Устранение проблем термоформования термопластичных композитов
Примечание. Информация и изображения для этой статьи получены из курса «Продвинутое формование термопластичных композитов», проводимого Исследовательским центром термопластичных композитов (TPRC).
Термопластические композиты (ТПК) впервые получили преимущество в связи со спросом на более высокие темпы производства в аэрокосмической отрасли и других легких приложениях. Производство деталей за считанные минуты сделало термоформование (также известное как штамповка) наиболее распространенным процессом термопластичных композитов и первым в мире массовым производством летающих деталей (см. «Внутри очага термопластичных композитов» и «Время закрепления термопластичных композитов…»).
Процесс начинается с заготовки - предварительно уплотненного термопластичного композитного ламината с требуемой ориентацией слоев - и включает следующие этапы (рис. 1):Подготовка заготовки (резка и фиксация), заготовка нагрев, перенос в форму, позиционирование заготовки, формовка, охлаждение, извлечение детали из формы и обрезка / чистовая обработка. Процесс термоформования - это простая концепция, но она связана со сложностями и проблемами, которые необходимо решить для получения воспроизводимых высококачественных композитных деталей.
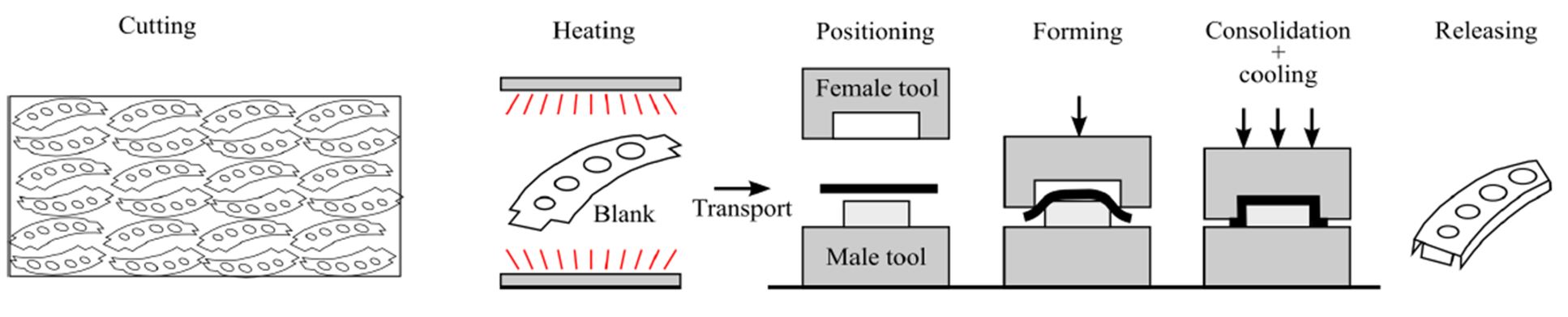
Избегайте морщин
Морщинка - это визуальный и функциональный дефект. Это можно описать как изгиб материала вне плоскости. Основная причина - недостаточные деформации сдвига, такие как промежуточное скольжение и сдвиг внутри слоя, во время обработки. Сморщивание происходит преимущественно на двояко изогнутых поверхностях. Рассмотрите следующие действия, чтобы уменьшить морщины.
Достаточный предварительный нагрев и быстрый перенос. Во время формования заготовки температура должна оставаться выше температуры плавления (T m ) матрицы TPC, чтобы обеспечить деформацию сдвига. Учтите, что во время перехода от стадии предварительного нагрева к форме температура может значительно упасть - возможно, на 40-50 ° C за три секунды. Таким образом, предварительный нагрев должен быть достаточно высоким, чтобы полимер оставался выше T m . - или температура стеклования (T g ) для аморфных полимеров - после переноса и при формовании. Холодная заготовка не деформируется должным образом, и на ней появятся морщины. Однако будьте осторожны, чтобы не перегреть заготовку, чтобы избежать деградации полимера.
Стиль переплетения и расположение ткани . Атласные ткани (HS) имеют лучшую драпируемость из-за более легкой деформации сдвига в плоскости, что помогает предотвратить появление морщин. Драпируемость тканых материалов от высшей к низшей составляет:8HS> 5HS> саржа 2 x 2> полотняное переплетение. Ткань 5HS часто является хорошей отправной точкой, поскольку она сочетает в себе драпируемость и механические характеристики. Заготовки, изготовленные с использованием однонаправленного армирования (UD), склонны к более сильному складыванию, чем ткани HS, из-за высокого трения между волокнами, которое сопротивляется сдвигу в плоскости. Разрешение сдвига в плоскости является ключом к успеху при формовании UD-заготовок, особенно с дважды искривленными поверхностями.
Ориентация слоев, например [0, 90, ± 45] s найденный в квазиизотропной укладке, может подавлять деформацию сдвига, которая усиливает морщины. В качестве альтернативы, укладка перекрестного слоя (например, [0, 90]) поможет предотвратить образование складок, поскольку сдвиг не ограничивается другими слоями.
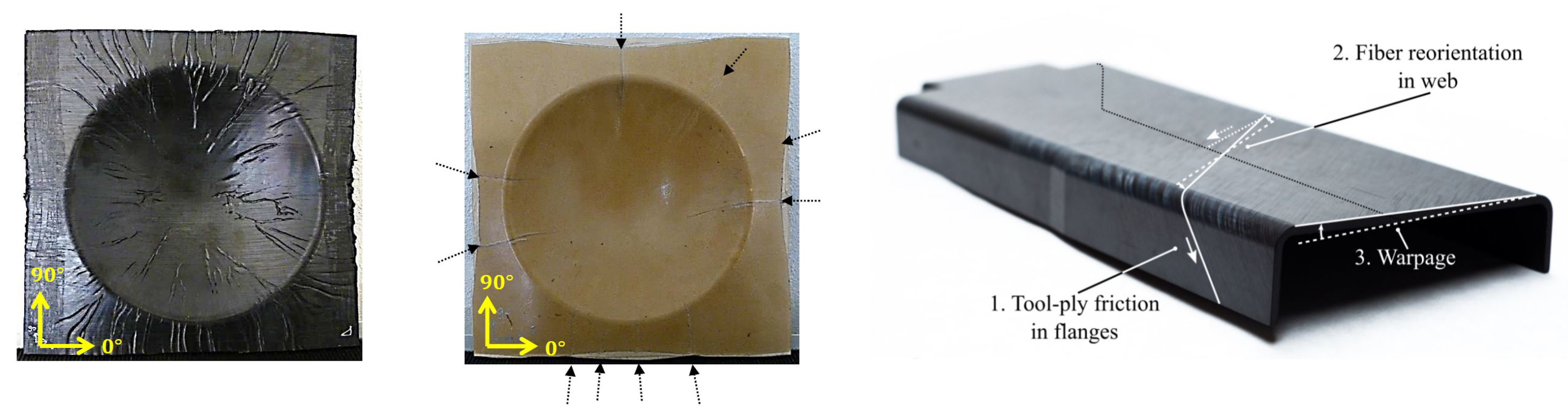
Рис. 2. Избегайте морщин и короблений
Полусферическая часть показывает множество мелких и крупных морщин при использовании бланка UD (слева) , а при использовании бланка 8HS видны только крупные морщины (справа) . Деформация в этом композитном лонжероне возникла в результате переориентации волокон из-за трения между пластинами во фланцах. Фотография:«Пределы образования термопластичных композитов» Д.Дж. Wolthuizen, et. al. ( слева ) и «Быстрое производство термопластичных композитов по индивидуальному заказу с помощью автоматической укладки и штамповки» Тджитсе К. Сленж ( справа ).
Подготовка и фиксация пустого места . Захваты и натяжители могут использоваться для удержания заготовки в напряжении в областях, склонных к изгибу вне плоскости. Поиск оптимизированной конфигурации может занять много времени, потребуется несколько итераций, но использование программного обеспечения для моделирования процесса помогает. Правильное натяжение заготовки также предотвращает провисание заготовки, которое может вызвать проблемы во время переноса и формовки. Такие проблемы включают в себя слишком быстрое касание заготовки формы, что может привести к попаданию слишком большого количества материала на форму до того, как произойдет драпирование, что приведет к короблению и складкам. Заготовка также может провиснуть и коснуться нагревателя, что может привести к повреждению заготовки или остановке процесса.
Оптимизация окончательной геометрии заготовки и обрезка ее до почти чистой формы может предотвратить образование складок и уменьшить количество брака. Порезы и вытачки также могут помочь предотвратить изгибание вне плоскости за счет снижения напряжения волокон, что способствует лучшему формованию.
Решение проблем с дизайном пресс-форм
Во время термоформования и аналогичных процессов формования сама форма может создавать проблемы. Правильная конструкция пресс-формы может помочь избежать проблем, связанных с затратами на пресс-форму, нагревом, дефектами деталей и демонтажем.
Материалы инструмента для литья под давлением . Чтобы выбрать правильный материал для термоформовочного инструмента, примите во внимание материалы, используемые для конечной детали, так как они будут влиять на требуемую температуру пресс-формы (T mold ). Например, следуя практическому правилу T mold =(Т м + Т g ) / 2 , деталь из армированного PPS (полифениленсульфид T m =280 ° C) потребуется T пресс-форма примерно 180 ° C. (Аморфные и полукристаллические термопластичные полимеры имеют T g , но полукристаллические полимеры также имеют T m .) Таким образом, требуется металлическая форма для отвода тепла от плиты нагретого пресса или нагретого инструмента для формования детали. Электропроводность также необходима для эффективного охлаждения деталей. Однако для детали, изготовленной с использованием армированного ПММА (полиметилметакрилата), который имеет гораздо более низкую T g (~ 100 ° C), деревянного или эпоксидного инструмента может быть достаточно при комнатной температуре.
Другие соображения включают текущий этап разработки и доступный бюджет, а также количество деталей, которые должны быть изготовлены из инструмента. Во время обработки пресс-формы подвергаются трению, высокой температуре и давлению. Поскольку древесина и эпоксидная смола имеют более низкую термостойкость и несущую способность по сравнению с металлами, формы, изготовленные из этих материалов, будут иметь более короткий срок службы и больше подходят для мелкосерийного производства, тогда как металлические инструменты будут предпочтительнее для крупносерийного производства.
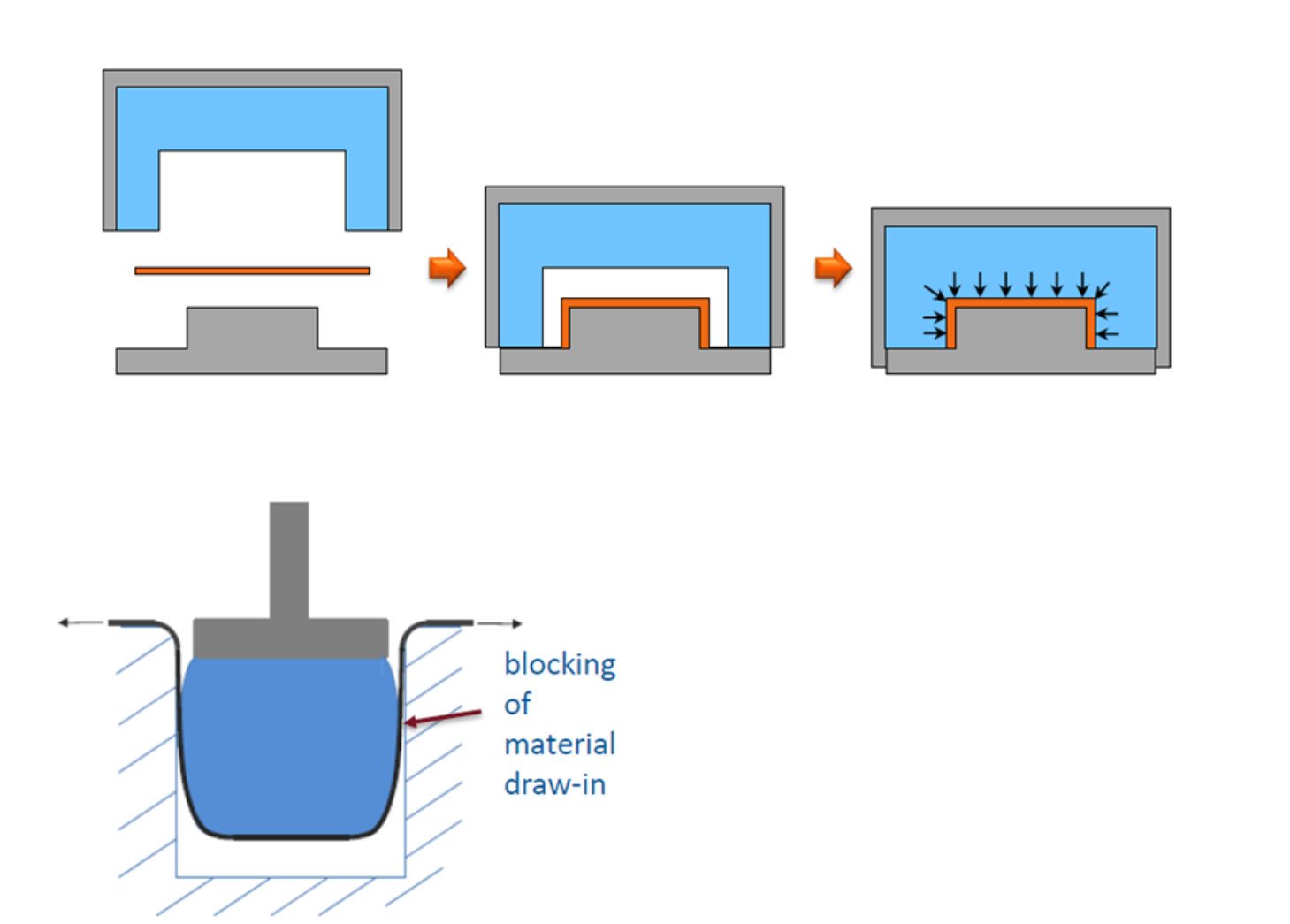
Еще одна система материалов, которую следует учитывать для инструментов, - это металл-резина. , где одна половина согласованного набора металлическая, а другая - резина. Это обеспечивает гибкость производства и может использоваться для деталей с большими допусками. Металлорезиновый инструмент также обеспечивает равномерное гидростатическое давление, что полезно в областях фланца и в заготовках с различной толщиной, типичными для специальных заготовок, изготовленных из нескольких слоев UD.
Это внутреннее приложение гидростатического давления также является преимуществом, когда одна и та же деталь производится с разной толщиной, что исключает стоимость отдельных форм для каждой толщины. При разработке инструмента из резины и металла важно также учитывать следующие недостатки и проблемы:
- Металлическая сторона инструмента будет более гладкой по сравнению с резиной.
- Металло-резиновые инструменты будут иметь на порядок более высокий коэффициент теплового расширения (КТР), чем цельнометаллические инструменты.
- Из-за более низкой теплопроводности по сравнению с металлом охлаждение займет немного больше времени и приведет к большей задержке в реакции регулятора температуры.
- Повышенный износ и старение приводят к сокращению срока службы по сравнению с цельнометаллическими инструментами.
Формовка и разборка. Правильная конструкция формы обеспечивает достаточное давление, оптимальную драпировку, помогает предотвратить дефекты и способствует безопасному удалению деталей. Хотя существует множество проблем, связанных с формовкой и демонтажом, некоторые из наиболее важных включают:
- Давление. Во время термоформования низкое давление может привести к плохой консолидации, ухудшению механических свойств и нестандартным размерам деталей. Для подобранного инструмента металл-металл устраните концевые упоры, чтобы постоянное давление на ламинат не предотвращалось зазором, создаваемым концевыми упорами.
- Разрешение затягивания материала . Чтобы избежать расширения резиновой стороны формы во время прессования (так называемого бочонка), которое может блокировать движение материала во время прессования (втягивания), поместите резину на охватывающую сторону формовочного инструмента (см. Рис. 3). .
- Удаление части . Для L-образных деталей проектируйте форму с желаемым углом L, наклоненным к V, что уменьшит трение с инструментом и позволит легко снимать детали. Для коробчатых деталей используйте угол уклона 1-2 градуса с каждой стороны; для более глубоких деталей могут потребоваться более высокие углы.
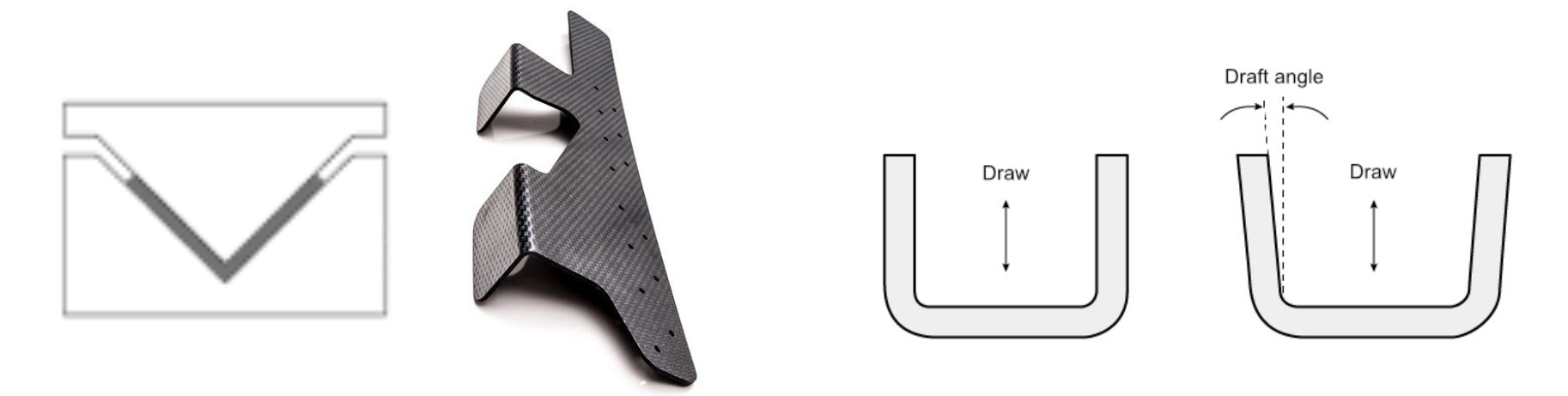
Деформация и подпружинивание
Деформация и подпружинивание - это искажения формы, вызванные анизотропными свойствами материала и неравномерным охлаждением смолы, которые возникают после формования детали и могут привести к выходу размеров детали за допустимые пределы, что может привести к проблемам со сборкой и списанию деталей. Коробление возникает, когда область высокого напряжения при формовании внутри детали пересекается с областью низкого напряжения при формовании. Этот дисбаланс напряжений устраняется за счет того, что область высокого напряжения искажает область низкого напряжения, что приводит к изгибу или скручиванию ламината.
Подпружинивание происходит в изогнутых панелях или в деталях с угловыми секциями, когда напряжение при формовании заставляет секции стены деформироваться внутрь под углом, меньшим, чем заданный угол. Это часто случается с композитами, армированными волокном, из-за их анизотропных свойств. Геометрия детали также имеет значение. Дифференциальная усадка между плоскостной (низкий КТР в направлении волокна) и по толщине (высокий КТР матрицы) может вызвать уменьшение угла на 1-3 градуса.
Устранение искажений формы может быть дорогостоящим и трудоемким. Для более быстрой разработки деталей настоятельно рекомендуется использовать инструменты моделирования и проектирования. При столкновении с короблением обратите внимание на следующие возможные причины и способы их устранения:
- Параметры процесса . Температура формы влияет на свойства по толщине, связанные с кристаллизацией и вязкоупругими эффектами, которые могут повлиять на коробление. Снижение температуры пресс-формы может уменьшить подпружинивание, но увеличить внутренние напряжения, которые могут привести к подпружиниванию после отпускания. Эту неопределенность следует тщательно изучить. Высокое давление и скорость формования также могут уменьшить подпружинивание и, возможно, способствовать возникновению противоположной проблемы - отскока - за счет ограничения промежуточного скольжения. Увеличение времени выдержки может обеспечить полное затвердевание матрицы и устранить остаточное тепло, что снижает усадку после снятия детали и, следовательно, пружинение.
- Дизайн пресс-формы . Компенсация подпружинения может быть произведена путем изменения углов стенок в форме. Кроме того, как уже упоминалось, металлические формы способствуют более равномерному охлаждению и могут помочь снизить риск коробления, особенно в толстых деталях.
- Макет . Симметричные укладки обычно используются для уменьшения коробления, но во время термоформования может произойти переориентация волокна, что приведет к асимметрии и короблению. Еще одно проявление асимметрии - миграция смолы при формировании радиуса (включая углы). Это вызывает перераспределение волокна и локальные изменения объемной доли волокна, что способствует анизотропии и короблению. Различные укладки и последовательности укладки ведут себя по-разному, поскольку волокна реагируют на напряжения, которые, в свою очередь, влияют на коробление. Инструменты моделирования и прогнозирования могут помочь справиться с этим сложным поведением материала.
Хотя процесс термоформования / штамповки включает в себя несколько параметров и сложное поведение материала, существуют основные принципы и действия, которые могут помочь в успешной разработке. По мере того, как все чаще используются термоформованные детали TPC, и особенно заготовки, изготовленные по индивидуальному заказу UD, новые проблемы решаются с помощью инновационных решений и улучшенных инструментов проектирования / моделирования.
Смола
- Covestro увеличивает инвестиции в термопластические композиты
- Переработка:армированные непрерывным волокном термопластические композиты с переработанным поликарбонато…
- Термопластические композиты в Oribi Composites:CW Trending, эпизод 4
- Термопластические композиты:структурный кронштейн бампера
- Toray Advanced Composites расширяет возможности термопластичных композитов
- ACMA выпускает программу конференции Thermoplastic Composites Conference 2020
- Двери из термопласта впервые для автомобильных композитов
- Термопластические композиты:живописный вид
- Предварительный просмотр CAMX 2018:расширенные композиты TenCate
- Сварка термопластичных композитов