Лучший процесс переработки газа в доменной печи
Лучший процесс доменной печи для рециркуляции газа
В области производства чугуна (ЧМ) в доменных печах (ДП) наиболее перспективной технологией значительного снижения выбросов СО2 (двуокиси углерода) является утилизация СО (монооксида углерода) и Н2 (водорода) из газ, выходящий из верха доменной печи. Содержание CO и H2 в газе верхней доменной печи потенциально может действовать как восстановительные элементы газа, и, следовательно, их рециркуляция в доменную печь рассматривается как эффективная альтернатива для улучшения производительности доменной печи, увеличения использования C (углерода) и H2 и уменьшить выброс СО2. Эта технология «рециркуляции верхнего газа» (TGR) в основном основана на снижении использования ископаемого углерода (кокса и угля) с повторным использованием восстановителей (CO и H2) после удаления CO2 из верхней доменной печи. газ. Это приводит к снижению потребности в энергии. Из-за преимуществ высокой производительности, высокой скорости PCI (впрыска пылевидного угля), низкой скорости подачи топлива и низкого уровня выбросов CO2 и т. д.. , процесс TGR-BF считается одним из перспективных процессов производства чугуна в будущем.
В TGR-BF кислород (O2) вдувается в доменную печь вместо горячего воздуха для удаления азота (N2) из верхнего доменного газа. Часть колошникового газа доменной печи, содержащего CO и H2, снова используется в качестве восстановителя в доменной печи. CO2 из колошникового газа доменной печи улавливается, а затем хранится. Было предложено, оценено или практически применено несколько процессов переработки для различных целей. Эти процессы различаются (i) с удалением CO2 или без него, (ii) с предварительным нагревом или без него и (iii) положением впрыска.
Концепция ТГР-ДП (рис. 1) включает в себя множество технологий, которые включают (i) вдувание компонентов восстанавливающего топочного газа доменной печи CO и H2 в фурмы шахты и пода, (ii) снижение потребления ископаемого углерода за счет меньшего количества кокса. скорость, (iii) использование чистого газообразного O2 вместо воздуха горячего дутья в фурменной печи (удаление N2 из процесса) и (iv) извлечение чистого CO2 из колошникового доменного газа для подземного хранения.
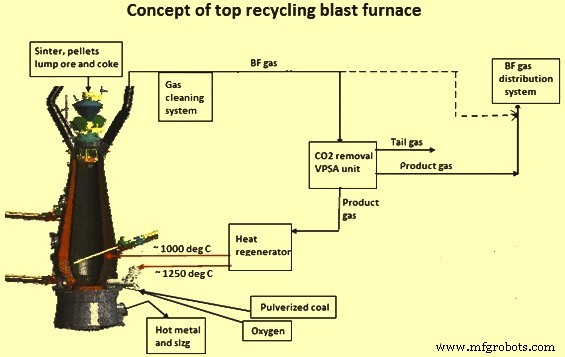
Рис. 1. Концепция TG-BF
Концепция рециркуляции колошникового газа была экспериментально проверена на экспериментальной доменной печи LKAB (EBF) в Лулео, Швеция. Была модернизирована ЭП, и рядом с ЭП была построена газоразделительная установка на основе технологии VPSA (вакуумная короткоцикловая адсорбция).
История переработки топочного газа доменной печи
Для снижения расхода восстановителя и повышения производительности доменной печи в двадцатом веке было введено несколько новых концепций, основанных на традиционном процессе доменной печи.
Уже в 1920-х годах была разработана концепция подачи горячего восстановительного газа в доменную печь. Меньший объем газа из фурм в печи необходимо было компенсировать за счет подачи предварительно подогретого восстановительного газа при 1000°С с содержанием 27 % СО, 33 % Н2 и 26 % N2 в нижнюю зону шахты. В результате оказалось, что только 30 % кокса (в то время 345 кг/т ТМ) необходимо для процесса доменной печи. В середине 1960-х годов эта идея снова была подхвачена в Бельгии, а в начале 1970-х годов были проведены первые испытания на доменной печи диаметром 4,6 м в Кокериль-Серайнге в Бельгии. В нижнюю шахту доменной печи закачивалось определенное количество 400 н м3/тнм риформинг-газа, предварительно подогретого до 1000°С. Наблюдался коэффициент замены от 0,22 кг до 0,26 кг кокса на Н м 3 восстановительного газа.
Дальнейшие исследования не проводились по экономическим причинам из-за высокой стоимости природного газа. В конце 1970-х годов в Германии началась разработка нового процесса, в котором впрыск холодного чистого O2, топлива и рециркулирующего газа осуществлялся на двух фурменных уровнях. На основе этой идеи в 1984 г. в Канаде был разработан процесс для обычной доменной печи без второго фурменного ряда. Главной особенностью этой концепции было впрыскивание угля вместо кокса. Обе концепции так и не были реализованы и закончились лишь исследованием.
Примерно в то же время эта идея была использована НКК в Японии, где в середине шахты был установлен второй ряд фурм. В эти фурмы подавался подогретый восстановительный газ, состоящий из рециркулируемого колошникового газа без удаления CO2. Газ нагревали частичным сжиганием с кислородом. В фурмы горна вдували холодный O2, уголь и холодный рециркулирующий колошниковый газ. НКК опробовал процесс на экспериментальной доменной печи с 3 фурмами, внутренним объемом 3,9 куб. м и диаметром горна 0,95 м. Расход угля может быть увеличен до 320 кг/т ТМ, а расход кокса может быть снижен до 350 кг/т ТМ. Нехватка топливного газа на металлургическом комбинате из-за рециркуляции колошникового газа остановила развитие этого процесса, так как цена на электроэнергию и природный газ в Японии была высокой.
Первая промышленная эксплуатация доменной печи с рециркуляцией колошникового газа была осуществлена в конце 1980-х годов в 12 кампаниях НПО «Тулачермет» в России на доменной печи № 2 с полезным объемом 1033 м3. В этой полностью коксовой концепции процесса доменной печи горячий колошниковый газ, почти не содержащий CO2, вдувался в фурмы пода вместе с чистым O2. Декарбонизированный колошниковый газ нагревали в горячих печах до 1200°С. С помощью этого нового процесса было произведено почти 250 000 тонн чугуна (ТМ). Наименьший достигнутый расход кокса составил 367 кг/т ТМ по сравнению с контрольным значением 606 кг/т ТМ, что означало снижение расхода кокса на 239 кг (39 %). Во время этих кампаний были замечены серьезные прогары фурм, что привело к изменению конструкции фурм. Трудности с системой очистки от СО2 окончательно остановили процесс. Принимая во внимание эти предварительные исследования, в 2004 году была разработана концепция ULCOS (производство стали со сверхнизким содержанием углекислого газа) TGR-BF.
Разработка ULCOS TGR-BF
Работы по развитию проводились в два этапа. На первом этапе разработки, который длился с 2004 по 2009 год, процесс назывался «Новый доменный процесс ULCOS». На этом этапе были разработаны и испытаны три новых концепции процесса. На втором этапе, начавшемся в 2009 г. и получившем название «Процесс рециркуляции колошникового газа в доменной печи ULCOS», были проведены две дополнительные кампании ULCOS TGR-BF.
При разработке использовались модели тепломассобаланса и трехмерная осесимметричная модель доменной печи для расчета основных данных и внутреннего состояния процесса для выбора наилучших режимных параметров. Были определены и исследованы четыре альтернативы на предмет возможной достижимой экономии углерода и возможности запуска BF в соответствии с этими новыми концепциями. Был сделан вывод, что альтернативы 1, 3 и 4 должны обеспечивать экономию ископаемого углерода на уровне 21 % или выше при высоком уровне вдувания пылевидного угля. Альтернатива 2 была отклонена из-за низкой ожидаемой экономии углерода и необходимости сложной технологии нагрева рециркулирующего газа в две стадии сначала в рекуператоре, а затем дальнейшего нагрева путем частичного окисления. Все альтернативы включали удаление СО2 и вдувание богатого СО газообразного продукта в фурмы пода, использование чистого О2 и вдувание угля вместе с восстановительным газом. Во всех альтернативах в будущем рассматривалось использование биомассы, частично восстановленной руды и газа, богатого водородом.
В варианте 1 (рис. 2) декарбонизированный продукт-газ впрыскивается холодным с чистым O2 и углем в фурмы пода и горячим в фурмы шахты. Одним из критических моментов в этом альтернативном варианте была небольшая скорость потока холодного газа на уровне фурмы горна, что приводило к меньшим размерам каналов и более высоким температурам пламени по сравнению с обычным процессом доменной печи. Кроме того, потребовалась новая конструкция фурмы из-за небольшого расхода газа.
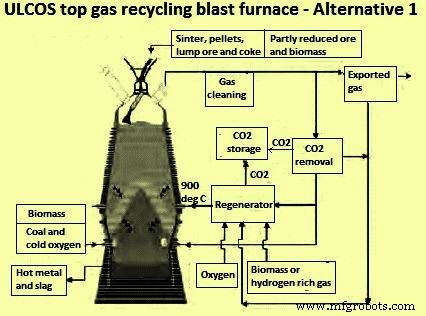
Рис. 2. Доменная печь с рециркуляцией колошникового газа ULCOS – вариант 1
В варианте 3 (рис. 3) декарбонизированный газообразный продукт впрыскивался в горячем виде в фурмы нормального горна вместе с O2 и углем. Для достижения высокой экономии углерода необходимо было работать с низкой ОПТ (адиабатической температурой факела пламени) и в то же время с высокой скоростью вдувания угля.
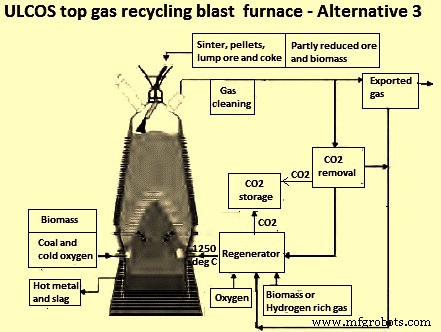
Рис. 3. Доменная печь с рециркуляцией колошникового газа ULCOS – вариант 3
В варианте 4 (рис. 4) декарбонизированный газообразный продукт впрыскивался горячим в фурмы пода и горячим в нижнюю шахту. Температура рециркулирующего газа варьировалась от комнатной до 1250°С.
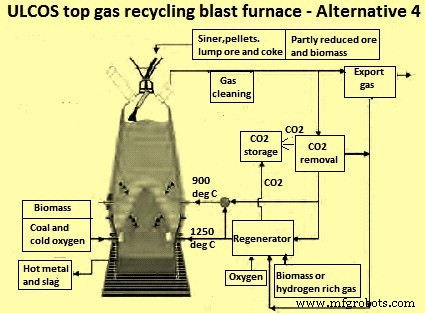
Рис. 4. Доменная печь с рециркуляцией колошникового газа ULCOS – вариант 4
В вариантах 1 и 4 продукт-газ также вводят через шахтные фурмы. Различия заключаются в температуре впрыска газа и положении точек впрыска. Во всех случаях в регенеративной системе нагревалась наименьшая часть газа. Ожидаемая экономия ископаемого углерода для варианта 1 составила 21 % при расходе угля 170 кг/т ТМ, варианта 3 – 24 % при расходе угля 180 кг/т ТМ и варианта 4 – 25 % при расходе угля 150 кг/т ТМ. .
Затем было проведено математическое моделирование условий канала и испытания по газификации, а также лабораторные и пилотные исследования по проектированию и проектированию фурм в условиях одновременной подачи рециркулируемого газа, чистого O2 и пылевидного угля. По результатам расчетов улучшена геометрия фурмы, чтобы избежать горячих точек и отказов в процессе эксплуатации, а также сохранить достаточный импульс газового потока для формирования канавки достаточной глубины.
Кампании процесса TGR-BF в экспериментальной доменной печи
Цель испытаний состояла в том, чтобы продемонстрировать работу ЭДП в полном режиме ТГР с чистым О2 и ПВК на фурмах пода. Это было выполнено в соответствии с тремя определенными альтернативами. Железная шихта состояла из 30 % окатышей и 70 % агломерата. Производительность ТМ поддерживалась на постоянном уровне 1,5 тонны в час, а скорость ПВК варьировалась от 130 кг/т ТМ до 170 кг/т ТМ. В течение различных испытательных периодов объем рециркулируемого колошникового газа был максимальным, чтобы получить максимальную экономию ископаемого углерода. Затем результаты, полученные в ходе испытаний в EBF, сравнивались с модельными расчетами.
Альтернатива 3 и альтернатива 4 были протестированы в 2007 году во время первой кампании после обычного пуска. Альтернатива 3 была проверена на оптимизацию осенью 2009 г. во время второй кампании, за которой последовало тестирование альтернативы 1. В третьей и последней кампании в 2010 г. основное внимание уделялось альтернативе 4 при температуре 900°C. Альтернатива 4 считалась оптимальной. предпочтительная альтернатива для последующего демонстрационного проекта ULCOS BF в промышленных масштабах. Предел 900°C для температуры повторно закачиваемого газа был установлен, чтобы избежать проблем с восстановлением диоксида кремния водородом огнеупорных материалов.
Во время каждой кампании на месте замеры температуры и состава газа, а также образцы шихтового материала были взяты из EBF с помощью двух внутрибуровых зондов. Для исследования поведения шихтового материала в новых условиях эксплуатации корзины с различными материалами агломерата и окатышей были загружены в EBF непосредственно перед остановкой кампании. Эти корзинки были извлечены из ЭБФ при вскрытии печи после закалки азотом. Это было сделано во время кампаний в 2007 и 2010 годах. Во второй кампании в 2009 году удалось провести только закалку из-за неподготовленного завершения кампании из-за проблемы в системе зарядки EBF, и, следовательно, корзины не были заряжены.
Во время кампаний были отобраны образцы из когезионной зоны и измерены размер и форма дорожки качения для дальнейшего исследования. Кампании начались с одной недели обычной работы доменной печи (обдув горячим воздухом) с агломератом, сначала для нагрева и термостабилизации, а затем для установления эталона для обычной работы доменной печи. После обращения производилась остановка для отключения нагнетателя и подключения продуктового газа к галечным нагревателям (регенераторам). Пуск в режиме ТГР-ДП производился искусственным дутьем, состоящим из холодного О2 от фурм и горячего N2 от галечных нагревателей. Постепенно N2 из галечных нагревателей заменяли декарбонизированным колошниковым газом (продуктовым газом).
Результаты кампаний ULCOS TGR-BF
Первый вывод, сделанный в результате кампаний, заключается в том, что процесс ULCOS TGR-BF можно использовать. Во время кампаний с новым процессом не возникало проблем, связанных с безопасностью. Работа блока ВПСА, второго по значимости объекта, прошла бесперебойно и без серьезных сбоев. EBF в сочетании с подразделением VPSA очень хорошо работали во время кампаний.
Однако следует отметить, что на работу установки ВПСА повлияли изменения состава колошникового газа и объема газа из ЭБФ. Следовательно, оба подразделения должны были эксплуатироваться в очень тесной взаимосвязи. Максимальный коэффициент рециркуляции колошникового газа, достигнутый в ходе кампаний, составил около 90 %.
В ходе кампаний процесса ТГР-ДП наблюдалась стабильная работа доменной печи с плавным спуском шихты и легко поддерживалась термостабильность. Эффективность газа в шахте доменной печи была стабильной при различных вариантах, и было хорошее распределение газа, как показали измерения зондов внутри ствола. Однако во время кампаний было несколько отказов оборудования, из-за которых ЭП приходилось останавливать во время работы в новых технологических условиях. Несколько длительных остановок потребовалось вернуться к рабочему этапу «обычной работы» с искусственным горячим дутьем холодного O2 и горячим N2. Небольшие остановки требовали только прекращения подачи газа и добавления некоторого количества кокса и/или угля.
После запуска с N2, когда нет доступного топочного доменного газа, продукт-газ можно снова рециркулировать в течение примерно 1 часа. Все проблемы были решены, как и предполагалось, и термическая стабильность BF никогда не подвергалась серьезной опасности. В ходе кампании накопленный опыт и повышенная уверенность позволили постепенно ускорить восстановление EBF (на производственном уровне). Каждый раз при смене альтернатив (с 3 на 4, с 3 на 1) доменная печь останавливалась примерно на 8 часов для выполнения необходимых подключений газа к шахтным фурмам и замены фурм пода.
Эксперименты, проведенные на лабораторном уровне, показали, что обычная шихта не будет проблемой для нового процесса. Это подтвердилось во время походов. Никаких особых технологических проблем не было связано со свойствами шихтовых материалов. Результаты как зондов, так и образцов из выемки показали профиль восстановления центральной рабочей печи, который представляет собой низкий уровень восстановления у стенки и более высокий уровень восстановления в центре печи как для образцов агломерата, так и для окатышей. Испытания на акробатику образцов из раскопок показали характеристики распада, сходные с таковыми при обычном процессе доменной печи, что соответствовало лабораторным испытаниям. Из результатов испытаний шихты можно сделать вывод, что свойства шихты, используемые в современных обычных доменных печах, по-видимому, не представляют проблемы для процесса ULCOS TGR-BF.
Результаты, достигнутые во время кампаний ULCOS TGR-BF, были очень обнадеживающими в отношении экономии углерода (угля и кокса). Испытания всех трех кампаний показали существенное снижение расхода восстановителя, которое было достигнуто закачкой декарбонизированного колошникового газа. В течение трех кампаний ввод угля и кокса снизился с примерно 530 кг/т ТМ до 400 кг/т ТМ, что представляет собой значительную экономию углерода. Поступление углерода сократилось с 470 кг/т ТМ до примерно 350 кг/т ТМ, что привело к экономия углерода около 25 %.
Хотя вариант 1 не мог быть полностью изучен из-за ранней остановки второй кампании, максимальное снижение поступления углерода с коксом составило 21 % по сравнению с базовым периодом при обычной работе доменной печи. Для этого варианта была разработана новая фурменная технология. Конструкция фурмы состояла из коаксиальных труб, внутренняя труба которых использовалась для вдувания пылевидного угля, а внешняя труба – для вдувания О2. Три установленные фурмы работали очень хорошо и после разборки не наблюдалось ни повреждений, ни износа. Установка VPSA смогла рециркулировать до 88 % колошникового газа доменной печи.
Что касается альтернативы 3, потребление углерода может быть снижено до 15 % в первой кампании при коэффициенте рециркуляции верхнего газа около 72 %. Результаты этого варианта оказались ниже (около 15 %), чем ожидалось по расчетам баланса тепла и массы (24 %), поскольку это был первый опыт использования режима рециркуляции колошникового газа, и процесс не был оптимизирован. Во второй кампании результаты этой альтернативы были намного лучше, когда было достигнуто максимальное снижение ввода углерода примерно на 25 % при коэффициенте рециркуляции верхнего газа до 90 %.
В случае варианта 4 экономия углерода составила 24 % при коэффициенте рециркуляции верхнего газа 90 %. По расходу кокса и угля экономия до 123 кг/т ТМ в новом процессе (вариант 4) по сравнению с базовым периодом эксплуатации. Из этих результатов можно определить хорошую корреляцию между количеством закачиваемого газа (CO+H2) и снижением расхода восстановителя. Поступление углерода через кокс и уголь может быть уменьшено в среднем на 17 кг на 100 н. куб. м закачиваемого газа (CO+H2).
Кампании EBF доказали, что можно запустить процесс доменной печи при гораздо более низком уровне потребления ископаемого углерода по сравнению с уровнем потребления современной доменной печи. Экономия углерода до 25 % была подтверждена закачкой восстанавливающего обезуглероженного колошникового газа. Это значительное снижение по сравнению с современным процессом доменной печи с наилучшей эксплуатацией. На самом деле ожидается, что применение технологии BF-TGR на современной доменной печи приведет к снижению потребления углерода с нынешнего уровня около 405 кг C/т ТМ до уровня около 295 кг C/т ТМ.
Установка ВПСА работала стабильно. Было замечено, что установка VPSA может обрабатывать 97 % колошникового газа доменной печи. Средняя объемная доля СО2 в закачиваемом газе составила около 2,67 %, а степень извлечения СО составила 88 %, что соответствует требованиям по количеству и качеству. В сочетании с установками VPSA и CCS выбросы CO2, сниженные процессом TGR-BF, могут достигать 1270 кг/т ТМ, что составляет 76 % от общего объема выбросов CO2 в процессе производства чугуна. 24 % сокращенного количества CO2 было получено за счет рециркуляции газа, а остальные 52 % транспортировались и хранились под землей с помощью CCS.
С технологической точки зрения можно констатировать, что работа ULCOS более стабильна, чем обычная работа доменной печи, в том, что касается температуры и качества ТМ. По-видимому, это в основном связано с меньшим влиянием реакции потери раствора, связанной с гораздо более низкими уровнями скорости прямого восстановления (DRR). Наименьшее наблюдаемое значение этого DRR составляет 5 %. В результатах эксплуатации не было указаний на то, что это действительно минимальное значение, которое могло быть достигнуто в ULCOS TGR-BF. На качество ТМ большое влияние оказала эксплуатация УЛКОС ТГР-БФ. В частности, наблюдалось существенное снижение содержания кремния (более 1% абсолютного содержания) и соответствующее увеличение содержания С. Однако следует отметить, что содержание кремния в обычном доменном печи намного ниже (около 0,5 % в обычном доменном печи по сравнению с примерно 2,0 % в EBF), и, следовательно, не следует ожидать столь больших изменений при применении ULCOS. Процесс BF-TGR в промышленном масштабе.
Испытательные кампании ULCOS TGR-BF показали, что новый процесс TGR-BF осуществим и прост в эксплуатации. Его можно эксплуатировать с хорошей безопасностью, высокой эффективностью и сильной стабильностью. Испытательные кампании показали, что можно переключать работу EBF между 4 режимами работы (традиционный, варианты 1, 3 и 4). Также было доказано, что процесс доменной печи и газоразделительную установку VPSA можно эксплуатировать в замкнутом цикле. Полученная экономия углерода соответствовала прогнозам расчетов технологической схемы. Испытания также показали, что обычные шихтовые материалы, агломерат, окатыши и кокс подходят для процесса ULCOS TGR-BF.
Основываясь на опыте кампаний EBF, вопросы, которые требуют внимания для безопасного и устойчивого промышленного применения процесса ULCOS TGR-BF:(i) риск утечки газа на уровне фурмы может потребовать, чтобы уровень фурмы был физически отделен от литейного двора для противопожарная защита, (ii) риск утечки из-за изгиба фланцев при высоких температурах, (iii) удлинение дымохода от горячих печей/нагревателей, чтобы избежать ядовитого газа в окружающей среде, (iv) для предотвращения отказов на этапе запуска , эксплуатационный персонал должен быть обучен работе с искусственным газом во время эксплуатационных испытаний, (v) важны оптимальные параметры нагнетания, чтобы избежать налипания/засорения на носу фурмы, (vi) важность индивидуального управления потоком дутья на фурмах, чтобы избежать нарастания избыточного O2 и пылевидного угля в фурме в случае ее засорения, (vii) следует изменить выбор огнеупоров и изготовление огнеупорных изделий и по возможности избегать использования анкеров из углеродистой стали, попеременно должны использоваться другие материалы, кроме стали C, или стали, покрытой оксидом алюминия, и (viii) важно избегать металлической пыли посредством тщательного выбора металлических деталей.
Результаты испытаний показали, что вариант 4 продемонстрировал наилучший эффект снижения выбросов и был выбран в качестве первого выбора для испытания на промышленной доменной печи на следующем этапе.
Производственный процесс
- Система автоматизации, измерения и управления доменными процессами
- Производство и использование доменного газа
- Использование орехового кокса в доменной печи
- Вдувание пылевидного угля в доменную печь
- Неисправности доменной печи во время работы
- Система охлаждения доменной печи
- Системы верхней загрузки доменных печей
- Химия производства чугуна в доменной печи
- Огнеупорная футеровка доменной печи
- Понимание процесса газовой сварки