Проектирование литьевых деталей, часть 2:следы раковины
При разработке изделий, изготовленных методом литья под давлением, всем нам нужны красивые изделия. А в бизнесе мы хотим, чтобы проект шел гладко, потому что на сбои и задержки никогда не бывает времени и, в свою очередь, денег. Таким образом, обнаружение больших раковин прямо там, на передней поверхности вашей первой детали, изготовленной методом литья под давлением, которая также должна иметь блестящую поверхность при производстве, может привести к осознанию того, как это исправить и как исправить это быстро.
Что делать? Вы можете наклеить на него значок с логотипом продукта, но его уже планируется разместить в другом месте и скрыть ворота для литья под давлением для детали. Может еще бейдж? Есть лучший способ исправить это как при обработке форм для литья под давлением, так и в конструкции детали.
Так почему бывают раковины? Дифференциальное охлаждение в пластиковом материале детали, изготовленном методом литья под давлением, обычно в толстой части стенки пластиковой детали, например, там, где внутреннее ребро или выступ соединяется со стенкой, будет втягивать материал, поскольку середина толстой части остывает в последнюю очередь, оставляя ямку на противоположная сторона. Это более заметно на гладких, блестящих поверхностях, особенно из более темных пластиковых цветов.
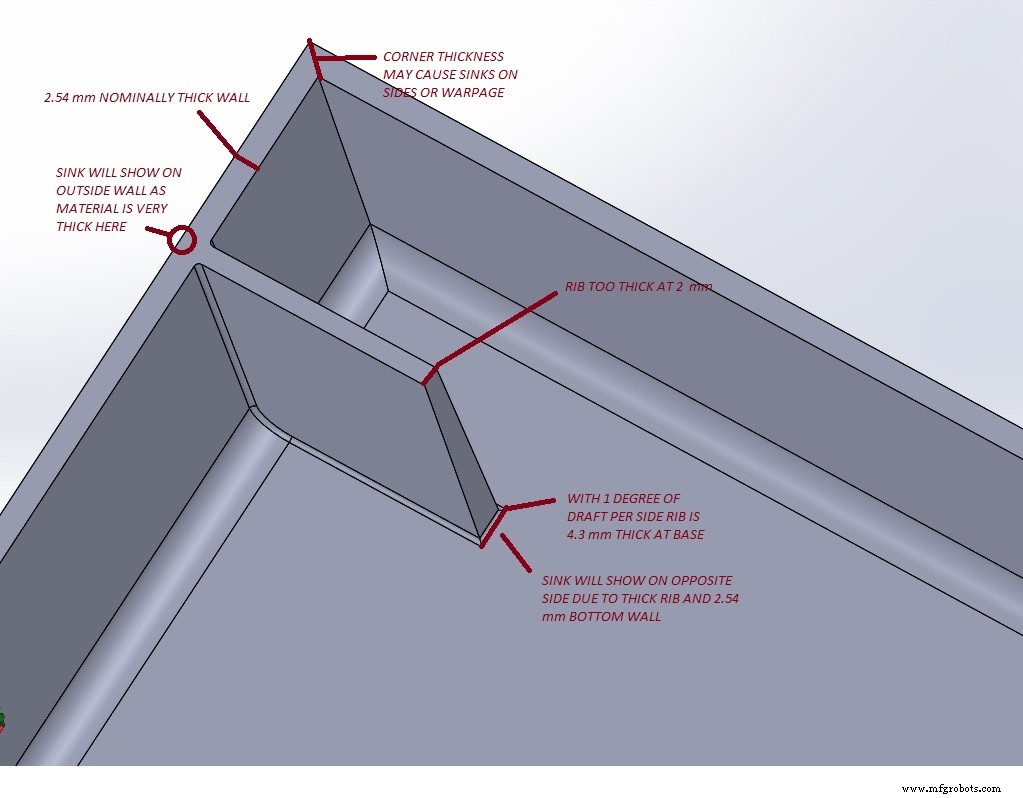
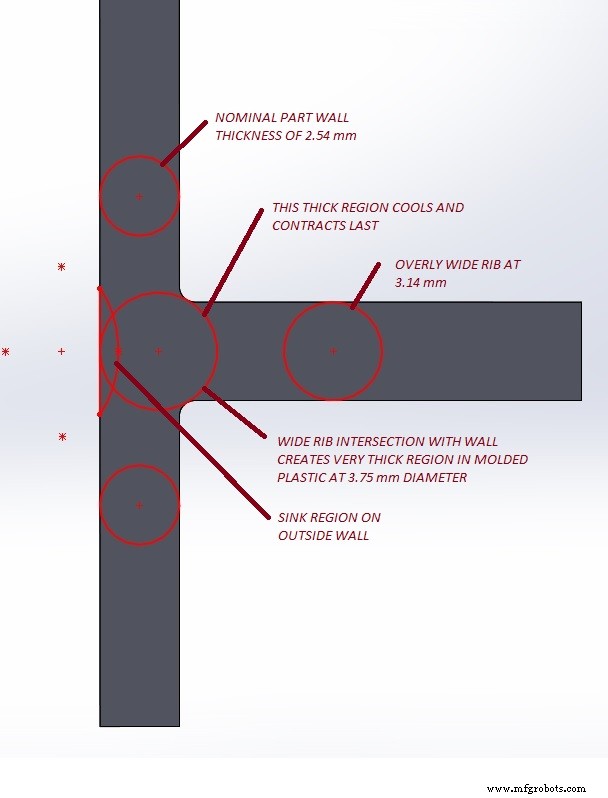
Там, где встречаются две внешние стены или где скошенные поверхности соприкасаются с ребром правильного размера на «вздорном срезе», тоже могут возникнуть раковины. Следование некоторым общим рекомендациям по толщине внутренних стенок и ребер, оставаясь на уровне от 50 до 60 процентов от номинальной внешней стенки, может иметь большое значение, чтобы помочь избежать толстых пятен на деталях, изготовленных литьем под давлением, и, в свою очередь, уменьшить дефекты.
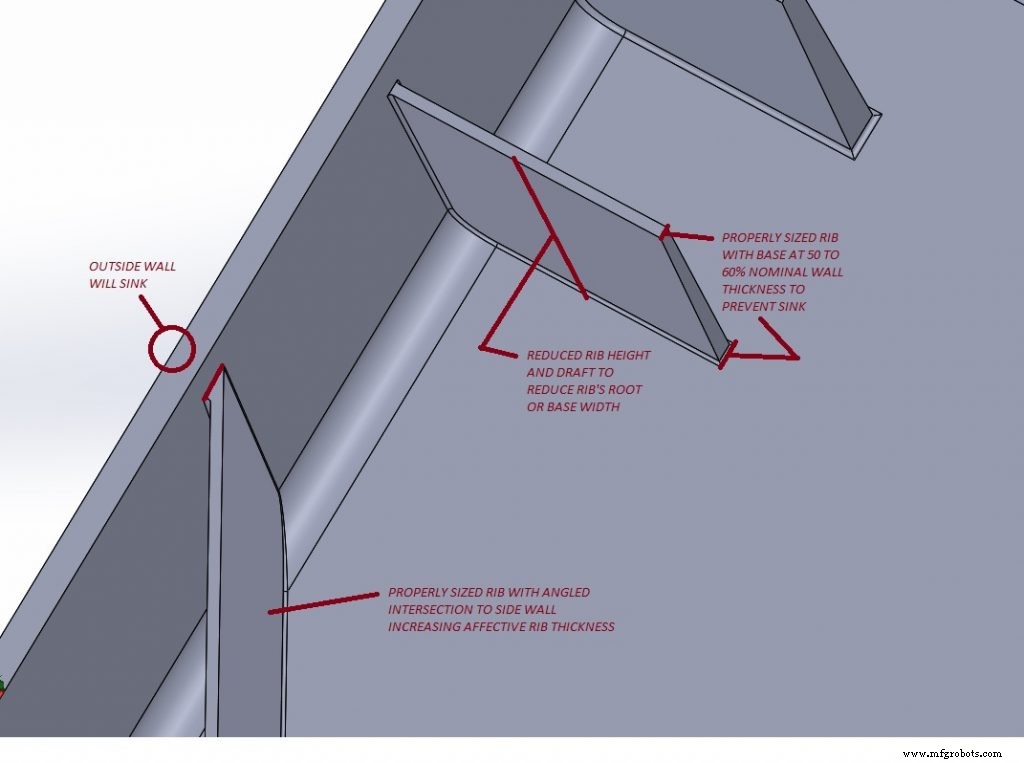
Однако в более сложных формах и переходах в конструкции детали, отлитой под давлением, толстые секции могут быть упущены во время разработки. Для детали, полученной литьем под давлением, может потребоваться дополнительная обработка на пересечениях менее заметных элементов. Блестящее белое основание дозирующей канистры, показанное выше, обычно имело обычную толщину стенок без сильных внутренних ребер.
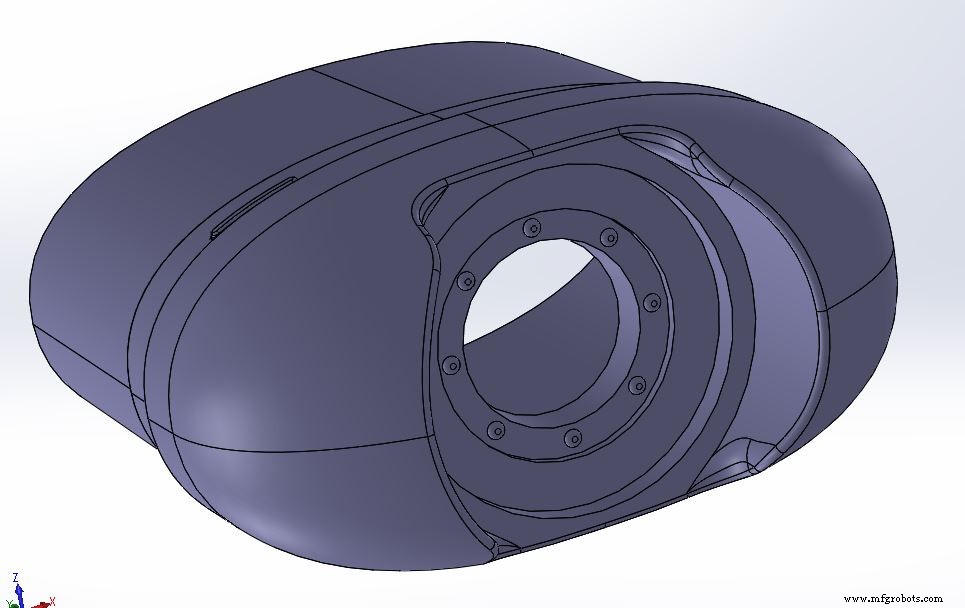
Однако нижнее отверстие для винта с накатанной головкой создавало угловые пересечения стен, что приводило к видимым опусканиям. При внимательном изучении точного местоположения в поперечном сечении было обнаружено совпадение характеристик и материала.
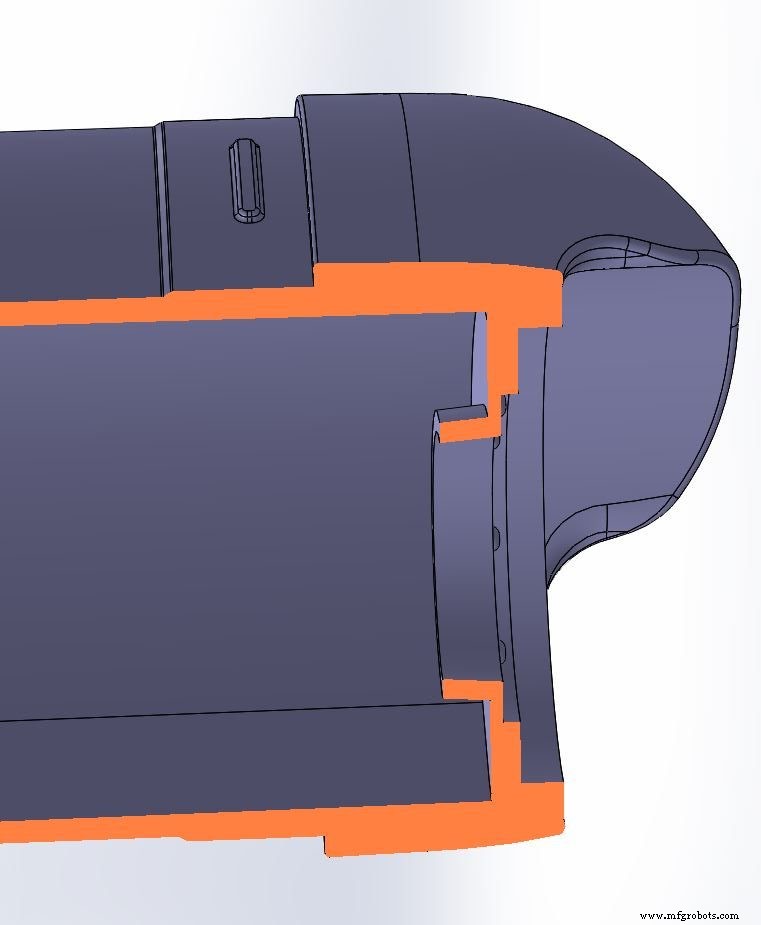
Элементы, которые создали эту толстую секцию, не были легкими кандидатами на прореживание, перемещение или удаление для сохранения небольших размеров и функциональности продукта. А раковины снаружи были недопустимы.
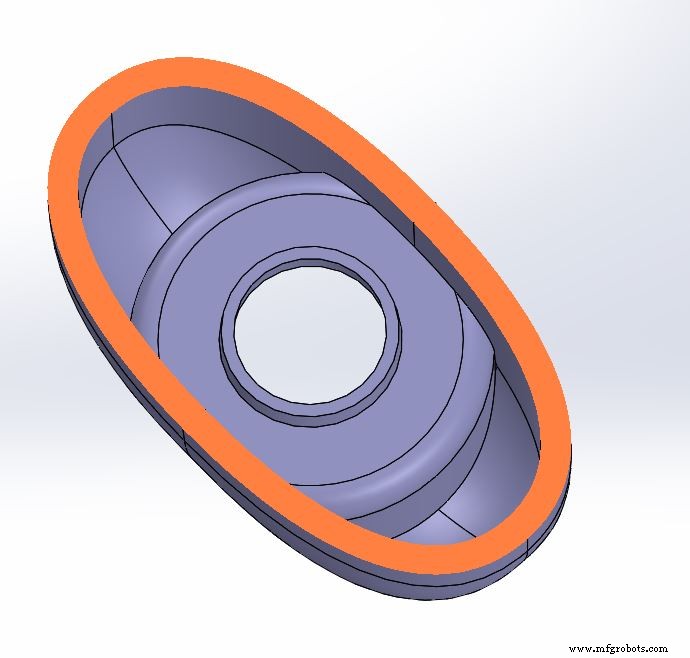
Незначительные внутренние элементы керна, добавленные к сердцевине инструментальной стали для литейной формы, позволили освободить часть материала отлитой под давлением детали для следующего выпуска изделия.
-
До того, как были добавлены функции отбора проб -
После:восстановление материала на стыках стен.
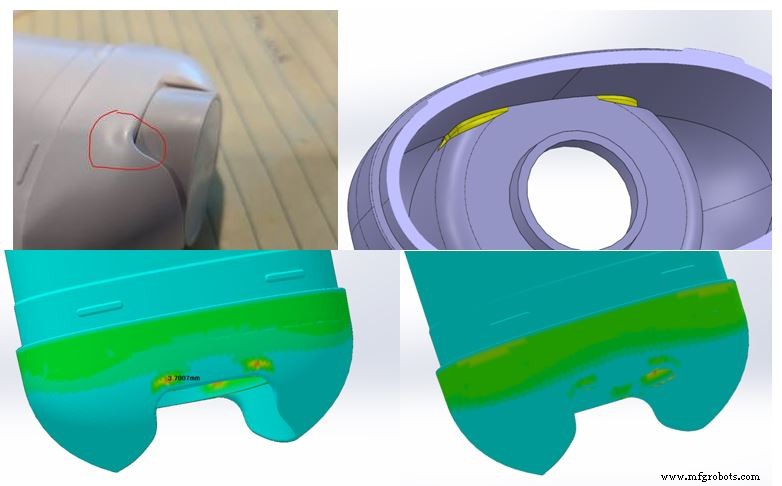
Это наряду с работой с формовщиком для увеличения времени цикла (охлаждение в форме) и усовершенствованием процесса позволило получить безупречную и функциональную деталь. Тесная координация позволила быстро решить проблемы.
Бобышки также представляют собой проблему для деталей, изготовленных литьем под давлением, поскольку они имеют решающее значение для сборки. Их можно представить как конические ребра. Они должны быть такого размера, чтобы они хорошо работали с резьбовым креплением и были прочными, но при несоблюдении определенных методов они открывают много возможностей для толстых участков. Мы поговорим о боссах подробнее в будущем, поскольку они являются важной конструктивной особенностью, требующей множества соображений, и все они сами по себе.
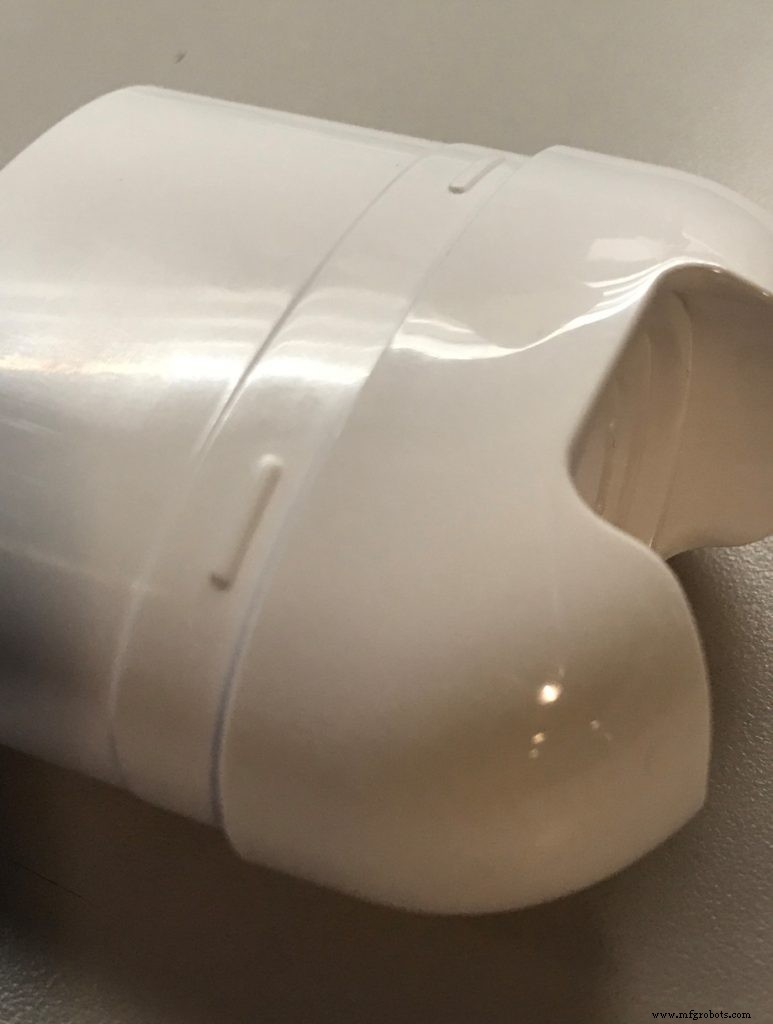
Используя передовые методы проектирования форм для литья под давлением и доступные инструменты 3D CAD, можно спроектировать литые под давлением детали, чтобы минимизировать риск утолщения и других косметических дефектов. Благодаря тесному сотрудничеству с формовщиком и изготовителем инструмента в качестве членов команды, детали, изготовленные литьем под давлением, могут включать усовершенствования, поэтому в результате получаются высококачественные косметические детали, изготовленные литьем под давлением, которые функционируют, как и планировалось. При таком подходе время выхода на рынок будет сведено к минимуму.
Так что имейте в виду рекомендации для внутренних стен и ребер в отношении толщины и пересечений. Сведите к минимуму эти элементы и подумайте о том, чтобы немного уменьшить их осадку, чтобы их толщина варьировалась минимально. Используйте инструменты САПР, такие как анализ толщины, и вручную просматривайте сложные пересечения с помощью инструмента поперечного сечения на предмет областей возможного проседания. А затем поработайте с формовщиком над их анализом пресс-форм и рекомендациями. Это может потребовать дополнительной координации во время производства первой и второй частей изделия, но тесное сотрудничество и внимание к деталям сократят время выхода на рынок. И вам не нужно будет добавлять еще один значок, чтобы скрыть дефект литья под давлением на передней части вашей детали.
Ссылки на:часть 1, часть 3, часть 4
Производственный процесс
- Дизайн литьевых деталей, часть 6:Управление командами и контрактными производителями
- Дизайн литьевых деталей, часть 5:черновик
- Дизайн литьевых деталей, часть 4:деформация
- Дизайн литьевых деталей, часть 3:выступы
- 6 Важные соображения при проектировании для 3D-печати из металла
- Как создать составную деталь из термореактивного материала [Инфографика]
- Руководство по проектированию для обеспечения технологичности – Часть 2
- Руководство по проектированию для обеспечения технологичности – Часть 1
- Какова наилучшая обработка поверхности SPI для вашей литой детали?
- Советы по проектированию для литья под давлением