Композиты 4.0:цифровая трансформация, адаптивное производство, новые парадигмы
Composites 4.0 - это одна маленькая галактика во вселенной Индустрии 4.0, которая представляет собой цифровую трансформацию того, как товары и услуги проектируются, производятся, доставляются, эксплуатируются, обслуживаются и выводятся из эксплуатации. При производстве композитов цель состоит в том, чтобы использовать автоматизацию, датчики и данные, связь 5G, программное обеспечение и другие постоянно развивающиеся цифровые технологии, чтобы сделать продукты и процессы более эффективными, интеллектуальными и адаптивными.
Производители композитов проходят через эту цифровую трансформацию по всему спектру. Первоначальные шаги включают поточный контроль и оптимизированные процессы, которые сокращают отходы и затраты, одновременно повышая качество деталей и выход продукции. Более продвинутые решения направлены на интеллектуальное автономное производство, которое не только гибко, но и реагирует на запросы и даже ожидает меняющиеся рынки и потребности клиентов.
«Composites 4.0 - это не конец, а инструмент», - объясняет д-р Майкл Эмонтс, управляющий директор AZL Aachen Center for Integrative Lightweight Production при RWTH Aachen University (Ахен, Германия), чей проект iComposite 4.0 продемонстрировал адаптивную цепочку процессов с потенциал снизить стоимость поддонов для автомобильных полов на 50-64%.
«Существует разница между простым внедрением цифровых технологий и цифровой трансформацией, которая фактически меняет процессы, лежащие в основе вашего бизнеса, и открывает новые возможности и бизнес-модели», - утверждает Кристиан Коппенберг, управляющий директор производителя композитных деталей Dynexa (Лауденбах, Германия).
«Composites 4.0 - это не просто использование роботов», - утверждает доктор Михаэль Купке, глава Центра легких производственных технологий (ZLP, Аугсбург) Немецкого аэрокосмического центра (DLR), который разработал рабочую ячейку с искусственным интеллектом [AI]. где коллаборативные роботы могут переключиться с производства композитных задних переборок давления на панели фюзеляжа без перепрограммирования или переобучения. «Это технология, которая гарантирует, что вам не придется обучать роботов, потому что для этого нет экономического обоснования. Composites 4.0 - это больше, чем просто повышение эффективности и сокращение затрат. Это изменение в том, как компании думают и подходят к производству, что определит, какие компании выживут, а какие нет ».
Адаптивное предварительное формование, RTM
«Идея проекта iComposite 4.0 заключалась в создании преформ из экономичных ровингов и жгутов путем объединения сухого, длинного стекловолокна (25-30 миллиметров), напыленного и впоследствии армированного сеткой из однонаправленных (UD) углеродных волокон с помощью автоматизированного размещения волокон. (AFP) », - поясняет Эмонтс. «Выбранный демонстрационный образец, задний поддон под полом автомобиля, ранее был изготовлен из более дорогих тканей, которые также давали более 60% отходов».
Преобразование Composites 4.0 потребовало интеграции процессов напыления волокна, осаждения волокна и последующего формования с переносом смолы (RTM), чтобы они взаимодействовали друг с другом и адаптировались на основе качества детали, измеренного между этапами (рис. 1). «Мы использовали систему машинного зрения от Apodius GmbH [Ахен, Германия] с оптическим лазерным датчиком и модулем камеры для определения топологии поверхности напыляемой преформы», - говорит Эмонтс. «Apodius адаптировал программное обеспечение для анализа процентного содержания волокон в каждом направлении. Линия iComposite 4.0 сравнила это с цифровым дизайном и решила, соответствует ли он механическим требованиям. Если да, то для армирования применялась стандартная сетка UD. Если нет, было решено, где разместить дополнительные слои волокна UD ».
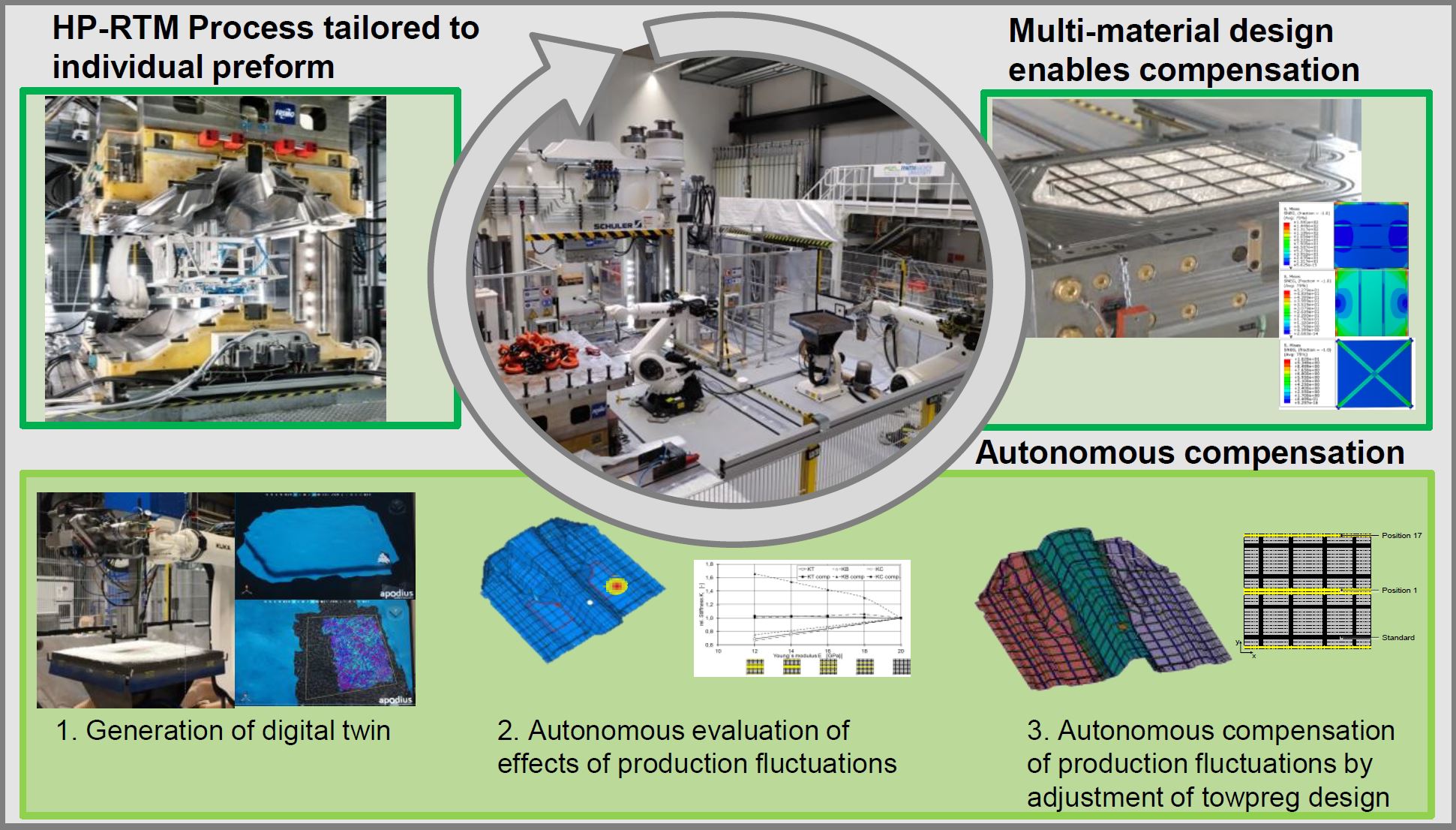
Однако эти дополнительные слои UD могут привести к превышению допусков по толщине и геометрии детали. «Поэтому, - объясняет он, - мы объединили линию предварительного формования с адаптивным процессом RTM, который при необходимости регулирует толщину детали, увеличивая давление на определенные части пресса». Это тоже было автоматизировано с целью заменить вмешательство оператора линии, но требовало моделирования работы детали с использованием данных измерений и стандартного программного обеспечения FEA.
«В настоящее время моделирование механических свойств детали выполняется в автономном режиме», - говорит Эмонтс. «Мы создали базу данных вариаций процессов и деталей, создали алгоритмы реагирования на каждое изменение и проверили их с помощью FEA. Таким образом, на основе изменений, измеренных линией, алгоритмы предписали ей выполнить соответствующее смягчение. Чтобы сделать линию адаптируемой на месте, следующим шагом будет добавление машинного обучения ». Между тем, AZL реализует множество проектов Composite 4.0, включая самооптимизирующееся производство гибридных термопластичных композитов и литых под давлением деталей с интегрированным усилением жесткости специально подобранных заготовок на основе ленты.
Крылья из углепластика без дефектов
Проект ZAero (см. «Производство композитных деталей без дефектов») - еще один ключевой проект Composites 4.0, который стартовал в 2016 году. Он был направлен на повышение производительности для больших конструкций из армированного углеродным волокном пластика (CFRP), таких как крылья крыльев. Дефекты могут быть уменьшены за счет использования автоматизированной поточной инспекции с использованием либо препрега AFP, либо автоматизированного размещения сухого материала Danobat (Эльгойбар, Испания) (ADMP, см. «Доказательство жизнеспособности сухих тканей, инфузия для больших аэроструктур»). Мониторинг процесса во время инфузии смолы или отверждения препрега может спрогнозировать состояние отверждения и сократить время цикла. Собранные данные о процессах и дефектах использовались с FEA для прогнозирования характеристик деталей. Затем это было введено в инструмент поддержки принятия решений по устранению выявленных дефектов. Было разработано моделирование потока деталей для крыльев из углепластика, которое при использовании в этом инструменте помогло оптимизировать стратегию доработки (рис. 2). Сегодня многие такие детали переделываются во время производства, но только после NDI. Ранее переделки и улучшенное управление технологическим процессом действительно были целями проекта ZAero, а также способствовали его целевому увеличению производительности на 15% и сокращению производства на 15-20%. себестоимость продукции и на 50% меньше отходов.
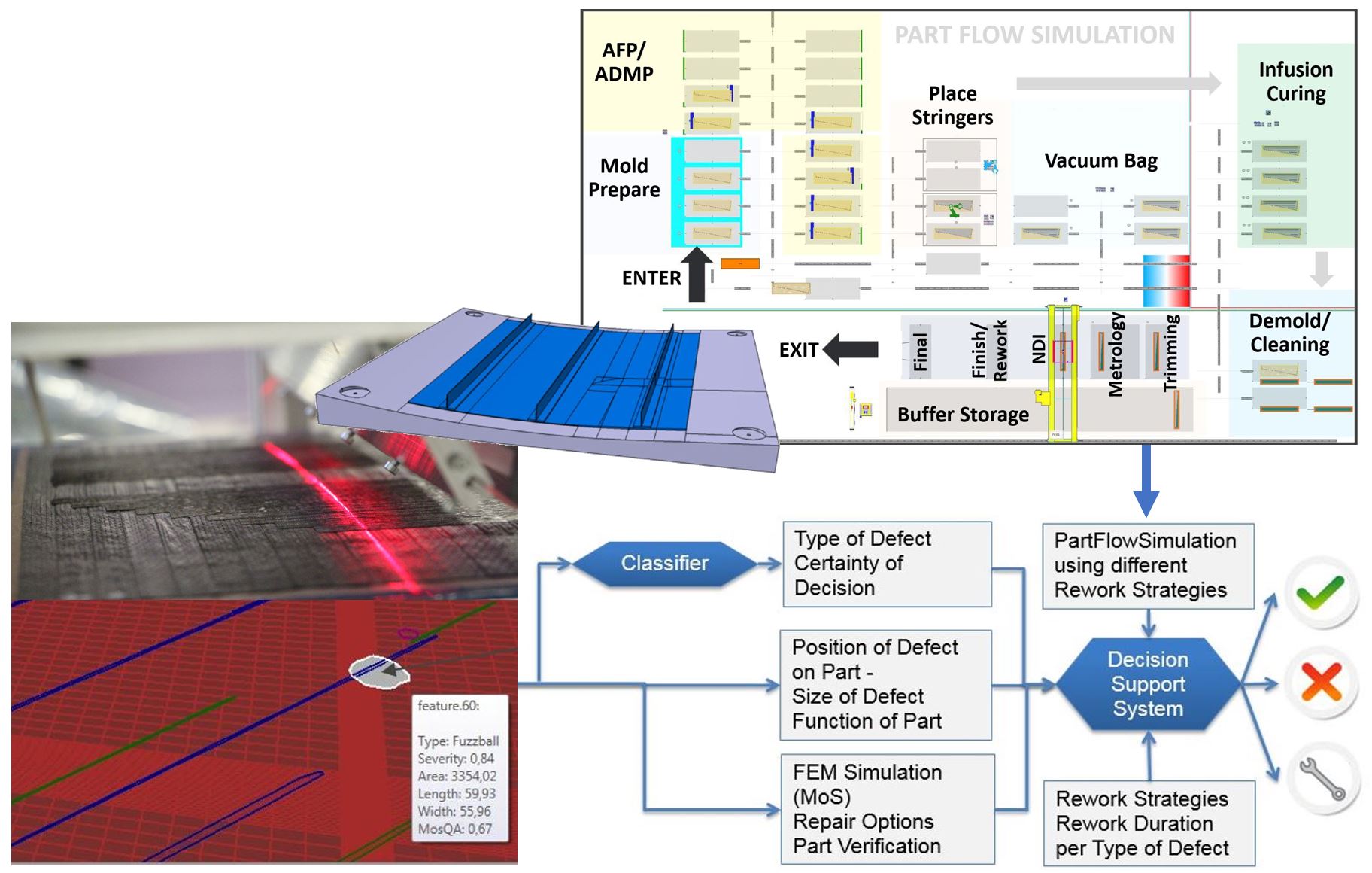
К моменту окончательной проверки в сентябре 2019 года датчик AFP из препрега, разработанный руководителем проекта Profactor (Штайр, Австрия), не только обеспечивал автоматическую поточную проверку, но также мог использоваться для исправления деталей на месте. «Этот датчик может обнаруживать стандартные дефекты, такие как зазоры, перекрытия, FOD, пушистые комки и скрученные жгуты, а также раннюю и позднюю обрезку каждого жгута», - говорит д-р Кристиан Эйтзингер, руководитель отдела машинного зрения компании Profactor. Отсутствующий буксир можно исправить автоматически, разместив дополнительный буксир точно там, где он был пропущен. Однако машину необходимо остановить, чтобы удалить пушистые комки или перекрученную паклю. «База данных, созданная с использованием 3D-опыта Dassault Systèmes (Париж, Франция) для CATIA, позволяет нам рассчитывать влияние на производительность детали в зависимости от размера, формы и типа дефекта. Обработка всех дефектов в слое занимает всего несколько секунд. Затем оператор станка решает, какие дефекты можно оставить, а какие исправить ».
Для мониторинга и управления процессом инфузии компания Airbus (Тулуза, Франция) через дочернюю компанию InFactory Solutions (Тауфкирхен, Германия) разработала три датчика, которые измеряют температуру, состояние отверждения и фронт потока смолы (см. «Датчики для мониторинга фронта потока инфузии смолы». ) «Мы интегрировали их с CATIA 3D Experience и показали, что данные могут быть надежно получены и добавлены в цифровой поток каждой части», - говорит Эйтзингер. (См. Врезку в Интернете «Композиты 4.0:Цифровая нить против цифрового двойника».)
Последней из трех частей была подсекция обшивки верхнего крыла с тремя стрингерами (см. Врезку онлайн «Обновление проекта ZAero»). В этой части инструмент поддержки принятия решений Profactor был продемонстрирован в прямом эфире в партнерской компании FIDAMC (Мадрид, Испания), подключенной к моделированию частичного потока, основанной на программном обеспечении Tecnomatix Plant Simulation компании Siemens PLM (Плано, Техас, США), работающей на сервере Profactor в Австрии. Помимо создания базы данных дефектов, ZAero провела эксперименты с машинным обучением. Созданные вручную генеративные компьютерные модели в сочетании с глубокими нейронными сетями обнаруживают и классифицируют дефекты, обеспечивая 95% правильную классификацию различных областей (разрыв, перекрытие, буксировку, нечеткий шар) в реальных данных мониторинга ADMP, даже если искусственно созданные данные о дефектах использовались для глубокого обучения сети (аналогично тому, как системы ультразвукового контроля калибруются по целому ряду преднамеренных дефектов).
«Мы обязательно продолжим какой-то следующий этап», - говорит Эйтзингер. Между тем, Profactor продает модульные датчики ориентации волокна и дефектов во время автоматической укладки. InFactory Solutions также предлагает свои датчики AFP и инфузии смолы, а партнеры по размещению волокна Danobat и MTorres (Торрес-де-Элорз, Наварра, Испания) теперь продают свое оборудование со встроенной системой контроля.
Путь Dynexa к цифровой трансформации
Dynexa - производитель композитных деталей, специализирующийся на трубах и валах из углепластика. «Мы всегда пытались все оцифровать», - говорит управляющий директор Коппенберг. «Мы уже избавились от ручных и аналоговых процессов, интегрировав все в основном в нашу систему ERP [планирование ресурсов предприятия]. Но как это сделать на производстве? Мы понимали, что все, что мы вкладываем в рабочий протокол или процедуру, - это код, и это основа для цифровой трансформации. Но где это хранится? На локальном сервере, в облаке или на машине? Мы бы спросили пять человек и получили семь ответов о том, что нам делать ». (См. Врезку в Интернете, «Композиты 4.0:с чего начать?»)
К счастью, правительство Германии разработало программу для университетов по предоставлению бесплатных консультаций по Индустрии 4.0 для малых и средних предприятий (МСП). Dynexa начала работать с Дармштадтским центром компетенции «Mittelstand (SME) 4.0». «Они сказали, что не стоит беспокоиться о цифровой архитектуре, а лучше подумать о том, что вам нужно измерить и как это сделать», - вспоминает Коппенберг. «Мы выбрали один процесс, который требовал значительного ручного измерения, когда мы знали, что у нас есть проблемы с качеством, временем и стоимостью».
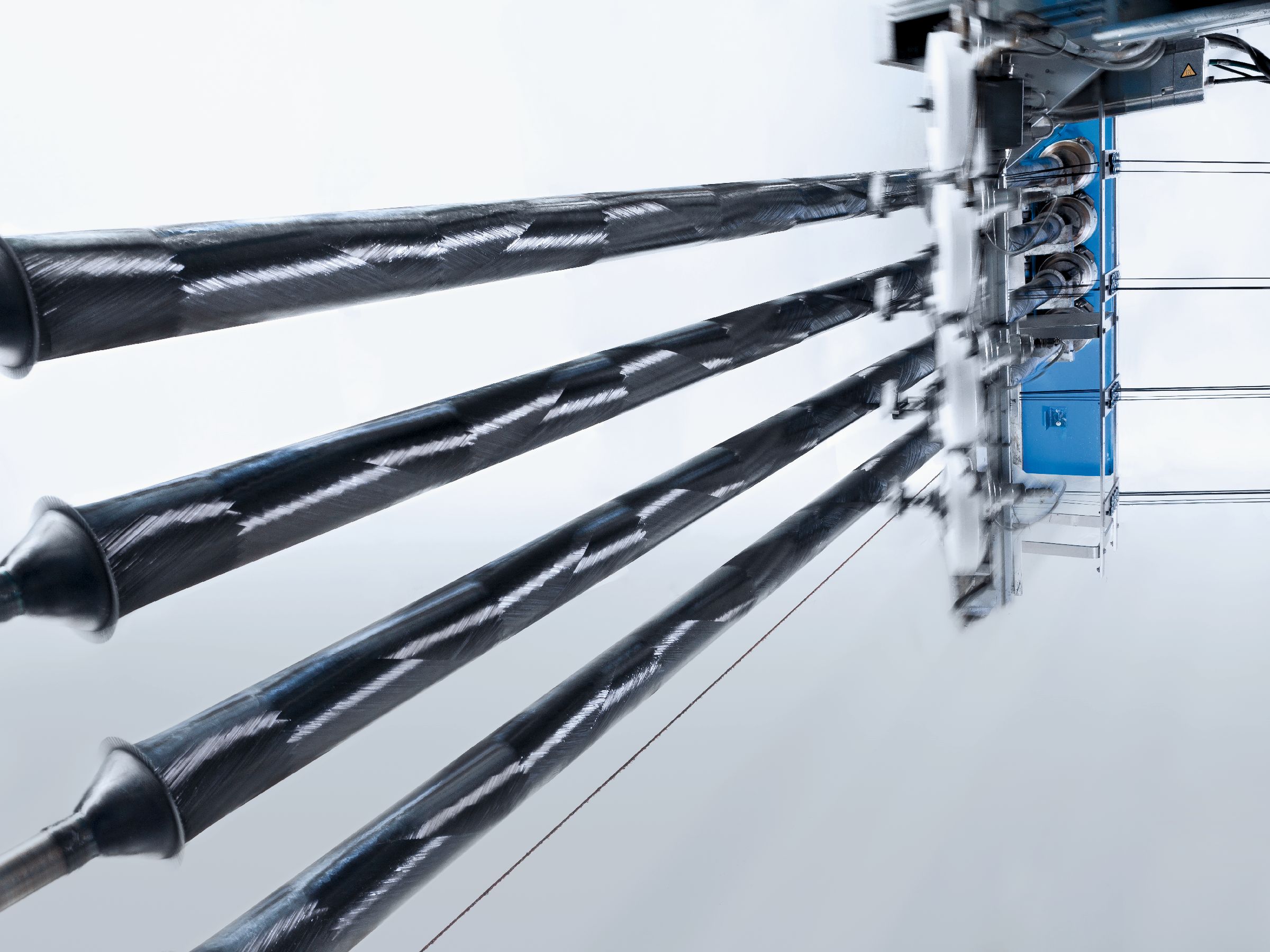
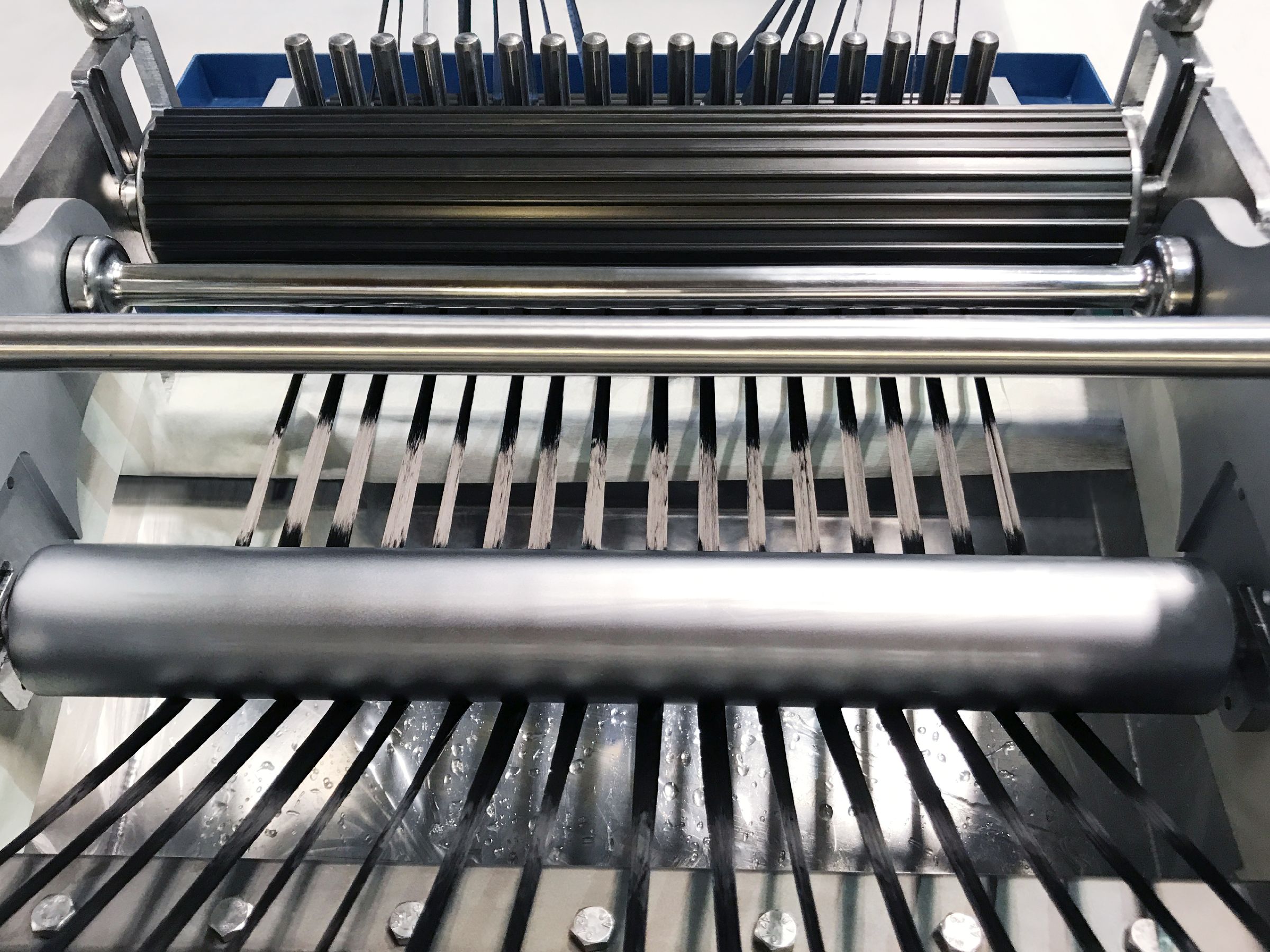
Dynexa использует процесс мокрой намотки нити (см. «Выходной вал из композитного материала, готовый для автомобильного испытательного полигона)». Ключевым этапом является сбор смолы, когда сухое волокно перемещается на уплотняющий валок, который скатывается из ванны со смолой. Напротив уплотняющего валика находится ракельный нож, который определяет количество смолы, которое необходимо соединить с сухой нитью перед ее намоткой. «Если мы соберем слишком много смолы, мы можем превысить указанный диаметр трубы, - говорит Коппенберг, - но при слишком малом количестве смолы мы рискуем упасть ниже минимально допустимого диаметра».
«Без измерения вы узнаете только окончательный диаметр после отверждения, когда вложена вся стоимость», - отмечает он. «Итак, оператор должен остановить машину, измерить деталь, записать ее и затем перезапустить. По многолетнему опыту мы знаем, какой должна быть толщина ламината на каждом этапе намотки. Таким образом, оператор сравнивает измерения и регулирует дозирующее лезвие для корректировки захвата смолы по мере необходимости, но это делается вручную и зависит от навыков и опыта оператора ».
Чтобы оцифровать это, Dynexa поговорила с множеством производителей лазеров и фотоаппаратов. «Они скажут:« У нас есть решение », но тогда никто не сможет заставить его работать», - отмечает Коппенберг. Команда Университета Дармштадта, однако, позволила использовать камеру, вычислив поправки, необходимые из-за определенных физических факторов, таких как отражение света от влажной поверхности. «Теперь у нас есть намоточная машина, подключенная к измерительному устройству, которое работает очень стандартизированным образом», - добавляет он.
Команда разработала базу данных таблиц коррекции и алгоритмов принятия решений, которые позволяют машине намотки нити знать, какой должна быть цель для каждой стадии конкретной наматываемой трубы. «Если входной сигнал измерительного устройства показывает, что смола находится не там, где должна быть», - объясняет Коппенберг, - «машина для намотки нитей реагирует регулировкой ракельного ножа, чтобы вернуть его в соответствие с характеристиками, не останавливая намотку для измерения».
Теперь каждая намоточная машина имеет цифровую измерительную систему, и карта Ethernet. «Самой дорогой частью была установка и прокладка кабелей к серверу, - шутит Коппенберг, - но теперь мы можем разговаривать с каждой машиной и собирать все данные». И есть еще одно преимущество. «Раньше операторы программировали на станках, но как только мы подключили их к серверу, мы можем программировать на любом настольном или портативном компьютере. Это еще больше сократило время простоя и устранило еще одно узкое место в производстве ».
Этот первый цифровой шаг позволил Dynexa улучшить контроль, качество и эффективность процессов, что позволило компании стать более рентабельной. Это также стимулировало дальнейшие преобразования.
Изменение парадигм для композитов
«Мы находимся в поэтапном процессе создания новой экосистемы для наших клиентов», - говорит Маттиас Брукхофф, глава отдела продаж и маркетинга Dynexa. Он приводит пример:«В Amazon вы можете видеть, что вы купили и когда, а также предлагаемые новые продукты. Раньше мы изучали требования клиентов, а затем через несколько дней отвечали на них, используя наши инструменты для расчетов и проектирования. Теперь это будет онлайн. Наши клиенты изучат продукты и рассчитают, что им нужно, стоимость и доставку за считанные минуты. Это не ново, но есть для нашей отрасли. Подобно тому, как мы освободили наших операторов станков, чтобы они могли сосредоточиться на большем количестве машин и задачах более высокого уровня, теперь мы освободим нашу команду инженеров, чтобы сосредоточиться на более специализированных и сложных продуктах ».
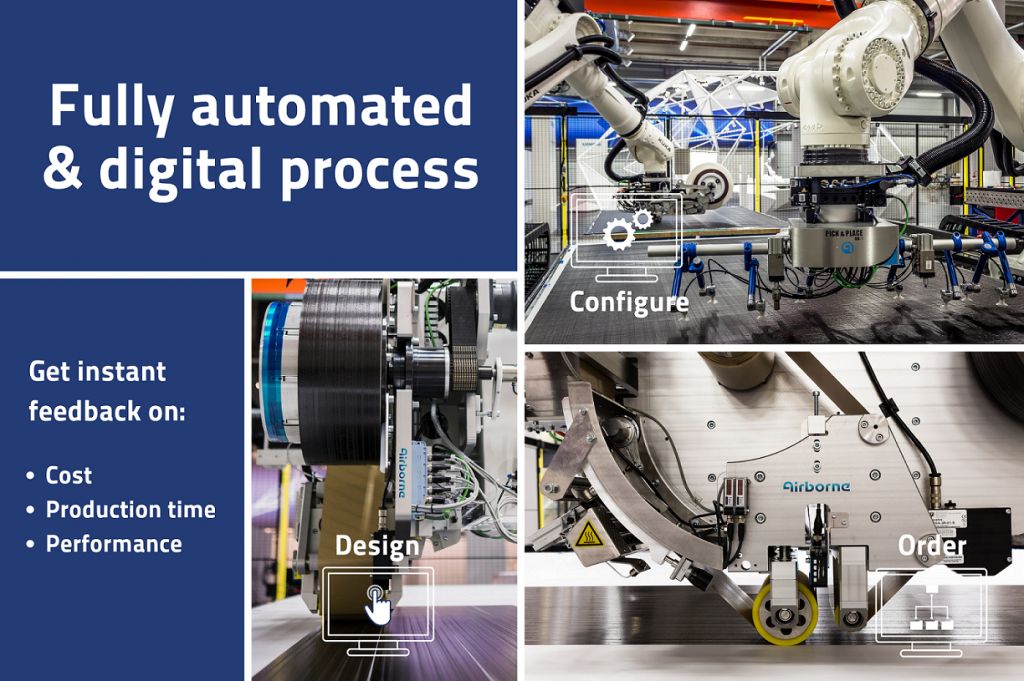
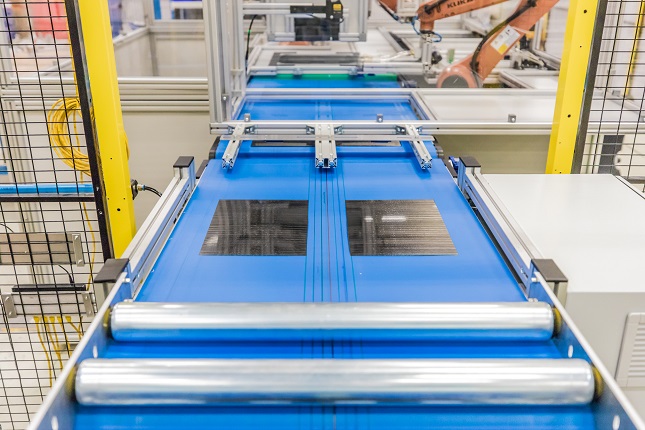
Airborne (Гаага, Нидерланды) запустил свой производственный портал по требованию для автоматизированного производства композитов в сентябре 2019 года (см. «Airborne запускает портал для композитной печати»). Используя этот инструмент, клиенты вводят дизайны в веб-платформу. Затем система на лету создает машинный код и определяет продолжительность и стоимость производства. Затем продукты могут быть настроены и, после заказа, произведены в автоматизированной производственной ячейке. Портал был запущен с использованием автоматизированного ламинатора (ALC) Airborne для обработки термореактивного препрега. Он будет распространен на другие процессы, например, на линию по производству крупносерийных термопластичных композитов (TPC), разработанную для бизнес-подразделения SABIC (Эр-Рияд, Саудовская Аравия).
«Этот портал является ключевым элементом нашего видения цифрового будущего производства композитов», - говорит Маркус Кремерс, технический директор Airborne. «Пять лет назад мы перешли от бизнес-модели производства деталей к помощи клиентам в автоматизации и оцифровке. Мы разрабатываем портфель решений, которые упрощают клиентам создание композитных материалов ». Этот портфель включает в себя ALC, автоматизированную заливку сотовыми заполнителями, автоматическую компоновку слоев и линию большого объема с использованием лент TPC, получившую название Digital Composites Manufacturing Line (DCML) от SABIC и Falcon от Airborne. Последний пример индивидуальных решений Airborne. «Мы встраиваем наши знания о производстве композитных материалов и деталей в эти автоматизированные системы, чтобы клиентам не приходилось быть специалистами», - говорит Кремерс.
У Airborne есть три бизнес-модели:купить автоматизацию, арендовать ее или оставить Airborne для работы через производство как услугу (MaaS). Бортовые автоматизированные ячейки имеют датчики и встроенные системы контроля, которые генерируют предупреждения на основе базы данных дефектов и допусков, определенных заказчиком. «Линия Falcon имеет очень низкие допуски на визуальные дефекты качества, - отмечает Кремерс, - но наша автоматизация для аэрокосмической промышленности больше зависит от конструктивных допусков. Мы также постоянно совершенствуем наши технологии, чтобы они были самообучающимися и адаптирующимися. Например, наша следующая версия программного обеспечения для укладки ленты ALC будет иметь возможность выявлять дефекты и изменять производственную программу на лету ».
В долгосрочной перспективе видение состоит в том, чтобы расширить портал по запросу для сбора производственных мощностей по производству композитных деталей, распределенных между несколькими компаниями и регионами. Кремерс цитирует компанию Protolabs (Мейпл-Плейнс, Миннесота, США), которая предоставляет прототипы, изготовленные методом литья под давлением, из листового металла, обработанные на станке с ЧПУ или напечатанные на 3D-принтере, по запросу всего за день. Точно так же онлайн-приложение Plyable’s (Оксфорд, Великобритания) предоставляет формы для производства композитов, предлагая различные материалы, от полиуретановой плиты до стали, включая композитные инструменты и инструменты, напечатанные на 3D-принтере. «Это другой способ организации цепочки создания стоимости», - говорит Кремерс. «Мы создаем машины и программное обеспечение, которые сделают это возможным для композитных деталей».
AZL Aachen также преследует эту цель со своей сверхбыстрой машиной для уплотнения, разработанной для производства многослойных ламинатов TPC менее чем за пять секунд. Внедрение в производство в 2019 году, в нем используются роботизированные аппликаторы AFP с лазерной системой управления Conbility (Ахен, Германия) и ленты UD шириной 25 мм, а также принцип поштучной печати - новейшее достижение в индустрии высокоскоростной печати. для производства ламината TPC, просто скрепленного или полностью закрепленного, различной толщины с местным усилением. «Наше видение состоит в том, чтобы предоставить масштабируемые машины, которые позволят использовать онлайн-платформы», - говорит Эмонтс. «Линии могут иметь несколько станций, каждая с несколькими аппликаторами AFP. Заказчик вводит требования и получает варианты plybook, стоимости и доставки. После завершения аппликаторы общаются друг с другом для организации производства, а не с оператором. Это полностью интеллектуальное производство композитных материалов на заказ ».
Автоматизация автоматизации
ZLP специализируется на автоматизированном производстве конструкций из углепластика. «Трудно оправдать автоматизацию только одной части или программы», - отмечает Флориан Кребс, руководитель группы ZLP по гибкой автоматизации. «Однако, если вы перейдете от машин для решения конкретных задач к платформе автоматизации, которую можно реконфигурировать практически без дополнительных настроек, то теперь у вас есть бизнес-решение. Чем гибче платформа, тем быстрее окупятся инвестиции ».
Рабочая ячейка, показанная на начальных изображениях, была спроектирована как часть проекта ZLP PROTEC NSR для создания семейства деталей, которое следует одному и тому же технологическому маршруту:укладка сухих материалов без обжима и инфузия смолы (см. Врезку онлайн «Нет бизнес-кейс для обучения роботов »). «Этот процесс был разработан для задней герметичной переборки Airbus A350, но вы также можете сделать панель фюзеляжа или крышку крыла на этой линии, потому что шаги аналогичны», - говорит Кребс.
«Для создания гибких платформ автоматизации требуются определенные технологические блоки, включая алгоритмы для роботов, а также датчики и способы понимания данных, которые они производят», - говорит Купке. «Например, производственная линия PROTEC NSR разработана с учетом максимальной модульности - все модули связаны друг с другом, чтобы продемонстрировать самоконфигурируемую, корректирующую и оптимизирующую систему, масштабируемую по размеру и сложности».
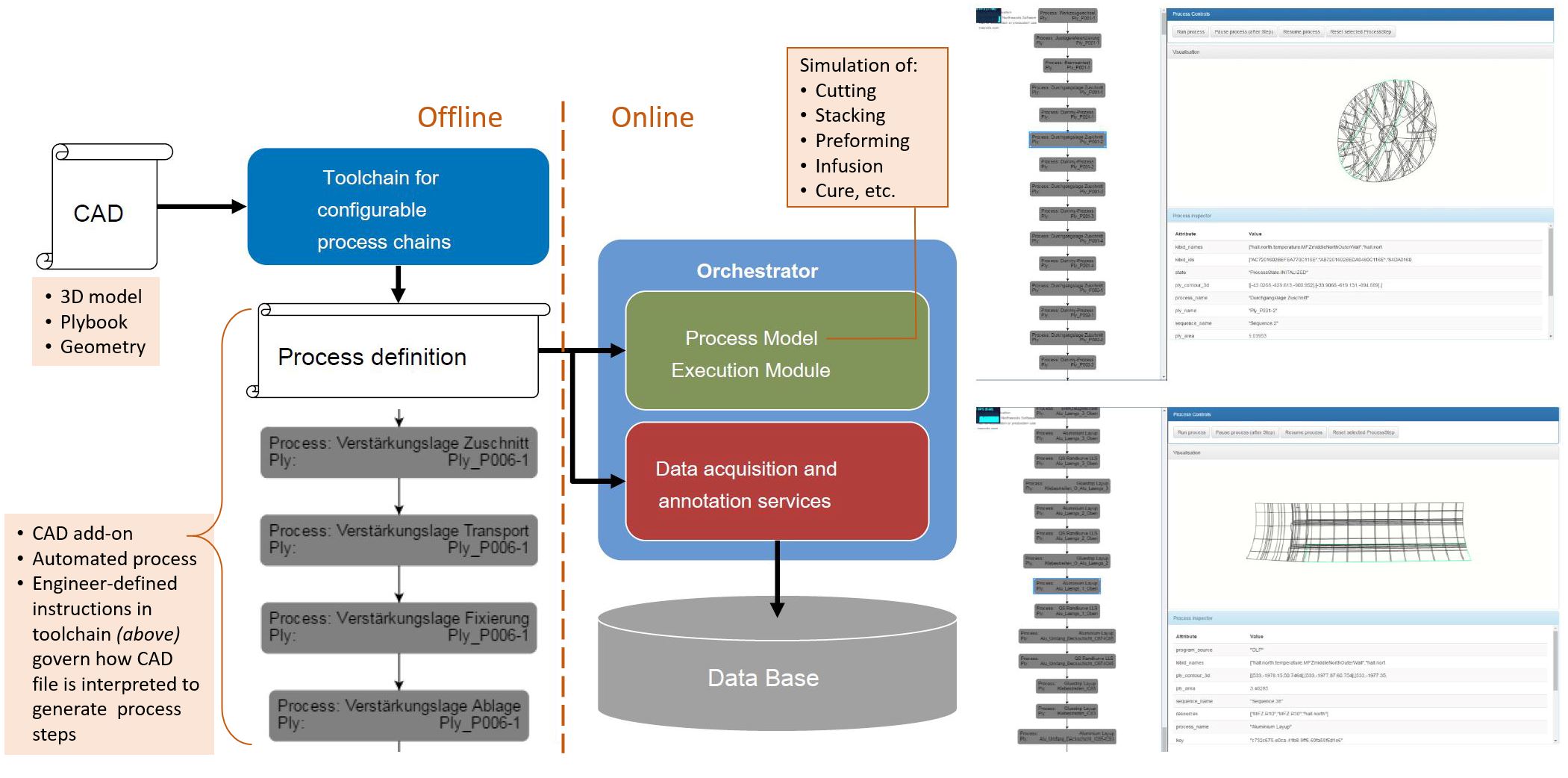
Он объясняет модули, показанные на рис. 5, которые включают модель CAD, определение процесса, модель процесса, которая позволяет моделировать и выполнять процесс, производственный исполнительный модуль, датчики для сбора данных, программное обеспечение для аннотирования данных и базу данных для хранения.
«В левой части этой диаграммы вы составляете план. Модуль выполнения затем реализует этот план », - говорит Купке. «На этапах процесса мы собираем данные со всех задействованных машин и процессов, например, резака, роботов, здания (температура, давление, влажность), камер во время сбора и т. Д. Мы анализируем данные в реальном времени во время процесса, а также автоматически аннотировать собранные данные метаданными, чтобы передать их в базу данных, которая формирует основу для цифрового двойника процесса. Самый важный момент цифрового двойника - иметь одно центральное хранилище, один источник истины. CAD-модель каждой детали и определение процесса являются частью единого источника достоверной информации ».
С этими модулями линия работает автономно одним нажатием кнопки. По модели CAD, производственному плану и камерам роботы определяют, какая вырезанная деталь будет следующей, и ищут ее на столе (например, из 100 других вырезанных деталей). «Они решают, как сконфигурировать захват, чтобы поднять его и положить в инструмент, и знают, где его разместить». На основе производственного плана роботы определяют каждый начальный / конечный путь для всех этапов процесса и знают, когда каждый из них будет выполнен. «Обычно этим путям обучает человек», - отмечает Купке. «Но в нашей системе каждый путь определяется автоматически, без столкновений и в реальном времени. Если вы измените модель CAD или определение процесса, роботы адаптируются без каких-либо дополнительных усилий по обучению. Но что, если полностью поменять деталь? С помощью этого типа автоматизации вы можете внести это изменение очень быстро. Это путь к гибкому производству. Наша роль в ZLP - проложить этот путь, разрабатывая технологические блоки и соединяя их вместе ».
Возможности и онтология
Пандемия COVID-19 подчеркнула важность гибкого производства. Это также создало все более непредсказуемую бизнес-среду. «За последние два-три года ситуация стала более нестабильной, - отмечает Брукхофф из Dynexa. «Наши клиенты хотят получить ответы очень быстро, чтобы отреагировать на них. Предлагая нашу новую онлайн-экосистему, мы делаем всю цепочку поставок более конкурентоспособной ».
Это хорошо известно в авиационной отрасли. «Нам нужна цифровая основа для производственных линий и целых объектов, которая обеспечивает как горизонтальную, так и вертикальную интеграцию», - говорит Марк Фетте, председатель Технического отдела аэрокосмических технологий VDI - Немецкой ассоциации инженеров и главного операционного директора Центра композитных технологий (CTC, Штаде, Германия), R&T, дочернее предприятие Airbus. Проекты CTC в Composites 4.0 включают отслеживание материалов и активов, совместных роботов, расширенные цепочки процессов и многое другое. Но Фетте подчеркивает необходимость онтологии - терминологии и общего протокола для цифровой связи и обмена данными. (См. Врезку в Интернете «Архитектура и онтология Composites 4.0».)
«Вам нужна целостная сеть для всех машин и производственных систем на данном предприятии, - объясняет он, - но это также должно распространяться на всю цепочку создания стоимости, включая такие дисциплины, как проектирование, закупки, логистика и сертификация материалов и процессов. , с одной стороны. С другой стороны, все заинтересованные стороны, такие как поставщики, должны быть рассмотрены и вовлечены в этот процесс изменений. Мы видим много пилотных проектов, но если посмотреть в деталях, все еще не хватает стратегии для целостного подхода к каждой компании или производственной цепочке ».
Он продолжает:«У нас очень большая глобальная сеть поставщиков, и они предъявляют те же требования, чтобы работать как цифровая цепочка поставок. Большинство наших поставщиков - это малые и средние предприятия, работающие как с производителями самолетов, так и с Airbus и Boeing. Если не обсуждается общий стандарт, вы перекладываете эти задачи на поставщиков. Скорее всего, они не могут позволить себе соблюдать два набора различных стандартов для всех своих машин, включая документацию, оценку данных, кибербезопасность и т. Д. »
Фетте признает, что это большие идеи, и говорит, что производители самолетов создают планы для решения этих проблем. «Но есть много подобных препятствий, и это действительно сложно, затрагивая не только технологии, но и социальные, экономические, эргономические и правовые вопросы - это процесс изменения мыслей. Мы только в начале пути. Но чтобы добиться успеха, мы должны понимать, что эти новые системы полагаются на людей, и эти люди должны работать не только в OEM-производителях, но и во всей глобальной сети ».
“Markets are becoming more fragmented across all industries and everyone is facing a paradigm shift,” notes ZLP’s Krebs. “Many people don’t see that as an opportunity,” adds Kupke, also of ZLP. But those who do see that opportunity envision democratized access to composites enabled by Composites 4.0, and with that, a much broader market, including applications that we are only beginning to conceive.
Смола
- Оптимизация цифровой трансформации в производстве товаров народного потребления
- Стратегия цифровой трансформации требует нового подхода к работе с талантами
- Управляемая данными цифровая трансформация поднимает Airbus к новым высотам
- Как новая эпоха цифровой трансформации меняет сектор электроэнергетики?
- Evonik построит новое производство PA12
- План успешной цифровой трансформации
- Что такое цифровая трансформация в производстве?
- 7 драйверов цифровой трансформации
- Проблемы цифровой трансформации в производстве
- Цифровая трансформация производства:новогоднее решение