Изготовление цифровых композитов на основе решений
Природа создает удивительно прочные, универсальные и адаптивные структуры, которые растут и функционируют в соответствии с окружающей средой - подумайте о деревьях, костях и хитине. Последний образует как жесткие оболочки , так и гибкие суставы ракообразных. Природные конструкции практически не производят отходов, потребляют очень мало энергии и перерабатываются в конце своей функциональной жизни. В отличие от этого, искусственные конструкции обычно носят предписывающий характер, потребляют большое количество энергии, производят токсичные отходы и в большинстве случаев не перерабатываются. Согласно данным Агентства по охране окружающей среды США за 2018 год, доля переработанных материалов составляет всего 9% для пластмасс (без изменений с 2010 г.), 25% для стекла и 33% для металлов (оба показателя ниже, чем в 2010 г.). Хотя цифровое проектирование и производство быстро развиваются и позволяют производить сложные, многофункциональные конструкции и компоненты, эти технологии еще не сделали того же прорыва в области устойчивого развития.
Это было вдохновением и целью проекта цифрового производства на водной основе, разработанного Mediated Matter Group в Медиа-лаборатории Массачусетского технологического института (MIT, Кембридж, Массачусетс, США), начиная с 2013 года. Эта инициатива позволила создать новое цифровое производство. Технология, сочетающая самые распространенные на Земле природные материалы с роботизированной многокамерной экструзионной системой, которая осаждает различные концентрации биокомпозитных растворов - первым был хитин из панцирей ракообразных и уксусная кислота - для создания структур с анизотропными свойствами. Градиенты механических, химических и оптических свойств достигаются в масштабах от миллиметров до метров, обеспечивая не только уникальную геометрию и многофункциональность, но и потенциал для самостоятельной сборки конструкций. Например, влажные осаждения могут быть спроектированы таким образом, чтобы формировать формы (например, цилиндры) по мере высыхания в ответ на направленные напряжения испарения в многослойных композитах.
Это цифровое производство, основанное на решениях, было задумано как мост между биологической и искусственной средами с потенциальными приложениями в экологичных архитектурных панелях, перерабатываемой упаковке и потребительских товарах или легких биоразлагаемых деталях автомобилей. В конечном итоге Массачусетский технологический институт исследовал композиты с использованием целлюлозных микроволокон, пектина, водорослей и керамических нанопластинок. Но что, если бы вы могли объединить это цифровое осаждение на водной основе с технологиями аддитивной экструзии с непрерывным армированием и короткими волокнами, которые быстро развиваются в современных 3D-печатных композитах?
Почему раствор хитозана?
Первоначальные эксперименты в проекте цифрового производства на водной основе использовали хитозан, полученный из хитина. Хитин, второй по распространенности природный полимер на Земле после целлюлозы, имеет химическую структуру, аналогичную целлюлозе, и включает в себя не только высокомодульные и высокопрочные панцири ракообразных и насекомых, но и прочную, но гибкую ткань в их суставах. «Природные материалы, особенно полимеры и полисахариды, такие как хитин и целлюлоза, - представляют собой обширный возобновляемый ресурс, производимый с гораздо большей скоростью, чем искусственные синтетические полимеры», - объясняет Лайя Могас-Солдевила, один из ключевых исследователей Массачусетского технологического института в этом проекте. Она утверждает, что производные полисахаридов могут заменить существующие полимеры на нефтехимической основе, обеспечивая новые комбинации свойств и обеспечивая более устойчивое производство.
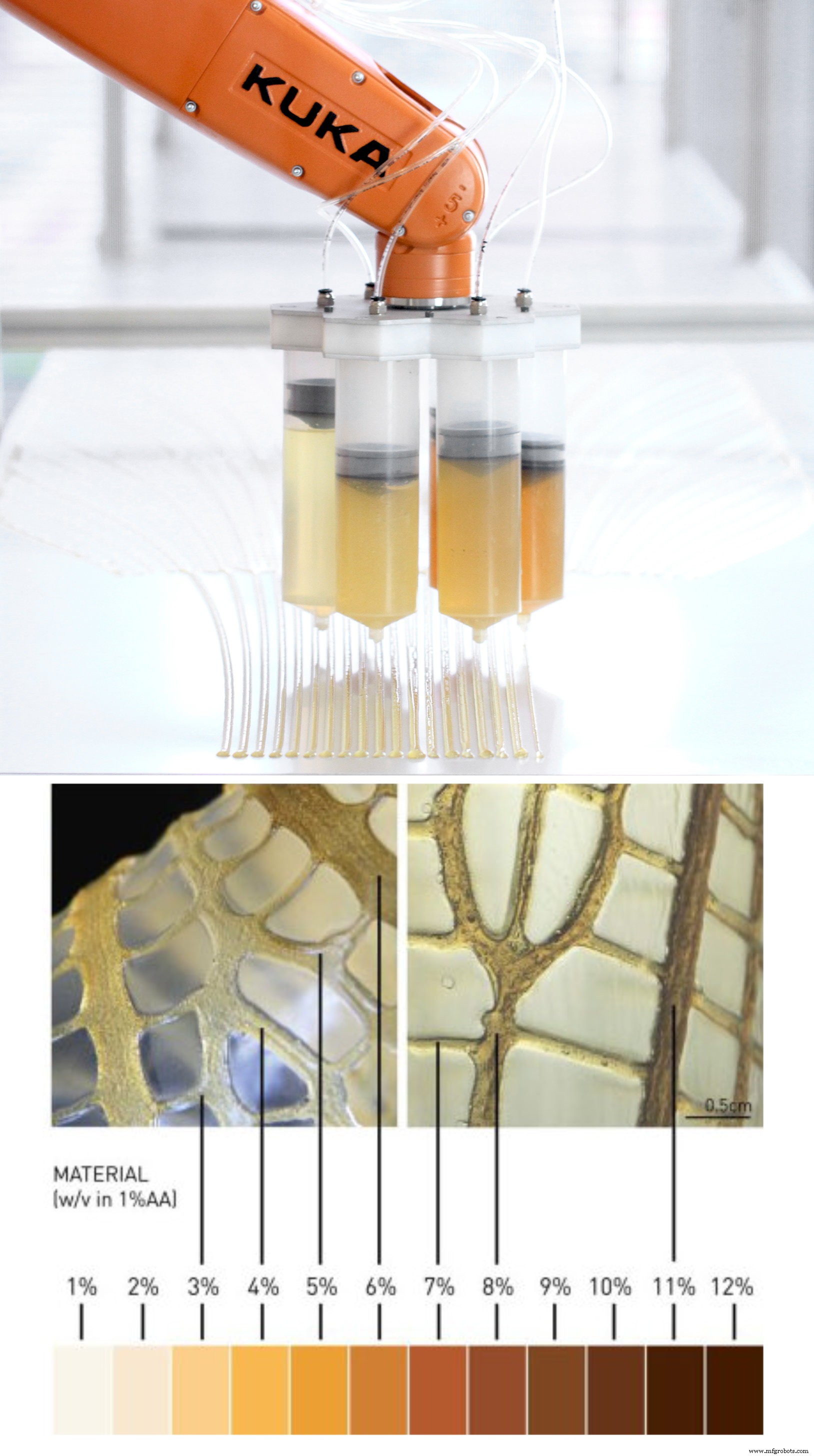
Могас-Сольдевила дает превосходный обзор развития технологий Массачусетского технологического института в своей диссертации 2015 года «Цифровое проектирование и производство на водной основе:исследования материалов, продуктов и архитектуры при печати хитозана и его композитов». Она объясняет, что идея использовать цифровое производство на основе растворов возникла в результате изучения методов струйного и соплового биопроизводства для производства мягких материалов в качестве основы для роста тканей.
Было решено попробовать трехмерное осаждение с помощью форсунки с использованием порошка хитозана, переработанного в гель, при концентрациях массы к объему (мас. / Об.) 1–12% с использованием 4% мас. / Об. Уксусной кислоты в водном растворе. Эти гидрогели варьировались от полупрозрачной жидкости с вязкостью, подобной водянистому меду при концентрации 3%, до непрозрачного материала с консистенцией натурального каучука при концентрации 12% (рис. 1). Первые результаты депонирования и высушивания Пленки хитозана показали предел прочности на разрыв 40 мегапаскалей, который Mogas-Soldevila описал как сопоставимый с нейлоновым полимером или деревом в направлении волокна. Конструкции были изготовлены и отверждены при комнатной температуре.
Новая платформа цифрового производства
Специальная роботизированная платформа для аддитивного производства, разработанная Массачусетским технологическим институтом для нанесения хитозановых гелей, объединила в себе шестиосевую роботизированную руку Agilus KR1100 компании KUKA (Аугсбург, Германия) (54-килограммовая платформа с 10-килограммовой полезной нагрузкой и повторяемостью / точностью ± 0,03 миллиметра) с концевой эффектор на основе экструзии. Новый концевой эффектор содержал шесть цилиндров для гидрогелей хитозана, подключенных к управляемой компьютером системе давления воздуха, которая включала положительное (баллон сжатого воздуха) и отрицательное (вакуумный насос) давление воздуха с цифровым регулятором PSI и двумя шаговыми двигателями для управления экструзией.
Этот концевой эффектор весил 4 кг, включая загруженные шприцы и материал для осаждения. Типичный расход составляет от 8 до 4000 кубических миллиметров в секунду при использовании сопел с внутренним диаметром 0,5-8 миллиметров. Линейное движение системы варьировалось от 10-50 миллиметров в секунду. Площадь наплавки составляла 1000 миллиметров в длину и 500 миллиметров в ширину, однако ограничения по длине позже были сняты с помощью скользящей платформы для печати.
Шаговые двигатели, пневматическая система и роботизированная рука управлялись цифровым способом для координации соотношений подачи / скорости, обеспечения возможности изменения соотношений смешивания и скоростей экструзии, а также регулировки давления и скорости осаждения на лету в зависимости от желаемой геометрии экструзии и свойств материала. Роботизированное движение и выдавливание не были явно связаны, то есть обе функции были независимы друг от друга, что позволяло независимое управление каждым моторным шприцем, а также смещение концевого эффектора роботизированной руки. Система успешно создавала крупномасштабные 3D-формы без форм и позволяла получать широкий спектр геометрических форм с различными структурными свойствами.
Цифровой дизайн для осаждения
Первоначальные производственные испытания были основаны на биологических структурах, таких как листья и крылья стрекозы. Основная продольная структура обеспечила глобальную форму, сделанную с более толстым слоем диаметра и более высокой концентрацией материала для жесткости. Вторичные структуры затем были сформированы осажденными сетками материалов меньшего диаметра и меньшей концентрации. В производственной системе использовалось несколько методов для создания этих структур:применение различных концентрационных растворов по определенным траекториям, цифровое управление давлением во время осаждения для управления шириной и высотой материала и повторяющееся наслоение. Эти стратегии были закодированы в инструкции по положению, скорости, давлению и материалу, которые отправлялись в режиме реального времени роботу KUKA (позиционирование) и концевому исполнительному элементу экструзии (осаждение).
Для начала, структуры были смоделированы в программе САПР, а затем программное обеспечение для срезов преобразовало их в напечатанные слои. Цифровая система управления проверила и оптимизировала пути наплавки. Геометрические траектории инструмента, обеспечивающие управление и работу системы экструзии, были разработаны с помощью программного обеспечения для моделирования Rhino3D (Robert McNeel and Associates, США) и его плагина сценариев Grasshopper.
Затем система закодировала массив независимых параметров, связанных с цифровым дизайном, а также основные механические и химические свойства материала. Он также смягчал зависящие от платформы ограничения, задаваемые производственной системой, такие как вязкость, скорость сдвига, типы стволов, время отклика оборудования и / или размер оболочки. Затем все эти параметры были объединены с зависящими от дизайна вариации, такие как тип форсунки, состав материала и карты давления в зависимости от времени. Полученные в результате расчеты затем выводят необходимые скорости потока, схемы наполнения цилиндров и скорости позиционирования. Наконец, были сгенерированы специальные инструкции по изготовлению, кодирующие команды движения и экструзии для систем позиционирования и осаждения соответственно.
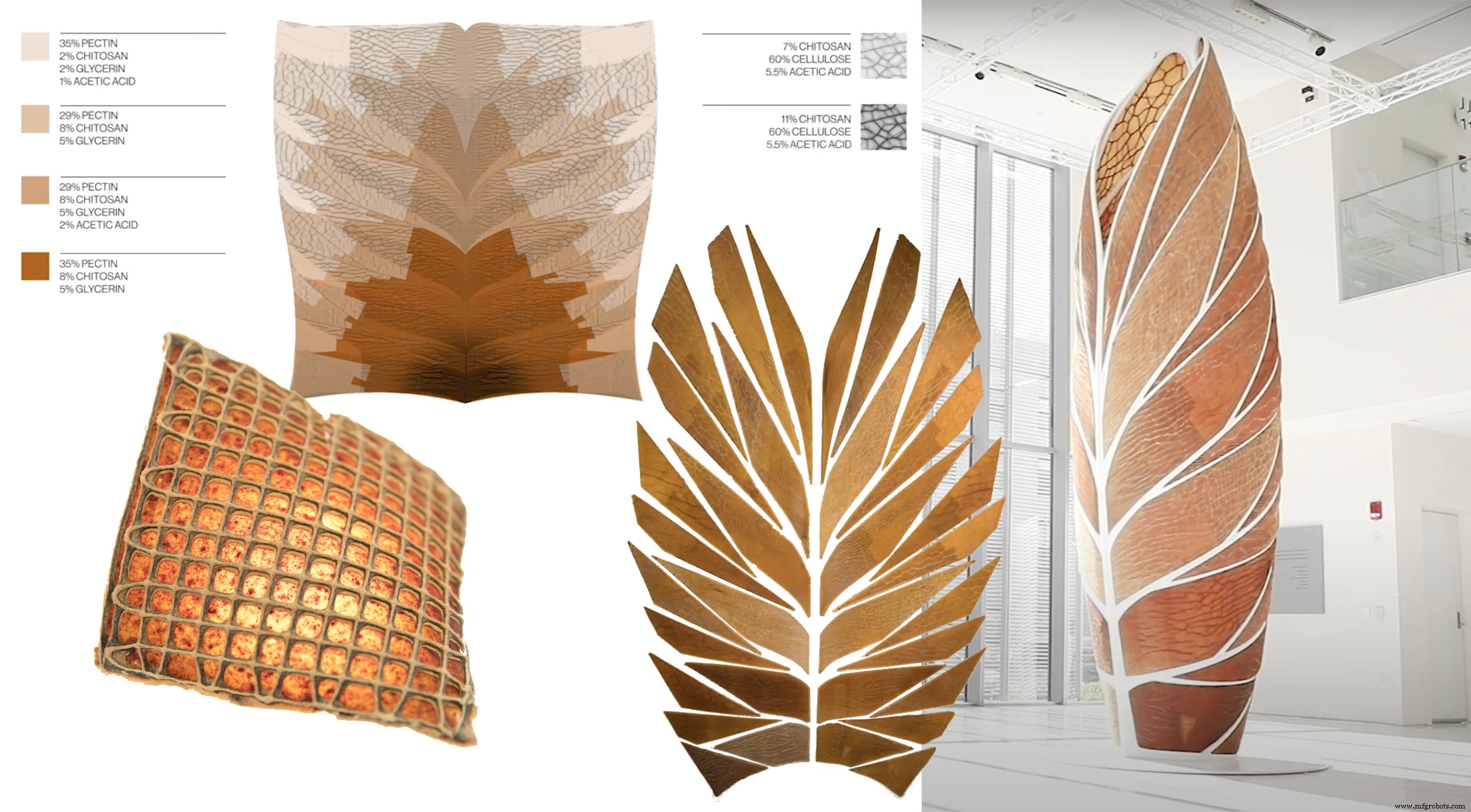
Исследование новых построек
Производственные испытания, описанные Могас-Сольдевилой, включают в себя структуру длиной 50 сантиметров, вдохновленную крыльями стрекозы. Его структурные «жилки» были сделаны из хитозанового геля, загущенного натуральным порошком альгината натрия, на который была наложена прозрачная устойчивая к растяжению мембрана из 3% хитозанового геля. Благодаря самовосстановлению материалов мембрана была прикреплена к прожилкам во время осаждения. Эта концепция была дополнительно исследована на множестве листовидных структур длиной до 3 метров. В другом примере сетка размером 5 x 15 миллиметров была нанесена на плоскую поверхность с использованием раствора целлюлозного микроволокна в 2% -ном хитозановом геле. По мере высыхания он образовывал цилиндр длиной 50 сантиметров, используя возможность расчета внутренних напряжений испарения, как обсуждалось выше.
Эта технология была впервые предложена Хорхе Дуро-Ройо, архитектором, инженером и ведущим исследователем в MIT Mediated Matter Group под руководством профессора Нери Оксман, и получила дальнейшее развитие в проектах Агуаходжа, где были созданы и сформированы кожеподобные структуры («ходжи») с помощью водные растворы («агуа»). Aquahoja I включал в себя архитектурный павильон высотой 5 метров (рис. 2) и библиотеку экспериментов с материалами, которые были выставлены в 2018 году и затем приобретены Музеем современного искусства Сан-Франциско (SFMOMA, Калифорния, США) для своей постоянной коллекции. . Aguahoja II была частью выставки 2019 года, организованной совместно Cube Design Museum (Керкраде, Нидерланды) и Cooper Hewitt, Смитсоновский музей дизайна (Нью-Йорк, Нью-Йорк, США).
Платформа для производства роботов в проектах Aguahoja эволюционировала и теперь включает в себя как роботизированные, так и портальные системы. Павильон состоял из 95 отдельных сегментов, напечатанных на 3D-принтере. Белый корешок был напечатан с использованием имеющейся в наличии системы моделирования наплавленным осаждением F900 (FDM) и термопласта из акрилонитрилстиролакрилата (ASA). Множественные биокомпозитные панели были разработаны с различной степенью жесткости, гибкости и непрозрачности для создания областей, которые служат структурой, окном и фильтром окружающей среды. Некоторые материалы в Aguahoja I меняются в зависимости от влажности и тепла, другие темнеют или светлеют в зависимости от времени года. Материалы варьируются от хрупких и прозрачных до гибких и похожих на кожу, но все они могут быть запрограммированы на разложение в воде (например, под дождем), тем самым восстанавливая составляющие строительные блоки естественной экосистемы.
С тех пор Могас-Сольдевила защитила докторскую диссертацию в Silklab при Tufts Biomedical Engineering (Медфорд, Массачусетс, США), изучая, как использовать шелк и другие натуральные волокна и материалы, в том числе те, с которыми она работала в Массачусетском технологическом институте. Сейчас она доцент кафедры архитектуры в Школе дизайна Стюарта Вайцмана Пенсильванского университета, где преподает и исследует материально-ориентированный дизайн на стыке экологичности и передовых наук о жизни. Некоторые из ее недавних работ можно найти на сайте dumolab.com. «Это природные материалы, которые очень легко поддаются обработке - мы можем смешивать их, добавлять в них и трансформировать. Мы действительно можем настроить их на конкретные производственные возможности. Мы смотрим, что будет завтра ».
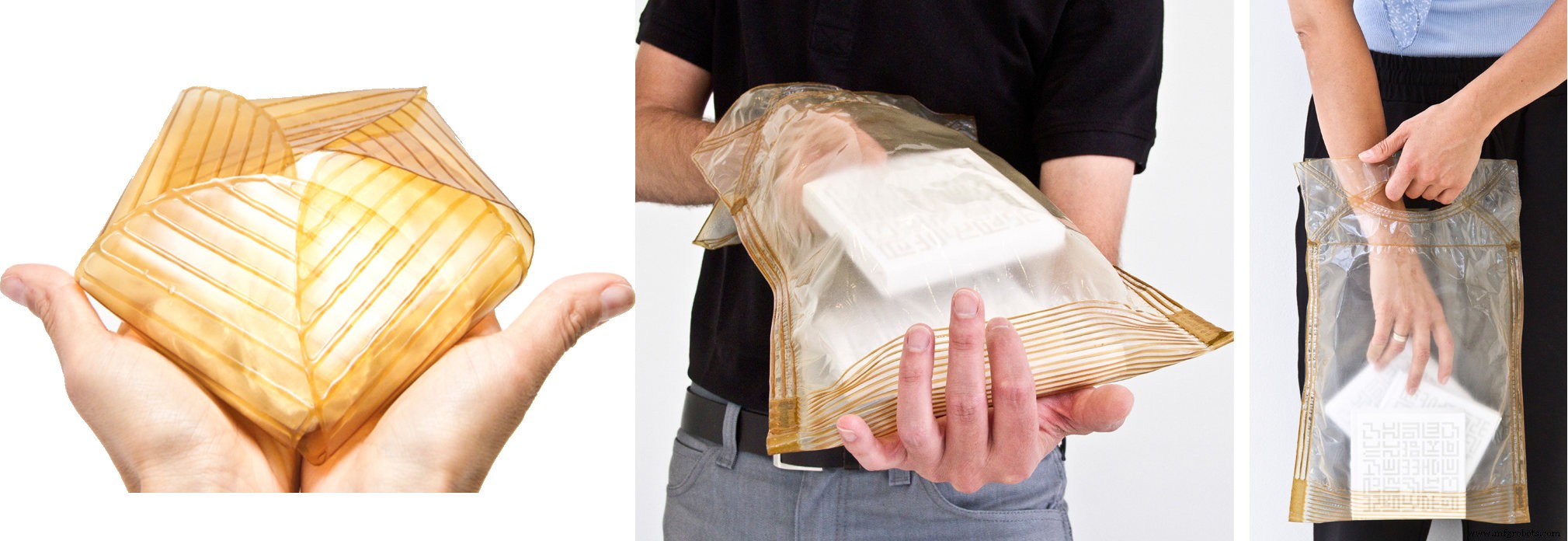
Композитный материал
- Введение в производство металлов
- Использование вольтметра
- Почему цифровой?
- Свойства термореактивных композитов в HVAC
- Инструмент высокого качества для термореактивных композитов
- Причины использования термореактивных композитов в вашем продукте
- Композиты из углеродного волокна на рулоне автомобильных колес
- RS Electric Boats выбирает Norco для изготовления композитов
- Высокопроизводительные композиты в Израиле
- Что такое цифровая рабочая сила?