Методы контроля качества поверхности и внутреннего качества отливок
Проверка отливок в основном включает проверку размеров, визуальный осмотр внешнего вида и поверхности, анализ химического состава и проверку механических свойств. Для отливок с высокими требованиями также требуется неразрушающий контроль. Например, методы неразрушающего контроля для контроля качества отливок из ковкого чугуна включают контроль проникающей жидкости, вихретоковый контроль, контроль магнитных частиц, радиографический контроль и ультразвуковой контроль.
Испытания поверхностных и приповерхностных дефектов отливок
Испытание на проникающую жидкость
Капиллярная дефектоскопия используется для проверки различных дефектов вскрытия на поверхности отливок, таких как поверхностные трещины, поверхностные точечные отверстия и другие дефекты, которые трудно обнаружить невооруженным глазом.
Обычно используемое пенетрантное тестирование - это тестирование красителя, которое заключается в смачивании или распылении пенетранта с высокой проницаемостью на поверхности отливки, проникновении пенетранта в открытые дефекты, быстром стирании слоя пенетранта, а затем распылении легкосохнущего проявителя на отливку. поверхность. После того, как пенетрант, оставшийся в дефектах отверстия, будет откачан, проявитель будет окрашен, чтобы отразить форму, размер и распределение дефектов.
Отмечено, что чем более гладкой является тестируемая поверхность, тем лучше результаты тестирования на проникновение. Поверхность, отшлифованная шлифовальным станком, отличается высочайшей точностью контроля, можно обнаружить даже межкристаллитные трещины.
В дополнение к тестированию красителей, флуоресцентное пенетрантное тестирование также является широко используемым методом жидкостного пенетрантного контроля. Он должен быть оснащен ультрафиолетовой лампой для наблюдения за облучением, а чувствительность тестирования выше, чем при тестировании красителя.
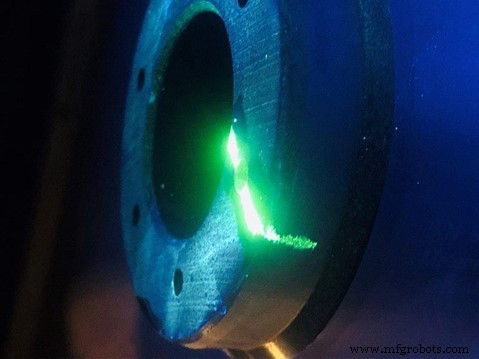
Вихретоковый контроль
Вихретоковый контроль подходит для проверки дефектов под поверхностью, глубина которых обычно не превышает 6-7 мм. Вихретоковый контроль делится на два типа:метод с размещенной катушкой и метод с катушкой сквозного типа.
Когда испытуемый образец помещается рядом с катушкой с переменным током, переменное магнитное поле, входящее в испытуемый образец, может индуцировать вихревой ток, протекающий в направлении, перпендикулярном магнитному полю возбуждения в испытуемом образце. Вихревой ток создаст магнитное поле, противоположное направлению магнитного поля возбуждения, что частично уменьшит первоначальное магнитное поле в катушке, что приведет к изменению импеданса катушки.
Если на поверхности отливки есть дефекты, электрические характеристики вихревого тока будут искажены, чтобы обнаружить наличие дефектов. Основные недостатки вихретокового контроля заключаются в том, что он не может напрямую отображать размеры и форму обнаруженных дефектов. Как правило, он может только определить положение поверхности и глубину дефектов. Кроме того, его чувствительность к дефектам малых отверстий на поверхности отливки не так чувствительна, как к пенетрантному контролю.
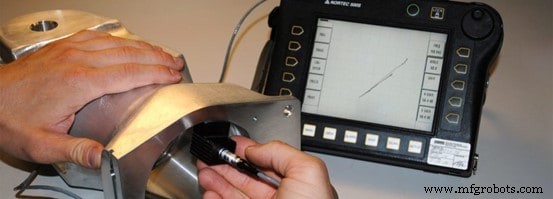
Испытание магнитными частицами
Магнитопорошковая дефектоскопия подходит для проверки поверхностных дефектов и дефектов глубиной в несколько миллиметров под поверхностью. Для тестирования требуется оборудование для намагничивания постоянным (или переменным) током и магнитные частицы (или магнитная суспензионная жидкость).
Намагничивающее оборудование используется для создания магнитного поля на внутренней и внешней поверхности отливки, а магнитопорошковая или магнитная суспензионная жидкость используется для выявления дефектов. Когда магнитное поле генерируется в пределах определенного диапазона отливки, дефекты в намагниченной области будут генерировать магнитное поле рассеяния. Когда магнитная частица или суспензионная жидкость разбрызгиваются, магнитная частица притягивается, так что дефекты могут быть отображены.
Дефекты, выявляемые при магнитопорошковом контроле, - это в основном те, которые пересекают магнитную силовую линию, но дефекты длинных полос, параллельных магнитной силовой линии, не могут быть обнаружены. Поэтому необходимо постоянно менять направление намагничивания во время работы, чтобы можно было проверить каждый дефект в неизвестном направлении.
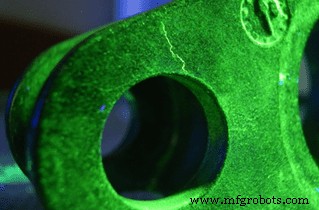
Испытания внутренних дефектов отливок
Для внутренних дефектов обычно используемыми методами неразрушающего контроля являются радиографический контроль и ультразвуковой контроль. Среди них наилучший эффект рентгенологического контроля. Он может получить интуитивное изображение, отражающее тип, форму, размер и распределение внутренних дефектов. Однако для более толстых крупных отливок очень эффективен ультразвуковой контроль, который позволяет точно определить местоположение, эквивалентный размер и распределение внутренних дефектов.
Рентгенографическое исследование
Необходимы радиографические испытания, обычно рентгеновские или гамма-лучи в качестве источника излучения, оборудование для генерации излучения и другие вспомогательные средства. Когда отливка подвергается воздействию поля луча, на интенсивность излучения луча будут влиять внутренние дефекты отливки. Интенсивность излучения, испускаемого через отливку, изменяется локально в зависимости от размера и характера дефектов, формируя рентгенографическое изображение дефектов, которое отображается и регистрируется рентгенографической пленкой.
Метод записи с помощью рентгенографического изображения пленки является наиболее часто используемым методом, который обычно называют рентгенографическим контролем. Изображение дефекта, отраженное рентгенографией, является интуитивно понятным, и могут быть представлены форма, размер, количество, положение в плоскости и диапазон распределения дефектов.
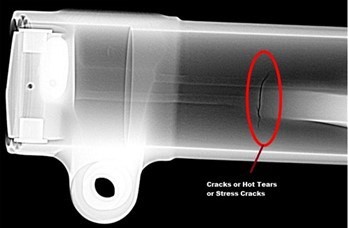
Ультразвуковой контроль
Ультразвуковой контроль использует распространение звуковых лучей с высокочастотной звуковой энергией внутри отливки для создания отражений при попадании на внутренние поверхности или дефекты. Величина отраженной акустической энергии зависит от направленности и свойств внутренних поверхностей или дефектов и акустического импеданса такого отражателя. Таким образом, акустическая энергия, отраженная от различных дефектов или внутренних поверхностей, может использоваться для обнаружения местоположения дефектов, толщины стенок или глубины дефектов под поверхностью.
Как широко используемый метод неразрушающего контроля, ультразвуковой контроль обладает основными преимуществами:высокая чувствительность контроля, позволяющая обнаруживать небольшие трещины; большая проникающая способность, позволяющая обнаруживать отливки толстого сечения. Его основными ограничениями являются:сложность интерпретации сигналов отражения для прерывистых дефектов со сложными контурными размерами и плохой направленностью; нежелательные внутренние структуры, такие как размер зерна, микроструктура, пористость, содержание включений или мелкодисперсные осадки, также затрудняют интерпретацию сигналов.
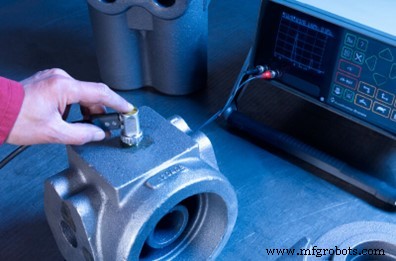
Промышленные технологии
- Повышение качества и безопасности при отслеживании продуктов
- 4 причины, по которым тестирование и проверка оборудования так важны
- Что такое проверка качества сварки? - 10 распространенных дефектов сварки
- Руководство по методам тестирования печатных плат
- Введение в неразрушающий контроль отливок
- Основы контроля качества и контроля при обработке с ЧПУ
- Ротационная плоскошлифовальная машина и качество обработки
- Тестирование печатных плат:акцент на внутрисхемном и функциональном тестировании
- Специализированные методы внутреннего шлифования
- Все в курсе:тестирование и проверка роботизированных деталей