Введение в аддитивное производство металлов с помощью DMLS
По мере ускорения разработки продукта правила проектирования меняются. Нигде это не проявляется так очевидно, как при аддитивном производстве металлов. Прямое лазерное спекание металлов — это технология аддитивного производства металлов со значительным потенциалом в медицинской и аэрокосмической промышленности. Но это требует нового мышления даже на ранних этапах проектирования. Во многом это представляет собой переход, с которым приходится сталкиваться дизайнерам при рассмотрении новых технологий, позволяющих сделать разработку и производство продуктов более быстрыми и инновационными.
У DMLS есть несколько преимуществ, в первую очередь то, что дизайнеры могут изготавливать конструкции необычной формы с экономией времени и средств. Как и другие технологии 3D-печати, DMLS создает детали послойно путем спекания распыленного металлического порошка с помощью мощного лазера.
Зачем использовать аддитивное производство для металлических деталей?
Дизайнеры продуктов и инженеры часто обращаются к процессу, чтобы поэкспериментировать с органическими формами, которые не могут быть легко обработаны. Например, возможность создавать имплантируемые части тела, которые идеально подходят реципиенту. Традиционно эти имплантаты обычно необходимо производить с помощью субтрактивного производственного процесса, такого как 5-осевой станок с ЧПУ. Теперь существует технология, позволяющая сканировать реальную структуру кости человека и печатать прямую замену DMLS, адаптированную к его телу.
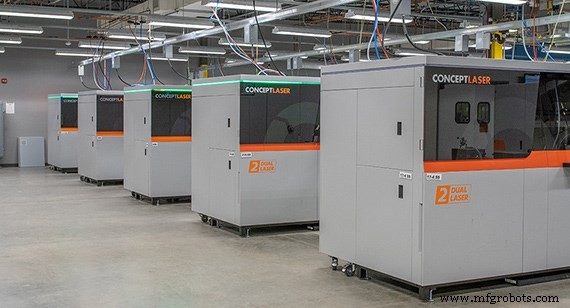
Еще одна возможность — хирургические инструменты с ультратонкими характеристиками и медицинские компоненты органической формы. Эти устройства могут быть разработаны для литья под давлением или литья металла, оба из которых имеют относительно высокие затраты на оснастку и сроки изготовления, которые могут составлять недели. Но с помощью DMLS вы можете напечатать прототип хирургического ручного инструмента с точным весом и прочностью конечного продукта и уже через несколько дней получить его в руки хирурга. Традиционное литье металлов под давлением по-прежнему ценно и будет иметь более низкую цену за штуку при больших количествах, но это по-прежнему составляет от 6 до 12 недель вместо пары дней.
Аэрокосмическая промышленность — еще одна отрасль, которая быстро внедрила 3D-печать металлом. Материалы, часто встречающиеся в аэрокосмической отрасли, такие как инконель и титан, легко доступны в процессе DMLS. Возможность изготовления сложных металлических деталей с полыми элементами открывает ряд возможностей для конструкторов, пытающихся создать легкие компоненты. Еще одним преимуществом 3D-печати металлических деталей является интеграция внутренних охлаждающих каналов внутри детали.
Атрибуты времени, экономии средств и свободы проектирования являются ключом к возможности экспериментировать, быстро проектировать и видеть, что работает. Но DMLS требует изменения дизайнерского мышления. Одна из самых больших корректировок заключается в том, как адаптироваться к введению внутренних напряжений в процессе сборки. Начиная с металлического порошка комнатной температуры, применяя тепло для мгновенного плавления с последующим быстрым охлаждением, возникает напряжение в каждом слое во время процесса сборки. Внутренние напряжения, возникающие во время сборки DMLS, приводят к тому, что деталь пытается загнуться вверх во время сборки.
Как проектировать металлические детали, напечатанные на 3D-принтере
Теперь, когда мы обсудили общие области применения и преимущества технологии 3D-печати металлом, давайте взглянем на некоторые основные рекомендации по проектированию элементов металлических деталей, напечатанных на 3D-принтере.
Самонесущие углы
Самонесущий угол описывает угол элемента относительно рабочей пластины. Чем меньше угол, тем меньше вероятность того, что он будет поддерживать себя. Каждый материал будет работать немного по-разному, но общее эмпирическое правило заключается в том, чтобы избегать проектирования самонесущей конструкции с углом наклона менее 45 градусов. Этот совет поможет вам со всеми доступными материалами. Как вы можете видеть на рисунке выше, по мере уменьшения угла поверхность детали становится более шероховатой, и в конечном итоге деталь выйдет из строя, если угол будет слишком сильно уменьшен.
Выступы
Выступы отличаются от самонесущих углов тем, что представляют собой резкие изменения геометрии детали, а не плавный наклон. DMLS довольно ограничен в поддержке выступов по сравнению с другими технологиями 3D-печати, такими как стереолитография и селективное лазерное спекание. Любой выступ более 0,020 дюйма (0,5 мм) должен иметь дополнительную поддержку, чтобы предотвратить повреждение детали. При проектировании свесов разумно не расширять границы, так как большие свесы могут привести к уменьшению детализации деталей и, что еще хуже, к разрушению всей сборки.
Каналы и отверстия
Внутренние каналы и отверстия являются одним из основных преимуществ DMLS, поскольку они невозможны при других методах производства. Конформные каналы обеспечивают равномерное охлаждение всей детали и помогают уменьшить вес компонента. Рекомендуется, чтобы диаметр каналов не превышал 0,30 дюйма (8 мм). Подобно неподдерживаемым конструкциям, если вы превысите 0,30 дюйма, конструкции, обращенные вниз, будут искажены. Совет, как обойти это ограничение, — избегать проектирования круглых каналов. Вместо этого создайте каналы в форме капли или ромба. Каналы такой формы обеспечивают более однородную поверхность канала и позволяют максимально увеличить диаметр канала.
Рекомендуется, чтобы диаметр каналов не превышал 0,30 дюйма (8 мм). Подобно неподдерживаемым конструкциям, если вы превысите 0,30 дюйма, конструкции, обращенные вниз, будут искажены. Совет, как обойти это ограничение, — избегать проектирования круглых каналов. Вместо этого создайте каналы в форме капли или ромба. Каналы такой формы обеспечивают более однородную поверхность канала и позволяют максимально увеличить диаметр канала.
Мосты
Мост — это любая плоская обращенная вниз поверхность, поддерживаемая двумя или более элементами. Минимально допустимое расстояние без поддержки, которое мы рекомендуем, составляет 0,080 дюйма. По сравнению с другими технологиями 3D-печати это расстояние относительно короткое из-за нагрузок при быстром нагреве и охлаждении. На картинке ниже вы увидите, как мост втягивает опорные конструкции по мере увеличения безопорного расстояния. Детали, которые превышают этот рекомендуемый предел, будут иметь низкое качество на обращенных вниз поверхностях и не будут структурно прочными.
Постобработка металлических деталей, напечатанных на 3D-принтере
После завершения сборки детали внутри машины можно предпринять несколько шагов для улучшения ее механических свойств, качества обработки поверхности и обеспечения того, чтобы характеристики детали находились в пределах допуска.
Термическая обработка
Прохождение деталей через термообработку необходимо после того, как деталь построена, так как это поможет снять внутренние напряжения, возникающие в процессе спекания. Напряжения в сборке распространяются наружу к краю детали и нарастают с каждым дополнительным слоем. Например, детали с толстым поперечным сечением будут подвергаться большему напряжению. Для решения этой проблемы можно использовать различные процессы термообработки:
- Вакуумная печь: Детали помещаются в вакуумную герметичную печь, а затем подвергаются воздействию высокой температуры, что снижает внутренние напряжения.
- Горячее изостатическое прессование (HIP): В этом процессе, обычно называемом HIP, к детали применяется как давление, так и нагрев, чтобы уменьшить пористость и увеличить плотность.
Постобработка с ЧПУ
В некоторых случаях может потребоваться дополнительная обработка после 3D-печати металлического компонента. Это полезно, когда для определенных элементов требуются жесткие допуски или улучшенное качество обработки поверхности, но общая геометрия требует аддитивного производства. Например, компонент ракетного двигателя со сложными каналами охлаждения имеет функцию сопряжения, для которой требуется допуск +/- 0,001 дюйма. более эффективное использование материалов.
Проверки качества
Часто металлические детали, созданные с помощью аддитивного производства, требуют проверки размеров или оценки микроструктуры материала. Для этого можно использовать координатно-измерительные машины (КИМ) для проверки того, что характеристики детали находятся в пределах допуска. КТ или рентгеновское сканирование также можно использовать для изучения внутренних элементов и предоставления неразрушающего решения для обеспечения структурной целостности.
Подробнее о 3D-печати металлом
Если вы хотите узнать больше о DMLS и 3D-печати металлом в целом, у нас есть несколько других доступных ресурсов. Во-первых, начните с прочтения нашего информационного документа по производству металлических деталей. Это охватывает как механическую обработку, так и 3D-печать, и поможет вам решить, какой процесс лучше всего подходит для вашего приложения. А чтобы узнать больше о проектировании металлических деталей для аддитивного производства, посмотрите наш веб-семинар по запросу «Проектирование для 3D-печати металлом».
Промышленные технологии
- Жидкостное аддитивное производство:построение 3D-объектов с жидкостью
- Аддитивное производство против субтрактивного производства
- Преимущества аддитивного производства
- Улучшение аддитивного производства с помощью обратного проектирования
- Что можно сделать с помощью 3D-печати на металле?
- Аддитивное производство металлов:что нужно знать
- Пять удивительных фактов о аддитивном производстве металлов
- Что такое аддитивное производство? Начните с 3D-печати
- Использование гибридного производства с металлическими аддитивными и субтрактивными технологиями
- Аддитивное производство в аэрокосмической отрасли