Интервью с экспертом:специалист по аддитивному производству команды Renault Formula One Пэт Уорнер
Пэт Уорнер - менеджер ADM в Renault Sport Formula One Team - штатный специалист по аддитивному производству, работающий над поставкой первоклассных печатных компонентов как для прототипов, так и для производственных целей. Пэт был глубоко вовлечен в аддитивное производство в рамках F1 на протяжении более 19 лет, и стал свидетелем ряда ключевых разработок в технологии и ее приложениях, которые он любезно обсудил с AMFG в интервью ниже:
AMFG:Как вы изначально начали заниматься аддитивным производством?
Пэт:Изначально я был машинистом ЧПУ в тогдашней Benetton Formula Team, а в 1997 году перешел в отдел CAM. Мы купили нашу первую машину SLA в 1998 году, но не знали, что с ней делать. Станок был помещен в комнату, примыкающую к механическому цеху, и задача программирования была передана группе CAM. К 2000 году мы нашли достаточно приложений для реализации соглашения SLA для двух новых, более быстрых моделей. К 2002 году мы купили еще два. В 2003 году мы добавили в отдел лазерного спекания и с тех пор постепенно расширили существующий отдел, состоящий из девяти машин.
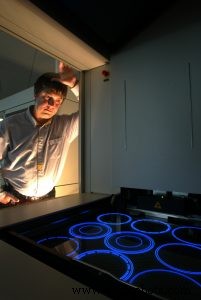
AMFG:Какие из самых больших историй успеха AM вы наблюдали за время работы в Renault?
Пэт:За эти годы их было так много.
Мы прототипируем каждый новый компонент автомобиля и собираем его для работы / соответствия. В этом нет ничего нового в мире аддитивов, но это означает, что мы можем очень быстро находить свои ошибки. Упаковка современного автомобиля Формулы-1 - сложная задача для команды дизайнеров, поскольку предоставить механикам место для доступа к частям автомобиля сложно, глядя на экран.
Мы производим собственные модели литья по выплавляемым моделям для наших конструкционных элементов из титана, таких как корпус редуктора. Мы потратили много времени и усилий на совершенствование этого процесса и обычно заканчиваем тем, что литейный цех, который мы используем, запрашивает у нас образцы (на данный момент мы делаем компоненты только для команды).
Аддитивное производство, без сомнения, увеличило темпы развития аэродинамических труб F1. Когда мы работали неограниченное количество часов в аэродинамической трубе, мы производили более 600 деталей в неделю только для того, чтобы питать туннель. Количество обычных производственных ресурсов, необходимых для достижения той же цели, будет огромным.
Быстрые приспособления и приспособления помогли в производстве автомобиля и в доработках трассы в последний момент. Выявление проблем в пятницу, изготовление заменяемых предметов и их своевременная доставка на трассу для подготовки к квалификации происходило во многих случаях.
Конечно, у нас тоже были свои маленькие беды, но все они помогают в процессе обучения.
AMFG:С какими ключевыми проблемами вы столкнулись, когда дело дошло до AM как инструмента как для создания прототипов, так и для производства?
Пэт:Опять же, их было так много.
Когда мы только начали с этим, долговечность детали была огромной проблемой, материалы SLA были очень хрупкими и плохо переносили влажность. Если бы вы могли держать деталь на столе в течение недели, чтобы никто ее не сломал, она исказилась бы, поскольку впитывала влагу из воздуха. Разработка материалов позаботилась об этих проблемах и по ходу дела внесла ряд значительных улучшений.
Когда мы начали закупать компоненты у внешних поставщиков, мы обнаружили, что в некоторых случаях вы редко получаете одну и ту же деталь дважды, даже если она была из одной и той же сборки. Это побудило нас привлечь больше сотрудников, уделять больше времени пониманию оборудования и материалов и совершенствованию наших процессов. В 2004 году мы стали партнерами Boeing. Это партнерство помогло нам обоим на этом пути и позволило нам устанавливать больше компонентов на наши автомобили. Мы разработали материалы специально для наших нужд, которые коммерчески доступны (правила FIA требуют, чтобы они были) и используются в других местах.
Образование также было проблемой, хотя технология существует уже довольно давно, ее внедрение в основное производство было постепенным, как и образование. В результате у нас по-прежнему появляются новые дизайнеры, которые не сталкивались с аддитивным производством.
AMFG:Какие нововведения вы бы больше всего хотели видеть как в печатных платформах, так и в материалах?
Пэт:Обе области прошли долгий путь за те 19 лет, что я работаю, но есть еще возможности для развития технологии. Нам по-прежнему необходимо уделять много внимания нашим процессам, чтобы достичь требуемых результатов, и мы по-прежнему видим несоответствия в некоторых компонентах, которые мы покупаем. Некоторые из этих несоответствий могут быть в используемом нами оборудовании, но недавно были предприняты хорошие шаги в этой области некоторые поставщики препятствуют использованию указанного оборудования и переработке материалов. Однако дело не только в платформах и материалах; нам также нужны более совершенные инструменты дизайна для AM.
Все мы видели легкие полые конструкции с решеткой внутри. Это должно быть идеально для автоспорта и аэрокосмической промышленности, но на самом деле мы не можем достаточно хорошо предсказать прочность, жесткость и механизмы разрушения таких компонентов, чтобы использовать их в полной мере.
AMFG:Каким вы видите развитие использования AM в F1 в ближайшие несколько лет?
Пэт:Мы постоянно находим новые приложения. По мере дальнейшего увеличения размера набора инструментов будет увеличиваться и количество приложений.
Металлы стремительно развиваются с каждым годом, как и высокотемпературные полимеры. По мере того, как они продвигаются дальше и мы лучше понимаем, как их использовать, мы сможем получить гораздо больше от компонентов AM.
Это довольно интересное время для AM, оно привлекает много внимания и финансирования. Это может быть полезно только для всей отрасли, поскольку нам еще предстоит пройти долгий путь, прежде чем мы сможем полностью бросить вызов традиционному производству.
www.renaultsport.com
3D печать
- Пересмотр процесса интеграции программного обеспечения для операций аддитивного производства
- Интервью с экспертом:Феликс Эвальд, генеральный директор DyeMansion
- Интервью с экспертом:Ибрахим Хадар из Markforged
- Интервью:Доминик Парсонсон из Fuji Xerox Australia
- Интервью с экспертом:Джеймс Хайнбо из Expanse Microtechnologies
- Интервью с экспертом:генеральный директор PostProcess Technologies о решении узких мест постобработки для аддитивного п…
- Интервью с экспертом:президент Sintavia Дуг Хеджес о достижении серийного производства с помощью 3D-печати на мет…
- Интервью с экспертом:Брайан Александер из Solvay о разработке высокоэффективных полимеров для 3D-печати
- Интервью с экспертом:Rush LaSelle от Jabil о будущем аддитивного производства
- Аддитивное производство в аэрокосмической отрасли