Шедевр с интенсивным использованием композитов:Corvette 2020, часть 1
Для Части 2 прочтите «Шедевры с интенсивным использованием композитов:Corvette 2020, Часть 2».
Долгожданный Chevrolet восьмого поколения Corvette (C8) от General Motors Co. (GM, Детройт, штат Мичиган, США), которая вызывает похвалы с момента ее официального открытия 18 июля 2019 года, начала коммерческое производство в начале этого года. Новый Corvette Stingray Кабриолеты и купе примечательны не только своей красотой, но и тем фактом, что GM произвела высокоэффективный, уличный, среднедвигательный ракетный корабль стоимостью менее 60 000 долларов США, что составляет одну треть от цены сопоставимого по характеристикам среднемоторного корабля. автомобили, но они также обладают впечатляющим набором нового и действительно инновационного композитного контента, который мы опишем здесь и во второй части в следующем месяце.
Новая конфигурация движка меняет все
Инженеры GM приступили к предварительному проектированию, зная, что они будут работать над среднемоторным автомобилем - первым серийным Corvette в восьми поколениях, чтобы иметь такую конфигурацию. «Мы развили архитектуру с передним расположением двигателя, насколько могли, для повышения производительности, поэтому переход на конструкцию со средним расположением двигателя был следующим логическим шагом на пути к совершенствованию и без того отличного автомобиля и к лидерству в сегменте», - объясняет Тэдж Юхтер из GM, исполнительный главный инженер. -Глобальный Корвет . Оснащенный пакетом производительности Z51, Corvette Stingray 2020 года может разогнаться от 0 до 96 км / ч (0-97 км / ч) за 2,9 секунды и достичь максимальной скорости 194 миль / ч (312 км / ч). Смещение двигателя к задней части автомобиля повлияло на многие вещи, в том числе на центр тяжести автомобиля, относительное положение пассажиров, расположение трансмиссии и конструкцию панелей днища и багажника. Конструкция с центральным расположением двигателя также привнесла более высокие рабочие температуры и шум в новые части автомобиля.
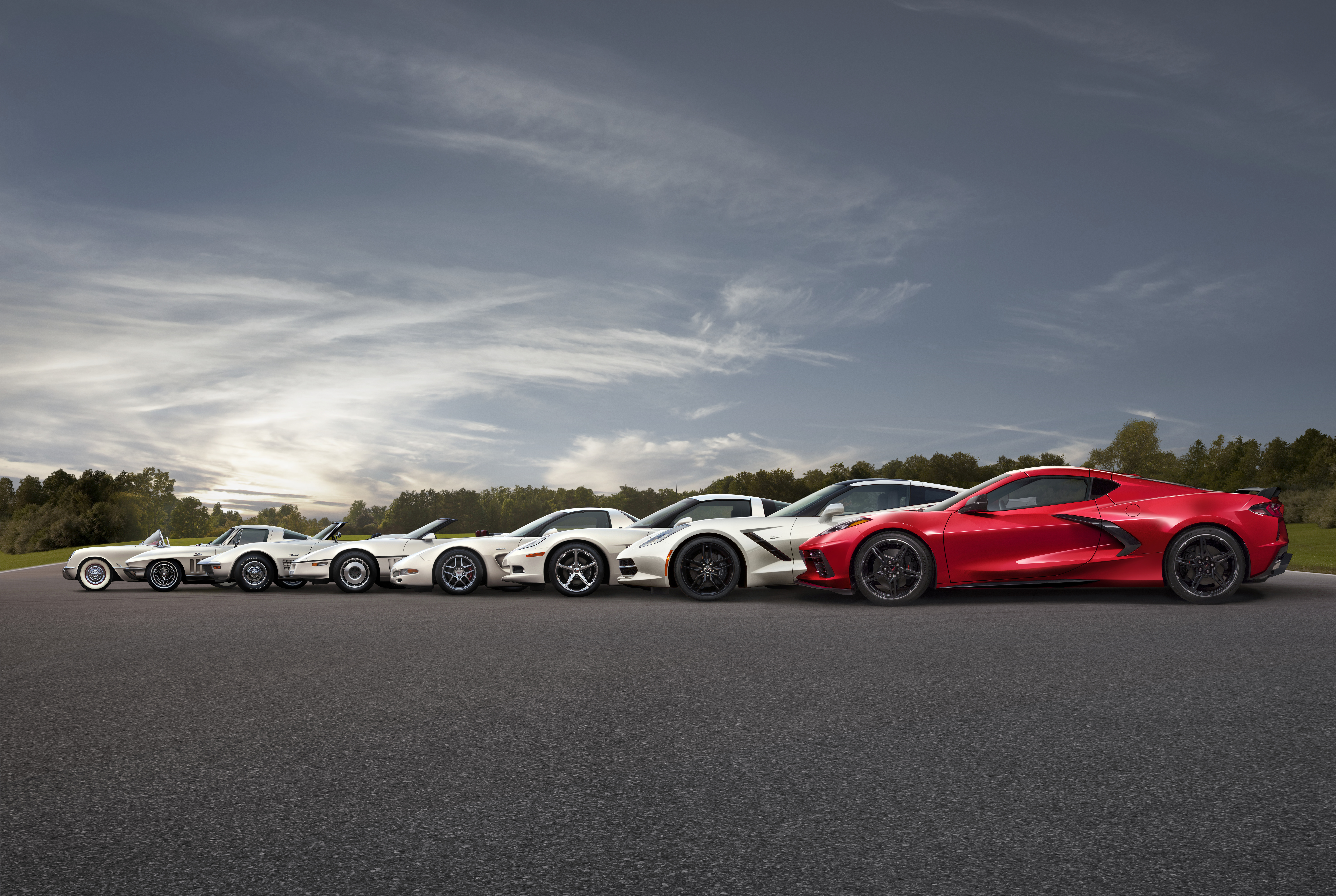
«Из-за среднего двигателя нам пришлось действовать по-другому, - объясняет Эд Мосс, Corvette . руководитель инженерной группы по конструкции кузова. «С самого начала у нас было очень много дискуссий о том, как расположить конструкцию кузова. В какой-то момент все было на столе, поскольку мы обсуждали лучший способ спроектировать и построить каждую систему. Например, мы обсуждали металлический или композитный материал для рулевых рубок. Если бы мы сохранили композитные колесные арки C7, нам пришлось бы прикрепить их к шарнирной стойке [стойке], которая непосредственно примыкает к переднему колесу в автомобиле со средним расположением двигателя, оставляя очень мало места для упаковки. Мы пошли туда с металлом. Мы даже вкратце обсудили металлические и композитные панели кузова. Однако было бы экономически нецелесообразно создавать линии стиля C8 в металлике ».
«Настоящая проблема, с которой мы столкнулись, заключалась в том, как обеспечить подачу воздуха», - вспоминает Крис Базела, Corvette . Ведущий инженер по конструкции кузова объясняет необходимость другого метода направления охлаждающего воздуха в и через безнаддувный 6,2-литровый двигатель V8 мощностью 495 лошадиных сил, который генерирует 470 фут-фунтов (637 Ньютон-метров) крутящего момента. «Мы испробовали всевозможные конструкции, которые заставляли воздух идти по действительно мучительным путям, создавая водовороты и потоки, которые нам не нужны. Потребовалось много итеративной работы с командой силовых агрегатов, чтобы разработать лучший путь для воздушного потока, потому что автомобиль должен дышать свободно и без ограничений. Нам также нужен был доступ к воздушной коробке и пришлось работать с пространством в задней части багажника. Другой проблемой было тепло и шум двигателя в салоне, потому что пассажиры больше не сидят за двигателем, а находятся прямо перед ним. И мы особенно заботились о качестве воздуха в салоне, поскольку со времени принятия C7 в Европе и других странах изменились законы, поэтому мы очень много работали над сокращением выбросов ЛОС [летучих органических соединений] ».
«Даже разрабатывая, как собрать машина была проблемой », - добавляет Мосс. «Благодаря конструкции с передним расположением двигателя у вас есть длинный капот и большой моторный отсек, что дает операторам достаточно места для сборки автомобиля изнутри отсека, даже с уже приваренной балкой переднего бампера. На среднем двигателе Corvette с его очень коротким передним зажимом, мы держим переднюю часть автомобиля открытой, когда автомобиль собирается, а затем прикручиваем болтами передний бампер ».
«Это было довольно сложным делом, чтобы получить правильные формы, одновременно гарантируя, что наши поставщики могут производить детали и наша команда в Боулинг-Грин [ Corvette , находящийся в Кентукки, GM. сборочный завод] мог их собрать », - продолжает« Базела ». «В конце концов, остался только один композит, перенесенный с кузова C7 на C8». Это был жесткий листовой формовочный компаунд класса A с удельным весом 1,2 (SG), разработанный для Corvette 2016 года. и используется во множестве внешних закрывающих устройств на новом автомобиле.
Архитектура автомобиля
На четыре поколения (C5-C8), Корветы имеют трехслойную структуру из нескольких материалов: рама обычно смесь алюминия или стали - на этот раз с частью из композитного материала, армированного углеродным волокном (CFRP); строение тела , который в значительной степени представляет собой склеенный композит, позволяющий извлечь выгоду из гибкости конструкции и производства; плюс прикрученные распродажи (панели кузова), которые были составными со времен Covette Июнь 1953 г. Дебют. Эта многоуровневая гибридная структура не только обеспечивает доступную легкость при больших объемах производства - особенно для автомобилей этого класса производительности, - но также позволяет производить несколько вариантов транспортных средств с небольшими затратами на инструменты. Фактически, для нынешнего C8 GM удалось произвести все композитные панели кузова класса A (склеенные внутренние и внешние) как для базовой модели купе, так и для кабриолета, используя всего 20 инструментов.
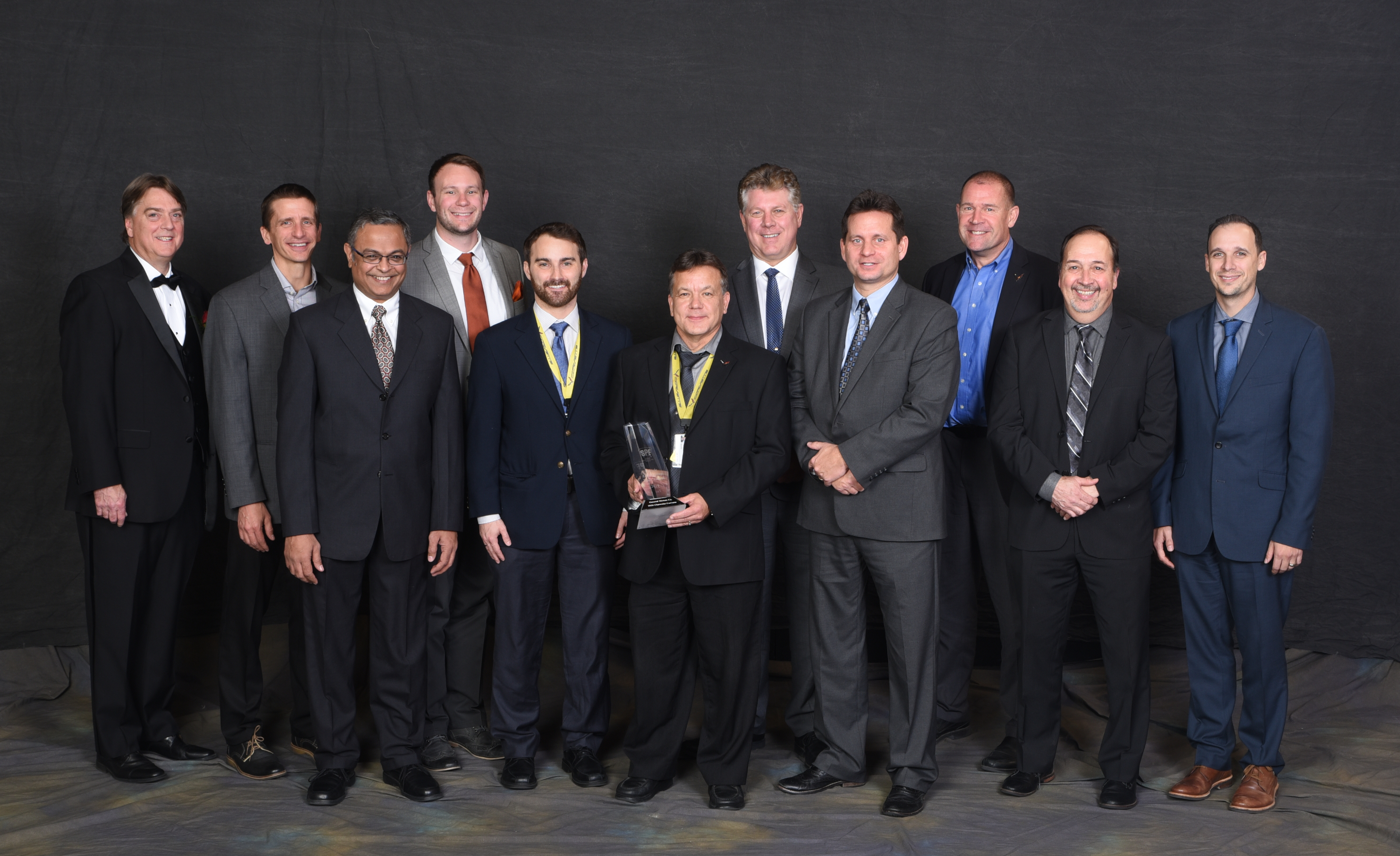
Кроме того, Корветы всегда проектировались с архитектурой открытой крыши, независимо от того, являются ли они на самом деле кабриолетами или купе с фиксированными или съемными панелями крыши. Поскольку автомобили с открытой крышей обычно менее жесткие, чем автомобили с фиксированной крышей, каждому Corvette ’ уделяется большое внимание. Наша инженерная задача - всегда создавать как можно более прочный фундамент для улучшения подвески и рулевого управления. Исторически туннели (кожухи трансмиссии и карданные валы на автомобилях с передним расположением двигателя) преобладали Corvette конструкции кузова и сыграли ключевую роль в достижении высокой жесткости на кручение. В случае нового Corvette GM добилась еще большей жесткости. При снятой крыше кузов C8 на 53,78% жестче, чем у эталонного высокопроизводительного конкурента со средним расположением двигателя, на 29,27% жестче, чем у второго высокопроизводительного конкурента со средним расположением двигателя, и на 13,79% жестче, чем у C7. Две составные части внесли важный вклад в жесткость автомобиля:одна прикреплена непосредственно к конструкции рамы (балка заднего бампера), а другая прикреплена к днищу (закрытие нижнего туннеля).
Структура кадра
Рама C8 в основном изготовлена из алюминиевого сплава с одной деталью из углепластика, разработанной для соответствия строгим требованиям GM по цене "доллар за килограмм". В отличие от этого, рама C7 была полностью алюминиевой, а C6 в основном стальным.
Единственная композитная деталь, непосредственно прикрепленная к раме, которая проходит вместе с кузовом в белом (BIW) путем электрофоретического покрытия ржавчиной (который GM называет ELPO), - это уникальная балка заднего бампера из углепластика. Эта деталь помогает придать раме жесткость и улучшить характеристики при ударе сзади. Его изогнутая форма - возможная благодаря новому процессу, называемому радиусная пултрузия, разработанному Thomas GmbH + Co. Technik + Innovation KG (TTI, Бремервёрде, Германия) - позволяет ему соответствовать задним стилям и помещаться в ограниченном пространстве упаковки, сохраняя при этом целостность размеров близко до жары моторного отсека. В качестве первой изогнутой пултрузионной детали в автомобильной промышленности (см. Полную версию этой части в выпуске CW за май 2020 г.) полая двухкамерная балка была произведена компанией Shape Corp. (Гранд-Хейвен, Мичиган, США) на оборудовании, разработанном и построен TTI. Балка весит всего 1,3 килограмма и имеет прикрепленную / закрепленную болтами проушину для буксирного крюка, обеспечивающую тяговое усилие 25 килоньютон.
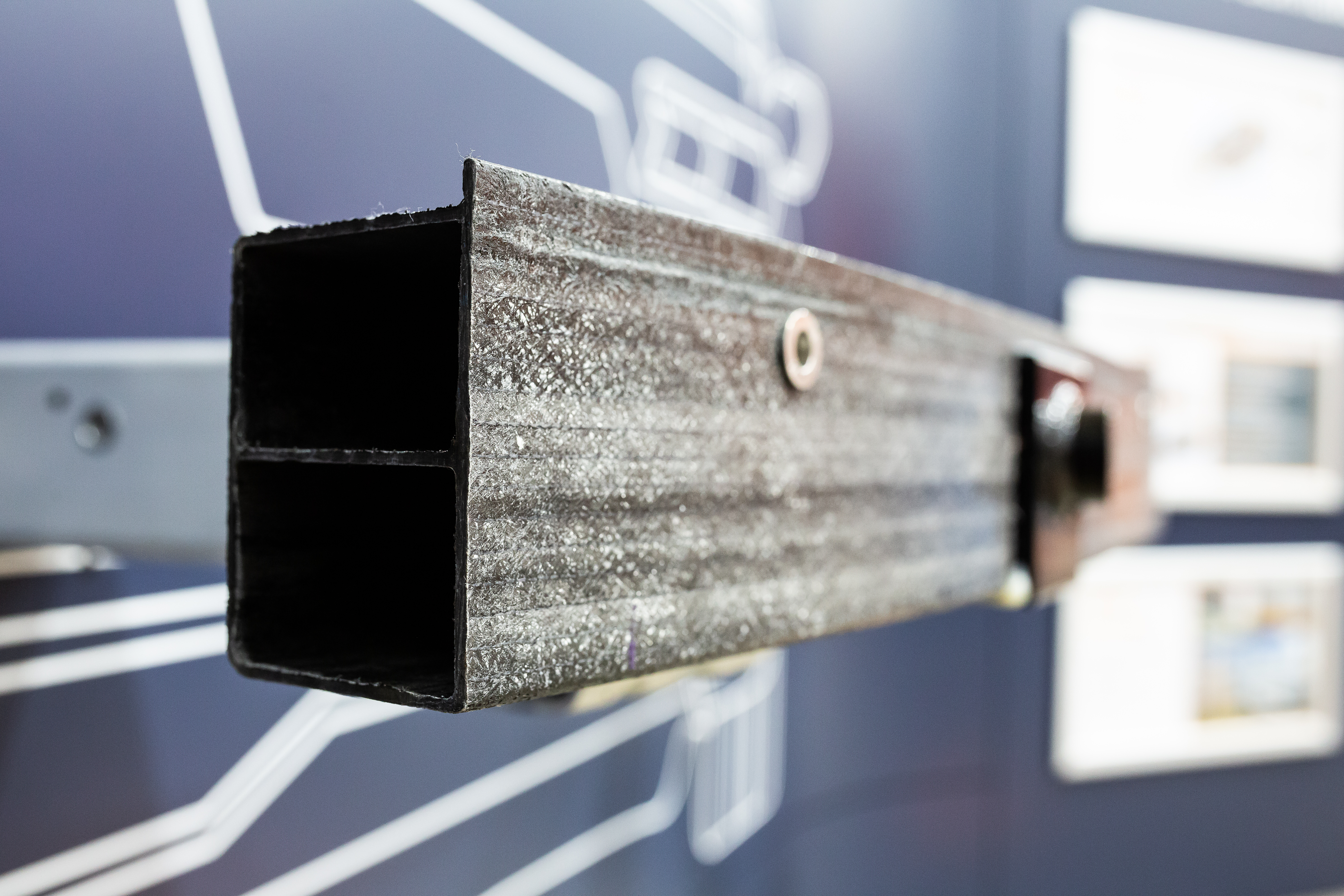
Структура тела:часть A
Практически все компоненты конструкции кузова C8 являются композитными и приклеиваются и / или прикручиваются к раме после того, как последняя подвергается ELPO. Известные композитные детали на этом уровне включают структурные крышки днища и пола, о которых мы расскажем в этом выпуске, а также передние и задние стволы, воздуховоды, а также заднюю окантовку и переборку, которые мы рассмотрим вместе с панелями кузова и отделкой. в следующем месяце.
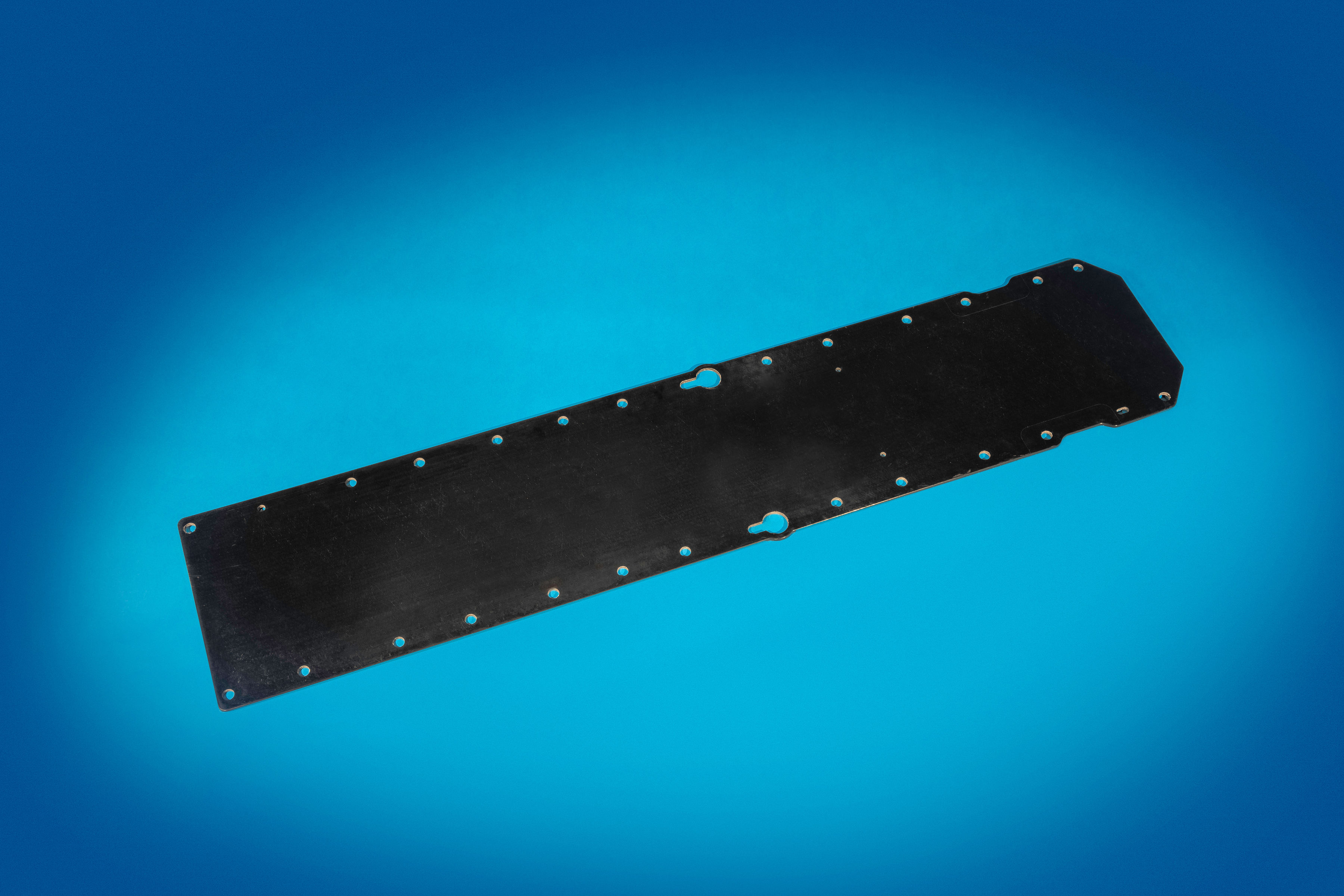
Съемное закрытие конструкции нижнего туннеля на C8, которое действует как люк, обеспечивает более 10% жесткости автомобиля на кручение и действует как основной путь нагрузки во время аварии. Эта гибридно-композитная панель состоит из трех слоев заготовки из стекловолокна. Они состоят из непрерывных / тканых и рубленых / случайных волокон с объемной долей волокна (FVF) 38%, с вуалью, добавленной к верхнему и нижнему поверхностным слоям на каждой стопке для улучшения качества поверхности. Стеклянные преформы чередуются с двумя слоями преформ, изготовленных из углеродного волокна со стандартным модулем упругости T700 12K фирмы Toray (Токио, Япония) в виде двухосной ткани NCF с 21% FVF и матрицы на основе сложного винилового эфира (VE). Распродажа производится компанией Molded Fiber Glass Co. (MFG, Аштабула, Огайо, США) с использованием собственного процесса PRiME (Предварительное армирование, обеспечивающее производственное превосходство), типа жидкостного компрессионного формования (LCM).
За исключением единственной алюминиевой перегородки рядом с задними колесами, которая является частью опоры двигателя, остальные панели днища состоят либо из прессованного пластика SMC, либо из термопласта, полученного литьем под давлением. Помимо других преимуществ, эти панели уменьшают турбулентность и сопротивление днища кузова, улучшают топливную экономичность и предотвращают попадание влаги, пыли и камней в двигатель и трансмиссию автомобиля. Кроме того, они обеспечивают пространственную основу для множества внешних и внутренних интерфейсов.
Низкоплотный, но структурный Панели SMC имеют новый состав (в данном случае 40% измельченного стекловолокна FVF / ненасыщенный полиэфир (UP)), разработанный MFG. Материал называется «плавающий» SMC, потому что плотность каждой панели меньше 1,0 (средний удельный вес =0,97) и, следовательно, может плавать в воде. Компания MFG произвела все структурные детали из SMC и LCM для автомобиля.
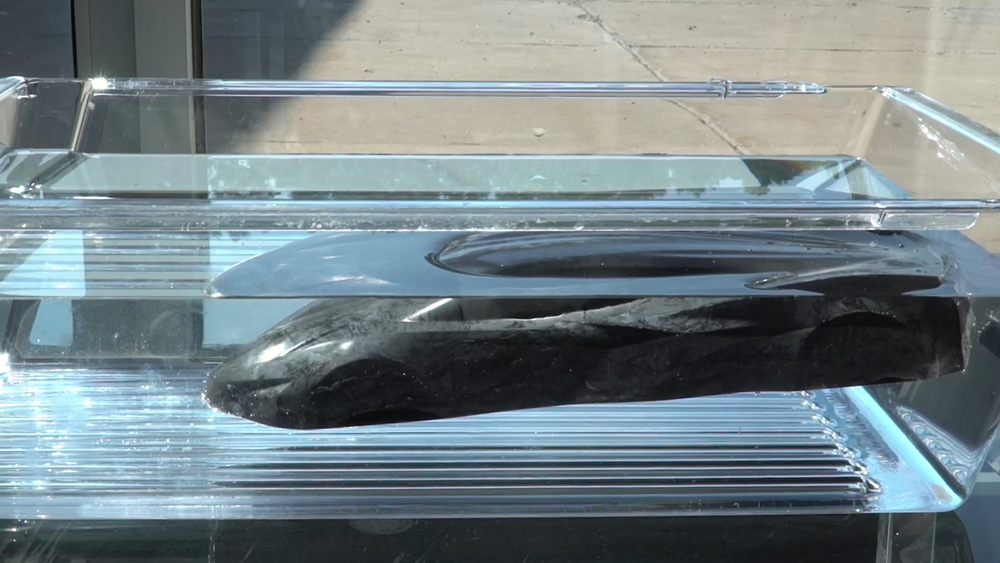
Автомобиль также оснащен гибридным полом, оптимизированным для защиты от изгиба при кручении и боковых ударов (зацепляя панели коромысла и туннель, к которому он прикреплен). Панели пола изготовлены из штампованного алюминия, обращенного к кабине, приклеенного к листам дорожного композита 1.5-SG (60 мас.% Непрерывного и тканого стекловолокна / VE), произведенного по технологии PRiME. Перед термическим склеиванием обоих слоев полиуретановым структурным клеем Pliogrip 9100 от Ashland Global Holdings Inc. (Уилмингтон, Делавэр, США) MFG очищает и подготавливает материалы.
Все композитные детали, непосредственно прикрепленные к раме C8, сначала подвергаются лазерной абляции - процессу, разработанному GM, MFG и Adapt Laser Systems LLC (Канзас-Сити, Миссури, США) для 2016 Corvette, и адаптирован из метода очистки форм, применяемого в производстве композитов. Лазерная абляция заменяет ручное шлифование и сокращает трудозатраты, время и затраты, устраняет пыль и улучшает повторяемость. Путь лазера, угол атаки и уровень энергии настраиваются в зависимости от материала и геометрии каждой детали. Чтобы максимизировать производственную гибкость, вся нижняя часть кузова, включая пол, соединяется с рамой и с самим собой с помощью соединения и винтов.
В августовском номере CW мы продолжим освещать инновации в области композитных материалов на новом Corvette . , продолжая с дополнительными компонентами на уровне структур кузова и заканчивая внешними замками (кузовными панелями), а также дополнительной отделкой и модернизацией. См. Часть 2.
Смола
- 10 преимуществ облачных вычислений в 2020 году
- Будущее 3D-печати:12 ключевых выводов конференции AMFG AM Landscape Digital 2020 (часть 1)
- Руководство по техническому обслуживанию, часть 3
- Введение в гармоники:Часть 1
- Устойчивое развитие в производстве. Часть 3
- Тенденции и вызовы 2020 года, на которые повлиял Covid-19:часть I
- Поворот необязателен
- Что такое номер детали?
- Обработка мелких деталей
- Цилиндричность в GD&T