Набирая обороты с Markforged:формование и литье колес, напечатанных на 3D-принтере
Примечание редактора. Этот гостевой пост написал Чарльз Гуан, выпускник MIT по машиностроению, бывший инструктор по механическому цеху и дизайну Массачусетского технологического института. Он также является создателем робота Overhaul для BattleBots от ABC. Он работает инженером-консультантом в области робототехники и транспорта, и его спонсирует Markforged для участия в BattleBots и других соревнованиях по робототехнике. Посетите его веб-сайт и посетите Equals Zero Robotics, чтобы узнать больше!
Дизайн колес
Колеса. Имея за плечами более 6000 лет истории, вы могли бы подумать, что мы бы уже сделали их идеальными. Как я на собственном опыте выяснил во время второго сезона BattleBots, во многих отношениях это далеко не так. Вы действительно можете изобрести велосипед и ошибиться. Я разработал Overhaul 2.0 с мощной и устойчивой квадратной шестиколесной платформой с намерением использовать скорость в своих интересах при захвате противников в его захватном подъемнике. Я выбрал колеса, основываясь на том, что знал:промышленные литейные колеса средней твердости с протектором из термопластичного эластомера (TPE), которые с самого начала использовались в боях роботов. Пропустить через эти колеса 16-сильные двигатели в робота, который разгоняется до 19 миль в час за 1 секунду, было неизведанной территорией.
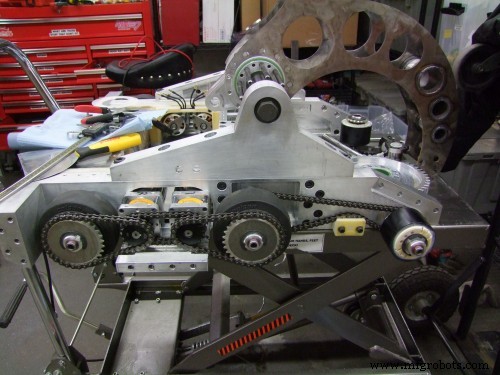
На арене это совсем не пошло мне на пользу. Колеса TPE начали разваливаться, буквально таяли от пропускаемой через них мощности. Их гладкий протектор скользил по рыхлым обломкам и частицам в ящике, как бот ехал по льду. В результате мои 16 лошадиных сил бесщеточного двигателя были потрачены впустую. Если вы посмотрите мой матч против Beta в прошлом сезоне, вы увидите, что большую часть матча я принял BattleBots за Гран-при D1.
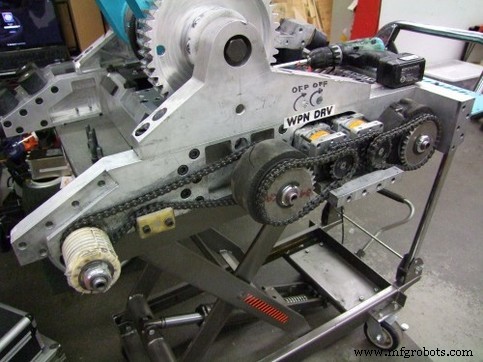
После турнира BattleBots Season 2 я задумался о дальнейших шагах. Колеса нужно будет изменить, чтобы заставить бота работать на земле. Здесь я начал исследовать литьевые резиновые смеси. Я был не против сделать несколько форм, разлить материал, а затем поработать над чем-то еще, пока оно застынет. Во время 2 сезона BattleBots я наблюдал, как некоторые участники, в том числе Бета, заливают свои собственные уретановые колеса на месте.
Я ничего не знал ни о конструкции шин и колес, ни о литье и литье. Поговорим о выстреле в темноте! К счастью, летом я поймал нескольких представителей компании Smooth-On на выставке Detroit Maker Faire и подробно рассказал им, что они думают о том, какой из их продуктов подходит для изготовления тяговых колес. Smooth-On - это компания, в первую очередь ориентированная на изготовление форм и литье для спецэффектов, костюмов и реквизита, а не на промышленное использование. Однако их дистрибьюторы работают по всей стране, поэтому их материалы очень легко доступны для экспериментов - всего в 15 минутах езды от Бостона. Миссия:изучить рабочий процесс литья из смолы, производя нестандартные колеса для модели Overhaul в масштабе 30 фунтов, которую я проектировал во время конкурса осенью 2016 года.
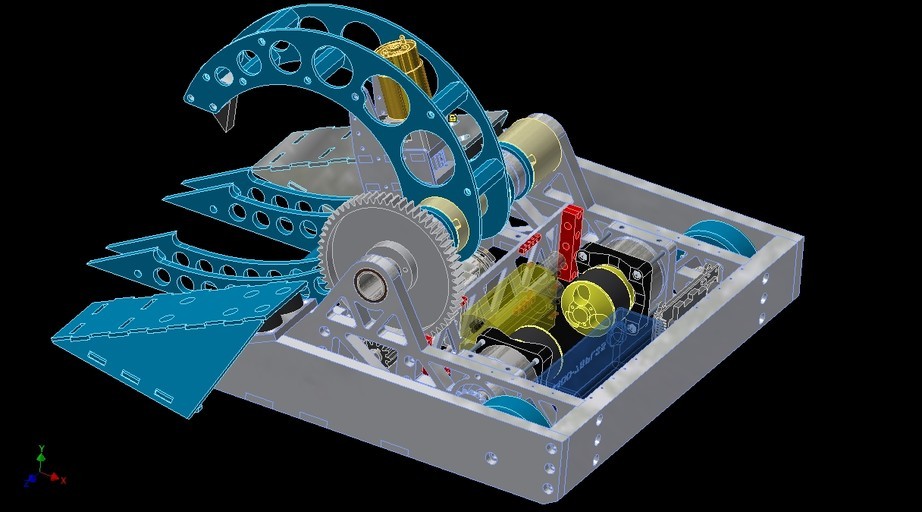
Разработка формы
Представители указали мне два материала, которые обладали благоприятно высокими показателями сопротивления разрыву и прочности на разрыв:серии Reoflex и Simpact. Эти две характеристики желательны для колесной смеси, где резина постоянно срезается по толщине протектора и волочится по земле. Я взял в руки образец ReoFlex 50 (для твердомера 50 А, который достаточно мягкий, как подошва обуви) и приступил к разработке формы и ступицы.
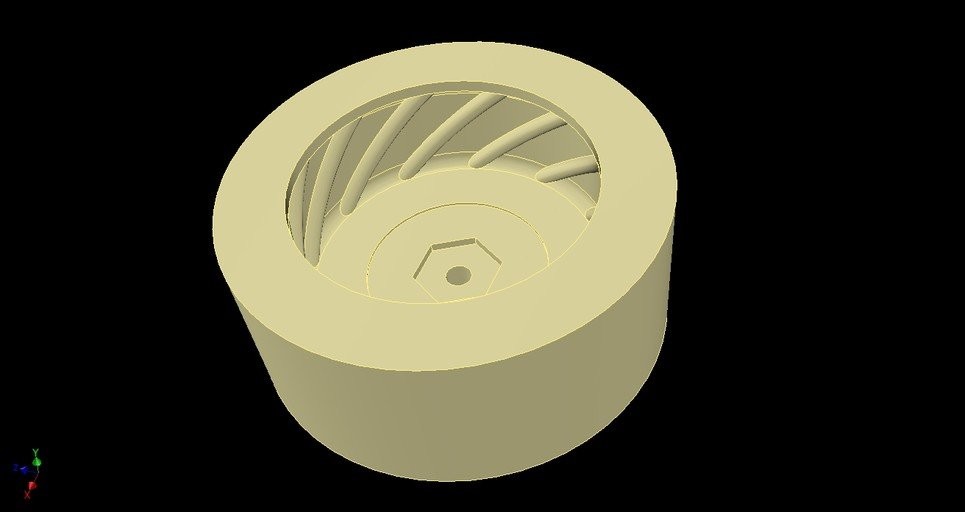
После проведения капитального ремонта в коробке я был полностью убежден, что на поверхности колеса необходима какая-то функция очистки от мусора. Хотя мы не пытаемся направлять воду или царапать грязь, как в случае с автомобильными шинами, на самой арене по-прежнему оставались рыхлые детриты и хлопья краски, с которыми приходилось бороться. Для начала сделал простой спиральный рисунок протектора. Это ни в коем случае не было оптимизировано - я просто хотел поскорее перейти к этапу формования. Я полагал, что спиральные канавки будут отталкивать мусор в сторону от пятна контакта. Точная ориентация и количество канавок, очевидно, все еще являются нерешенной наукой, если вы когда-либо ходили за покупками шин.
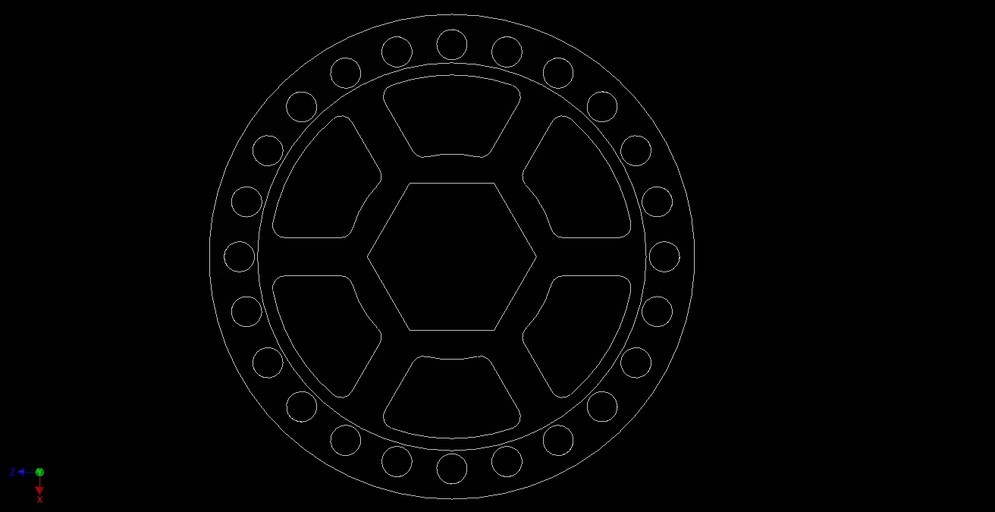
Далее передо мной стояла задача спроектировать ступицу колеса. Я просмотрел коробку колес для скутера и скейтборда в поисках вдохновения. У всех них была общая черта:сквозные отверстия или щели, в которые текла уретан. Я очень хотел, чтобы материал протектора мог оставаться на ступице даже при нарушении адгезии. Я смоделировал довольно простую цилиндрическую ступицу, но с множеством сквозных отверстий в сужающемся центральном ребре, чтобы обеспечить максимальную площадь и поперечное сечение для прилипания уретана, я выбрал оникс вместо обычного нейлона для ступицы из-за его более высокой жесткости и прочности. с учетом адгезионных свойств. Повышенная жесткость позволила бы сделать ступицу колеса легкой, а смола лучше прилегала бы к микроскопически шероховатой текстуре оникса по сравнению с глянцевым нейлоном.
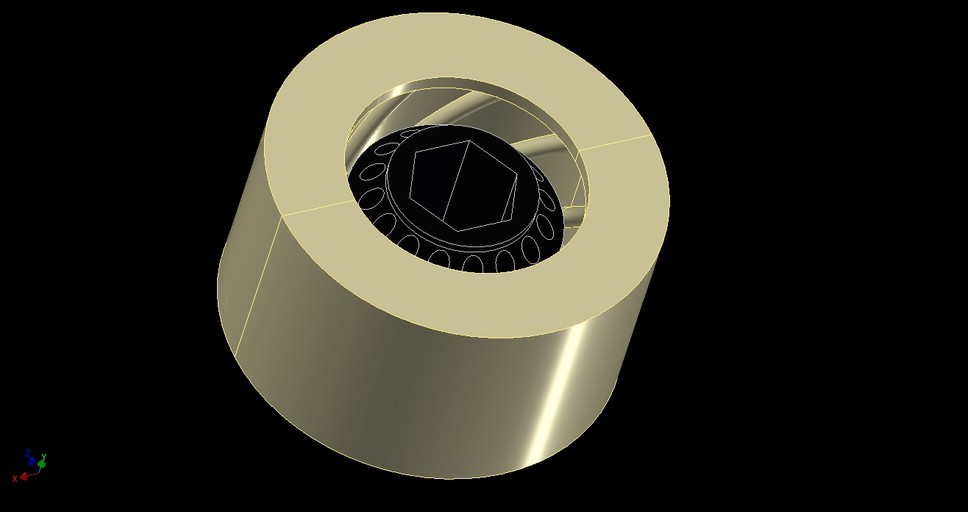
Поскольку для Tiny Overhaul также потребуются передние колеса меньшего размера, я использовал параметрические функции Autodesk Inventor, чтобы быстро создать 2-дюймовую модель. У этой формы была довольно узкая область для заливки, поэтому мне было интересно, как будет вести себя материал.
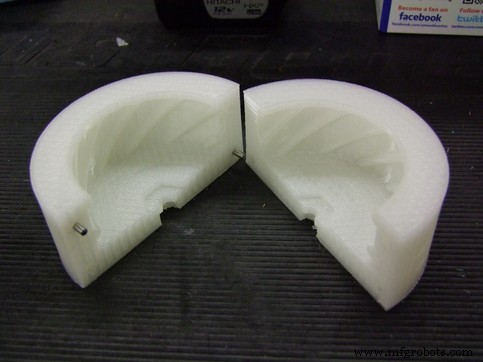
Я напечатал тестовую форму, используя простой неармированный нейлон на Mark Two. Форма была очень разреженной - 4 слоя стен и 4 слоя крыши и пола, но заполнение только 25%, напечатанное с настройкой самого грубого слоя 0,2 мм. Я смоделировал отверстия для регистрационных штифтов в половинах, чтобы обеспечить совмещение.
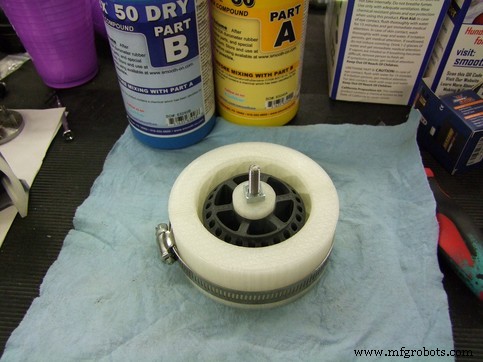
Заливка формы
Половинки формы предназначены для удержания вместе с помощью одного обычного шлангового зажима. Внутри ступица колеса сидит на переходной втулке, чтобы удерживать ее по центру в форме, и эта переходная втулка имеет сквозное отверстие на нижней стороне половин формы, так что я мог установить стопорную гайку и болт вертикально, чтобы герметизировать нижнюю поверхность ступица колеса против формы. Перед сборкой я покрыл половинки формы смазкой для формы, наносимой распылением.

По совету друзей, у которых был более обширный опыт формования и литья, я одолжил вакуумный горшок, чтобы вытащить все пузырьки воздуха из смешанной смолы. Smooth-on рекламирует свои смолы как «минимизирующие задержку воздуха», но наблюдение за кипением смеси показало мне, что это было неэффективно. Захваченные пузырьки воздуха могут ухудшить целостность протектора колеса, так как это вызовет множество разрывов в материале. Я дегазировал чашку со смешанным материалом вместо того, чтобы поместить всю форму с жидкой смолой в камеру, так как весь воздух внутри половин формы из-за того, что напечатан пустотелым, скорее всего, деформирует их или даже будет вытекать и медленно пузыриться.
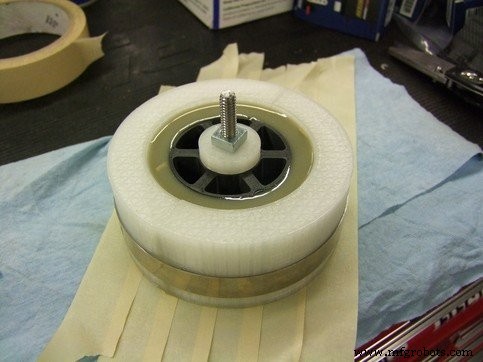
На заливку 3-дюймовой колесной формы ушло около 2 минут - я наклонил чашу для смешивания ровно настолько, чтобы поддерживать непрерывный поток жидкости, позволяя смоле осесть на дно, а не скапливаться или выступать над формой. Позволить смоле «найти свою ватерлинию» - вот как избежать попадания в деталь больших пузырьков воздуха.
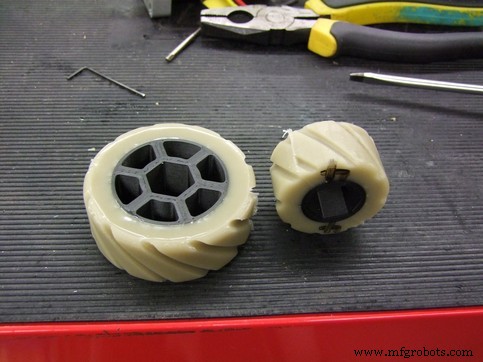
Я залил как колесо диаметром 3 дюйма, так и колесо диаметром 2 дюйма в качестве стартовой партии. После того, как первые два колеса хотя бы окрепли, пришло время заняться производством. Я напечатал дополнительные формы, чтобы можно было заливать 4 или более колес одновременно - одна из моих чашек для смешивания идеально подходила для двух колес по 3 дюйма и двух колес по 2 дюйма, так что это стало стандартом.
Процесс лечения
Большинство производителей смол рекомендуют медленное отверждение при комнатной температуре с последующим нагреванием материала для большего усиления поперечных связей полимера. Например, в техническом описании Reoflex 50 сказано, что материал следует нагревать до 65 по Цельсию в течение 4-8 часов. Я использовал камеру, нагретую до температуры примерно 70 градусов по Цельсию:новые колеса, полученные в результате этого ускоренного отверждения, были определенно более жесткими и более упругими на ощупь.
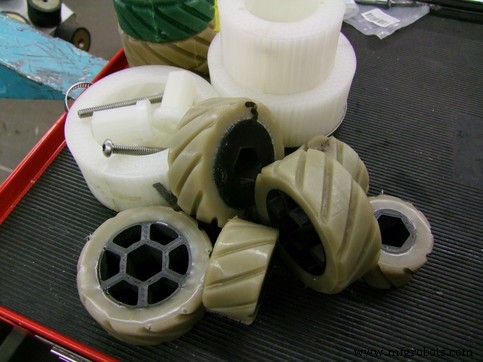
Результатом после недели экспериментов было около полдюжины колес каждого размера. Я исчерпал свой запас ReoFlex 50, поэтому решил, что это хорошее место, чтобы остановиться и убедиться, что колеса действительно работают в условиях конкуренции, прежде чем тратить больше денег на материал. За последние несколько дней у меня был хороший цикл:я заливал формы в последнюю очередь вечером перед отъездом, снимал их утром, а затем запекал в течение дня.
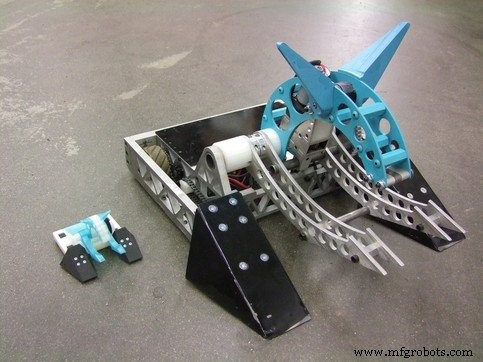
Вот так они и выглядят, установленные в боте. Если вас интересует разработка «30-Haul», как мы его назвали, вы можете проверить ветку его сборки на моем веб-сайте.
Ну и что дальше? Теперь, когда я изучил производственный процесс и передо мной базовый дизайн, пришло время начать настоящую науку. Следите за обновлениями во второй части этой серии, где я пытаюсь сделать колеса из различных составов и проверить их сцепление на окрашенном стальном полу. А пока вот как эти колеса выглядели после нескольких жестких соревнований по вождению!
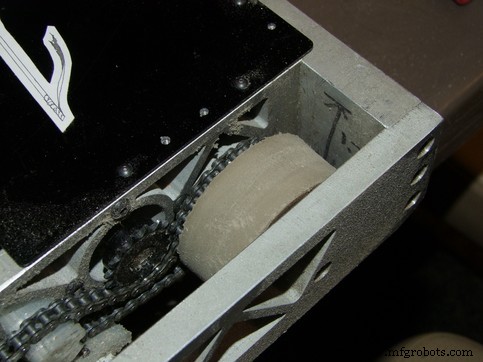
Узнайте больше о принтерах Markforged и о том, как они подходят для ваших приложений!
3D печать
- Интервью с экспертом:Спенсер Райт из pencerw.com и nTopology
- Обработка 3D-печатных деталей ... мелками?
- Интервью с экспертом:Ибрахим Хадар из Markforged
- Stratasys сотрудничает с GrabCAD и e-Xstream
- Stratasys возрождает MakerBot с помощью метода
- Литье в песчаные формы с использованием технологии FDM
- Лучший контроль качества с 3D-печатными деталями
- Закрепите себя функциональными деталями, напечатанными на 3D-принтере!
- Новый взгляд на картинг с 3D-печатными деталями
- Прототипирование и мелкосерийное производство методом литья под давлением