Когда следует использовать литье под давлением в малых объемах
Литье под давлением — полезный метод производства, который дает производителям возможность создавать идентичные детали в больших объемах с постоянным качеством и характеристиками. Во время производства сопло под давлением впрыскивает расплавленный пластик в прочную металлическую форму, предназначенную для охлаждения детали и ее быстрого извлечения. После извлечения детали пресс закрывается, и операция повторяется. Многие предметы повседневного обихода — от расчесок и крышек для бутылок до автомобильных деталей и шестерен — изготавливаются методом литья под давлением.
Исторически сложилось так, что литьевые детали приходилось производить в больших количествах, чтобы компенсировать высокие начальные затраты. Пресс-форма из закаленной стали стоит десятки тысяч долларов, и на ее изготовление могут уйти недели или месяцы, но со временем ее долговечность позволяет производителям окупить свои инвестиции, а также снизить себестоимость детали.
Однако по мере развития рынков — о чем свидетельствует, например, продолжающийся переход к заказным и мелкосерийным продуктам — производители адаптируют свои операции, чтобы использовать преимущества новых, более эффективных методов. Одним из таких методов является литье под давлением в малых объемах.
Ключевые преимущества мелкосерийного литья под давлением
В процессе мелкосерийного литья под давлением вместо форм и вставок из закаленной стали используются более мягкие алюминиевые, которые обычно проще и дешевле изготовить. Эти пресс-формы, очевидно, не так долговечны, как их аналоги из закаленной стали, но преимущество для производителей заключается в том, что они часто не нужны при производстве деталей в небольших объемах. При стратегическом использовании мягкие пресс-формы могут в конечном итоге снизить затраты на оснастку и сократить производственные графики.
Как правило, малосерийное литье под давлением относится к изготовлению деталей в количестве 100 000 или меньше. Хотя это число, вероятно, покажется непрофессионалу высоким, оно все же относительно мало по сравнению с крупносерийным производством, которое может легко достигать десятков миллионов деталей. Хотя 100 000 – это не официальное ограничение, оно служит общим ориентиром для точки, в которой алюминиевые формы становятся менее рентабельными, чем инвестиции в формы из закаленной стали.
В то же время закаленная сталь, необходимая для традиционных пресс-форм, требует значительных предварительных затрат времени и денег. Однако формы из алюминия и низкосортной стали намного дешевле в изготовлении и могут быть изготовлены быстрее. С помощью этих пресс-форм производители могут создавать прототипы и производить жизнеспособные детали без необходимости устанавливать высокие минимальные заказы, продолжая при этом совершенствовать конструкцию и производство деталей по мере необходимости. Это позволяет производителям начинать производство раньше и во многих случаях значительно ускорять выход на рынок, тем самым сокращая время, необходимое для окупаемости инвестиций.
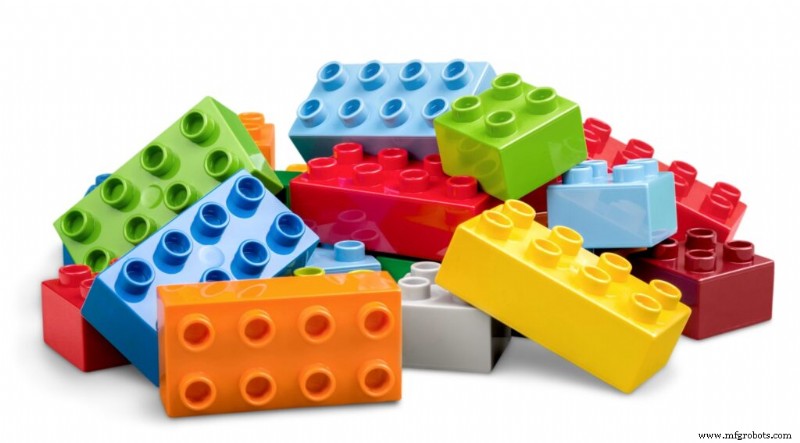
Сокращение времени выполнения заказа особенно полезно для небольших групп по производству продукции с ограниченным бюджетом, которые теперь могут производить детали с относительно небольшим минимальным заказом, при этом получая прибыль. Кроме того, хранение и утилизация избыточных запасов может быстро стать дорогостоящим, но быстрое литье под давлением в небольших объемах помогает минимизировать излишки, позволяя производственным группам производить детали только в необходимых количествах.
В дополнение к созданию возможностей для создания небольших партий или деталей по индивидуальному заказу, процесс быстрого литья под давлением обеспечивает эффективные средства мостовой оснастки. Это позволяет компаниям-производителям начать изготовление пресс-форм из закаленной стали, одновременно используя алюминиевые пресс-формы для производства деталей.
Еще одним важным преимуществом использования более мягких форм для литья под давлением является то, что они редко оказывают негативное влияние на качество деталей:пластиковые детали, изготовленные в небольших объемах, не уступают по качеству изготовленным с помощью форм из закаленной стали, если принять во внимание надлежащие конструктивные соображения.
Ключевые аспекты проектирования для литья под давлением в малых объемах
Есть несколько важных соображений, которые необходимо учитывать при проектировании деталей для технологичности в небольших объемах, включая общую сложность детали, осадку, толщину стенки и качество поверхности.
Как правило, когда вы работаете с алюминием, вы не хотите реализовывать боковые действия или подъемники, обычно связанные со сложными конструкциями инструмента. Хотя эти операции обычно вызывают износ инструмента — более мягкий алюминий не может выдерживать такое давление очень долго — стали с низкой твердостью, такие как P20, служат оптимальными инструментальными материалами для замены.
Уклон относится к конусу, встроенному в конструкцию, который облегчает извлечение детали из формы. Рассмотрим прямоугольную форму для выпечки — если бы форма была действительно прямоугольной, было бы трудно извлечь торт. Тем не менее, закругленные края и сужающиеся стороны, встроенные в форму формы, позволяют пирогу легко выходить из формы. Этот принцип действует и при извлечении отлитых под давлением деталей из форм. Все вертикальные грани должны иметь уклон не менее 0,5 градуса, хотя предпочтительнее ближе к 2 или 3 градусам, если позволяет конструкция детали. Для некоторых сложных поверхностей может потребоваться наклон до 5 градусов.
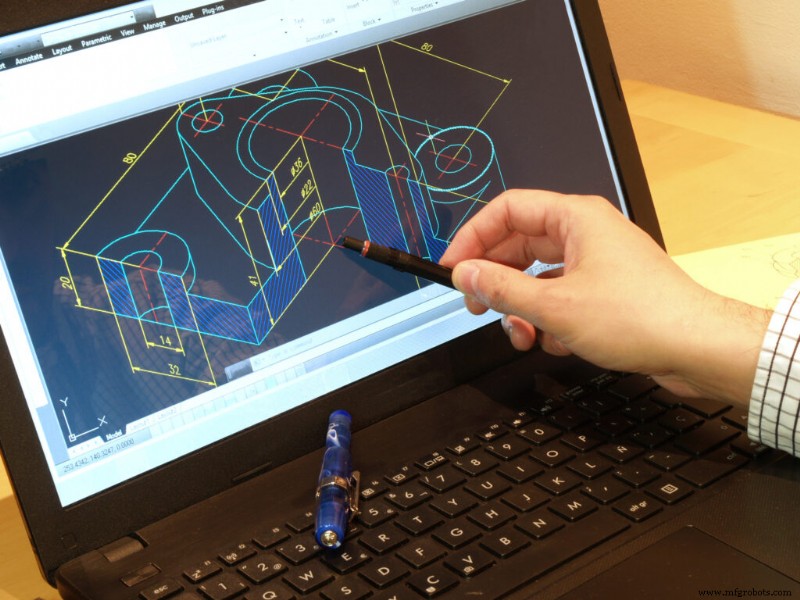
Также необходимо учитывать толщину стенок компонента, поскольку более толстые стенки не обязательно означают большую прочность или производительность, особенно при работе с термопластичными материалами. Толстые поперечные сечения на самом деле увеличивают вероятность деформации или провисания деталей в процессе охлаждения, поэтому толщина стенок обычно должна составлять от 0,040 до 0,140 дюймов (от 1 до 3,5 мм) по всей детали.
Производители также могут сэкономить на инструментах и времени, отказавшись от ненужной обработки поверхности своих пресс-форм. Если для применения детали не требуется чрезвычайно гладкая поверхность — для чего может потребоваться ручная полировка полостей пресс-формы алмазными полировальными кругами — в ней, вероятно, нет необходимости. Использование наиболее экономичной отделки, совместимой с областью применения данной детали, является ключом к снижению производственных затрат и сокращению сроков производства.
Использование мелкосерийного литья под давлением в ваших интересах
Литье под давлением — невероятно полезный производственный метод, часто используемый для создания большого количества идентичных деталей. Высокая стоимость оснастки для пресс-форм из закаленного металла означает, что детали должны производиться в больших объемах, чтобы проект оказался рентабельным. Однако разработки в производственных процессах и технологиях теперь позволяют группам разработчиков экономично создавать детали для быстрого литья под давлением в меньших количествах и предоставлять эффективные решения для мостовой оснастки.
В Fast Radius мы всегда стремимся выполнять свою работу более эффективно. Это означает тесное сотрудничество с каждым из наших клиентов — от проектирования и прототипирования до постпроизводства и реализации — чтобы гарантировать, что они получают высококачественные детали, которые производятся по доступной цене и доставляются в короткие сроки. Свяжитесь с нами сегодня, чтобы узнать, как мы можем воплотить ваши проекты в жизнь.
Промышленные технологии
- Руководство по литью малых объемов
- Литье под давлением с использованием технологии PolyJet
- Литье против литья под давлением
- Литье под давлением против реактивного литья под давлением (RIM)
- Литье под давлением против реакционного литья под давлением
- Литье пластмасс под давлением в автомобильной промышленности
- 5 распространенных ошибок, которых следует избегать при литье под давлением
- 6 типов ворот для литья под давлением и когда их использовать
- Когда использовать процесс многослойного формования с литьем под давлением
- Литье под давлением и 3D-печать объединяются для создания «невозможных» деталей