Интервью с экспертом:изучение технологии дневной полимерной печати Photocentric с управляющим директором Полом Холтом
Photocentric - британский производитель 3D-принтеров и материалов. Компания, основанная в 2002 году, известна своим уникальным и инновационным подходом к 3D-печати, который она называет дневной полимерной печатью.
В отличие от аналогичных технологий на основе смол, таких как стереолитография (SLA) или цифровая обработка света (DLP), технология дневной полимерной печати Photocentric не использует УФ-лазер или проектор для изготовления деталей, напечатанных на 3D-принтере.
Вместо этого его технология использует свет ЖК-экранов для создания 3D-печатных деталей путем отверждения жидкой фотополимерной смолы слой за слоем. Эти смолы Daylight, также производимые Photocentric, затвердевают под воздействием света с ЖК-экранов принтеров.
Примечательно, что в 3D-принтерах Photocentric используются ЖК-экраны мобильных телефонов, телевизоров и планшетов, что делает их более доступными по сравнению с технологиями SLA / DLP, но при этом обеспечивает такое же качество.
Чтобы узнать больше об уникальной технологии Photocentric и примерах ее использования, мы поговорим с Полом Холтом, управляющим директором Photocentric.
Не могли бы вы рассказать мне о Photocentric и своей миссии как компании?
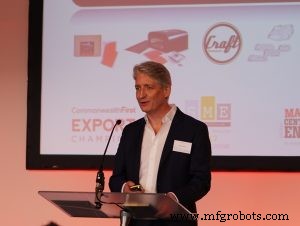
Компания Photocentric изначально была основана для производства запатентованной упаковки фотополимеров. С тех пор наша компания выросла и вышла на самые разные рынки, и мы применяем наши фотополимерные инновации в самых разных отраслях, включая 3D-печать.
Инновационные фотополимерные технологии лежат в основе нашего бизнеса. . В 2005 году мы изобрели концепцию использования ЖК-экранов для 3D-печати. В 2014 году мы разработали наш первый прототип ЖК-дисплея. Мы только что выпустили седьмой принтер с ЖК-дисплеем, и мы планируем выпустить еще больше.
В число пользователей нашей технологии входят дизайнеры ювелирных изделий, стремящиеся ускорить производство или создавать уникальные геометрические изделия с помощью 3D-печати, зубные техники, которым нужен высокопроизводительный и точный принтер для моделей и производителей, ориентированных на конкретного пациента, инженеры. и изобретатели, которые хотят превратить свои дизайнерские концепции в осязаемые прототипы или функциональные части конечного использования.
В конечном итоге наша миссия - изменить мировое производство, а не только 3D-печать. Мы делаем это, делая 3D-печать доступной, крупномасштабной и функциональной, а также предоставляя возможность массового производства на заказ во всем мире.
Как работает ваша технология дневной полимерной печати и что отличает ее от других доступных на рынке машин на основе смол?
В полимерной печати Daylight используется жидкая фотополимерная смола Daylight собственной разработки. Смола отверждается слой за слоем при воздействии на наши 3D-принтеры с ЖК-экраном высокого разрешения.
Изделие создается после того, как каждый слой смолы затвердевает под действием света, излучаемого ЖК-экраном.
Одним из ключевых отличий наших технологий является качество наших машин. Каждый этап наших продуктов проходит тщательную процедуру контроля качества, чтобы гарантировать, что наши клиенты получат наилучшие впечатления от доступных продуктов.
Кроме того, наш подход разработан, чтобы снизить стоимость 3D-печати и расширить применение технологии. Повседневные экраны, такие как экраны телефонов или телевизоров, стали основой наших 3D-принтеров. Эти ЖК-экраны представляют собой надежные и недорогие устройства цифровой обработки изображений.
Это в сочетании с нашей фотополимерной смолой означает, что мы можем предложить доступную упаковку для 3D-печати. Многие компании, занимающиеся 3D-печатью, занимаются разработкой, а затем передают химию на аутсорсинг - мы все делаем сами.
Мы также предлагаем самый крупный на рынке принтер на основе ЖК-экрана с нашей машиной Liquid Crystal Magna. , поэтому мы можем достичь высокого уровня точности в больших масштабах.
Какие отрасли могут извлечь наибольшую пользу из ваших технологий?
Мы можем предоставить решения для 3D-печати в таких отраслях, как стоматология и ювелирное дело, где типичны небольшие и точные приложения, а также решения для отраслей, где требуются крупномасштабные компоненты и прототипы.
В частности, мы чувствуем, что у Photocentric есть огромный потенциал в области стоматологии. Посетив выставку IDS 2019 в этом году, мы увидели огромный спрос на ЖК-печать в этом секторе.
Вот почему огромная часть наших исследований и разработок посвящена производству продуктов для стоматологии, таких как Liquid Crystal Dental - наш оптимизированный стоматологический принтер для кабинетов или лабораторий, выпуск которого запланирован на конец этого года.
С другой стороны, наша технология также подходит для крупных компонентов в автомобильной промышленности и индустрии развлечений. Возможности огромны, особенно с учетом универсальности наших разработок для ЖК-принтеров.
Не могли бы вы рассказать об одном или двух успешных применениях вашей технологии?
Одним из уникальных клиентов является Quimbaya Orfebreria, аргентинский ювелир, который производит специальные изделия для своих клиентов.
Поскольку спрос начал преобладать над предложением, и они столкнулись с ограничениями дизайна, Quimbaya решила отказаться от традиционных методов и внедрить 3D-печать. в их рабочий процесс. Они выбрали наш настольный принтер высокого разрешения LC Precision 1.5.
Используя 3D-печать, они смогли сократить время производства на 80%. Их производство также увеличилось на 400%, и теперь они могут производить более сложные и сложные конструкции для своих клиентов.
Еще одним примером является Ортопедическая больница Роберта Джонса и Агнес Хант в Великобритании. Oswestry, специализированная ортопедическая больница с давними традициями инноваций в лечении своих пациентов.
Используя модели, напечатанные на LC Pro, предшественнике LC Magna, хирург смог спланировать сложную остеотомию бедра у несовершеннолетнего пациента с деформацией бедра. Необходимые разрезы были запланированы заранее, а также предварительно сформирована форма имплантата, необходимая для успешной коррекции. Эти 3D-принты в конечном итоге сэкономили NHS более 1000 фунтов стерлингов и сэкономили час времени в кинотеатре.
Какие проблемы необходимо решить, чтобы ускорить внедрение аддитивного производства?
Самая большая проблема - отсутствие свойств материала.
Когда мы впервые начали заниматься 3D-печатью, мы обнаружили, что три ключевых проблемы препятствуют более широкому внедрению 3D-печати:1) чрезвычайно высокая стоимость, 2) отсутствие масштабируемости производства и 3) отсутствие функциональных свойств.
ЖК-экраны, безусловно, изменили первую проблему:тысячи недорогих мобильных экранов предлагают печать с чрезвычайно высоким разрешением. Широкоформатные ЖК-экраны начали решать проблему масштаба, однако вопрос о свойствах материалов еще не решен должным образом.
В настоящее время мы работаем с BASF над разработкой самого широкого диапазона смол, обеспечивающих долговечные свойства, чем можно функционально использовать в промышленности.
Каким вы видите развитие технологий аддитивного производства и отрасли?
Для нас ЖК-экраны действительно разрушительны и изменят правила игры для SLA-печати.
С помощью ЖК-экранов мы можем обеспечить массовое производство деталей по индивидуальному заказу либо с помощью отдельных больших экранов, на которых можно производить большие детали за меньшую часть времени, чем технологии, использующие лазеры или проекторы, либо с помощью серии более мелких , экраны с более высоким разрешением, которые производят множество мелких деталей.
Я также вижу, что все машины становятся автоматическими, что устраняет необходимость в ручном вмешательстве. Я ожидаю, что функциональные пластиковые детали, напечатанные на 3D-принтере, будут использоваться на производственных линиях в течение 2 лет, поскольку преимущества отсутствия инструментов, нестандартного дизайна и свободы геометрической формы используются в промышленных масштабах.
Другое изменение, которое я вижу, преобразующее производство керамических и металлических деталей, - это создание зеленого тела с помощью 3D-печати с последующим спеканием для получения прочной и жизнеспособной керамики и металлов. Этот процесс является менее энергоемким и более дешевым, что позволяет производить более широкое производство этих материалов на заказ.
Photocentric недавно анонсировала свой новый 3D-принтер Liquid Crystal Magna. Не могли бы вы рассказать нам о некоторых характеристиках и преимуществах этой машины?
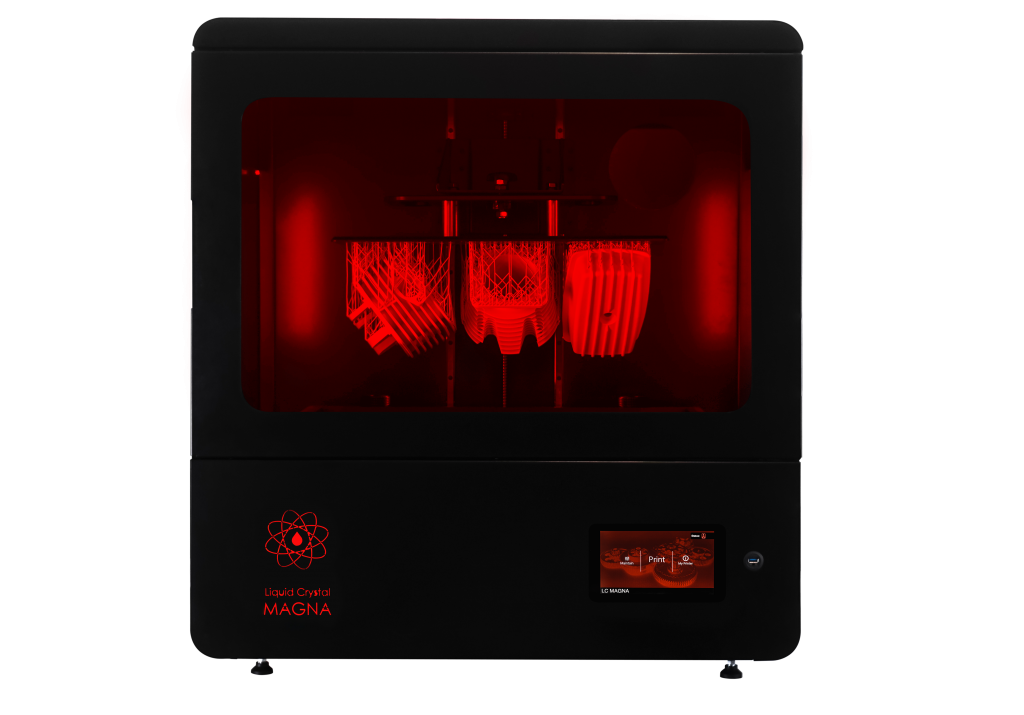
Цель нашей машины LC Magna - обеспечить массовое производство по индивидуальному заказу и создание прототипов крупных компонентов по рентабельной цене. LC Magna может изготавливать сотни нестандартных деталей при значительно низких затратах.
LC Magna имеет большой объем сборки и предлагает высокоточную печать, что делает ее идеальной для массового производства на заказ. Его объем сборки составляет 510 мм x 280 мм x 350 мм, что делает его самым большим 3D-принтером на основе ЖК-экрана, доступным в настоящее время.
LC Magna также имеет 23,4-дюймовый экран 4K Ultra HD в сочетании со специальной подсветкой. Эти два элемента работают вместе, обеспечивая чрезвычайно высокую точность и детализацию печати. Яркость подсветки позволяет принтеру отображать слои толщиной 100 микрон за 3–8 секунд.
Устройство в основном предназначено для зубных техников, дизайнеров продукции, инженеров и производителей, которые смогут увеличить их производительность, ускорить сборочное производство и сократить время выполнения заказа.
Например, производитель очков теперь может массово производить 36 оптических оправ в течение 12 часов, то есть менее 20 минут для каждого комплекта. Зубной техник, которому требуется большое количество моделей для конкретных пациентов, теперь может напечатать 46 плоских дуг чуть более чем за 1 час - это будет стоить менее 1,06 фунтов стерлингов за арку при использовании с нашей собственной смолой для стоматологических моделей Daylight.
Что ожидает Photocentric в следующие 12 месяцев?
Мы считаем, что индустрия 3D-печати открывает множество возможностей - она влияет на все аспекты производства. Учитывая широкий спектр неизведанных возможностей в этой области, мы активно участвуем в ряде интересных проектов.
Например, мы работаем над рядом новых 3D-принтеров для производства пластмасс, керамики. и металлы.
Мы также расширяем нашу команду, особенно в отделе исследований и разработок, чтобы глубже заняться 3D-печатью на металле и керамике. Это существенно повлияет на наш подход к производству материалов.
Чтобы узнать больше о Photocentric, посетите:https://photocentricgroup.com/
3D печать
- Интервью с экспертом:профессор Нил Хопкинсон, директор по 3D-печати в Xaar
- Интервью с экспертом:Филип Коттон, основатель 3Dfilemarket.com
- Интервью с экспертом:Спенсер Райт из pencerw.com и nTopology
- Интервью с экспертом:доктором Альваро Гоянесом из FabRx
- ACEO® представляет новую технологию для 3D-печати с силиконом
- Интервью с экспертом:д-р Бастиан Рапп из NeptunLab
- Интервью с экспертом:Феликс Эвальд, генеральный директор DyeMansion
- Интервью с экспертом:Ибрахим Хадар из Markforged
- Интервью с экспертом:генеральный директор Nanoe Гийом де Калан о будущем керамической 3D-печати
- Интервью с экспертом:президент Ultimaker Джон Кавола о будущем 3D-печати