Исследование молекулярной динамики при наноразмерной обработке на основе наконечников:обзор
Аннотация
Подходы к наномеханической обработке (TBN) на основе наконечников оказались мощным и осуществимым методом изготовления микроструктур. Моделирование молекулярной динамики (МД) широко применяется в подходе TBN для изучения механизма, который не может быть полностью выявлен экспериментально. В данной статье рассматривается недавний научный прогресс в моделировании методом МД TBN. Сначала представлены методы создания имитационной модели для различных материалов. Затем обсуждается анализ механизма обработки для подхода TBN, включая анализ силы резания, анализ удаления материала и анализ дефектов в геологической среде. Наконец, приведены текущие недостатки и будущие перспективы метода TBN в моделировании МД. Надеюсь, что этот обзор может предоставить определенные ссылки для последующих исследований.
Введение
Технология микро / нанопроизводства широко используется в различных областях, включая окружающую среду, энергетику, биологию, медицину, национальную оборону и другие области, что играет все более важную роль в содействии национальному развитию и социальному прогрессу [1,2,3,4] . Для реализации высокоточного микро / нанопроизводства подход к механической обработке на основе атомно-силовой микроскопии (АСМ), известный как TBN, включает простое оборудование и операции, точность обработки в нанометрах с низкими требованиями к окружающей среде, и было показано, что он является мощным и осуществимым. подход к созданию микроструктур [5, 6]. До сих пор наноточки, линии / канавки, двумерные (2D) / трехмерные (3D) структуры и даже наноструктуры на изогнутых поверхностях, известные как основные компоненты наноустройств, уже были успешно изготовлены методом TBN [7].
Чтобы изготовить наноструктуру с более высокой точностью, необходимо глубокое понимание процесса обработки с использованием методов TBN. Многие ученые исследовали механизм подхода TBN с помощью экспериментов с различными материалами, такими как металлы [8], полупроводники [9, 10] и полимеры [11]. Однако дальнейшее экспериментальное исследование внутреннего механизма подходов TBN затруднено. Было продемонстрировано, что моделирование молекулярной динамики (МД) является мощным инструментом для исследования процесса наномеханической обработки, который не может быть полностью выявлен экспериментально [12, 13]. По сравнению с экспериментальным методом, метод МД может лучше объяснить микромасштабный механизм удаления материала и образования поверхности посредством анализа сил резания, напряженного состояния, диссипации энергии и топографии поверхности [12].
В прошлом некоторые ученые уже использовали технологию моделирования MD для исследования процессов TBN. Fang et al. исследовали влияние подачи скрайбирования и угла конуса на процесс нанолитографии [14, 15]. Исоно и Танака проанализировали влияние температуры, обрабатываемости и межатомных сил металлического никеля [16, 17]. Ян и др. исследовали эффекты геометрии острия в процессе литографии на основе АСМ [18]. В настоящее время некоторые новые процессы TBN были исследованы с помощью моделирования MD. Xiao et al. сравнил разницу между методом статической вспашки и методом динамической вспашки и обнаружил, что наноструктуры меньшего размера могут быть изготовлены с помощью метода динамической вспашки [19]. Geng et al. выполнили МД моделирования контролируемого нагрузкой наноцарапания путем непосредственного приложения постоянной нормальной нагрузки к зонду [20]. Чтобы изготовить наноканавки с более высокой плотностью, необходимо изучить минимальную подачу (MF). Ren et al. представили новый подход, который включает критерий от грубого к мелкому для определения MF с использованием моделирования MD [21]. Результаты показывают, что достигается высокая точность МП. Однако в предыдущей обзорной статье [12, 13, 22, 23, 24] эти новые достижения технологии моделирования МД, используемые для процесса TBN, не включены. Таким образом, в этом обзоре мы сосредоточимся на последних достижениях в области моделирования МД для методов TBN. Сначала обсуждаются технологии моделирования из различных материалов и новые методы обработки. Затем рассматривается механизм методов TBN, включая анализ силы резания, анализ удаления материала и анализ дефектов в геологической среде. Наконец, в этом обзоре также представлены оставшиеся проблемы и перспективы на будущее в моделировании TBN при МД.
Методы моделирования
Для получения точных результатов прогноза необходимо оптимизировать имитационную модель и соответствующую конфигурацию обработки. Имитационная модель в основном содержит атомную конфигурацию и потенциальную функцию. Атомную конфигурацию можно разделить на кристаллическую и аморфную структуру. Атомы в кристаллических материалах, таких как медь, железо, кремний и т. Д., Расположены регулярным и упорядоченным образом, а аморфные материалы, такие как полимеры, состоят из нерегулярных молекулярных цепочек. Поведение материала в наномасштабе представлено в моделировании МД с помощью потенциальных функций, и различные потенциальные функции были предложены и использовались для моделирования поведения материала в атомистических моделированиях. Кроме того, следует учитывать конфигурацию обработки, такую как различные условия обработки и подходы к обработке. В следующих разделах будут представлены методологии создания модели и конфигурации обработки.
Создание модели MD
Внутренняя атомная конфигурация кристаллических материалов различна, например, медь (гранецентрированная кубическая), железо (объемно-центрированная кубическая), титан (плотноупакованная гексагональная) и кремний (структура алмаза) [27, 28]. Большинство кристаллических материалов имеют монокристаллическую и поликристаллическую структуру. Монокристаллическое твердое тело имеет атомную структуру, периодически повторяющуюся по всему объему, при отсутствии дефектов. Дублирование элементарной ячейки во всех трех пространственных направлениях может легко установить модель монокристалла [13]. При создании атомарной модели MD следует учитывать различную ориентацию поверхности, которая может влиять на свойства обработки детали [29,30,31]. Поликристаллическая структура имеет структуру с различным размером зерен, построенную по методу мозаики Вороного [32]. Наноспутанный (NT) материал представляет собой особую структуру из поликристаллов, которая стала более важным объектом исследований благодаря своим выдающимся механическим свойствам, таким как сверхвысокая прочность, хорошая пластичность и высокая вязкость разрушения [33,34,35,36] . В данном обзоре в качестве примера приводится метод построения NT поликристаллической меди [25]:сначала строится мультислой, состоящий из множества монокристаллических слоев Cu одинаковой толщины, и между соседними слоями образуется TB. Во-вторых, рассчитывается угол каждого зерна. Наконец, поликристаллический NT с периодическими граничными условиями генерируется с использованием конструкции Вороного, которая учитывает многослойность и полученный угол зерен. На рисунке 1а представлены атомные конфигурации меди, включая одиночную кристаллическую Cu, поликристаллическую Cu и NT поликристаллическую Cu, в которых атомы окрашены общим соседом.
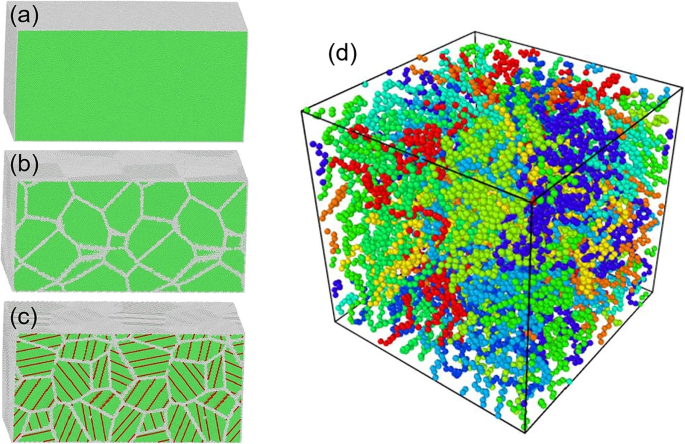
а Микроструктура монокристалла Cu. б Микроструктура нанополикристалла. c Микроструктура поликристалла НТ. Атомы окрашены в соответствии со значениями CNA, так как зеленый и белый цвета обозначают ГЦК и дефектные атомы [25]. г Модель уравновешенного единого атома аморфного ПЭ, модель окрашена в разные молекулярные цепочки [26]
В предыдущих исследованиях полимер моделировался с помощью общей крупнозернистой модели [37, 38]. Например, детали для создания модели полиэтилена (PE) представлены следующим образом [39]:(i) исходная PE-система с 10 молекулярными цепями была получена с использованием алгоритма самоизбегания случайного блуждания Монте-Карло [39]; (ii) первый атом каждой цепи сначала был вставлен в доступный участок решетки, а затем молекулярная цепь начала расти в определенном направлении на основе вероятностного ступенчатого способа в соответствии с длиной связи и незанятыми участками в ячейке. .; (iii) после того, как задана начальная плотность, определяется размер блока моделирования. В нашем моделировании размер исходного блока моделирования составлял примерно 80,06 × 80,06 × 80,06 Å 3 . для системы, состоящей из 10 цепей ПЭ. МД-модель ПЭ показана на рис. 1г.
Геометрия наконечника обычно сложная и изменчивая, включая форму конуса [40], треугольную пирамиду [18] и полусферу (тупую форму) [21], которая играет важную роль в процессе TBN. В частности, форма пирамидального инструмента в модели MD соответствует форме в процессе обработки AFM, а сферический инструмент соответствует абразивному зерну в процессе шлифования; таким образом, механизм обработки можно лучше объяснить, сравнив результаты моделирования с экспериментальными результатами. В большинстве случаев острие считается бесконечно жестким, что достигается сохранением относительного положения атомов постоянным и движением с постоянной скоростью [41].
Также очень важно выбрать подходящие функции потенциальной энергии, которые определяют достоверность результатов моделирования [21]. EAM - это многотельный потенциал, подходящий для металлических систем [24]. Это обеспечивает более реалистичное описание металлической когезии и позволяет избежать неоднозначности, унаследованной зависимостью от объема, которая используется для описания взаимодействия между металлическими атомами, такими как медь [42] и железо [43]. Доказано, что потенциалы Терсоффа [44] и Стиллингера-Вебера (SW) [45] особенно подходят для моделирования материалов с кубической структурой алмаза. Чтобы исследовать механизм Si в процессе TBN, необходимо наблюдать дислокационное скольжение и фазовое превращение в МД-моделировании. По сравнению с потенциалом Терсофф, потенциал SW не только обладает достаточной гибкостью для описания ряда различных конфигураций кремния, но также обеспечивает наиболее близкое соответствие с результатами зарождения дислокаций ab initio в бездефектном кремнии [46, 47]. Таким образом, потенциальная функция SW может иметь больший потенциал для описания взаимодействия между атомами кремния. Потенциалы аналитического порядка связи (ABOP), реактивного эмпирического порядка связи (REBO) и адаптивного межмолекулярного реактивного эмпирического порядка связи (AIREBO) представляют собой класс потенциалов, которые расширяют потенциальную функцию Терсофф в соответствии с приближением сильной связи и полагаются на фундаментальные величины [ 48]. Потенциал ABOP идеален для взаимодействий между атомами кремния и углерода, который используется для исследования деформации материала и поведения удаления в процессе SiC. Потенциал REBO особенно популярен при моделировании углеродных и углеродных нанотрубок. Модель AIREBO была разработана для преодоления недостатков потенциальной функции REBO, обеспечивая более точное приближение, чем у членов REBO, а также добавляла возможности моделирования более сложных взаимодействий [41]. Межмолекулярные и внутримолекулярные взаимодействия в образце полистирола описываются хорошо известным потенциалом AIREBO [49].
Большинство МД-моделирования было выполнено с использованием крупномасштабного атомно-молекулярного массивно-параллельного симулятора (LAMMPS) [50]. Некоторые сложные модели заготовок, такие как поликристаллический и поликристаллический материал с наноплетками, могут быть выполнены с помощью Атомска [51]. Конструкция полимеров, включая атомы, угол связей, несобственные и их различные типы, получается из файла данных, созданного в Material Studio (MS) [52]. И Open Visualization Tool (OVITO) [53], и визуальная молекулярная динамика (VMD) [54] являются полезными инструментами для визуализации модели или процесса обработки.
Используя моделирование МД, можно эффективно создавать различные модели материалов. Однако большинство моделей деталей имеют размер менее 50 нм × 50 нм × 50 нм, что может привести к отклонению от реальных результатов [40, 55, 56]. Кроме того, по-прежнему отсутствуют потенциальные функции, которые могли бы эффективно описывать некоторые материалы, такие как GaAs и Lu 2 О 3 . Таким образом, модели MD и связанные с ними потенциальные функции все еще нуждаются в оптимизации для более точного описания процесса моделирования.
Конфигурация обработки
В экспериментах по TBN режим управления нагрузкой обычно осуществляется путем приложения постоянной нормальной нагрузки к наконечнику. Было продемонстрировано, что этот режим имеет более высокую точность, особенно при проведении наномеханической обработки наклонных или изогнутых поверхностей. Однако многие МД-моделирование процессов TBN выполняется в режиме контроллера смещения, что может привести к расхождению между моделированием и экспериментом [18, 57]. Так, некоторые ученые выполнили МД-моделирование процесса наноцарапания, контролируемого нагрузкой, путем непосредственного приложения постоянной нормальной нагрузки к зонду [20, 58]. В процессах обработки его можно разделить на три части:стадия релаксации, стадия проплавления и стадия царапания. Кроме того, игла не полностью перпендикулярна заготовке из-за изгиба луча атомно-силового микроскопа (АСМ), подложки с углом наклона, а также шероховатости поверхности образца. Таким образом, нельзя пренебрегать эффектом наклона наконечника. Лю и др. выбрали наконечники с разными углами наклона, чтобы исследовать влияние наклона наконечника на результаты обработки [59]. Кроме того, износ наконечника является ключевым фактором для процесса обработки, который оказывает большое влияние на качество обработки. Наночастицы со смазкой водным слоем могут снизить износ наконечника, увеличить срок службы инструмента и гарантировать качество обработки. Однако механизм обработки, на который влияет смазка водным слоем, все еще недостаточно изучен. Чтобы решить этот вопрос, Ren et al. использовал метод моделирования методом МД для исследования влияния смазки водного слоя на результаты обработки монокристаллической медью [60].
Было доказано, что процесс одиночной царапины является простым методом изготовления наноканавки, но он имеет ограничение на размер канавки. Для увеличения размера наноканавки был представлен метод многопроходного царапания [62]. Geng et al. изучили разницу между однопроходным подходом и многопроходным подходом с помощью МД-моделирования и экспериментальных результатов [20]. Как однопроходный, так и многопроходный подходы можно рассматривать как литографию статической вспашки, которые проводятся в контактном режиме системы AFM. Однако статическая литография плуга может вызвать незначительный износ наконечника при выполнении процесса царапания на большом расстоянии. Техника обработки на основе режима нарезания резьбы называется литографией динамической вспашки, которая может снизить износ наконечника. На рис. 2 показаны схемы статической и динамической литографии вспашки на монокристалле меди соответственно. При статической вспашке алмазный наконечник сначала подавался вниз, а затем начинал вспашку в отрицательном направлении x ось. По окончании вспашки наконечник отводили вверх в исходное вертикальное положение. Для процесса динамической вспашки алмазный наконечник перемещался по синусоидальной кривой с заостренной амплитудой и периодом пика-впадины [19]. Основываясь на принципе обработки на основе режима нарезания резьбы, Sundaram et al. разработали новый метод наномеханической обработки с использованием АСМ, который называется наноударной обработкой с использованием вибраций с помощью свободных абразивов (VANILA). В этом методе АСМ используется в качестве платформы, а наноабразив вводится в суспензию между кремниевой заготовкой и вибрацией наконечника АСМ. Кинетическая энергия абразивов генерируется вибрацией наконечника АСМ и, как следствие, приводит к удалению материала образца в наномасштабе [61]. Схематическое изображение процесса VANILA показано на рис. 2б, в.
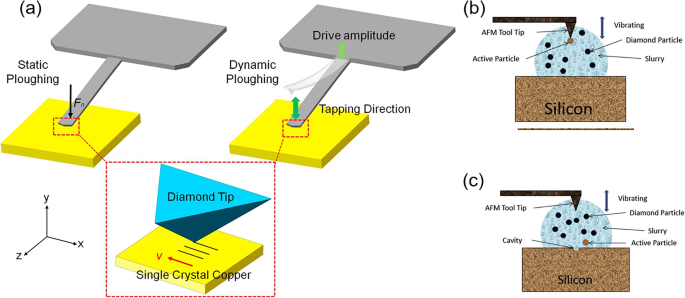
а Схема статической и динамической литографии вспашки на монокристалле меди [19]. б Кончик инструмента AFM ударяет по алмазной частице. c частицы алмаза ударяются о заготовку [61]
Анализ результатов моделирования
Анализ силы резания
Сила резания может четко отражать процесс удаления материала и эволюцию дефекта, что является важным физическим параметром для понимания явления резания [19, 63, 64]. Кроме того, сила резания тесно связана с мощностью резания и стойкостью инструмента, что может служить руководством для процесса обработки TBN [65]. В процессе TBN, сила резания в основном оценивается методом калибровки силы, но боковая сила не может быть получена этим методом [66, 67]. Используя технологию молекулярной динамики, изменение сил резания, включая поперечные и тангенциальные силы, можно наблюдать в реальном времени для всего процесса [68]. Кроме того, среднюю силу и равнодействующую силу можно также определить с помощью метода моделирования методом МД.
Хотя анализ изменения силы резания, можно отразить различие различных структур материалов и влияние параметров обработки на процесс TBN. Ли и др. обнаруженные более высокие силы для царапания на поликристаллической Cu по сравнению с монокристаллической Cu объясняются тем фактом, что анизотропия поверхностных зерен мало влияет между заготовкой и наконечником, когда наконечник переходит от одного зерна к другому зерну с различной ориентацией кристаллов, в то время как стабильное пластическое течение показано при удалении материала монокристалла Cu за счет его единой системы ориентации [25]. Также обнаружено, что сила резания для различных кристаллических структур увеличивается с увеличением скорости резания, потому что более высокая скорость наноцарапания дает больше стружки [69]. Напротив, изменение силы резания представляет собой неблагоприятное поведение в процессе царапания SiC, поскольку более высокая скорость может генерировать больше атомов аморфной кристаллической структуры, что делает материал SiC более пластичным и более легким для удаления [70]. Ян и др. исследовали технологичность бислоев Cu / Ni с помощью метода МД-моделирования и обнаружили, что сила бислоев Ni-Cu выше по сравнению с Cu, Ni и бислоями Cu-Ni, поскольку движению дислокаций препятствует граница раздела двух слоев, которая служит как барьер распространения [71]. Что касается аморфных полимеров, на характеристики механической обработки влияет скорость царапания в трех различных аспектах, а именно [72]:во-первых, большая высота скопления перед наконечником, возникающего при более высокой скорости, приводит к большей тангенциальной силе из-за большего сопротивление наконечнику. Затем более высокая скорость приводит к более высокой скорости деформации, что может вызвать деформационное упрочнение материала. Это также приведет к увеличению сил резания. Наконец, с увеличением скорости эффект термической мягкости позволяет более легко обрабатывать заготовку, уменьшая касательную и нормальную силы. В процессах механической обработки полимеров силы резания увеличиваются с увеличением скорости, что указывает на то, что эффект накапливания и упрочнения со скоростью деформации играет более важную роль в определении сил царапания. Помимо влияния материалов заготовки, геометрия наконечника также играет важную роль в процессе обработки [18, 73, 74]. Ren et al. исследовали влияние углов при вершине на силу резания с конической головкой. Установлено, что силы возрастают с увеличением углов при вершине из-за увеличения площади контакта между материалом наконечника и заготовкой [21]. Кроме того, коэффициент трения сильно уменьшается с полувершиной, в то время как твердость увеличивается [75].
Некоторые ученые также исследовали изменение силы резания в определенных условиях обработки. Ren et al. проанализировали корреляцию между толщиной водного слоя и царапающими силами. Изменение сил царапания с изменением толщины слоя воды показано на рис. 3. В отличие от процесса макроцарапания, когда слой воды в основном играет роль смазки и уменьшения силы резания, сопротивление слоя воды является преобладающим по сравнению со смазывающим эффектом и более толстый слой воды приводит к увеличению общих сил резания [60]. Кроме того, влияние наклона острия также обсуждается при анализе твердости (нормальная сила на атом) и коэффициента трения [59]. Результаты показывают, что нормальная твердость более чувствительна в прямом или обратном направлении по сравнению, и влиянием бокового наклона наконечника можно пренебречь. Кроме того, влияние наклона на нормальную силу является основной причиной изменения коэффициента трения, а влияние наклона на силу царапания намного меньше, чем влияние на нормальную силу.
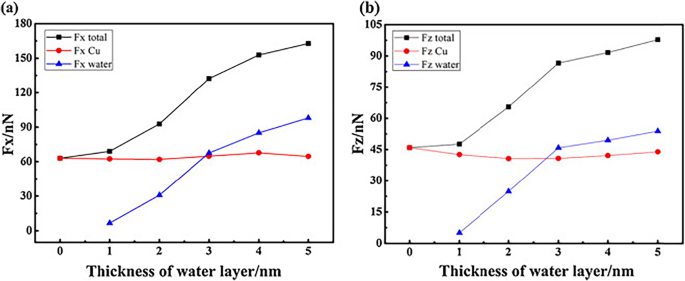
а Изменение средних сил царапания при изменении толщины слоя воды: a касательные силы и b нормальные силы [60]
Сравнивая силу резания при статической вспашке и динамической вспашке, можно выявить разницу в механизме. Сила резания в литографии динамической вспашки резко колеблется при периодическом постукивании алмазного наконечника, тогда как при статической вспашке наблюдаются небольшие колебания. Более того, среднее усилие обработки при динамической вспашке меньше половины от такового при статической вспашке, что указывает на меньший износ наконечника в литографии динамической вспашки [19]. В процессе динамической вспашки ориентация режущей кромки оказывает большое влияние на силу резания. Ян и др. объединили глубину канавки и усилие вспашки для сравнения эффективности обработки. Результаты показывают, что боковая сторона наконечника вперед имеет лучшую эффективность, поскольку у него аналогичная сила вспашки с силой ориентации наконечника лицом вперед, но в то же время более чем в два раза превышает глубину канавки [63]. С помощью анализа сил резания можно было бы дополнительно объяснить механизм процесса обработки TBN с различными материалами и условиями обработки. Более того, сравнение сил резания в различных режимах обработки может дать рекомендации по оптимизации процесса для подхода TBN.
Анализ состояния удаления материала
Анализ состояния удаления материала также является важным методом для выявления механизма подхода TBN. Удаление материала и топография в процессе обработки обычно наблюдаются с помощью сканирующего электронного микроскопа (SEM) и AFM. Однако морфология канавки и состояние удаления могут быть обнаружены только после обработки, а процесс удаления материала невозможно понять динамически. Недавно Zhang et al. использовали линейные режущие инструменты, напрямую подключенные к SEM, чтобы увидеть процесс формирования стружки при резке материала, в то время как этот метод сложен, и SEM следует модифицировать [76]. Таким образом, этот метод трудно обобщить. По сравнению с экспериментальным методом, метод моделирования методом МД может быть легко использован для исследования механизма удаления материала и образования поверхности в наномасштабе, а процесс обработки можно наблюдать в реальном времени с помощью метода МД.
Из результатов МД моделирования процесса TBN известно, что состояния деформации подразделяются на состояние вспашки и состояние резания. При движении наконечника атомы материала заготовки перед наконечником сжимаются, а затем накапливаются, образуя непрерывную стружку в состоянии резания. Одновременно с этим на левой и правой сторонах изготовленной канавки после прохождения иглы накапливаются некоторые атомы материала заготовки [57]. Сравнивая отношение состояния резания к состоянию без резания, мы можем определить, занимает ли состояние резания или состояние вспашки доминирующую роль, когда для царапания с разной глубиной царапания используется различный радиус наконечника [77]. В течение последних нескольких лет многие ученые дополнительно исследовали свойства материала в зависимости от состояния удаления материала. Например, монокристаллический материал проявляет анизотропию в процессе TBN, что оказывает большое влияние на удаление материала [20]. По сравнению с монокристаллическими материалами границы зерен имеют важное влияние на механические свойства поликристаллических материалов. Gao et al. обнаружили, что ориентация зерна, а не размер зерна, также является доминирующей при определении профиля скопления [78]. Кроме того, геометрия наконечника также сильно влияет на съем материала. Были выбраны три типа наконечника (конический, треугольный пирамидальный и полусферический), чтобы выявить влияние геометрии наконечника на состояние съема материала. Для конического наконечника наблюдается четкая зависимость от угла половины при вершине. Чем больше половина угла при вершине наконечника, тем больше объем стружки и улучшается гладкость царапающей поверхности, но требуется более высокая сила царапания, создается больший коэффициент трения и более высокая температура в заготовке, а также увеличивается подповерхностное повреждение [40]. Альхафез также исследовал влияние половины угла при вершине на образование скоплений [75]. Обнаружено, что при царапании с малым половинным углом при вершине наконечника наросты в основном накапливаются в прямом направлении, в то время как боковые наложения преобладают для условий обработки с большим половинным углом при вершине наконечника. Некоторые исследования были сосредоточены на треугольной пирамидальной вершине, которая согласуется с реальной геометрией острия в процессе обработки на основе AFM [19, 20, 63, 79]. В основном сравнивались три направления обработки:кромкой вперед, лицевой стороной вперед и боковой стороной вперед. В процессе обработки SiC состоянием удаления материала можно просто управлять, регулируя направление царапания инструмента. Направление царапания кромкой вперед может обеспечить более стабильный процесс, что может привести к большей точности размеров и однородности полученных канавок [79]. Однако состояние удаления материала полимеров более чувствительно к температуре по сравнению с металлическими или полупроводниковыми материалами. Во время процесса царапания локальная температура в зоне царапания выше температуры стеклования, что указывает на то, что заготовку в зоне царапания можно удалить пластично [72]. Zhan et al. исследовали микроскопические механизмы трения аморфного полистирола. Они обнаружили, что гибкость молекулярных цепей увеличивается с повышением температуры, что может позволить молекулярным цепям легче скручиваться и возвращаться в исходное состояние [56]. Du et al. обнаружили, что скорость обработки имеет большое влияние на результаты обработки полистирола. Внутрицепные изменения доминируют над остаточной деформацией образца полистирола при небольшой скорости обработки, в то время как межцепочечное скольжение более выражено при большой скорости обработки [80].
Как видно из приведенного выше обсуждения, большинство исследований в основном сосредоточено на сухих условиях, а не на жидкостях. Однако количество атомов, скопившихся перед инструментом, уменьшается, а заусенцы вдоль канавок не очевидны при большой толщине слоя воды, а шероховатость поверхности заметно уменьшается, что приводит к относительно гладкой поверхности. Можно объяснить, что водный слой действует как смазка для уменьшения области прилипания между инструментом и свежеобразованной поверхностью стружки и уменьшает силу сопротивления, проявляемую на границе лицевой поверхности стружки и инструмента. Прямым следствием этого является то, что качество поверхности значительно улучшается. По мере увеличения толщины водного слоя качество поверхности может постепенно улучшаться [60]. В некоторых новых подходах к обработке Shockly et al. исследовали влияние параметров (скорость удара, угол удара и рабочая температура) при наноударной механической обработке с использованием вибрации на формирование нанополости и обнаружили, что рабочие параметры имеют существенное влияние на глубину и ширину создаваемых нанополостей, как показано на рис. 4 [61]. Xiao et al. Установлено, что глубина и ширина канавки в процессе динамической вспашки меньше, чем в процессе статической вспашки, что означает, что наноструктуры с небольшими элементами могут быть изготовлены с помощью литографии динамической вспашки. Кроме того, размер канавок может контролироваться соотношением амплитуд привода в процессе динамической вспашки, и это демонстрирует, что изготовление канавок также можно контролировать [19].
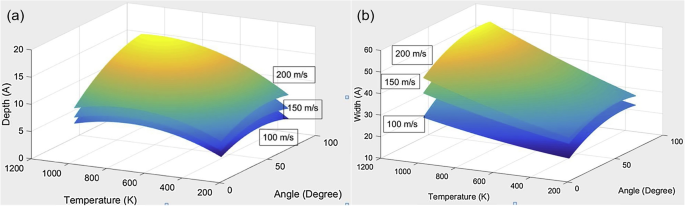
График множественной линейной регрессии для a глубина нанополости (скорость удара, угол удара и рабочая температура) и b ширина нанополости (скорость удара, угол удара и рабочая температура) [61]
В процессе удаления материала наконечник изнашивается. В большинстве предыдущих исследований наконечник определялся как твердое тело, что означает, что явление износа инструмента нельзя было наблюдать напрямую [13]. Многие ученые исследовали износ инструмента, изучая состояние съема материала, напряжение и распределение температуры [70, 77]. Чтобы отразить реальное явление износа наконечника в процессе обработки, Meng et al. установили наконечник как деформируемое тело и обнаружили износ наконечника в процессе обработки [81]. Результаты показывают, что форма алмазного абразивного износа в основном представляет собой адгезионный износ на начальной стадии и атомный износ на стадии стабильности обработки, а величина атомного износа абразива меньше зависит от скорости резания [ 81]. Примечательно, что отчетов об износе жала относительно мало. Надеемся, что использование деформируемого тела наконечника будет способствовать дальнейшему исследованию поведения наконечника при износе в процессе наномеханической обработки.
Анализ состояния съема материала обеспечивает эффективную поддержку для мониторинга процесса обработки в реальном времени. Однако из-за ограничения масштаба длины, как упомянуто выше, морфология обработанной поверхности и процесс удаления материалов могут быть проанализированы только путем качественного сравнения. It is difficult to predict the accurate processing results.
Defect Evolution Process Analysis
To obtain the information about the defects generated during the scratching process, TEM is usually employed after the FIB sample preparation techniques, which has several disadvantages, such as relatively complicated operation, high cost, and strong material dependence.
The MD simulation method can obtain the defects generated beneath the sample surface easily. Moreover, the defect evolution process during the scratching could also be observed by using the MD simulation approach, which could not be obtained by experimental method. Many available algorithms to extract defect types were presented, including common neither analysis (CNA) [82], centro-symmetry parameter (CSP) [83], slip vector analysis [84], Ackland-Jones analysis [85], etc. However, these methods are not suitable for tracing the propagation of dislocations, especially when a large number of dislocations are generated by tip scratching along certain direction, and we can no longer investigate what is going on inside the specimen using these methods [86]. Chen et al. presented slipping analysis for visualizing the atomic slipping process for material deformation, which could filter out those atoms that have slipped relative to its neighbor atoms during a specified period of time in the condition with large numbers of atoms [86]. By using this method, Xiao et al. investigated the slipping process during dynamic and static ploughing lithography [19]. The relationship between the cutting force and slipping process is shown in Fig. 5. It could be seen that for dynamic ploughing, the sample material mainly flows downwards and sidewards, whereas no obvious downwards material flow is observed in static ploughing process. In addition, the propagation of the dislocation is dependent on the orientation of the tip, leading to the various morphologies of the grooves. Dislocation extraction algorithm (DXA) is also a useful dislocation analysis tool to identify the lattice dislocation and to determine their Burger vector [87]. By using this method, Gao et al. investigated the behavior of the nanoscratching of iron. They found that a distinct reorganization of the dislocation network. At the beginning, the plastic zone grows linearly with the scratching length along the path. Then, the dislocation density decreases rapidly after some length dislocation reactions. Plastic activity then is concentrated only on the scratch front. Only few dislocations remain in the middle of the scratch. Vacancies in this zone are created by dislocation reactions. It is also found that point defects vacancies generated by dislocation reactions and deformation twining [88].
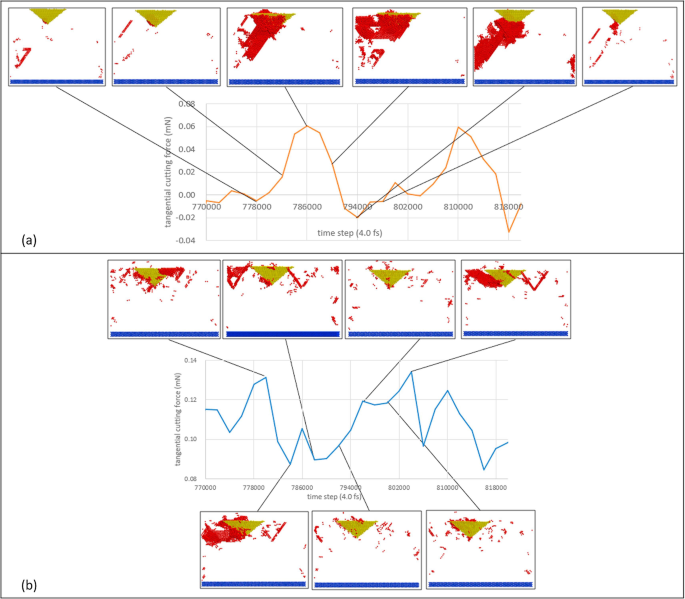
Slipping processes in a dynamic ploughing and b static ploughing [19]
For the polycrystalline materials, the deformation mechanism was mediated by dislocation nucleation within grain interior as well as grain boundary dislocations in polycrystalline material [43]. While the dislocation propagation is associated with the formation of nanovoids and interstitial clusters in the case of larger grain size, and the formation of twins at the grain boundary was dominating for smaller clusters. This behavior was attributed to the transition of dislocation movement from smooth (larger grain) to rough (smaller grain) during scratching process. Li further concluded the difference of material deformation mechanism about single crystal Cu, polycrystalline Cu, and NT polycrystalline Cu. The results show that the plastic deformation is mainly affected by the interaction between dislocations during scratching process in single crystal Cu; while for polycrystalline Cu both dislocations and GB dominate the plastic deformation; and the plastic deformation is controlled by the interactions of the dislocation, grain boundary (GB), and twin boundary (TB) accompanied with twinning/detwinning [25].
Furthermore, many studies focused on the MD simulation of the TBN process on the semiconductor materials, such as silicon, silicon carbide, gallium arsenide, and aluminum nitride. To investigate these brittle materials, phase transformation is also an important deformation mode in addition to dislocation slip [89]. The interaction between dislocation and phase transformation varies with the crystal orientation. The results indicate that prior to the “Pop-In” event, Si (010) undergoes inelastic deformation accompanied by the phase transformation from the Si-I to the Si-III/ Si-XII, which is not occurred in Si (110) and Si (111). While, the phase transformation from the Si-I to the bct-5 is the dominant mechanism of incipient plasticity for each crystallographic orientation, and dislocation nucleation is also an operating deformation mode in the elastic-plastic transition of Si (010). Dai et al. investigated the subsurface damage mechanism on single crystal silicon during TBN process. It is found that the evolution of crystalline phases is consistent with the distribution of hydrostatic stress and temperature [40]. SiC is also a kind of important semiconductor material, which has the similar property as silicon. The SiC material removal process is achieved through the phase transfer from zinc blended to amorphous structure with few hexagonal diamond structures. Higher scratching speed generates more amorphous structure atoms, fewer hexagonal diamond atoms, and fewer dislocation atoms due to larger impaction and less rearrangement time [90]. While Meng et al. found when the phase transition is not the dominant deformation mechanism, the Schmidt coefficient method can effectively predict the sliding motion of 3C-SiC during the TBN process (elastic sliding motion and dislocation slip motion) [79]. Moreover, Meng et al. further studied on the strain rate and heat effect on the removal mechanism of SiC. They found that the strain rate effect and the thermal softening effect directly affect the material removal amount and form of the subsurface damage (SSD). The influence of the thermal softening effect on the stress in the processing region under the condition of high strain rate exceeds that of the decrease in the growth rate of the dislocation generation speed. The polycrystalline SiC removal process is dominated by the amorphous phase transition. Furthermore, several hexagonal diamond structure atoms and dislocations are found in the GBs during the scratching. Higher scratching speed and larger depth of cut promotes more atoms to transfer into the amorphous structure due to larger impaction [81]. Compared with monocrystalline SiC, the microstructure in polycrystalline makes the SiC more soften by generating less normal scratching force and amorphous structure phase transition and thinner plastic deformation induced SSD [91]. Dislocation propagation and phase transition analysis could explain the mechanism in machining process. However, most researches focused on single crystalline materials and the materials with complex structure are rarely reported, which should be further studied.
Future Research Directions and Challenges
At present, the research on the TBN process through MD simulation is widely reported. However, there are still some limitations to be considered. Thus, future directions are discussed in this review.
- (1)
With the development of TBN methods, some novel technologies have been proposed in this field. For example, AFM tip-based nanomilling process has a broad prospect due to its great machining performance and size control properties [92, 93]. However, the mechanism of nanomilling has not been fully understood due to limitation of the detection equipment. With the use of MD simulation, it is hopeful that the variation of the cutting force, the dynamics change of defects, and the removal state of workpiece materials during rotating process of the tip. In addition, sample vibration-assisted nanoscratching method has not been reported yet. MD simulation approach could provide meaningful guidance in the early stage.
- (2)
Due to the limitation of the length and time scales, MD methods still could not fully describe the experimental process quantitatively. In some studies combining experiments and MD simulations, MD simulation approach could only qualitatively explain the experimental phenomena [19, 20, 94]. In particular, for some time-dependent materials such as amorphous polymers, the velocity of the probe has a significant impact on the removal state of polymers. Thus, in order to accurately predict the experimental process and quantitative analyze the experimental results, the improvement of algorithm and computing capability is indispensable.
- (3)
Many nanostructures have been achieved on polymer materials using the TBN method [95,96,97]. In particular, the mechanical machining process of polymer materials based on TBN method keeps the normal load constant so as to guarantee the accuracy of the machined nanostructures [98]. However, the reports of MD simulation of polymer in TBN process are limited until now. Moreover, thermal scanning probe lithography is developing in polymer, which has the potential to improve the machining accuracy of the TBN process. It is necessary to reveal the material removal mechanism of the polymer materials when conducting nanoscale scratching process with the mechanical-thermal effect.
Заключение
It is undeniable that MD simulations technology plays an increasingly crucial role in nanomachining process to reveal hitherto unknown phenomena [99]. This review concluded the recent progress in MD simulation of TBN method, and the above contents are summarized as follows:
- (1)
The establishment of MD models of various materials and related potential function were summarized. In particular, the modeling process of NT polycrystalline materials and amorphous polymers were discussed in this section. The accuracy of MD models is of great significant to the subsequent simulation results.
- (2)
The new technologies of TBN methods, including multi-scratching, dynamic ploughing, and VANILA were presented. With the help of MD simulation, the mechanism of these methods could be better understood. In particular, the essential difference between static ploughing and dynamic ploughing was revealed by MD method from the aspects of internal defects, morphology and cutting forces.
- (3)
The analysis of MD simulations in TBN process, including the cutting force, the state of material removal, and defect analysis are also summarized. Besides, some novel analysis methods like slipping analysis are also given. With these methods, the processing mechanism based on TBN approach is reviewed, which shows the materials dependence on the TBN machining process.
Сокращения
- TBN:
-
Tip-based nanomachining
- AFM:
-
Атомно-силовая микроскопия
- MD:
-
Молекулярная динамика
- NT:
-
Nanotwined
- PE:
-
Полиэтилен
- EAM:
-
Встроенный атомный метод
- SW:
-
Stillinger-Weber
- ABOP:
-
Аналитический потенциал заказа облигаций
- REBO:
-
Reactive Empirical Bond Order
- AIREBO:
-
Adaptive Intermolecular Reactive Empirical Bond Order
- LAMMPS:
-
Large-scale Atomic/Molecular Massively Parallel Simulator
- MS:
-
Material studio
- OVITO:
-
Открыть инструмент визуализации
- VMD:
-
Visual molecular dynamics
- VANILA:
-
Vibration-Assisted Nano Impact machining by Loose Abrasives
- SEM:
-
Сканирующий электронный микроскоп
- CNA:
-
Common neighbor analysis
- CSP:
-
Centro-symmetry parameter
- DXA:
-
Dislocation extraction algorithm
- GB:
-
Grain boundary
- TB:
-
Twin boundary
- SSD:
-
Subsurface damage
Наноматериалы
- Нано-анод и аккумуляторный анод:обзор
- Обзор применения биосенсоров и наносенсоров в агроэкосистемах
- Поверхностный эффект на транспортировку нефти в наноканале:исследование молекулярной динамики
- Моделирование молекулярной динамики и имитация алмазной резки церия
- Исследование новой червеобразной мицеллярной системы, усиленной наночастицами
- Противоопухолевое исследование наногелей хондроитинсульфат-метотрексат
- Исследование влияния направления удара на абразивный нанометрический процесс резания с помощью молекулярно…
- Исследование фрикционного поведения графена на золотых подложках в наномасштабе с помощью молекулярной дин…
- Низкий туннельный распад соединений одной молекулы алкана с концевым йодом
- Новое исследование изучает динамику производительности и движущие силы в обрабатывающей промышленности США