Первичные аэроструктуры из термопласта делают еще один шаг вперед
Преимущества термопластичных композитов, такие как ударная вязкость, сравнительно высокая внеплоскостная прочность и устойчивость / пригодность к вторичной переработке, привлекают авиастроение дизайн инженеров к понятию первичных конструкций из термопластичных композитов на протяжении десятилетий. Но авиастроение производство инженеры не знали, как найти экономичный способ перейти от моделирования САПР к производственному цеху. Однако это не останавливает:усилия по развитию необходимых производственных технологий продолжаются по всему миру - возможно, нигде так упорно, как в Нидерландах.
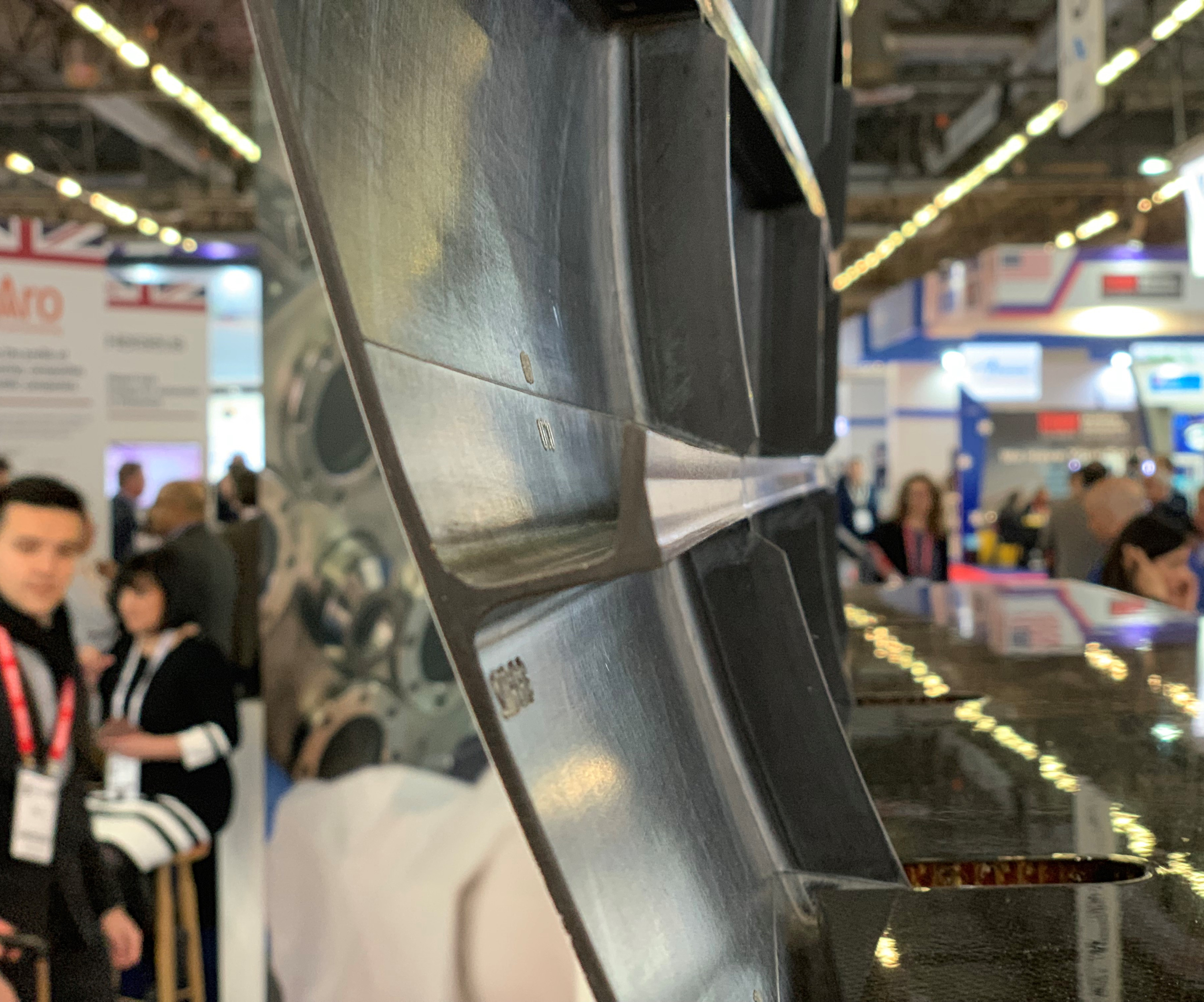
Встроенные L-образные стрингеры. Фюзеляж GKN Fokker из углеродного волокна / PEKK, спроектированный и изготовленный для компании Gulfstream, включает изогнутые продольные L-образные стрингеры со слегка тупым углом для отсоединения инструмента. CW фото | Джефф Слоан
В 2009 году девять голландских промышленных компаний и исследовательских институтов вместе с Airbus (Тулуза, Франция) сформировали Консорциум доступной первичной конструкции самолета из термопласта (TAPAS). В 2014 году инициатива расширилась до 12 партнеров и продолжилась как TAPAS2. Ориентируясь на приложения, разработанные Airbus в рамках TAPAS2, компания GKN Fokker (Хогевен, Нидерланды) недавно разработала демонстрационный образец фюзеляжа, используя так называемую «технологию стыковых соединений ортосетки», которая позволяет производить рентабельное производство конструкции фюзеляжа из термопластичного композита.
Полная отдача от первичной конструкции самолета из термопластического композита - хотя это еще не все - теперь может быть в пределах видимости, поскольку Gulfstream Aerospace (Саванна, Джорджия, США) в партнерстве с GKN Fokker продвигает свою технологию фюзеляжа TAPAS2, указывая путь к возможному применению материалы и процесс до полного фюзеляжа. История недавно разработанной панели фюзеляжа (которая была представлена на выставке JEC World ранее в этом году) является одним из достижений в методах проектирования и производства, а также в более комплексном подходе к проектированию и производству.
«Традиционно, - объясняет главный инженер GKN Fokker Андриес Буйтенхуис, - независимо от того, использовали ли они ткани или однонаправленные ленты, дизайнеры в основном придерживались обычных слоев с ориентацией под 0, 90 и 45 градусов. Они будут работать со своих столов для укладки слоев, независимо от других дисциплин ». Новый подход представляет собой интегрированную, оцифрованную программную платформу для проектирования и производства (разработанную с помощью TAPAS), в которой инженеры из разных дисциплин смотрят на одну и ту же цифровую модель и имеют возможность концептуализировать более сложные конструкции деталей. «Это открывает целый новый мир беспрецедентных возможностей оптимизации», - продолжает Буйтенхейс. «На сложных формах направления волокон могут быть повсюду. Мы можем изготовить нестандартный ламинат и по-новому взглянуть на конструктивные возможности, производственные зазоры и перекрытия, радиусы…. И вы можете оптимизировать прочность конструкции на месте ». Эти расширенные варианты конструкции более полно используют возможности управления волокном машин для автоматической укладки волокна (AFP), а также усовершенствования в других производственных возможностях, обсуждаемых ниже.
Свобода проектирования, предоставляемая этой интегрированной цифровой системой, оказалась незаменимой при проектировании и производстве панелей для бизнес-джетов. В конструкции фюзеляжа TAPAS2 панель из углеродного волокна / полиэфиркетонекетона (PEKK) (сделанная с использованием Solvay APC PEKK-FC) имеет сварное соединение каркаса с обшивкой без застежек, что является важным фактором экономической эффективности конструкции. «Мы прогнозируем достижение паритета стоимости алюминиевых корпусов фюзеляжа, - объясняет Арнт Оффринга, руководитель отдела технологии термопластичных композитов в GKN Fokker, - и это потому, что алюминиевые корпуса склепаны». Ожидается, что отказ от механических креплений приведет к снижению затрат на 20% и уменьшению веса основных конструкций самолета на 10% по сравнению с традиционными композитными решениями. Конечно, большая часть экономии средств и веса происходит за счет отказа от самих крепежных элементов, а также затрат на рабочую силу для их установки. Также большое значение имеет устранение отверстий в композитных компонентах для размещения крепежных деталей - отверстий, требующих дополнительного усиления и, следовательно, увеличения веса.
GKN Fokker достигла уровня технологической готовности (TRL) 3 (доказательство концепции) с Airbus для герметичного фюзеляжа, демонстрируя паритет стоимости с алюминиевыми панелями фюзеляжа в рамках TAPAS2 в декабре 2017 года. Попутно команда GKN Fokker расширила свое видение этого термопласта технологии фюзеляжа от коммерческих авиалайнеров до бизнес-джетов.
Интерес компании Gulfstream
История успешной работы GKN Fokker для Gulfstream над компонентами из термопластичного композита сделала партнерство с производителем бизнес-джетов следующим логическим шагом. «Широко известно, что компания Gulfstream уже много лет занимается поставками деталей из термопластичных композитов, - говорит Марк Чапман, менеджер инициативы Gulfstream по усовершенствованным конструкциям и материалам (ASMI). Он добавляет, что проект панели фюзеляжа «является естественным продолжением того, что мы делали, начиная с более простых деталей и заканчивая основными конструктивными деталями». GKN Fokker сотрудничает с Gulfstream в разработке многочисленных вторичных компонентов из термопластичного композита, включая рулевые колонки и рули направления, а также панели пола на G650.
В 2015 году Offringa и Buitenhuis представили компании Gulfstream разработки проекта TAPAS2, и Чапман и его команда осознали потенциал получения преимуществ от результатов TAPAS2. «Мы увидели потенциальные преимущества снижения веса, повышения ударопрочности и прочности, а также улучшенных характеристик», - вспоминает Чепмен. Также привлекателен дизайн без застежек. «Сварочная технология позволила бы нам собрать фюзеляж более эффективно», чем сборка с механическим креплением, - говорит Чепмен.
Партнерство с GKN Fokker поддерживает исследования и разработки Gulfstream более сложных форм фюзеляжа, производство которых с металлическими конструкциями может быть экономически нецелесообразным. «Пока что можно только растягивать металл», - отмечает Чепмен. «Соединения и несущая конструкция, необходимые для сложных форм, не очень эффективны». Оффринга соглашается:«Такие сложные геометрические формы сложно изготовить с помощью обычных технологий».
Совместное проектирование и производство
Чтобы получить производимую конструкцию без застежек, подход GKN Fokker направлен на противодействие двум ключевым силам, которым подвергаются шарниры фюзеляжа:давлению в кабине и ударам, например падению инструмента. Давление в кабине создает радиальные силы на фюзеляж, создавая высокие нагрузки в стыке рамы с обшивкой. В обычных конструкциях каркасы фюзеляжа содержат «мышиные норы», через которые проходят продольные стрингеры. Под действием давления в кабине эти «мышиные норы» служат неоднородностями, которые подвергаются сильному отслаиванию, что является серьезной проблемой для конструкции без застежек, учитывая низкую прочность композитов вне плоскости по сравнению с металлами. Удары также создают высокие нагрузки в стыке рамы с обшивкой, поскольку рама не прогибается при ударе.
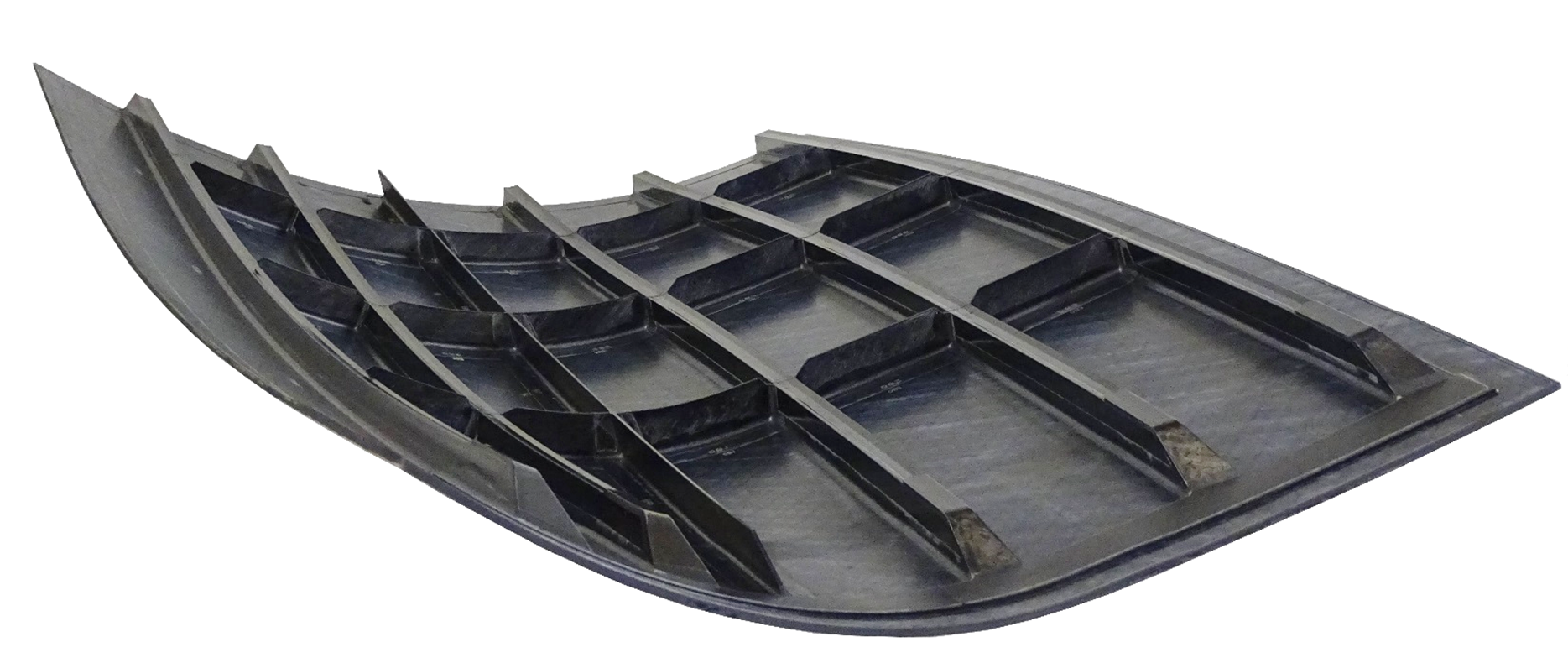
Двойная кривизна. Панель фюзеляжа из термопластичного композита соответствует сложной геометрии кормовой части фюзеляжа бизнес-джета Gulfstream с укладкой обшивки AFP с оптоволоконным управлением и совместной консолидацией ортосетки. Обратите внимание на продольные стрингеры лопастей, которые позже привариваются к раме. Источник | ГКН Фоккер
Команда GKN Fokker / Gulfstream знала, что невозможно решить проблемы, создаваемые сложной кривизной, с помощью металла или традиционных подходов к проектированию и производству композитных материалов. В частности, Буйтенхейс отмечает:«Сложная конструкция фюзеляжа была бы невозможна без волоконного управления». Эта способность машин AFP - это то, что позволило разработчикам оптимизировать локальную ориентацию волокна на основе сложной формы оболочки и отклониться от стандартных вариантов ориентации волокон 0/45/90. «Волоконное рулевое управление для оптимизации формы и веса - одно из самых значительных достижений в этом проекте», - считает Чепмен.
GKN Fokker изготовил обшивку панели фюзеляжа на ультразвуковой машине AFP, которую компания разработала для быстрой укладки термопластической ленты. Лента однонаправленная, что также улучшает характеристики ламината по сравнению с тканевыми лентами.
Успешно справляясь с высокими нагрузками, создаваемыми давлением в кабине и ударными силами, а также другими требованиями к характеристикам, новая концепция, разработанная в рамках TAPAS и TAPAS2, которая теперь используется в панели Gulfstream, представляет собой то, что описывается как «стыковое соединение с ортогональной жесткостью кожа со сварными шпангоутами ». При распаковке этого описания выделяются три ключевые конструктивные особенности и производственные разработки, необходимые для их реализации:(1) ортосетка, (2) стыковое соединение и (3) технология сварки.
Ортосетка
Требования к прочности панели частично удовлетворяются за счет полностью взаимосвязанных ортогональных решеток жесткости. Эта ортосетка устраняет пиковые нагрузки, связанные с отверстиями для мыши, избавляя конструкцию от точек, в которых усиливается отслаивание. Ортосетка состоит из непрерывных продольных стрингеров и шпангоутов, состоящих из двух отдельных компонентов:прерывистых, но связанных продольных стрингеров лопастей и шпангоутов, приваренных поверх них.
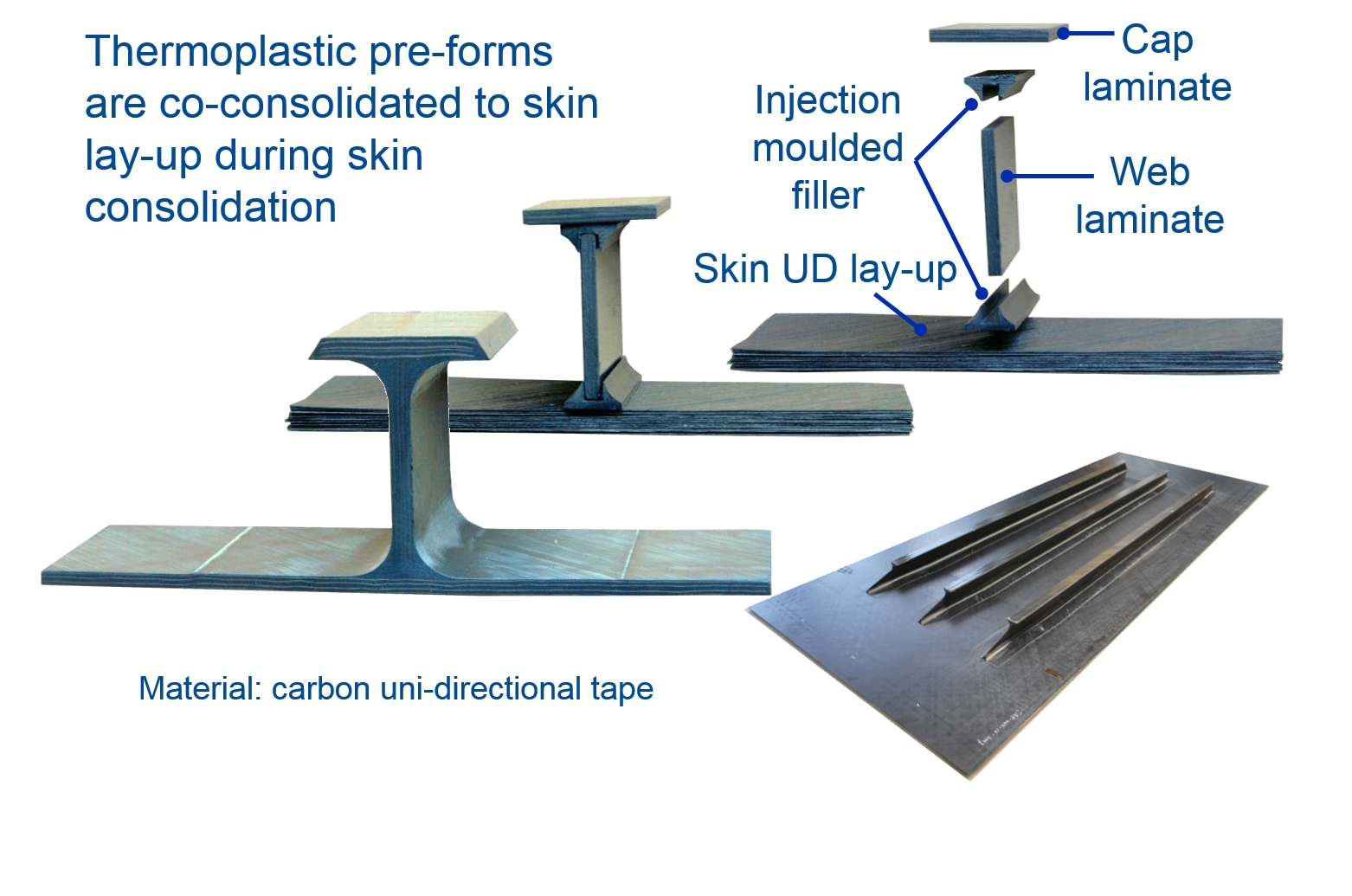
Экономичное стыковое соединение. Компания GKN Fokker разработала и запатентовала стыковое соединение, которое обеспечивает соединение ортосетки и ортосетки с обшивкой с использованием экономичных коротковолоконных элементов, полученных литьем под давлением, и плоских слоистых материалов из непрерывных волокон для стрингера и крышки (здесь Т-образный стрингер; панель Gulfstream включает L стрингеры той же техники). Источник | ГКН Фоккер
Таким образом, это новое поколение элементов жесткости фюзеляжа, которое эволюционировало за годы разработки ортосеток. Первоначально компания GKN Fokker использовала Т-образные стрингеры, в которых крышки как продольных, так и окружных элементов были непрерывными и перекрывались по углам. Однако соединение с рамой потребовало снятия периферийного колпачка. Таким образом, Т-образные стрингеры превратились в L-образные стрингеры, а шпангоуты превратились в стрингеры с окружными лопастями с приваренными к ним шпангоутами.
Требуется еще одна модификация, потому что изогнутые стрингеры, используемые как в продольном, так и в периферийном направлениях, значительно затрудняют снятие инструмента. Таким образом, L-образные стрингеры спроектированы с углом наклона колпачка к перемычке более 90 градусов, так что детали инструмента всегда могут выскользнуть из сетки стрингера вбок.
Стыковые соединения
Компания GKN Fokker разработала не только дизайн ортосетки, но и новый подход к ее производству, а также механизм соединения сетки с кожей. «Сетка может быть чрезмерно дорогой в изготовлении, - отмечает Оффринга, - но наша сетка состоит из плоских ламинатов и простых« наполнителей », полученных литьем под давлением».
В частности, GKN Fokker применила свою запатентованную технологию стыкового соединения к панели Gulfstream (также к предыдущим панелям TAPAS). Полотно и крышка компонентов T- или L-стрингера, а также компоненты стрингера с лопастями изготавливаются из преформ, вырезанных гидроабразивной резкой из плоского ламината из углеродного волокна / PEKK. Соединительные элементы (оболочка к полотну и полотно к крышке) представляют собой наполнитель в форме буквы «пи», изготовленный методом литья под давлением из коротковолокнистого углеродного материала / материала PEKK. Тип смолы и углеродного волокна соответствует типу элементов сетки.
Обшивка и ортосетка совместно консолидируются в инструменте внутренней пресс-формы из инвара (IML). Инструмент имеет канавки, в которые загружаются компоненты ортосетки и блоки инструментов. Затем сформированная AFP оболочка помещается на IML, и вся сборка упаковывается в мешки и герметизируется в автоклаве.
Сварка
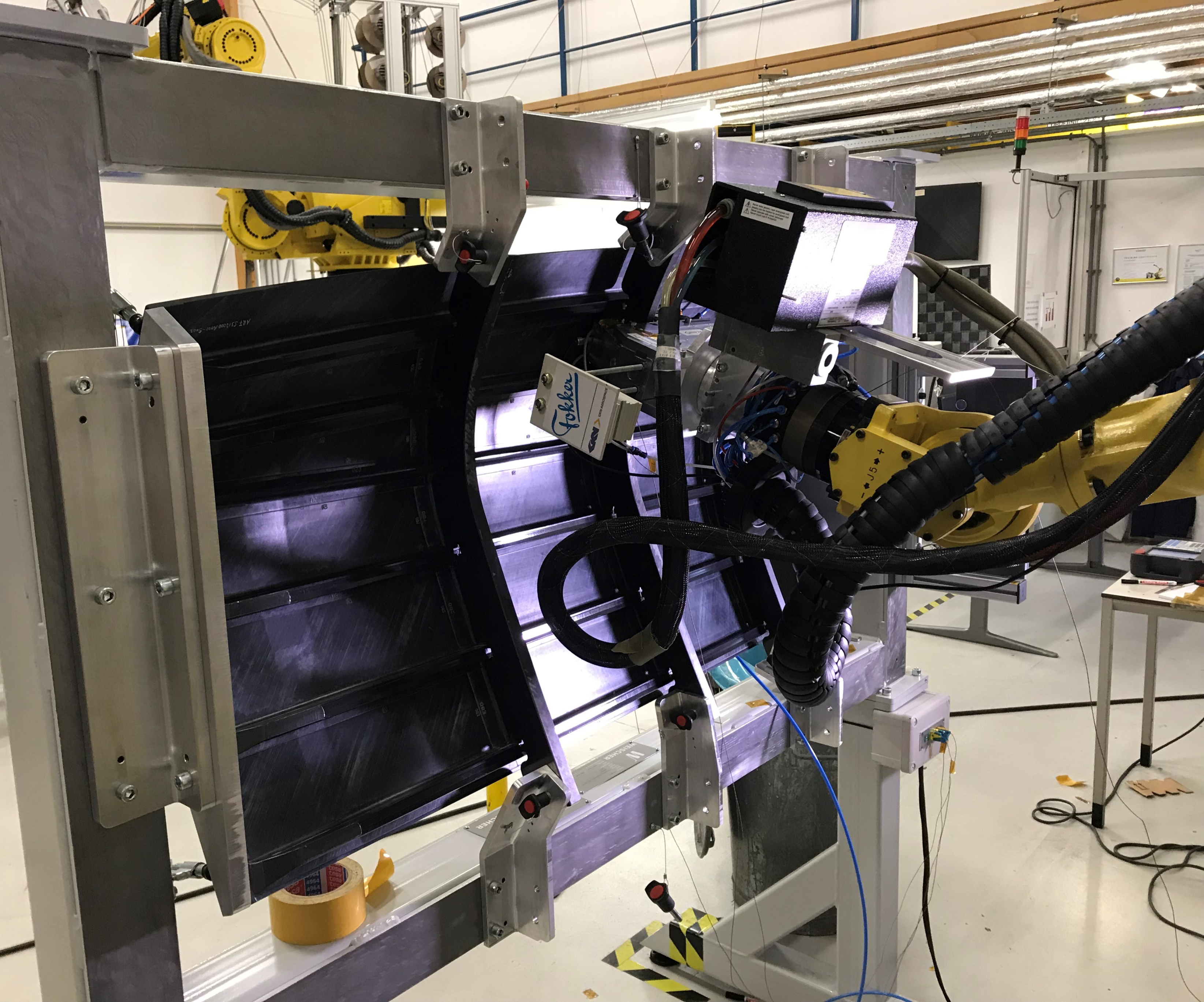
Автоматическая сварка. Содействуя экономической целесообразности создания панели фюзеляжа из термопластичного композита, компания GKN Fokker разработала и применила технологию роботизированной сварки. Источник | ГКН Фоккер
Комбинация ортосетки и конструкции стыкового соединения обеспечивает соединение ортосетки и рамы без застежек с помощью сварки. Несколько сварочных технологий были разработаны членами команды TAPAS на этапе TAPAS2, включая индукционную, кондуктивную и ультразвуковую сварку. Панель Gulfstream использовала проводящую сварку для соединения стенки рамы с продольным стрингером лопасти. Эта задача выполняется с помощью сварочной головки, установленной на роботе - еще одна разработка, которая способствует рентабельности производства.
Один шаг из нескольких
GKN Fokker начала сотрудничество с Gulfstream в 2017 году, создав концепцию дизайна панели фюзеляжа. В 2018 и 2019 годах последовало проектирование и изготовление нескольких изогнутых панелей, а в этом году на выставке JEC World был показан знаковый демонстрационный образец первой панели.
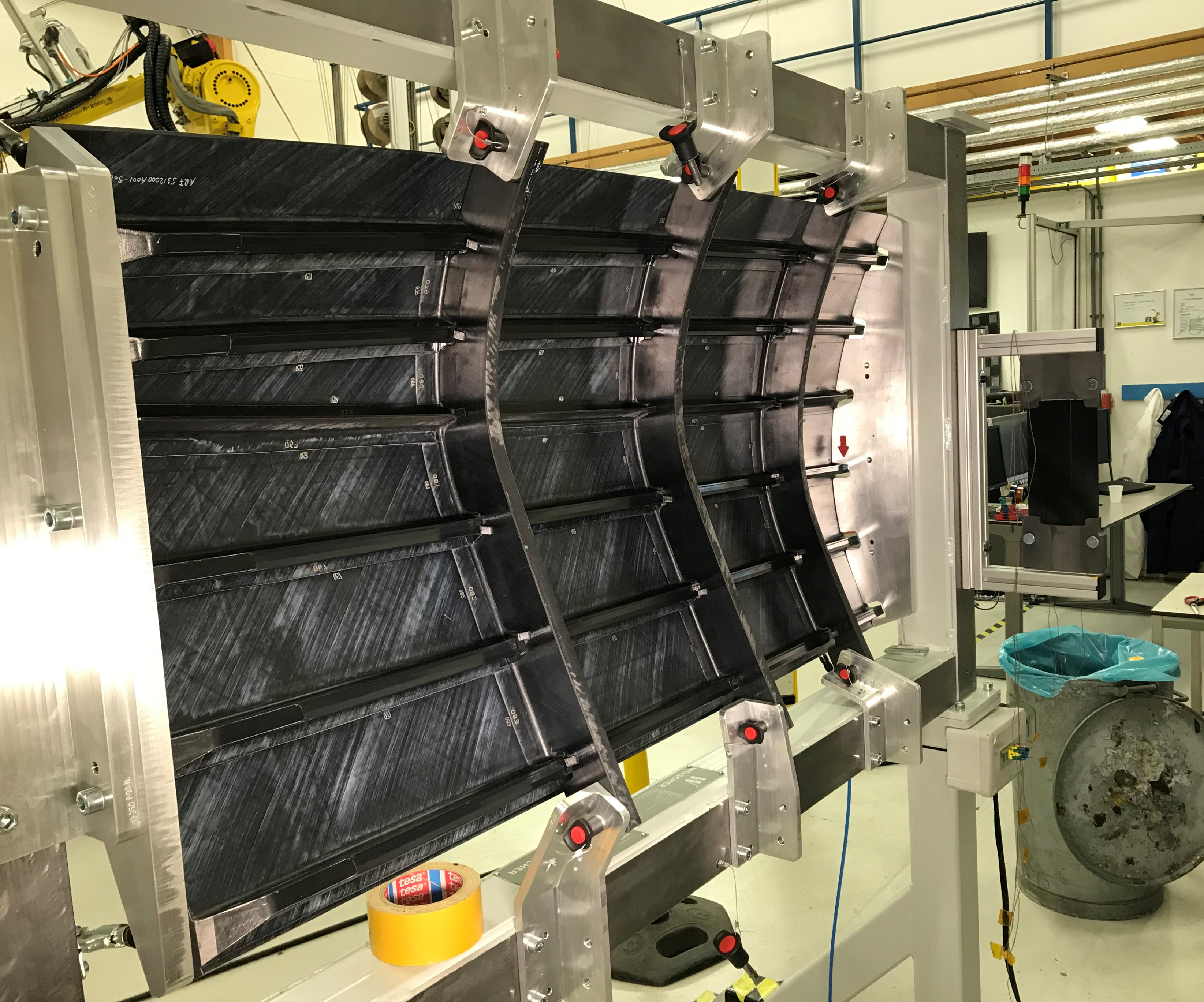
Готовый компонент. С элементами рамы, приваренными к продольным балкам лопастей, панель фюзеляжа Gulfstream готова к испытаниям, оценке и дальнейшему развитию, поскольку компании работают над производством фюзеляжей из термопластичных композитов. Источник | ГКН Фоккер
GKN Fokker продолжает производство панелей и рассчитывает достичь TRL4 (проверка компонентов) в конце этого года. «В настоящее время мы обсуждаем путь к полной зрелости», - сообщает Offringa. Указывая на то, что конструкция панели не нацелена на конкретную платформу, Чепмен сообщает, что испытания панели помогут углубить понимание компанией Gulfstream свойств и рабочих характеристик материалов. Что касается более широкого экономического обоснования первичных структур из термопластического композита, включая характеристики струи, стоимость производства, стоимость использования и долговечность, Чепмен отмечает:«Мы получим лучшее понимание этого по мере дальнейшего продвижения по пути исследований и разработок. На данный момент мы сосредоточены на создании этих сложных форм с минимальными затратами ».
Смола
- Covestro увеличивает инвестиции в термопластические композиты
- Запущены суперконцентраты термопластов, армированных графеном
- Solvay увеличивает емкость термопластичного композитного материала
- Новый поворот в переговорах о тарифах
- Термопластические композиты в Oribi Composites:CW Trending, эпизод 4
- Институт конструкций и дизайна DLR увеличивает зрелость термопластичных композитных конструкций фюзеляжа
- Suprem расширяет возможности термопластов
- Сварка термопластичных композитов
- Дизайнерам необходимо воспользоваться тенденциями индустрии литья под давлением
- Советы по проектированию для литья под давлением