Проверка сварки LM PAEK для многофункционального демонстратора фюзеляжа
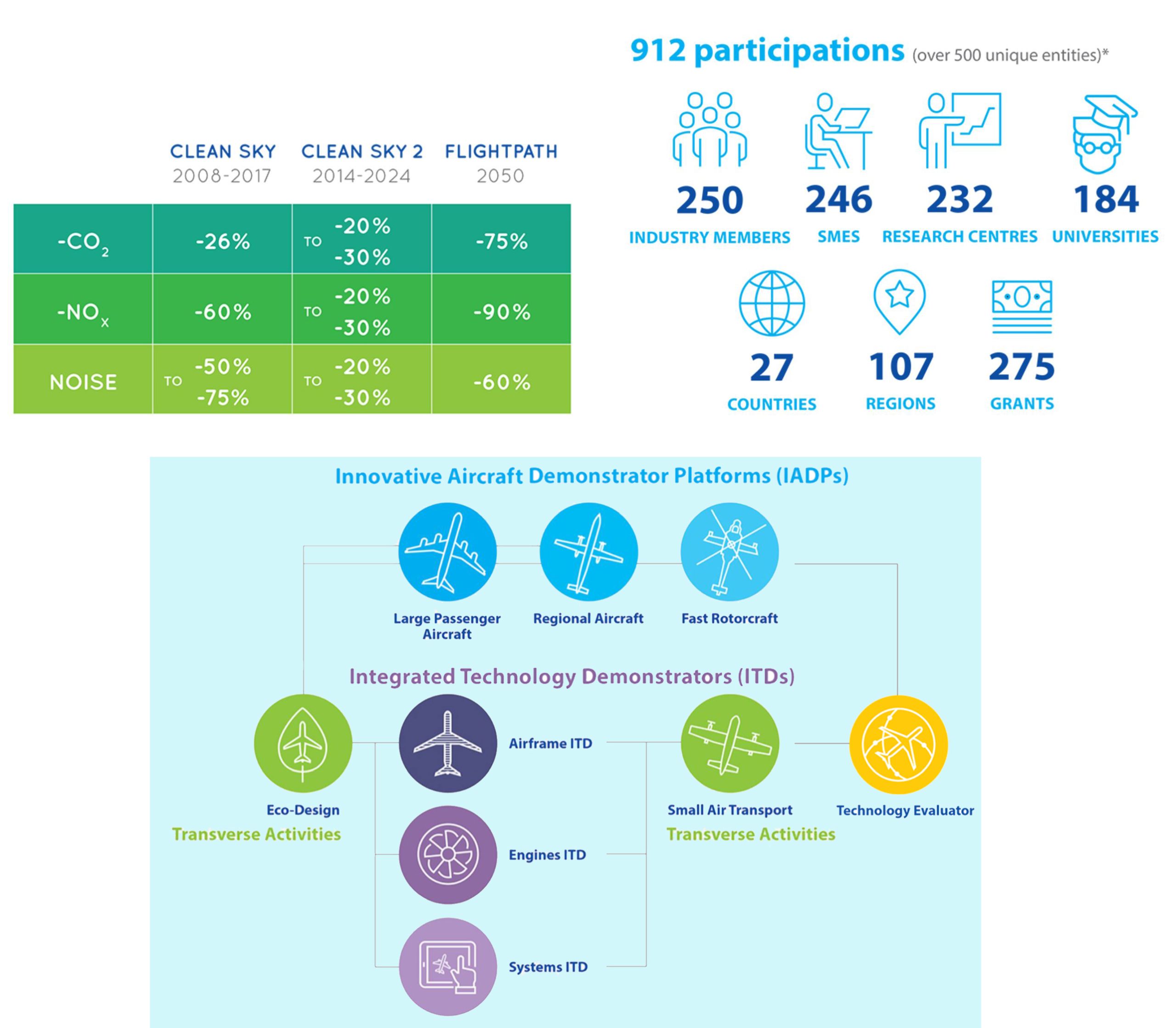
Этот тип аэронавигационных исследований начался с Рамочной программы Европейской комиссии (FP) по финансированию НИОКР, охватывающей FP2 (1987–1991) до FP7 (2007-2013). Эти программы внесли существенный вклад в доведение широкого спектра технологий до уровня технологической готовности (TRL) 6 и их внедрение в таких самолетах, как Airbus A350.
Одно из отличий Clean Sky 2 - организация вокруг крупных демонстрантов. MFFD - одна из трех полноразмерных секций фюзеляжа, производимых на платформе для демонстрации инновационных самолетов (IADP) для больших пассажирских самолетов (LPA) (см. Синий текст вверху синего квадрата на инфографике выше) . В LPA IAPD есть три платформы. MFFD находится в платформе 2 «Инновационная физическая интеграция кабины-система-структура», которая включает два других больших демонстратора.
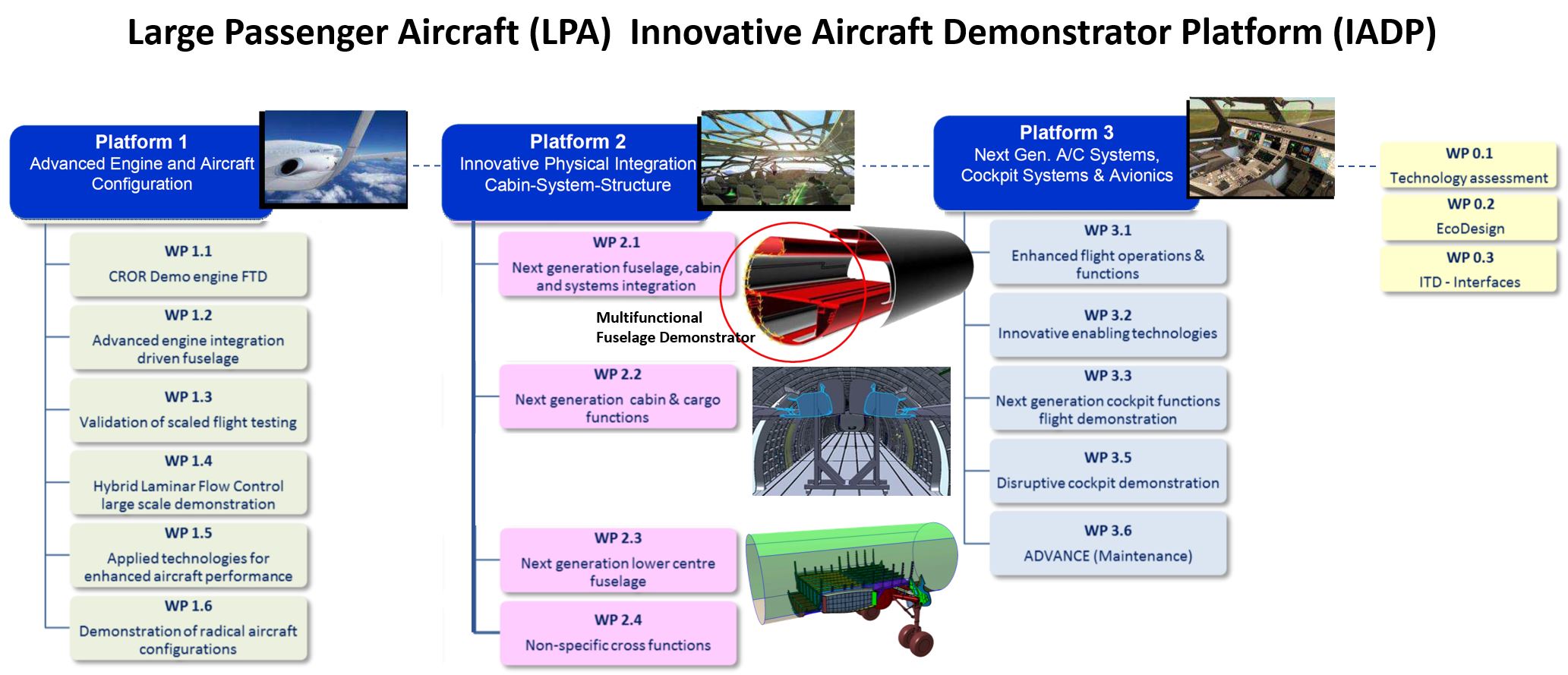
Чтобы понять, что это означает, я возвращаюсь к тому, что мне рассказали инженеры Airbus Airframe Research &Technology (R&T) из Хетафе, Испания, когда я исследовал многофункциональные композиты в 2015 году. По сути, они сказали:«Мы больше не хотим дублирования и отходы изготовления внешнего структурного цилиндра и внутреннего цилиндра; мы хотим интегрировать структурный планер с системами кабины ». Я изо всех сил пытался представить себе, что это означает, пока не увидел эскиз MFFD.
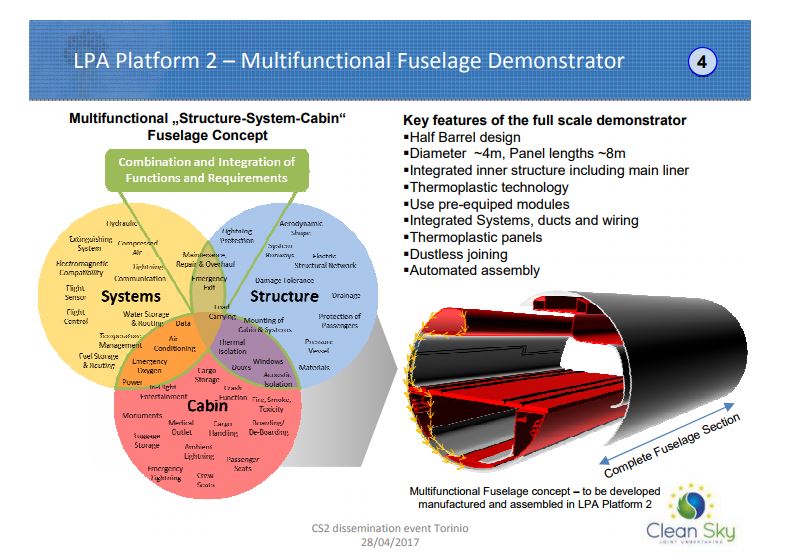
ИСТОЧНИК | Распространение Clean Sky 2 (CS2) и «Демонстрации термопластичных композитов - дорожная карта ЕС для будущих планеров».
«Модульность, интеграция и создание общих платформ являются ключевыми факторами», - говорит Ральф Херрманн (R&T Typical Fuselage Airframe R&T) в Airbus Operations GmbH (Бремен, Германия) и руководитель программы MFFD. Я цитирую здесь со страницы MFFD на веб-сайте Clean Sky 2:
Херрманн:«Мы давно знали, что выгоды от снижения веса и снижения текущих затрат при производстве самолетов - при использовании термопластичных композитов - может быть достигнуто только путем интеграции нескольких дисциплин. Это означает, что сосредоточение внимания только на структуре не может в полной мере использовать преимущества технологии композитов ».
По словам руководителя проекта Clean Sky 2 Паоло Тринкьери, универсальность термопластов необходимо сочетать с дизайнерским подходом:«Необходимо устранить искусственное разделение функций . на стадии предпроектных работ и с самого начала планировать высокие темпы производства, сборки и монтажа самолетов ».
Херрманн ранее был руководителем проекта FP7 MAAXIMUS (более доступная структура самолета за счет расширенного, интегрированного и зрелого численного расчета). В период с апреля 2008 года по сентябрь 2016 года MAAXIMUS включал 60 партнеров и был нацелен на демонстрацию быстрой разработки и правильной первоначальной проверки - путем одновременного создания виртуальных и физических средств поддержки - высокооптимизированного композитного фюзеляжа для сокращения времени сборки на 50%. большие секции фюзеляжа, сокращение текущих расходов на 10%, снижение веса конструкции на 10% и сокращение цикла разработки на 20%. Цели MFFD можно рассматривать как продолжение:
- Обеспечьте производительность 70–100 самолетов в месяц.
- Уменьшить вес фюзеляжа на 1000 кг.
- Сократите текущие расходы на 20%.
Один из ключевых факторов - беспыльное соединение (без отверстий, без креплений) с помощью сварных компонентов из термопластичного композита. Херрманн объясняет, что нынешний последовательный подход к производству самолетов, при котором конструкция фюзеляжа должна быть достаточно завершена, прежде чем можно будет установить системы, а также кабину и грузовые элементы, требует много времени и «чувствителен к сбоям». Вместо этого MFFD разрабатывает предварительно оборудованные, высокоинтегрированные структурные элементы и системные модули, которые можно установить довольно рано, задолго до окончательной сборки.
Переход на продольные швы и LM PAEK
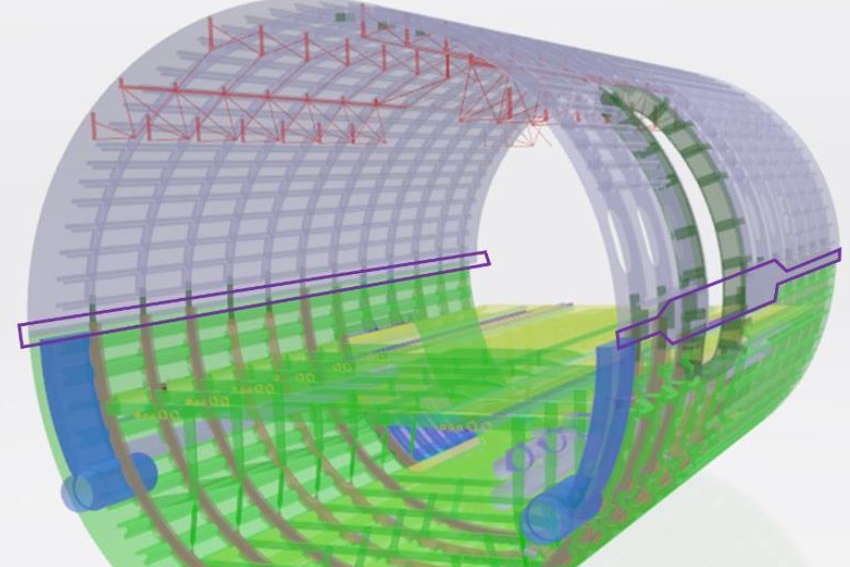
Деятельность по проекту MFFD началась в 2017 году. Каждый год проводится как минимум один конкурс заявок (CFP), в котором руководители проектов намечают темы, требующие дальнейшего развития. Как видно на изображении ниже, конструкция косого сочленения, показанная на CFP08 (апрель 2018 г.), была изменена на продольную к CFP09 (сентябрь 2018 г.).
«Косой стык вызвал проблемы, связанные с доступом и креплением перекрытий, которые, как мы понимали, будет трудно преодолеть в указанные сроки», - поясняет Херрманн. «Поэтому мы решили вернуться к традиционному дизайну, чтобы снизить риск. Наш главный интерес - показать, как интегрировать все системы и элементы кабины, которые могут быть установлены перед сборкой основных компонентов (MCA). Это также будет первый случай, когда этот термопластический композитный материал будет применяться в полномасштабных первичных конструкциях фюзеляжа для больших пассажирских самолетов ».
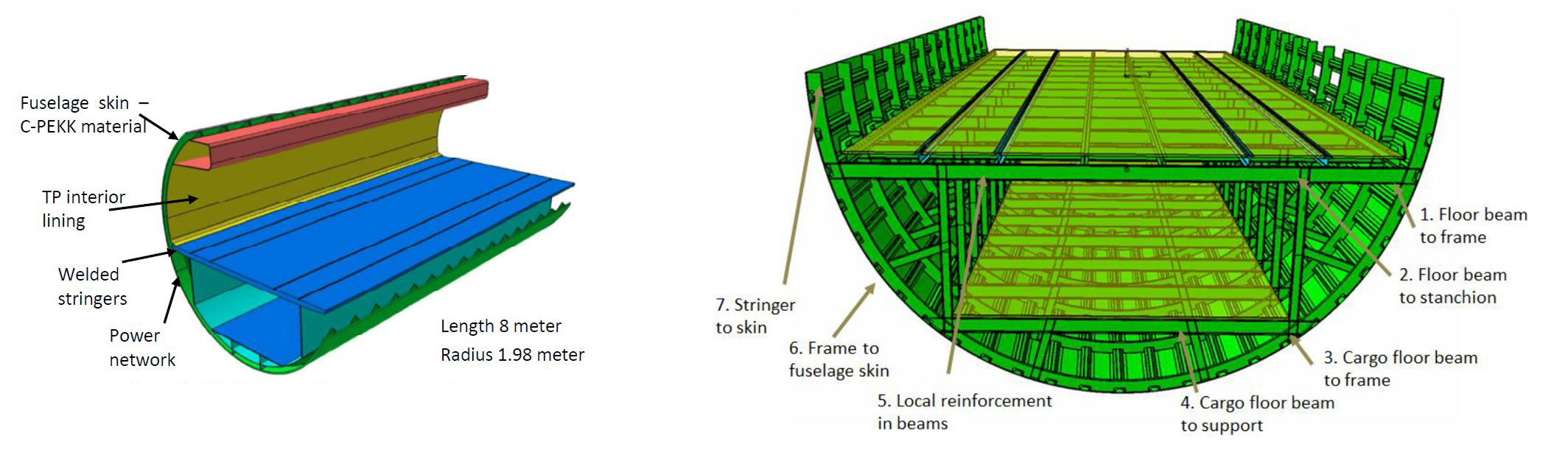
В 2018 году конструкция MFFD изменилась с косого шарнира на более традиционный продольный шов. ИСТОЧНИК | CFP08 стр. 87 (слева) и CFP09 стр. 133 (справа).
Еще одно изменение коснулось материала матрицы из термопластичного композита (ТПК). Темы MFFD в CFP08 и CFP09 относятся к углеродному волокну / PEKK (полиэфиркетонекетон), но в CFP10 (март 2019 г.) базовый материал был описан как углеродное волокно и PAEK (полиарилэфиркетон). PAEK - это общее семейство полимеров, в котором находятся PEEK, PEKK и LM PAEK.
Как описано в моем блоге о сравнении PEEK, PEKK и PAEK, поставщик материалов Cetex TenCate, ныне Toray Advanced Composites, производит все три полимера в виде ленты, армированной углеродным волокном, и утверждает, что свойства в основном те же. Однако Cetex TC1225 CF / LM PAEK лента плавится при 305 ° C а TC1320 CF / PEKK лента плавится при 340 ° C . И, по словам глобального технического директора Toray Advanced Composites Скотта Унгера, «LM PAEK имеет гораздо лучший поток ... и также может обрабатываться на более высоких скоростях, чем PEKK и PEEK». TC1225 также стоит меньше.
Нижняя часть фюзеляжа MFFD:проект STUNNING
STUNNING - это название проекта по разработке и производству полностью оборудованной нижней части MFFD. Проект нацелен на дальнейшее развитие:
- Автоматизированные сборочные процессы
- Технологии производства и сборки термопластов
- Комплексные технологии проектирования и разработки производства.
- Разработка передовых архитектур электрических систем.
Бас Вельдман, менеджер программы GKN Fokker (Хоогевен, Нидерланды) и руководитель проекта STUNNING, объясняет, что MFFD будет иметь длину 8 метров и ширину 4 метра с радиусом от 2 до 2,5 метров, что является реальным масштабом для узкофюзеляжного коридора. Самолет семейства А320. «Он похож на A321, который не совсем круглый, а примерно яйцевидный (немного выше ширины)», - добавляет он.
Нижняя часть фюзеляжа на 180 ° будет включать нижнюю оболочку фюзеляжа со сварными стрингерами и шпангоутами, конструкцию кабины и грузового пола, а также соответствующие основные внутренние и системные элементы. «Мы доставим большие предварительно укомплектованные модули для очень быстрой сборки по принципу« plug-and-play »», - говорит Велдман.
GKN Fokker является ведущим партнером STUNNING и имеет четыре подразделения, в том числе Aerostructures (Папендрехт, Нидерланды), Fokker ELMO (Хугерхайде, Нидерланды), GKN Fokker Engineering Romania (Бухарест) и GKN Fokker Technologies (Папендредхт, Нидерланды). GKN Fokker ELMO - поставщик жгутов проводов для самолетов и оборудования для электрических систем. «Он отвечает за системную архитектуру в STUNNING и сосредоточится на оптимизации электрической системы, - объясняет Велдман, - и сотрудничает с MISSION консорциума CFP08 в разработке инновационной системы шин питания».
«Diehl Aviation (Лаупхайм, Германия) отвечает за внутреннюю структуру, включая подсистемы и пол, боковые панели и способы их соединения, интерфейсы памятников и интеллектуальные многопортовые системы», - продолжает Вельдман. «NLR (Нидерландский аэрокосмический центр, Амстердам) отвечает за производство обшивки фюзеляжа и стрингеров, а TU Delft оказывает помощь в сборке, основываясь на своем опыте в области ультразвуковой сварки». (Подробнее об ультразвуковой сварке см. «Сварка термопластичных композитов».)
Программа испытаний сварки MECATESTERS
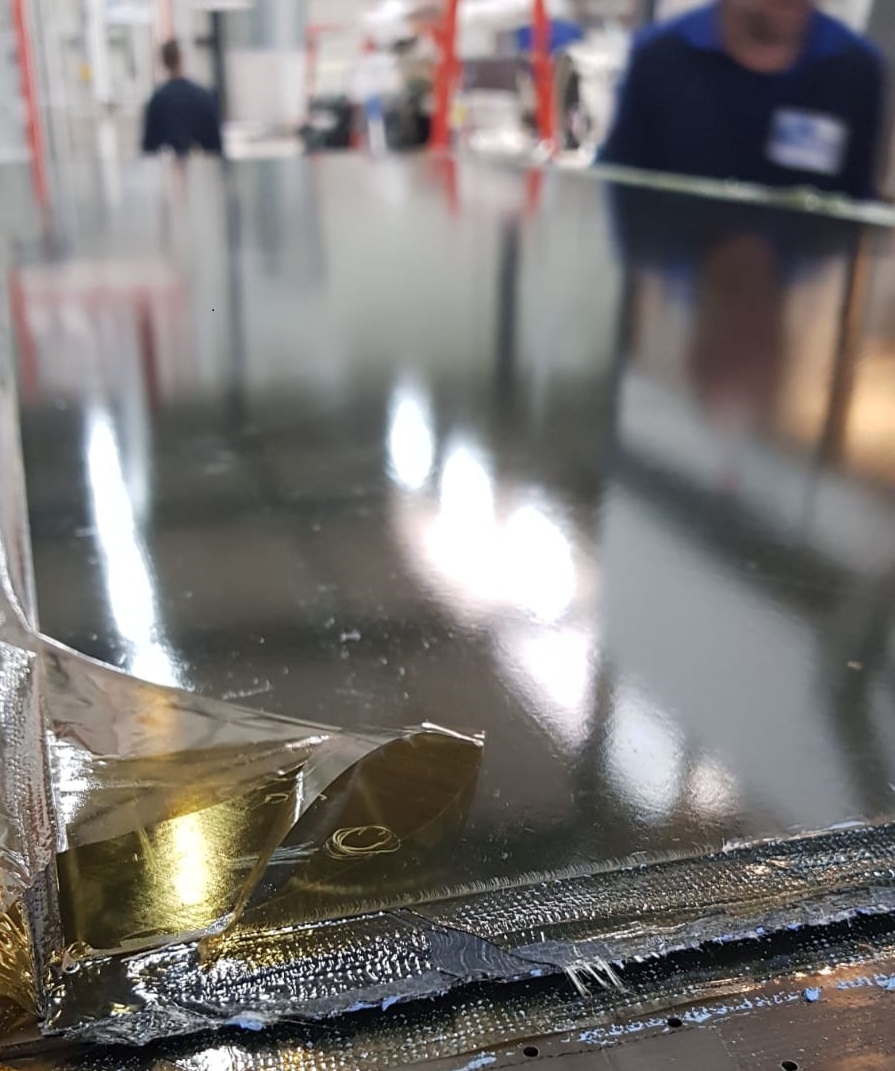
«STUNNING запустил семь тем CFP, и пять уже начали работу, в том числе MAYA, MISSION, EMOTION, TCTool и MECATESTERS», - говорит Велдман. Последний представляет собой большую программу испытаний сварки с KVE Composites (Гаага, Нидерланды) и Rescoll (Пессак, Франция), стартовавшая в апреле 2019 года и рассчитанная на 30 месяцев. Велдман объясняет, что, хотя KVE имеет долгую историю индукционной сварки термопластичных композитов как ткани, так и ленты UD, в деталях, свариваемых индукционной сваркой, летающих на самолетах до настоящего времени, использовалась ткань. «В STUNNING мы внедряем передовой опыт с UD-армированием и материалами LM PAEK, а также сравниваем индукционную сварку с кондуктивной сваркой при типичных эксплуатационных нагрузках и условиях окружающей среды». Хотя контактная сварка и ультразвуковая сварка включены в другие рабочие пакеты MFFD и CFP (см. « Соединение двух половин ”Ниже), индукционная сварка и кондукционная сварка - единственные два метода в MECATESTERS.
Лабордус из KVE объясняет, что для трех рабочих пакетов MECATESTERS (WP 1, 2 и 3) KVE будет изготавливать все тестовые ламинаты, используя отверждаемые в автоклаве углеродное волокно TC1225 UD / ленту LM PAEK (см. «Первый ламинат Toray LM-PAEK для Проект Clean Sky MECATESTERS »). KVE также подготовит образцы с индукционной сваркой для испытаний, GKN Fokker изготовит образцы с индукционной сваркой, а Rescoll выполнит все физические испытания. «Название Rescoll происходит от исследования и коллажа, что по-французски означает связь, - говорит Лабордус. «Они известны своими исследованиями по всем типам склеивания и предлагают хорошо оборудованную лабораторию для испытаний полимеров и композитов, включая механические, экологические, воспламеняющиеся и всевозможные испытания для квалификации в аэрокосмической, автомобильной, железнодорожной и других отраслях».
Параметры процесса и тесты
«Фактически мы начинаем с WP 2, чтобы установить параметры процесса, такие как верхние и нижние границы для температуры и давления индукционной сварки», - говорит Лабордус. «Например, у нас есть номинальный давление, которое мы обычно используем, но мы будем снижать давление до тех пор, пока не начнем видеть дефекты, такие как пустоты, а затем оценим эти свойства сварного шва, чтобы установить нижнюю границу давления ». Тестирование также позволит оценить скорость сварки, которая влияет на скорость охлаждения и кристалличность сварного шва, а также, возможно, на механические свойства. Те же параметры будут исследованы в Fokker для кондуктивной сварки.
Для оценки программа MECATESTERS выполнит несколько тестов, в том числе:
- Тест Лапшира согласно ASTM D5868–01
- Испытание на отрыв и сдвиг купонов с L-образным профилем.
- GIC и GIIC согласно ISO 15024 и ISO 15114 соответственно.
(это испытание на ударную вязкость будет фактически завершено в WP 1)
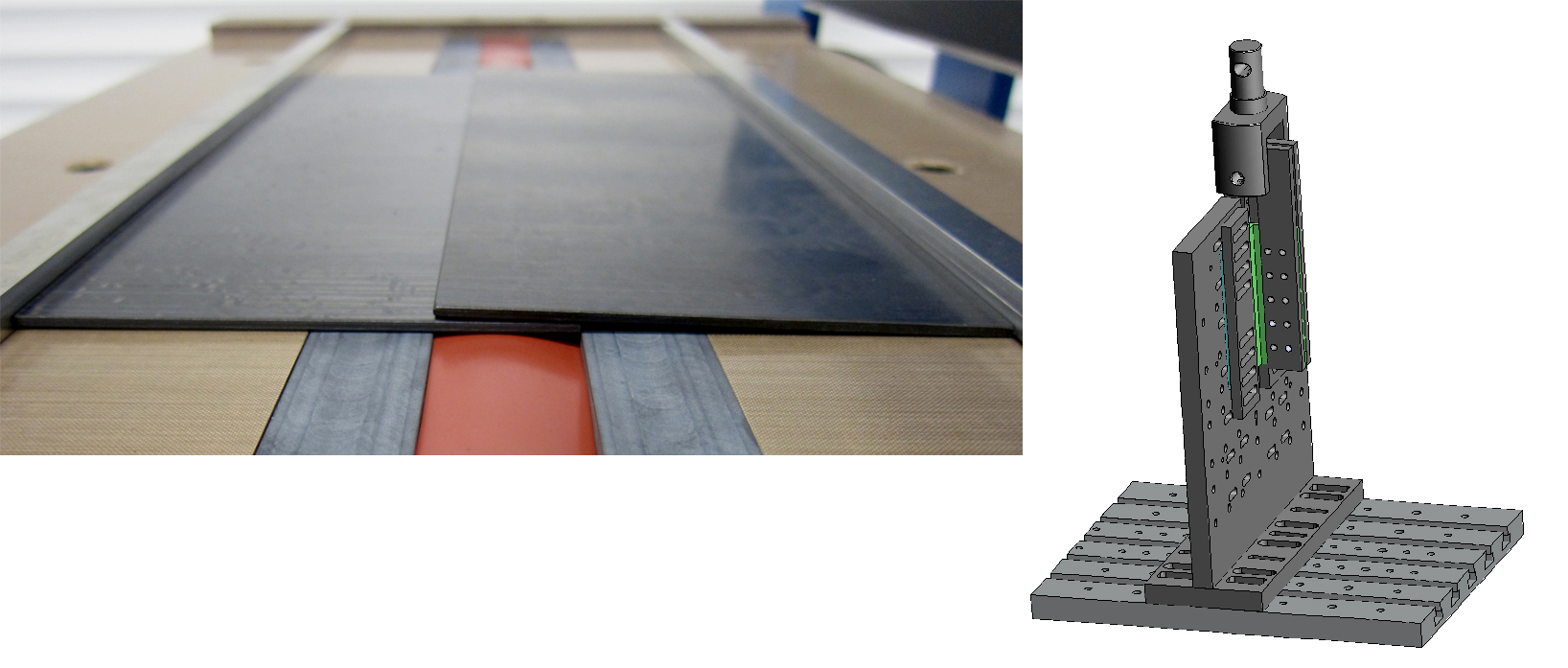
Купон на сдвиг внахлест из многослойной ленты UD, готовый к индукционной сварке (слева), и испытательное приспособление для комбинированных испытаний на сдвиг и отслаивание сварного образца L-профиля с использованием инструмента, разработанного Rescoll (справа). ИСТОЧНИК | KVE Composites, Rescoll.
«Метод испытания на отрыв основан на внутреннем стандарте, разработанном GKN Fokker, - поясняет инженер Rescoll Томас Салат. «Испытание на отрыв сварных профилей проводится перпендикулярно к обшивке при нагрузке на отслаивание, - отмечает Лабордус, -« и параллельно к обшивке при нагрузке на сдвиг ». Отслаивание и сдвиг - две крайности, но мы также протестируем их новые комбинации, которые отражают практические условия нагрузки в процессе эксплуатации ». Это испытание будет выполнено для двух различных толщин ламината, полученных из конструкции фюзеляжа MFFD - 2,2 и 2,8 миллиметра - при комнатной температуре (RT), низкой температуре (-55 ° C) и высокой температуре (80 ° C) с использованием статической нагрузки.
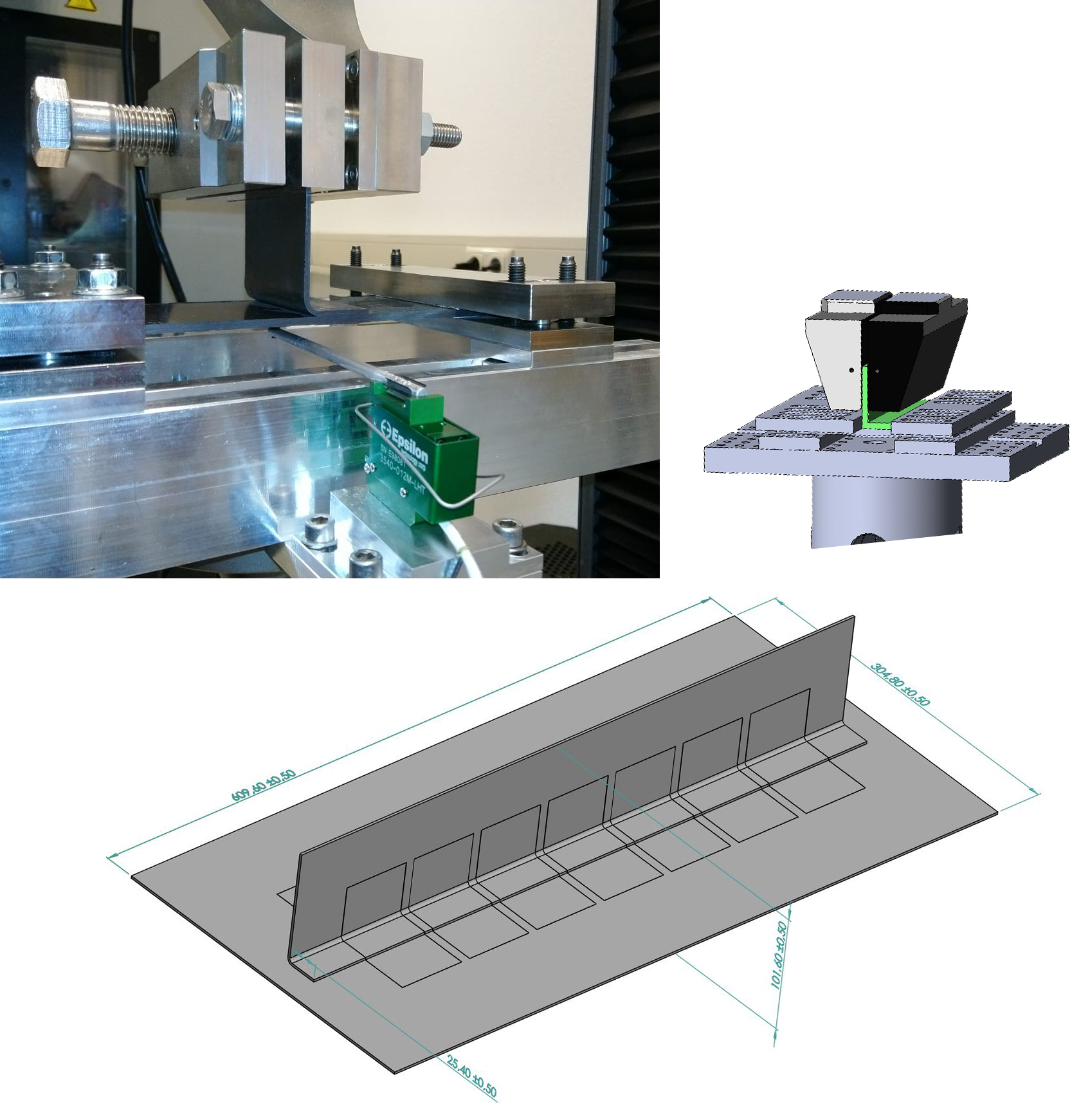
Испытания на отрыв купонов L-профиля в KVE Composites (вверху слева). В MECATESTERS для этого типа тестирования будет использоваться захват и испытательная установка, разработанные Rescoll для устранения отклонения кожи (вверху справа). Тестовые купоны будут вырезаны из сварных панелей (внизу). ИСТОЧНИК | Rescoll, KVE Composites.
Подготовка поверхности, старение и усталость
WP 1 начнется с испытаний на ударную вязкость. «Для испытаний на растрескивание (GIC и GIIC) мы инициируем трещину в композите и измеряем, как эта трещина ведет себя при нагрузке», - поясняет Салат. «Один из них - статический тест, который увеличивает нагрузку до отказа. Мы также проведем динамический тест, в котором мы повторяем статическую нагрузку один миллион раз, что займет от одной до двух недель. Посмотрим, выдержит ли композитный сварной шов такую усталость. Этот режим II представляет собой новый вид циклических испытаний. Мы разрабатываем метод, взятый из технической статьи, опубликованной Европейским университетом, и сейчас дорабатываем параметры ».
Также в WP 1 параметры сварки, установленные в WP 2, будут использоваться для изучения эффектов подготовки поверхности, а также старения и усталости. «Мы рассмотрим поверхностные загрязнения и то, как они могут повлиять на сварной шов», - говорит Лабордус. «Мы также исследуем три различных типа разделительных агентов, обычно используемых в прессах и автоклаве; специальные виды подготовки поверхности, включая шлифовку, абразивную и плазменную обработку; а также использование дополнительной пленки смолы на свариваемой поверхности. Кроме того, мы изучим влияние ориентации волокна, например, плюс / минус 45 градусов на границе сварного шва ».
По словам Салата, Rescoll также будет использовать камеру кондиционирования с температурой 70 ° C и влажностью 90% для имитации старения в процессе эксплуатации. «Затем мы проведем стандартные испытания, чтобы увидеть, влияет ли это на характеристики сварки». Лабордус добавляет, что ограниченное количество образцов будет отобрано при температуре 100 ° C и 120 ° C, «чтобы подтвердить заявление о том, что термопластичные композиты не выдерживают резкого падения температуры выше 80 ° C».
В дополнение к испытаниям на динамическое растрескивание / GIIC, усталостные испытания будут проводиться в режимах сдвига и отрыва за один проход. «Мы начнем с 80 процентов статической нагрузки отказа и перейдем к 50 или 75 процентам от усталости за миллион циклов», - говорит Лабордус. «Мы проведем и другие тесты, но их все еще обсуждаем», - добавляет Салат.
Приварка коротких составных кронштейнов
Хотя детали рабочего документа WP 3 все еще дорабатываются, он направлен на исследование сварных швов прессованных скоб, изготовленных из коротковолокнистого материала, к обшивке из ламината UD. «Мы снова проверим параметры процесса и охарактеризуем механические свойства сварного шва, - говорит Лабордус, - но мы все еще работаем над определением геометрии для тестирования».
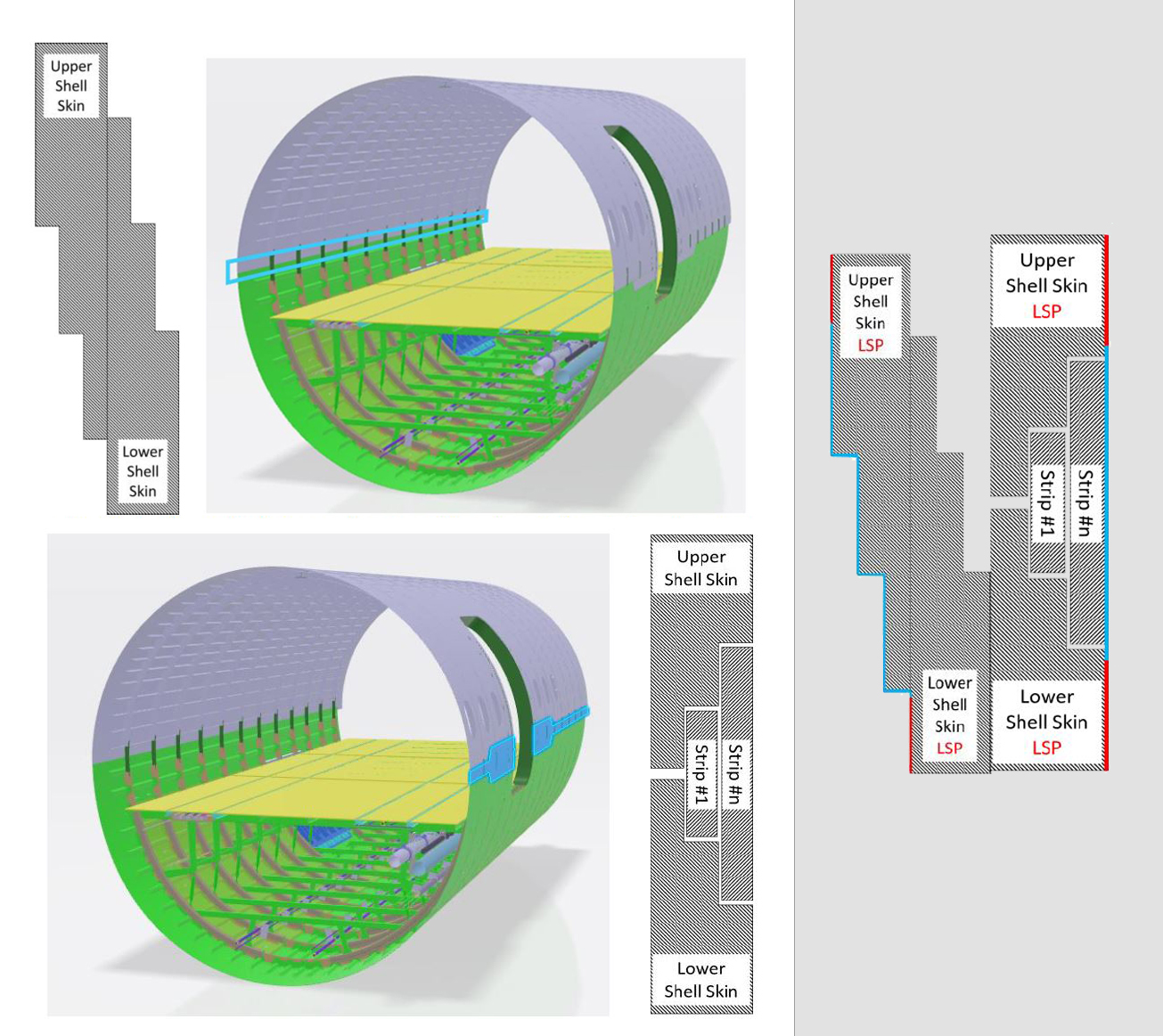
Стрингеры и зажимы приварены к фюзеляжу из термопласта. ИСТОЧНИК:Clean Sky 2 11 th Конкурс предложений JTI-CS2-2020-CfP11-LPA-02-35, «Инновационные средства защиты от отслаивания для длинных сварных швов из термопласта», рис. 2, стр. 94.
Сварные зажимы и скобы
Как указано в теме CFP10 JTI-CS2-2019-CfP10-LPA-02-31, все зажимы рамы и системные кронштейны для нижней части фюзеляжа MFFD будут изготавливаться путем литья под давлением из коротковолокнистых смесей, полученных путем повторного использования заводских отходов от руководитель темы GKN Fokker Производство ламинатов TPC с непрерывным волокном. CF / PAEK - это базовый материал, а сварка - базовый метод соединения, хотя конкретный метод сварки не предписан.
Согласно тексту CFP10, нижняя часть фюзеляжа MFFD будет иметь 13 шпангоутов и около 36 стрингеров, для чего потребуется примерно 500 зажимов рамы (обратите внимание, что это основные конструкции, требующие структурных испытаний, и это общее количество включает зажимы, используемые для испытаний) и примерно 270 кронштейнов системы (которые являются второстепенные конструкции) разделены по типам, показанным ниже:20 системных кронштейнов (1), 120 системных кронштейнов (2), 50 системных кронштейнов (3) и 80 системных кронштейнов (4).
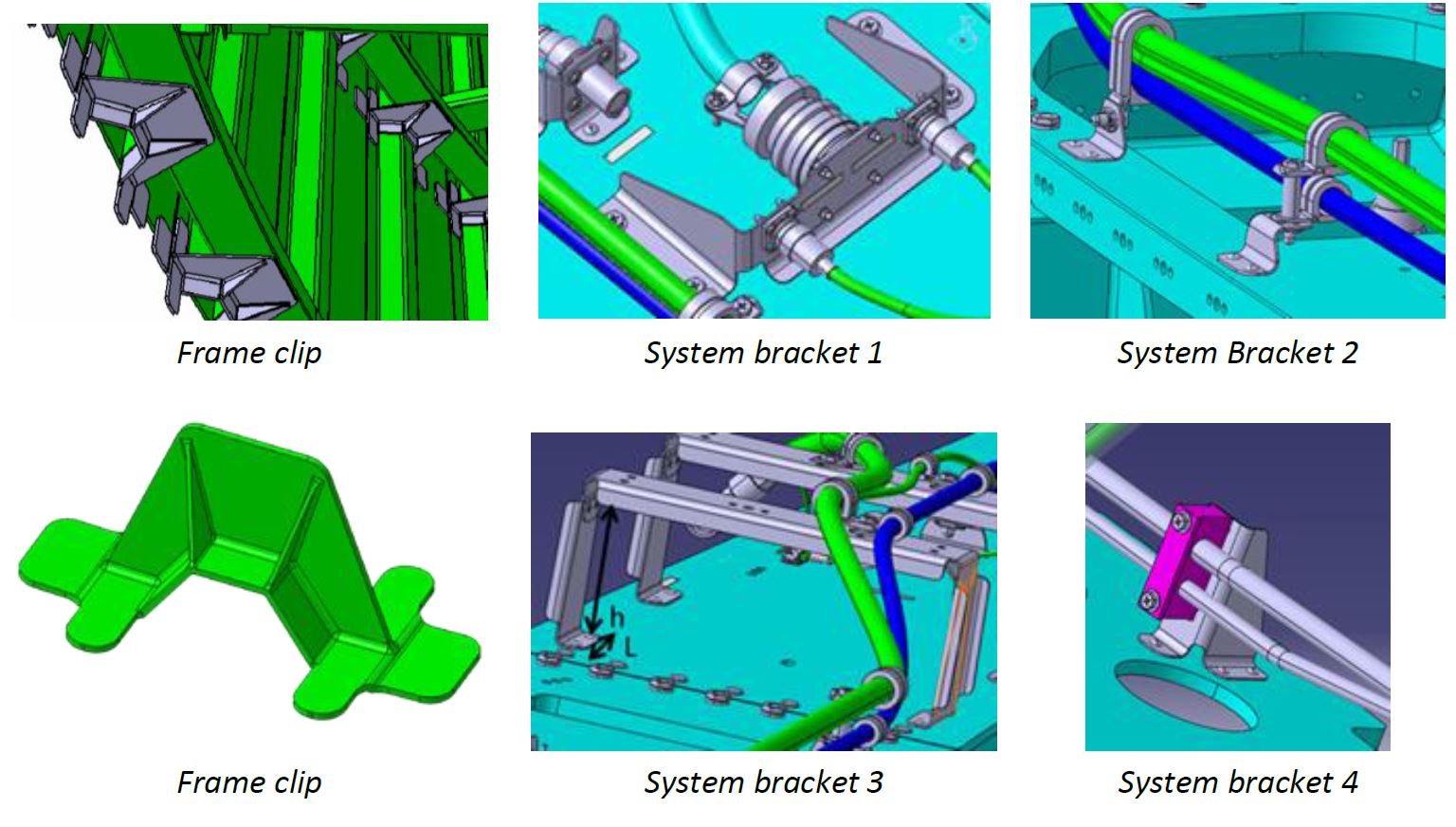
Примеры деталей, которые будут доставлены в теме «Чистое небо 2» JTI-CS2-2019-CfP10-LPA-02-31, рисунок 2. ИСТОЧНИК | Чистое небо 2 CFP10, стр. 146.
Также в CFP10 представлена тема MFFD для верхней части фюзеляжа JTI-CS2-2019-CfP10-LPA-02-30, «Разработка инновационных систем сварки для структурных стыков композитов на основе термопластической матрицы» под руководством Aernnova Composites Illescas (Ильескас, Испания). Планируется, что он начнется после 1 квартала 2020 г., и его объем заключается в разработке сварочной системы для достижения структурной связи между элементами армирования (косынки, клинья, фурнитура) и структурными каркасами для получения высоко интегрированной конструкции дверного окружения (DSS). Я надеюсь дать более подробную информацию о верхней части фюзеляжа MFFD в будущем блоге. На данный момент достаточно понять, почему рабочий пакет MECATESTERS 3 важен и сколько будет достигнуто после завершения MECATESTERS, STUNNING и MFFD.
Соединение двух половинок
После завершения нижняя половина MFFD будет передана в Институт технологий производства и передовых материалов им. Фраунгофера IFAM (Штаде, Германия), где будет объединена с верхней половиной, поясняет Вельдман. «Мы намерены поставить половину фюзеляжа к концу 2021 года», - добавляет он.
Как отмечалось выше, Ральф Херрманн в Airbus является руководителем проекта MMFD; Таким образом, Airbus объединяет работу Fraunhofer IFAM и консорциума CFP07 MultiFAL (Многофункциональная система автоматизации для сборочного конвейера фюзеляжа), который отвечает за соединение двух половин фюзеляжа, работая вместе с командой STUNNING и верхней части фюзеляжа. - разработать решения для множества проблем.
Некоторые из них раскрываются в двух темах 11-го -го Конкурс предложений (ноябрь 2019 г.), оба под руководством Airbus начнутся после четвертого квартала 2020 г. и озаглавлены «Инструменты, оборудование и вспомогательное оборудование для закрытия продольного стыка ствола:»
- JTI-CS2-2020-CfP11-LPA-02-33, «:интеграция прикладываемого ремня и непрерывность защиты от ударов молнии»
- JTI-CS2-2020-CfP11-LPA-02-34, «:Соединение внахлест и интеграция рамной муфты».
Автор Пит-Кристоф Велькен, менеджер по темам в Airbus Bremen и руководитель рабочего пакета MFFD. Основные проблемы в этих темах включают:
JTI-CS2-2020-CfP11-LPA-02-33
- Стыковое соединение ремешка (Рис. 3 ниже):
- Левая сторона демонстратора (в направлении полета) включает дверное ограждение пассажира. Из-за разницы в толщине обшивки в этой области требуется ступенчатая интеграция затыльника, соединяющая верхнюю и нижнюю обшивки.
- Учитывая сложность соединения, кондуктивная сварка использование нагретой прижимной пластины является предпочтительной технологией соединения.
- Обеспечение непрерывности защиты от ударов молнии (Рис. 4 ниже):
- Электрическая непрерывность металлической молниезащиты (LSP) должна быть обеспечена через оба продольных шва на внешней стороне фюзеляжа.
- Предполагается, что для этой цели можно использовать инструментальную головку, предусмотренную для крепления стыковой лямки.
JTI-CS2-2020-CfP11-LPA-02-34
- Соединение внахлест (Рис. 2 ниже):
- 8-метровый стык внахлест на правой стороне демонстрантов (в направлении полета) соединяет верхнюю и нижнюю обшивки фюзеляжа. В продольном направлении толщина пленки менее 3 мм в зоне сварки постоянна. В окружном направлении оболочки имеют ступенчатую геометрию для улучшения структурных характеристик.
- Ультразвуковая сварка является предпочтительным соединением для достижения высокой производительности.
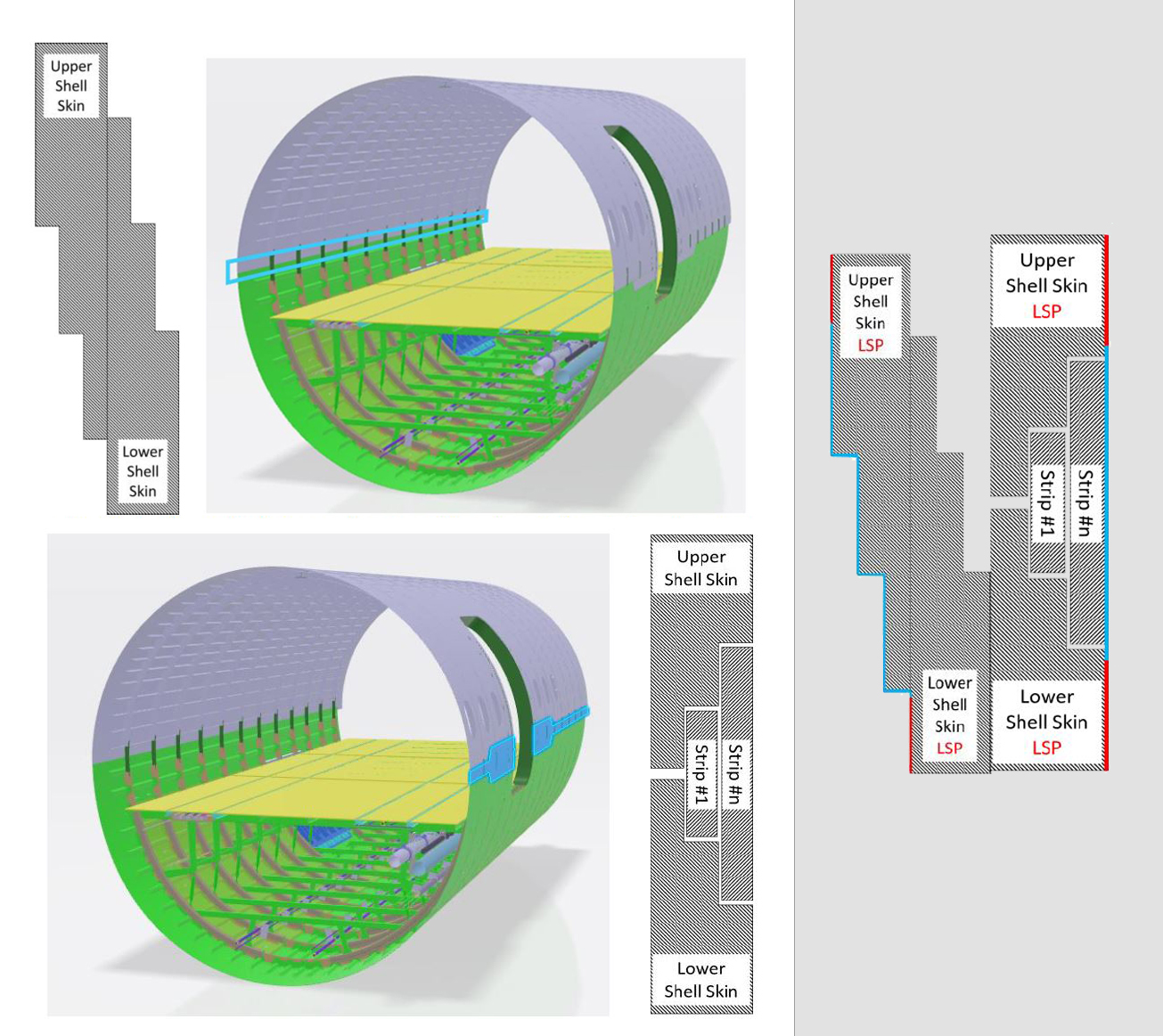
Рис. 2 (Вверху слева) :Соединение внахлест:При проектировании соединения внахлест был использован поэтапный подход. Обратите внимание, что нижняя оболочка лежит на внутренней стороне фюзеляжа. Рис. 3 (Внизу слева) : Интеграция стыковой ленты:ряд вышележащих лент требует интеграции через ступенчатое соединение. Обратите внимание, что стыковой ремень находится на внешней стороне фюзеляжа. Рис. 4 (справа) :Электрическая целостность металлических LSP должна быть достигнута через продольные стыки на внешней стороне фюзеляжа из углепластика. Красный указывает на предварительно оборудованный LSP, синий указывает на то, что LSP должен применяться как часть этой темы. ИСТОЧНИК | Чистое небо 2 11 th Объявление о приеме заявок JTI-CS2-2020-CfP11-LPA-02-33 и -34, «Интеграция стыкового ремня и непрерывность защиты от ударов молнии», стр. 78 и 86.
JTI-CS2-2020-CfP11-LPA-02-34
- Интеграция с соединением кадров (Рис. 5):
- Соединение внахлест:муфты рамы под соединением внахлест должны структурно соединять верхнюю и нижнюю рамы оболочки.
- Прикладная лямка:муфты рамы под прикладной лентой должны структурно скреплять верхнюю и нижнюю рамы оболочки, а также соединяться с кожей.
- Контактная сварка является предпочтительной технологией для решения этой технической задачи.
Интеграция рамной муфты. Обратите внимание, что в рамках демонстрации технологии рамные муфты различаются по сторонам. ИСТОЧНИК | Чистое небо 2 11 th Конкурс предложений JTI-CS2-2020-CfP11-LPA-02-34, «Инструменты, оборудование и вспомогательные средства для закрытия продольного шарнира ствола:соединение внахлест и интеграция рамы», рис. 5, стр. 86.
Методы сварки, инструментальные головки и допуски
Херрманн поясняет, что кондуктивная сварка будет демонстрироваться на левой стороне через стыковое соединение, а ультразвуковая сварка на правой стороне через стык внахлест, в то время как контактная сварка будет использоваться для соединений рамы. «MFFD продемонстрирует множество технических подходов, поэтому это не то же самое, что при производстве настоящего фюзеляжа, а вместо этого спроектировано как средство демонстрации и развития технологий», - добавляет он.
Разработка головок сварочного инструмента
Целью этих двух тем, написанных Велькеном, является разработка необходимых инструментальных головок для этих сварных соединений. «Когда вы свариваете две детали, вы должны приложить тепло и давление», - объясняет он. «Итак, это применяется головкой инструмента во время сварки. Для процесса кондуктивной сварки типа Fokker вы активно прикладываете тепло и давление с одной стороны, а пассивное давление со стороны опоры - с другой. Стыковое соединение представляет собой стопку из шести лент, и при соединении мы будем размещать стопку и нагревать ее во время сварки. Однако, поскольку ленточный материал LM PAEK UD является относительно новым в сварке, мы должны понимать условия процесса и то, как мы можем компенсировать допуски. Итак, мы должны определить материалы и толщину, а также геометрию инструментальной головки ».
«Обратите внимание, что использование стыкового соединения этого типа является стандартным процессом для того, что мы делаем с другими соединениями в нашем самолете», - отмечает Велькен. «Для MFFD мы хотим оставить верхнюю и нижнюю части фюзеляжа неизменными по сравнению с этой стандартной практикой, чтобы свести к минимуму количество материала, который мы должны адаптировать».
Гибкость допусков
Велькен отмечает, что, поскольку самые верхние сварочные поверхности по существу плавятся в жидкости, а затем спрессовываются вместе, «это дает большую гибкость для учета допусков». Обратите внимание, что в настоящее время используется термореактивный Крылья и фюзеляжи из армированного углеродным волокном полимера (CFRP) устраняются с помощью жидкого клея для прокладок. Хотя немногие люди хотят обсуждать это публично, общая проблема использования прокладок в композитных авиационных конструкциях получила широкое признание, и были опубликованы инициативы по ее сокращению и / или устранению, такие как метод сборки Flexmont для вертикального оперения.
“ Мы действительно рассчитываем получить преимущества в соблюдении допусков за счет использования термопластичных композитов, - говорит Велькен, - в частности, используя наши концепции дизайна и опираясь на наш опыт работы с термореактивным углепластиком и сваркой металлов. Ключевым моментом будет мониторинг на месте во время нагрева и приложения давления ». Он подчеркивает, что тепло является параметром номер один. «Я удивлен, насколько устойчивы процессы сварки термопластичных композитов к давлению. Основная проблема здесь - сдерживание этого давления и то, как оно снижается. В настоящее время мы контролируем обратную сторону сварного шва ».
Система автоматизированного сборочного производства Fraunhofer IFAM (вверху слева) с размерами в начале рабочей темы CFP07 (вверху справа) модифицируется, чтобы приспособить фюзеляж на 360 ° для сварки продольных и кольцевых швов MFFD. ИСТОЧНИК | Фраунгофер IFAM и cfk-valley.com, Clean Sky 2 7 th Объявление о приеме предложений, JTI-CS2-2017-CfP07-LPA-02-22, стр. 76.
Автоматизация сборки
В 7-м -м Конкурс предложений, тема JTI-CS2-2017-CfP07-LPA-02-22, «Разработка полноразмерной автоматизированной системы установки для продольных и окружных шарниров фюзеляжа» проводится Fraunhofer IFAM в рамках консорциума MultiFAL. Приведенный ниже отрывок проливает свет на то, как можно было бы реализовать описанные выше головки сварочного инструмента, которые сейчас находятся в разработке:
«При реализации процесса сборки фюзеляжа из термопласта, допуски становятся главной темой. The positioning and orientation of the fuselage shells, as well as resulting deformations caused by the welding process, need to stay within the tolerances. Comparable accuracies can be oriented to the state-of-the-art process of longitudinal joint. Here, the position error in each direction should be within 0.5 mm (in some exceptions up to 1 mm). … it can be assumed that a pre-load on the joint surface from both sides of approximately 1000N (independent of the welding technology) for a welding seam of 20 mm width is required by the automation system.”
Fraunhofer IFAM — which was also CTC Stade’s partner in developing the Flexmont VTP assembly process — describes its starting point:an in-house assembly plant system which can manipulate parts from 2 to 8 meters long and up to 6 meters high, including a 180° shell of a single-aisle aircraft. The system is enabled by a flexible arrangement of 10 cooperating hexapods (see “Reconfigurable Tooling:Revolutionizing composites manufacturing”), 24 linear units and modular rack elements. Vacuum grippers with 6-axis force and torque sensors adjust the pose and shape of the part, as required, to manage tolerances during assembly. The guidance and monitoring of these rapid, iterative adjustments is achieved through optical measuring devices.
According to the CFP07 text, Fraunhofer IFAM will modify this assembly plant system for holding a complete 360° fuselage, with work scheduled to begin in Q2 2018 and completed in 36 months.
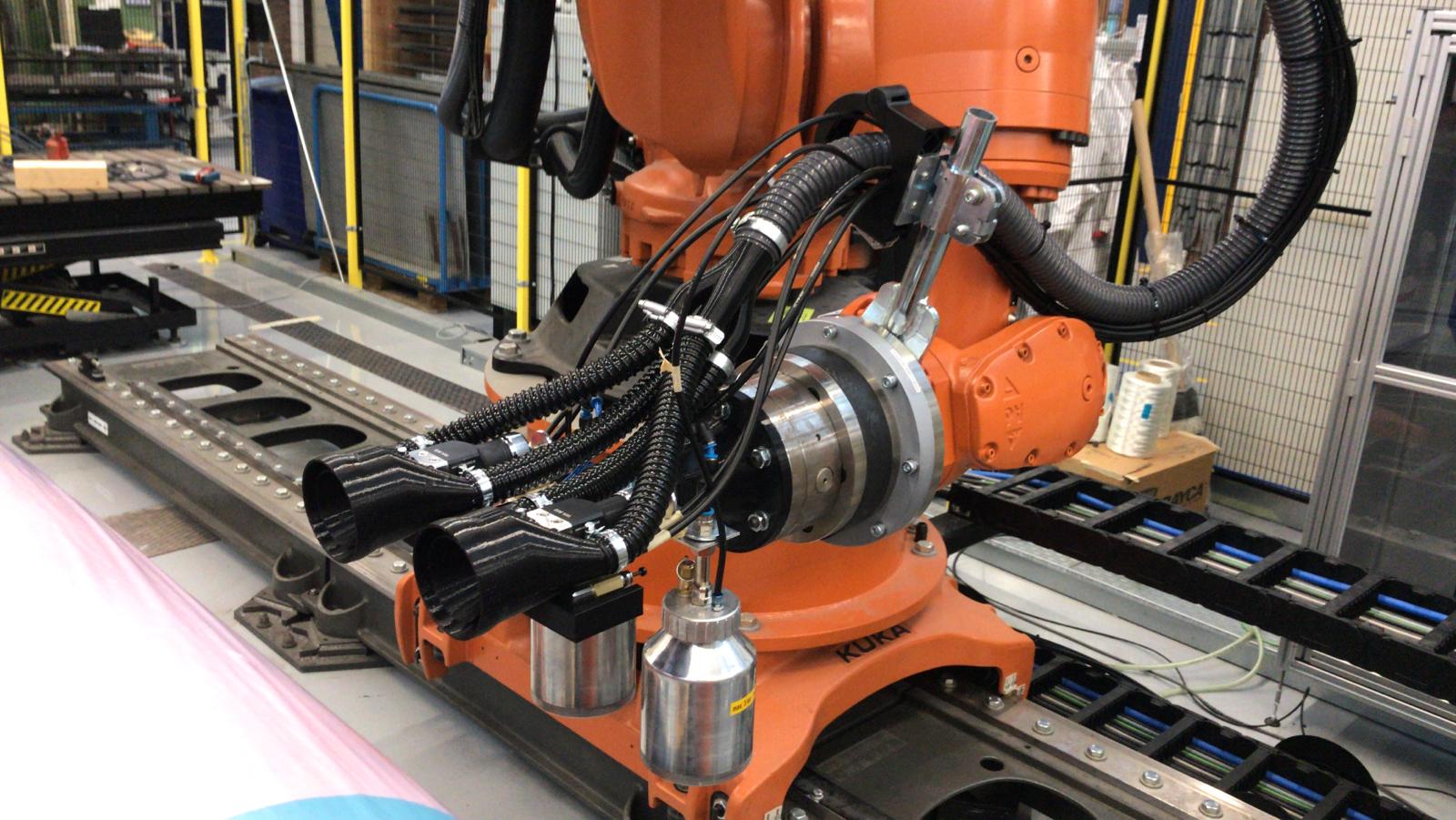
The STUNNING consortium is working with SAM|XL to develop automation for assembling the MFFD lower fuselage. SOURCE | samxl.com
Within STUNNING, activities are planned with the collaborative research center SAM|XL (Smart Advanced Manufacturing XL, Delft, Netherlands) to demonstrate automated welding techniques for assembling the lower fuselage. Specializing in automation for manufacturing large, lightweight composite structures, SAM|XL brings together TU Delft’s Aerospace Engineering group and Robotics Institute. GKN-Fokker is a major participant. One of the methods being investigated is sequential spot ultrasonic welding, which was proven in the Clean Sky 1 Eco Design project and TAPAS 2 as a fast and effective for connecting short fiber-reinforced brackets or clips to fuselage structures.
In her 2016 paper, titled “Smart ultrasonic welding of thermoplastic composites,” Villegas states that it is possible to scale up the ultrasonic welding process via sequential welding — that is, letting a continuous line of adjacent spot welds serve the same purpose as a continuous weld bead. Lab-scale sequential spot welding was used in the Clean Sky EcoDesign demonstrator’s TPC airframe panel, using flat energy directors to weld a CF/PEEK hinge and CF/PEKK clips to CF/PEEK C-frames (Fig. 6). Experimental comparisons with mechanically fastened joints in double-lap shear and pull-through tests showed promise. The process is further explored in 2018 papers {and 2019 papers} by Villegas’ TU Delft team member Tian Zhao {and in Villegas’ 2019 paper}.
— “Welding thermoplastic composites”, G. Gardiner, 2018.
The STUNNING consortium’s work with TU Delft and SAM|XL is adapting this technology to weld multiple system and semi-structural brackets, stiffening elements and stringers to the MFFD lower fuselage shell.
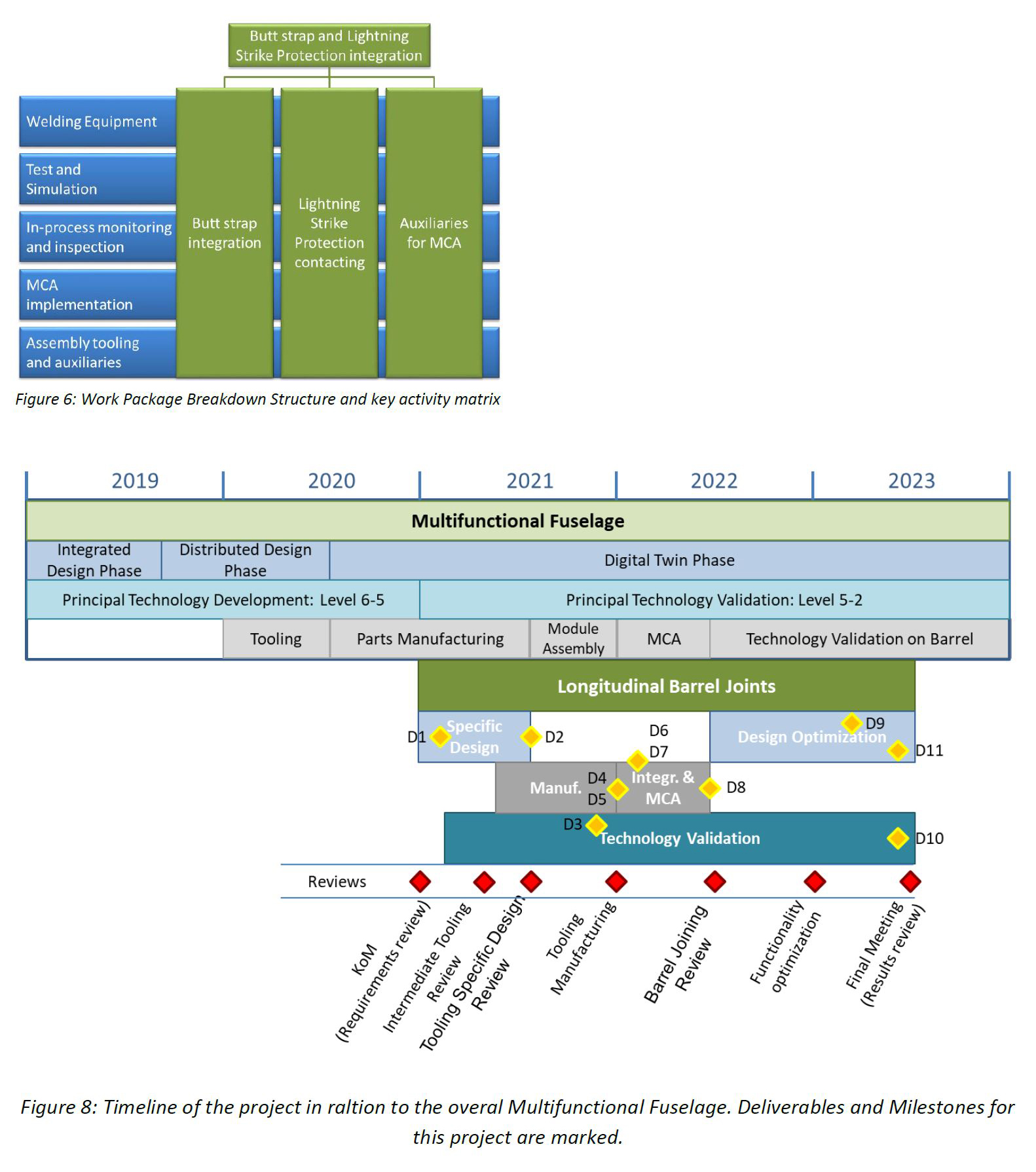
Work breakdown and timeline for MFFD assembly. SOURCE | Clean Sky 2 11 th Call for Proposals JTI-CS2-2020-CfP11-LPA-02-33, “Tooling, Equipment and Auxiliaries for the closure of a longitudinal Barrel Joint:Butt strap integration and Lightning Strike Protection continuity”, pp. 79 and 82.
Digital twin phase, 2020 and beyond
According to the Clean Sky website, the MFFD program reached an important milestone in Nov 2019 with the successful passing of its Critical Design Review (CDR). In the timeline above, the MFFD design enters a “Digital Twin Phase” in 2020-2021. What does this mean? “Though we have wrapped up the majority of the design phase, we are taking it a bit further by working with a specific lifecycle management approach,” explains Herrmann. “We are modeling imperfections and nonconformities from the NDT results and process parameters during component manufacturing. We want to combine this Industry 4.0 data with lifecycle management so that we continue to tailor the design according to what we are actually manufacturing. We want to see how far we can push this and what we can accomplish by the end of Clean Sky 2.”
For 2020, the chief agenda is manufacturing. “We hope to present various parts as they come together this year,” says Veldman. What will the largest challenge be for the STUNNING program? “Assembly,” he answers. “Not so much within STUNNING, but our lower fuselage has interfaces with the door surround structure, multiple Airbus-delivered components and the whole upper fuselage. Getting everything delivered at the right time and then bringing it all together will require a number of developments yet.”
That brings us to perhaps the biggest question:Will thermoplastic composites be used on the next aircraft entering production in 2030-35? “For sure, we want to try to use the technologies we are working on,” says Herrmann, “but I cannot say if or when thermoplastic composites will be on future aircraft. The most important part for us is that they are an enabler for dustless joining regarding ramping production to more than 70 aircraft per month. We have to show that it is feasible, not only with metallics but also with thermoplastic composites.”
“By the end of this project, we will have a more complete understanding of thermoplastic composite welding and will gain approval for its use in large primary aircraft structures,” says Salat. “If we can use this for future aircraft, we can achieve significant weight savings and improved sustainability.” But perhaps just as important is Clean Sky’s ability to bring Europe’s aviation research and innovation stakeholders closer together. “We have quarterly meetings where I sit with all of the LPA steering committee,” says Veldman. “I’m talking to the whole of the European aerospace industry, and it most certainly helps to open up opportunities for the future, not only for companies who can supply to us, but for a wide range of collaborations.”
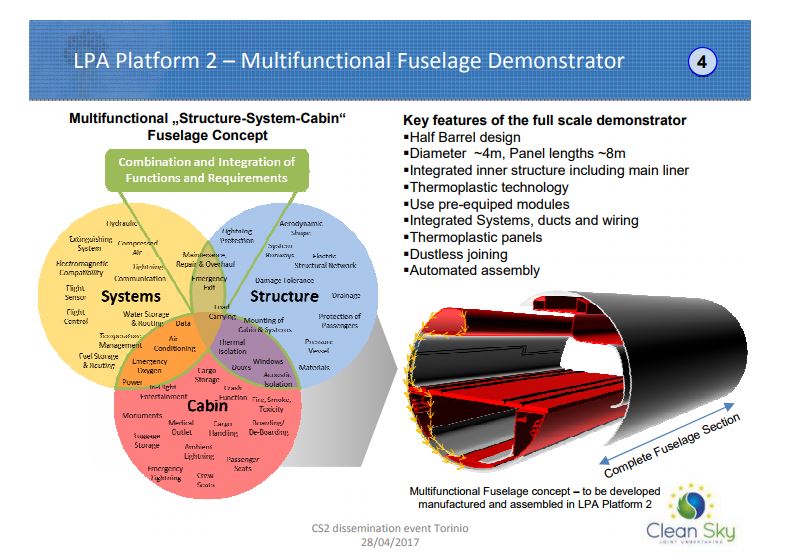
Смола
- 10 стартапов для 3D-печати, которых нужно остерегаться в 2020 году
- Обзор приложений:3D-печать для салонов самолетов
- Выжимание значения из данных для AI
- 6 советов по сварке для обслуживания оборудования
- Ищете сверхпрочный пластик? Оцените FR-4!
- Материалы:медицинские соединения и концентраты для лазерной сварки
- Советы и рекомендации по сварке инконеля
- Партнер Victrex и Bond для 3D-печати деталей из PAEK
- Первая секция фюзеляжа из композитных материалов для первого коммерческого реактивного самолета из компози…
- Основные советы по сварке алюминия