На пути к цифровому производству интеллектуальных многоматериальных волокон
Аннотация
Волокна встречаются повсеместно и обычно пассивны. Оптоэлектроника, реализованная в оптоволокне, может революционизировать множество областей применения, включая биосинтетическую и носимую электронику, зондирование окружающей среды и сбор энергии. Однако реализация высокопроизводительной электроники в волокне остается сложной задачей из-за труднодостижимости стратегии обработки материала, которая позволила бы обернуть устройства, сделанные из кристаллических полупроводников, таких как кремний, в волокно в упорядоченном, адресуемом, и масштабируемым образом. Современные подходы к изготовлению волоконных датчиков либо немасштабируемы, либо ограничивают выбор полупроводников аморфными, такими как халькогенидные стекла, уступающие кремнию по своим электронным характеристикам, что приводит к ограниченной полосе пропускания и чувствительности таких датчиков по сравнению со стандартным кремнием. фотодиод. Наша группа обосновывает универсальное внутриволоконное производство логических схем и сенсорных систем по аналогии с очень крупномасштабной интеграцией (СБИС), которая сделала возможным появление современного микропроцессора. Мы разрабатываем универсальную методологию изготовления гибридных материалов, которая объединяет структуры волоконных материалов, типичные для интегрированных микроэлектронных устройств и систем из диоксида кремния, кремния и жаропрочных металлов. Эта методология, получившая название «СБИС для волокон» или «СБИС-Fi», сочетает в себе трехмерную печать преформ, тепловую вытяжку волокон и сборку интегрированных устройств со встроенными волокнами после вытяжки посредством выборочного пространственно-когерентного разрушения капилляров. сердечников волокна. Мы полагаем, что этот метод предоставит новый класс долговечных, недорогих, повсеместно распространенных оптоволоконных устройств и датчиков, позволяющих интегрировать ткани, соприкасающиеся с искусственными объектами, такими как мебель и одежда, в Интернет вещей (IoT). Кроме того, это будет стимулировать инновации в области 3D-печати, распространяя подход цифрового производства на сферу наноэлектроники.
Введение
Хотя вытянутые из стекла волокна восходят к римским временам, первые функциональные оптические волокна были изготовлены в 1792 году французскими братьями Чаппе для целей связи [1]. В 1842 году швейцарский физик Жан-Даниэль Колладон показал, что свет может направляться внутрь через водную струю [2]. Эти два открытия привели к десятилетиям усовершенствований оптики и материаловедения, которые привели к появлению современных эффективных волокон, обеспечивающих высокоскоростную связь и хранение данных на километрах по всему миру, таких как завершенный Транстихоокеанский подводный кабель (TPC) протяженностью 25000 км. в 1996 г. [3, 4]. Более того, волоконно-оптические датчики (FOS) используются в большом количестве биомедицинских, нефтегазовых, морских, архитектурных, химических и аэрокосмических приложений [5, 6].
Управление и улучшенные характеристики распространения света с использованием волоконных фотонных кристаллов (ФКФ), разработанные в 1996 году Филипом Расселом, открыли двери для исследований более сложных внутренних функциональных структур волокон [7,8,9]. Новые микроструктуры также приветствовали интеграцию разнообразия материалов в их состав [10, 11] для разработки интеллектуальных волокон для электроники [12], оптоэлектроники [11], внутриволоконного синтеза [13], микрофлюидики [14], микроэлектромеханических систем [15, 16] и биосинтетический интерфейс [17]. Интеллектуальные волокна отличаются от традиционных волокон тем, что включают в себя нетрадиционные функции, помимо оптической связи и типичного использования волокон в коммерческих тканях. Интеллектуальные волокна можно использовать для эстетики в электронном текстиле, контролируя внешний вид волокон из-за оптических помех в их микроструктуре [18] или для улучшения характеристик, например, в случае обычных волоконно-оптических направляющих и диэлектрической подкладки зеркал, позволяющих направлять свет. по воздуху [19, 20].
Чтобы сделать волокно функциональным, оно должно состоять из материалов с различными электронными свойствами, его архитектура должна быть специально спроектирована для выполнения заданной функции, а его внутренние характеристики должны быть уменьшены в наномасштабе, на порядки меньше, чем ядро современных телекоммуникаций. волокна. Волокна обычно создаются методами изготовления оптического волокна, то есть термически вытягиваются из макроскопических цилиндрических или кубовидных стержней, называемых «заготовками». Процесс изготовления начинается с выбора подходящих материалов сердечника и оболочки, таких как металлы, изоляторы и полупроводники. Например, первое волокно, включающее структуры металл-диэлектрик-полупроводник, было разработано в 2004 году для фотодетектирования [21]. Материалы для преформы выбираются такими, чтобы их вязкость μ , сопоставимы при температуре вытяжки, попадая примерно в окно 4
Преформа, которая, по сути, является увеличенной версией волокна, может быть изготовлена с использованием различных технологий, таких как скручивание листов материала, например ковер, укладка фрезерованных деталей, например пазл, или 3D-печать, как показано на рис. 1а. (I) и обсуждались в этом обзоре, а затем закреплены вакуумным спеканием. Затем преформа нагревается в печи и вытягивается в волокно, подобное карамели или ириске (см. Чертеж конуса на рис. 1а (II)), сохраняя при этом ее расположение в поперечном сечении на основе заданных термомеханических свойств конструкции, таких как вязкость, граница раздела фаз. энергии, взаимной адгезии и дифференциального теплового расширения (рис. 1a (III)) [22]. Этот процесс для преформы, напечатанной на 3D-принтере, схематично проиллюстрирован на рис. 1а. Типичная вытяжка может дать километры волокна с очень мелким наноразмерным диаметром поперечного сечения около 5 нм [23, 24].
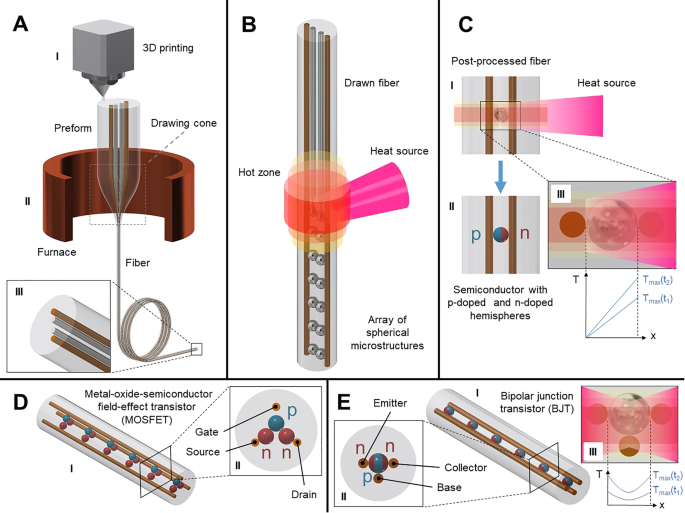
VLSI-Fi:концептуальные схемы технологии VLSI-Fi, представляющие подход «2D + 1D + 0D» . а Преформа, напечатанная на 3D-принтере a (I) термически вытянутый a (II) в длинное тонкое волокно, сохраняющее геометрию поперечного сечения преформы (2D). б Формирование осевого рисунка волокна посредством пространственно когерентного, избирательного по материалу капиллярного разрыва (+ 1D), что приводит к сборке изначально непрерывных отдельных сердечников в массивы дискретных устройств, контактирующих параллельно. c Управляемый сегрегацией контроль легирования в полупроводниковых частицах после распада, позволяющий контролировать внутреннюю архитектуру отдельного устройства c (II) через температурный градиент c (III). г (I) Схематическое изображение полевого транзистора металл-оксид-полупроводник (MOSFET) через СБИС-Fi, где полупроводники p-типа и n-типа показаны синим и красным соответственно. Золотые непрерывные стержни, встроенные в кремнеземное волокно, действуют как затвор, исток и сток. Полученное поперечное сечение волокна показано на d . (II). Аналогичным образом e (I) показывает схематическое изображение биполярного переходного транзистора (BJT), реализованного с помощью VLSI-Fi, достигаемого за счет воздействия источников тепла как со стороны эмиттера, так и со стороны коллектора. Поперечное сечение волокна е (II) показаны эмиттер, коллектор и база BJT (непрерывные стержни, встроенные в волокно), причем полупроводники p-типа и n-типа n-p-n перехода показаны синим и красным цветом соответственно
На этапе последующей вытяжки, играя на капиллярной нестабильности, волокно может быть повторно разжижено путем нагрева, чтобы обеспечить разрыв сердцевины пространственно когерентным избирательным образом, что позволяет осуществлять осевой контроль над структурами, встроенными в волокна [25,26, 27], как показано на фиг. 1b. Альтернативные методы формирования рисунка ядер в осевом направлении включают УФ-облучение через фотошаблоны в фотополимерных ядрах, что приводит к получению микрочастиц нетривиальной формы [28]. Другие методы гибридной функционализации включают покрытие поверхностей волокна функциональными материалами [10, 29] и ограничение оболочки волокна вытяжкой [12] на массив оптоэлектронных устройств, изготовленных стандартным производством дополнительных металл-оксид-полупроводник (CMOS).
Волокна могут быть сплетены в ткани или сети для достижения коллективной функциональности, превосходящей функциональность отдельного волокна [30]. Созданные с помощью биомимикрии, волокна могут быть сформированы в соответствии с полезными свойствами природы для повышения функциональности ткани, например гидрофобности [31]. Волокна также могут быть задуманы как платформы синтеза для производства недорогих материалов, таких как преобразование алюминиевых сердечников в кремний в волокнах с кварцевой оболочкой [13] или термически индуцированное изготовление пористых структур путем разделения фаз [32]. Волокна также могут использоваться для дистанционного и распределенного обнаружения сигналов, например для химического определения опасных летучих веществ в окружающей среде [29]. Гибкость конструкции волокна такова, что в одном волокне можно объединить несколько функциональных модальностей для сложных приложений, таких как глубокая стимуляция спинного мозга и мониторинг у мышей для исследования нейродегенеративных заболеваний [33]. Эти примеры демонстрируют некоторые из множества областей, в которых интеллектуальные волокна являются естественным решением.
Мотивация
Несмотря на то, что волокна повсеместно распространены, интеграция высокоэффективных микроэлектронных систем в тонкое волокно остается серьезной проблемой [11, 12]. Были предложены различные подходы к решению этой проблемы, при этом усилия в основном были сосредоточены на низкотемпературных материалах. Например, химическое осаждение из паровой фазы под высоким давлением (HPCVD) использовалось для интеграции сложных полупроводников в микроструктурированные оптические волокна (MOF) [34], а также для создания гибких кремниевых волокон с p-i-n-переходом [35]. В качестве альтернативы CO 2 Лазер был использован для рекристаллизации SiGe сердцевины в кварцевых световодах с целью изменения их электронных свойств [36]. Такие подходы либо приводят к устройствам с ограниченной электронной полосой пропускания, как в случае с халькогенидными материалами, которые по своей природе аморфны, либо по своей природе немасштабируемы.
Таким образом, Лаборатория систем с поддержкой волокон и аддитивного производства (FAMES Lab) разработала и в настоящее время реализует методику управления трехмерной архитектурой волокон, которая описана в этом обзоре. Поскольку сложность конечного волокна коррелирует со сложностью поперечного сечения преформы, изготовление преформ произвольной формы обеспечивает функциональность волоконных устройств, недостижимую в противном случае. Кроме того, 3D-печать широко доступна, что делает ее экономичной и удобной технологической альтернативой традиционно используемым методам, позволяя использовать широкий спектр материалов, от термопластов до высокотемпературных материалов, а также биоматериалов [37].
Кроме того, в лаборатории FAMES Lab есть возможность обрабатывать высокотемпературные материалы наряду с более традиционным использованием термопластов в аддитивном производстве, что позволяет нам использовать такие свойства, как высокая подвижность электронов в Si / Ge [38]. в качестве будущего использования цирконата титаната свинца (PZT) / BaTiO 3 композиты для пьезоэлектрических применений, имеющие большие пьезоэлектрические коэффициенты по сравнению с полимерами [39, 40] и более высокую акустическую полосу пропускания [41].
Помня об этих проблемах, мы предлагаем оптимизационные решения с использованием аддитивного производства для более быстрого и сложного изготовления преформ, моделирования разрыва капилляров для оптимизации осевого контроля волокна и комбинации наших волокон с тканевой инженерией. Эти стратегии позволяют создавать реалистичные биомедицинские платформы с возможностями биочувствительности и биофункционализации для анализа лекарств и лечения in vitro как одного из многообещающих приложений волоконных устройств.
Концепция
Чтобы реализовать функциональные волокна, мы черпаем вдохновение в очень крупномасштабной интеграции (СБИС) - технологии цифрового проектирования и производства, которая в 1970-х годах положила начало современным микропроцессорам. Этот метод использует фотолитографию и химическую / термическую обработку открытых участков пластины полупроводниковой подложки для определения характеристик интегральной схемы в этом слое (2D), в то время как изготовление полной схемы осуществляется путем наложения таких отдельных слоев в направлении, перпендикулярном к поверхность пластины (+ 1D). Кроме того, электронное легирование отдельных компонентов схемы (+ 0D) может контролироваться имплантацией и термической активацией [42]. Наш подход к волокнам, получивший название «СБИС для волокон» или «СБИС-Fi», аналогичен:во-первых, аддитивное производство и тепловая вытяжка преформы определяют геометрию поперечного сечения волоконного устройства (2D); во-вторых, получившееся в результате волокно может быть впоследствии сформировано в осевом направлении (+ 1D), что позволяет собирать массивы интегрированных дискретных устройств из изначально непрерывных, но разделенных сердечников; и, в-третьих, может выполняться управляемое сегрегацией структурирование отдельных встроенных в оптоволокно устройств (0D). В таблице 1 проводится сравнение двух методов, подчеркивая соответствие между каждой степенью контроля геометрии, возможной с помощью каждого метода («2D + 1D + 0D»). Схема описанных шагов подробно показана на рис. 1, где примеры возможных встроенных в оптоволокно устройств могут быть реализованы с использованием техники VLSI-Fi.
Экспериментальный раздел
В этом разделе мы сначала опишем нашу работу по 3D-печати поликарбонатных преформ, а затем последующие достижения в области 3D-печати на стекле с использованием стереолитографии. Затем мы подходим к формированию осевого рисунка волокон через пространственно когерентный, избирательный по материалам капиллярный разрыв, который позволяет собирать изначально непрерывные отдельные сердечники в массивы дискретных устройств, контактирующих параллельно. Наконец, мы предлагаем применение наших биообрабатывающих волокон в сочетании с тканевой инженерией для мониторинга роста жизнеспособных тканей in vitro. Функции становятся возможными благодаря использованию микрожидкостных каналов внутри волокна для доставки клеток и передачи биохимических веществ, а также проволоки из сплава с памятью формы для управления движением и пьезоэлектрических элементов для отображения окружающей среды с помощью ультразвуковых волн.
Рисование преформ, напечатанных на 3D-принтере
Как указывалось ранее, традиционные методы изготовления преформ, такие как прокатка тонкой пленки и пакетирование и сырье [10], ограничены в производстве сложных геометрических структур, занимают значительное время в процессе вытяжки волокна и требуют квалифицированных специалистов. рабочая сила и дорогое оборудование. 3D-печать решает эти проблемы с помощью растворимого вспомогательного материала и частично автоматизированного и удобного для пользователя процесса. Это позволяет легко печатать очень сложные геометрические формы за относительно короткий период времени.
Чтобы оценить влияние угла печати преформ из поликарбоната (Hatchbox 3D), цилиндрические и квадратные стержни были напечатаны с помощью одноголовочного FDM-принтера Prusa i3 MK2. Температуры экструдера и печатной платформы были установлены на 235 ° C и 105 ° C соответственно, а принтер был настроен на изготовление преформ со 100% -ным заполнением с соплом 0,35 мм. Ориентация слоев в преформе зависит от горизонтальной ориентации детали по отношению к печатному слою, и когда преформа вводится в печь во время термической вытяжки, на тепловой поток влияет ориентация слоев. Чтобы проверить, какая ориентация лучше всего подходит для термической вытяжки, были напечатаны преформы с ориентацией 0 °, 15 °, 30 °, 45 ° и 90 °. Все углы измеряли между продольной осью преформы и горизонтальной осью. Заготовки, напечатанные на 3D-принтере, прошли процесс термической вытяжки в печи с тремя температурными зонами:90 ° C, 100 ° C и 200 ° C. Для цилиндрических преформ термическая вытяжка прошла успешно при углах 0 ° и 45 °. При вытяжке преформы под углом 90 ° всегда происходит сбой из-за расслоения слоев.
Мы также смогли успешно нарисовать неравновесные структуры, такие как квадратный стержень с импровизированным узором заливки, как показано на рис. 2a (I), где вместо прямолинейного узора заливки также было настроено заполнение по периметру и печать в упорядоченной структуре. Вытяжка преформы с квадратным углом 0 ° прошла успешно, и, хотя она немного деформировалась, волокно все еще могло сохранять форму преформы. Волокна с размерами всего 40 мкм × 60 мкм были успешно вытянуты и показаны на рис. 2а, без отслоения слоев. Кроме того, все слои были закреплены должным образом. Пример поперечного сечения волокна показан на рис. 2a (IV), а изображения волокна до и после отжига показаны на рис. 2a (V) и 2a (VI) соответственно, где мы видим, что отожженное волокно достигает оптической прозрачности, которая будет охарактеризована в будущих работах. Из этих экспериментов мы пришли к выводу, что наиболее успешными являются преформы, напечатанные под углом 0 °, тогда как 90 ° всегда отслаиваются в процессе вытяжки. Укрепление слоев в термически вытянутых волокнах улучшилось по мере уменьшения угла ориентации преформы, напечатанной на 3D-принтере.
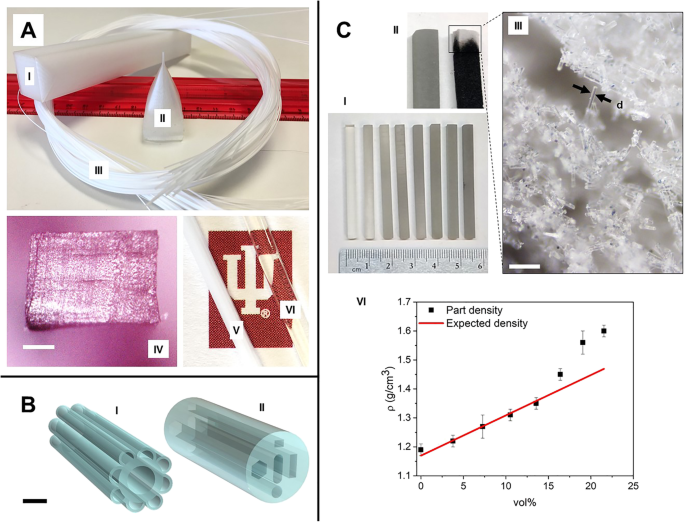
Преформы, напечатанные на 3D-принтере: a (I) Преформа из поликарбоната, напечатанная на 3D-принтере с квадратным основанием. а (II) Рисование конуса. а (III) Поликарбонатное волокно, полученное после термической вытяжки. а (IV) Поперечное сечение волокна после процесса вытяжки без расслоения слоев. Поперечное сечение имеет прямоугольную форму из-за неизотропной пористости рисунка заполнения (шкала 200 мкм). а (V) Вытянутое волокно перед отжигом. а (VI) Вытянутое волокно после отжига с очевидной оптической прозрачностью. б CAD-модели стеклянных преформ, успешно реализованные в натриево-известковом стекле с помощью высокоточной экструзионной 3D-печати. б (I) Структура имитирует волосы синего птицееда. б (II) Модель преформы с неравновесной геометрией поперечного сечения (масштабная линейка 1 см). c (I) Образцы стекла квадратной формы с увеличивающимся стеклянным заполнением (слева направо), напечатанные методом SLA. c (II) Деталь образца стекла перед выпечкой (слева) и во время запекания (справа). В последнем случае можно увидеть черную окраску, вызванную карбонизированными остатками смолы, в то время как кончик имеет белый цвет после удаления этих остатков золой. c (III) Изображение под микроскопом осоленного участка (масштабная линейка 200 мкм), где белая окраска является результатом естественного цвета уплотненных измельченных волокон во взаимосвязанной пористой структуре. Кроме того, номинальная ширина стекловолокна, обозначенная на изображении буквой d, соответствует ожидаемым значениям 16 мкм (№ 38 Fiber Glast). c (IV) График плотностей напечатанных стеклянных заготовок ( ρ ) в зависимости от объемной доли стекловолокна, смешанного со смолой, а также от средней плотности материала для печати
3D-печать стеклянных преформ
Помимо термопластов, стекла, в том числе плавленый кварц, имеют важные научные и инженерные приложения в оптике, связи и электронике [43]. Структурированные кремнеземные волокна могут быть полезны во многих областях, например, для окрашивания тканей без красителей для модной одежды, фотонно-кристаллических волокон для оптико-химического обнаружения или одномодовых волокон для телекоммуникаций и жесткой фокусировки света. Эти волокна обычно производятся в два этапа:изготовление преформы и термическое вытягивание преформ в волокно. Хотя процесс вытяжки относительно прост и дешев, изготовление преформы на данном этапе требует индивидуальной обработки, и для каждой конкретной конфигурации преформы должна быть разработана и применена отдельная технология.
На рис. 2b показаны модели автоматизированного проектирования (САПР) преформ из натриево-кальциевого стекла, которые были успешно реализованы с высокой точностью в технологии печати на основе экструзии, аналогично продуктам, описанным компанией Micron3DP [44]. Этот материал имеет многообещающие оптические свойства, особенно в длинноволновых диапазонах, таких как ИК [45], что делает его интересным кандидатом для изготовления волокон с новыми оптическими функциями. Модель преформы, показанная на рис. 2b (I), имитирует структуру волос синего птицееда, аналогичную структуре, представленной в [46], а на рис. 2b (II) поперечное сечение преформы содержит неравновесные геометрические формы и является таким образом, он подвержен изменению формы из-за минимизации поверхностного натяжения. Эти модели были разработаны и реализованы как проверка возможности получения сложных неравновесных поперечных сечений преформ.
Поскольку структура оболочки обеспечивает механическую целостность волокна во время процесса вытяжки и состоит из наиболее вязкого материала, наши усилия до сих пор были сосредоточены на этом компоненте волокна, где мы в конечном итоге стремимся к сохранению геометрии поперечного сечения. преформы. В долгосрочной перспективе мы стремимся разработать методы экструзии нескольких материалов, которые позволят нам монолитно объединить несколько материалов в одной печати. В качестве альтернативы можно заполнить структуру порошкообразными материалами, такими как Si или Ge. Затем заполненную структуру можно спекать для получения преформы. Гуменник и др. описали аналогичный подход [47].
Если есть интерес к производству волокна с натриево-кальциевым стеклом в качестве материала сердцевины, одним из простых подходов будет печать преформы с подвешенным сердечником. Волокна с подвешенной сердцевиной представляют интерес для различных приложений, включая зондирование [48] и терагерцовое наведение с низкими потерями [49], и обычно реализуются из полимеров [49]. В этом типе геометрии волокна сердцевина поддерживается подпорками, которые соединяют ее с внешним слоем. После рисования эти структуры уменьшаются до размеров порядка интересующей длины волны таким образом, что для направленного света создается эффект подвешенного сердечника. Монро и др. сообщили о волокнах с подвешенной сердцевиной из различных материалов, таких как кремнезем и висмутовое стекло [48]. Они также предоставляют серию примеров использования этих волокон для измерения, в частности, для биологического и химического распознавания, подтверждая жизнеспособность этих геометрических форм волокон.
Новые подходы к трехмерной печати стекла на основе стереолитографии с использованием специальных смол были разработаны с использованием фотоотверждаемого нанокомпозита кремнезема [50]. Здесь мы предлагаем метод, при котором преформы из стекловолокна изготавливаются с помощью 3D-печати на основе имеющихся в наличии коммерческих смол, что делает его экономически эффективным и более простым методом изготовления стеклянных деталей, напечатанных на 3D-принтере, с использованием стереолитографии (SLA). Принтер SLA (форма 2 от Formlabs) работает с использованием лазера с длиной волны 405 нм для сшивания смолы через дно чана, поскольку построенная платформа постепенно поднимается слой за слоем.
Чтобы получить оттиски на стекле, мы используем смесь коммерческой прозрачной смолы (Formlabs FLGPCL04 Clear) с волокнами боросиликатного стекла 0,79 мм (1/32 дюйма) (# 38 Fiber Glast) для процесса печати. Это позволяет полностью контролировать процесс печати. Окончательный состав материала для печати и гибкость в достижении желаемых свойств волокна. Стекловолокно диспергировали в прозрачной смоле с помощью магнитной мешалки. Стекло добавляли небольшими порциями и гомогенизировали в течение примерно 3 минут после каждого добавления. принтер был установлен в открытый режим, чтобы можно было использовать нашу специальную смолу. Кубовидные преформы размером 4 × 4 × 50 мм были напечатаны под углом 90 °. После печати детали были погружены в изопропанол на 10 минут для удаления излишков смолы. и пост-отверждение УФ-светом в течение 30 мин при 60 ° C.Застекленные стеклянные заготовки с увеличивающимся объемным соотношением стеклянных волокон, смешанных с печатной смолой (слева направо), показаны на рис. 2c (I).
Затем преформы подвергаются последующей обработке для удаления остаточной смолы и спекания стеклянных частиц, в результате чего получается деталь, полностью состоящая из стекла. Влияние этих процессов на преформу показано на рис. 2c (II), где мы видим преформу после отверждения (слева) и после процесса обжига (справа). В последнем случае можно увидеть черное окрашивание в результате запекания в печи для озоления, в то время как кончик имеет белый цвет после удаления связующего. На рис. 2c (III) показано изображение, полученное под микроскопом преформы перед спеканием, где можно увидеть, что вся смола действительно спеклась из детали, в результате получилась взаимосвязанная структура, образованная только стеклянными волокнами. Необходимо контролировать несколько параметров, например температуру выпечки и профиль нагрева, чтобы контролировать химические реакции и усадку. Термическое удаление связующего было достигнуто с использованием печи для озоления. Полученные коричневые детали спекали в высокотемпературной трубчатой печи. Спекание проводили при температуре 1300 ° С и давлении 5 × 10 -2 . мбар в соответствии с протоколом, описанным в [51]. Фаза выдержки при 800 ° C была установлена для испарения молекулярно-связанной воды и связанных с поверхностью силанольных групп. Спекание в вакууме увеличивает оптическую прозрачность, так как уменьшает задержку воздуха внутри детали из спеченного стекла [52].
После постобработки измеряется объем и вес деталей для определения плотности. Затем это сравнивается со средней плотностью материала для печати, состоящего из смеси отверждаемой смолы и стекловолокна, которая рассчитывается по формуле ρ avg = ρ смола (1 - χ v ) + ρ стекло ( χ v ), где ρ смола =1,17 г / см 3 - плотность отвержденной прозрачной смолы, ρ стекло =2,55 г / см 3 - плотность измельченных стеклянных волокон, а χ v объемная доля стекловолокна, смешанных со смолой.
Результаты показаны в Таблице 2 и графически на Рис. 2c (IV), где мы представляем плотность отпечатанных частей для различных объемных пропорций стекловолокна в смоле по сравнению со средней плотностью материала для печати. Мы видим, что для более низких объемных соотношений стекла, смешанного со смолой, полученные результаты находятся в пределах ожидаемых. Однако при более высоких концентрациях стекла мы видим отклонение от линейного поведения идеальной плотности. Это может быть связано с осаждением во время печати, которое становится значительным при таких объемных соотношениях, что приводит к более высокой концентрации стекла в этих отпечатках. Процесс печати происходит на дне резервуара, где концентрация стекла из-за осаждения постоянно растет во время печати. Он начинается с (и выше) начальной однородной концентрации, которая должна попадать на расчетную кривую.
Из таблицы 2 видно, что при 21,54 об.% Измельченных стеклянных волокон, заполняющих детали, измеренная плотность составила 1,61 г / см 3 . , что означает, что фактическая доля объема составляет 31,88 об.%. В процессе эксперимента был получен образец с фактическим наполнением измельченных стекловолокон 34,78 об.%. Этот результат был недалеко от наполнителя кремнеземом 37,5 об.%, Который был изготовлен Котцем и др. [53], где была разработана специальная смола, в отличие от коммерческой смолы, которую мы используем в этой работе. Будущие направления этой работы включают процедуры термообработки, спекание деталей и изучение механических и оптических свойств полученных деталей.
Когерентный материал-селективный разрыв капилляров и контроль сегрегации допинга
После термической вытяжки преформы получается длинное тонкое волокно с сохраненным поперечным сечением, как показано на рис. 1а (III). В случае волокна с одной или несколькими сердцевинами они могут быть сформированы в осевом направлении посредством пространственно-когерентного, избирательного по материалу процесса разрушения капилляров [26], показанного на рис. 3. В то время как модель Tomotika исследует формирование периодических нестабильностей в бесконечный, равномерно нагретый цилиндр жидкости, с учетом эффектов окружающей жидкости [55], распространение неустойчивостей Рэлея вводит понятие распространения фронта [56]. Хотя в литературе можно найти несколько примеров математического описания капиллярной нестабильности, например, у Liang et al. [57], эти работы в основном посвящены изотермическим режимам, которые в нашем случае неприменимы. Более того, в нашем случае есть дополнительное усложнение распространения теплового градиента и, следовательно, градиента вязкости. Таким образом, он, вероятно, ближе к процессу, основанному на критериях предельной нестабильности, как упоминалось в Powers et al. [56]. Объединив наши расчетные и экспериментальные результаты, мы стремимся создать математическую модель разрыва волокна посредством явления осевого теплового градиента.
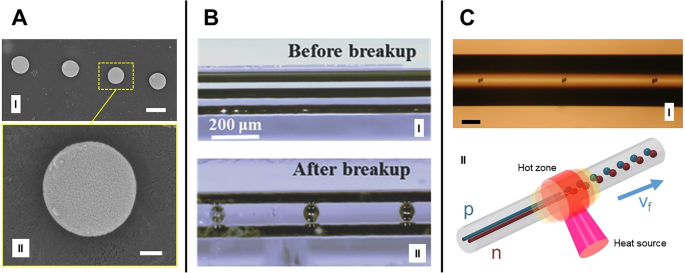
Разрыв капилляров: а (I) Участок волокна, показывающий сферы Si, образованные в результате капиллярного разрушения (шкала 0,5 мкм). а (II) Изображение одной сферы, показывающее качество формы (масштабная шкала 100 нм), из Гуменника и др. [26]. б (I) Пример фотодетекторного устройства металл-полупроводник-металл в одиночном кварцевом волокне до b (I) и после b (II) процесс распада, от Wei et al. [54]. c (I) Распад двужильного волокна на бисферические кластеры (шкала 100 мкм), из Гуменника и др. [26]. c (II) Схематическое изображение процесса, показанного на c (I), с сердечниками p- и n-типа показаны синим и красным соответственно
Современный этап моделирования разрыва капилляров ориентирован на стационарный режим. Нас интересует анализ того, как нестабильности впервые возникают в изначально неподвижном волокне, подверженном тепловому градиенту. Этот процесс аналогичен начальному этапу экспериментов по разрыву капилляров, выполненных Гуменником и др. [26], где кварцевое волокно с Si-сердцевиной толщиной 4 мкм пропускается через горячую зону водородно-кислородного пламени при расходах 0,3 и 0,1 л / мин соответственно. Хотя максимальная температура, достигаемая с помощью этого типа горелки, может достигать 2800 ° C, максимальная температура, которую испытывает волокно, должна быть ниже точки кипения кремнезема, равной 2230 ° C.
Considering that the flame width is between 3 and 3.5 mm and that the fiber has a diameter of about 300 μm, it is easy to understand why it is not feasible to experimentally measure the temperature gradient to which the fiber is exposed. Furthermore, the dynamic nature of the breakup process and the fact that it involves multiple materials with varying emissivities further adds to the complexity of the problem, while the fiber’s high aspect ratio and sharp viscosity ratios render the numerical simulation of the full Navier-Stokes equations computationally challenging.
In our simulations (using COMSOL Multiphysics® 5.3a, with its Microfluidics and Heat Transfer modules) shown in Fig. 4a, we assume an axisymmetric fiber with radius r fiber = 140 μm, composed of a thin Silicon core (r core = 2 μm) enclosed in a Silica cladding. Initial heat-transfer simulations showed that a fiber length of 15 mm is sufficient to ensure that the fiber extremities remain at room temperature, thus avoiding influence from the boundaries to the breakup process. Through the sweep of different parameters such as heat source length and distance to the fiber surface, as well as power, we can observe the changes produced in the breakup behavior, thus collecting information about the temperature gradient. Also of importance are the breakup period and speed, parameters which can be compared to experimental results and used for the refinement of the simulations.
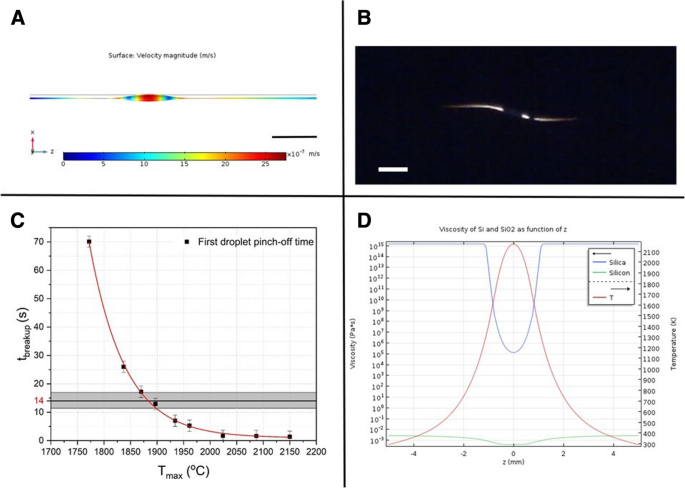
Capillary breakup simulations:a Image of the simulated Si core during the first droplet formation, right before the pinch-off for T max = 1900 °C. Color scale represents surface velocity (scale bar = 50 μm). б Snapshot of fiber breakup experiment recording just after the first droplet pinch-off, indicating a breakup time of 14 ± 3 s (scale bar = 60 μm). c Breakup time t breakup for different values of T max . The exponential dependence of t breakup on T max is evident, a behavior that is expected due to the dependence of t breakup on the core’s viscosity, which in turn depends exponentially on the temperature. The shaded rectangle encompasses the temperature range compatible with this breakup time-scale. г Si core and SiO2 cladding viscosities as a function of axial position, with temperature pro le over-imposed, for T max = 1900 °C
The simulations are performed in two steps:first, the steady-state temperature profile is calculated for different heat source powers, in order to achieve the desired maximum temperature T max . The results are then exported to a time-dependent fluid-flow simulation, where the Navier-Stokes equation is solved with time steps of 0.05 s, from 0 s until the first droplet pinch-off (t breakup ), which is dependent on T max , as can be seen in Fig. 4c, where t breakup is plotted for different values of T max . It is possible to observe that t breakup has an exponential dependence on T max , which is expected since t breakup is proportional to the core’s viscosity, which in turn is exponentially dependent on the temperature.
The relevant parameters used in these simulations are listed in Table 3. Preliminary simulations indicate that the phase transition of the Si core has no significant influence on the steady-state temperature pro le obtained, neither on the subsequent fluid-flow simulations since, in the entire region where the capillary instabilities occur, the temperature is higher than the melting point of Si. Therefore, in order to maintain the model as less computationally intensive, we simulate a core of liquid Si as a first approximation. Moreover, although a fully coupled heat-transfer and fluid-flow simulation is preferable, we consider that the effects of coupling bring second-order corrections to the solution and thus can be neglected at this stage. An image of the simulated core during the first droplet formation, right before the pinch-off, is shown in Fig. 4a, for T max = 1900 °C. A plot of the densities of silica and silicon, as a function of the axial position (in the simulation, the z-axis) for this particular simulation, is presented in Fig. 4d, with the temperature profile over-imposed.
Our results allow us to define the ranges of viscosities for which the time scales for breakup are comparable to those observed experimentally, thus assessing qualitatively the temperature profile imposed on the fiber. Fig. 4b shows a snapshot of a fiber breakup experiment recording just after the first droplet pinch-off, at the frame corresponding to t = 39 s. Since the resolution of the images before this frame is not ideal, judging on the basis of the symmetry of the breakup behavior, it is possible to assess that the pinch-off of the first droplet occurs at t = 35 ± 3 s, which translates to a breakup time after the temperature steady-state regime is achieved, of 14 ± 3 s. The shaded rectangle in Fig. 4c encompasses the temperature range compatible with this breakup time-scale, from which we can infer that the maximum temperature to which the fiber is exposed is 1885 ± 15 °C. With the collection of statistics on the breakup behavior in the future, we aim to develop a procedure for the temperature measurement of the process, which is otherwise unattainable by conventional means [26, 58, 59].
Moreover, segregation-driven control of doping in post-breakup semiconducting particles is attainable, allowing to control an individual device’s internal architecture. It is possible to control the structure of a single sphere, as was demonstrated by Gumennik et al. [47] shown in Fig. 5. When the droplet is exiting the flame, it experiences a thermal gradient:it is colder on the end distant from the flame, and consequently, it is expected to solidify laterally, starting from the colder side. If the sphere is doped with a material that is more soluble in a liquid than in a solid, this dopant will be repelled into the liquid as the solidi cation front propagates, collecting predominantly on the hot side. This effect is shown schematically in Fig. 1c and can be used to synthesize structured particles, composed for example of Ge-rich Si, (as shown in Fig. 5):Starting with 50:50 Si-Ge mixture in the fiber core, after the breakup the sphere will solidify, such that the Ge is extruded into the melt as the solidi cation evolves, leading to anisotropic distribution and resulting in axially oriented Janus particle heterojunctions [47]. This method can be extremely useful in assembling complex fiber-embedded devices such as heterojunctions, as shown in Fig. 1d and e.
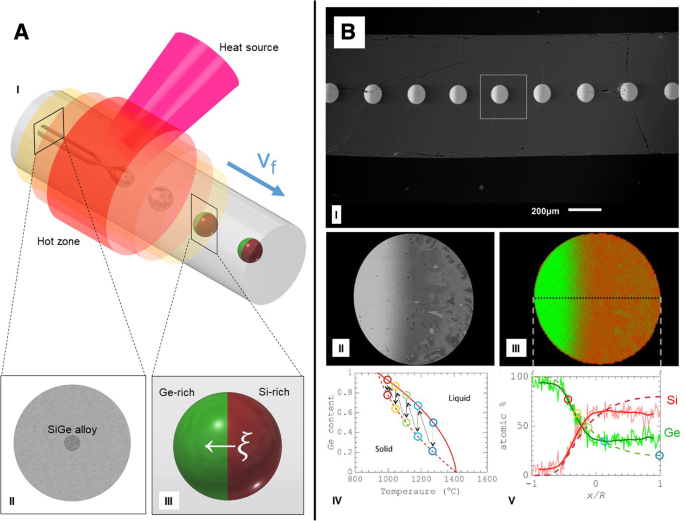
Segregation control of doping:a (I) Schematic illustration of the segregation-driven control of doping in post-breakup semiconducting particles. Details:cross section of a Ge-rich Silicon continuous core in silica fiber a (II) and post-breakup schematic drawing of doping-segregated sphere, or Janus particle, with the Ge-rich side indicated in green a (III). б (I) Scanning Electron Microscope image in backscattered mode of the fiber, polished along its axis, showing an array of Janus particles. б (II) Detail of single Janus particle cross section. б (III) Energy-dispersive X-ray spectroscopy (EDS) map of Janus particle, indicating non-homogeneous distribution of Ge along the cross section, from overlaid maps of Si (in red) and Ge (in green). б (IV) Si-Ge equilibrium phase diagram, liquidus (solid line), and solidus (dashed line). б (V) SiGe atomic content distribution along the dashed line in b (III). (From Gumennik et al. [47])
Biomedical Application
Fiber technology is frequently utilized in various biomedical applications as chemical, biological, and physical sensors. Fiber-embedded sensors have been designed to monitor physical parameters such as stresses, temperature, pressure, and humidity or chemical parameters such as pH level, oxygen concentrations, and carbon dioxide concentrations [60]. Fiber bundles are beneficial to embed multiple sensors together in a single system and in increasing signal reception levels, resulting in higher signal-to-noise ratios. Lightness, flexibility, and unique optical properties are the main characteristics that lead the demand for fiber sensors in biomedical studies. To meet clinical usage requirements, preforms must be fabricated from biocompatible, non-toxic, and chemically inert materials to prevent immune reaction from the patient. Examples of smart fiber development include a neural fiber probe composed of a polymer and metal core composition that enables flexibility and bending stiffness of the neural probe as it provides in vivo optogenetic stimulation and delivers drugs as an input in order to record feedback electrical and physiological output signals [33]. Another example is a fiber integrating microfluidic principles with complex cross-sectional geometries and meter-long microchannels which analyzes cell separation by dielectrophoresis (DEP). Live and dead cells are separated by inertial and dielectrophoretic forces by sheathless, high-throughput microfluidic cell separator which contains conductive materials in the microchannels [14]. The following strategies show a new array of possibilities where smart fibers can be used in biological interfacing.
Consider an artificial gut that can serve as a bioactivity testing platform at the microscale and at the macroscale. With today’s progress in tissue engineering, a variety of functionalities can be integrated in bioink-coated fibers co-extruded using a bioprinter for tissue fabrication, as shown in Fig. 6(I). Traditionally, bioprinting research aims at creating tissue grafts for regenerative medical practice and does so by carefully designing the hydrogel (Fig. 6(II)) with the appropriate nutrition and signaling molecules for the type of cells required based on the application (Fig. 6(III)). Tissue engineering is very challenging to study as the whole biology of the system completely changes microseconds after the experiment has been launched. Monitoring and regularly tuning a tissue’s maturation remains very complex.
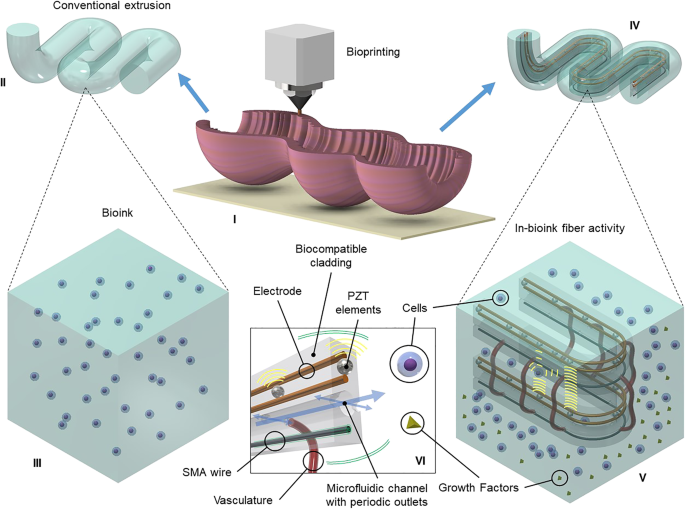
Biological interfacing. (I) Three-dimensional bioprinting of a tissue. (II) Standard microextrusion of bioink. (III) Conventional bioink with cells suspended in hydrogel. (IV) Novel coaxial microextrusion of biointerfacing fiber coated in bioink. (V) Close-up view of fiber where biointerfacing occurs:epithelial cells and vascular epithelial growth factors are excreted from different microchannels and result in cellular self-assembled vasculature between two orifices; piezoelectric elements measure surrounding cell density by ultrasound; and shape memory alloy wires provide peristaltic motion in the tissue. (VI) Visualization of biointerfacing fiber and its components
We propose here a solution by introducing smart fibers in the design (Fig. 6(IV)) to provide a better understanding of the climate and environmental growth. The embedded fiber holds multiple functionalities (Fig. 6(VI)) such as inducing vasculogenesis, ultrasonic imaging, peristaltic movement, and microfluidic flow. Control of the microenvironment takes place via the fiber hooked to syringe pumps and wired to an analytical software. The features of this application (Fig. 6(V)), including pilot experimental data, are detailed in the next subsections.
The Extracellular Matrix and Vasculature
Tissue engineering is widely explored with the increase of artificial tissue needs [61, 62], and the ability to bioprint realistic tissue has an important role to play in tomorrow’s drug and treatment development [63, 64]. One of the biggest challenges is the design of the extracellular matrix (ECM), composed of proteins, growth factors, and other biomolecules, that guide the cell’s contribution to the tissue [65]. Naturally, the ECM gives purpose and structure to the cells, and its extraction typically works by decellularizing tissue and recycling or reusing the ECM for a new cellular construct. The ECM comes in the form of solvents, hydrogels, biopolymers, bioceramics, aerogels, or foams to provide biodegradable or resorbable structure to the tissue [66]. Due to tissue engineering’s high complexity in defining the specifics of the biosystem—mechanical properties, scaffold dissolvability or absorption rates, initial cell types, nutrition, density and ratios, growth factors introduction, and its resulting bioactivity and tissue self-assembly—it is vital to assess the behavior of different types of naturally produced ECM or artificially developed biomaterials in the presence of interacting cells. Moreover, viable tissue requires an organized vascular system that supplies nutrition and oxygen to the tissue for the health and growth of cells. Vascularization provides the natural microfluidic feed of biochemicals to initiate proliferation, specialization, interactions, and motion. The vascular network is formed by vasculogenesis, arteriogenesis, and angiogenesis. Vasculogenesis develops its network through the differentiation and division of endothelial stem cell [67]. Angiogenesis forms new sprouts from existing vessels that are formed in the early embryonic vasculogenesis stage [68].
In-Fiber Microfluidic Feed
Microfluidic conduits with periodic microchannels for content delivery can be used to weave microfluids to specific locations in tissue constructs. The liquefaction front at the boundary of the hot zone defines the droplets’ pinch-off location as described previously. Multiple cores can therefore be broken up in a spatially coherent manner. For example, a silica fiber including a platinum and a silicon core can become a fiber tube with multiple outlets, by inducing the silicon core into an array of spheres and then thinning the fiber using hydrogen fluoride, etching the silicon spheres with potassium hydroxide and etching the platinum core with regal water. An example of the result is shown in Fig. 6(V). The flexibility of fibers allows the microfluidic feed to be integrated in multiple ways in tissue construct. In Fig. 6(IV), the microfluidic channels are used to provide the necessary cell type and growth factors to initiate vascularization and angiogenesis as the tissue reaches maturity.
Biomaterial and Biochemical Testing
In parallel to fiber development, a new testing platform (Fig. 7a (I)) was designed to analyze vascularization and cell-to-cell interactions in the presence of growth factors (Fig. 7a (II)). The platforms were printed in high resolution at an orientation of 30 from biocompatible resin by stereolithography (Formlabs’ Form 2 and Dental LT Clear resin). The print result, shown in Fig. 7a (III), was assembled with two glass capillary tubes with outer diameters of 1.8 mm and 1.0 mm where biological agents are fed. Initial trials will assess diffusion parameters of biochemicals and the growth of cellular colonies in various biocompatible materials. These platforms are designed to be single-use. In 2 h, 24 testing wells can be printed at a relatively low cost. The distance between each capillary outlet of two parallel fibers can be adjusted between 100 and 400 m to investigate the optimum vasculogenesis range that is accepted around 200 m [67]. The medium of interaction in the well’s chamber will first host commercial bioinks (Cellink, USA), one containing sodium alginate and nanofibrillar cellulose and the other containing gelatin methacryloyl, before developing our own in-house biomaterials. The glass capillary tubes shown in Fig. 7a (I) will eventually be replaced by the microfluidic fiber shown in Fig. 6a (V) which will be discussed in the next section.
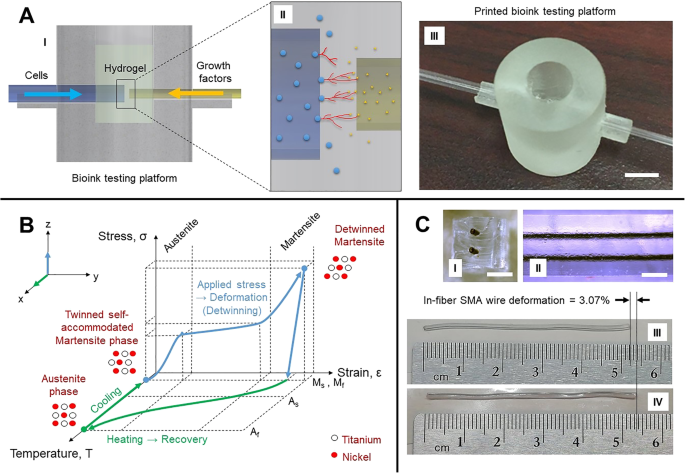
Pilot experiments for biointerfacing:a (I) Cross section of biotesting well showing fluidic feed. а (II) Example of the interaction of epithelial cells (blue circles on the left) with vascular endothelial growth factors (yellow dots on the right) resulting in vasculogenesis excreted by the cells (red lines in the center). а (III) Printed testing platform in biocompatible resin (scale bar = 5 mm). б Temperature-stress-strain graph of the shape memory effect. c (I) Cross section of in-fiber SMA wires (scale bar = 1 mm). c (II) Side view of in-fiber SMA wires (scale bar = 1 mm). c (III) 5.2-mm segment of an in-fiber SMA wire in contraction after being heated at 80 °C. c (IV) 5.36-mm segment of extended in-fiber SMA wire at room temperature
Peristaltic Motion
Shape memory alloy (SMA) wires are lightweight, non-corrosive, and cost-efficient actuating materials for refined applications in a variety of applications such as prosthetic biomimicry [69], self-expandable surgical implants [70], and aerospace engineering [71].
SMAs are metal compounds known for their shape memory effect and pseudoelasticity. Although such properties are typically found in nickel-titanium, these properties can be found in a range of different other metal alloys. Figure 7(b) shows the shape memory effect in terms of temperature, stress, and strain. As shown, at low temperatures, the SMA in its martensite solid state can be deformed by mechanical force, and when thermally induced, goes through a non-diffusive molecular reordering, converting to an austenite solid state. When cooled, the material will return to its initial martensite form, hence the shape memory effect. This thermal cycle is defined by four temperatures, the starting and finishing martensite and austenite temperatures (M s, M f , A s , and A f ), which specifies the start and end of transition periods between states. When the SMA is deformed in as martensite, the molecular de-ordering is defined as detwinning, and it allows the material to experience elongation, which is particularly useful for actuation applications. Essentially, the shape memory effect cycle can occur hundreds of times for an average elongation of 6% and contraction [72], hence its nickname “muscle wire” for its close similarity to muscular myofibrils.
This unique characteristic was first reported by Alden Greninger and Victor Mooradian in 1938 [73], can also be triggered by magnetic field energy [74], namely ferromagnetic shape memory alloys (FSMA), and can be found in polymers (SMP) as well [75]. Today, SMA’s mechanical fatigue and fracture, elasticity, and thermodynamics have been characterized well experimentally [76] and mathematically [77], and its behavior has been modeled [78].
Although the shape memory effect allows for nice contraction behavior of a material, for appropriate robotic applications, the motion needs to be reversable. Typically, an SMA is set in tandem with an opposite mechanism, such as springs, electric drives, elastic bands, or simply another SMA wire. Furthermore, the assembly changes whether it is a linear or rotatory actuation and if the opposing contractions of the actuation are equal. Although wires are thin and weak alone, they can be bundled together to reach the desired force and keep its shape memory effect response time. SMA wires can also be coiled around a capstan to provide greater elongation over shorter distances. Various strategies have been reviewed and chosen for specific applications [79]. The thermal induction is typically best controlled by powering the SMA wire and varying the input current of the order of hundreds of milliamperes. Cooling can be done naturally or by including heat sinks and ventilation.
Fiber drawing technology allows us to play on different material characteristics and to provide to an SMA wire an elastic coating that helps preserve the disorder state of the SMA fiber. As shown in Fig. 7c (I) and c (II), a fiber can be drawn with multiple embedded SMA wires. Styrene-ethylene-butylene-styrene (SEBS) was chosen as the surrounding structure to the SMA wires. SEBS is a copolymer elastomer that can withstand the drawing temperature of 80 °C. While preliminary results show that the actuation can work but with lower efficiency than bare SMA wires, the back-and-forth motion through heating (Fig. 7c (III)) and cooling (Fig. 7c (IV)) cycles is observed for a deformation of approximately 3.07%. More research is required to optimize the setup, but this early stage of experimentation in-fiber SMA actuation shows promising outlooks. The wires were physically pulled and heated using a hot plate to prove the concept. Heating by current would allow speeding up the shape memory effect and controlling better the heat’s diffusion through the fiber. The 5.35-mm wire was measured to have a diameter of 0.11 mm and a resistance of 18.2 was recorded across the fiber segment. To provide a frame of reference, according to SMA wire manufacturers (Dynalloy, Inc.), a 0.1-mm-thick wire made of nickel and titanium requires approximately 200 mA of current for a 1 s contraction. Controlling each wire individually would allow for directional movement, and adding more SMA wires to the design would allow multi-directional motion and greater contraction strength. Moreover, if ferromagnetic SMA wires were used, the control of the motion could become locally controllable via tuning of the interacting magnetic field. Additionally, the FAMES Lab’s drawing tower having the ability to rotate a preform as it is drawing into a fiber enables the possibility to manufacture spring-like structures of SMA wires in the fiber which allows for greater deformation, similar to commercially available SMA springs. Clearly, varieties of strategies are enabled with in-fiber SMA wires.
Biosensing
Biosensors are developed in a wide variety of ways. They can be designed label-based or label-free to detect specific expressions from biological elements such as cells, bacteria, hormones, proteins, DNA, and more [80, 81], from sampling blood, urine, saliva, sweat, or tears. Psychophysiological conditions can be observed from real-time biofeedback such as blood pressure, electrodermal activity, skin conductance, respiration and heart rates, and more [82, 83]. Bioimaging has been done by optical imaging, ultrasound, magnetic resonance frequency, computed tomography, near-infrared spectroscopy, quantum dot probing, and by many more techniques [84].
In optical fiber research, previous biosensing fibers have been fabricated relying on silicon photonic crystal detection of biological radiation [85]. Photonic crystal technology has been used before to monitor in label-free real-time cellular morphology and survival [86]. Such progress in biophotonics has led to hollow-core microstructured fibers visible under magnetic resonance imaging (MRI) [87]. The hollow core allows the propagation of the optical radiations along the fiber over very long distances. The geometry of the hollow fibers varies to tune the photonic bandgaps and dispersion of different detected wavelengths. The inner walls of these hollow tubes are coated with oppositely charged polyelectrolytes and magnetite nanoparticles which are used as contrast agents for MRI. Such design therefore enables new biomedical precision diagnosis opportunities, for example, in the observations of neural activity in vivo [87, 88].
Ultrasonography technology enables us to observe density of cells in liquid or gel in a non-intrusive manner [89, 90]. Ultrasonic probes typically function according to the piezoelectric effect (generation of electricity from applied stress), which was first discovered by Jacques and Pierre Curie in 1880 [91]. The inverse piezoelectric effect (deformation of a piezoelectric crystal from an applied electric field) was induced mathematically by Gabriel Lippmann in 1881 [92] and later in 1916, Chilowsky Constantin and Paul Langevin developed ultrasonic submarine detection for World War I military applications [93]. Thereon, sonar applications have been diverse, such as underwater imaging and fish-finding [94, 95] and energy harvesting [96, 97].
The piezoelectric elements convert electrical energy to and from mechanical energy and transmit sound waves between each other. All frequency and bandwidth parameters require precise regulation, and good energy transmission requires good acoustic and damping matching impedances. Two fibers with integrated piezoelectric elements, designed as pulsing emitter and receiver, can create an ultrasonic waveguide between each other to measure density over the wave’s trajectory. This fiber enables us to sense the microstructures of the environment as the tissue reaches maturation. The piezoelectric elements are created by capillary breakup from a PZT core for example. PZT elements have an acoustic impedance of 33.7 × 10 6 kg/m 2 s with a resonance frequency below 25 MHz. The produced spheres are lined with conductive electrodes to a transducer. This setup provides the feedback in a control system to better adjust microfluidic and motion feed. The in-fiber ultrasonic imaging of the microenvironment clearly helps understand how the tissue environment behaves over time.
Выводы
We have formulated the concept of VLSI for fibers (VLSI-Fi)—a combination of liquid-phase processing techniques in microelectronic materials forming a toolbox for fabrication of high-performance devices and systems in fibers and textiles. Our experimental work focuses on a set of demonstrations substantiating our control over narrower aspects of VLSI-Fi, such as preform 3D printing, in-fiber circuit assembly by material-selective spatially coherent capillary instability, and segregation-driven doping control at the level of an individual fiber-embedded device. We envision that VLSI-Fi will enable realization of product in multiple technological areas, one of which is fabrication of active biomimetic scaffolds for engineered tissues with realistic microstructures.
Доступность данных и материалов
Not applicable.
Сокращения
- BJT:
-
Bipolar junction transistor
- CAD:
-
Computer-aided design
- CMOS:
-
Complementary metal-oxide-semiconductor
- DEP:
-
Dielectrophoresis
- ECM:
-
Extracellular matrix
- EDS:
-
Energy-dispersive X-ray spectroscopy
- FAMES Lab:
-
Fibers and Additive Manufacturing Enabled Systems Laboratory
- FOS:
-
Fiber optic sensors
- FSMA:
-
Ferromagnetic shape memory alloys
- HPCVD:
-
High-pressure chemical vapor deposition
- IoT:
-
Internet of Things
- MOF:
-
Microstructured optical fibers
- MOSFET:
-
Metal-oxide-semiconductor field-effect transistor
- MRI:
-
Magnetic resonance imaging
- PCF:
-
Photonic crystal fiber
- PZT:
-
Lead zirconate titanate
- SEBS:
-
Styrene-ethylene-butylene-styrene
- SLA:
-
Stereolithography
- SMA:
-
Shape memory alloy
- SMP:
-
Shape memory polymers
- TPC:
-
Trans-Pacific undersea cable
- UV:
-
Ультрафиолет
- VLSI:
-
Very large-scale integration
- VLSI-Fi:
-
Very large-scale integration for fibers
Наноматериалы
- Оптимизация цифровой трансформации в производстве товаров народного потребления
- GE открывает интеллектуальный завод в Алабаме
- Развитие цифровых технологий в интеллектуальном производстве
- Производственные задачи, управляемые данными
- Что такое цифровая трансформация в производстве?
- Использование цифровых технологий в производстве
- Цифровая фабрика:интеллектуальное производство стимулирует Индустрию 4.0
- GE Digital:трансформация производства с помощью Smart MES
- Умное производство Autodesk
- Цифровое производство:отрасль завтрашнего дня