировать деталь, или, как правило, нескольких стандартов для определения детали, которую вы производите, ее механических свойств, характеристик и допусков, а также иметь возможность отследить его до исходной партии, из которой он был получен, вплоть до химического состава элементов, которые вошли в него, тогда вы не сможете поместить его на аэрокосмическую платформу.
Мы можем создавать невероятно сложные геометрические формы и изготавливать детали с помощью AM, которые по-другому физически невозможны. Мы можем сэкономить массу, время, материалы и расходы, производя детали с помощью AM.
Свобода в дизайне и производстве, которую предоставляет нам AM, очевидна. Но недостаток в том, что это здорово, если вы можете сыграть свою роль, но если вы не можете доказать, что это хорошая роль, это никому не принесет никакой пользы.
Стандарты - это то, что позволяет нам производить и продавать детали и использовать их в производстве для авиакосмической промышленности.
Таким образом, аэрокосмические стандарты являются одним из ключевых элементов головоломки, прежде чем вы сможете создавать детали.
В течение долгого времени в этой области очень много работали различные организации, занимающиеся разработкой. Я работаю волонтером над стандартами ASTM около 10 лет и вижу преимущества того, что мы делаем.
Как я уже упоминал, я внес свой вклад в разработку оригинального титанового стандарта для плавки в порошковой подложке. У меня (и у нескольких других людей) ушло чуть больше двух лет на то, чтобы утвердить этот первый. Впоследствии мы смогли обработать дополнительные примерно за половину этого времени.
Сейчас ситуация действительно начинает ускоряться. ASTM недавно открыла свой Центр передового опыта в Оберне, штат Алабама, совместно с Обернским университетом.
За этим стояло намерение использовать целевое финансирование исследований и разработок и усилия партнеров по сотрудничеству для быстрого достижения большего количества стандартов. Отрасль и правительственные органы активно сотрудничают с целью выявления пробелов и стандартов, которые мы воспринимаем в отрасли, и это то, что нам нужно для продвижения вперед.
Возможно, вы слышали о дорожной карте ANSI. Это очень хороший документ, в который некоторые из нас, работающих в отрасли, внесли свой вклад, чтобы определить наши ключевые пробелы, которые нам необходимо заполнить, чтобы добиться реального производства для аддитивного производства.
Я считаю, что в последней версии этой дорожной карты был выявлен 91 пробел, в основном в областях стандартов, и некоторые из них имеют очень высокий приоритет. Центр передового опыта ASTM - это один из инструментов, который используется для проведения исследований и разработок, чтобы закрыть эти пробелы в стандартах.
В другой области SAE International разработала Спецификацию аэрокосмических материалов (AMS). Первыми для аддитивного наплавления порошкового покрытия были AMS 7000, 7001, 7002 и 7003 для никелевого сплава 625, которые были недавно выпущены.
Это отличные работы, которые принесут много результатов. Многие из нас уже используют эти стандарты для разработки производственных деталей.
С вашим опытом внедрения AM, каковы были некоторые проблемы при внутренней интеграции технологии и как вы справлялись с этим процессом?
Oerlikon AM стремится предоставить решения AM, которые отвечают требованиям самых требовательных отраслей, таких как аэрокосмическая и медицинская, среди прочих.
На всех наших предприятиях у нас есть правильные системы качества, такие как AS9100 для авиакосмической промышленности и ISO 13485 для медицины. Но что касается интеграции всех систем, необходимых для достижения этой цели, это было проблемой, хотя есть некоторые решения, которые предоставляют кусочки головоломки.
Я бы сказал, что не существует единого решения, охватывающего все аспекты того, что нам нужно, от начала до конца. Но есть много хороших инструментов, которые охватывают части всей этой непрерывной цепочки поставок.
Итак, одна из наших задач - найти решения, которые охватывают различные аспекты нашей цепочки поставок, принести добавьте те, которые охватывают необходимые нам аспекты, и интегрируйте их.
Например, некоторые решения очень хорошо справляются с финансами и инвентаризацией, но не очень подходят для производственных рабочих процессов. Другие хорошо справляются с производственными рабочими процессами и производственным планированием, но не справляются, скажем, с оценкой времени сборки, проблемами анализа материалов или проблемами геометрических компонентов, таких как чертежи и 3D-модели.
Так что их много. различных аспектов, и наша задача состоит в том, чтобы объединить все эти компоненты, чтобы получить единое комплексное решение. В настоящее время это довольно ручной процесс, но мы работаем над тем, чтобы сделать его более автоматизированным по мере продвижения вперед.
Можете ли вы поделиться какими-либо историями успеха о том, как вы использовали AM в производственной среде?
Хотя я не могу конкретно обращаться к этим клиентам без их разрешения, у нас есть несколько компонентов, которые активно находятся в разработке. Некоторые из них, о которых я могу подумать, - это компоненты, связанные с аэрокосмической и оборонной отраслями.
Итак, один из них - это компонент полета, который является частью системы миссий на военном вертолете. Мы производим этот компонент уже два года и на сегодняшний день успешно поставили более 200 единиц.
Мы также производим еще один компонент, который используется для датчика грунта, где у вас есть интегрированная система из 80 различных отдельных компонентов в одну монолитную деталь. Этот тоже производился почти два года.
У нас есть ряд других производственных компонентов, которые мы производим - для нефтегазовых и подводных разведочных зон, которые находятся в активном производстве для подводной робототехники - для другого нашего клиента, которому мы производим детали для, которые активно используются как в нефтегазовой, буровой и разведочной, так и в подводной робототехнике.
Каким вы видите развитие аддитивного производства в следующие пять лет как с точки зрения технологии, так и с точки зрения отрасли в целом?
<цитата>
В течение следующих пяти лет я вижу развитие технологий с появлением большего количества систем с несколькими лазерами, которые позволят производить детали быстрее, тем самым снижая стоимость компонентов. Это будет способствовать дальнейшему внедрению частей AM.
Стоимость деталей является ключевым фактором, а время лазера - ваш главный фактор, влияющий на стоимость компонента AM. Таким образом, если вы сможете втиснуть в деталь больше лазеров и сертифицировать компоненты, используя эти многолазерные системы, вы сможете изготавливать такую же деталь быстрее и, следовательно, дешевле.
Другая эволюция заключается в том, что мы будем иметь более совершенные системы мониторинга производственных процессов. В настоящее время существует несколько различных систем от разных производителей, но у меня сложилось впечатление, что, хотя многие из них являются хорошими системами, они еще не достигли того уровня возможностей, который потребуются пользователям, таким как я, для их реализации. с истинной производительностью.
Я надеюсь, что скоро у нас будет настоящий внутрипроцессный мониторинг, чтобы мы могли отслеживать, что происходит на машине во время процесса, и иметь возможность выявлять проблемы с компонентом, прежде чем он покинет машины.
Идеальным сценарием было бы наличие интеллектуального программного обеспечения, которое могло бы выявлять проблемы и потенциально вносить исправления с технической поддержкой на лету. Конечно, было бы лучше иметь по-настоящему надежные машины, у которых нет проблем и которые работают круглосуточно и без выходных.
Есть ли какие-то тенденции, которые вас волнуют?
Я с энтузиазмом отношусь к различным разработкам, в том числе к системам текущего контроля, как я уже упоминал.
Есть также некоторые новые материалы, которые разрабатываются и запускаются. Мы разрабатываем несколько различных материалов, которые позволяют некоторым нашим клиентам создавать очень революционные компоненты.
Еще меня воодушевляет то, что производители по всему миру стали намного более разнообразными. Вначале большинство машин AM производились в нескольких странах Европы. Теперь есть новые производители и разные страны, которые применяют разные и новаторские подходы к созданию машин.
Они снижают стоимость машин и извлекают уроки из их использования в отрасли, чтобы сделать их более интуитивно понятными для операторов.
По моему опыту первых нескольких лет работы с этими машинами, они очень привередливы и требуют много внимания и «присмотра за детьми». И, честно говоря, большая часть машин была не очень удобна для производства.
Я вижу, что сейчас в машины встроено много удобного для пользователя, поскольку производители машин получают отзывы от своих пользователей.
Что будет дальше с Oerlikon, особенно с предприятием, которое вы помогаете контролировать и управлять?
Наша краткосрочная цель для этого предприятия - установить и сертифицировать все приобретенное оборудование. Итак, в настоящее время у нас есть 18 онлайн-систем со слоем металлического порошка, и мы делаем производственное оборудование для многих из этих систем.
Нашим следующим шагом в этом направлении является завершение свойств материалов для всех наших систем материалов на всех наших машинах и наборов данных для них. Но это очень затратно по времени и дорого.
К счастью, у нас здесь много очень талантливых людей с большим опытом в области материалов, металлургии и инженерии, и я очень горжусь тем, что являюсь членом этой команды.
Другая цель состоит в том, чтобы выдержать все остальное оборудование для создания настоящего непрерывного производственного объекта.
Недавно мы запустили нашу печь HIP и вакуумную печь и работаем над их сертификацией.
Мы также привезли некоторое оборудование с ЧПУ, и у нас также есть значительное количество дополнительных печей и оборудования с ЧПУ для постобработки. Итак, цель состоит в том, чтобы все это оборудование было установлено, сертифицировано и оперативно интегрировано для создания целостной, целостной производственной системы.
Чтобы узнать больше об Oerlikon, посетите: https://www.oerlikon.com/en/
3D печать
- Интервью с экспертом:профессор Нил Хопкинсон, директор по 3D-печати в Xaar
- Интервью с экспертом:Филип Коттон, основатель 3Dfilemarket.com
- Интервью с экспертом:Спенсер Райт из pencerw.com и nTopology
- Интервью с экспертом:доктором Альваро Гоянесом из FabRx
- Интервью с экспертом:генеральный директор Nanoe Гийом де Калан о будущем керамической 3D-печати
- Интервью с экспертом:президент Ultimaker Джон Кавола о будущем 3D-печати
- Как компания Ford Motor внедряет 3D-печать для автомобильной промышленности:экспертное интервью с Гарольдом Сирсо…
- Интервью с экспертом:соучредитель Nano Dimension Саймон Фрид о развитии 3D-печати для электроники
- Интервью с экспертом:Брайан Александер из Solvay о разработке высокоэффективных полимеров для 3D-печати
- Интервью с экспертом:обзор сверхбыстрых промышленных 3D-принтеров SLA от Nexa3D