Использование мобильных сенсоров для инновационной индукционной сварки термопластов
Группа Institut de Soudure (IS Groupe, Вильпент, Франция) - буквально «институт сварки» Франции - имеет более чем 100-летний опыт сварки металлов и в настоящее время занимает лидирующие позиции в области сварки термопластичных композитов. Как сообщается в CW "Сварка термопластичных композитов" за 2018 год, IS Groupe и ее бренд композитов Composite Integrity разработали процесс «динамической индукционной сварки», используемый для соединения стрингеров из углеродного волокна (CF) / полиэфиркетонкетона (PEKK) с однонаправленной (UD) лентой и обшивки фюзеляжа в демонстрационном проекте «Arches TP» с поставщиком Airbus Tier 1 STELIA Aerospace (Тулуза, Франция) , который был представлен на Парижском авиасалоне в 2017 году.
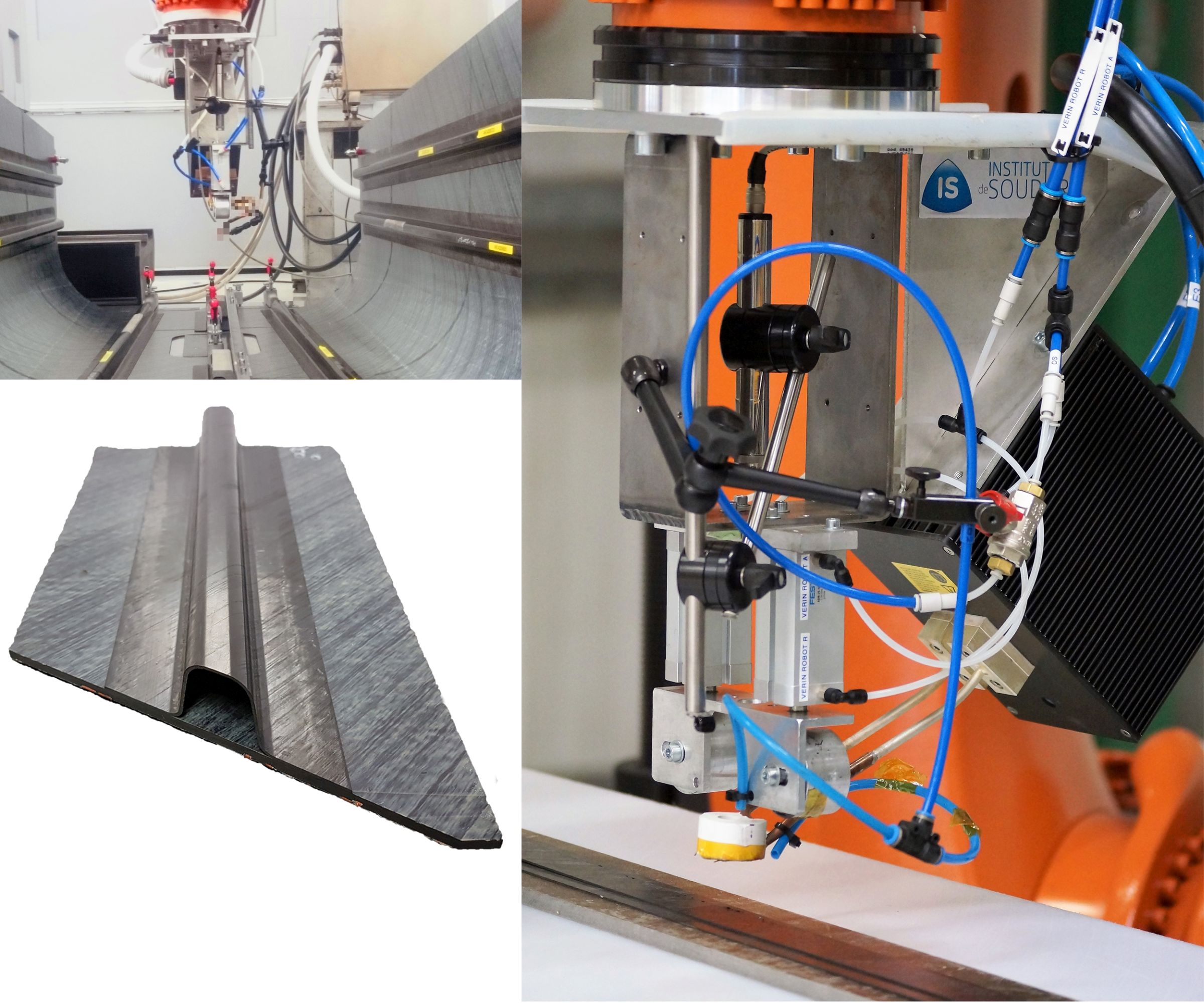
«Это было началом нашей разработки по индукционной сварке деталей авиационных конструкций», - объясняет Жером Рейналь, директор по аэронавтике и композитам IS Groupe. «Хотя процесс динамической индукционной сварки, который мы разработали, оказался успешным, у него были некоторые ограничения в отношении характеристик в радиусе приклеенного стрингера и общего нагрева панели, поскольку на границе раздела нет токоприемника».
Токоприемник - это материал, помещенный между двумя стыками сварного соединения из термопластичного композитного материала, который нагревается индукционной катушкой в сварочной головке. Токоприемник может быть электропроводным для резистивного нагрева или магнитным для гистерезисного нагрева, расплавляя матрицу на границе раздела сварного шва, которая одновременно сжимается для создания соединения плавлением с очень высокой прочностью. Как поясняется в статье Брюса Финка, Шридхара Ярлагадды и Джона У. (Джека) Гиллеспи «Конструкция резистивного токоприемника для равномерного нагрева во время индукционного соединения композитов», токоприемники, используемые в термопластичных композитах с индукционной сваркой, изначально были металлическими. экран или сетка, иногда пропитанная полимером.
IS Groupe полагала, что первоначальные проблемы, с которыми она столкнулась, могут быть решены путем дальнейшего развития. «Мы начали новый виток внутреннего размышления», - говорит Рейнал. Это включало обсуждения с поставщиком термопластических материалов (ТП) Arkema (Коломб, Франция), который перешел к партнерству в области развития. «Сейчас мы разработали и запатентовали новую технологию с Arkema под названием Innovative Solution for Welding (ISW)», - добавляет Рейнал.
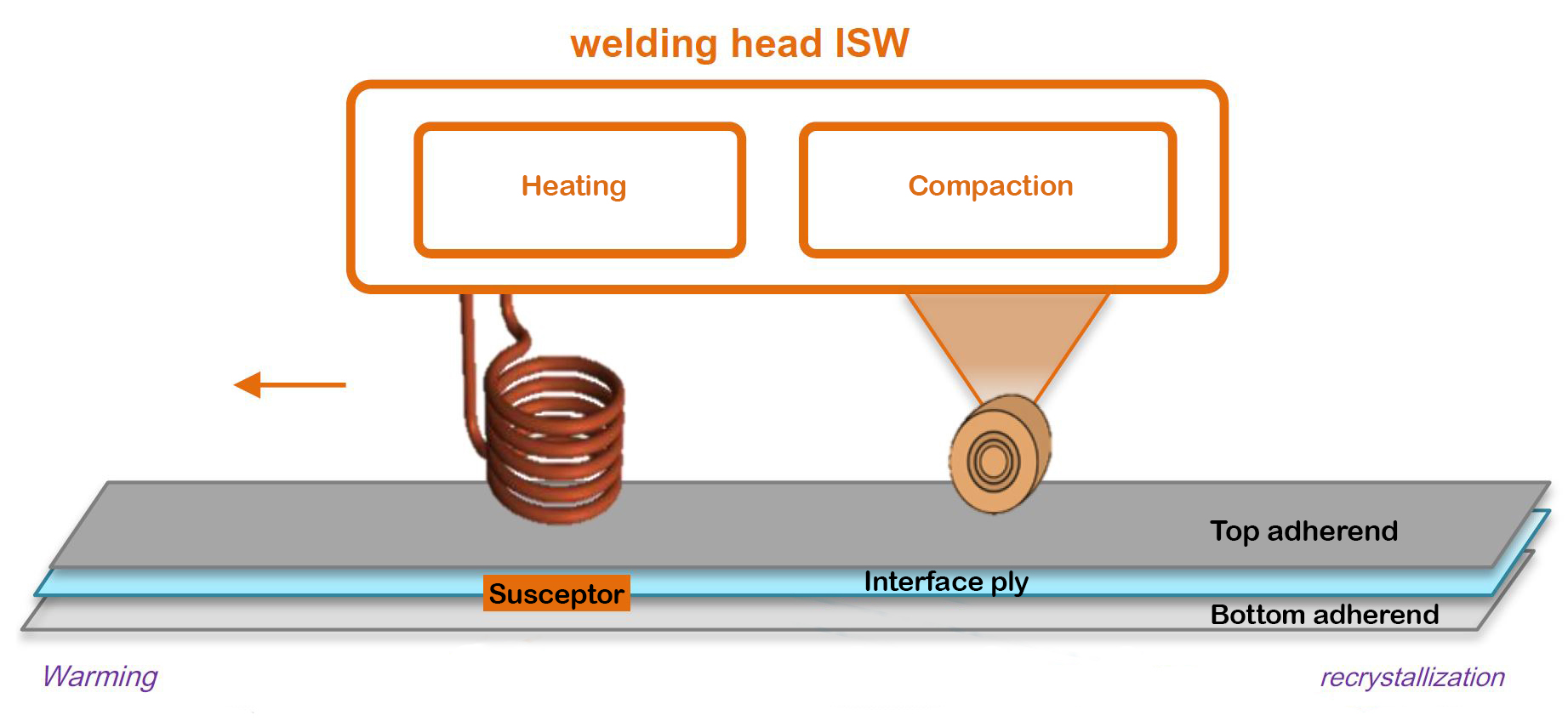
Основы ISW
«Основа ISW заключается в использовании токоприемника для нагрева поверхности стыка сварного шва, но это мобильный датчик, связанный со сварочной головкой», - поясняет Рейнал. «Токоприемник позволяет нам идеально расположить зону нагрева на сварном шве, но сварочная головка с токоприемником движется так, что на границе раздела ничего не остается, что нарушало бы свойства сварной конструкции». На ранних этапах индукционной сварки в сварном шве оставались токоприемники из металлической сетки, но это считалось нежелательным. Более современные методы позволили устранить чувствительные элементы, поскольку углеродное волокно в обычных слоистых материалах для авиакосмической промышленности является электропроводным. Это также позволило использовать материалы из углеродного волокна в качестве приемников.
Другая часть решения ISW заключается в использовании чистой TP-матрицы или слоя с малым объемом волокон на границе сварного шва для увеличения потока смолы. Температуру плавления и вязкость этого промежуточного слоя можно регулировать, а также можно использовать для обеспечения электропроводности или изоляции для предотвращения гальванической коррозии, например, между углеродным волокном и алюминием или сталью.
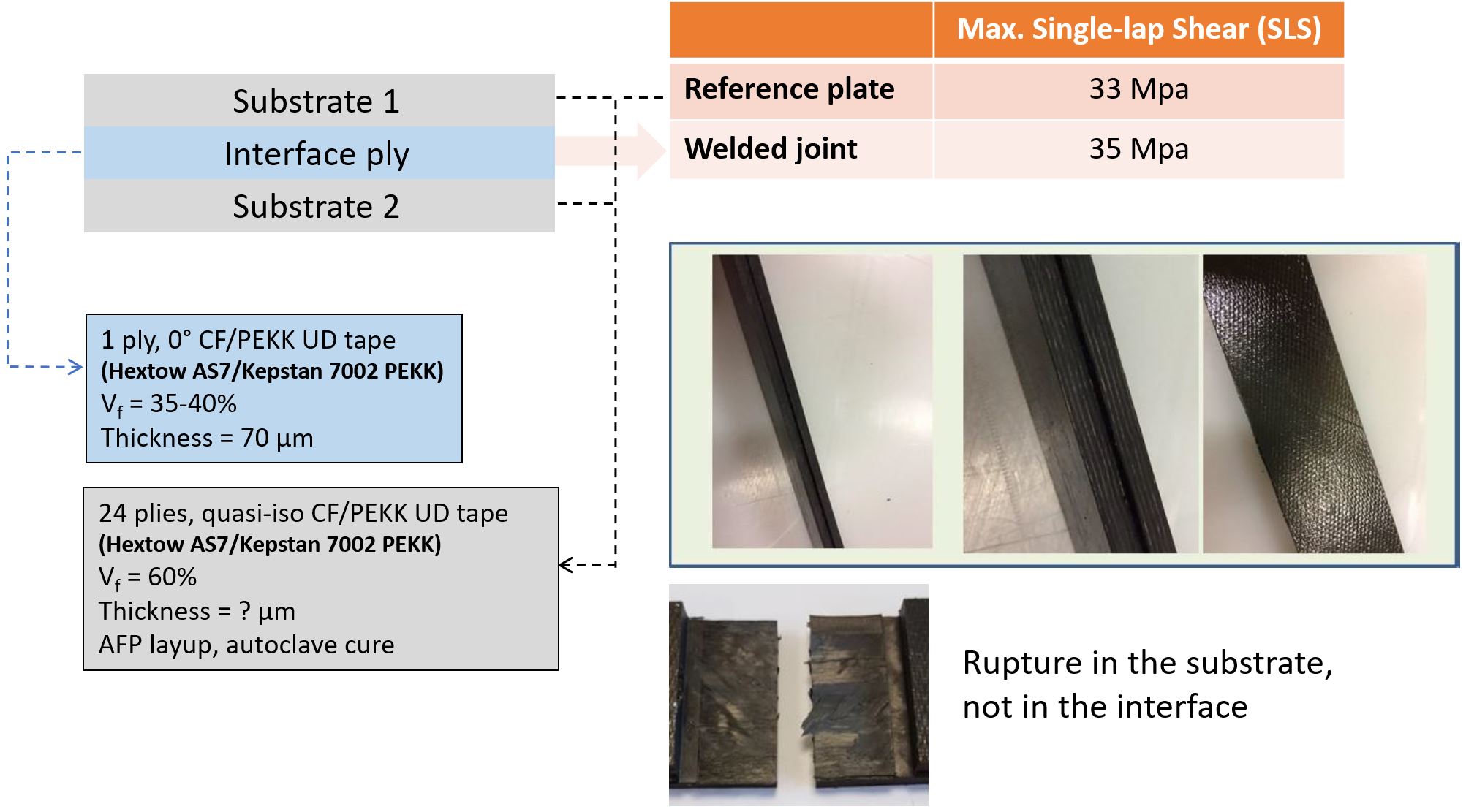
Результаты ISW
«В итоге мы получаем общий коэффициент 80-90%», - говорит Рейнал. Коэффициент соединения соответствует прочности сварного шва и используется с металлом, пластиками и композитами. «При испытании на сдвиг внахлест двух предварительно уплотненных пластин, сваренных вместе с использованием ISW, мы достигли 80-90% свойств несваренных, закрепленных в автоклаве эталонных пластин». В этих испытаниях использовалась лента UD, изготовленная из углеродного волокна Hextow AS7 (Hexcel, Стэмфорд, Коннектикут, США) и Arkema Kepstan 7002 PEKK.
Рейнал говорит, что ISW можно использовать для сварки любых видов матриц:PE, PA, PEKK, PEEK, а также термопластичных композитов, армированных углеродным, стеклянным или арамидным волокном. «Мы также показали, что без проблем сваривать компоненты с медной сеткой для защиты от ударов молнии (LSP), что является ключевым моментом при производстве авиационных конструкций», - добавляет он. ISW полностью автоматизирован:сварочная головка прикреплена к 6-осевой роботизированной руке.
Контроль температуры
Как объяснялось в статье Кирка / Ярлагадды / Гиллеспи выше, общая проблема с металлическими сетчатыми токоприемниками, подвергающимися воздействию магнитного поля, заключается в результирующем неоднородном распределении температуры в свариваемой детали. «Мы контролируем это с помощью токоприемника, который плавит только поверхность сварного шва», - объясняет Рейнал. «Мы измеряем температуру с помощью лазерного пирометра, который фактически измеряет край токоприемника сбоку. Итак, мы точно знаем температуру на границе раздела. Мы также используем охлаждение, чтобы помочь контролировать температуру и обеспечить достаточную кристаллизацию термопластического материала на всем протяжении сварного шва ».
Испытания по сварке стрингеров STELIA
Поставщик уровня 1 для Airbus, STELIA (Тулуза, Франция), является одним из первых заказчиков этой разработки для индукционной сварки. IS Groupe и Arkema выполнили специальное исследование для STELIA по привариванию 7-слойного стрингера CF / PEKK к 14-слойной обшивке с медной сеткой для защиты от ударов молнии (LSP). Конечная цель - сваривать конструкции длиной 30 метров с прямыми и двояковыпуклыми профилями. Компоненты были изготовлены с использованием ленты UD плотностью 194 г / м2, содержащей углеродное волокно Tenax HST45 (Тейджин, Осака, Япония) и Kepstan 7002 PEKK. STELIA указала гомогенный сварной шов с механическими характеристиками> 85% эталонного материала, закрепленного в автоклаве, и без ухудшения термических или механических свойств адгезивов. Он также запросил процесс, устойчивый к изменению толщины адгезива. Химические испытания и испытания свойств сварных компонентов были выполнены IS Groupe.
Компании IS Groupe и Arkema смогли удовлетворить требования STELIA, достигнув> 85% характеристик прочности на сдвиг внахлест (SLS) и прочности на межслойный сдвиг (ILSS) по сравнению с эталонными ламинатами, консолидированными в автоклаве. Не было распаковки или деградации ламинатов компонентов или сетки LSP. Единственная область, в которой они потерпели неудачу, - это скорость. STELIA запросила скорость сварки ≥ 1 метр / минуту. «В настоящее время наша скорость составляет 0,3 метра (10 дюймов) в минуту, - признает Рейнал, - но мы продолжаем работать над достижением этой целевой скорости». Есть ли ограничение по толщине свариваемой подложки? «Мы можем сваривать толщину, типичную для аэрокосмических конструкций, и сваривать компоненты толщиной 5 миллиметров с 5-миллиметровой подложкой».
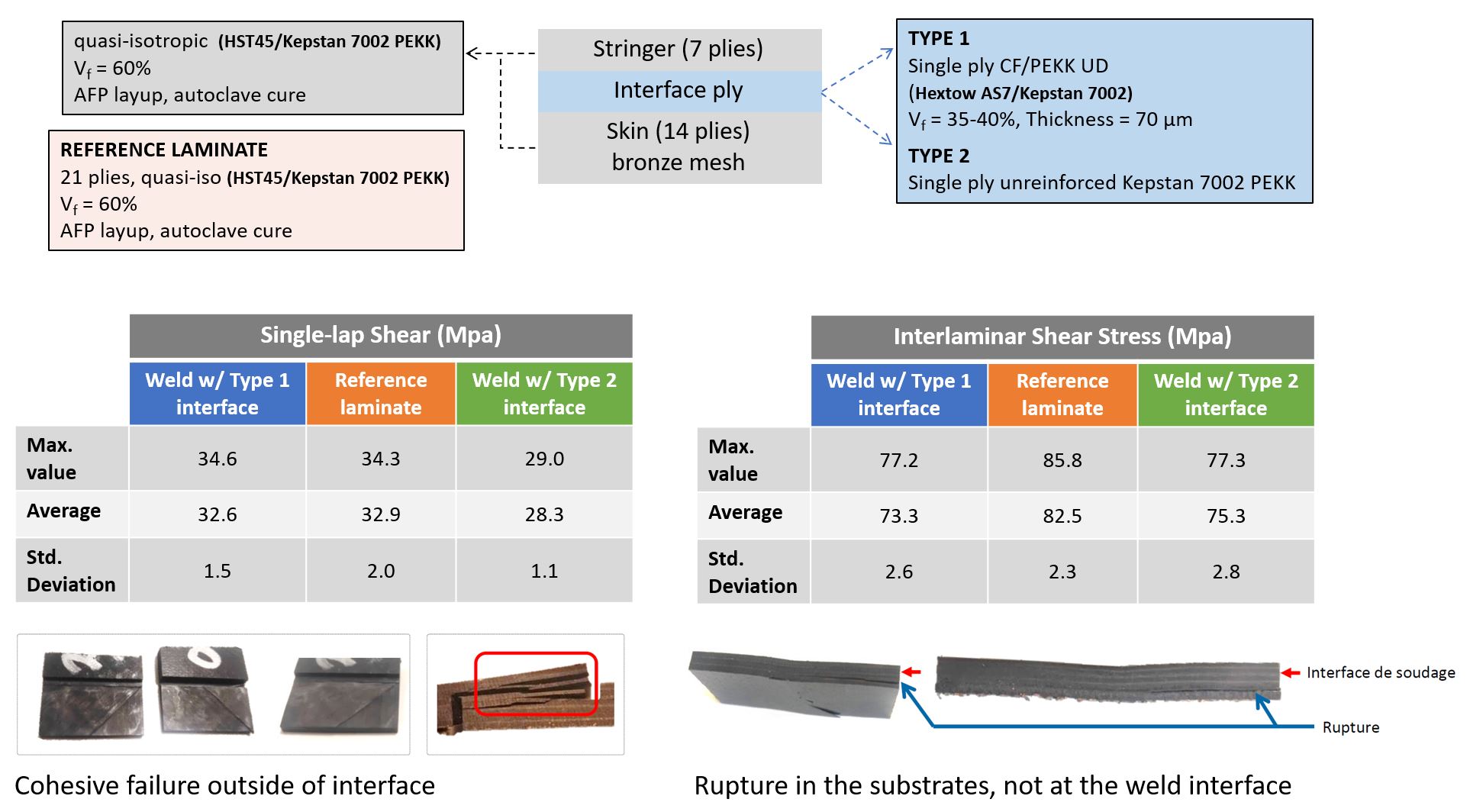
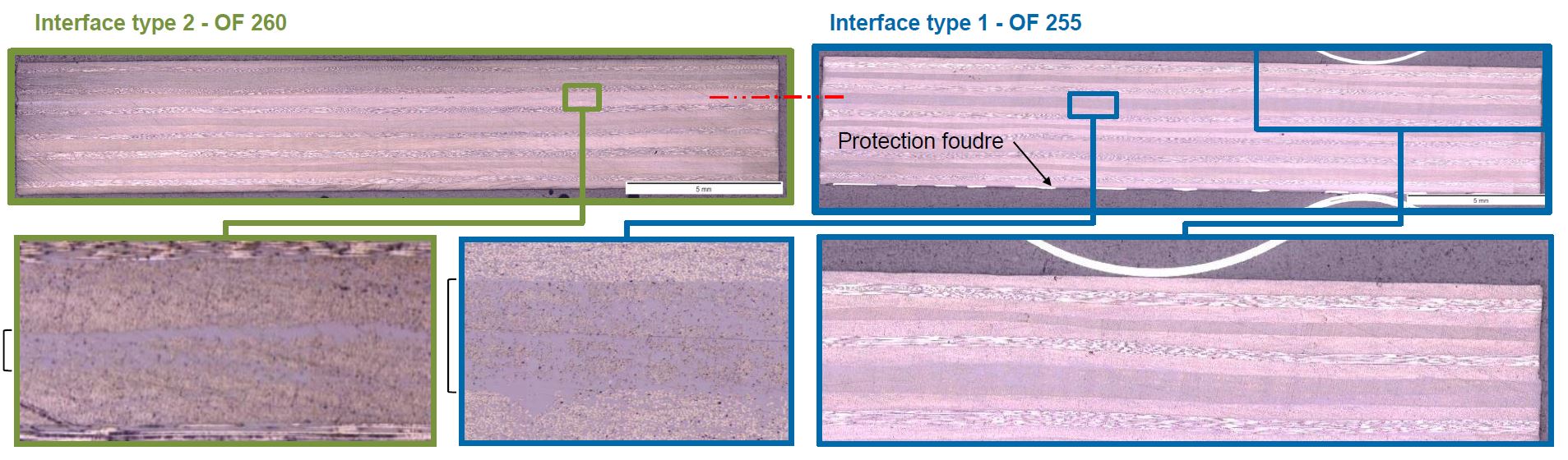
Партнерство с Arkema, возможности и проблемы
Почему стоит работать с Аркема? «Потому что существует взаимосвязь между технологией и материалами», - объясняет Рейнал. «Например, материалы на границе раздела и их объемная доля имеют значение. Мы специалисты по процессу, но нам нужно было тесно сотрудничать с партнером по материалам. Эта совместная разработка была необходима для полной оптимизации технологии сварки ».
IS Groupe и Arkema являются совладельцами технологии ISW и защищают эту технологию солидным портфелем патентов, который включает уже пять французских и международных патентных заявок. ISW можно использовать с любой термопластичной композитной матрицей, и IS Groupe демонстрирует эту технологию в рамках своих программ с компаниями в Европе и США, включая Latécoère . (Тулуза, Франция) и Collins Aerospace Aerostructures . (Чула-Виста, Калифорния, США).
По словам Рейнала, компания Arkema делает акцент на PEKK, отмечая ее стратегический альянс с Hexcel в 2018 году для разработки CF / термопластичных лент для будущих самолетов, уделяя особое внимание обеспечению более низких затрат и более высокой скорости производства для своих клиентов. В рамках этого партнерства во Франции создается совместная научно-исследовательская лаборатория.
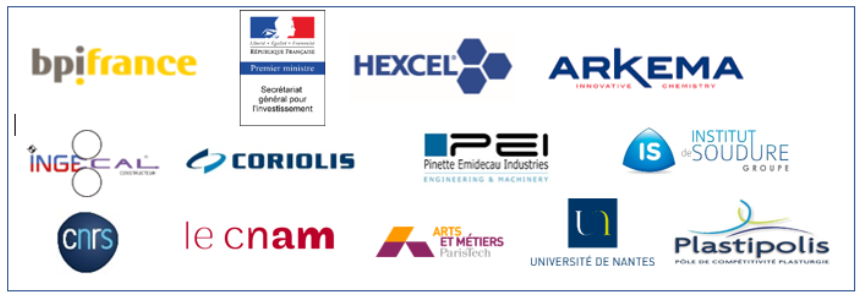
Полностью автоматизированные интегрированные композиты для создания адаптируемых структур за 13,5 миллионов евро, 48 месяцев. (HAICoPAS) является продолжением стратегического альянса Arkema-Hexcel. В это полностью французское сотрудничество входят IS Groupe, а также разработчик оборудования на заказ Инжекаль (Шасье), Coriolis Composites (Квевен), Pinette Emidecau Industries (Шалон-сюр-Сон) и консорциум университетских лабораторий. HAICoPAS оптимизирует разработку и производство материалов для производства композитных деталей для достижения конкурентоспособной стоимости при высокой скорости. Он также направлен на разработку более производительной технологии размещения / укладки композитных материалов и новой системы сборки готовых деталей путем сварки с онлайн-контролем качества.
Целевые области применения включают основные конструкции самолетов, конструктивные детали для автомобильной промышленности и трубопроводы для нефтегазовой промышленности. Преимущества вторичной переработки и устойчивости, обеспечиваемые термопластическими материалами, также важны для этих рынков и будут продемонстрированы и количественно оценены в HAICoPAS.
«Одно из преимуществ, которое мы можем предложить с ISW, - это сокращение электроэнергии более чем на 50% по сравнению с нашим динамическим процессом индукционной сварки с 2017 года », - отмечает Рейнал. «При использовании обычной индукции для нагрева поверхности требуется большая мощность. Но с токоприемником на границе раздела поверхность, которую вы нагреваете, намного меньше и требует гораздо меньше энергии ». Он отмечает, что это также помогает избежать разуплотнения в радиусе стрингеров. «Если вы нагреете слишком сильно, вы можете размягчить материал по радиусу и позволить волокнам двигаться здесь. Итак, нам нужно безупречно прогреть только зону контакта свариваемых подложек без нагрева радиуса. С ISW это не проблема ».
Однако по-прежнему существуют проблемы с температурой. «С плоскими формами терморегулирование несложно, но становится сложнее с увеличением сложности формы», - говорит Рейнал. «На 2020 год основная цель - продолжить разработку и добиться приварки стрингеров к обшивке в представительном масштабе. Мы также стремимся внедрить эту технологию в программы разработки новых самолетов ».
Подробнее см. Composite Integrity на выставке JEC World 2020, зал 5, стенд N89.
Смола
- 5 главных преимуществ индукционной сварки
- С# с использованием
- Введение в ультразвуковую сварку пластмасс
- Covestro увеличивает инвестиции в термопластические композиты
- Запущены суперконцентраты термопластов, армированных графеном
- Solvay увеличивает емкость термопластичного композитного материала
- Термопластические композиты в Oribi Composites:CW Trending, эпизод 4
- Сварка термопластичных композитов
- Чего не хватает муниципалитетам, если они не используют мобильные проверки
- Предотвращение проблем и дефектов сварки с помощью проверенных металлов