Убедитесь, что конструкции для литья под давлением готовы к производству с помощью этого контрольного списка
Литье под давлением позволяет производить большие объемы идентичных деталей по низкой цене за деталь. Процесс включает в себя впрыск расплавленного материала в прочные металлические формы через сопло под давлением, выброс детали после затвердевания материала и повторение. Широкий спектр предметов повседневного обихода, в том числе бутылки с водой, пластиковые игрушки и корпуса для электроники, изготавливаются методом литья под давлением. В то время как термопласты и термореактивные материалы являются наиболее распространенными материалами, используемыми при литье под давлением, металл также может быть отлит под давлением.
Когда вы изготавливаете деталь методом литья под давлением, вам необходимо учитывать ряд переменных, влияющих на качество и функциональность конечного продукта. Существует множество причин, по которым деталь, изготовленная литьем под давлением, может выйти из строя, включая линии потока, утяжины и деформацию, но вы можете избежать большинства проблем, следуя нескольким ключевым принципам проектирования.
Здесь, в Fast Radius, мы каждый день работаем с клиентами над их деталями, изготовленными методом литья под давлением. Инженеры часто обращаются к нам с отличными конструкциями деталей, которые необходимо скорректировать, прежде чем их можно будет эффективно изготовить. Наши специалисты по проектированию для производства (DFM) оценили и скорректировали тысячи конструкций деталей, а также определили и собрали наиболее распространенные проблемы, с которыми они столкнулись. Исправление этих распространенных ошибок в вашем проекте может предотвратить дорогостоящие ошибки и сэкономить много времени при пересмотре проекта.
Перед отправкой проекта детали для литья под давлением проверьте его на соответствие этому списку правил проектирования:
Используйте соответствующие углы уклона
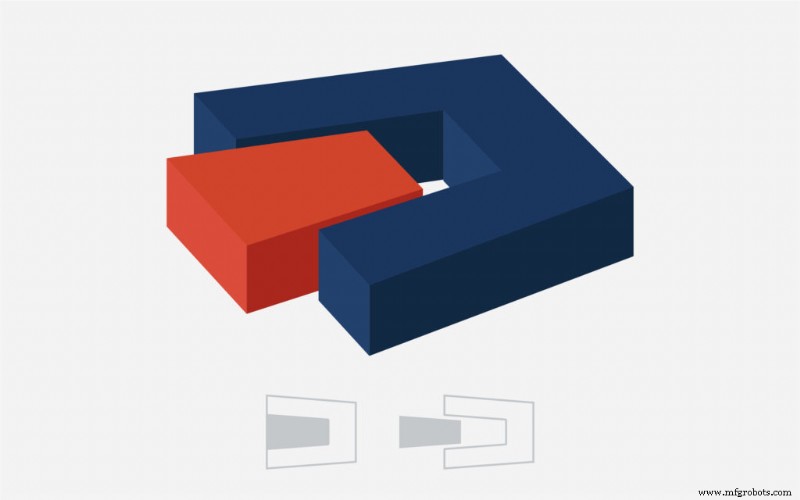
1,5–2 градуса уклона обычно являются безопасным минимумом для большинства деталей.
Углы уклона относятся к плавному конусу, добавленному к поверхностям отлитой под давлением детали, который совпадает с направлением вытягивания, что позволяет извлекать деталь из формы без повреждения трением или всасыванием.
Требуемый угол наклона детали зависит от нескольких факторов, в том числе от толщины стенки, степени усадки материала детали, глубины вытяжки и того, потребуется ли для детали обработка поверхности или текстурирование во время постобработки. Хотя средний уклон должен увеличиваться на 1 градус на каждый дополнительный дюйм глубины детали, 1,5–2 градуса обычно являются безопасным минимумом для большинства деталей.
Поддерживайте по возможности одинаковую толщину стенок
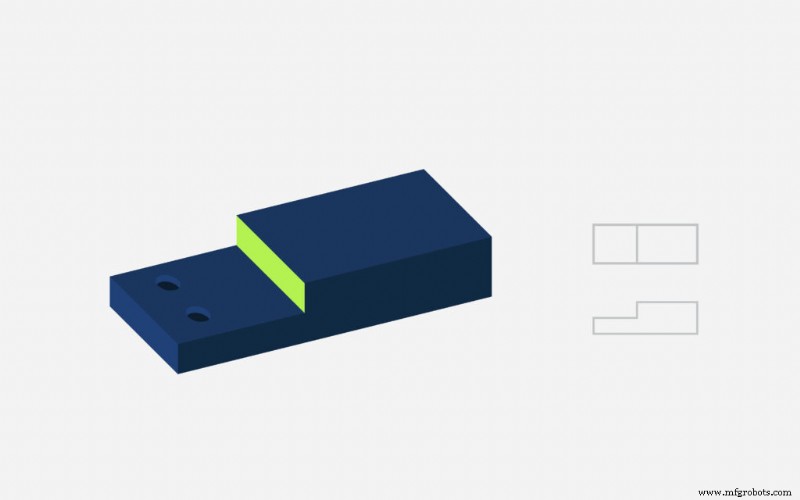
Если возможно, компоненты, полученные литьем под давлением, должны иметь одинаковую толщину стенки по всей детали. Различия в толщине стенок могут привести к тому, что впрыснутый материал будет остывать с разной скоростью, что может привести к утяжкам, пустотам и деформации.
Как правило, толщина стенки от 1,2 мм до 3 мм идеальна (хотя возможны некоторые отклонения в зависимости от материала). Толщина стенки почти всегда должна быть менее 5 мм, так как более толстые стенки увеличивают продолжительность производственного цикла, а также могут отрицательно сказаться на механических свойствах детали.
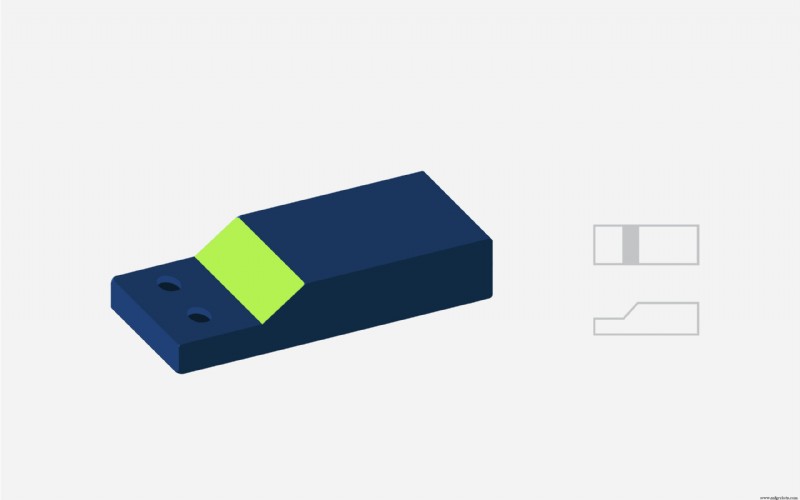
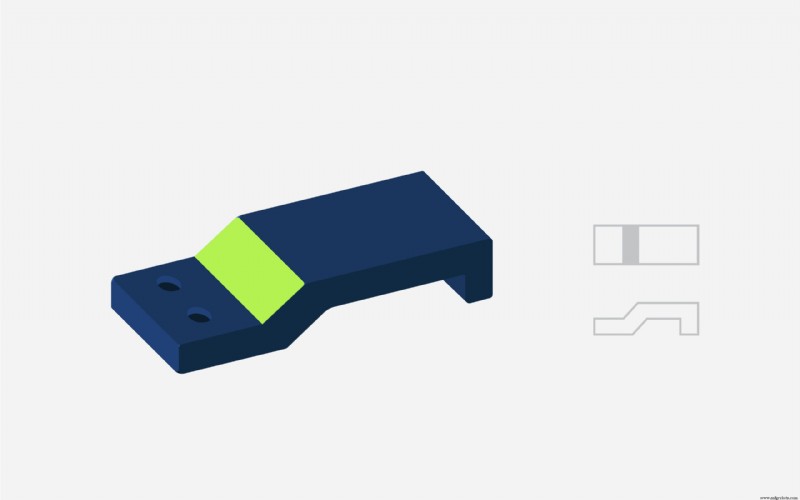
Если деталь требует изменения толщины стенки, то следует сделать переход между сечениями как можно более плавным. Вы можете сделать это, включив фаски (наклонные углы или края) или скругления (закругленные углы или края) в конструкцию детали, которые помогают гарантировать, что порция расплавленного пластика полностью заполнит форму, полностью и равномерно остынет и предотвратит коробление или -равномерная усадка.
Как правило, длина перехода между секциями с разной толщиной стенки должна быть в 3 раза больше изменения толщины стенки (например, если толщина стенки уменьшается на 1 мм, переход должен происходить через 3 мм).
Избегайте подрезов
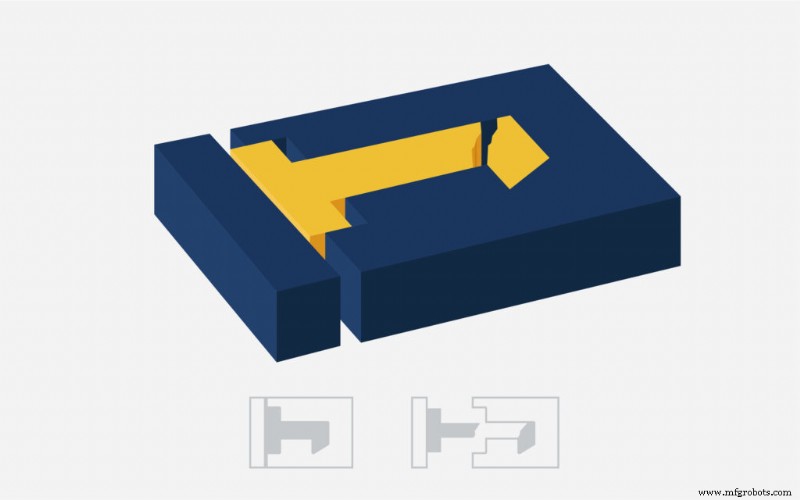
Поднутрения — это утопленные или выступающие поверхности или элементы, такие как резьба, канавки или защелки, которые предотвращают выталкивание детали из формы одним однонаправленным усилием без повреждений. Можно избежать поднутрений, ориентируя элементы параллельно линии рисования или включив действия в конструкцию пресс-формы.
Скруглите острые края и углы
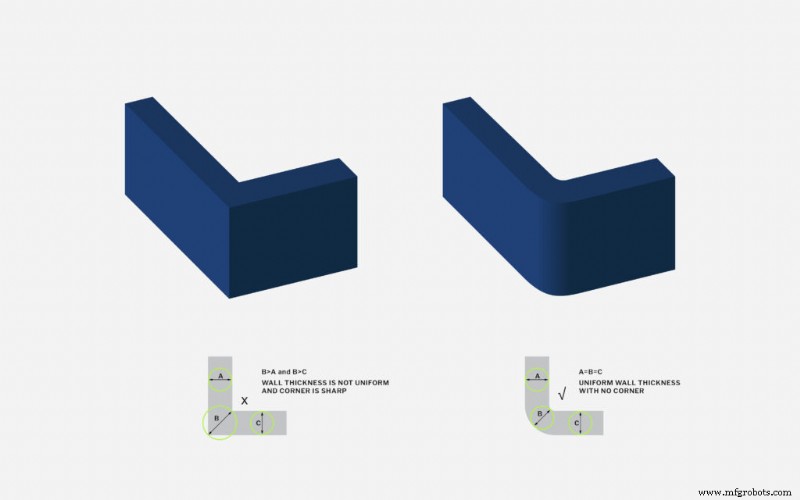
Когда это возможно, дизайнеры и инженеры должны выбирать круглые элементы вместо острых краев и углов. Для заполнения кромок требуется дополнительное давление, что затрудняет эффективное и равномерное попадание дроби в форму. Острые края также имеют тенденцию цепляться за пресс-форму во время выталкивания, увеличивая риск повреждения деталей и появления дефектов. Вы можете избежать обеих этих проблем с помощью закругленных внутренних и внешних углов.
Внутренние углы или те, где части стен соприкасаются с полом, должны иметь радиус не менее 50 % толщины прилегающей стены. Внешние углы или углы в верхней части стенок должны иметь радиус 150% от прилегающей стены, чтобы позволить пластику течь более эффективно и действенно. Это также помогает свести к минимуму остаточное напряжение и растрескивание.
Основание всех вертикальных элементов внутри детали (таких как бобышки, ребра или защелки) также должно быть закруглено. Радиус бобышки должен составлять 25 % от прилегающей стены с минимальным радиусом 0,015 дюйма (или 0,381 мм).
Стратегически расположите линии разделения
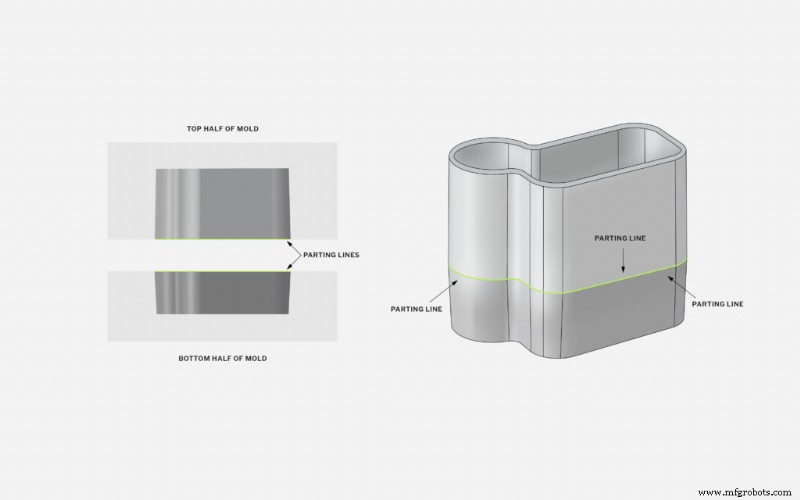
Физическая метка, известная как линия разъема, появится там, где встречаются две половины пресс-формы. Во многих случаях линии разъема можно легко увидеть и почувствовать, но это больше, чем эстетическая проблема. Расположение линии разъема определяет, как открывается пресс-форма (и, следовательно, направление, в котором вам нужно добавить уклон к элементам детали), и это может повлиять как на стоимость оснастки пресс-формы, так и на любую необходимую постобработку.
Часто можно улучшить внешний вид и функциональность детали, разместив пробор вдоль края, а не на плоской поверхности. Это помогает скрыть шов, а также снижает вероятность заусенцев (избыток материала вокруг места соединения формы).
Рассмотрите размещение выталкивающего штифта
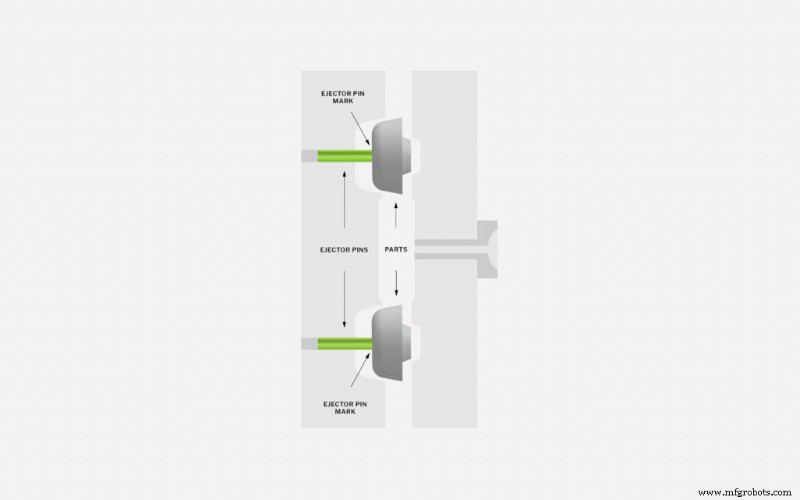
Для правильной работы выталкивающих штифтов требуются плоские поверхности или прокладки, расположенные перпендикулярно направлению движения штифта. Размещение и количество штифтов должны определяться формой детали, углами наклона, текстурой боковой стенки и глубиной стенки — все это влияет на то, как деталь будет цепляться за стенки пресс-формы.
Выбор материала также должен учитываться при размещении или размере штифтов. Например, более липкие смолы, как правило, требуют большего усилия для выброса. Аналогичным образом, для более мягкого пластика, скорее всего, потребуется либо большее количество штифтов, либо более широкие штифты, чтобы эффективно распределять усилие выброса и не повредить деталь.
Оптимизировать размер опорных ребер
Ребра часто используются для усиления части стенок в ситуациях, когда две части стенок сходятся под углом 90 градусов или когда длина определенной секции уменьшается за счет толщины стенки секции.
Важно отметить, что более толстые ребра не обязательно означают большую поддержку — на самом деле, слишком толстые ребра часто приводят к утяжкам. Толщина основания опорных ребер должна составлять не более двух третей толщины прилегающей стены.
Учитывайте толщину стенок пресс-формы
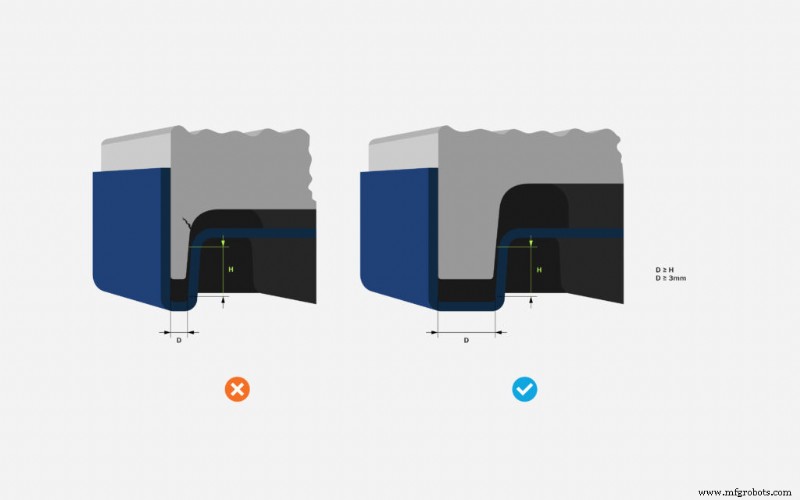
Толщина стенок пресс-формы — еще одно важное соображение, которое в первую очередь будет определяться расстоянием между деталями. Убедитесь, что вертикальные элементы, такие как ребра и выступы, не расположены слишком близко друг к другу, к разделяющим стенкам или тонким областям, так как это усложняет процесс охлаждения.
Толщина стенки пресс-формы также может повлиять на стоимость оснастки. Большинство форм для литья под давлением изготавливаются с помощью станков с ЧПУ, и более тонкие стенки металла в форме труднее правильно обрабатывать. Более тонкие стенки также приводят к сокращению срока службы пресс-формы.
Хотя минимально допустимая толщина стенок пресс-формы определяется физическими и механическими свойствами материала детали, обычно допускается зазор в 3 мм между элементами детали.
Эффективное и эффективное проектирование деталей, изготовленных методом литья под давлением
Ошибки в дизайне дорого обходятся. Переделка инструмента для исправления ошибки проектирования может отбросить команду разработчиков на несколько недель назад и стоить тысячи долларов. Хороший партнер-производитель поможет вам избежать дорогостоящих изменений с помощью DFM, но этот процесс также увеличит ваши сроки. Проверка конструкции на наличие проблем, описанных в этом руководстве, перед отправкой ее партнеру-производителю поможет вам быстрее получить более качественные детали.
Есть много вещей, которые могут пойти не так при литье под давлением, поэтому вам нужно найти партнера, которому вы можете доверять, чтобы получить ваши детали правильно. Здесь, в Fast Radius, мы здесь, чтобы облегчить вам жизнь, и мы заинтересованы в успехе вашего проекта. Свяжитесь с нами сегодня, чтобы начать работу над вашим следующим проектом по литью под давлением.
Чтобы узнать больше о литье под давлением — от выбора материала до различий между одногнездными и многогнездными пресс-формами и того, как мы использовали этот процесс для производства масок для лица, которые борются с распространением COVID-19, — посетите учебный центр Fast Radius. .
Готовы создавать детали с помощью Fast Radius?
Начать цитатуПромышленные технологии
- Литье под давлением с использованием технологии PolyJet
- Интерфейс шестиосных роботов с прессами для литья под давлением
- Как ведущие компании по литью под давлением расширяют возможности с помощью цифрового маркетинга
- Что такое дефекты литья под давлением и как их предотвратить:10 дефектов пластиковых деталей
- Микроформование с полиуретанами
- Что такое реакционное литье под давлением
- Литье против литья под давлением
- Литье под давлением против реактивного литья под давлением (RIM)
- Литье под давлением против реакционного литья под давлением
- Каковы преимущества литья пластмасс под давлением?