Поведение при спекании SiC, спеченного плазменной искрой, с композитными наночастицами Si-SiC, полученными методом термической плазмы постоянного тока
Аннотация
Композитная наночастица SiC (Si-SiC), покрытая Si, была получена путем термической плазменной обработки твердотельного синтезированного порошка SiC без переноса дуги и использовалась в качестве спекающей добавки для формирования керамики SiC. Спеченные таблетки SiC были приготовлены методом искрового плазменного спекания (SPS), и было исследовано влияние наноразмерных композитных частиц Si-SiC на характеристики спекания порошка SiC микронного размера. Отношение смешивания композитной наночастицы Si-SiC к SiC микронного размера было оптимизировано до 10 мас.%. Твердость и относительная плотность по Виккеру увеличивались с увеличением температуры спекания и времени выдержки. Относительная плотность и твердость по Виккеру были дополнительно увеличены за счет реакционного связывания с использованием дополнительного активированного угля к смеси SiC микронных размеров и Si-SiC наноразмеров. Максимальная относительная плотность (97,1%) и твердость по Виккеру (31,4 ГПа) были зарегистрированы при температуре спекания 1800 ° C в течение 1 мин выдержки, когда к смеси SiC / Si-SiC было добавлено 0,2 мас.% Дополнительного активированного угля.
Фон
Керамика из карбида кремния (SiC) привлекает большое внимание благодаря своим феноменальным свойствам, таким как высокотемпературная твердость, износостойкость, низкий коэффициент теплового расширения, высокая теплопроводность, высокая коррозионная стойкость и высокая стабильность в агрессивной среде. применяется в различных областях, таких как лопатки турбин, детали дизельных двигателей, материалы для аэрокосмических и ядерных реакторов [1,2,3,4,5,6]. Однако уплотнение SiC без добавок затруднено из-за ковалентной природы связи Si – C и низкого коэффициента самодиффузии [7,8]. Объемные материалы SiC обычно получают либо из спеченного в твердом состоянии карбида кремния (SSS-SiC), либо из спеченного в жидкой фазе карбида кремния (LPS-SiC) из исходных кристаллических порошков SiC [7, 8]. В случае SSS-SiC никакие жидкости, образующие добавки, такие как бор, алюминий, углерод или их соединения, не использовались для уплотнения SiC за счет снижения поверхностной энергии зерен и реакции между диоксидом кремния, присутствующим на поверхности, и углерод. Однако этот процесс требует для спекания температуры более 2000 ° C [7, 9, 10]. LPS-SiC регулируется образованием жидкой фазы добавки оксида металла при температуре спекания, и эта жидкая фаза действует как масс-транспортная среда во время спекания SiC [8, 11, 12]. За исключением оксида магния и алюминия, оксиды оксида иттрия и других редкоземельных элементов в основном используются в качестве спекающих добавок, а температура спекания может быть снижена до 1850 ° C, в зависимости от используемой комбинации спекающих добавок [11, 12]. Однако наличие аморфного силикатного соединения на границах зерен и тройных точках вызывает снижение твердости и сопротивления высокотемпературной ползучести по сравнению с SSS-SiC [12]. Но добавки, используемые для улучшения обработки, неизменно становятся «слабой» вторичной фазой в конечной керамике, что обычно снижает ее механические свойства при высокой температуре [13]. Этот вредный эффект означает, что желательна наименьшая фракция добавок. Кроме того, эффективность добавок во многом зависит от однородности их распределения [13]. Существует также другой подход для изготовления объемного SiC, который называется реакционно-связанным карбидом кремния (RB-SiC). В RB-SiC реакция расплавленного кремния с углеродным порошком приводит к образованию SiC [13,14,15,16]. Хотя этот подход требует более низкой температуры спекания и нет ограничений по форме и размеру продукта, низкая плотность тел является недостатком [17, 18]. Однако снижение температуры спекания необходимо для экономии энергии. В последнее время энергосбережение становится движущей силой для поиска других методов, подходящих для изготовления объемной керамики SiC при низкой температуре.
В последнее время наноразмерный SiC широко исследуется для изучения их механических, физических и химических свойств, которые отличаются от свойств в объемных формах и часто используются [19,20,21]. Например, нанопорошки, в первую очередь за счет более высоких удельных площадей поверхности и поверхностной активности, могут обеспечить низкотемпературную спекаемость наноразмерного SiC в процессе консолидации и улучшение механических свойств, позволяя достичь высоких плотностей [22]. Поэтому в настоящее время мы разработали новый метод получения наночастиц SiC (Si-SiC), покрытых Si, для применения в качестве спекающей добавки, с использованием термической плазменной обработки на постоянном токе без переноса твердотельного синтезированного порошка SiC [23]. / P>
В этом исследовании наноразмерные композитные частицы Si-SiC в качестве спекающей добавки применялись для получения объемной SiC-керамики с помощью процесса искрового плазменного спекания (SPS), а также влияние добавления наноразмерных композитных частиц Si-SiC на спекание. были исследованы температура, относительная плотность и твердость по Виккеру спеченной керамики SiC. Кроме того, для дальнейшего увеличения относительной плотности и твердости спеченного SiC в процесс спекания SiC была введена реакционная связь между свободным кремнием наноразмерных частиц Si-SiC и активированным углем, который был дополнительно добавлен. Механизм спекания SiC-керамики, полученной с наноразмерной композитной добавкой Si-SiC с помощью процесса SPS, также обсуждался на основе наноразмерного эффекта и эффекта реакции связывания. Это исследование предлагает новую многообещающую стратегию получения керамики SiC с высокой плотностью и твердостью при относительно низкой температуре спекания.
Экспериментальный
На рис. 1 показаны процедуры получения порошка SiC микронного размера путем реакции твердое тело-твердое тело (прокаливание), порошка SiC наноразмеров с помощью процесса термической плазмы без переносимой дуги и спеченных таблеток SiC с помощью процесса SPS. В этой работе порошки SiC двух различных размеров, порошок SiC микронного размера (в качестве основного материала для спекания) и наноразмерный композитный нанопорошок Si-SiC (в качестве спекающей добавки), были приготовлены с помощью процессов прокаливания и плазмы соответственно. P>
Экспериментальная процедура получения порошка SiC микронного размера путем прокаливания и порошка композитного наноразмерного Si-SiC плазменным способом и спекания керамики SiC методом SPS
Подготовка порошка SiC микронного размера
SiC микронного размера был синтезирован с использованием порошков Si со средним размером частиц 25 мкм (99,9%; Neoplant Co. LTD.) И активированного угля со средним размером частиц 32 мкм (Sigma-Aldrich). В типичной процедуре Si и углерод при мольном соотношении 1:1,5 смешивали вместе с использованием шаровой мельницы в течение 15 часов. Смешанный порошок помещали в вертикальную трубчатую печь и нагревали при 1300 ° C в течение 2 часов со скоростью нагрева 10 ° C / мин в присутствии газообразного аргона (1 л / мин). После завершения реакции полученный порошок растирали в агатовой ступке для дальнейшей характеристики.
Плазменная обработка синтезированных порошков SiC
Плазменная обработка проводилась в дуговом термоплазменном реакторе с непередаваемой дугой, как сообщалось в нашей предыдущей работе [21, 23]. Измельченный порошок SiC подавался в плазменную дугу по внутреннему питающему трубопроводу с внутренним диаметром 2 мм в плазмотроне с помощью специально разработанного устройства подачи порошка. Система подачи порошка состояла из контейнера для образца, вибратора и линии газа-носителя. Порошки подавали вибропитателем при 70 В со скоростью подачи 1 г / мин. Типичные эксперименты по синтезу проводились при давлении в системе 200 Торр и расходе плазменного газа Ar 30 л / мин, H 2 расход газа около 3 л / мин и постоянный ток 300 А (при 45 В). После плазменного зажигания по питателю подавался порошок SiC микронных размеров. Синтезированные нанопорошки собирались со стенок реактора и со дна системы плазменного реактора. Доходность составила около 80–85%.
Подготовка спеченных гранул SiC
Гранулы спеченного SiC были приготовлены методом SPS (как показано на рис. 1). Оба материала SiC, то есть порошок SiC микронного размера, синтезированный в процессе прокаливания, и наноразмерный порошок Si-SiC, полученный плазменным способом, использовались без дополнительных добавок. Содержание наночастиц Si-SiC в порошке SiC микронного размера было изменено с 5 до 15 мас.%.
Смешанные порошки помещали в графитовую фильеру (диаметром 20 мм) и спекали в системе SPS в вакуумной атмосфере (10 -2 Торр). Скорость нагрева была зафиксирована на уровне 600 ° C / мин, а прилагаемое давление - 80 МПа. Температуру спекания изменяли с 1600 до 1800 ° C. Время выдержки при заданной температуре варьировали от 0 до 1 мин при 1800 ° C. После спекания поверхности образцов шлифовали для удаления графитового слоя, а затем полировали алмазной пастой. Плотность спеченных образцов измеряли методом Архимеда в деионизированной воде в качестве иммерсионной среды.
Образец характеристики
Кристаллографические структуры твердых образцов были определены с помощью XRD (D / Max 2005 Rigaku), снабженного графитовым монохроматизированным высокоинтенсивным излучением Cu-Kα1 ( λ =1,5405 Å). Картины XRD были записаны от 20 ° до 80 ° (2 θ ) со скоростью сканирования 0,04 ° / с. Размер и морфология частиц были исследованы с помощью сканирующего электронного микроскопа (SEM; JSM-5900, JEOL) и просвечивающего электронного микроскопа (TEM; JEM-2010, JEOL).
Результаты и обсуждение
На рис. 2 показаны рентгенограмма и изображение FESEM SiC, синтезированного твердотельным методом с использованием смеси Si и C в мольном соотношении 1:1,5. Картина XRD подтверждает образование β-SiC с небольшим количеством α-SiC, как показано на рис. 2а. Других примесных фаз, таких как свободный кремний и SiO 2 не было. . Изображение FESEM показало образование частиц SiC микронного размера, причем размер частиц варьировался от 2 до 5 мкм, как показано на рис. 2b.
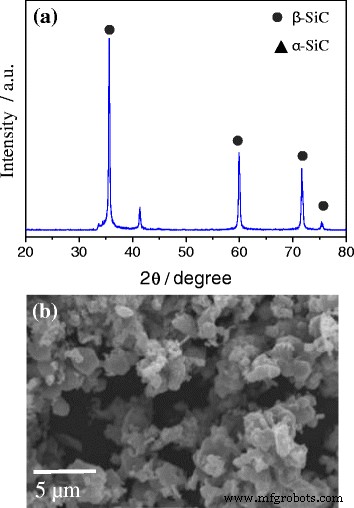
Профиль XRD ( a ) и изображение FESEM ( b ) SiC микронных размеров, синтезированного твердотельным методом
Наноразмерный порошок SiC был приготовлен из этого порошка SiC микронного размера с использованием термической плазменной обработки, как показано на рис. 3. На рис. 3a, b было изображение FESEM и изображение TEM, соответственно. Эти фотографии подтверждают образование наноразмерных частиц Si-SiC, размер которых варьировался от 20 до 70 нм. На рис. 3с представлено изображение ПЭМ наночастиц Si наноразмерных частиц SiC, которое подтверждает формирование наноразмерных композитных частиц Si-SiC, поскольку представлены прозрачные полосы решетки обоих материалов (Si и SiC). Площадь поверхности наноразмерного порошка SiC составляла 69 м 2 . / г.
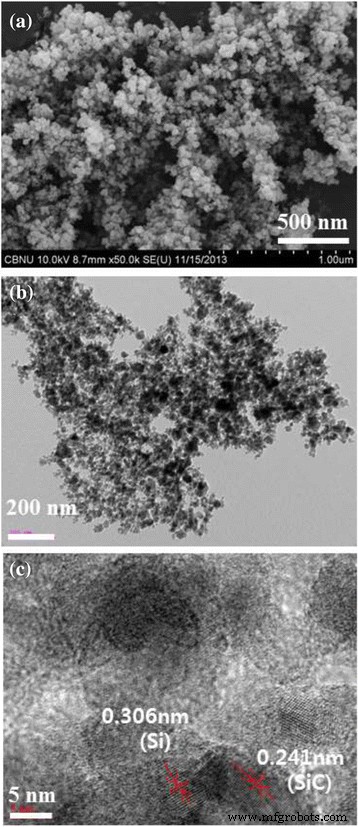
ЭМ-изображения композитных частиц Si-SiC, полученных с помощью процесса термической плазмы без переносимой дуги: a ФЕСЕМ, б ТЕМ и c HR-TEM
Фаза и структура наноразмерных частиц SiC были проанализированы с помощью XRD и показаны на рис. 4. Подобно SiC микронного размера, он также показывает образование β-SiC с небольшим количеством α-SiC. Однако наноразмерный SiC показал свободный Si и SiO 2 . пики. Появление кремниевого пика связано с частичным разложением SiC в процессе термической плазменной обработки. Происхождение SiO 2 Возможно, пик был связан с частичным окислением поверхности SiC при выдержке на воздухе после плазменной обработки. Спеченная керамическая таблетка SiC была приготовлена из этих двух типов SiC, то есть из композитов SiC микронного размера и композитов Si-SiC наноразмеров. Смесь была спечена методом SPS с использованием различных составов SiC микронного размера и Si-SiC наноразмеров, а температура спекания, время выдержки при температуре спекания и давление сжатия менялись, как показано в Таблице 1.
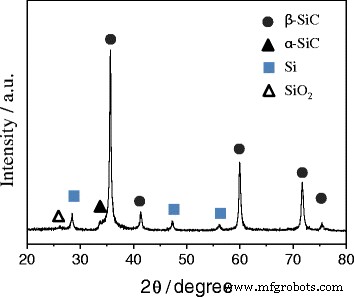
Профиль XRD композитных наночастиц Si-SiC, полученных методом термической плазмы без переносимой дуги
Изменения относительной плотности и твердости по Виккеру спеченного SiC в зависимости от температуры спекания и времени выдержки при заданной температуре спекания также приведены в таблице 1. Относительная плотность и твердость возрастают с увеличением температуры спекания, а также с максимальной относительной плотностью (87,4%) и твердостью. (18,6 ГПа) были зарегистрированы при 1800 ° C. Относительная плотность и твердость были дополнительно увеличены до 88,2% и 21,2 ГПа соответственно при увеличении времени выдержки с 0 до 1 мин при температуре спекания 1800 ° C. Это говорит о том, что относительная плотность и твердость возрастают с увеличением времени выдержки; К сожалению, время выдержки при 1800 ° C нельзя было увеличить из-за ограничений системы SPS.
На рис. 5 показаны изображения поверхности спеченного SiC, полученные методом FESEM, при изменении температуры спекания и времени выдержки. Размер зерна SiC увеличивался с увеличением температуры спекания, как показано на рис. 5a – c. Форма и размер частиц SiC микронного размера практически сохранялись до 1600 ° C (рис. 5а), а рост зерен SiC начинался с 1700 ° C, что привело к увеличению относительной плотности и твердости до 86,1 % и 14,8 ГПа соответственно (рис. 5б). При температуре спекания 1800 ° C размер зерна SiC составлял 2–4 мкм, а текстура кристалла была более плотной (рис. 4в). Относительная плотность и твердость при 1800 ° C составили 87,4% и 18,6 ГПа соответственно. Рост зерна дополнительно регистрировали, когда образец выдерживали в течение 1 мин при температуре спекания 1800 ° C, о чем свидетельствует увеличение относительной плотности и твердости до 88,2% и 21,2 ГПа соответственно (рис. 5d).
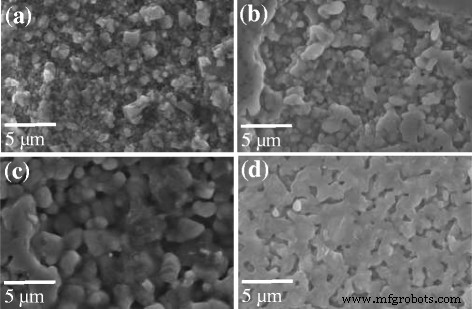
Изображения FESEM спеченного SiC с наноразмерными композитными частицами Si-SiC с помощью процесса SPS в a 1600 ° С, b 1700 ° С, с Температура спекания 1800 ° C при времени выдержки 0 мин и d Температура спекания 1800 ° C при времени выдержки 1 мин при заданной температуре
Для увеличения относительной плотности количество добавляемого наноразмерного Si-SiC в микронный порошок SiC было изменено с 5 до 15 мас.%. Кроме того, в эту смесь был добавлен дополнительный активированный уголь для увеличения относительной плотности за счет реакционного связывания (RB) со свободным кремнием наноразмерного Si-SiC. Относительная плотность и твердость по Виккеру спеченного SiC в зависимости от различных составов SiC микронных размеров, Si-SiC наноразмеров и активированного угля приведены в таблице 2.
Температура спекания (1800 ° C), время выдержки (1 мин) и давление (80 МПа) поддерживались постоянными на протяжении всего эксперимента. В отсутствие добавленного углерода относительная плотность и твердость возрастают с увеличением содержания наноразмерного SiC до 10 мас.%, А затем уменьшаются. Например, относительная плотность и твердость составляли 85,9% и 21,1 ГПа, когда содержание наноразмерного Si-SiC составляло 5 мас.%. Относительная плотность и твердость увеличились до 88,2% и 21,2 ГПа, соответственно, при 10 мас.% Наноразмерного Si-SiC. Тогда как при содержании 15 мас.% Твердость заметно снизилась до 16,6 ГПа, хотя относительная плотность все еще оставалась 85,6%. Это главным образом связано с тем, что чрезмерно добавленные наноразмерные частицы Si-SiC могут создавать большое количество пор в спеченном SiC. Для дальнейшего увеличения относительной плотности и твердости дополнительно был добавлен активированный уголь. Добавление 0,1 мас.% Активированного угля привело к значительному увеличению относительной плотности (93,1%) и твердости (25,2 ГПа). Относительная плотность и твердость были дополнительно увеличены до 97,1% и 31,4 ГПа соответственно при увеличении содержания активированного угля до 0,2 мас.%. Проведенный рентгеноструктурный анализ этих спеченных таблеток SiC различного состава показан на рис. 6. Не было изменений в кристаллической структуре даже после спекания, за исключением слабого пика кремния, зарегистрированного при 29 °, который, возможно, возник из-за добавления наноразмерные композитные частицы Si-SiC.
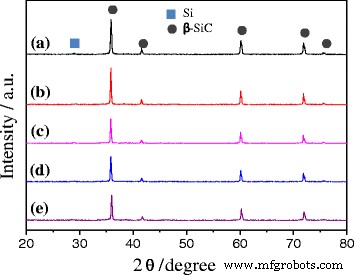
Профили XRD гранул SiC, спеченных с наноразмерными композитными частицами Si-SiC и активированным углем с помощью процесса SPS (детали a, b, c, d и e приведены в таблице 2)
На рис. 7 показаны FESEM-изображения поверхности спеченных таблеток SiC с различными микронными размерами SiC и наноразмерными составами Si-SiC. Размер зерна SiC составлял 2–3 мкм с более крупными порами, когда содержание наноразмерного Si-SiC составляло 5 мас.% (Рис. 7а). Размер зерна увеличивался с увеличением содержания наноразмерного Si-SiC, как показано на рис. 7b, c. Размер зерна таблеток SiC с 10 и 15 мас.% Si-SiC составлял примерно 3–5 и 4–6 мкм соответственно. На рис. 7d, e представлены FESEM-изображения спеченных гранул SiC после добавления активированного угля. Когда было добавлено 0,1 мас.% Активированного угля, начинают появляться гигантские зерна, что свидетельствует о том, что уплотнение текстуры SiC происходило за счет реакции связывания кремния с активированным углем. Дальнейшее увеличение содержания активированного угля до 0,2 мас.% Привело к полному уплотнению текстуры SiC, как показано на рис. 7e.
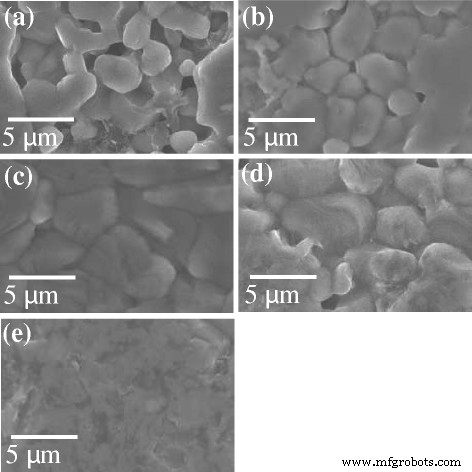
FESEM-изображения таблеток SiC, спеченных с наноразмерными композитными наночастицами Si-SiC и активированным углем с помощью процесса SPS (подробности a , b , c , d и e приведены в таблице 2)
На рис. 8 представлены усадочные перемещения спеченных образцов SiC разного состава при разной температуре спекания. Для всех образцов было зарегистрировано расширение до 1500 ° C, что в основном связано с расширением газов, присутствующих в смеси SiC (рис. 8a – e). Это также можно наблюдать по увеличению на 1,0–1,28 мм высоты графитовой формы с порошковой смесью SiC после спекания по сравнению с начальным этапом спекания. Дальнейшее повышение температуры спекания привело к усадке всех образцов из-за эффекта спекания наночастиц Si-SiC. Увеличение времени выдержки образцов при температуре спекания от 0 до 1 мин также привело к увеличению усадки образцов. Добавление дополнительного активированного угля к смеси SiC и Si-SiC показало более высокое смещение усадки после 1500 ° C по сравнению со смесями SiC / Si-SiC без активированного угля (рис. 8d, e). Кроме того, смещение усадки увеличивается с увеличением количества дополнительного активированного угля. Например, смещение при усадке было увеличено с 1,11 до 1,61 мм, когда количество добавленного активированного угля было увеличено с 0,1 до 0,2 мас.% Соответственно, как показано на фиг. 8d, e. Это связано с эффектом реакции связывания свободного кремния композитной наночастицы Si-SiC и активированного угля. Экзотермический характер этой реакции приводит к повышению реальной температуры внутри таблетки SiC во время спекания. Таким образом, эти результаты четко подтверждают, что эффект реакции связывания кремния и активированного угля может увеличить относительную плотность и твердость керамики SiC.
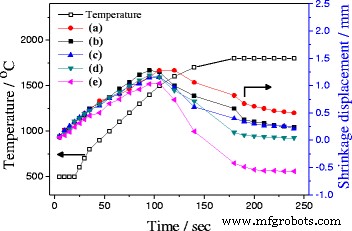
Изменение усадочного смещения таблеток SiC, спеченных с наноразмерными композитными наночастицами Si-SiC в процессе SPS (детали a, b, c, d и e приведены в таблице 2)
Из приведенных выше экспериментальных результатов мы можем резюмировать механизм спекания порошка SiC микронного размера с наноразмерным композитным порошком Si-SiC и активированным углем следующим образом. В таблице 1 было определено, что спекание порошка SiC микронного размера с 10 мас.% Наноразмерного композитного порошка Si-SiC начиналось при 1600 ° C, и реакция спекания ускорялась с увеличением температуры спекания и времени выдержки. На основе этого результата мы подтвердили влияние наноразмеров композитных наночастиц Si-SiC на спекание порошка SiC микронного размера. При этом, если активированный уголь добавлен к смеси SiC микронного размера и наноразмерного композитного порошка Si-SiC, реакционное связывание, возникшее в результате экзотермической реакции между свободным кремнием композитных наночастиц Si-SiC, может быть вызвано процесс спекания, как схематично показано на рис. 9. Следовательно, можно было обнаружить, что механизм спекания порошка SiC микронного размера с наноразмерным композитным порошком Si-SiC и активированным углем в качестве спекающих добавок зависит от обоих эффектов:наночастиц размерный эффект и эффект связывания реакции, которые были внесены в наноразмерный композитный порошок Si-SiC.
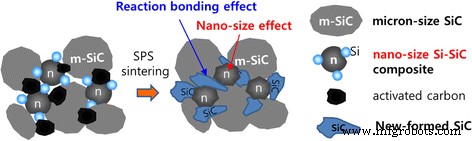
Схематическое изображение механизма спекания порошка SiC микронного размера с наноразмерным композитным порошком Si-SiC и активированным углем в качестве спекающих добавок
Выводы
Порошок SiC микронных размеров (2–5 мкм) был синтезирован твердотельным методом с использованием порошка Si и источников активированного угля. Наноразмерный композитный порошок Si-SiC с размером частиц 20–70 нм был приготовлен методом термической плазмы без переноса дуги. Спеченные таблетки SiC были приготовлены методом SPS с использованием смеси с различным соотношением порошка SiC микронного размера и наноразмерных композитных частиц Si-SiC в качестве спекающей добавки. При фиксированном соотношении SiC микронного размера и Si-SiC наноразмеров (90:10) относительная плотность и твердость по Виккеру увеличиваются с увеличением температуры спекания и времени выдержки. Максимальная относительная плотность (88,2%) и твердость по Виккеру (21,2) были зарегистрированы при температуре спекания 1800 ° C в течение 1 мин выдержки. Относительная плотность и твердость по Виккеру были дополнительно увеличены за счет добавления дополнительного количества активированного угля к смеси SiC микронных размеров и Si-SiC наноразмеров. Относительная плотность и твердость по Виккеру были увеличены до 97,1% и 31,4 ГПа, соответственно, с добавлением 0,2 мас.% Дополнительного активированного угля к смеси SiC / Si-SiC. Было обнаружено, что наноразмерный эффект композитной частицы Si-SiC и экзотермический характер реакции кремний-углеродного взаимодействия являются причиной увеличения относительной плотности и твердости. Поэтому было высказано предположение, что наноразмерные композитные частицы Si-SiC могут быть многообещающей добавкой для спекания керамики SiC.
Наноматериалы
- Процесс спекания тугоплавких сплавов
- Значительное повышение теплопроводности силиконового композита с помощью сверхдлинных медных нанопроволок
- Электроспряденные полимерные нановолокна, украшенные наночастицами благородных металлов для определения х…
- Композитные мембраны, содержащие наночастицы неорганических ионообменников для электродиалитического опре…
- Простой синтез окрашенного и проводящего композита CuSCN, покрытого наночастицами CuS
- Нацеливание на эндотелиальные клетки с помощью многофункциональных наночастиц GaN / Fe
- Электрические свойства композитных материалов с выравниванием нанокарбоновых наполнителей с помощью элект…
- Синергетические эффекты наночастиц Ag / BiV1-xMoxO4 с повышенной фотокаталитической активностью
- Исследование влияния направления удара на абразивный нанометрический процесс резания с помощью молекулярно…
- Токсичность наночастиц CoFe2O4, покрытых ПЭГ, с лечебным эффектом куркумина