Что такое экструзия? Различные типы процессов экструзии?
Процесс экструзии – это один из типов процессов объемного формования, при котором рабочий металл продавливается или сжимается через отверстие матрицы для достижения определенной требуемой формы поперечного сечения.
Проще говоря, экструзия — это процесс металлообработки, при котором металл продавливается через отверстие матрицы под повышенным давлением, чтобы сжать его поперечное сечение.
С развитием процесса экструзии мир стал зависеть от экструзии для производства стержней, труб и профилей любой формы, как полых, так и сплошных.
Поскольку эта операция включает проталкивание или протягивание заготовки через матрицу, усилия, необходимые для выдавливания заготовки, довольно велики. Горячее выдавливание является наиболее распространенным методом, поскольку сопротивление деформации металла при высоких температурах низкое, а холодное выдавливание обычно выполняется только для мягких металлов.
История:
Хотя концепция экструзии рождается из процесса формовки. Записано, что в 1797 году инженер по имени Джозеф Брама запатентовал процесс экструзии.
Испытание включало предварительный нагрев металла, а затем продавливание его через полость штампа для изготовления трубы из заготовки. Он использовал ручной поршень, чтобы протолкнуть металл.
Затем Брама изобрел гидравлический процесс после изобретения экструзии. Затем Томас Берр использовал технологию гидравлического пресса и базовую технику экструзии, объединив отдельные технологии для производства трубы (полой). Он также был запатентован в 1820 году.
Затем технология стала основной потребностью в растущем мире, в то время как этот процесс не мог работать с твердыми металлами. В 1894 году Томас Берр представил экструзию сплавов меди и латуни, что привело к развитию техники экструзии.
С момента изобретения метода экструзии этот процесс превратился в множество методов, позволяющих производить широкий спектр продуктов сложной структуры с минимально возможными затратами.
Классификация или типы процесса экструзии:
Различные типы процессов экструзии :
- Горячее прессование
- Холодная экструзия
- Теплая экструзия
- Фрикционная экструзия
- Микроэкструзия
- Прямая экструзия
- Непрямое вытеснение
- Гидростатическая экструзия и
- Ударное выдавливание Процесс.
№1. Процесс горячей экструзии:
В этом процессе горячего прессования заготовка обрабатывается при температуре, превышающей ее температуру рекристаллизации. Эта горячая обработка позволяет предотвратить наклеп заготовки и позволяет пуансону легко протолкнуть ее через матрицу.
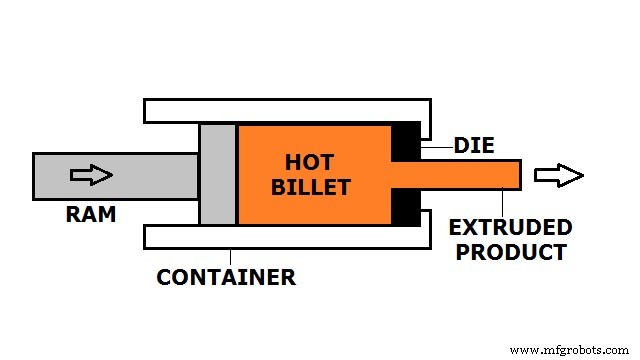
Горячее прессование обычно выполняется на горизонтальных гидравлических прессах. Давление, участвующее в этом процессе, может варьироваться от 30 МПа до 700 МПа. Для сохранения высокого давления используется смазка. Масло или графит используются в качестве смазки при низкотемпературной экструзии, а стеклянный порошок используется при высокотемпературной экструзии.
Заготовка нагревается от 0,5 до 0,75 Тм для получения качественной операции.
Температуры горячей экструзии некоторых часто используемых материалов приведены ниже:
Материал | Температура (˚C) |
Алюминий | от 350 до 500 |
Медь | от 600 до 1100 |
Магний | от 350 до 450 |
Никель | от 1000 до 1200 |
Сталь | от 1200 до 1300 |
Титан | от 700 до 1200 |
ПВХ | 180 |
Нейлон | 290 |
Преимущества процесса горячей экструзии:
- Деформацию можно контролировать в соответствии с требованиями.
- Заготовка не подвергается упрочнению за счет наклепа.
- Для нажатия требуются меньшие усилия.
- Материалы с преждевременными трещинами также можно обрабатывать.
Недостатки процесса горячей экструзии:
- Плохая отделка поверхности.
- Точность размеров может быть нарушена.
- Меньший срок службы контейнера.
- Возможность окисления поверхности.
#2. Холодная экструзия:
Это процесс придания металлу формы ударом пули. Этот удар осуществляется пробойником или тараном в закрытой полости. Ползун проталкивает металл через полость матрицы, чтобы преобразовать твердую заготовку в твердую форму.
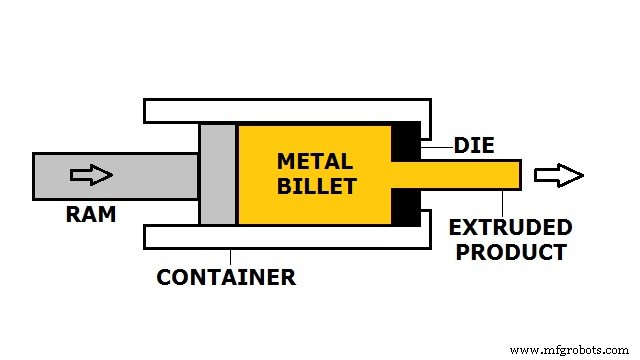
В этом процессе заготовка подвергается деформации при комнатной температуре или немного выше комнатной температуры.
Поскольку требуемые усилия слишком высоки, в этой технике используется мощный гидравлический пресс. Давление колеблется до 3000 МПа.
Преимущества:
- Без окисления.
- Улучшенная прочность продукта.
- Более жесткие допуски.
- Улучшенная обработка поверхности.
- Повышена твердость.
Недостатки:
- Требуются более высокие силы.
- Для работы требуется больше энергии.
- Нельзя обрабатывать непластичные материалы.
- Деформационное упрочнение экструдируемого материала является ограничением.
#3. Процесс теплой экструзии:
Горячая экструзия – это процесс экструзии заготовки при температуре выше комнатной и ниже температуры рекристаллизации материала. Этот процесс используется, когда необходимо предотвратить микроструктурные изменения материала, происходящие в процессе экструзии.
Этот процесс важен для достижения надлежащего баланса требуемых усилий и пластичности. Температура любого металла, используемого в этой операции, может составлять от 424 до 975 градусов Цельсия.
Преимущества теплого процесса:
- Улучшенная прочность.
- Это повысило твердость продукта.
- Отсутствие окисления.
- Можно добиться очень жестких допусков.
Недостатки:
- Нельзя экструдировать непластичные материалы.
- Отопительное оборудование является дополнительным.
#4. Выдавливание трением:
В методе фрикционной экструзии заготовка и контейнер вынуждены вращаться против друг друга, в то время как при одновременной работе заготовка проталкивается через полость матрицы для получения желаемого материала.
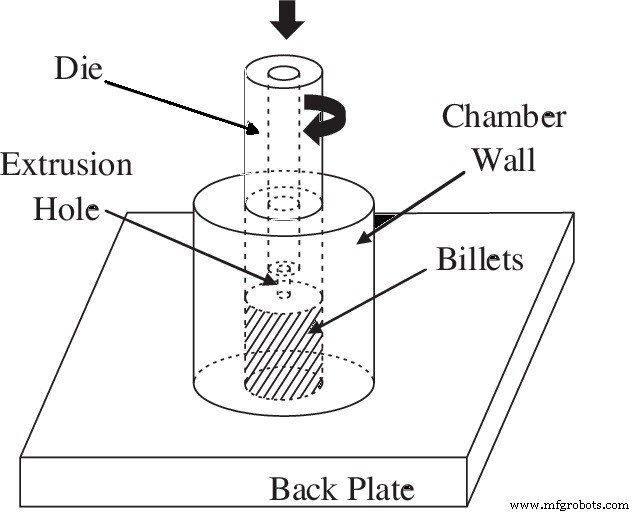
На процесс влияет относительная скорость вращения между заготовкой и матрицей. Относительное вращательное движение загрузки и матрицы оказывает существенное влияние на процесс.
Во-первых, это приводит к возникновению большого количества касательных напряжений, вызывающих пластическую деформацию заготовки. Во-вторых, при относительном движении заготовки и матрицы выделяется большое количество тепла, поэтому предварительный нагрев не требуется, что делает процесс более эффективным.
Он может производить существенно консолидированную проволоку, стержни, трубы и другие некруглые металлические формы непосредственно из различных исходных материалов, таких как металлический порошок, чешуйки, отходы механической обработки (стружка или стружка) или сплошная заготовка.
Преимущества процесса трения:
- Нагрев не требуется.
- Создание касательных напряжений приводит к повышению усталостной прочности изделия.
- В качестве заготовки можно использовать любой тип материала, что делает этот процесс экономичным.
- Низкое энергопотребление.
- Лучшее сопротивление коррозии.
Недостатки трения Процесс:
- Ожидаемое окисление.
- Высокая начальная настройка.
- Сложное оборудование.
#5. Процесс микроэкструзии:
По номенклатуре понятно, что этот процесс связан с производством изделий субмиллиметрового диапазона.
Подобно экструзии на макроуровне, здесь заготовка проталкивается через отверстие матрицы, чтобы придать заготовке ожидаемую форму. Результат может пройти через квадрат со стороной 1 мм.
Прямая или прямая и обратная или непрямая микроэкструзия являются двумя наиболее фундаментальными методами, используемыми в эту эпоху для производства микроэлементов.
При прямой микроэкструзии поршень перемещает заготовку вперед, а заготовка движется в одном направлении, тогда как при обратной микроэкструзии поршень и заготовка движутся в противоположных направлениях.
Микроэкструзия широко используется в производстве компонентов для резорбируемых и имплантируемых медицинских устройств, начиная от биорезорбируемых стентов и заканчивая системами контролируемого высвобождения лекарств.
В то время как в области механики применение можно широко наблюдать в производстве крошечных шестерен, крошечных труб и т. д.
Преимущества микропроцесса:
- Можно создавать очень сложные поперечные сечения.
- Можно производить крошечные элементы.
- Улучшенные геометрические допуски.
Недостатки :
- Создание небольшого штампа и контейнера, отвечающих нашим потребностям, — непростая задача.
- Требуется квалифицированный рабочий.
#6. Прямое или прямое выдавливание:
В процессе прямой экструзии металлическая заготовка сначала помещается в контейнер. Контейнер имеет контурное отверстие штампа. Чтобы протолкнуть металлическую заготовку через отверстие матрицы, используется ползун, после чего изделие изготавливается.
В этом типе направление потока металла совпадает с направлением движения ползуна.
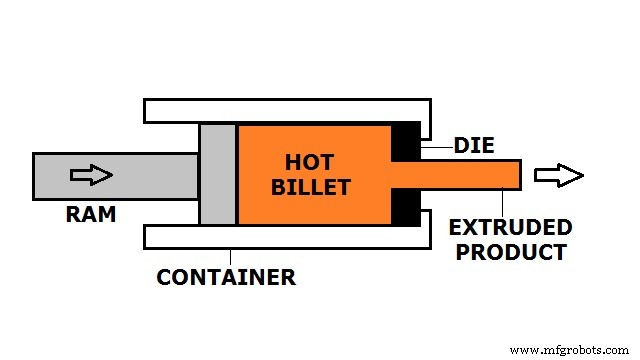
Поскольку заготовка вынуждена двигаться к отверстию матрицы, возникает большое трение между поверхностью заготовки и стенками контейнера. Существование трения требует значительного увеличения силы ползуна, что приводит к потреблению большей мощности.
В этом процессе выдавливание хрупких металлов, таких как сплавы вольфрама и титана, затруднено, поскольку они разрушаются во время процесса. Растягивающие силы на протяжении всего процесса вызывают быстрое образование микротрещин, что приводит к переломам.
Прессование хрупких металлов, таких как сплавы вольфрама и титана, затруднено, поскольку они разрушаются в процессе. Силы растяжения вызывают быстрое образование микротрещин, что приводит к переломам.
Также наличие оксидного слоя на поверхности заготовки усиливает трение. Этот оксидный слой может вызвать дефекты в экструдированном изделии.
Чтобы решить эту проблему, между пуансоном и рабочей заготовкой помещается фиктивный блок, чтобы уменьшить трение.
Примерами могут служить трубы, банки, чашки, небольшие шестерни, валы и другие экструдированные изделия.
Некоторые части заготовки всегда остаются в конце каждой экструзии. Это называется прикладом. . Он удаляется из продукта, разрезая его сразу после выхода из матрицы.
Преимущества прямого процесса:
- Этот процесс позволяет выдавливать более длинные заготовки.
- Улучшенные механические свойства материала.
- Хорошее качество поверхности.
- Возможна холодная и горячая экструзия.
- Возможность работать непрерывно.
Недостатки прямого процесса:
- Хрупкие металлы нельзя выдавливать.
- Большое усилие и высокая мощность.
- Возможность окисления.
#7. Косвенное или обратное выдавливание:
В этом процессе экструзии в обратном направлении матрица остается неподвижной, тогда как заготовка и контейнер движутся вместе. Матрица устанавливается на плунжере, а не на контейнере.
Металл проходит через отверстие матрицы на стороне ползуна в направлении, противоположном движению ползуна, поскольку он сжимается ползунком.
Когда заготовка сжимается, материал проходит между оправкой и, следовательно, отверстием матрицы.
Поскольку между заготовкой и контейнером нет относительного движения, трение не регистрируется. Это поднимает процесс над процессом прямой экструзии, в результате чего используемая сила ползуна меньше, чем при прямой экструзии.
Чтобы матрица оставалась неподвижной, используется «стержень», длина которого превышает длину контейнера. Прочность столбца штока определяет конечную и максимальную длину экструзии.
Поскольку заготовка движется вместе с контейнером, все силы трения легко устраняются.
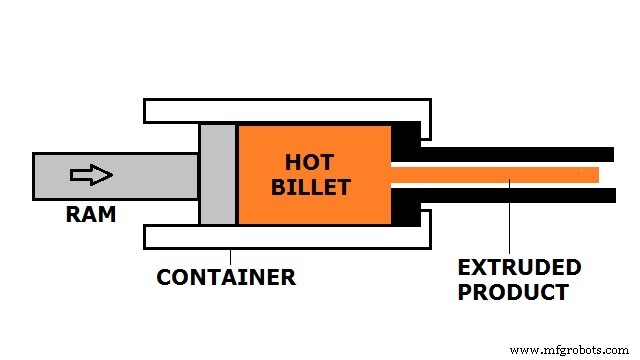
Преимущества непрямых процессов:
- Требуется меньшее усилие экструзии.
- Меньшие поперечные сечения можно экструдировать.
- Уменьшение трения на 30%.
- Увеличена скорость работы.
- Зарегистрировано очень мало износа.
- Маловероятность возникновения дефектов экструзии или крупнозернистых кольцевых зон, поскольку течение металла более стабильное.
Недостатки непрямого процесса.
- Поперечное сечение экструдируемого материала ограничено размером используемого штока.
- Возможность остаточных напряжений после экструзии.
- Загрязнения и дефекты влияют на чистоту поверхности и делают продукт некачественным.
#8. Гидростатическая экструзия:
В процессе гидростатической экструзии заготовка окружена жидкостью внутри контейнера, которая прижимается к заготовке под действием поступательного движения плунжера. Внутри контейнера отсутствует трение из-за жидкости, а трение в отверстии штампа очень мало.
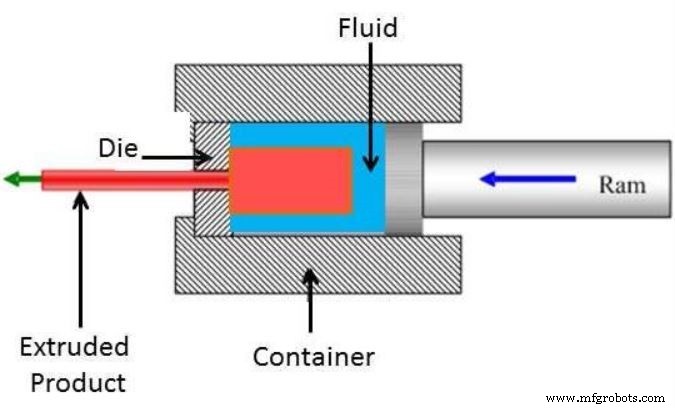
Заготовка не смещается при заполнении отверстия контейнера, так как на нее действует равномерное гидростатическое давление. Это успешно приводит к заготовке с огромным соотношением длины к диаметру, даже бухты проволоки могут быть безупречно экструдированы или имеют неровное поперечное сечение.
Основное различие между гидростатической и прямой экструзией заключается в отсутствии прямого контакта между контейнером и заготовкой во время гидростатической экструзии.
Работа при высоких температурах требует использования специальных жидкостей и процессов.
Когда материал подвергается гидростатическому давлению и отсутствует трение, его пластичность увеличивается. В результате этот метод может использоваться для металлов, которые слишком хрупкие для обычных методов экструзии.
Этот подход используется для пластичных металлов и позволяет добиться высоких коэффициентов обжатия.
Преимущества:
- Экструдированные товары имеют превосходную полированную поверхность и точные размеры.
- Никаких разногласий.
- Минимальные требования к силе.
- В процессе не остается остатков заготовки.
- Поток материала равномерный.
Недостатки:
- При работе при высоких температурах следует использовать специальные жидкости и процедуры.
- Каждая заготовка должна быть подготовлена и сужена на одном конце перед работой.
- Трудно сдержать жидкость.
#9. Ударное выдавливание:
Ударная экструзия является еще одним основным методом производства металлических экструдированных профилей. В отличие от традиционного процесса экструзии, который требует высоких температур для размягчения материала, ударная экструзия часто использует заготовки из холодного металла. Эти заготовки экструдируются при высоком давлении и эффективности.
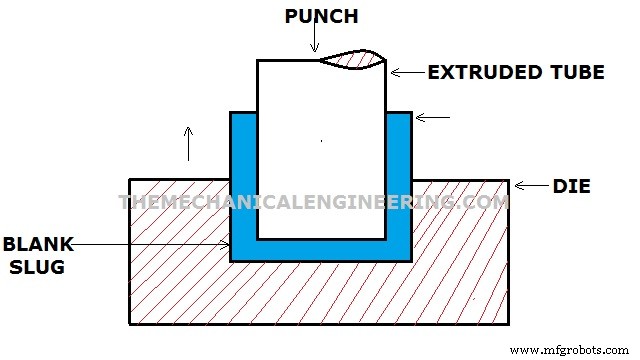
Смазанная соответствующим образом заготовка помещается в полость матрицы и ударяется пуансоном за один ход во время обычной операции ударного выдавливания. Это заставляет металл течь обратно вокруг пуансона через зазор между матрицей и пуансоном.
Этот процесс лучше работает с более мягкими материалами, такими как свинец, алюминий или олово.
Этот процесс всегда выполняется в холодном состоянии. Процесс обратного удара позволяет получить очень тонкие стенки. Например, сделайте тюбики из-под зубной пасты или батарейки.
Он выполняется в более быстром темпе и с более короткими ударами. Вместо приложения давления используется ударное давление для выдавливания заготовки через головку. Воздействие, с другой стороны, может быть выполнено путем прямого или обратного выдавливания или их комбинации.
Преимущества:
- Значительное уменьшение размера.
- Быстрый процесс. Сокращение времени обработки до 90%.
- Увеличение производительности.
- Повышенная целостность допуска.
- Экономия сырья до 90%.
Недостатки:
- Требуется очень высокое усилие сжатия.
- Размер заготовки является ограничением.
Факторы, влияющие на силу выдавливания:
На усилие выдавливания влияют следующие факторы:
- Рабочая температура.
- Конструкция оборудования, горизонтальная или вертикальная.
- Тип экструзии.
- Коэффициент экструзии.
- Величина деформации.
- Фрикционные параметры.
Применение или использование процесса экструзии:
- Он широко используется в производстве труб и полых труб. А также используется для производства пластиковых предметов.
- Процесс экструзии используется для производства рам, дверей, окон и т. д. в автомобильной промышленности.
- Металлический алюминий используется в строительстве во многих отраслях промышленности.
Промышленные технологии
- Что такое протяжка? - Процесс, работа и типы
- Что такое ковка? - определение, процесс и типы
- Что такое экструзия? - Работа, типы и применение
- Какие существуют виды гибки труб?
- Каковы различные типы ремонтных работников?
- Какие существуют типы сварки?
- Какие существуют виды прототипирования?
- Какие существуют 4 типа производственного процесса?
- Различные типы процесса электродуговой сварки
- Различные типы процессов формовки листового металла