Новые горизонты в сварке термопластичных композитов
Этот блог сопровождает публикацию в сентябре 2018 г. «Сварка термопластичных композитов». Это подборка изображений и деталей, которые не вошли в печатную статью, включая график разработок в области индукционной сварки и подробности о квалификации будущих коммерческих самолетов, а также короткие разделы о ремонте, разработках для автомобилей и термореактивных термопластах (TS -ТП) сварка.
Чтобы еще раз подчеркнуть, почему сварные сборки из термопластичного композита (TPC) представляют интерес как для аэрокосмических, так и для автомобильных легких конструкций, сравните два изображения ниже задней переборки давления Airbus A320. Верхнее изображение - текущая версия из алюминия. Обратите внимание на большое количество заклепок. А теперь сравните это со сварным демонстратором TPC, представленным Premium Aerotec на авиасалоне ILA 2018 в Берлине. Обратите внимание на отсутствие заклепок. Для композитов это не только снижает вес, время и стоимость крепежа, но также сокращает время и стоимость размещения и сверления отверстий, а также очистки и проверки этих отверстий. Это также означает более легкие конструкции без ламинатных накладок, необходимых для компенсации разрезов в несущих волокнах.
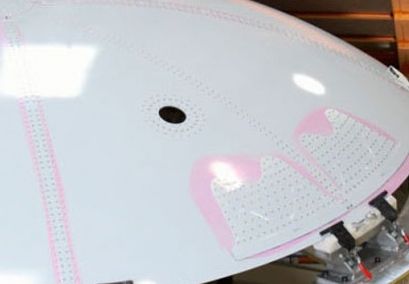
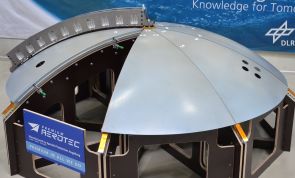
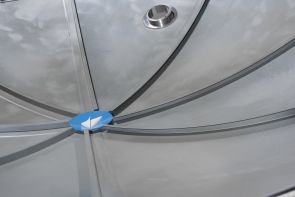
Сварная задняя перегородка A320 из термопластичного композита (внизу) предлагает безклепочное решение по сравнению с нынешней алюминиевой конструкцией (вверху).
ИСТОЧНИК:RUAG (вверху) и Premium Aerotec (внизу), Центр технологий легкого производства DLR (Аугсбург, Германия)
«Еще одним преимуществом является то, что контроль сварных конструкций проще по сравнению со сборками, склеенными клеем», - говорит д-р Ханс Луинге, директор по исследованиям и разработкам термопластичных композитов и директор по разработке продукции TenCate-Toray Group, поставщика материалов TPC. «С-сканирование работает хорошо, показывая, нет ли в ламинате пористости, что означает, что сварной шов хороший. Для структур, склеенных с помощью клея, у вас может быть соединение поцелуев или загрязнения, которые трудно обнаружить ». Хотя TenCate-Toray не занимается разработкой сварочных технологий, она поддерживает целый ряд отраслевых проектов и проектов заказчиков. «Мы оптимизируем наши материалы по мере необходимости, - говорит Луинг, - и пытаемся помочь направить разработки в правильном направлении, основываясь на нашем многолетнем участии в таких усилиях, как TAPAS, и с такими партнерами, как KVE Composites, TPRC, рядовыми поставщиками и OEM-производителями».
Разработки для индукционной сварки
Компания KVE Composites разрабатывает индукционную сварку для TPC с 2001 года. В первых приложениях использовалась ткань из углеродного волокна / ламинат PPS, в том числе рули высоты и руль направления для самолетов бизнес-класса Gulfstream G650 и Dassault Falcon 5X.
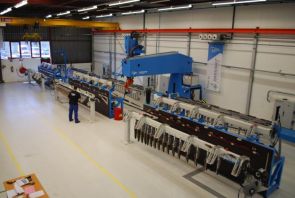
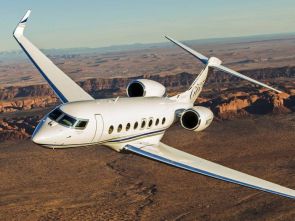
Композиты KVE помогли развивать производство GKN Fokker сваренных индукционной сваркой рулей высоты и руля направления (слева) для самолетов Gulfstream G650 (справа) и Dassault Falcon 5X.
ИСТОЧНИК:KVE Composites, GKN Fokker (слева) и Gulfstream (справа).
Другие области применения индукционной сварки TPC включают люки доступа к топливным бакам производства AVIACOMP S.A.S. (Launaguet, Франция и теперь входит в Sogeclair Group) для крыла Airbus A220 (ранее Bombardier CSeries). (Авиакомп также произвел стрингеры для сварного фюзеляжа TPC компании STELIA, показанного на Парижском авиасалоне в 2017 году.)
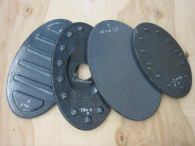
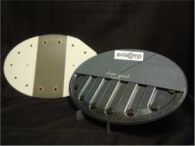
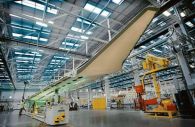
Aviacomp использует индукцию Технология сварки, разработанная KVE Composites при производстве люков доступа к топливным бакам TPC для узкофюзеляжных самолетов Airbus A220.
ИСТОЧНИК:Aviacomp, часть Sogeclair Group.
Эта общая категория входных дверей дает возможность сварке TPC сократить расходы, что показано в исследовании конструкции и производства, проведенном KVE Composites. Даже небольшие самолеты могут иметь до 60 таких панелей доступа, все различной формы и обычно изготавливаемых с использованием композитной многослойной конструкции с механически обработанной сотовой сердцевиной. «Если вы используете сварную сборку из термопласта, вы можете изготовить все различные панели доступа для самолета, затратив всего 100 000 долларов на инструменты, что является значительной экономией», - говорит управляющий директор KVE Composites Харм ван Энгелен. «Нам не нужно обрабатывать сердечник, мы просто используем« лего-подобные »компоненты - плоские листы и штампованные ребра жесткости, сваренные вместе, чтобы сформировать различные формы. Кроме того, наши инструменты больше похожи на сварочные приспособления, поэтому они относительно невысоки по сравнению с тем, что они используют сегодня. Все люки для доступа к самолету можно было изготовить в одной сварочной камере ».
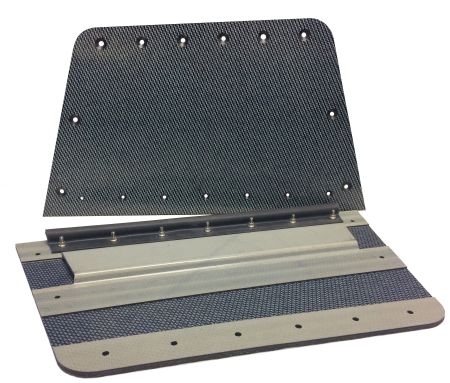
Сварная термопластическая сборка для навесных панелей самолета изготавливаться с использованием автоматических формовочных и сварочных ячеек и сэкономьте 100 000 долларов на инструментах. ИСТОЧНИК:Композиты КВЭ.
KVE Composites продолжает разработку технологий сварки TPC, как показано на графиках ниже. Производственная ячейка, показанная внизу на 2019 год, представляет собой машину Falko ATL (автоматическая укладка ленты), произведенная компанией Boikon (Лик, Нидерланды) с использованием концевого эффектора для ультразвуковой сварки, разработанного GKN Fokker. «Эта роботизированная ячейка обеспечивает более эффективный процесс и систему управления для следующего уровня объемного производства деталей TPC по сравнению с методами захвата и размещения, используемыми сегодня», - объясняет руководитель отдела исследований и разработок KVE Composites Мартен Лабордус. «Например, вы можете полностью автоматизировать укладку слоистых пластиков обшивки и ребер для региональной поверхности управления струей (которая составляет примерно 60 мм x 3 м), применить этап консолидации и формовки вне автоклава, а затем завершить сборку в соседняя сварочная ячейка ». Аппарат Falko ATL также демонстрирует систему управления с обратной связью, уже разработанную GKN Fokker для ультразвуковой сварки. «Машина способна регулировать уровень энергии в зависимости от типа, толщины и формы материала, однако после формования готовой детали TPC требуется полное уплотнение расплава плоской преформы», - поясняет Арнт Оффринга, руководитель отдела Aerostructures R&T для GKN. Фоккер.
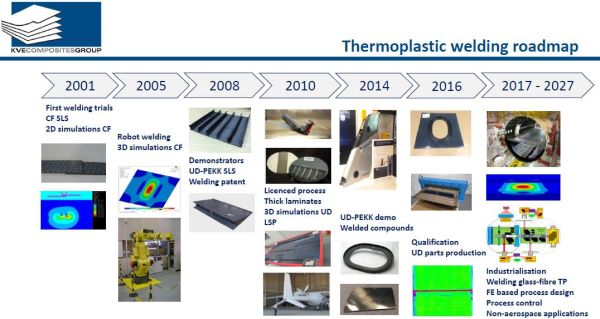
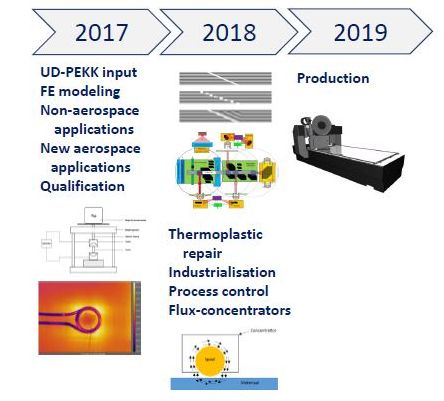
Квалификация
Показано выше как ключевая инициатива развития в 2017 году, квалификация индукционной сварки для авиационных конструкций TPC является постоянным приоритетом. Согласно аннотации к предстоящей презентации KVE Composites на 4 th Int. Конф. и выставка термопластичных композитов (ITHEC, 30-31 октября 2018 г., Бремен, Германия), за последние несколько лет в сварке термопластичных композитов (TPC) произошел сдвиг от полимеров, таких как PPS и PEI, к полимерам более высокого качества, таким как PEEK. , PEKK, а теперь и Low Melt PAEK (LM PAEK, подробнее читайте в моем блоге «PEEK против PEKK против PAEK ...»), а также на автоматически размещаемые ленты UD и более толстые ламинаты для более высоконагруженных структур. В ответ KVE Composites стремилась улучшить и стандартизировать инструменты и оборудование, а также имитационные модели на основе FEA.
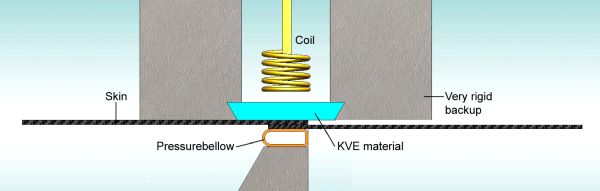
Стандартизированная установка для аттестации индукционной сварки новыми материалами.
ИСТОЧНИК:Композиты KVE
Чтобы помочь в развитии и аттестации процесса индукционной сварки этих новых композитных ламинатов, KVE Composites разработала стандартизированную установку для сварки на сдвиг внахлестку, а также испытательные образцы на L- и T-отрыв. Эта установка включает:
- Жесткий каркас для восприятия нагрузок от давления на ламинат во время сварки.
- Нижний инструментальный блок, который можно разместить под рамой, чтобы обеспечить воспроизводимую сварку стандартных панелей.
- Надувной стержень (сильфон на рисунке выше) в нижнем блоке инструментов, который может расширяться только в одном направлении для сжатия ламината, привариваемого к специальному радиатору («материал KVE» на рисунке выше), чтобы удерживать тепло при сварке. интерфейс.
Меняя местами нижние блоки инструментов, можно сваривать различные стандартные образцы, а затем подвергать их ультразвуковому контролю, после чего образцы меньшего размера можно разрезать и испытать механически. Эта стандартизованная установка уже установлена:
- Исследовательский центр термопластов (TPRC, Энсхеде, Нидерланды)
- Центр Макнейра в Университете Южной Каролины (Колумбус, Южная Каролина, США)
- Нидерландский аэрокосмический центр (NLR, Marknesse, Нидерланды).
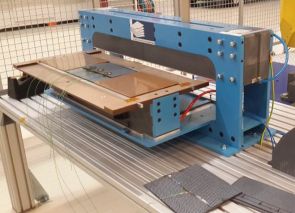

Стандартизированная индукционная сварка установка на KVE (слева) и сварной образец углеродного волокна UD / PEKK с термопарами для регистрации температуры на линии сварки (справа).
ИСТОЧНИК:Композиты КВЭ.
Ремонт
Еще одно ключевое направление развития - ремонт авиастроек TPC. «Сначала мы сосредотачиваемся на структурах CF fabric / PPS, которые квалифицированы и летают», - говорит Лабордус. «Процесс в основном такой же, как и при ремонте из термореактивного композита:удалить поврежденный материал, подготовить эту область с помощью конической косынки, а затем приклеить ремонтную заплату из препрега. Лабордус говорит, что одна из проблем заключается в том, что термопластический препрег при комнатной температуре становится твердым и не прилипает, «поэтому трудно добиться соответствия геометрии». Однако он считает, что роботизированные ремонтные системы, разрабатываемые Airbus, Lufthansa и другими, предлагают решение.
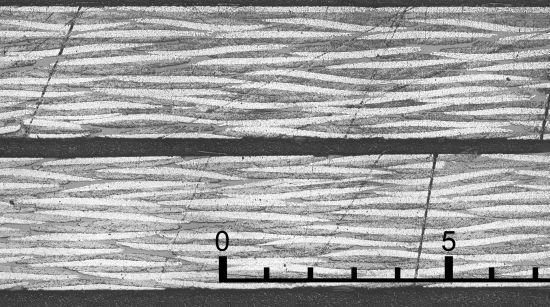
В рамках продолжающегося развития ремонтных работ на основе сварных конструкций из термопластических композитов, KVE Composites добилась индукционной сварки 2D линейных конических соединений в слоистых материалах CF ткань / PPS с однородной толщиной и 90% свойств первичного материала.
ИСТОЧНИК:Композиты КВЭ.
Такие системы используют метрологию для точного измерения конических шарфов, обработанных с помощью робототехники, а затем склеивают предварительно изготовленную заплату, которая была обработана с помощью роботизированной конической обработки для соответствия. «Мы хотим использовать индукционную сварку, чтобы приварить заплатку из термопласта к исходной конструкции», - говорит Лабордус, но все еще остаются проблемы, которые необходимо решить. «В зависимости от формы детали и участка вихревые токи образуются не везде, поэтому мы можем получить области охлаждения или перегрева. Компания KVE Composites проработала это и смогла получить двухмерное линейное коническое соединение в слоистых материалах CF ткань / PPS с однородной толщиной и идеальным сварным швом. «Мы были в пределах 10% от свойств первичного материала», - говорит Лабордус.
Следующим шагом будет индукционная сварка двух прямоугольных деталей, каждая со скошенной кромкой, а затем приварить конусообразный участок к круглому / эллиптическому отверстию с коническим скосом, что по сути является методом, используемым для ремонта термореактивных композитов. «Если это сработает, мы перейдем к ламинату UD, изготовленному из PEEK и PEKK», - говорит Лабордус. Он отмечает, что система использования индукционной катушки для ремонта в полевых условиях еще не была продемонстрирована, «но может сделать это в лаборатории». Другой вопрос - как приложить давление для достаточно тесного контакта ремонтной заплатки и конической поверхности. «Сейчас в лабораторном приборе используется давление 5 бар. Я не уверен, достаточно ли давления только из вакуумного мешка, но для более плоского UD-материала достаточно 1 бара из вакуумного мешка ».
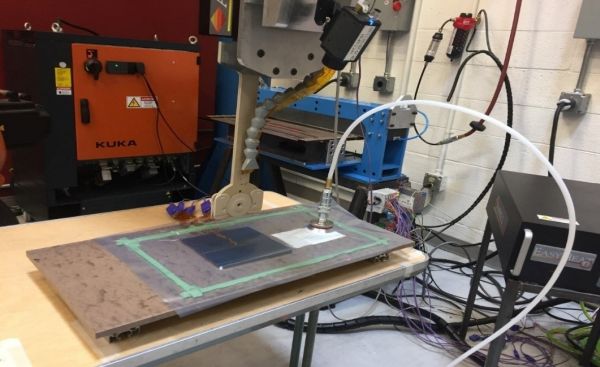
Индукционная сварка под вакуумным мешком - возможное средство для будущего ремонта термопластических композитов в полевых условиях - разрабатывается Мишелем ван Туреном и его командой в Центре Макнейра Университета Южной Каролины. ИСТОЧНИК:Michel van Tooren.
Эту работу в KVE Composites расширяет Мишель ван Турен, директор Центра многофункциональных материалов и конструкций SmartState, входящего в Центр Макнейра в Университете Южной Каролины (Колумбия, Южная Каролина, США). «Мы производим индукционную сварку термопластичных композитов под вакуумным мешком, что очень похоже на то, как сегодня проводится ремонт композитов в полевых условиях с использованием горячего склеивания и теплового покрова», - поясняет он. «Вакуумный мешок ведет себя как мягкий инструмент для сжатия двух частей. Вы применяете индукционный ток и добиваетесь ремонта плавлением. Вам просто нужно определить границы и параметры процесса. В некотором смысле это проще, чем ремонт термореактивного материала, потому что вы всегда можете переплавить ремонт при необходимости, даже на другом конце света или после 20 лет эксплуатации. И в результате получается не адгезионное соединение, а связная деталь, таким образом, вы устраняете все проблемы со склеиванием и как узнать, есть ли у вас хорошее соединение при ремонте из термореактивного материала ». Он также считает, что с развитием технологий автоматизированного ремонта роботов «индукционная сварка ремонт будет относительно несложной задачей».
Термореактивный материал для сварки термопластов
Van Tooren также разрабатывает индукционную сварку для соединения термореактивных и термопластичных композитов. «Мы вводим термопласт в термореактивный композит, но только там, где мы хотим сваривать», - поясняет он. «Мы прививаем наночастицу и проводим небольшую кросс-полимеризацию. В результате получается островок термопласта, имплантированный в термореактивный композит и химически расплавленный с ним. Затем я могу приварить островок из термопласта ». Опять же, видение - это альтернативные методы соединения и сборки композитов, которые позволяют избежать сверления отверстий и проблем, связанных с обычным клеевым соединением.
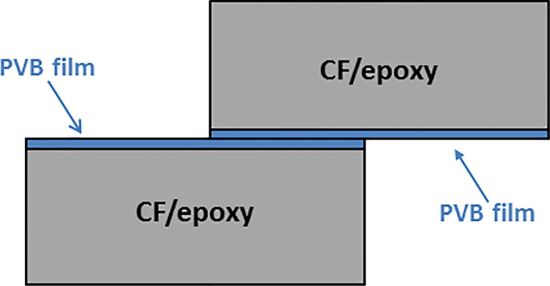
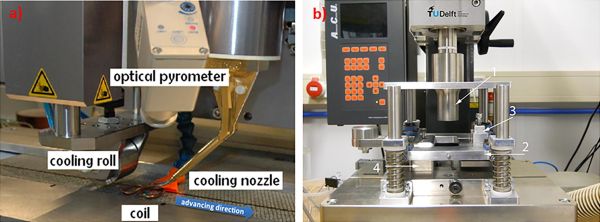
Схема соединения TSC-TSC через термопластический связующий слой ПВБ перед сваркой (вверху). Установки (внизу) для индукционной сварки (слева) и ультразвуковой сварки (справа).
ИСТОЧНИК:«Гибридная сварка композитов на основе CF / эпоксидной смолы».
Сварка термореактивных композитных материалов (TSC) с ламинатами TPC (или сварка TS-TP) проводится несколькими исследовательскими организациями. Ирен Фернандес Виллегас из Технического университета в Делфте, которая упоминается в печатной статье как лидер в разработке непрерывной ультразвуковой сварки TPC, стала соавтором статьи 2017 года под названием «Гибридная сварка композитов на основе эпоксидной смолы, армированной углеродным волокном» вместе с Франческой Лионетто в Университет Саленто (Лечче, Италия), Сильвио Паппада из CETMA Composites (Брандизи, Италия) и другие. Основы следующие:
- Поливинилбутирал (ПВБ) представляет собой полукристаллический недорогой термопластичный полимер с температурой плавления 150–170 ° C, характеризующийся превосходной связующей и пленкообразующей способностью и адгезией ко многим поверхностям.
- ПВБ (Mowital, поставляется Kurakay) использовался в качестве связующего слоя, добавлялся и отверждался совместно с 14-слойным слоистым материалом из углеродного волокна / эпоксидной смолы TSC (препрег Hexcel 3501-6 с объемным содержанием волокна 58% и 180 ° C отверждения).
- Макромеханическое сцепление между соединительным слоем PVB и композитом CF / эпоксидной смолы было достигнуто за счет частичного проникновения смолы PVB в первый слой TSC (обычно толщиной от 10 до нескольких сотен микрон) во время совместного отверждения и диффузия эпоксидных мономеров в термопластичную пленку ПВБ.
- Индукционная сварка и ультразвуковая сварка привели к получению достаточно прочных сварных соединений, в результате чего соединения CF / эпоксидной смолы с CF / эпоксидной смолой, сваренные через соединительные слои PVB, показали прочность на сдвиг внахлестку ≈25 МПа, что находится в типичном диапазоне значения прочности для клеевых соединений CF / эпоксидной смолы.
Автомобильная промышленность
Почти все компании, упомянутые в статье о термопластической сварке, занимаются как автомобильной, так и аэрокосмической отраслями. «Сварка помогает сделать композиты конкурентоспособными по сравнению с алюминием», - говорит Оффринга из GKN Fokker. «Автомобильная промышленность также рассматривает сварку как быструю альтернативу склеиванию. Мы поговорили с несколькими автомобильными компаниями по поводу быстрой обработки композитов ». Он отмечает, что автомобильные кузова из углеродного волокна в основном термореактивные, склеенные с помощью клея определенной толщины. «Если бы вы могли сделать эти детали из термопласта композитов и устранение зазоров между компонентами путем сварки сборки, тогда вы сможете сделать конструкцию корпуса более жесткой, что принесет выгоду в весе, стоимости и производительности ».
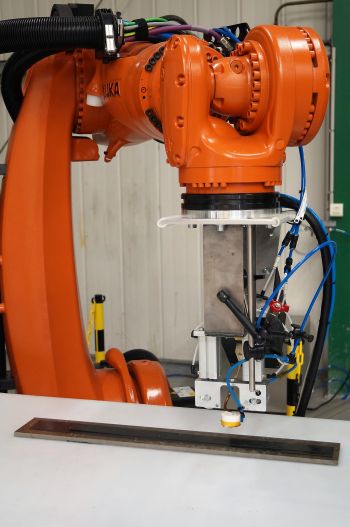
динамический наладка процесса индукционной сварки.
ИСТОЧНИК:Composite Integrity.
Жером Рейналь, менеджер по развитию бизнеса Composite Integrity, также видит потенциал. Его компания работала со STELIA Aerospace над разработкой процесса динамической индукционной сварки, используемого для соединения ленточных стрингеров CF / PEKK UD и обшивки фюзеляжа в демонстраторе TP, представленном на Парижском авиасалоне в 2017 году. «Мы разработали резистивную сварку для автомобилей с композитами из полиамида [PA, нейлона] и полипропилена [PP]», - говорит Рейнал. «Для этого у нас есть множество различных технологий. Например, мы можем вставить металлическую проволоку в одну часть, поместить ее в контакт с другой частью и ввести ток. Мы также можем разместить резистивную накладку из углеродного волокна на стыке сварки, чтобы генерировать необходимое сварочное тепло ». В одной из разработок два компонента из CF / PA были сварены с использованием специально разработанной резистивной накладки, изготовленной из того же полимера и стекловолоконного полотна, чтобы электрически изолировать прилегающий ламинат и сконцентрировать энергию на линии сварки. А как насчет металлических вставок, которые очень характерны для автомобильных запчастей? «Детали с металлическими вставками не представляют проблем при контактной сварке, а при индукционной сварке вы должны использовать специально разработанную катушку или каким-либо другим образом изменять электромагнитные поля и ток», - отвечает Рейнал. «Это необходимо разработать, но это похоже на то, что мы уже продемонстрировали для автоматизированного производства конструкций самолетов».
Дальнейшие разработки и другие проекты
Одно замечание относительно начального изображения. На нем показана CAD-визуализация автоматизированного процесса, разработанного DLR Center for Lightweight Production Technology (DLR ZLP, Аугсбург, Германия) с использованием ультразвуковой сварки Возьмите промышленного робота KUKA Quantec KR210, чтобы соединить восемь секций TPC в заднюю переборку давления (RPB) для самолета типа A320. В сопроводительной печатной статье о сварке TPC я рассказал о разработке контактной сварки , разработанной DLR ZLP. Метод, который использовался на демонстраторе A320 RPB Premium Aerotec, представленном на авиасалоне ILA 2018 в Берлине. По словам Ларса Ларсена, руководителя группы по технологиям сборки и соединения в DLR ZLP, «параллельно с процессом контактной сварки с использованием« сварочного моста »мы также разработали роботизированную головку для ультразвуковой сварки. Мы завершили предварительные испытания, чтобы определить соответствующие параметры сварочного процесса, и в следующие месяцы мы доработаем интеграцию этого рабочего органа ультразвуковой сварки в нашего робота. Наша цель - разработать единый производственный процесс сварки стрингеров фюзеляжа самолетов и задней переборки давления, изготовленных из термопластичных композитов ».
Другие проекты, которые у меня не было возможности охватить в этот раз, включают EireComposites и его участие в проектах Ybridio и Innova, исследуя потенциал сварки для снижения затрат и повышения автоматизации. Компания сообщает о возможности индукционной и контактной сварки композитов CF / PEEK, CF / PEKK и GF / PP, а также о том, что термопластическая сварка была оценена для крыла Bombardier CSeries (теперь Airbus A220).
Компания Tods Aerospace, теперь входящая в состав Unitech Aerospace, участвовала в Национальной программе использования аэрокосмических технологий (NATEP), спонсируемой Rolls-Royce, в рамках которой рассматривалась разработка метода контактной сварки без использования металлических встроенных имплантатов. TenCate-Toray и Национальный центр композитов (Бристоль, Великобритания) также были партнерами.
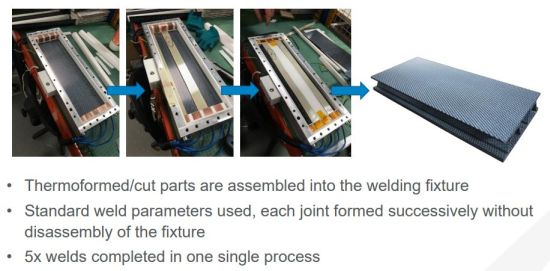
Этот демонстратор процесса исследовал метод изготовления конструкций TPC с жесткой шляпкой. ИСТОЧНИК:Unitech Aerospace (начало с Раздела 6, стр. 39)
Следите за обновлениями, поскольку я планирую в ближайшем будущем осветить разработки Laser Zentrum Hannover (LZH) по лазерной сварке термопластичных композитов.
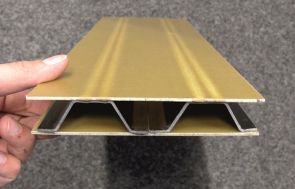
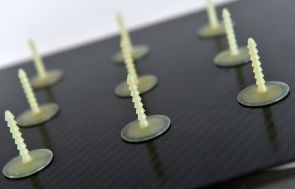
ИСТОЧНИК:LZH Laser Zentrum Hannover eV
Смола
- Covestro увеличивает инвестиции в термопластические композиты
- Термопластические композиты в Oribi Composites:CW Trending, эпизод 4
- Проект RECONTRAS проверяет использование микроволн и лазерной сварки для получения перерабатываемых композитов
- Новые походные ботинки Salewas из термопластичных композитов
- Устранение проблем термоформования термопластичных композитов
- Термопластические композиты:структурный кронштейн бампера
- Toray Advanced Composites расширяет возможности термопластичных композитов
- Консорциум термопластичных композитов IRG CosiMo представляет новые объекты
- Термопластические композиты:живописный вид
- Сварка термопластичных композитов