Развитие AFP для следующего поколения
Если автоматическое размещение волокна (AFP) и автоматическая укладка ленты (ATL) были производственными процессами, которые позволили широко применять композиты в Boeing 787 и Airbus A350, то AFP / ATL также будут проложить путь для следующего поколения коммерческих самолет, теперь на чертежных досках. В чем разница на этот раз? Оценить.
По оценкам Boeing, к 2037 году миру потребуется более 31 000 новых узкофюзеляжных самолетов для удовлетворения потребностей пассажиров. Airbus прогнозирует потребность в более чем 28 000 узкофюзеляжных самолетов к 2037 году. Обе компании рассматривают возможность замены своих неизменных узкофюзеляжных самолетов - 737 (Boeing) и A320 (Airbus). Ожидается, что обе компании будут широко использовать композиты в любом новом самолете, который они разрабатывают. Обе компании сообщают своим цепочкам поставок ожидаемые темпы производства этих самолетов на уровне 60-100 самолетов в месяц, с акцентом на 100. Категория узкофюзеляжных самолетов для обеих компаний составляет около двух третей от общего мирового спроса, что означает, что производственная среда, разработанная для узкофюзеляжных самолетов, в обозримом будущем станет стандартной производственной средой для аэрокомпозитов.
Все это означает, что технология автоматизации должна быть разработана сейчас, если она хочет соответствовать требованиям к качеству и скорости производства самолетов следующего поколения. Ничто из этого не упускает из виду старший инженер Electroimpact (EI, Мукилтео, Вашингтон, США) Тодд Рудберг. Рудберг и EI вошли в мир композитов в 2004 году, когда компания разработала технологию AFP для производства передней части фюзеляжа 787 Section 41, изготовленной Spirit AeroSystems (Уичито, Канзас, США). Впоследствии EI продолжила производство систем AFP и ATL для изготовления других конструкций 787, конструкций А350, конструкций двигателей и, совсем недавно, лонжеронов крыла Boeing 777X. Теперь Рудберг смотрит в будущее производства самолетов следующего поколения и видит возможности для улучшения AFP. По существу.
По словам Рудберга, возможности очевидны, если посмотреть на данные. Фактически, EI разработала несколько показателей, чтобы помочь компании понять, что у ее оборудования хорошо, а что можно улучшить. Во-первых, глядя на ландшафт AFP 2019 года, Рудберг видит множество угроз для нынешней технологии AFP, включая ATL, простоя руки, плоские заряды тканых материалов и, конечно же, алюминия.
Метрики AFP, разработанные Рудбергом, взяты из проекта полнофункционального демонстратора (FPD), для которого EI провела четыре предпроизводственные сборки. Данные одной из этих сборок, выполненных в феврале 2019 года с использованием «стандартной» технологии EI AFP, выявили существенные проблемы с загрузкой машины, когда время использования машины приходилось на один из семи сегментов:
- Лазерная проекция:30%.
- Запуск:27%
- Инспекция:22%
- Перерыв:10%
- Остановка, вызванная оператором:6%
- Устранение ошибок:3%
- Изображение:2%
Если посмотреть с другой стороны, с нынешними технологиями, в AFP есть одна операция с добавленной стоимостью (запуск), а все остальные операции считаются операциями, не приносящими добавленной стоимости. Таким образом, соотношение стоимости к операциям без стоимости составляет 1:3. «Промышленность действительно хочет 3:1, и я тоже, - говорит Рудберг, - и я хотел бы сделать это до того, как выйду на пенсию». Цель состоит в том, чтобы сократить время, затрачиваемое на операции, не приносящие добавленной стоимости.
Существует также одна всеобъемлющая метрика AFP, которая требует объяснения:среднее значение полосы до отказа (MSBF). Это среднее количество жгутов волокна, размещенных между ошибками размещения. Конечно, чем больше это число, тем надежнее машина и процесс. По словам Рудберга, в февральской сборке FPD было 5 365 MSBF.
Цели
По словам Рудберга, если более внимательно присмотреться к работе AFP, EI имеет прямой контроль только над тремя операциями:запуском, исправлением ошибок и проверкой. И именно здесь компания концентрирует свои усилия. Тем не менее, Рудберг отмечает, что авиаконструктор также должен сыграть свою роль, особенно в сокращении количества проверок качества, остановок и остановок, вызванных оператором. «Мы должны понимать, что время работы стало очень низким, потому что машины очень быстрые, - говорит он, - и все, что не приносит добавленной стоимости, оказывает огромное влияние на вашу загрузку. Получается, что это командный вид спорта. Мало того, что OEM - я - должен работать лучше, авиаконструктор также несет определенную ответственность ».
Для производства самолетов следующего поколения Рудберг хочет увеличить MSBF до> 20 000, увеличить время работы до 77% и полностью исключить лазерное проецирование, остановку и изображение, вызванные оператором. Как? Рудберг выделяет три технологические области, которые могут облегчить этот переход:шпулярники с сервоприводом, 100% контроль в процессе и управление данными или EI 4.0.
Все три были оценены EI в серии недавних сборок проекта FPD после этой первоначальной сборки в феврале. Данные самого проекта FPD доказывают, что EI движется в правильном направлении. Рудберг говорит, что используемая система AFP, называемая MuSCLE, обеспечивала пиковую мощность 1500 лошадиных сил, ускорение / замедление 0,5G, скорость укладки 4000 дюймов в минуту, время поворота головы 1 секунду, угловую скорость лонжерона 120 градусов / секунду и 6000 MSBF. (достигнуто в производстве).
По словам Рудберга, переход на шпулярники сервомотора и отказ от сервопневматических шпуров был сделан для увеличения скорости буксировки, точности размещения буксировки, контроля натяжения буксировки и общей надежности сборки. Последние два года компания работала над компактным сервоприводом, который можно установить на модульную головку EI. Результаты этой технологии пока многообещающие; Тестирование показывает:15 000 MSBF, скорость добавления на 87% выше, скорость резки на 36% выше, повышенная точность установки концов. Кроме того, EI доказала, что шпулярную систему серводвигателя можно использовать для укладки сухих углеродных волокон.
Ключ к проверке - это «незавершенная» часть. У EI уже есть технология проверки, разработанная с Aligned Vision (Челмсфорд, Массачусетс, США) и развернутая на производственной линии крыла 777X, в которой используются лазерные и видеотехнические технологии для проверки нахлестов, зазоров, складок, ошибок размещения концов и посторонних предметов ( FOD). Эта система, однако, существует независимо от системы AFP и требует для работы четкого поля зрения - это означает, что головка AFP должна перемещаться. Рудберг и EI разработали новую систему контроля, называемую RIPIT, которая является неотъемлемой частью головки AFP и проверяет размещение волокна, как только оно происходит.
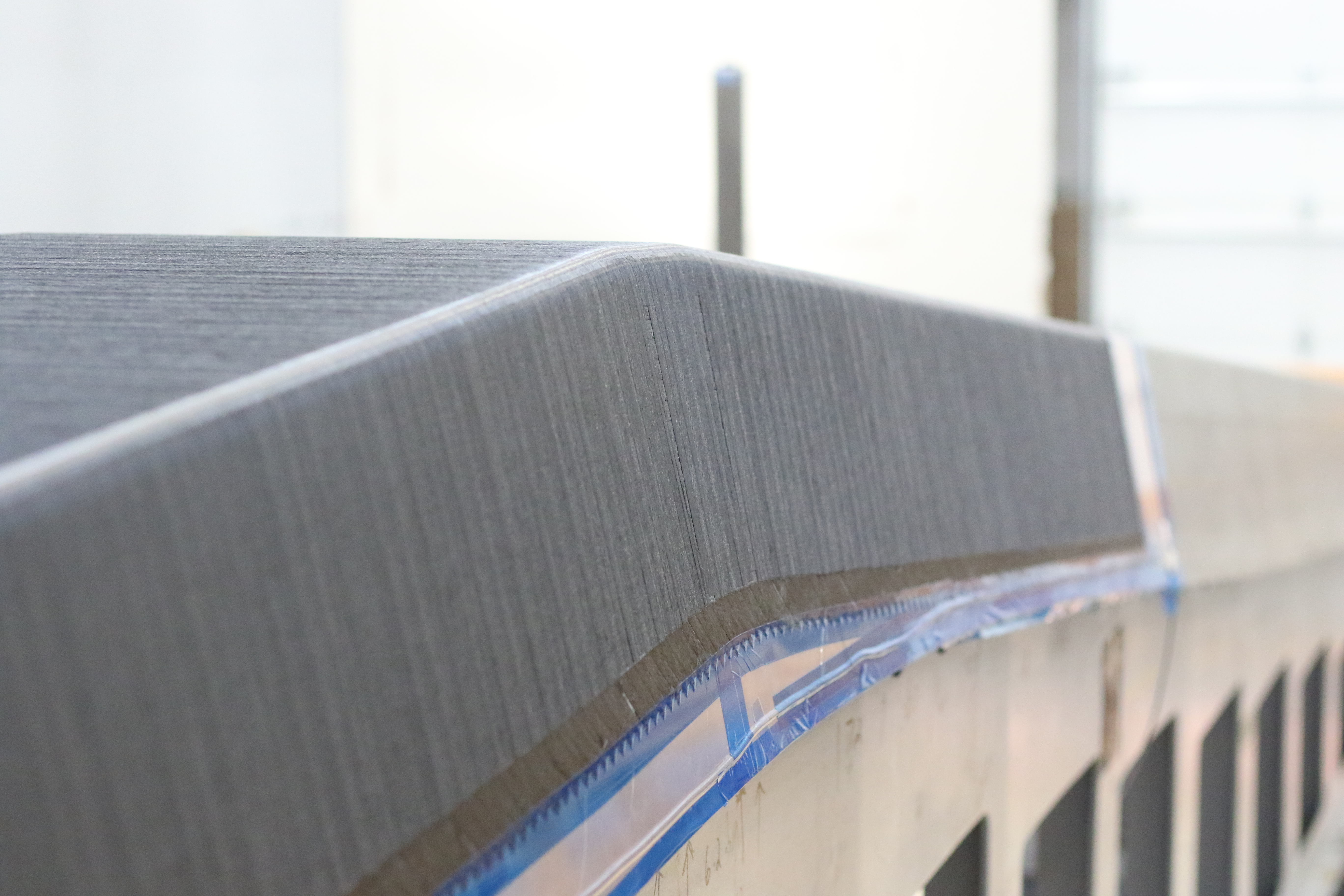
Поскольку Boeing и Airbus рассматривают процессы производства композитов вне автоклавов, способность систем AFP эффективно размещать сухие углеродные волокна будет иметь решающее значение. Этот демонстрационный лонжерон показывает сухое волокно, размещенное с помощью системы Electroimpact. Источник | Электроудар
EI не будет разглашать природу технологии, лежащей в основе RIPIT, за исключением того, что она не основана на лазерном или визуальном оборудовании. В любом случае, по словам Рудберга, тесты системы показывают, что она способна обнаруживать в реальном времени проскальзывание буксировочного устройства до ± 0,030 дюйма, добавлять размещение до ± 0,050 дюйма и размещение среза до ± 0,050 дюйма. Кроме того, говорит Рудберг, «мы провели множество испытаний по корреляции данных RIPIT с существующей системой технического зрения, соответствующей требованиям Boeing [система Aligned Vision, используемая на 777X], и мы получили корреляцию».
По словам Рудберга, ценность управления данными заключается в способности систем EI помогать производителям более четко видеть, насколько хорошо работает процесс AFP. С этой целью EI разработала программное обеспечение для визуализации данных - EI 4.0 - которое предлагает видимость не только того, как данная машина работала (на основе MSBF) во время данной сборки, но и того, как выполнялись отдельные буксировки и последовательности. По сути, программное обеспечение помогает оператору точно увидеть, где именно в головке AFP находится проблема. «Итак, мы будем использовать этот EI 4.0, чтобы указать, куда им [операторам] нужно обратиться и заглянуть в заголовок AFP, чтобы внести изменения», - говорит Рудберг.
Используя это программное обеспечение, можно графически отображать MSBF для различных функций машины и определять проблемные жгуты волокна и особенно сложные последовательности. Программное обеспечение также измеряет и сообщает о других действиях машины, которые могут снизить эффективность использования. Используя эти инструменты управления данными, EI смогла оптимизировать и сократить время сборки OPS с более чем 50 минут до чуть менее 40 минут. Другие инструменты включают сравнение характеристик переключения передач и сравнение угла наклона слоев.
«Я действительно считаю, что использование 75% - это реалистичная цель или ожидание», - утверждает Рудберг. «Но для этого потребуется командная работа, организационная инициатива и последующие действия со стороны авиаконструктора, для этого потребуются наши улучшенные технологии, для этого потребуются более качественные профилактическое и прогнозирующее обслуживание, а также более совершенные инструменты для анализа использования ячеек и производительность машины ».
Смола
- Индустрия 4.0 и Интернет вещей:тенденции рынка на следующие годы
- Дополненная реальность - следующая важная вещь для HR?
- DARPA работает над материалами следующего поколения для гиперзвуковых транспортных средств
- Новые кристаллы для технологий отображения следующего поколения
- Как подготовиться к следующему нарушению цепочки поставок
- Пять правил для следующего кризиса цепочки поставок
- Мерчандайзинг в облаке - следующая необходимость в розничной торговле
- Материал для следующего поколения интеллектуальных датчиков
- COVID-19:спрос на умные фабрики следующего поколения
- Что делать дальше с революцией в области автоматизации?