Трехмерная намотка нити накала позволяет использовать концепцию сиденья транспортного средства
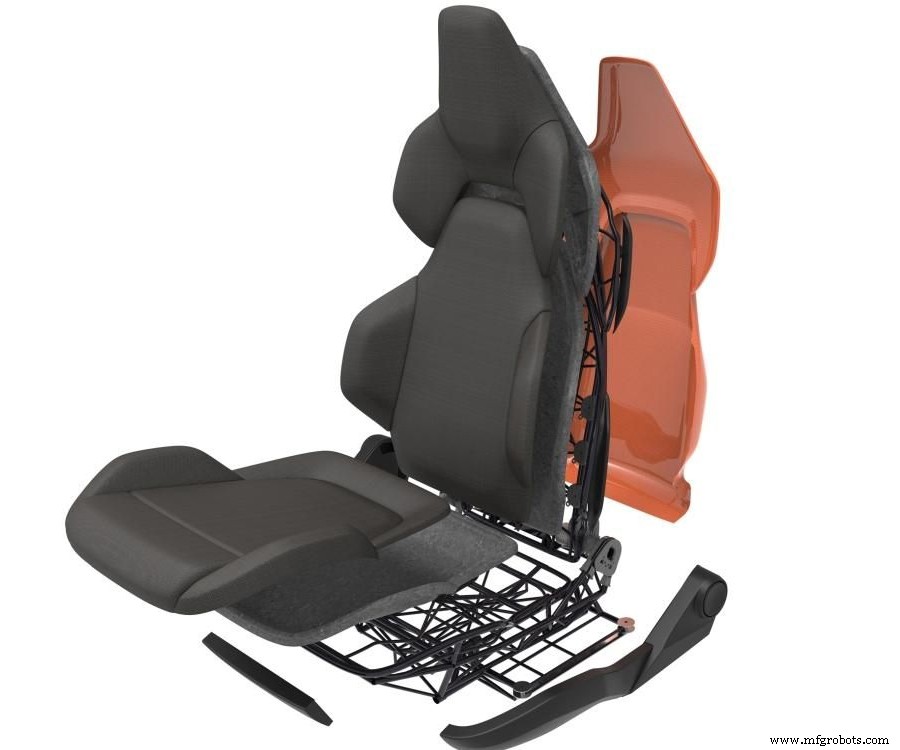
Устойчивое развитие и экологическая ответственность становятся все более распространенными драйверами технологических тенденций в автомобильной промышленности. Транспортные средства с низким энергопотреблением и низким уровнем выбросов стали приоритетом для международного автомобильного сектора, и тенденции к альтернативным транспортным технологиям, таким как электромобильность и городская воздушная мобильность (UAM), набирают обороты. Производители оригинального оборудования обращаются к новым материалам и процессам как к возможностям реализации этих перспективных способов передвижения, но изменения в автомобильном секторе часто происходят медленно. Чтобы новые материалы и процессы были полностью адаптированы, они должны быть не только квалифицированными, но и рентабельными, и они должны обеспечивать возможность крупносерийного производства.
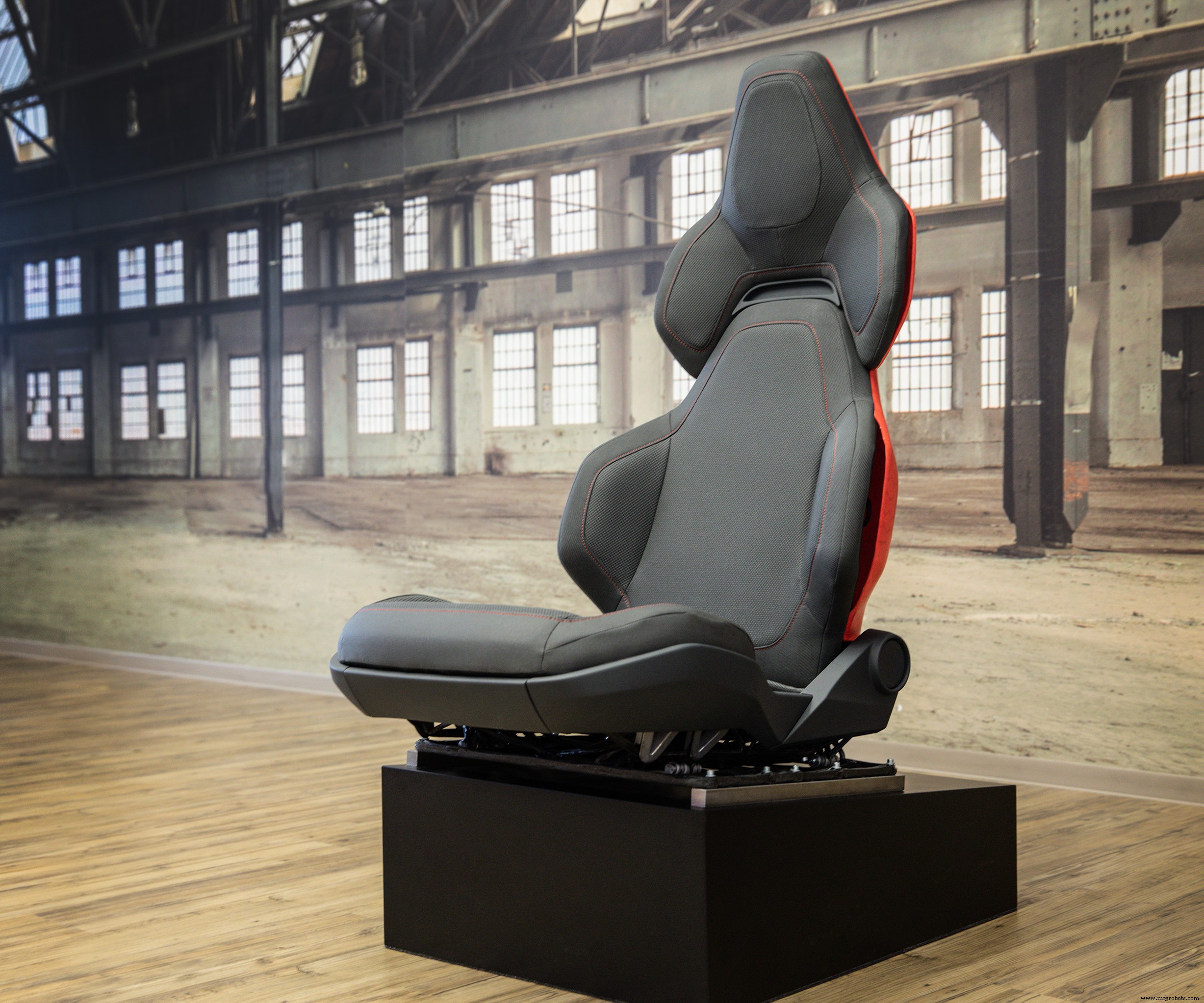
Сверхлегкое сиденье . Концепция кресел Ultra Leichtbausitz (ULBS) была разработана в результате сотрудничества нескольких компаний с использованием комбинации технологий. Источник | csi entwicklungstechnik
Недавно инновационный проект с потенциалом для автомобильного сектора, а также для развивающихся рынков, таких как гиперкары и авиатакси, продемонстрировал, как новые материалы, процессы и технологии, а также тесное сотрудничество между компаниями могут сделать возможным использование транспортных средств следующего поколения. Цель проекта заключалась в том, чтобы полностью переосмыслить автокресло с использованием передовых генеративных технологий и сделать это с использованием только такого количества подходящего материала, которое необходимо в нужном месте - и чтобы быстро дать результат. Получившийся в результате прототип сверхлегкого гибридного автомобильного сиденья из металлокомпозитного материала был разработан от проектирования до производства всего за семь месяцев с помощью подхода к проектированию, основанного на моделировании, гибких методов управления проектами и тесного сотрудничества и системной интеграции между участвующими компаниями.
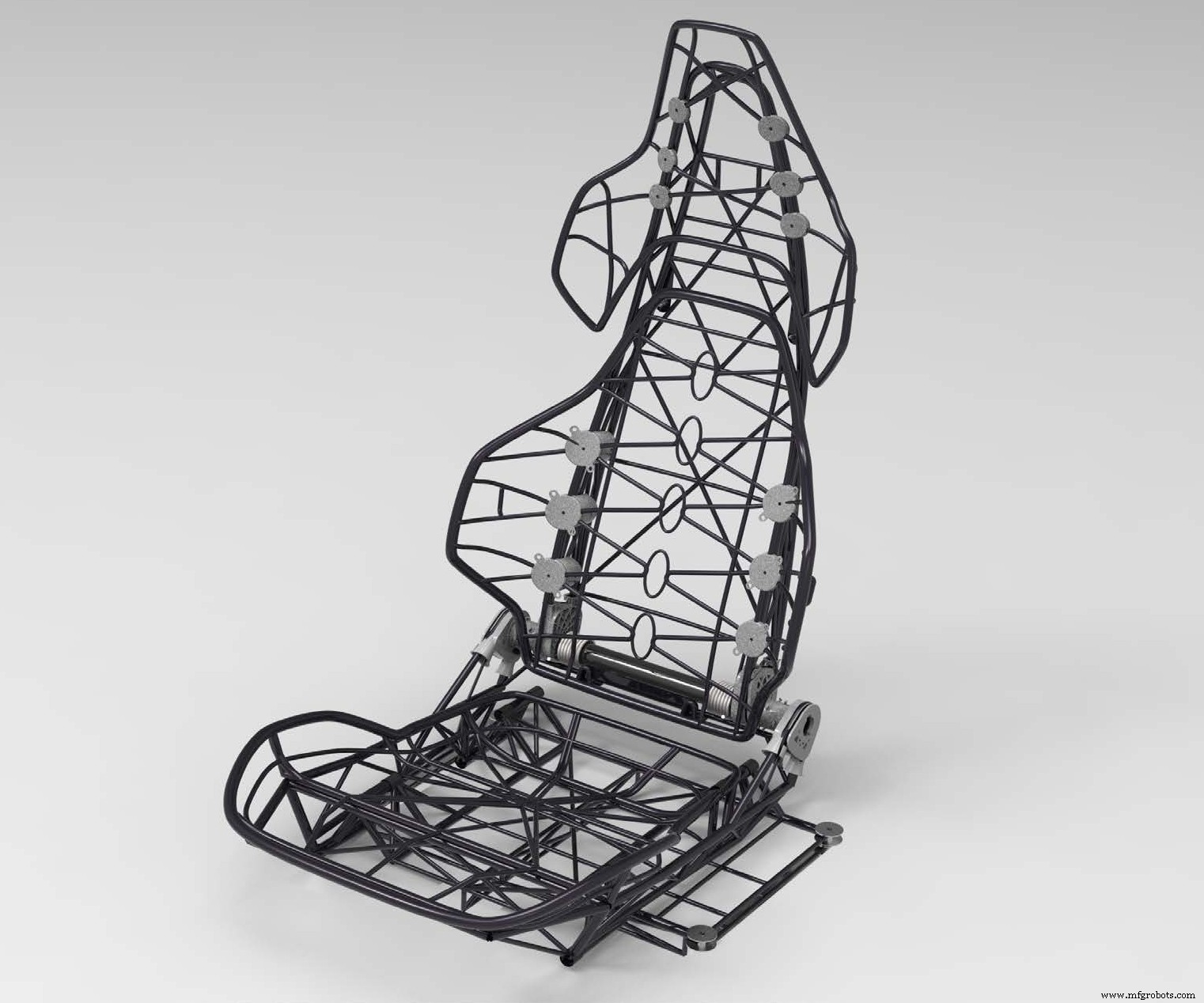
Улучшение сиденья
Технико-экономическое обоснование сверхлегкого сиденья Ultraleichtbausitz (ULBS) было разработано в результате сотрудничества нескольких компаний с использованием комбинации технологий. По словам группы, видение проекта заключалось в «создании концепции сверхлегкого сиденья, выдающейся на рынке с точки зрения оптимизации веса». Компании-инициаторы csi entwicklungstechnik GmbH (CSI, Неккарзульм, Германия), Alba Tooling &Engineering (Форстау, Австрия) и Automotive Management Consulting (AMC, Пенцберг, Германия) разработали концепцию прототипа сиденья в сотрудничестве с Covestro (Леверкузен, Германия), LBK Fertigung (Фридберг, Германия), Роберт Хофманн (Лихтенфельс, Германия) и 3D | CORE (Херфорд, Германия).
Результатом совместного проекта стал прототип сиденья весом чуть более 10 килограммов, которое включает в себя подушку, структурную раму, функциональные вставки и консоль для сидения, которая позволяет устанавливать его на автомобиль. Сиденье на 20% легче, чем аналогичные легкие сиденья, представленные на рынке, многие из которых являются сиденьями послепродажного обслуживания. По словам руководителя проекта ULBS Стефана Херрманна, ответственного за облегченную конструкцию в CSI, в настоящее время на рынке нет конкурирующих кресел весом менее 12 кг.
«Тем не менее, прямое сравнение часто не является прямым сравнением яблок с яблоками, потому что послепродажные сиденья часто не включают в себя консоль для сидения при определении веса», - говорит Херрманн. «Кроме того, комфорт сидения в ULBS намного выше по сравнению с сиденьями с подобный вес. Существующие сиденья часто представляют собой ковшеобразные сиденья, которые еще меньше по весу, но не такие удобные, или традиционные суперспортивные сиденья, которые имеют намного больший вес ».
ULBS использует несколько инновационных технологий, из которых наиболее важную роль играет структура каркаса волоконно-ровницы, основанная на технологическом процессе xFK в 3D. (См. Раздел «Намотка волокна, новое изобретение» для получения дополнительной информации о xFK в 3D и других технологиях намотки волокна.) Фундаментальная важность отмеченной наградами технологии для нанесения бесконечного ровинга волокна заключается в ее свободе дизайна, в моделировании и использовании материалов. оптимальное размещение волокон точно в направлении нагрузки, а также простое, экономичное и безотходное применение волокнистого материала. Для передачи нагрузки в этой каркасной конструкции использовались детали, напечатанные на 3D-принтере. В местах с наибольшими нагрузками, таких как спинка, сиденье использует 3D-печатные конструкции из нержавеющей стали с высокой прочностью и высоким модулем упругости. На менее загруженных участках применяется 3D-печать алюминием.
csi entwicklungstechnik, инжиниринговая компания, специализирующаяся на конструкциях кузова в белом (BIW), а также на интерьере и экстерьере автомобилей с бизнес-направлениями, включая полимеры, армированные углеродным волокном (CFRP) и аддитивное производство, курировала и координировала проект на основе идея инициирована AMC. CSI предоставил дизайн, поверхности, концепцию, моделирование, разработку дизайна и управление проектом.
Херрманн объясняет:«CSI отвечал за рабочие пакеты в области цифровой цепочки процессов - моделирование, инженерное проектирование, проектирование поверхностей, моделирование CAE, моделирование топологии, моделирование валидации и виртуальное подтверждение проекта».
Он подчеркивает, что проект ULBS примечателен не только использованием инновационных материалов и методов производства, но и разработкой сложной детали, включающей новые конструкции компонентов, в короткие семимесячные сроки при тесном сотрудничестве партнеров.
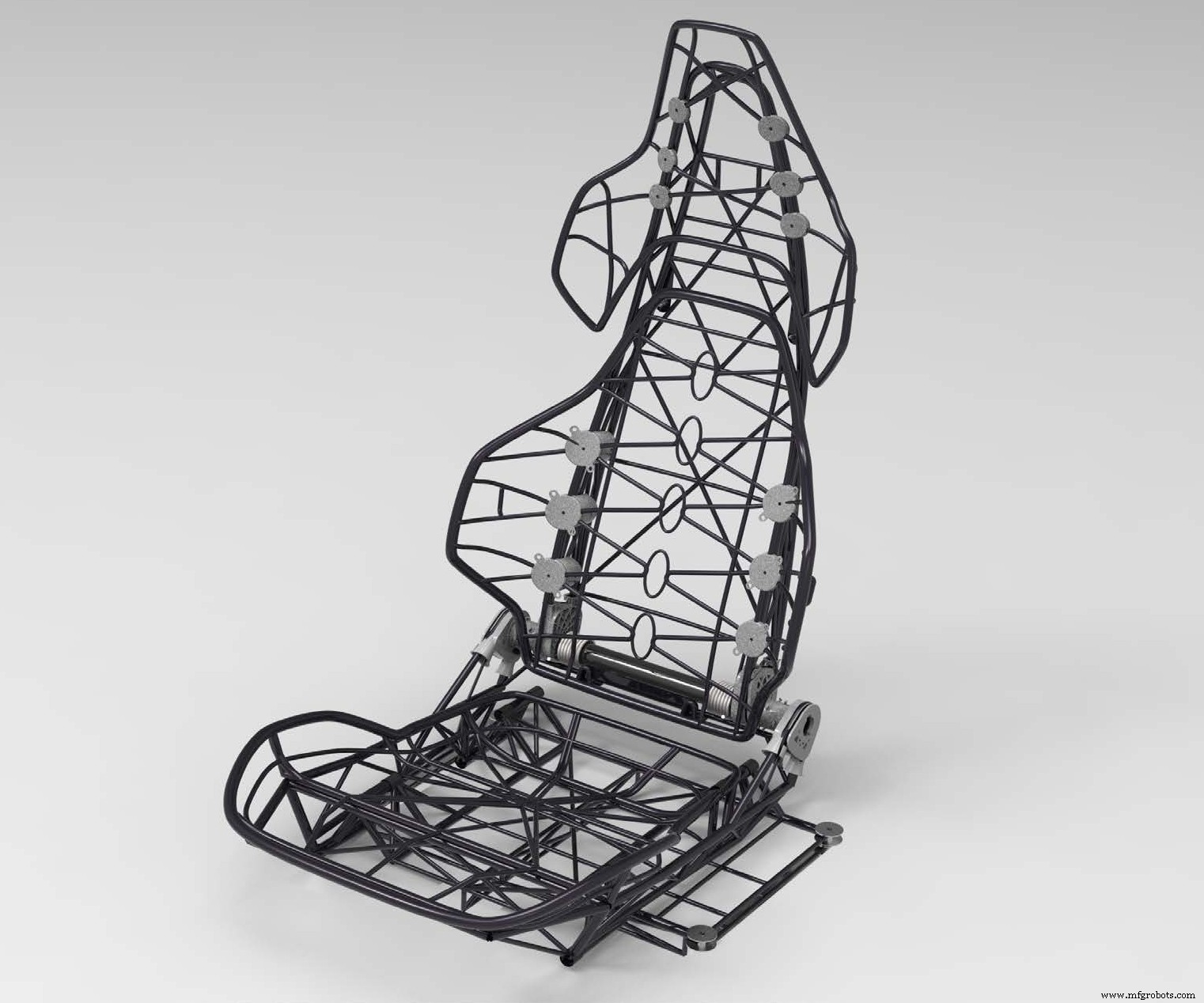
Каркас сиденья, намотанный нитью . Снижение веса в проекте ULBS в значительной степени связано с технологией намотки волокна xFK в 3D, разработанной AMC. Источник | csi entwicklungstechnik
Намотка рамы
В значительной степени снижение веса в проекте ULBS является результатом использования AMC xFK в 3D, очень гибкой, настраиваемой, рентабельной и устойчивой технологии композитных волокон для компонентов намотки.
xFK в 3D уже используется для множества продуктов и приложений для различных отраслей и сегментов рынка. SGL Group Wiesbaden, Германия) представила несколько автомобильных и велосипедных деталей, изготовленных с помощью этой технологии, на международной выставке композитных материалов JEC World 2018. Говорят, что одна из представленных деталей, кольцо велосипедной цепи из углеродного волокна, разработанное AMC, позволяет снизить вес на 70%. по сравнению с алюминиевой версией.
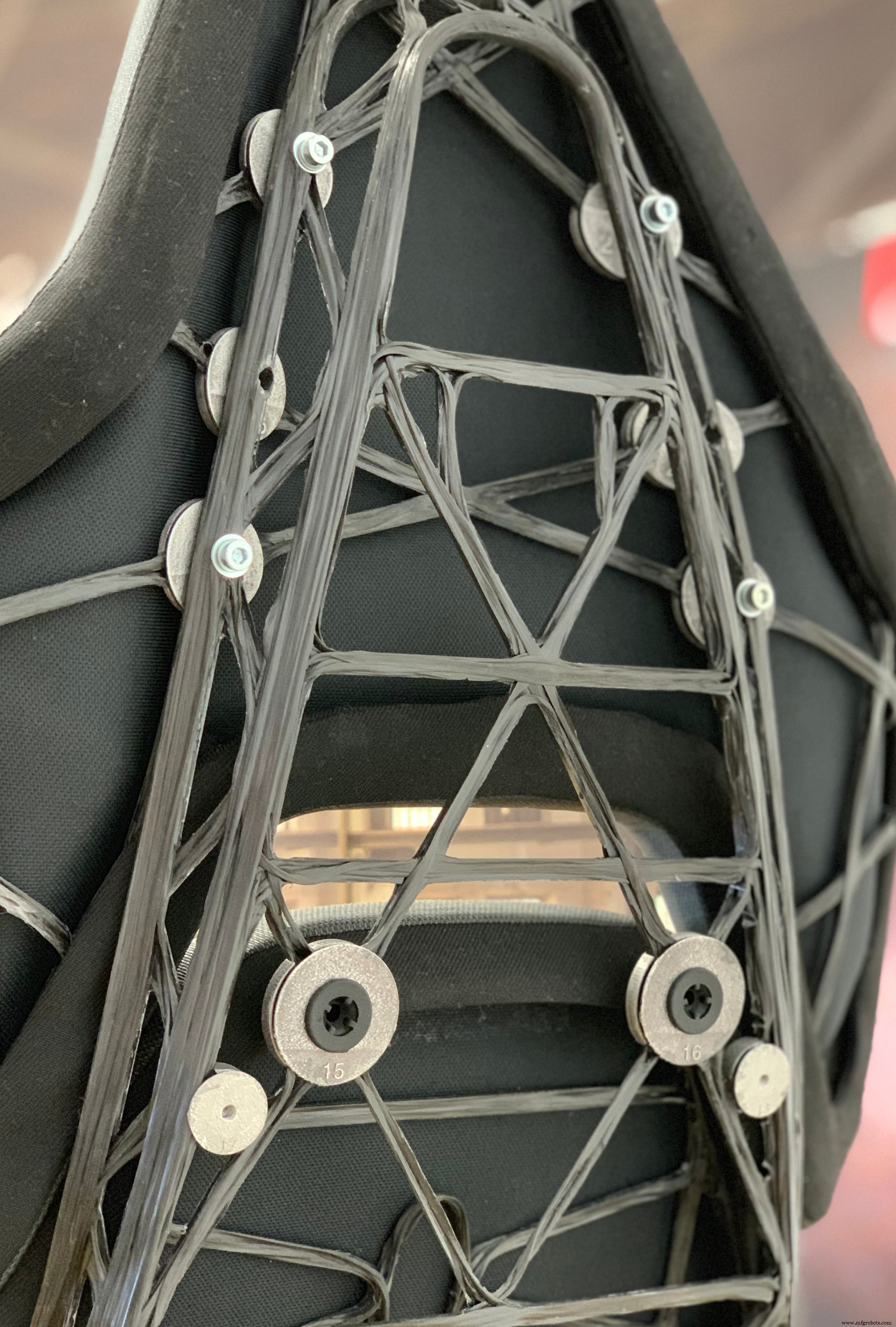
Обмоточные втулки. Пропитанный термореактивной смолой волокнистый ровинг наматывается вокруг фиксатора, позволяя расположить волокна в соответствии с нагрузками и желаемыми функциями каждой детали. Источник | csi entwicklungstechnik
Технология xFK in 3D наматывает несущие конструкции безотходным образом с использованием пропитанных термореактивной смолой непрерывных волокон. Волокнистый ровинг, пропитанный эпоксидной смолой, наматывается на приспособление для позиционирования или намоточные втулки, что позволяет размещать волокна в соответствии с нагрузками и желаемыми функциями каждой детали.
«Одним из основных преимуществ xFK в 3D является устранение слабых мест, касающихся передачи нагрузки и введения нагрузки в конструкции», - говорит Херрманн. Он объясняет, что слабые места часто находятся не в континууме конструкции, а в тех областях, где нагрузки вводятся в конструкцию, особенно там, где соседние компоненты соединены с конструкцией . Технология xFK в 3D обеспечивает передачу нагрузки между соединениями и позволяет выравнивать волокна в соответствии с желаемыми функциями компонентов и загружениями, а также производить их в трех измерениях.
Процесс намотки нити также дает дополнительные преимущества. Этот процесс помогает свести к минимуму отходы материала - тратится менее 1% волокнистой ровницы.
CSI признала сильные стороны xFK в 3D и разработала каркас сиденья ULBS, который будет сконструирован под руководством доктора Клауса Георга Байройтера, руководителя технологий AMC.
«Работая с инженерами CSI, консультантами AMC и экспертами по инструментам Alba, мы разработали эту концепцию и структуру для изготовления каркаса сиденья с использованием xFK в 3D-процессе», - говорит Питер Фассбендер, технологический консультант и инициатор xFK в 3D-технологии.
Альба изготовила оснастку для каркаса сиденья из углепластика и оказала техническую поддержку. Кроме того, хотя каркас сиденья был намотан из углеродного волокна, натуральные волокна или базальтовые волокна также являются хорошими кандидатами.
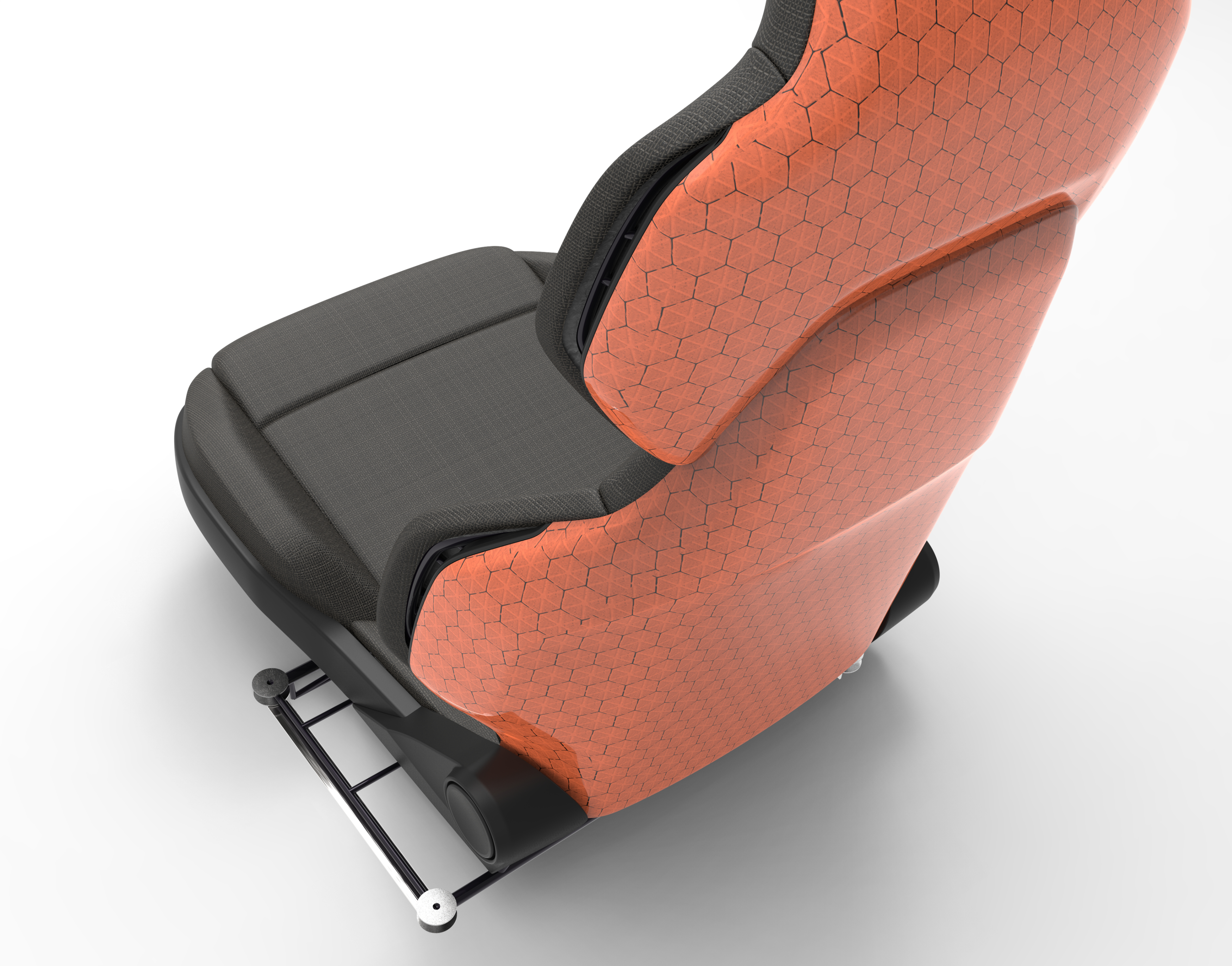
Новые технологии. В прототипе ULBS используется комбинация новых технологий, включая оболочку задней панели из интраламинарного армирующего материала (IRC) и напечатанные на 3D-принтере подушки спинки сиденья из термопластичного полиуретана (TPU). Источник | csi entwicklungstechnik
Гибридная структура материала
Помимо рамы, прототип ULBS включает еще несколько нововведений. Компания Alba, которая поставляла инструменты, также предоставила инструменты, проектирование и производство пенопласта для корпуса сиденья и выполнила сборку сиденья. Коврик из флиса покрывает каркас сиденья из углепластика, который затем покрывается вспененным чехлом из полиуретана, напечатанным на 3D-принтере. Подушка сиденья изготовлена из традиционного пенопласта.
Дальнейшее снижение веса было достигнуто за счет использования 3D | CORE, материала интраламинарного армирующего сердечника (IRC) в структуре оболочки задней панели спинки сиденья. Материал представляет собой материал внутрислойного армирующего сердечника (IRC) - структурный сэндвич-сердечник, который состоит из вспененных сердечников из экструдированного полистирола (XPS) и полиэтилентерефталата (ПЭТ), образующих интегрированный сотовый рисунок. Во время производства композитных деталей сотовая структура заполняется смолой, что обеспечивает высокую внутриламинарную прочность. 3D | Core собирается между двумя слоями стекловолокна, чтобы создать преформу, которая пропитана термопластичной эпоксидной смолой с использованием вакуумного литья под давлением (VA-RTM).
Covestro предоставила клей Dispercoll в качестве связующего для флисовых матов, а также напечатанную на 3D-принтере подушку для спинки. По словам Херрманна, механические свойства Dispercoll обеспечивают хорошую стойкость к истиранию, что важно, поскольку контакт поверхности между подушкой и каркасом может со временем изнашивать флис.
«Если у вас ровинг из одинарного волокна, когда вы помещаете его в ткань, вы получаете микродвижения между твердыми деталями из углепластика и флисовыми матами. Компоненты каркаса сиденья могут тереться о ткань и разрушать ее », - поясняет Херрманн.
Традиционные сиденья обычно имеют большую площадь поверхности, поддерживающей амортизацию, и не имеют этой проблемы. Однако при использовании xFK в 3D площадь контактной поверхности меньше из-за конструкции рамы.
«Когда xFK в 3D-структурах прижимается к флисовой ткани, вам потребуется специальное и прочное связующее; это то, что Dispercoll предлагает в этом контексте », - добавляет Херрманн.
Covestro также поставила, как говорят, первую в мире подушку, напечатанную на 3D-принтере. В то время как в спинках сидений обычно используется обычная и интенсивная пена для инструментов, использование напечатанных на 3D-принтере подушек спинки сидений, изготовленных из ТПУ (термопластичного полиуретана), еще больше увеличивает гибкость и адаптируемость сиденья ULBS с точки зрения его эстетики. функциональные возможности интеграции и комфорт.
Место для будущего
Проект ULBS преследует несколько целей. Получившаяся в результате концепция, еще не представленная на рынке, имеет потенциал для обслуживания многочисленных нишевых рынков, таких как гиперкары, авиатакси, сверхлегкие автомобили, микромобильность, вертолеты, мультикопты и авиация. Хотя ULBS, по общему признанию, дороже серийных автомобильных сидений, он демонстрирует несколько технологий, которые минимизируют отходы, тем самым снижая затраты на материалы. По сравнению с другими технологиями из углеродного волокна, xFK в 3D дает очень мало отходов. По сути, весь проект направлен на использование минимальных ресурсов и необходимого минимума материала. ULBS также предлагает возможность использования возобновляемых и устойчивых ресурсов, таких как натуральные волокна в конструкции каркаса, подушек и текстиля.
Но что более важно, проект демонстрирует, как компании могут минимизировать время выхода на рынок, работая вместе с помощью коротких и гибких процедур координации. Это также хороший пример использования дизайнерского мышления для успешного перехода продукта от идеи к прототипу оборудования, сосредоточив внимание на функциональных требованиях и заглянув в будущее приложений и целей устойчивого развития.
волокно
- Конфигурации обмотки
- Велосипедное сиденье
- Моноцикл
- Детское автокресло
- Чип со сверхшироким диапазоном частот обеспечивает доступ к автомобилю со смартфона
- Платформа пограничных вычислений обеспечивает глубокий доступ к автомобильным данным
- Рабочие характеристики пряжи из стекловолокна
- Крышка сиденья унитаза из углеродного волокна
- Новые технологии и рынки на мероприятии World of Filament Winding
- Намоточная машина Roth для облегчения значительного снижения веса / стоимости Ariane 6