Автоматизированное соединение сокращает время простоя роботизированной сварочной ячейки
Нет лучшего способа решить проблему, чем полностью избавиться от нее. По крайней мере, так считает KTH Parts Industries Inc.. (Санкт-Париж, Огайо) рассмотрела свое решение автоматизировать процесс ручной смены оборудования для своих роботизированных сварочных модулей.
KTH выбрала соединители общего назначения GA2 от ATI Industrial Automation (Apex, NC) для достижения этой цели. В частности, новое автоматическое соединение систем подачи воздуха и электроэнергии с ячейками устранило примерно 65 часов простоя в год на каждой линии, снизило общую стоимость операций и повысило коэффициент использования и производительность оборудования.
KTH Parts Industries, глобальный поставщик автомобильных деталей уровня 1 для элементов конструкции днища, имеет более 1100 инженеров и производственных партнеров, вовлеченных во многие этапы производства автомобильных деталей, включая разработку продукта, анализ продукта, формуемость продукта, прототипирование, производственную штамповку, формование, роботизированная сварка, сборка и отгрузка деталей.
Одной из основных компетенций KTH является проектирование и внедрение гибких сварочных линий для компонентов днища автомобилей. В его сварочных линиях используются сложные приспособления или приспособления, чтобы удерживать компоненты на месте, пока робот их сваривает. Для каждой модели автомобиля требуется свое приспособление, что приводит к многочисленным заменам оборудования на заводе.
Чтобы повысить гибкость и оптимизировать ограниченное производственное пространство, KTH создала двухсторонний рабочий модуль с поворотным столом. Цель этой конструкции состояла в том, чтобы поддерживать активность робота и сократить время настройки. Детали загружаются в приспособление с одной стороны поворотного стола, а робот сваривает детали с другой.
До установки вспомогательных соединителей ATI GA2 компания KTH полагалась на ручной труд для подключения и отсоединения кабелей, а также для установки зажимных приспособлений на проигрыватели. Умножьте это на одну-две переналадки на линию за смену, и вы получите ошеломляющее количество человеко-машинного взаимодействия в процессе.
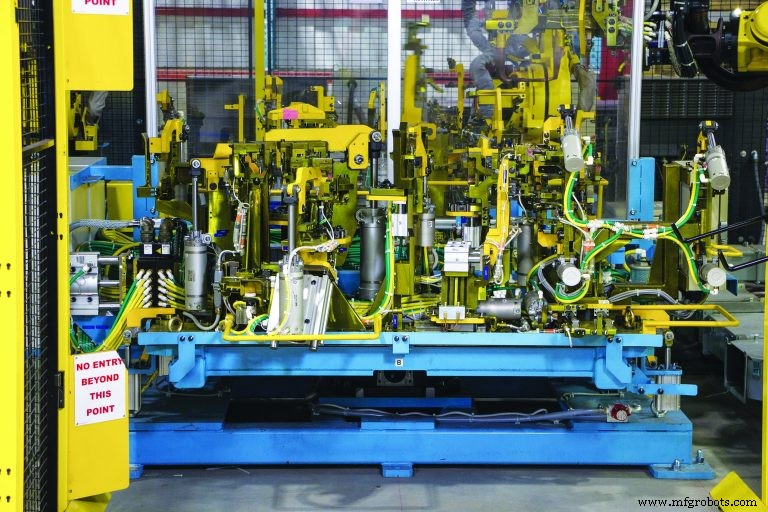
Дэйв Рид, руководитель проекта в отделе сварки KTH, так воспринял старый процесс:«До того, как мы начали использовать вспомогательные соединители ATI, у нас была воздушная линия и коллектор, и нам нужно было соединить их вместе стяжками. С электрической стороны нам пришлось соединить 40-контактные разъединители, скрутив их вручную. Этот процесс повторялся много раз для каждой смены приспособления».
Согласно KTH, требования к физическому труду в старом процессе были очень высоки, и, конечно же, каждый раз, когда сотрудник входил в рабочую камеру, существовал неотъемлемый риск. В этих условиях высокая частота отказов кабеля не была неожиданностью. Сцепление и разъединение тросов с непостоянным усилием и крутящим моментом приводило к чрезмерному износу. Несоосность разъемов привела к повреждению контактов. Без специального места для хранения неиспользуемых кабелей они оставались на полу или поверх другого оборудования в камере.
«У нас были перерезанные воздуховоды и течи, разъемы были повреждены», — сказал Рид. "Техническая поддержка была вызвана, чтобы попытаться оценить проблему, но в большинстве случаев это был просто погнутый контакт на разъеме, который стоил нам нескольких часов простоя — примерно 65 часов в год на каждую линию".
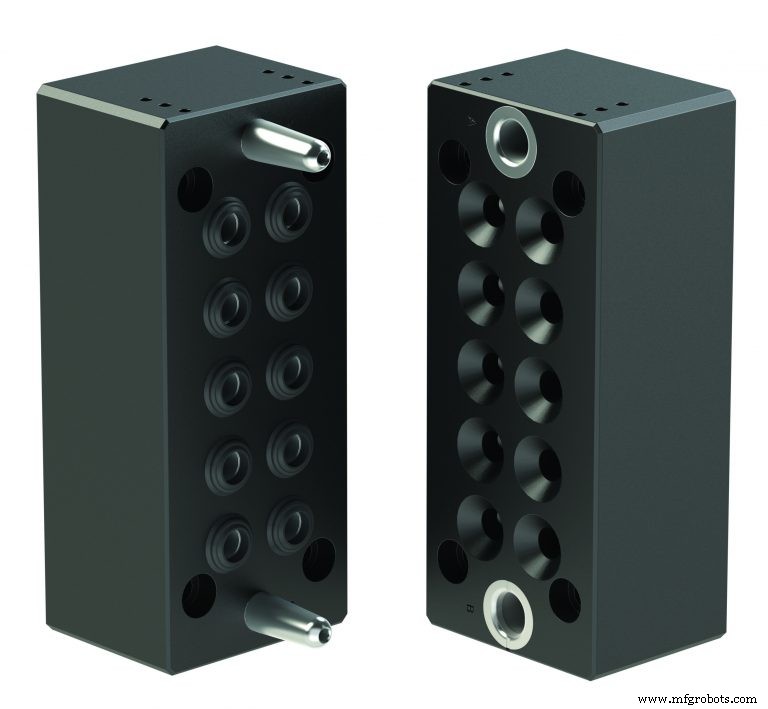
Помимо чрезмерного взаимодействия с людьми и отказов оборудования, старый процесс был кошмаром для группы поддержки оборудования. Руководитель секции группы Джона Страпп отметил:«После переналадки вам придется возиться с чем-то в камере, чтобы она снова заработала. Время простоя означает потерю денег. Когда это происходит, возникает небольшое давление, чтобы заставить линии работать».
Компания KTH была исключительно заинтересована в улучшении смены сварочного приспособления, чтобы обеспечить более плавный ход операций, повысить безопасность сотрудников и снизить количество отказов оборудования. Мэтт Майерс, штатный инженер инженерно-проектной группы KTH, пояснил:«Во время нашей обычной работы мы пытаемся выжать из линии как можно больше продукции. Каждый раз, когда мы делаем переналадку, мы теряем производственное время, что приводит к большому финансовому убытку в наших бухгалтерских книгах. Все, что мы можем сделать для сокращения времени простоя, чрезвычайно важно».
Это именно тот момент, когда переход на утилитарные соединители ATI стал эффективным решением, позволяющим сэкономить время. Вспомогательные соединители ATI хорошо подходят для смены сварочной линии KTH. Они обеспечивают питание, сигнал и пневматику. Муфты общего назначения ATI имеют встроенную податливость к вращению, чтобы обеспечить повторяемое соединение в прочном корпусе. Поскольку конструкция является модульной, служебные соединители работают с обширным семейством служебных модулей ATI для смены инструмента.
Вместе служебные соединители и модули также обслуживают ряд сетевых протоколов, пояснил Майерс из KTH. «Когда дело доходит до дизайна нового продукта, я могу положиться на команду инженеров ATI, которая быстро спроектирует электрический или пневматический продукт, соответствующий нашим потребностям, или сослаться на один из тысяч продуктов [доступных] на их веб-сайте». Для этой конкретной системы в KTH компания ATI настроила вспомогательный соединитель и 32-контактный электрический модуль дискретного ввода-вывода, который легко интегрировался в существующие линии.
«Когда мы впервые начали опробовать универсальный соединитель, сразу стало очевидно, что он будет иметь большое значение. Новые соединители очень надежны и работают без помощи рук. Нам не нужно возиться с ними. Они всегда работают», — сказал Стрэпп.
Когда его спросили, почему KTH выбрала ATI в качестве своего поставщика, Майерс ответил:«Основываясь на наших предыдущих отношениях со службой поддержки клиентов, быстрых сроках поставки и нашем местном менеджере по работе с клиентами, было легко выбрать ATI». KTH уже давно использует роботизированные устройства смены инструмента ATI, поэтому переход на автоматическое соединение с помощью вспомогательных муфт ATI прошел успешно.
Дэйв Рид подтвердил работоспособность вспомогательного соединителя ATI GA2:«За последний год я сменил, наверное, сотни этих приспособлений, и у меня никогда не было проблем с системой ATI. Вы устанавливаете приспособление туда и нажимаете кнопку. , он вдавливается, зажимается, все штифты совмещены, вы не допускаете погнутых штифтов или разрывов воздуховодов. Это в значительной степени безупречный продукт. Он значительно упрощает жизнь."
Система управления автоматикой
- Повышение производительности с помощью автоматической сварки
- 4 способа улучшить характеристики роботизированной сварки
- Как роботизированная сварка меняет тяжелое производство
- Роботизированная сварка:предотвращение распространенных причин незапланированных простоев
- Автоматизированное производство муфт для бурения нефтяных скважин
- Роботизированные модули обеспечивают автоматизированное обслуживание деталей
- Стандартизированные ячейки FastArc упрощают освоение роботизированной сварки
- Мощные роботизированные сварочные модули могут стать отличным первым шагом
- Автомат для контактной сварки:эволюция
- Введение в автоматизированный сварочный аппарат сопротивлением