Исследование влияния направления удара на абразивный нанометрический процесс резания с помощью молекулярной динамики
Аннотация
Полировка абразивным потоком играет важную роль в современной сверхточной обработке. Ультрамелкие частицы, взвешенные в среде абразивного потока, удаляют материал в наномасштабе. В этой статье выполняется моделирование трехмерной молекулярной динамики (МД) для исследования влияния направления удара на процесс абразивной резки во время полировки абразивным потоком. Программное обеспечение для моделирования молекулярной динамики Lammps использовалось для моделирования резки монокристаллической меди с абразивными зернами SiC под разными углами резки (0 o –45 o ). При постоянном коэффициенте трения мы обнаружили прямую зависимость между углом резания и силой резания, что в конечном итоге увеличивает количество дислокаций во время обработки абразивным потоком. Наше теоретическое исследование показывает, что небольшой угол резания способствует улучшению качества поверхности и уменьшению внутренних дефектов в заготовке. Однако очевидной связи между углом резания и коэффициентом трения нет.
Фон
В современной сверхточной обработке технологии удаления материала играют важную роль в микроэлектронике, производстве микромеханических и оптических элементов. Потребность в миниатюрных устройствах с высокой точностью размеров и качественной поверхностью делает сверхточные процессы основным выбором в указанной области [1]. Более того, изменения поверхностных компонентов и подповерхностной структуры происходят в нанометровом масштабе. Технология полировки абразивными частицами играет важную роль во многих областях прецизионной обработки и, как и другие нетрадиционные технологии чистовой обработки, улучшает качество поверхности. Эта технология привлекла множество исследователей из-за ее важной роли. E. Uhlmann и другие исследователи сообщили о компьютерном моделировании полировки керамической поверхности абразивным зерном для разработанных экспериментов по проверке влияния различных факторов обработки на поток шлифовальной жидкости на режущие материалы [2]. Сехиджпал Сингх и другие исследователи используют технологию полировки абразивным потоком для резки медных и алюминиевых материалов. С помощью сканирующего электронного микроскопа они обнаружили глубокую бороздку на поверхности своей заготовки [3]. Г. Венкатеш и другие исследователи сообщили о технологии полировки абразивного зерна с помощью ультразвука для конической шестерни на сложной поверхности процесса чистовой обработки. В этом методе скорость абразивного зерна выше, чем у обычного потока абразивного зерна, который сталкивается с поверхностью заготовки, что может повысить эффективность обработки. Используя свои экспериментальные и теоретические методы, они обнаружили, что эта технология является одним из лучших вариантов для чистовой обработки зубчатых колес [4, 5]. K. Kamal et al. изучили реологические свойства абразивной жидкости в зависимости от вязкости абразивной жидкости, скорости сдвига и времени ползучести [6]. Однако большинство исследований полировки абразивным потоком основано на макроуровне, и очень редко внимание уделяется микроуровню. В процессе полировки абразивным потоком взвешенные частицы в среде будут течь вдоль материала с определенной скоростью под воздействием микроповерхности обрабатываемой детали (рис. 1).
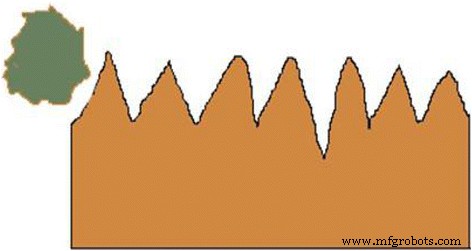
Эскиз абразивной резки заготовки. Все рисунки показывают влияние направления удара на процесс абразивной нанометровой резки с молекулярной динамикой. Фиг.1 представляет собой эскиз абразивной резки заготовки. В процессе полировки абразивным потоком взвешенные частицы в среде будут течь вдоль материала с определенной скоростью под воздействием микроповерхности обрабатываемой детали
Поскольку форма абразивных зерен нерегулярна, они имеют определенные края и углы, которые действуют на поверхность заготовки, подобно инструменту. Но процесс резки находится в атомном масштабе, что, очевидно, отличается от процесса удаления материала. Резка в наномасштабе включает в себя несколько нанометров или меньше поверхности материала, но очень трудно наблюдать этот процесс экспериментально. Таким образом, моделирование методом МД в качестве теоретического метода исследования очень полезно при изучении процесса нанометрической резки. Молекулярная динамика как метод компьютерного моделирования, в котором используется метод временной статистической механики для изучения взаимосвязи атомов для прогнозирования и анализа условий. Это также мощный инструмент для моделирования и понимания процессов удаления материалов. В литературе существует множество исследований, посвященных МД как инструменту для исследования прецизионной обработки. Олуваджоби и Чен проделали обширную работу по МД-моделированию наноразмерной обработки меди [7]. В своих исследованиях они исследовали различные параметры наномеханической обработки, такие как минимальная глубина резания, геометрия и межатомный потенциал [8]. Кроме того, результаты МД-моделирования в прошлом также были успешными для решения ряда проблем, связанных с нанометрическим процессом резки хрупких материалов, таких как кремний [9]. Komanduri et al. провели МД моделирование нанометрического вырезания монокристалла чистого кремния без дефектов, используя потенциал Терсоффа. Они изучили влияние переднего угла, ширины реза, глубины резания и заднего угла на съем материала и формирование поверхности [10]. Goel et al. исследовал атомистические аспекты пластичного отклика SiC в процессе нанометрической резки. Они обнаружили наличие перехода порядок-беспорядок sp3-sp2, который в конечном итоге привел к графитизации алмаза [11]. Cai et al. использовали MD для исследования резания кремния в пластичном режиме в наномасштабе. Они сообщили о режущей кромке инструмента и ее влиянии на напряжение сдвига в материале заготовки [12]. Арафин и др. обсудил влияние радиуса режущей кромки при резке кремниевой пластины в пластическом режиме на наноразмерном уровне [13]. Различные другие исследователи также выделили различные условия наномеханической обработки кремния с помощью моделирования методом МД. Эти исследования включают в себя силы резания, глубину резания, температуру, напряжение сдвига и другие параметры. Однако в этой области отсутствуют адекватные экспериментальные подтверждения. Qihong Fang et al. изучал механизм взаимодействия дислокаций в различных гетерогенных материалах с разным масштабом, а также дислокации и взаимосвязь между вязкостью материала и повреждением при разрушении. Они используют молекулярно-динамическое моделирование для изучения наноиндентирования трех различных кристаллических структур, включая монокристаллическую, поликристаллическую и поликристаллическую медь с нанодвойниками. С увеличением скорости царапания сила царапания и температура заготовки непрерывно увеличиваются из-за сильной пластической деформации и большого объема стружки, что приводит к скольжению дислокаций, скольжению ГЗ и двойникованию / расхождению двойников [14, 15].
Методы / экспериментальные
В эксперименте с абразивной полировкой заготовка обычно обрабатывалась абразивом SiC. После создания модели абразивных зерен SiC было выполнено молекулярно-динамическое моделирование заготовки с помощью программного обеспечения Lammps. Построена модель двух SiC абразивов, режущих монокристаллическую медь под разными углами. Имитационная модель процесса дробления монокристаллической меди абразивными зернами SiC показана на рис. 2.
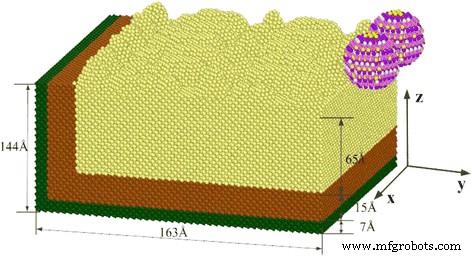
Имитационная модель абразивной резки SiC монокристаллической меди. На рис. 2 представлена имитационная модель монокристаллической меди, режущей абразивом SiC; мы построили два абразива SiC для резки монокристаллической меди. В эксперименте с абразивной полировкой заготовка обычно обрабатывалась абразивом SiC. После построения модели абразива SiC было проведено молекулярно-динамическое моделирование заготовки. Построена модель двух SiC абразивных режущих монокристаллов меди под разными углами
Размер модели показан на рис. 2, а количество смоделированных атомов составляло 159 020. Радиус абразива составляет 15 Å, общее количество атомов C и Si в абразивных зернах составляет 1406. Число атомов углерода и кремния составляет 681 и 725 соответственно. Число шагов релаксации установлено на 10 000 шагов для моделируемого равновесного ансамбля, шаги моделирования столкновений - на 100 000 шагов резания, каждый шаг симуляции составлял 0,001 пс, имитация резания, скорость абразивных частиц SiC в направлении резания 80 м / с. Зерна значения AFM анализа сталкиваются с обрабатываемой деталью во время полировки, абразивные зерна SiC сталкиваются с процессом резки под разными углами. В процессе резки абразивным потоком сила резания увеличивается с увеличением скорости резания, и величина силы резания напрямую влияет на эффект резания. Следовательно, выбор разумной скорости резки имеет важное значение для качества резки. Чтобы добиться высокого качества резки, мы выбрали скорость резания 80 м / с, поскольку она создает силу резания, которая может быстро разрушить взаимодействие между атомами заготовки [16].
При моделировании молекулярной динамики при низкой скорости резания, такой как 10 м / с, карты атомных смещений и картина того, как сила резания абразивных частиц карбида кремния и углы резания меняются в зависимости от размера шага моделирования, как показано на рис. 3 и 4. Поскольку скорость резания слишком мала, сила резания также недостаточна, что приводит к гораздо меньшей деформации и смещению решетки. В целом эффективность резки низкая, а качество резки относительно низкое. Напротив, когда скорость резки составляет до 80 м / с в микроскопическом эксперименте, химические связи между атомами меди могут быть разорваны быстро и эффективно, чтобы достичь цели мгновенной резки высокого качества. Следовательно, после всестороннего анализа скорость резания 80 м / с является приемлемой для моделирования.
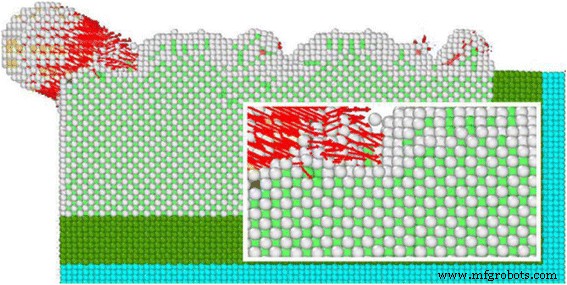
Атомное смещение с низкой скоростью
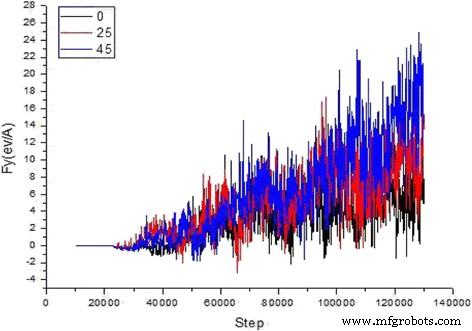
Связь между силой резания, углом резания и шагом моделирования
Чтобы смоделировать осуществимость и достоверность, мы выбираем разумную эмпирическую потенциальную функцию для рассмотрения межатомных потенциалов атомов. Согласно различным объектам, мы можем разделить потенциальную функцию на парную потенциальную функцию и потенциальную функцию многих тел. Две модели между монокристаллической медью и абразивными зернами описывают межатомные потенциалы атомов между ними с помощью потенциала Морзе [17], потенциал EAM используется для описания межатомных потенциалов атомов между атомами меди [18,19,20] и взаимодействие между частицами SiC описывается с помощью потенциала Терсоффа [21].
Во время процесса полировки направление столкновения абразивных зерен в среде является случайным; их траектории не проходят точно по поверхности заготовки. Во время процесса микрорезки направление резания абразивных зерен не всегда ортогонально материалу заготовки. Угол резания означает угол между направлением резания абразивного зерна и горизонтальной плоскостью. Положительно, когда частицы приближаются к поверхности детали. Эскиз угла резания показан на рис. 5.
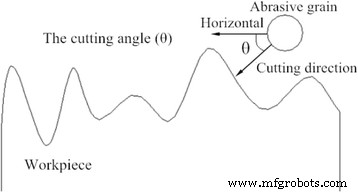
Эскиз угла реза. На рис. 5 показаны различные углы резания при резке абразивных зерен. Абразивное зерно с разных сторон режет материал заготовки, материал будет иметь производительность и качество обработки будет разным
В данном исследовании моделирование методом МД используется для моделирования мультиабразивов с различным направлением удара резанной монокристаллической меди. Как показано на рис. 5, угол резания составляет от 0 ° до 45 °, а поверхность медной заготовки шероховатая.
Результаты и обсуждение
Анализ столкновений при механической резке карбидом кремния
Воздействие абразива из карбида кремния на резку монокристаллического медного материала достигается за счет разрушения решеточной структуры монокристалла медного материала. Во время разрушения взаимодействия между атомами меди напряжение сдвига, создаваемое атомами C, Si абразивных частиц SiC на атомы Cu материала заготовки, было идентифицировано как сила резания, которая является важным физическим параметром для того, чтобы сила резания глубоко отражает процесс удаления материала заготовки из монокристаллической меди. Как обсуждалось ранее, существует большая разница между силой резания на микро- и макроуровне. Как правило, сила макрорезания представляет собой сумму силы резания и шлифования, тогда как при микрорезании сила резания создается за счет взаимодействия между абразивными зернами и атомами заготовки.
На рис. 6 мы показали изменения напряжения сдвига абразивных зерен в различных направлениях, влияние напряжения сдвига в разных направлениях и распределение сил резания по разным углам резания.
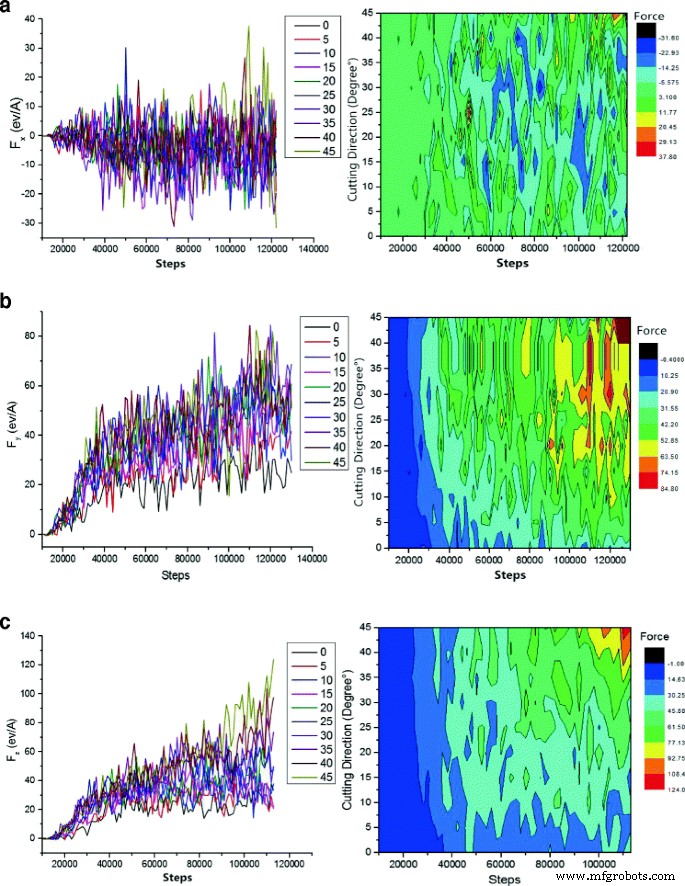
Как угол резания и размер шага моделирования влияют на силу резания. На рисунке 6 показано усилие резания SiC, угол резания и диаграмма шагов моделирования, с увеличением глубины резания количество разрушения кристаллической структуры увеличивается, максимальное значение колебания силы резания также становится больше. а [100] направление силы резания. б [010] направление силы резания. c [001] направление силы резания
Абразивные зерна карбида кремния режут и ударяют по монокристаллическому медному материалу под разными углами кромки, такими как [010] и [100]. Силы резания в направлениях [001] и [010] были поперечными силами. При дальнейшем моделировании глубина резания постепенно увеличивалась, что постоянно увеличивало силы резания в направлениях [001] и [010]. Однако до определенного предела эти силы колебались, как видно из рис. 6. Когда абразивные частицы перемещались по направлению к материалам детали, это полностью изменяло взаимодействие (от притяжения до отталкивания) между крайними атомами меди и атомами. SiC (Si и C). Первоначально при шлифовании материала заготовки силы резания были недостаточными из-за наличия сил отталкивания атомов меди. Для процесса чистовой обработки силы резания должны быть достаточно высокими, чтобы абразивные зерна могли легко разорвать химические связи в атомах меди и свободно двигаться. Кроме того, приращение глубины резания напрямую связано с атомными взаимодействиями. Когда атомы начали накапливаться, сила резания постоянно увеличивается до тех пор, пока абразивные частицы не войдут в заготовку, что требует постоянной силы резания. На этой относительно стабильной стадии колебания силы резания зависели от степени деформации решетки, реконструкции решетки, аморфного фазового перехода и образования стружки. По мере продвижения абразивных зерен вдоль направления резания на атом меди в ГЦК решетке действовала внешняя сила, что приводило к смещению атомов меди. Это смещение разрушает решетку ГЦК и превращает ее в новые решетчатые структуры с дислокациями. Аналогичная ситуация наблюдается и по силе резания. Нет положительной линейной корреляции между силой резания в направлении [010] и углом столкновения частиц. При столкновении под углом 0 °, 5 °, 10 ° и выше сила в направлении [010] была меньше и менее колебалась, чем сила в других направлениях резания. При резке под меньшим углом в основном удаляются заусенцы, поскольку заусенец может иметь диапазон высот 3,5 ~ 15 Å. При сравнении этих направлений друг с другом, если глубина резания относительно меньше, повреждение и деформация кристаллической структуры будут умеренными. Следовательно, во время всего процесса резания поперечная сила в направлении [010] сохранялась меньшей, как показано на графике кривой на фиг. 6b. На более позднем этапе моделирования сила резания достигла минимального значения 0 °. Также обнаружено, что сила резания имеет прямую зависимость от угла, как показано на фиг. 6c, что можно объяснить тем фактом, что когда скорость частицы достигает 80 м / с, достигается больший угол резания. С другой стороны, на том же этапе моделирования, чем больше скорость компонента в направлении [001], тем больше угол, тем глубже разрезаются частицы и тем больше атомных решеток разрушается. Однако между углом резания и силой резания была положительная корреляция. Когда зерна двигались в направлении [100], трение между атомами C, Si и Cu было источником режущей силы. Таким образом, сила резания не имела тенденции к постепенному увеличению. Однако при дальнейшем моделировании сила резания увеличивалась и колебалась, что было тесно связано с деформацией и реконструкцией решетки, а также с возникновением аморфного структурного фазового перехода. Прежде чем абразивные частицы могут разрушиться, происходит взаимодействие между атомами заготовки для удаления материала, что в конечном итоге постоянно увеличивает силу резания. При увеличении силы абразивного резания, превышающей критическое значение (сила связывания атомов), атомная решетка повреждается и связи диссоциируют, что приводит к образованию аморфной структуры. После этого сила резания упала до относительно низкого значения. Колебания силы резания возникали непрерывно в течение всего процесса обработки абразивным потоком, что связано с увеличением глубины резания и большим разрушением кристаллической структуры. Таким образом, делается вывод, что на этом этапе максимальное значение колебания силы резания было больше. Как показано на рис. 6b, красная область заняла большую площадь на более позднем этапе моделирования, что указывает на значительное увеличение силы резания. В то же время моделирования сила резания была меньше, когда угол резки был меньше 15 °, что означает, что небольшая часть кристаллической решетки была разрушена.
Энергетический анализ процесса ударной абразивной резки SiC
Полная термодинамическая энергия - это сумма полной потенциальной энергии и полной кинетической энергии в системе, которая показывает влияние работы, выполняемой абразивными зернами на заготовке. Влияние угла резания абразивного материала из карбида кремния на изменение энергии системы показано на рис. 7. В процессе резки монокристаллических материалов из меди с абразивными зернами карбида кремния работа, выполняемая абразивными зернами на материале заготовки, действует. двумя способами; одна часть преобразуется в кинетическую энергию, которая увеличивает тепло контакта атомов монокристаллической меди с частицами карбида кремния, функционирующими при полировке, другая часть преобразуется в потенциальную энергию, которая позволяет изменять внутреннюю структуру монокристаллической медной заготовки, деформацию решетки и выделение энергии решетки.
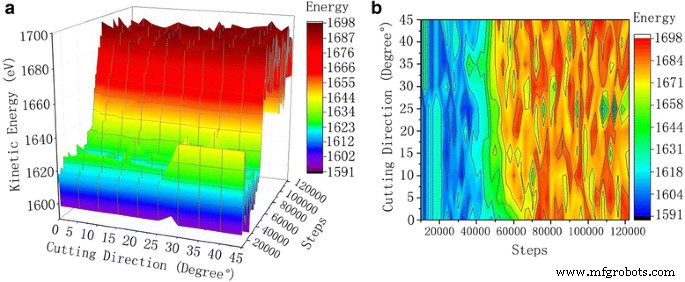
Кривая кинетической энергии атомов детали. На рис. 7 представлена кривая кинетической энергии для различных углов резания во время процесса резания. С увеличением количества шагов моделирования кинетическая энергия атомов колеблется в низком диапазоне, а затем в более высоком диапазоне колебаний. а 3D-кривая. б Контур
В процессе резки абразивного зерна заготовки из монокристаллической меди кинетическая энергия системы тесно связана с работой, выполняемой абразивом SiC над материалом заготовки. Вычисляя скорость частиц в системе в каждый момент времени, можно вычислить полную кинетическую энергию системы:
$$ K =\ sum \ limits_ {i =1} ^ N \ frac {1} {2} {m} _i \ left ({v} _ {\ mathrm {ix}} ^ 2+ {v} _ {\ mathrm {iy}} ^ 2+ {v} _ {\ mathrm {iz}} ^ 2 \ right) $$ (1)В формуле \ ({v} _ {\ mathrm {ix}} ^ 2 \), \ ({v} _ {\ mathrm {iy}} ^ 2 \) и \ ({v} _ {\ mathrm {iz}} ^ 2 \) представляют компонент скорости x , y , z направление атомов соответственно.
Кинетическая кривая на рис. 7 привела нас к выводу, что при увеличении шагов моделирования сначала кинетическая энергия атомов колеблется в низком диапазоне, а затем в более высоком диапазоне. При движении абразивных зерен между крайними атомами меди и атомами Si, C (SiC) обнаруживается дальнодействующее отталкивающее взаимодействие. Атомы меди в заготовке начинают получать кинетическую энергию и двигаться. Когда частицы карбида кремния контактируют с монокристаллом меди, температура атомов в контактирующей области увеличивается, что увеличивает тепловое движение атомов. Когда резка стабильна, кинетическая энергия атомов меди в материале передается и преобразуется в динамическом равновесном состоянии, а кинетическая энергия атомов колеблется в большом диапазоне.
Анализ кинетической энергии привел нас к выводу, что в процессе резки, когда частицы начинают контактировать с заготовкой, атомы в экструдированной области претерпевают деформацию решетки, координаты атомов меняются, и смещение изменяется вместе с кинетической энергией. Когда абразивные частицы попадают в монокристаллическую медь, пиковое значение кинетической энергии монокристаллической медной заготовки появляется, когда заготовка полностью входит в заготовку. Потому что кинетическая энергия и потенциальная энергия абразивных частиц просто взаимно преобразуются. Однако энергия всей системы не изменится, за исключением движущихся частиц, которые попадают в заготовку. Кроме того, движение частиц карбида кремния заставляет атомы детали двигаться одновременно с ними. Тепло, выделяемое при трении атомов, выделяется кинетической энергией и высвобождением энергии деформации из-за движения дислокации.
Преобразование тепла в кинетическую энергию рассчитывается по следующей формуле:
$$ \ frac {1} {2} {\ sum} _i {m} _i {v} _i ^ 2 =\ frac {3} {2} {nk} _B {T} _i $$ (2)В формуле n - количество атомов; vi представляет собой мгновенную скорость; к B - постоянная Больцмана, а T я это температура атомов.
Сила резания увеличивает атомную температуру области контакта абразива с материалом заготовки. При рассмотрении теплового движения атома и кинетической энергии атомов кинетическая энергия атомов меди частично увеличивается. Моделируемая система настроена на канонический ансамбль; общая температура системы колеблется в определенном диапазоне. Тепло, выделяемое при резке абразивных частиц, быстро передается слою атомов с постоянной температурой, поэтому общая кинетическая энергия системы изменяется очень мало.
Как видно из кривой потенциальной энергии на фиг. 8, при увеличении количества шагов моделирования потенциальная энергия среди монокристаллов атомов меди в заготовке также имеет тенденцию к увеличению. Когда абразив из карбида кремния контактирует с монокристаллом медной заготовки от начала до полностью стабильной резки, материал заготовки постепенно деформируется, а атомы меди смещаются, что приводит к искажению кристаллической решетки в кристалле. Это также приводит к появлению поля упругих напряжений, в котором энергия деформации увеличивается. Когда энергии деформации недостаточно для перегруппировки атомов материала, происходит дислокация атомов, которая увеличивает общую энергию системы. В отличие от потенциальных кривых от 0 ° до 45 °, мы можем видеть постоянство теплового движения атомов при постоянной температуре. Нет существенной зависимости между кинетической энергией атомов и углом резки абразивных зерен SiC. Кинетическая энергия атомов тесно связана с тепловым движением атомов. Однако изменение потенциальной энергии и полной энергии, очевидно, связано с углом резания абразивных частиц SiC. Величина атомной потенциальной энергии увеличивается с увеличением угла резания. Когда угол резания составляет от 0 ° до 20 °, наблюдается очевидное изменение потенциальной энергии. Однако, когда угол резания составляет от 25 ° до 45 °, потенциальная энергия остается такой, а общие кривые потенциальной энергии составляют от 0 ° до 20 ° угла резания. Как показано на рис. 9, тенденция общей энергии аналогична кривой потенциальной энергии. Суммарные значения энергии для всех углов резания очень близки друг к другу. Это связано с тем, что полная энергия равна потенциальной энергии и кинетической энергии системы, в то время как кинетическая энергия не изменяется в соответствии с углом резания во время процесса резания. Изменение кинетической энергии заготовки очень мало при разных углах резания. Следовательно, кривая изменения потенциальной энергии аналогична кривой полной энергии. Сравнивая диаграммы атомных смещений на рис.9, можно обнаружить, что при тех же условиях резания глубина резания в монокристаллической медной заготовке больше, когда угол резания составляет от 25 ° до 45 °, что можно отнести к увеличению смещения. атомов меди. Вдоль направления [001] частиц SiC образуется больше поврежденных атомов в решетке и дислокации. Энергия деформации, производимая за это время, выше, что приводит к высокой кривой изменения потенциальной энергии и кривой изменения общей энергии атомов детали.
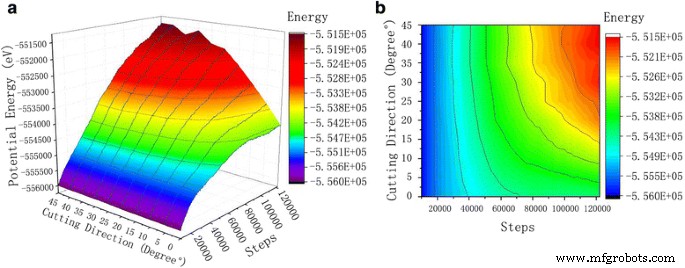
Кривая потенциальной энергии детали. Фиг. 8 представляет собой график изменения потенциальной энергии под разными углами резания во время процесса резания. С увеличением количества шагов для моделирования потенциал между монокристаллическими атомами меди экспоната имеет тенденцию к увеличению. а 3D-кривая. б Контур
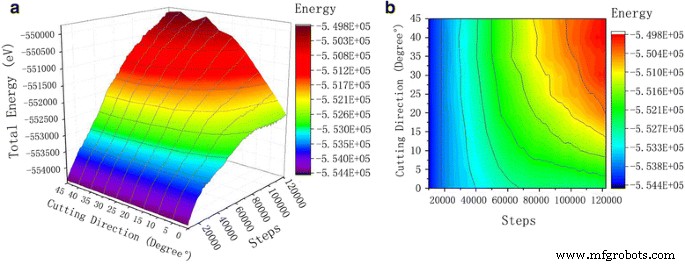
Кривая полной энергии. На рисунке 9 показана кривая полной энергии. В процессе резки SiC заготовки из монокристаллической меди, влияние абразивных зерен на заготовку проявляется в двух формах:часть из них преобразуется в кинетическую энергию, тепло атомов увеличивается, а локальная кинетическая энергия становится больше при полировке. область соединения монокристаллической медной заготовки и частиц SIC; другая часть преобразуется в потенциальную энергию, внутренняя структура монокристаллической медной заготовки изменяется, решетка деформируется, и энергия решетки высвобождается и превращается в потенциальную энергию. а 3D-кривая. б Контур
Анализ атомного смещения в процессе резания при столкновении абразивных частиц SiC
В процессе резки материала заготовки под разными углами абразивные зерна перемещаются вдоль направления резания, заставляя перемещаться атомы меди в заготовке. Из анализа направления движения заготовки полностью выясняется влияние абразивных зерен на материал заготовки, форма стружки и удаление материала. Согласно методу анализа валентных углов, предложенному Экланд-Джонсом, различная структура атомной решетки отмечена разными цветами для целей наблюдения и анализа. Плоскость ZOY выбрана для наблюдения за процессом резания отдельной частицы SiC, а диаграмма атомных смещений зоны резания увеличена, как видно из рис. 10.
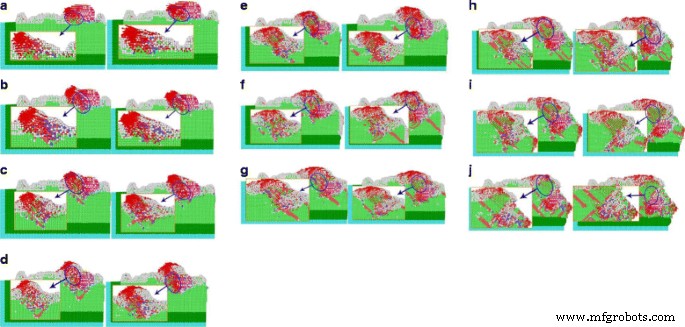
Различные углы резания вызывают смещения атомов. На рисунке 10 показаны смещения атомов под разными углами резания. Когда монокристаллические абразивные частицы SiC сталкиваются с заготовкой, режущей медь в разных направлениях, при резке абразивных зерен SiC, глубина резания увеличивается, поскольку скорость резания составляет 80 м / с, направление [001] Скорость движения равно v z =0,8 * грех θ , с увеличением глубины резания угла резания, [001] при том же угле резания увеличивается количество шагов моделирования, при этом глубина резания велика. а Смещение 0 °. б Смещения 5 °. c Смещение 10 °. г Смещение 15 °. е Смещение 20 °. е Смещение 25 °. г Смещение 30 °. ч Смещение 35 °. я Смещение 40 °. j Смещение 45 °. (атомный цвет: Структура HCP,
структура BCC,
Конфигурация FCC в виде белой аморфной структуры)
Когда монокристаллические абразивные частицы SiC сталкиваются с заготовкой, режущей медь в разных направлениях, глубина резания увеличивается по ходу процесса. Скорость в направлении резания составляет 80 м / с, где скорость компонента в направлении [001] составляет v z =0,8 ∗ грех θ . At the same simulation step, cutting depth increases with increasing the cutting angle. As shown in Fig. 10, there is an atomic position shift in both of the surface and interior of the workpiece material, contacting with the abrasive grains, where atoms of different lattice types are arranged and doped with each other. Due to the movement of these abrasive particles, the copper atoms accumulated at the tip of the abrasive grains, which results no cracks during abrasive particles cutting. It can be seen that the material removal mode of the abrasive particles is plastic deformation. At the same time, due to abrasive cutting, the atoms displacement in single crystal copper increases from 15° to 45°.
The number of the workpiece atoms along the abrasive grain motion direction also increases, and the atomic displacement is perpendicular to the direction of abrasive cutting. This part of the atomic displacement is due to that of the abrasive particles, change the cutting action to the extrusion upon the workpiece atoms. At cutting angle, the abrasive particles is between 0° and 10°, while the cutting depth is smaller than those of the 15° to 45°. Abrasive particles are performing mainly the cutting function, the extrusion of the workpiece atoms is marginal, and the number of atoms is small whose displacement direction is perpendicular to the direction of the abrasive grain motion. With the repeated cutting on the workpiece surface by numerous abrasive particles, the abrasive particles having large cutting angle produce deep pits on the workpiece material during the whole cutting process, while ones following smaller cutting angles will continue cutting along the cutting mark produced by the former. Under the combined action, the workpiece material is cut to a certain depth (micro-cutting) followed by whole abrasive flow polishing.
Dislocation Collision Analysis for SiC Abrasive Cutting
Dislocation is a special arrangement of atoms in crystal along certain crystal surface and crystal direction, or a boundary between the slip zone and the non-slip zone on the slip surface. Dislocation can be divided into edge dislocation, spiral dislocation, and mixed dislocation, among which mixed dislocation is most common. In the process of abrasive particle cutting, the single crystal copper workpiece is plastically deformed, the atoms move, and the crystal lattice breaks and reconstructs, which results in a large number of dislocations. The analysis for dislocation and bond angles at different incidence angles is shown in Fig. 10. In the simulation model of abrasive flow simulation, two abrasive particles are used for cutting the workpiece material. For ease of analysis, the generation and change of different dislocation lines in single crystal copper material, during cutting process and the different lattice structures in the cutting part are analyzed in the view of one single SiC particle on the YOZ surface, as shown in Fig. 11.
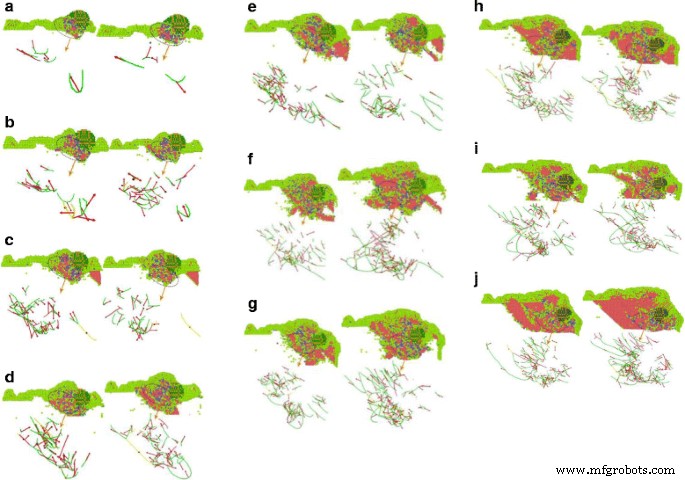
Different angles-bond angle dislocation line charts. Figure 11 represents the cutting dislocation line and the bond angle. As the repeated cuttings on the workpiece surface are done by the numerous abrasive particles during the polishing process, in the entire cutting process, the abrasive particles with larger cutting angle produce bigger pits, while the following abrasive particles with smaller cutting angles continue to polish along the cutting trace. Therefore, certain depth is done on the workpiece material and the whole micro-cutting of abrasive flow polishing is achieved. а Dislocation lines with 0° cutting angles. б Dislocation lines with 5° cutting angles. c Dislocation lines with 10° cutting angles. г Dislocation lines with 15° cutting angles. е Dislocation lines with 20° cutting angles. е Dislocation lines with 25° cutting angles. г Dislocation lines with 30° cutting angles. ч Dislocation lines with 35° cutting angles. i Dislocation lines with 40° cutting angles. j Dislocation lines with 45° cutting angles. (Note:the upper part of the key angle analysis, the figure in the atomic color: HCP
BCC
Amorphous structure
Abrasive grain; the lower part of the dislocation line diagram, the figure dislocation line color:
Stair-rod,
Shockley,
Hirth,
Perect,
Frank,
Burgers vectors)
Key angle analysis diagram of each cutting angle is shown in Fig. 11, where the sample from the interior workpiece simulation at time 60 and 70 ps, the atoms are colored individually according to different arrangement of atoms through BAD technology. To facilitate the analysis of the lattice changes in the cutting part, atoms of the FCC structure in the workpiece material are removed. By DXA techniques, different types of dislocations are marked in diverse colors:red arrow indicates the Burgers vector (Burgers vectors), green for Shockley partial dislocations (Shockley), light blue for the Frank partial dislocations (Frank), pink pole position for the pressure error (Stair-rod), and blue for the whole dislocation (Perfect).
As can be observed from the analysis of the bond angle portion in Fig. 11, a large number of dislocations and lattice deformations occurred under the impact of external cutting forces. The bond angle analysis shows that the internal HCP structure of the workpiece appears more clearly with increasing of cutting angle. On further simulations, the structure of HCP increases gradually. The silicon carbide particles continuously cut and squeeze the workpiece material at 80 m/s speed, resulting in a phase transition from the FCC structure to the HCP structure. During this phase transition, the atomic strain of the workpiece continues to increase. However, when the stress state of atoms of the workpiece has exceeded the threshold of thermodynamic phase transition, it turns to metastable state. As the strain increases, the HCP phase begins to nucleate and grow spontaneously, and the FCC lattice of copper undergoes absolute destabilization, which induces a sudden change in mechanical quantities. As the kinetic energy of the atom is directly related to the atomic temperature (formula 1), there is a saltatory augment in the kinetic energy change curve, as can be seen from Fig. 7. This is due to high strain energy, accumulated in the single crystal copper workpiece before the nucleation of HCP. The HCP structure increases the system temperature through metastable nucleation and partial stress release. Due to the abrasive cutting and extrusion, bonds of copper atoms in workpiece material break down which results in disorder. The original regular lattice structure is broken, where the partial copper atoms gradually change into disorder and form an amorphous structure. It can be seen from the bond angle analysis diagram that (Fig. 11) atoms with relatively disordered displacement tend to form amorphous structures at 60 and 70 ps, which is because of silicon carbide abrasive particles. At the same time, many atoms with the same displacement direction are transformed into HCP structures. Meanwhile, the particles shear downward and the atomic structure is rearranged due to the displacement of atoms in the original amorphous structure, results an amorphous structure of HCP. Atoms that have already been transformed into HCP structures, even before the next cut stage, change back into amorphous structure. As the cutting depth increases, the number of amorphous atoms near the abrasive particles also increases.
When the FCC crystal structure undergoes cutting by abrasive particles, a shear stress generates in atoms, which results in the displacement of atoms in the lattice and the arrangement of various lattice structures. In moving the atoms of workpiece, the rigid displacements of the atoms produce dislocations, also called as dislocation lines (Fig. 11). Dislocation line can be termed as the boundary between the slip zone and the non-slip zone, on the slip surface. According to the relation between the dislocation and the PATS vector, dislocation is parallel to the PATS vector, called the screw dislocations. The vertical ones are edge dislocations, and the mixed dislocations are neither parallel nor vertical. In Fig. 11, most of the dislocation lines are neither parallel nor vertical to PATS vectors, which are typical mixed dislocations. In the cutting process of abrasive particles, the dislocation line changes, moves and grows around the abrasive particles. The closer the particle, the greater the density of the dislocation line. Dislocation lines are also very dense, when the arrangement of atoms is complicated. The abrasive particles marked as orange, produce a large amount of HCP, BCC, and amorphous structures around them, which interlace and blend with each other to form dislocations that increases the internal energy of the crystals. When atoms arrange their self just like shown in Fig. 12b, possess maximum potential energy. While for the arrangement, shown in Fig. 12a–b, the atoms situate at the lowest potential energy position. The number of dislocation lines is directly related to the magnitude of strain energy of the crystal. The total strain energy of the unit length dislocation can be measured with the given formula:
$$ W=\alpha {Gb}^2 $$ (3)
Schematic view of dislocation changes. Dislocation is a special arrangement of atoms in crystals. It is the crystal in the atomic arrangement along a certain crystal face and crystal orientation occurred in a certain wrong line, and it is the boundary of the slip surface within the area where the slip has occurred and the area with no slip has occurred. In Fig. 12a - c , the relative displacement of the rigidity of the upper atom and the underlying atom produce dislocations, the upper atom belongs to the sliding region, and the lower atoms belong to the non-slip region, they are in the slip surface of the intersection line which is called dislocation line, that is, dislocation. Figure 12 is the process of dislocation generation and development
Where, α is the geometric factor (type dislocations, dislocation density) parameter related to, and generally 0.5 ~ 1.0; G is the shear modulus, and b is the slippage distance.
When the workpiece material is being cut, particles break the atomic arrangement and the lattice reconstructs, which constitutes, macroscopically, the plastic deformation of the workpiece material. In the process of plastic deformation, the dislocation was supposed to escape from the crystal and decrease the dislocation density. However, this dislocation density increases due to dislocation propagation. There are many ways of dislocation multiplication and the main one is the Frank–Reed dislocation source theory, of which the growth mechanism is shown in Fig. 11. As illustrated in Fig. 11, the density of the dislocation line increases markedly from 60 to 70 ps when the cutting simulation proceeds, change both the number and shape of dislocation lines in accordance with Frank–Reed dislocation source theory. At simulation time of 60 ps, there are many long Shockley dislocations. But after another 10 ps simulating, the long Shockley dislocation line becomes less and shorter. The original straight dislocation lines turn into bent, which is especially evident near the abrasive grains. From formula 3, the strain energy of the dislocation is proportional to b 2 . From the viewpoint of energy, the dislocations with the smallest b in the crystal should be most stable with low energy; however, dislocations with larger b will break down into ones. In addition, the energy of the dislocation is valued by the unit length of the dislocation line. Given the shortest line between two points is the straight, the strain energy of straight dislocation is lower than that of the bent one, means straight dislocations are more stable. Frank–Reed dislocation source theory argued that the long dislocation line becomes shorter and breaks down into smaller dislocations, thus decreasing the strain energy of the crystal.
Analysis for Friction Coefficient Between Workpiece Surface and Abrasive Particles
To quantitatively disclose mechanical properties and surface effect of SiC abrasive cutting single crystal copper material, the tangential force ([010] direction) and normal force ([001]direction) on the cutting surface are further analyzed. The friction coefficient can be defined as the ratio of the tangential force to the normal force, with the formula below:
$$ f=\frac{F_y}{F_z} $$ (4)Figure 13 shows the variation of friction coefficient along different cutting angles during abrasive cutting. The change of friction coefficient can be divided into two periods. Period I, when the cutting distance is less than half of the size of the abrasive particle, the friction coefficient fluctuates violently in certain range due to surface effect of the material; while in period II, all the friction coefficients fluctuate in very small range, and the friction coefficients remains steady state at different angles. However, at cutting angle of 5°, there is a small amount of abnormal fluctuation at the end of simulation. Moreover, in period I, abrasive particles contact the workpiece atoms to the abrasive grains enter into the workpiece of half abrasive diameter (shown in Fig. 13b), the cutting movement distance reaches 7.5 Å. In Fig. 6, the cutting force change curve shows that the tangential force and normal force are in an oscillating phase during period I. Since the friction coefficient can be characterized as the adhesion among atoms in the contact surface and is related to the two atoms contacting with each other, regardless of the cutting mode, which can interpret the phenomenon that change of cutting angle does not cause significant change of friction coefficient, as shown in Fig. 13a.
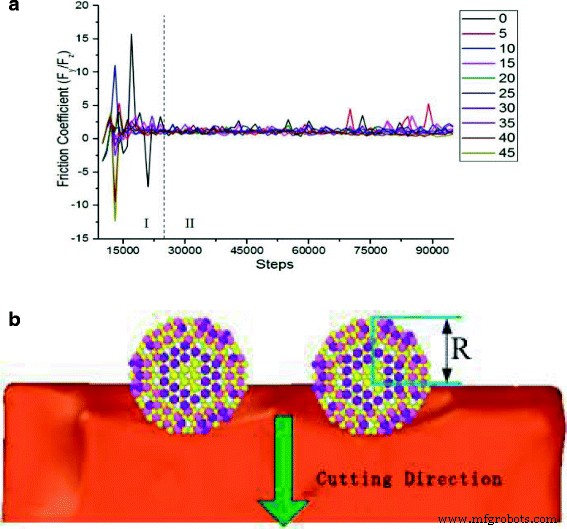
Friction coefficients of different cutting angles. Figure 13 is the changes of the frictional coefficients during SIC particles cutting single crystal copper from different angles. The change in cutting angle did not cause significant changes in friction coefficient. It described two kinds of coefficient of friction in contact with the relevant atoms in the cutting process, regardless of the cutting mode. а Friction coefficient variation curve with cutting angle. б Instantaneous structure when SiC abrasive grains move 7.5 Å
Выводы
The micro cutting simulation of single crystal copper by SiC abrasive particles is achieved during abrasive flow polishing. Comprehensive analysis of the SiC abrasive cutting reveals that when SiC abrasive particles cut at angle from 0° to 15°, cutting forces in along Y and Z direction are relatively small and tend to stay steady. A larger cutting angle results more dislocations, which brings about larger grooves damaging of the workpiece material. In the process of cutting, it is necessary to avoid more dislocations, which has an immediate adverse effect on the performance of all aspects of crystal material. Therefore, a cutting angle of 0° is better than other angles. Considering the amount of dislocation produced, or the change of cutting force and energy in the cutting process; cutting with small or medium angles is not only beneficial for improving surface quality but reduce the internal defects.
Наноматериалы
- Поверхностный эффект на транспортировку нефти в наноканале:исследование молекулярной динамики
- Моделирование молекулярной динамики и имитация алмазной резки церия
- Токсичность наночастиц CoFe2O4, покрытых ПЭГ, с лечебным эффектом куркумина
- Исследование фрикционного поведения графена на золотых подложках в наномасштабе с помощью молекулярной дин…
- Зависимости упругих свойств монокристаллов тантала от температуры и давления при растягивающем нагружении:…
- Синтез и исследование in vitro двухрежимного зонда, нацеленного на интегрин αvβ3
- Теплопроводность двух типов двумерных аллотропов углерода:исследование молекулярной динамики
- Гидроабразивная обработка и резка
- Преимущества процесса лазерной резки
- Абразивная резка плюсы и минусы