Интервью с экспертом:президент Sintavia Дуг Хеджес о достижении серийного производства с помощью 3D-печати на металле
Sintavia - независимый производитель, предоставляющий услуги аддитивного производства металлов для таких важнейших отраслей, как аэрокосмическая, оборонная и нефтегазовая. .
Сосредоточившись на серийном производстве металлических деталей с использованием аддитивного производства, компания предоставляет уникальные комплексные услуги, которые включают не только производство и постобработку, но и испытания. , металлургия и определение характеристик порошков в собственной лаборатории.
Недавно Sintavia объявила о своих планах по расширению, переехав в новый объект площадью 55 000 квадратных футов, который уделяет особое внимание производству.
На этой неделе мы рады поговорить с президентом Sintavia Дугом Хеджесом, чтобы обсудить, как компания производит высококачественные сертифицированные металлические детали, почему AM идеально подходит для аэрокосмической промышленности и для чего индустрия AM может ускорить внедрение технологии.
Не могли бы вы рассказать нам немного о Синтавии?
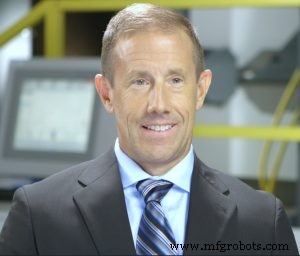
Sintavia была основана в 2012 году Брайаном Неффом, генеральным директором и председателем компании. Компания была основана как собственное предприятие по аддитивному производству с компанией CTS Engines, которая представляет собой независимое ТОиР для реактивных двигателей, базирующееся в Форт-Лодердейле, Флорида.
В 2015 году «Синтавиа» стала отдельной компанией, и мы переехали в Дэви, Флорида, где находимся и по сей день.
Как компания, мы имеем большой опыт работы в авиации. Мы увидели, что есть возможность использовать этот фон для создания вертикально интегрированной компании с множеством различных предложений. Чтобы хорошо разбираться в аддитивных технологиях, вам также необходимо хорошо разбираться в метрологии, металлургии, механической обработке, термообработке, тестировании и т. Д.
Так что, хотя нашим основным навыком является аддитивное производство, мы используем наш опыт в области производства ТОиР и OEM для создания новой автономной компании, ориентированной на аэрокосмическую и оборонную промышленность, а также на нефть и газ.
Уникальность Sintavia в том, что вертикальная интеграция лежит в основе всего, что мы делаем:от постобработки, качества, металлургии, сканирования и так далее. Все эти элементы находятся под одной крышей на нашем производственном предприятии в Дэви, Флорида.
Аэрокосмическая отрасль является основным направлением деятельности Sintavia. Не могли бы вы рассказать нам о некоторых преимуществах аддитивного производства для аэрокосмической промышленности?
Аддитивное производство хорошо работает в аэрокосмической отрасли по целому ряду причин.
Во-первых, важно отметить, что эта технология начиналась как инструмент разработки прототипов для OEM-производителей в аэрокосмической и оборонной промышленности, чтобы быстро итеративно проектировать и тестировать двигатели. Сейчас она дошла до того, что компании создают двигатели с добавками.
Так что это по-прежнему большой драйвер. Но есть и другие типичные преимущества, которые делают AM отличной технологией. Здесь я имею в виду уплотнение сварных деталей, сложные отливки, облегчение конструкции без инструментов. Конечно, сложность не бесплатна, но ее можно значительно расширить за счет добавления.
Например, при выборе деталей мы уделяем первостепенное внимание внешним клапанам на внешней стороне реактивных двигателей и воздуховодов. Мы также видим развивающийся рынок шасси и теплообменников в аэрокосмической промышленности.
Одна из используемых вами технологий 3D-печати на металле - это Powder Bed Fusion. Каковы преимущества этой технологии для аэрокосмических приложений?
Что ж, 3D-печать металлом в целом действительно поддается уникальному дизайну.
На ранней стадии того, что мы делаем, мы используем сплавление в порошковой подложке с помощью лазеров и электронных лучей для создания каналов и компонентов высокого давления слой за слоем. Очевидно, есть преимущество использования этой технологии в качестве инструмента для замены сварных деталей и отливок, уже используемых в отрасли.
Но сила добавки выходит далеко за рамки этого:вы можете изготавливать детали, которые лучше, легче и прочнее, что существенно способствует повышению производительности. В конечном итоге, чтобы по-настоящему использовать возможности AM, компоненты должны быть разработаны для аддитивного производства.
Вы можете использовать аддитивное производство - в первую очередь я говорю о лазерах - для таких компонентов, как теплообменники и шасси, для создания геометрических форм, которые ранее было невозможно изготовить.
У вас также есть, например, проточные тела или клапаны в сборе, которые можно изготавливать быстрее и консолидировать с помощью AM. Это позволяет нашим клиентам не только оптимизировать существующие цепочки поставок, но и производить более качественную продукцию и использовать сильные стороны OEM-рынка в аэрокосмической и оборонной промышленности.
Возьмем в качестве примера теплообменники:аддитивное производство позволяет вам для создания очень тонких стенок и небольших замысловатых геометрических форм внутри компонента. Таким образом, у вас может быть стена в 200 микрон или меньше. Кроме того, благодаря аддитивному производству теперь у вас есть лучший способ отвода тепла от компонента. Это здорово, потому что конечная цель теплообменников - отвести тепло от компонента, чтобы вы могли упаковать в него больше электроники.
Мы используем аддитивное производство металлов для улучшения своей продукции. Все, что угодно, от корпусов клапанов, внешних компонентов реактивного двигателя, каналов и теплообменников до шасси и различных типов трубных конструкций, которые были сделаны сваркой с использованием множества сложных приспособлений и приспособлений для их сварки.
Тем не менее, , мы делаем гораздо больше. Например, мы работаем над тем, что находится внутри турбомашинного оборудования, от меньшей крыльчатки, которая может быть внутри компрессора, до крыльчатки большего размера, которая может быть внутри ракеты.
Мы уделяем особое внимание коммерческой аэрокосмической отрасли - по сути, реактивным двигателям - и еще одно внимание уделяем силовым установкам, то есть частям ракетной техники.
Затем у нас есть «промежуточное звено» в аэрокосмической и оборонной промышленности, под которым я имею в виду малоизвестные компоненты, которые когда-то производились от 10 до 100 штук, но теперь мы можем производить в одна единичная деталь с использованием аддитивного производства.
Не могли бы вы подробнее остановиться на некоторых проблемах проектирования, связанных с этими приложениями?
AM - относительно новый производственный процесс. Мы используем лазеры или электронные лучи, чтобы расплавить порошок послойно. По сути, мы делаем сварные детали малых и средних размеров, или «микросварку».
В этом процессе микросварки происходит быстрое охлаждение там, где лазер обнажает металлический порошок. У вас есть две крайности:очень горячий процесс печати с одновременным быстрым охлаждением.
Из-за такой резкой разницы температур ваша деталь может деформироваться. Таким образом, эти детали не похожи на традиционные сварные конструкции из литых деталей; они являются уникальными изделиями сами по себе.
Одна из ключевых проблем - это способность предсказать, как эти детали будут перемещаться в процессе аддитивного производства. Ключевой частью этой задачи является использование этой самой современной технологии и высокотехнологичных инструментов для прогнозирования в самом начале, чтобы помочь в полной координации процесса.
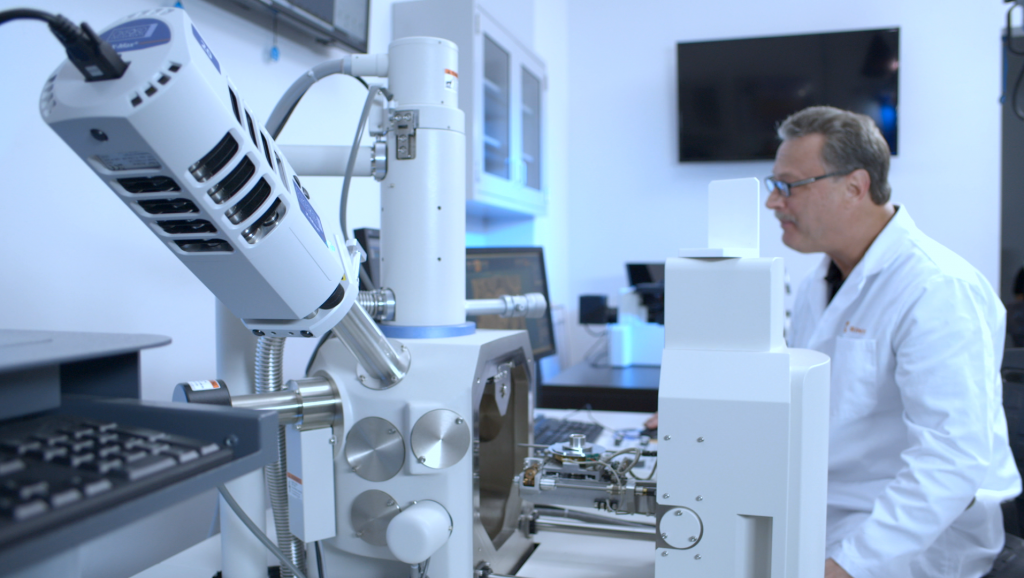
В Sintavia мы используем анализ методом конечных элементов (FEA) в начале цикла проектирования. Инженеры Sintavia получают исходные данные от наших клиентов в виде CAD-моделей, чертежей и спецификаций. Наши инженеры работают с нашими клиентами, чтобы определить ключевые параметры, например, как сориентировать деталь на рабочей пластине, под каким углом будет создаваться деталь и как будут использоваться опоры, чтобы удерживать деталь или отводить тепло из нее. деталь.
Мы используем математику, чтобы предсказать, как деталь будет искажаться, и минимизировать это искажение, чтобы сделать деталь очень точной. Нам нужно знать, как эта деталь будет двигаться и перемещаться по нам, чтобы мы могли добавить припуск на фланцы, отверстия, отверстия и т. Д., Чтобы убедиться, что на складе достаточно материала для очистки в конце процесса. Используя этот подход, мы также можем учесть постобработку этой части в более позднее время.
Следует иметь в виду, что аддитивное производство - чрезвычайно мощный процесс для создания сложных деталей, но его следует использовать в координации с традиционными процессами. Координация аддитивного процесса с вычитающим процессом имеет решающее значение.
Мы много слышим о проблемах, связанных с последующей обработкой металлических деталей, и это одна из услуг, которые предлагает Sintavia. Не могли бы вы рассказать нам о некоторых из самых серьезных проблем, связанных с постобработкой и вашим подходом?
Постобработка должна быть скоординированным процессом между самим процессом печати и постобработкой, которая сопровождает эту часть после производства.
Обычная проблема, с которой не сталкиваются большинство людей, - это удаление порошка после процесса. После печати весь порошок должен быть удален с детали. Поскольку некоторые из этих деталей имеют очень сложную геометрию, мы изготавливаем специальные машины - ультразвуковые или традиционные вибрационные системы - для удаления порошка.
Обычно перед следующим шагом с детали удаляют порошок, что почти всегда снимает напряжение. Мы самостоятельно снимаем напряжение с помощью вакуумной печи или коробчатой печи, чтобы снять остаточное напряжение в процессе аддитивного наращивания.
Оттуда вы переходите к электроэрозионному станку или ленточной пиле, чтобы снять деталь с пластины. Затем, конечно, нужно снять опоры. Эти опоры могут быть любыми, от простых решетчатых опор до чего-то очень прочного, используемого для удержания детали и изготовления очень больших деталей из никелевых суперсплавов. Они подвержены сильным тепловым нагрузкам.
Из-за этого вам может потребоваться очень надежный машинный процесс для снятия опор с этих частей. Для этого может потребоваться большая работа. И когда я говорю «машинный процесс», это может означать много разных вещей. Это может означать что-то столь же простое, как просто отломать их плоскогубцами от очень жесткого пятиосевого станка, чтобы удалить эти опоры с детали.
С этого момента у вас есть несколько вариантов. Например, вы можете перейти на HIP, который мы представляем на месте, или мы используем механическую обработку. В данном случае, когда я говорю «обработка», я имею в виду обработку для печати. Так что это действительно ничем не отличается от того, что вы увидите в механическом цехе.
По большей части у нас есть двухмерный чертеж с множеством элементов управления, и мы обрабатываем эту часть, чтобы привести ее в соответствие со спецификациями.
Что касается самих металлических порошков, каков процесс разработки металлических порошков в Sintavia?
Чтобы было понятно, мы не занимаемся разработкой порошков как таковых. Но мы участвовали в помощи компаниям в разработке сплавов, которые раньше не продавались.
У нас есть компании, с которыми мы работаем, у которых есть, скажем, вариант инструментальной стали или вариант нержавеющей стали. Как правило, это специальные сплавы, которые они разработали для использования в будущем для повышения производительности.
У нас есть одобренные к полетам порошковые решения для аэрокосмической промышленности. Мы закупаем порошок, приносим его в нашу лабораторию и проводим множество тестов перед началом сборки.
Одной из наших сильных сторон в Sintavia является то, что у нас есть возможность получить полную информацию о характеристиках порошка в нашей лаборатории. Это позволяет нам брать образцы и понимать, что происходит с порошком. Обычно другие компании передают этот процесс на аутсорсинг. Поэтому, хотя мы можем закупать материалы у нашего поставщика порошка, мы проводим испытания на текучесть, морфологию, гранулометрический состав, газовый анализ, ICP для химии и так далее.
Мы проводим около восьми или девяти тестов, чтобы убедиться, что порошки соответствуют производственным требованиям наших клиентов. Затем, по мере использования порошка, мы отбираем и архивируем эти образцы порошка, чтобы понять, что происходит с порошком по мере продолжения сборки. Это означает, что мы можем точно понять, что происходит с порошком по мере его постепенного использования.
Синтавиа объявила о планах открыть в этом месяце совершенно новый завод с увеличением числа машин. Не могли бы вы поделиться видением этого нового объекта?
Мы очень рады открытию нашего нового предприятия в этом месяце.
Площадь нового объекта составит 55 000 квадратных футов, и мы собираемся основать его на нашем прошлом успехе.
Ключевым моментом является то, что он будет в значительной степени ориентирован на производство. Мы собираемся разместить новое оборудование на сумму более 30 миллионов долларов, более крупное современное оборудование AM, системы обработки порошка, резервные генераторы, источники питания, инертный газ. Мы предполагаем, что добавим более 135 новых рабочих мест в Синтавии и Южной Флориде.
Новый объект - это действительно видение того, что мы сделали в меньшем масштабе, с использованием 12 машин здесь, на нашем текущем предприятии, и масштабирования этого предприятия до предприятия площадью 55 000 квадратных футов с площадью до 65 машины.
Большие усилия будут приложены в аддитивном производстве, в термообработке. постобработка, отделка, очистка и т. д.
По сути, мы стремимся управлять аддитивным процессом на одном предприятии. Это действительно бизнес-модель:мы хотим расширить то, что мы сделали, и внедрить это в производственный процесс, гарантирующий качество и повторяемость для наших OEM-клиентов.
Не могли бы вы в будущем заняться другими отраслями, такими как автомобилестроение или медицина, где также существует большой спрос на металлические детали, напечатанные на 3D-принтере?
Да, конечно. У нас есть кое-что, что происходит как в автомобильной, так и в медицинской сфере. Есть и другие отрасли, для которых присадки тоже имеют смысл.
Например, мы занимаемся промышленными газовыми турбинами. Несмотря на то, что наш опыт - это авиационные газовые турбины, наземные газовые турбины для производства энергии в основном увеличены в масштабе и немного отличаются от авиационных газотурбинных двигателей.
Эта технология также очень хорошо применима в биомедицинском секторе.
Sintavia имеет аккредитацию AS9100 - AS9100 - это система управления качеством для аэрокосмической промышленности. Наша лаборатория имеет аккредитацию ISO 17025 для механических измерений, которые могут означать все, от определения характеристик порошка и химического состава до испытаний на растяжение и усталостных испытаний.
У биомедицинской индустрии есть другое аккредитационное агентство; большая часть этого зависит от ISO 13485. После того, как у вас есть AS9100, вы можете перейти на ISO 13485. Переход между этими отраслями не представляет большого труда. В конце концов:качество - это качество, а процессы - это процессы. Если вы умеете заниматься аэрокосмической отраслью, вы можете перейти на другие рынки.
Кроме того, помимо всего, что я упомянул, наиболее важным аспектом является контроль качества.
С первого дня мы сосредоточились на разработке нашей системы качества с помощью AS9100, Сертификаты ISO и Nadcap. Все это очень выгодно для наших OEM-клиентов и определенно может быть полезным ресурсом и для других отраслей.
Что, по вашему мнению, необходимо для ускорения внедрения 3D-печати металлом?
Несмотря на все наши технологии и мастерство в области аналитики, мы действительно должны сосредоточиться на том, что движет бизнесом. Бизнесом движут деньги и скорость. Это означает, что технология должна стать быстрее, дешевле и более устоявшейся.
Тем не менее, мы видим, как все меняется. За время работы в Sintavia мы увидели, как эволюционировал металлический AM. Например, когда-то алюминий был относительно сложным материалом для печати в аддитивном производстве, но теперь это стало почти обычным явлением. По мере того, как мы видим дополнительные лазеры, когда мы видим опыт и разработку деталей для аддитивов, они предлагают нашим клиентам более высокую скорость и экономию средств.
Все это исторически возникло в индустрии прототипирования, и мы хотим перевести это в серийное производство. Есть определенные вещи, которые нам нужно сделать, чтобы сделать его быстрее и дешевле, обеспечить качество, а также предоставить преимущества, которые, как всем известно, может предложить металлическая добавка.
Каким вы видите развитие аддитивного производства металлов в следующие пять лет и как Sintavia вписывается в это видение?
Что нам действительно нужно сделать, так это начать производить детали в серийном производстве. В критических отраслях промышленности мы должны гарантировать, что мы производим настоящие металлические детали, которые полностью функциональны.
Мы знаем, что эти детали очень хорошо конкурируют с отливками по механическим свойствам. При правильном процессе и контроле они также могут конкурировать с сырыми продуктами, а в некоторых случаях даже с поддельными продуктами.
Контроль качества, то есть понимание требований к качеству и возможность проверить свою деталь, действительно будет иметь значение в будущем.
Но мы также не можем упускать из виду тот факт, что технология все еще относительно новая. Как отрасль, мы многое делаем впервые.
Это означает, что в первую очередь необходимо изучить переднюю часть процесса.
Например, в начале процесса инженерам необходимо понять стратегии поддержки. и потратьте время на изучение того, как лучше всего оптимизировать геометрию детали и геометрию опоры, что, в свою очередь, поможет изготавливать детали лучшего качества и обеспечить относительную легкость снятия опор.
Благодаря этой работе, вложенной в начните, вы предпримете то, что было дорогостоящим и трудоемким шагом по удалению поддержки, и сделаете его значительно дешевле. Инженерные усилия по созданию деталей действительно имеют решающее значение для достижения зрелости, позволяющей производить продукты один за другим.
Каким будет будущее "Синтавиа"?
Смотрится очень увлекательно! Конечно, это также выглядит довольно сложно, когда мы переезжаем в наш новый объект. Мы внедрим бережливое производство. У нас есть первое крупномасштабное бережливое производство аддитивов, специально разработанное для согласования с производителями оригинального оборудования и цепочкой поставок.
В 2019 году мы продолжим большую часть работы, которую выполняли последние пару лет, с точки зрения квалификации и разработки запчастей для наших клиентов.
Я не буду называть имен, но если вы посмотрите на ведущие аэрокосмические компании по всему миру, то очень высока вероятность того, что мы работаем на них.
В некоторых Например, наши отношения с Honeywell, где мы являемся первым поставщиком AM, получившим разрешение на производство готовых к полетам деталей для Honeywell Aerospace. Мы объединились с Honeywell, чтобы использовать наше текущее предприятие и наше следующее предприятие, чтобы реализовать это и изготовить производственные детали для Honeywell.
Honeywell относительно быстро внедряет эту технологию, и у них есть множество приложений. Но если вы выйдете за пределы компании Honeywell, есть большая вероятность, что мы работаем для них сейчас, будь то самолетостроение или силовая установка двигателей, будь то поставщик аэрокосмической и оборонной промышленности.
Мы считаем, что 2019 и 2020 годы будут для нас относительно важными с точки зрения внедрения металлических добавок. Это действительно здорово, что Honeywell здесь сегодня, но мы увидим, что в ближайшие годы у нас будет больше заказчиков, занимающихся серийным производством.
Мы стремимся к тому, чтобы наша компания предоставляла этот ресурс производителям оригинального оборудования по всему миру, чтобы у них был единый вертикально интегрированный партнер для производства этих деталей с помощью аддитивного производства.
Что-нибудь напоследок?
Я хотел бы повторить, что качество - это наша цель.
Наши клиенты, вне всякого сомнения, самые не склонные к риску клиенты в мире. Чтобы они чувствовали себя комфортно, управляя этими важными компонентами, изготовленными с помощью аддитивного производства, качество имеет первостепенное значение.
В конце концов, мы хотим привести продукты в соответствие с техническими чертежами и спецификациями, чтобы использовать их в реальных приложениях. Для этого необходимо сосредоточиться на соответствии.
Кроме того, сегодня AM - это то место, где сосредоточено все внимание средств массовой информации и на которое тратится много времени и денег. Но в конечном итоге речь должна идти о том, чтобы взять часть, которую вы сделали за счет аддитивного производства, и привести ее в соответствие с инженерными требованиями ваших клиентов.
Так что да, нам нравится говорить об аддитивном производстве. Но мне также нравится думать об этом как о продвинутом изготовление. Я хотел бы отойти от модных словечек аддитивного производства и сказать, что мы передовой производитель прецизионных деталей для аэрокосмической промышленности. Мы хотим производить передовые детали, чтобы наши клиенты могли значительно улучшить свои текущие конструкции.
Чтобы узнать больше о Sintavia, посетите: https://sintavia.com/
О Дуге Хеджесе
Дуг Хеджес имеет более чем 20-летний опыт работы в аэрокосмической отрасли, от разработки экспериментальных компонентов OEM до одобренных FAA ремонтов, изменений и разработки компонентов на основе отраслевых стандартных спецификаций и средств управления.
До Sintavia он работал в качестве старшего инженера в CTS Engines, занимался разработкой ремонтных работ и процессов капитального ремонта реактивных двигателей General Electric, ведущим инженером по проектам в HEICO Aerospace, старшим инженером PMA в Kapco Global и инженером-конструктором Rolls-Royce. Дуг имеет степень бакалавра наук в области машиностроения в Университете Миннесоты.
Интервью с экспертами
Серия экспертных интервью AMFG демонстрирует инновационные компании и отдельных лиц, которые помогают формировать будущее аддитивного производства. Для получения дополнительной информации об участии в серии обращайтесь по адресу [email protected].
3D печать
- Как можно масштабировать до серийного производства добавок с помощью аддитивного MES?
- Интервью с экспертом:профессор Нил Хопкинсон, директор по 3D-печати в Xaar
- Интервью с экспертом:Филип Коттон, основатель 3Dfilemarket.com
- Интервью с экспертом:доктором Альваро Гоянесом из FabRx
- Интервью с экспертом:президент Ultimaker Джон Кавола о будущем 3D-печати
- Интервью с экспертом:президент Sintavia Дуг Хеджес о достижении серийного производства с помощью 3D-печати на мет…
- Интервью с экспертом:Брайан Александер из Solvay о разработке высокоэффективных полимеров для 3D-печати
- Интервью с экспертом:соучредитель Carbon Филип Дезимоун о переходе к массовому производству с помощью 3D-печати
- 4 задачи аддитивного производства, которые можно решить с помощью программного обеспечения
- Интервью с экспертом:Rush LaSelle от Jabil о будущем аддитивного производства