Статистическая оптимизация условий процесса золь-гелевого электропрядения для получения связок нановолокна полиамида 6/66
Аннотация
Полимерные нановолокна широко изучаются в текстильной промышленности, поскольку с их помощью можно получить самые разные функциональные возможности. В этой статье были приготовлены растворы полиамида 6/66 (PA 6/66) с различными концентрациями (12, 17 и 22% масс.) Для получения нановолокон посредством основного процесса электроспиннинга, которые были охарактеризованы с помощью сканирующего электронного микроскопа (SEM). и продуктивность. Впоследствии жгуты нановолокон были изготовлены с использованием золь-гель процесса электроспиннинга, которые были охарактеризованы с помощью SEM и испытаний на растяжение. По результатам статистической оптимизации, основанной на однофакторном дисперсионном анализе (ANOVA) с post hoc Tukey HSD, было обнаружено, что пучки нановолокон с более высокой производительностью (1,39 ± 0,15 мг / мин), степенью вытяжки (9,0 ± 1,2) и предел прочности на разрыв (29,64 ± 7,40 МПа) был получен при концентрации 17%. Наконец, была проведена тепловая характеристика с помощью дифференциальной сканирующей калориметрии (ДСК), которая обнаружила доказательства T g и T м уменьшение количества нановолокон по сравнению с гранулами PA 6/66 и пучками нановолокон.
Фон
Нейлон - это полимер, классифицируемый как полиамид, который был открыт Уоллесом Хьюмом Каротерсом в 1934 году; выпускается в виде волокна и пластика в зависимости от условий обработки [1]. В продаже имеются различные виды нейлона, нейлона 6, нейлона 66, нейлона 6, 10 и т. Д., Имеющих общую амидную функциональную группу (–CO-NH-) [2]. Этот полимер используется для производства выдувных пленок и моноволокон посредством процессов прядения, и его можно сополимеризовать. Так обстоит дело с нейлоном 6/66, который производится с более низкой температурой плавления по сравнению с нейлоном 6. В последние несколько лет нейлон использовался во многих областях, таких как женские чулки, парашюты, молнии, лески, свадебные вуали, ковры. , музыкальные струны и веревка [3].
Обычные процессы трансформации нитей и нейлоновых нитей - это мокрое прядение, сухое прядение и прядение из геля, и они позволяют производить волокна диаметром от 20 до 400 мкм [4]. Эти процессы, которые осуществляются из растворов полимеров, зависят от концентрации, поскольку их изменение влияет на степень вытяжки и, следовательно, на механические свойства волокон [5].
Процесс электроспиннинга [6] используется даже в нанометровом масштабе для получения нейлоновых волокон меньшего диаметра [7]. Это также позволяет изготавливать полимерные нановолокна с полярностью, пористостью и регулируемым диаметром, которые дополнительно можно адаптировать к большому разнообразию размеров и форм. Кроме того, с помощью этого метода можно контролировать свойства, функциональность и состав нановолокон через концентрацию полимера и параметры электропрядения [8]. Ramkrisna et al. [9] подтверждают, что морфологический результат процесса электропрядения имеет высокую концентрационную зависимость, как и в случае обычных процессов прядения [5]; поскольку более высокая концентрация приводит к более высокой вязкости раствора полимера, по этой причине в исследовании этой статьи концентрация полимера оценивается как уникальная переменная в однофакторном дизайне. Это важно для оценки возможности проведения в промышленных масштабах.
Полимерные нановолокна, полученные методом электроспиннинга, могут быть использованы во многих областях промышленности:каркасы, датчики, фильтры, мембраны, батареи, защитная одежда, перевязочные материалы для ран и катализаторы [10]. В текстильной области нановолокна используются для получения определенных функций, таких как самоочищающиеся ткани, репелленты от вирусов и бактерий, контроль температуры, датчики и фильтры [11]. Также сообщалось о некоторых других применениях текстиля в качестве антибактериальной одежды [12], перевязочных материалов [13] и защитной одежды [14] благодаря их химическим свойствам и механической прочности.
Некоторые другие исследования, связанные с процессом электропрядения, адаптировали его к коагуляционной ванне и натяжным цилиндрам для разработки золь-гелевого процесса электропрядения (см. Рис. 1). В последнем случае пучки нановолокон из поливинилового спирта (ПВС) были охарактеризованы, произведены и применены в качестве вторичного армирования в ультратонких пастах портландцемента, уменьшая ретракцию и ширину трещин в раннем возрасте схватывания [15]. В статье, опубликованной Wu et al. [16] они получили и охарактеризовали агрегированные нановолокна из полиамида 6/66 посредством процесса электропрядения с использованием двух коллекторных валков, которые вращались со скоростью 300 об / мин. Они заявили, что полученные волокна имеют широкий спектр применения в тканевых каркасах, композитном армировании и сверхчувствительных сенсорах [17]. Используя аналогичную методологию здесь, мы представляем результаты и статистическую оптимизацию с использованием ANOVA с апостериорным тестом Tukey HSD для морфологических, производственных механических и термических характеристик пучков нановолокон из полиамида 6/66 (PA 6/66), полученных с помощью такого процесса, при котором было изучено влияние концентрации полимера на конечные свойства получаемых волокон для их последующего использования в текстильной области.
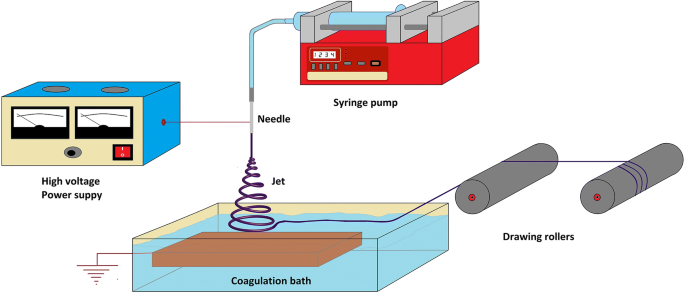
Электроформование золь – гель процесса
Методы
Материалы
Использовался PA 6/66, ссылка Ultramid C40 L, торговая марка Basf. В качестве растворителя использовалась смесь муравьиной кислоты и уксусной кислоты, а в качестве коагуляционной ванны - дистиллированная вода.
Приготовление растворов полиамида
Растворы готовили с различной концентрацией 12% масс., 17% масс. И 22% масс., Используя смесь муравьиной кислоты и уксусной кислоты в качестве растворителя в соотношении масс 4:1 [18], при комнатной температуре. и непрерывное перемешивание.
Базовый процесс электропрядения
Во всех процессах, проводимых с растворами при различных концентрациях, использовалось напряжение 27,5 кВ, подаваемое оборудованием модели E30 компании Gamma High Voltage Research Inc., подключенным к металлической игле, расположенной на расстоянии 12 см от коллектора. Расход раствора контролировали шприцевым насосом от Braintree Scientific Syringe Pump Brand Inc., который был установлен в пределах от 0,3 до 1 мл / ч.
Золь – гелевый процесс электропрядения
Этот процесс проводился с использованием коагуляционной ванны с дистиллированной водой и системы натяжного цилиндра с регулировкой скорости. Мы получили пучки нановолокон PA 6/66 в трех концентрациях (12, 17 и 22%), следуя однофакторному плану, полностью случайному с тремя репликами и уровнем значимости α =0,05. Изучаемые переменные включали производительность при нанесении нановолокон, степень вытяжки и прочность пучка нановолокон на разрыв. Важно отметить, что концентрации менее 12% по массе не оценивались, так как в предварительных испытаниях это условие не позволяло образовывать нановолокна при электроспиннинге; таким же образом не оценивались концентрации более 22% по массе, поскольку полученная вязкость была очень высокой, затрудняя перемешивание при приготовлении раствора и последующее течение в процессе электропрядения. Кроме того, исследовались только крайние концентрации и средняя точка.
Методы характеризации
Для основного процесса электропрядения для каждой концентрации определяли производительность (мг / мин) при нанесении матов из электропряденых нановолокон PA 6/66. Впоследствии их морфологически охарактеризовали с помощью сканирующего электронного микроскопа (СЭМ).
Для золь-гелевого процесса электропрядения после корректировки переменных процесса (напряжение, поток, расстояние между иглой и коллектором) для получения стабильной и непрерывной электропрядильной струи была определена степень вытяжки процесса, после чего были получены пучки нановолокон PA 6/66 были охарактеризованы с помощью SEM и испытания на растяжение. Наконец, оптимальные условия процесса были охарактеризованы с помощью дифференциальной сканирующей калориметрии (ДСК).
SEM
Образцы были покрыты золотом в машине для вакуумного нанесения покрытий [Denton Vacuum Desk IV] в течение примерно 200 с. В конце они были помещены в образец держателя растрового электронного микроскопа (JEOL JSM 6490 LV, Япония), снабженного вольфрамовой нитью. После этого мы создали в камере вакуум 30 Па для генерации электронов, сканирования и получения изображений. Затем с помощью программного обеспечения для обработки изображений были измерены средние диаметры нановолокон.
Испытание на растяжение
Триста нитей пучков нановолокон были протестированы на испытательной машине (EZ-Test L, Shimadzu, Япония) при пробной скорости 30 мм / мин и эталонной длине 50 мм в соответствии со стандартами ASTM D3822.
DSC
Для определения фазовых переходов использовали метод дифференциальной сканирующей калориметрии (ДСК) в соответствии со стандартом ASTM D3418-08, применяемым к анализу полимерных материалов. Мы использовали дифференциальный сканирующий калориметр (DSC) (TA Instruments, Q20, USA) с образцами массой 5 мг, которые были помещены в герметично закрытые алюминиевые тигли и подвергнуты двум последовательным циклам нагрева от 25 до 250 ° C со скоростью 10 ° C / мин. скорость с 5-минутными изотермами между каждым циклом. Программное обеспечение TA Universal Analyzer®, адаптированное к оборудованию, позволяло получать термограммы для определения температуры стеклования и плавления материала.
Результаты и обсуждение
Производительность основного процесса электропрядения
На рис. 2 показаны результаты производительности (мг / мин) осаждения нановолокон во время основного процесса электропрядения при различных концентрациях. Для этой переменной ANOVA сгенерировал p значение 0,015. Это указывает на то, что по крайней мере медиана другая. Затем был применен апостериорный тест Тьюки, который показал, что для этой переменной средние значения продуктивности при концентрациях 17 и 22% эквивалентны друг другу, но выше, чем полученные при концентрации 12%.
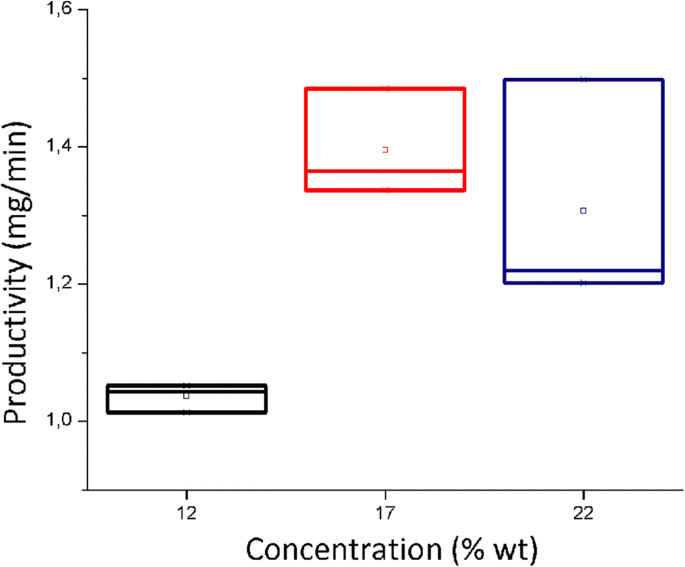
Производительность основного процесса электропрядения
Морфология / морфологическая характеристика нановолокон PA 6/66
Используя основной процесс электроспиннинга, были изготовлены нановолокна PA 6/66 в различных концентрациях. Результаты доказали, что при увеличении концентрации раствора полимера диаметр нановолокон увеличивался, как это видно на микрофотографиях SEM на рис. 3. Это связано с тем фактом, что увеличение концентрации оказывает влияние на реологическое загустение раствора [19], которое затрудняет уменьшение диаметра из-за повышения вязкости. Такое поведение совпадает с описанным Guerrini et al. [20], которые электроспрядили нановолокна PA 6/66 с разной молекулярной массой. Кроме того, было определено, что средний диаметр нановолокон с концентрацией 17% увеличился примерно на 85% по сравнению с нановолокнами, полученными с концентрацией 12%, и на 204% для нановолокон, полученных с концентрацией 22% по сравнению с волокнами с концентрацией 17%. .
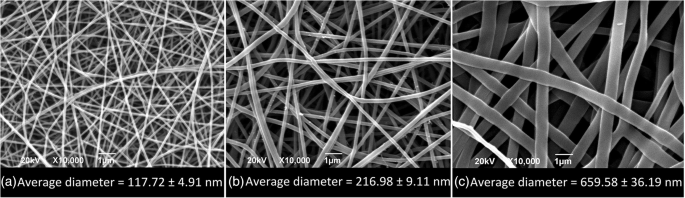
СЭМ-изображения электропряденых нановолокон PA 6/66 при различных концентрациях. а 12% масс., b 17% масс. И c 22% масс
Коэффициент вытяжки в золь-гелевом процессе электропрядения
На рис. 4 показаны результаты измерения степени вытяжки, измеренной в процессе золь-гелевого электроформования при различных концентрациях. Для этой переменной ANOVA сгенерировал p значение 0,000, которое указывает на то, что по крайней мере медиана отличается. Затем был применен апостериорный тест Тьюки, который показал, что для этой переменной медиана степени вытяжки, полученная при концентрации 17%, выше, чем полученная при 12 и 22% концентрациях, которые эквивалентны друг другу.
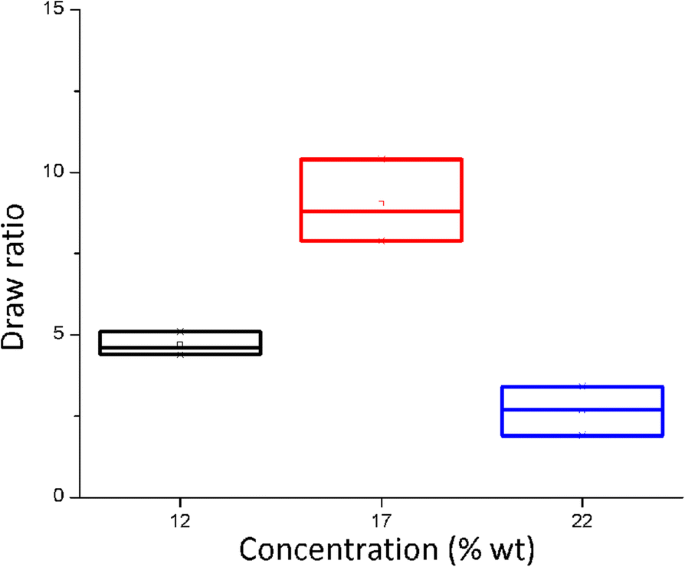
Степень вытяжки золь – гелевого процесса электроспиннинга
Морфология / морфологическая характеристика связки нановолокон PA 6/66
С помощью золь-гелевого процесса электроспиннинга жгуты полиамидных нановолокон были получены при различных концентрациях в растворе. После измерения их диаметров было обнаружено, что меньшее среднее значение было достигнуто при концентрации 17%, как это видно на микрофотографиях SEM на рис. 5. Полученные жгуты нановолокон с концентрацией 17% достигли диаметра почти половины диаметров, полученных с использованием 12 и 22% концентрации соответственно. Это связано с тем, что процесс проводился при более высокой скорости возврата волокон и большей степени вытяжки.
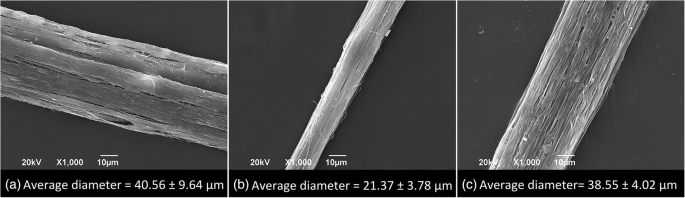
СЭМ-изображения пучков нановолокон полиамида 6/66, полученных с помощью золь-гель процесса электроспиннинга при различных концентрациях. а 12% масс., b 17% масс. И c 22% масс.
Прочность на разрыв пучка нановолокна
На рис. 6 представлена диаграмма прочности на разрыв, измеренная для пучков нановолокон, полученных в процессе золь-гель электропрядения при различных концентрациях. Для этой переменной ANOVA сгенерировал p значение 0,005, указывающее на то, что по крайней мере медиана отличается. Впоследствии был применен апостериорный тест Тьюки, показавший, что для этой переменной среднее значение прочности на разрыв пучков нановолокон, полученных при концентрации 17%, выше, чем результат для концентраций 12 и 22%, которые эквивалентны друг другу.
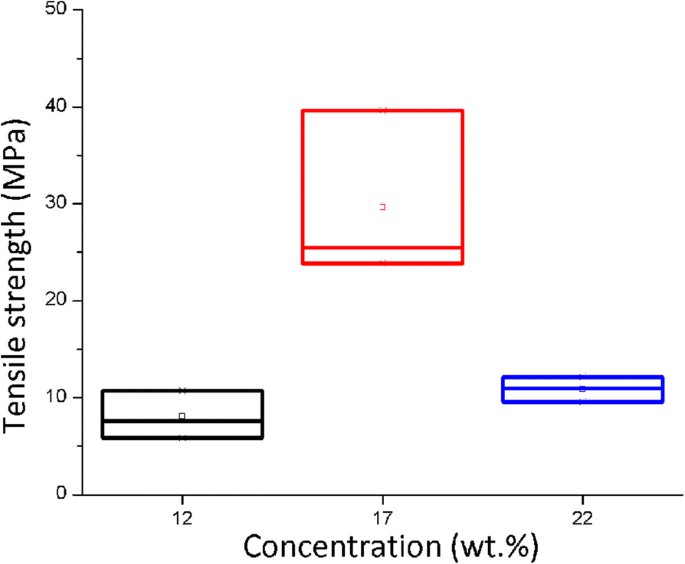
Прочность на разрыв пучков нановолокон из полиамида 6/66 при различных концентрациях
Кроме того, средний результат прочности на разрыв, полученный с концентрацией 17% нейлона (29,64 МПа), был аналогичен результату, описанному Wu et al. [16] в своем исследовании представили результаты 66 полиамидных нановолокон, сначала электроспряденных, а затем изогнутых со значениями прочности около 30 МПа.
Оптимальные условия процесса
Предыдущие результаты показывают, что разработка золь-гелевого процесса электроспиннинга из раствора PA 6/66 при 17% мас. концентрация позволяет изготавливать жгуты нановолокон с более высокой производительностью, степенью вытяжки и прочностью на разрыв. Кроме того, на рис. 7 более подробно показаны пучки нановолокон, позволяющие наблюдать увеличение поверхностной шероховатости. Это важно, если предполагается использовать эти волокна в качестве армирующего композитного материала, поскольку они обеспечивают лучшую механическую фиксацию к матрице по сравнению с обычными синтетическими волокнами, которые обычно имеют гладкую поверхность. Кроме того, эти волокна имеют высокое отношение площади к объему и высокое соотношение сторон, что дает им возможность найти применение в дизайне одежды, фильтров и нанокомпозитов [21].
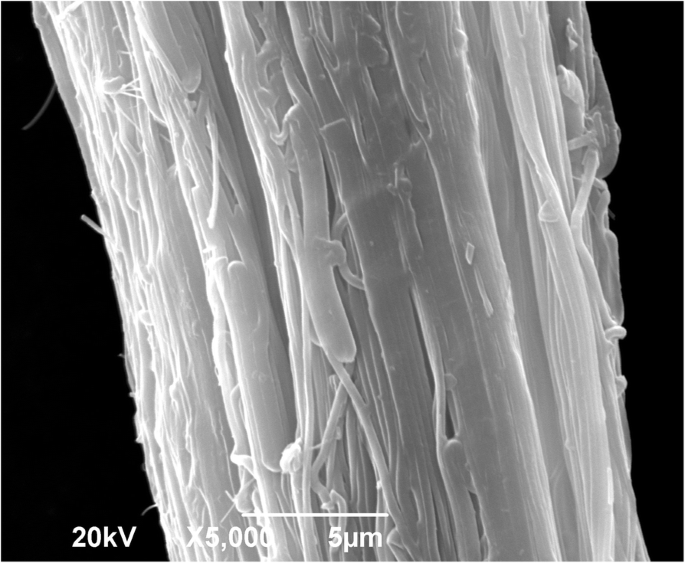
СЭМ-изображение поверхности пучков нановолокон PA 6/66
Термический анализ DSC связок нановолокна в оптимальном состоянии
Из оптимальных условий при концентрации 17% мы провели термический анализ каждой из стадий трансформации, поскольку материал находится в гранулах, он превращается в нановолокна и, наконец, превращается в пучки нановолокон. На рисунке 8 показаны результаты калориметрического теста, полученные с помощью ДСК для каждого этапа.
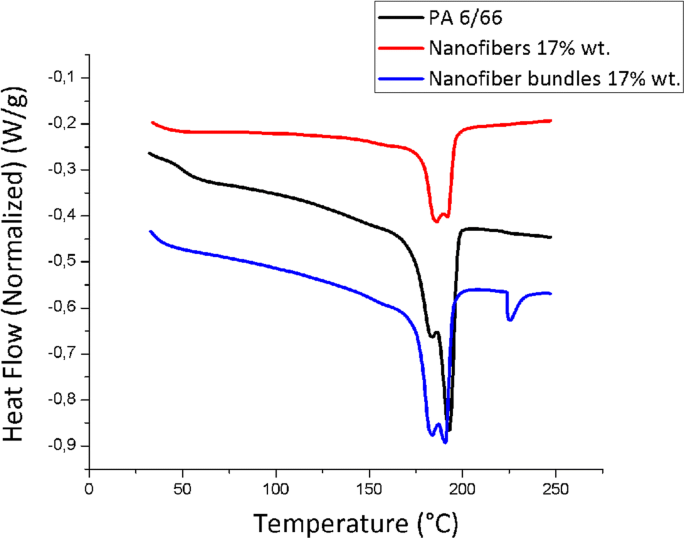
Полученные в результате термограммы оптимального состояния пучка нановолокон, полученные с помощью DSC
На основе этих термограмм была рассчитана температура стеклования ( T g ), температура плавления ( T м ) теплота плавления (Δ H м ) и степенью кристалличности ( X c ). Эти результаты можно увидеть в таблице 1.
Это видно из T g результаты показывают, что нановолокна при концентрации 17% демонстрируют более высокую межмолекулярную подвижность по сравнению с пучками нановолокон при той же концентрации. Последнее объясняется тем, что повышенная молекулярная подвижность вызвана увеличением пространства полимерной цепи, называемого свободным объемом, что уменьшает взаимодействия между ними. Таким образом, цепи с большей подвижностью требуют более низкой температуры для перехода от стекловидного твердого тела к каучуковому, что приводит к более низкому T g ценности.
Значение температуры плавления связано с температурой, необходимой для плавления упорядоченных структур (кристаллов) в полимер, и ее изменение связано с размером кристалла. Можно отметить, что нановолокна при концентрации 17% показали наименьшее значение температуры плавления по сравнению с пучками полиамида и нановолокон при той же концентрации. Это указывает на то, что основной процесс электропрядения и золь-гель электропрядения уменьшали количество кристаллических областей полимера по отношению к гранулам, превращая их в фибриллярные структуры [22], которые благодаря прядению и применяемой степени вытяжки ориентировали полимерные цепи. и показал восстановление степени кристалличности пучков нановолокон на 44,71% по сравнению с нановолокнами. Наконец, энтальпия плавления показывает степень кристалличности в анализируемом полимере [23], и ее значение связано с требуемой энергией плавления кристаллической структуры. Это доказывает, что нановолокна при концентрации 17% требуют меньше энергии для плавления, чем кристаллические структуры из пучков нановолокон и гранул PA 6/66.
Выводы
Золь-гелевый процесс электропрядения полиамида 6/66 показал значительное увеличение производительности (1,39 ± 0,15 мг / мин), степени вытяжки (9,0 ± 1,2) и прочности на разрыв (29,64 ± 7,40 МПа) при концентрации 17% по массе по сравнению с до двух других испытанных концентраций (12% масс. и 22% масс.). Эти статистически оптимизированные условия процесса позволили нам получить однородные пучки нановолокон PA 6/66 в результате стабильного и непрерывного процесса.
Сокращения
- DSC:
-
Дифференциальная сканирующая калориметрия
- PA 6/66:
-
Полиамид 6/66
- PVA:
-
Поливиниловый спирт
- SEM:
-
Сканирующий электронный микроскоп
Наноматериалы
- Пересмотр процесса интеграции программного обеспечения для операций аддитивного производства
- Устойчивы ли нейлоновые застежки к химическому воздействию?
- 3 основные причины нехватки нейлона 6/6
- Разработка процесса нанесения покрытия погружением и оптимизация производительности для электрохромных ус…
- Получение наноструктуры Au @ TiO2 - оболочка и ее применение для разложения и обнаружения метиленового синего
- Оптимизация проектирования спейсеров для безконденсаторной DRAM на основе туннельного транзистора с двумя за…
- Простой подход к получению наноразмерного оксида цинка в воде / глицерине с чрезвычайно концентрированными и…
- Электроформование нановолокон карбоксиметилхитозана / полиоксиэтилена для сохранения свежести фруктов
- Сбор полевых данных для оптимизации процесса
- Подготовка прототипов к производству Производственный процесс