Соединение композитов со сталью
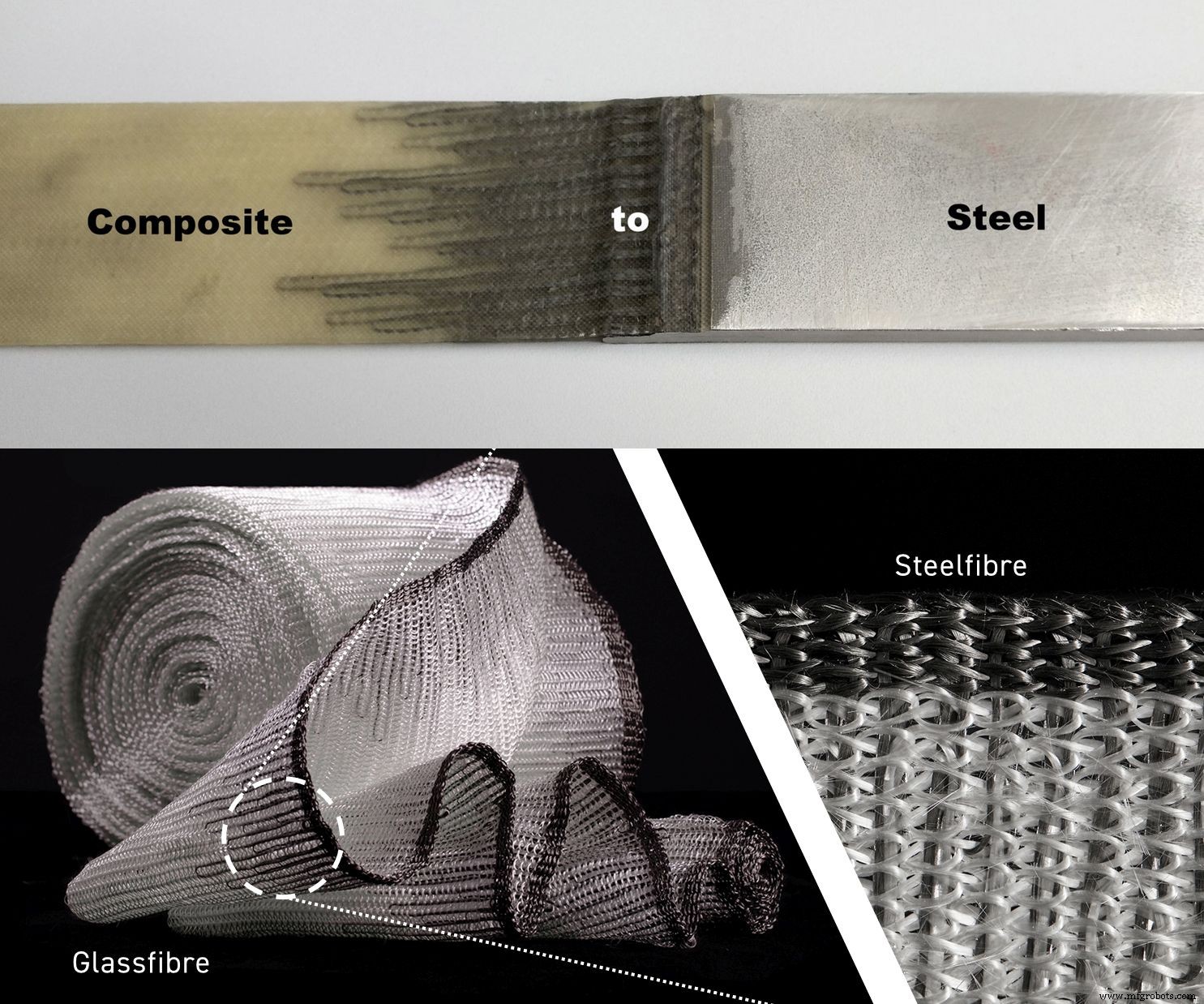
Этот блог является дополнением к моей тематической статье за декабрь 2019 г. «Устранение препятствий для облегчения кораблей с помощью композитов», в которой я поделился некоторыми другими подробностями и визуальными эффектами.
HYCONNECT GmbH (Гамбург, Германия) - это стартап, основанный доктором Ларсом Молтером, военно-морским архитектором и 10-летним ветераном Центра морских технологий (CMT, Гамбург, Германия), научно-исследовательского центра морской индустрии Германии. «У немецких компаний, строящих мегаяхты и круизные суда, одна и та же проблема», - говорит Молтер. «Их клиенты хотят добавить больше оборудования, другую площадку, большую изоляцию от шума и температуры или новые конструктивные особенности, такие как изогнутые формы и встроенное освещение. Даже если они смогут сделать эти конструкции из алюминия или стали, это будет очень затратно по времени и средствам ».
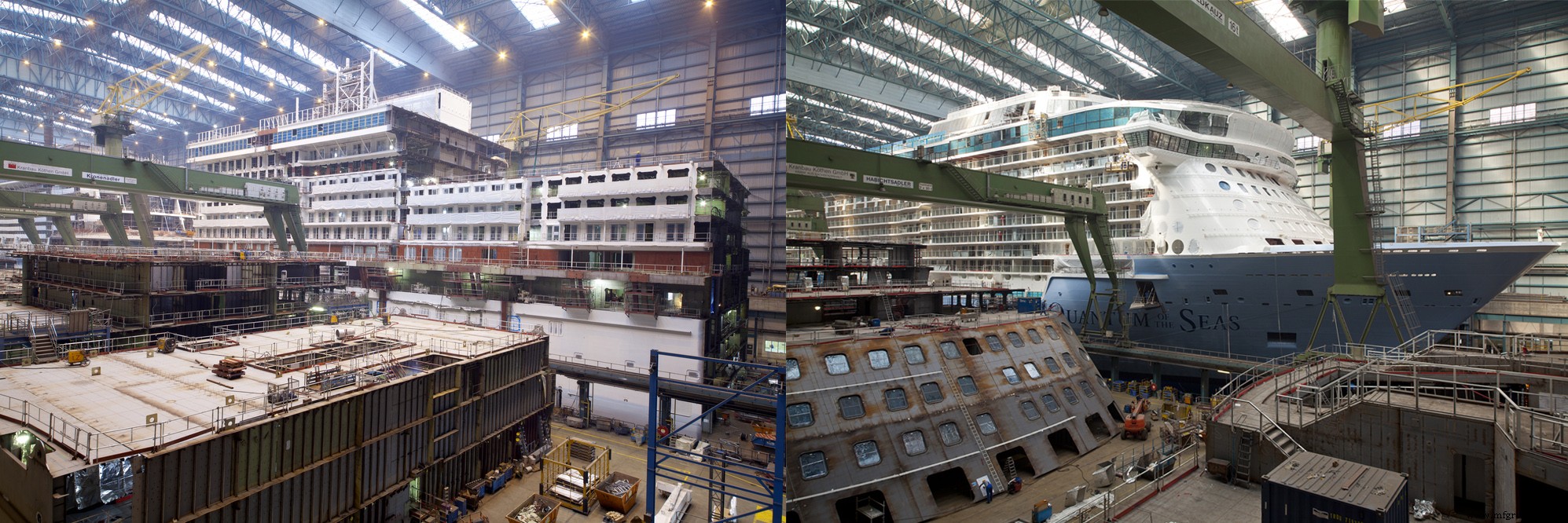
Как показано здесь, корабли обычно строятся из блоков сварных стальных компонентов для более быстрой сборки. Система стыков FAUSST позволяет вваривать большие композитные стеновые панели или другие конструкции в эти стальные каркасы, предлагая легкую конструкцию с использованием современных методов производства судов. ИСТОЧНИК | Мейер Верфт
Проблемы с клеевым соединением в гибридных конструкциях
Молтер и многие другие могут видеть преимущества, которые композиты могут предоставить для кораблей, но в настоящее время корабли строятся из стали. Многие работают над созданием судов, полностью состоящих из композитных материалов, но в то же время существует значительная возможность снизить вес корабля и выбросы с помощью различных компонентов из композитных материалов. Однако одна проблема заключается в том, как соединить их со стальным каркасом корабля. «Мы рассмотрели склеивание, - объясняет он, - но не существует стандартизированной конструкции стыка, которую можно было бы использовать на всех судах, и нет общих правил о том, как применять склеивание в СОЛАС».
Правила безопасности жизни на море (SOLAS), изданные Международной морской организацией (IMO, Лондон, Великобритания), требовали, чтобы коммерческие суда были построены из стали до 2002 года, когда MSC / Circ. Было выпущено 1002, разрешающие альтернативные конструкции. Однако эти альтернативы требуют проведения анализа рисков, показывающего, что альтернативный дизайн и конструкция эквивалентны стали - процесс, который является долгим, дорогим и индивидуальным для каждого построенного судна.
«Мы спросили DNV GL, что они одобрили бы для соединений из разнородных материалов», - говорит Молтер. «Они сказали, что первичная структура обычно требует механического крепления; чистое соединение было бы нелегко сертифицировать без дублирующих крепежных элементов ». Эти проблемы, связанные с индивидуальной сертификацией и требованиями регулирующих органов для резервных крепежных элементов по сравнению с чисто связанными первичными структурами, одинаково присутствуют в коммерческих самолетах. «Кроме того, со склеиванием вы должны контролировать окружающую среду и процесс», - говорит он, отмечая, что это сложно в условиях сварки и резки, которые обычно преобладают в строительстве верфей.
Соединения FAUSST
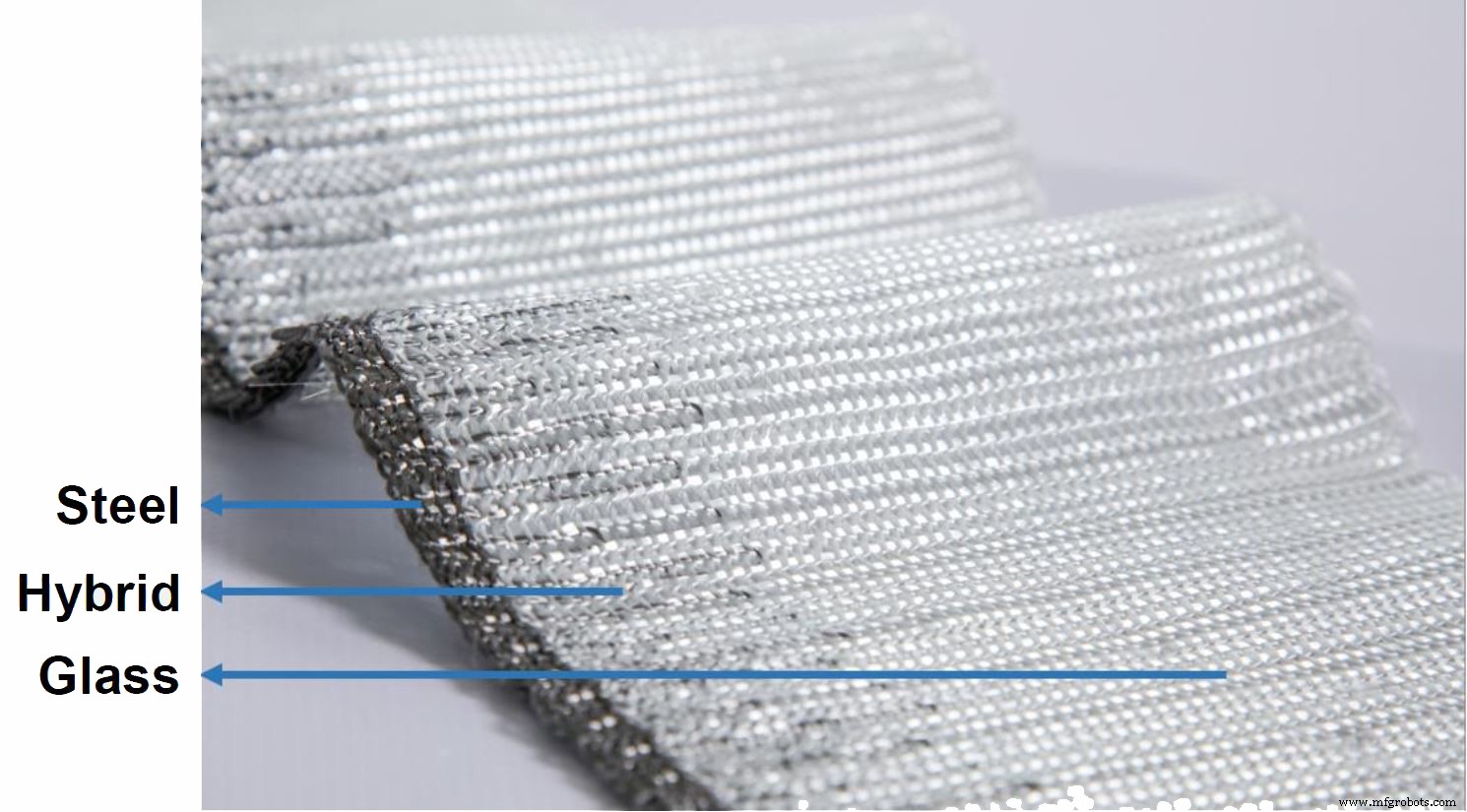
Гибридная ткань FAUSST, сочетающая стекловолокно и стальное волокно. ИСТОЧНИК | Хайконнет
«Итак, нам нужно было решение без склеивания, но с механическим креплением», - говорит Молтер. «Мы все время задавались вопросом, как соединить волокна с металлом?» CMT ответит, что в финансируемом Германией проекте FAUSST (совместный стандарт волокна и стали), который в сотрудничестве с Fritz Moll Textilwerke (Альтсхаузен, Германия) разработал гибридный трикотажный текстильный материал, в котором 100% стекловолокно превращается в 100% сталь. волокна.
Структура ткани спроектирована так, что стальные и стеклянные волокна изгибаются и перекрываются, что обеспечивает передачу нагрузки за счет трения, а также блокировку в точках пересечения. Эта архитектура также уравновешивает трикотажное полотно для механического сцепления с однонаправленными волокнами для переноса нагрузки через соединение. Ткань производится на вязальной машине с электронным управлением со скоростью до 100 метров / час.
Следующим шагом является прикрепление его к металлическому соединителю, который может быть пластиной или полым профилем. Стальные волокна привариваются к соединителю с помощью контактной сварки швом (прессовая сварка) с большим медным электродным колесом. Молтер объясняет, что это похоже на точечную сварку в автомобилестроении, но адаптировано для получения длинного непрерывного шва. Этот процесс позволяет эффективно производить соединители FAUSST с одним или несколькими слоями ткани с использованием надежного и хорошо известного процесса.
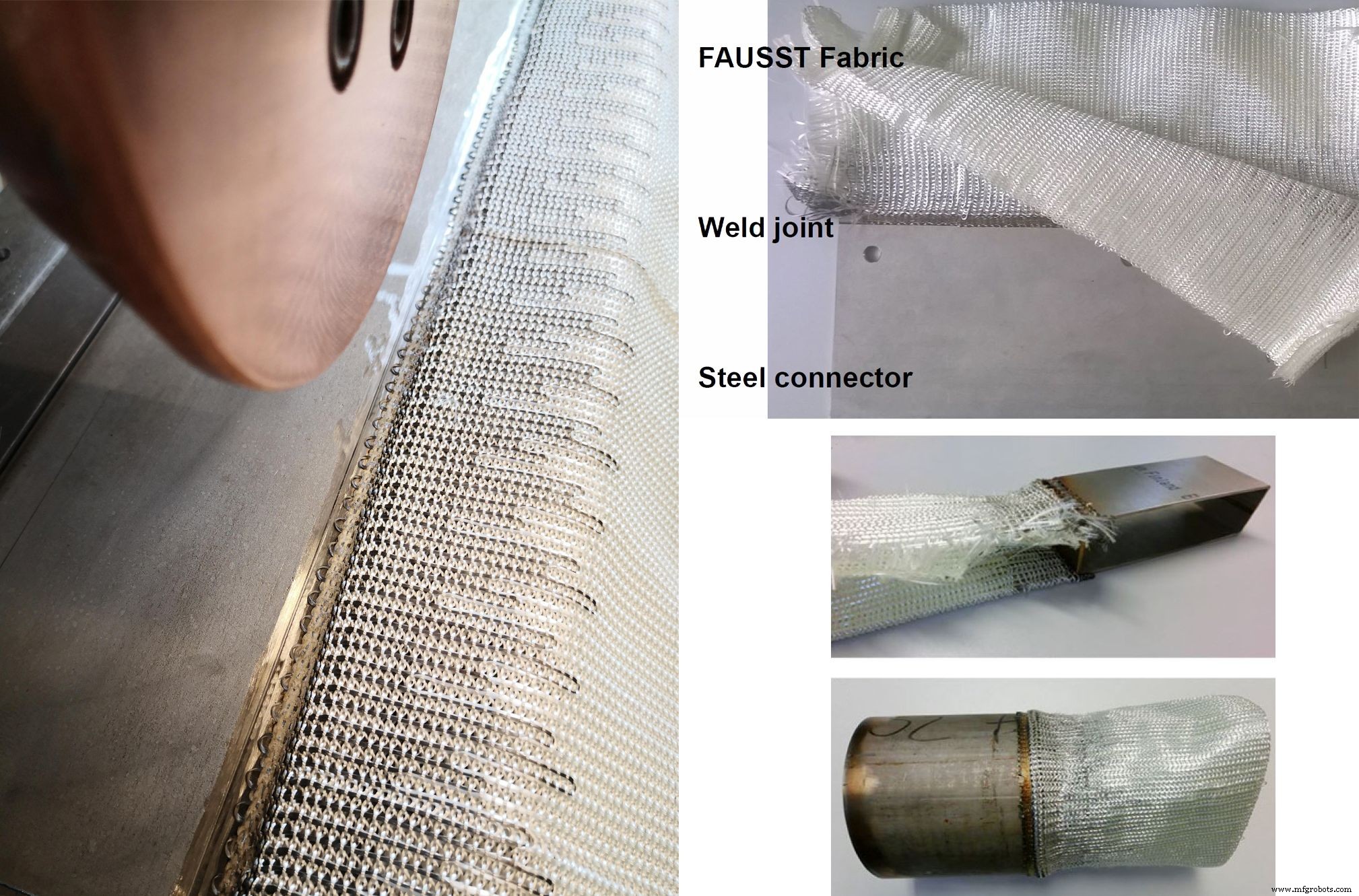
Hyconnect использует шовную сварку для соединения ткани FAUSST со стальными соединителями. ИСТОЧНИК | Hyconnect.
Это то, что продает HYCONNECT:ткань, приваренная к стальному соединителю. «Верфь или ее поставщик композитных конструкций решает использовать нашу систему соединений», - объясняет Молтер. «Они указывают нагрузку на соединение и тип стального соединителя, а затем мы проектируем и производим соединение FAUSST. Это то, что мы доставляем, и они затем вливают это в свои композитные конструкции, и верфь затем приваривает их к стальному каркасу корабля ».
Управление жесткостью и несоответствием КТР
Несоответствие жесткости между стальными и стеклянными волокнами в гибридной ткани FAUSST. Молтер объясняет, что это несколько смягчается способом изготовления ткани, «используя 5-7 слоев, где пряжа переплетена, и мы варьируем, насколько далеко стальные волокна проникают в стекловолоконную ткань. Вам не нужны большие пики при передаче нагрузки. Мы можем изменить жесткость, изменив эти слои и составляющие их волокна, например, процентное содержание и направление стекловолокна и т. Д. » Дополнительные волокна ± 45 ° могут быть добавлены для выдерживания более высоких напряжений сдвига, а также помогают управлять различными коэффициентами теплового расширения (CTE) между стальным соединителем и композитом из стекловолокна. «Мы также можем спроектировать для более высоких нагрузок или особые конструкции путем усиления по всей толщине с помощью тафтинговых волокон», - объясняет Молтер.
Также необходимо устранить несоответствие толщины стального соединителя и армированного волокном пластика (FRP). «Нейтральные оси обоих материалов должны быть выровнены», - говорит Молтер. «Обычно это достигается путем механической обработки края стального соединителя до конуса 30 °, создавая, по сути, коническое соединение для эффективной передачи нагрузки на FRP».
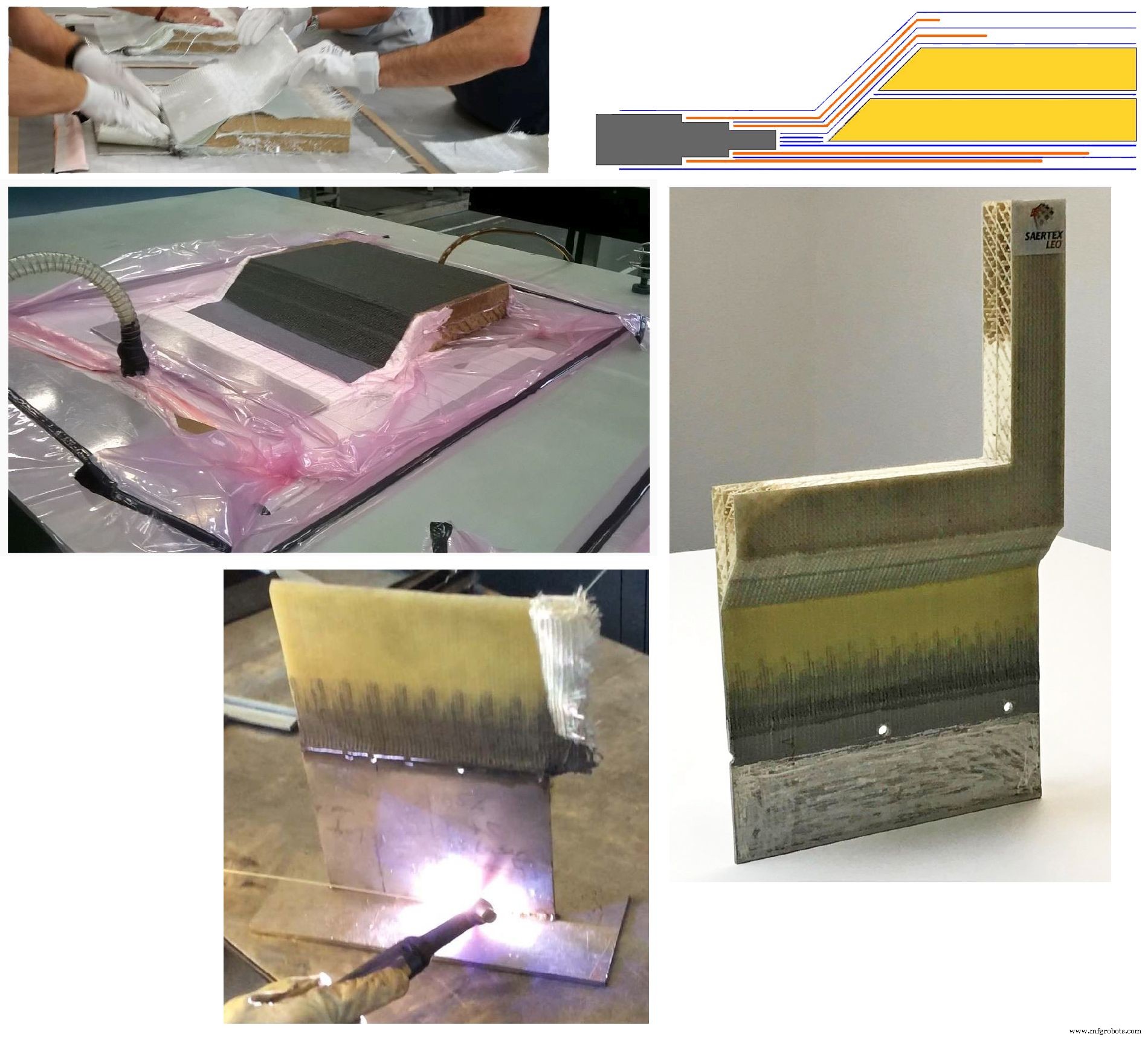
Hyconnect проектирует и производит соединения FAUSST, которые затем вплавляются в композитные конструкции и, наконец, привариваются к стальному каркасу корабля. ИСТОЧНИК | Hyconnect.
Разработка стандартизированной совместной системы
Молтер покинул CMT и в 2018 году основал компанию HYCONNECT, чтобы коммерциализировать совместную технологию FAUSST. Компания работала с различными отраслевыми партнерами и регулирующими органами для проведения испытаний и повторения совместных проектов. Цель состоит в том, чтобы разработать «семейство» совместных продуктов FAUSST. «Несущая способность увеличивается линейно за счет нанесения большего количества слоев ткани FAUSST», - объясняет Молтер. «Таким образом, базовым продуктом может быть четыре слоя FAUSST с приваренной к нему полосой длиной 1 метр, рассчитанной на определенную растягивающую и изгибающую нагрузку. Тогда были бы некоторые продукты, доступные слева, используя два или три слоя для более низкой номинальной нагрузки, и некоторые справа, например, пять или шесть слоев для более высокой номинальной нагрузки. Мы все еще дорабатываем эти детали, но наша цель - стандартизированная, простая в использовании система ».
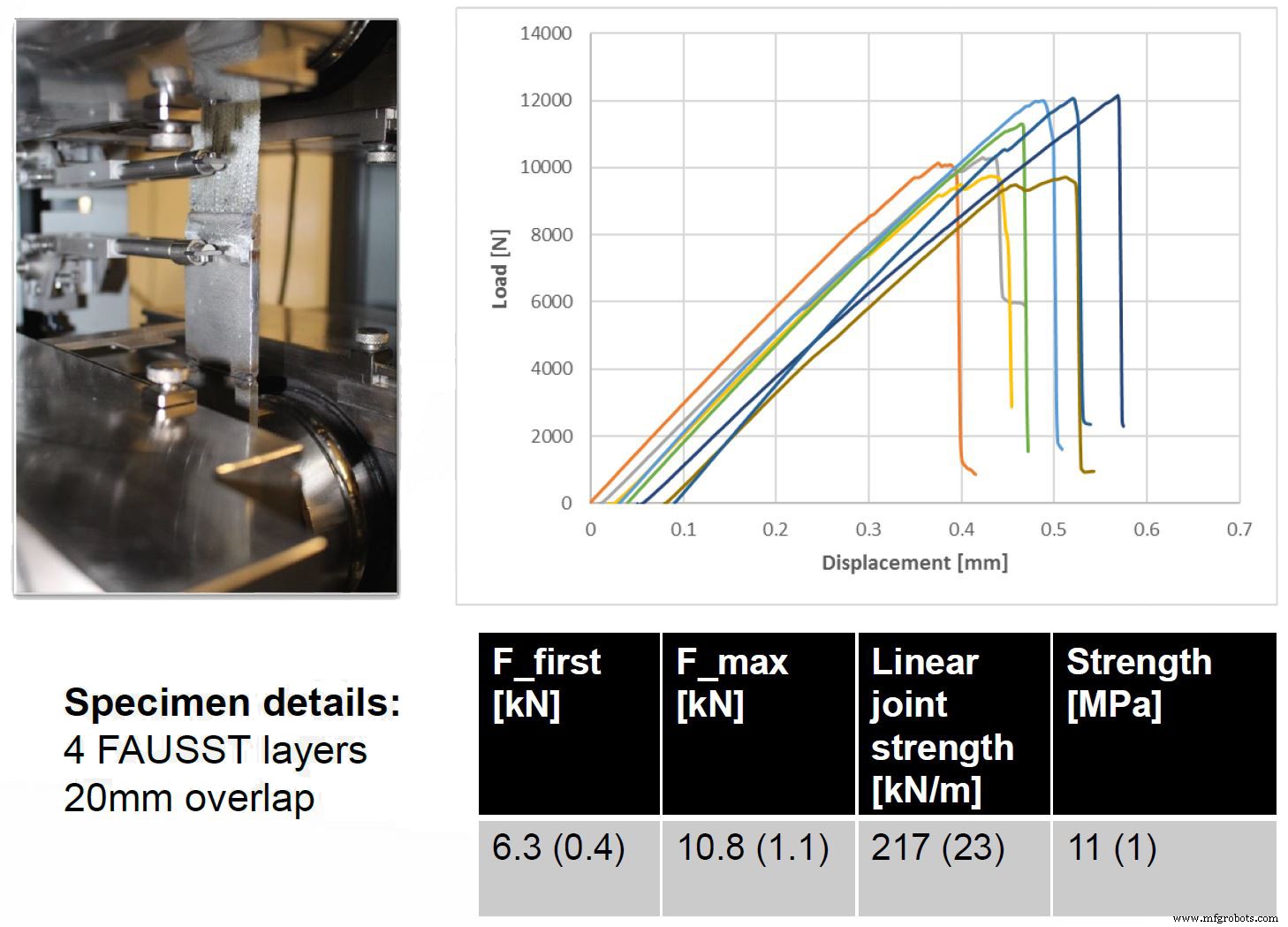
Испытания Hyconnect в соединениях, состоящих из четырех слоев ткани FAUSST, обеспечивают прочность соединения лайнера 217 кН / м. ИСТОЧНИК | Hyconnect.
Механическое определение характеристик швов FAUSST все еще продолжается, но Молтер отмечает, что они могут конкурировать с клеевыми швами. «Они также позволяют проводить 100% -ный контроль сварного шва с помощью ультразвукового или рентгеновского контроля», - добавляет он. Прототипы в настоящее время производятся для избранных клиентов и будут расширены в 2020 году.
Между тем, к HYCONNECT проявили интерес автомобильные компании и производители, заинтересованные в железнодорожных приложениях. «Есть потенциал для использования этой технологии для металлических вставок, и мы также видим возможные применения в строительстве», - говорит Молтер. «Все больше и больше отраслей видят ценность гибридных структур и возможность сокращения времени сборки с использованием предварительно укомплектованных полуфабрикатов».
волокно