17 Глава 7. Бережливое производство
ЦЕЛЬ
После завершения этого раздела вы сможете:
- Примените 5S в любой мастерской.
- Опишите концепцию Кайдзен.
- Опишите внедрение бережливого производства.
Бережливое производство 5S:
«5S» — это метод организации рабочего места, состоящий из пяти слов:«Сортировать», «Навести порядок», «Почистить», «Стандартизировать» и «Поддержать». Все эти слова начинаются с буквы S. Эти пять компонентов описывают, как хранить предметы и поддерживать новый порядок. При принятии решений сотрудники обсуждают стандартизацию, что сделает рабочий процесс понятным для работников. Благодаря этому каждый сотрудник почувствует свою ответственность за процесс.
Этап 0. Безопасность
Часто предполагается, что правильно выполненная программа 5S повысит безопасность на рабочем месте, но это неверно. Безопасность не вариант; это приоритет.
Этап 1. Сортировка
Просмотрите все предметы на рабочем месте, оставив только то, что необходимо.
Этап 2. Выпрямление
Все должно иметь место и быть на своем месте. Предметы должны быть разделены и промаркированы. Все должно быть организовано продуманно. Сотрудникам не нужно постоянно наклоняться. Размещайте оборудование рядом с тем местом, где оно используется. Этот шаг является частью того, почему Lean 5s не считается «стандартизированной очисткой».
Этап 3. Сияние
Следите за тем, чтобы рабочее место было чистым и опрятным. Делая это, будет легче осознавать, где находятся вещи и где они должны быть. После работы очистите рабочее пространство и верните все на прежнее место. Поддержание чистоты на рабочем месте должно стать частью повседневной жизни.
Этап 4. Стандартизация
Стандартизируйте рабочие процедуры и сделайте их согласованными. Каждый сотрудник должен знать, каковы его обязанности при выполнении первых трех шагов.
Этап 5. Поддержка
Оценивать и поддерживать стандарты. Вышеупомянутые шаги должны стать новой нормой в действии. Не возвращайтесь постепенно к старому. Принимая участие в новой процедуре, подумайте о том, как ее улучшить. Просмотрите первые четыре шага, когда будут представлены новые инструменты или требования к выходным данным.
Кайдзен
В то время как процесс бережливого производства 5S фокусируется на устранении потерь, Кайдзен фокусируется на практике постоянного совершенствования. Подобно бережливому производству 5S, Кайдзен выделяет три основных аспекта рабочего места:M уда (отходы), М ura (несоответствия) и M ури (нагрузка на людей и машины). Однако пошаговый процесс Кайдзен более масштабен, чем процесс бережливого производства 5S.
Обзор процесса Кайдзен:
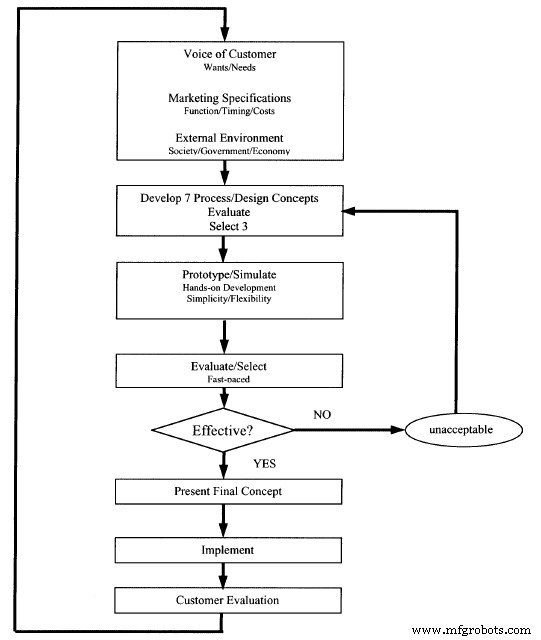
1. Определите проблему.
2. Сформируйте команду.
3. Соберите информацию от внутренних и внешних клиентов и определите цели проекта.
4. Просмотрите текущую ситуацию или процесс.
5. Проведите мозговой штурм и рассмотрите семь возможных альтернатив.
6. Выберите три лучших варианта из семи.
7. Смоделируйте и оцените эти альтернативы перед реализацией.
8. Представить идею и предложения менеджерам.
9. Физически внедрите результаты Кайдзен и примите во внимание эффекты.
Бережливое производство улучшается с течением времени, поэтому важно продолжать обучение по соблюдению стандартов. Крайне важно изменить стандарты и обучить рабочих, когда они получат новое оборудование или правила.
Экономичный
Думайте об отделе технического обслуживания как об обслуживании внутренних клиентов:различных отделов и сотрудников компании.
Бережливое производство отличается от традиционной западной модели массового производства, которая опирается на эффект масштаба для получения прибыли. Чем больше вы делаете, тем дешевле становится продукт, тем больше потенциальная прибыль. Он основан на прогнозировании потребностей клиентов или создании потребностей клиентов. Ему трудно справляться с необычными изменениями спроса.
Бережливое производство отвечает проверенному потребительскому спросу. Вытягивающая обработка – производство вытягивает заказчик. В массовой системе производитель продвигает продукт на рынок, продвигает переработку.
Создание долгосрочной культуры, направленной на улучшение.
Уважение к работникам, лучше обученным и образованным, более гибким
Бережливое производство — это философия, которая фокусируется на следующем:
- Удовлетворение потребностей клиентов
- Непрерывное постепенное улучшение
- Непрерывно улучшать продукты
- Оценка вклада сотрудников
- В долгосрочной перспективе
- Устранение ошибок
- Устранение потерь
Потери:использование слишком большого количества ресурсов (материалов, времени, энергии, пространства, денег, человеческих ресурсов, плохих инструкций)
Отходы:
- Перепроизводство
- Дефекты
- Ненужная обработка
- Ожидание (трата времени)
- Напрасная трата человеческого времени и таланта
- Слишком много шагов или слишком много движений. Слишком много транспорта.
- Избыточный инвентарь
Бережливое производство включает работу с поставщиками, субподрядчиками и продавцами для оптимизации всего процесса.
Цель состоит в том, чтобы производство шло гладко, избегая дорогостоящих запусков и остановок.
Идея называется точно в срок «производить только то, что нужно, когда нужно и только в необходимом количестве». Производственный процесс должен быть гибким и быстрым.
Инвентарь =только то, что вам нужно
В массовом производстве =на всякий случай. Дополнительные материалы и продукты хранятся на случай, если они понадобятся.
Терминология:
Упрощение процессов – процесс вне производственного потока
Дефекты — система массового производства проводит проверку в конце производства, чтобы выявить дефекты до того, как они будут отправлены. Проблема в том, что ресурсы уже «потрачены» на производство отходов». Старайтесь предотвращать проблемы сразу, как только они возникают, а затем предотвращайте их. Контроль в процессе производства, на каждом этапе производства.
Безопасность:больное время — пустая трата времени
Информация – нужна нужная информация в нужное время (слишком много, слишком мало, слишком поздно)
Принципы:
Poka-yoke — защита от ошибок, определение причины проблем и последующее устранение причины для предотвращения дальнейших ошибок
Ошибки суждения – поиск проблем после процесса
Информативные проверки – анализ данных проверок в процессе
Проверка источника — проверка перед началом процесса для предотвращения ошибок.
СРЕДНЕЕ МАКСИМАЛЬНОЕ
Один из терминов, применяемых к простому сокращению затрат и интерпретации бережливого производства, — это среднее бережливое производство. Часто современные менеджеры думают, что они занимаются бережливым производством, не понимая важности работников и долгосрочных отношений.
Техническое обслуживание, ориентированное на надежность
Техническое обслуживание, ориентированное на надежность, — это система разработки экономически эффективной программы технического обслуживания. Это может быть подробный комплекс, компьютер, управляемый статистикой, но в своей основе он довольно прост. Его идеи могут быть применены к проектированию и эксплуатации системы управления проектами, а также могут помочь вам в обучении при обслуживании, устранении неполадок, ремонте и энергоснабжении.
Это основные принципы RCM. Вот эти девять основных понятий:
- Ошибки случаются.
- Не все ошибки имеют одинаковую вероятность
- Не все ошибки имеют одинаковые последствия.
- Простые компоненты изнашиваются, сложные системы ломаются
- Хорошее техническое обслуживание обеспечивает необходимую функциональность при минимально возможных затратах.
- Техническое обслуживание может обеспечить только присущую конструкции надежность оборудования.
- Ненужное обслуживание отнимает ресурсы у необходимого обслуживания.
- Хорошие программы технического обслуживания постоянно совершенствуются.
Техническое обслуживание включает в себя все действия, предпринимаемые для обеспечения того, чтобы компоненты, оборудование и системы выполняли свои функции, когда это необходимо.
Система RCM основана на ответах на следующие вопросы:
1. Каковы функции и желаемые стандарты производительности оборудования?
2. Каким образом он может не выполнять свои функции? (Какие сбои наиболее вероятны? Насколько вероятен каждый тип сбоев? Будут ли сбои очевидными? Может ли это быть частичный сбой?)
3. Что вызывает каждый сбой?
4. Что происходит при каждом сбое? (Какой риск, опасность и т.д.?)
5. Какое значение имеет каждая неудача? Каковы последствия полного или частичного сбоя?
6. Что можно сделать, чтобы предсказать или предотвратить каждую неудачу? Сколько будет стоить прогнозирование или предотвращение каждого сбоя?
7. Что делать, если не удается найти подходящую упреждающую задачу (действия по умолчанию) (задание может быть недоступно или оно может быть слишком дорогостоящим для данного риска)?
Оборудование изучается в контексте того, где, когда и как оно используется
Все действия по обслуживанию можно отнести к одной из следующих категорий:
- Корректирующее обслуживание — восстановление утерянных или нарушенных функций
- Профилактическое обслуживание — сводит к минимуму возможность отказа функции
- Альтернативное техническое обслуживание. Устранение неудовлетворительного состояния путем изменения конструкции или использования системы.
В категории профилактического обслуживания все выполненные задачи можно отнести к одному из пяти (5) основных типов задач:
- Управление состоянием:продление срока службы на основе измеренного состояния по сравнению со стандартом
- Управление временем – Возобновление жизни независимо от состояния
- Поиск сбоев – определите, произошел ли сбой.
- Обслуживание — добавление/пополнение расходных материалов
- Смазка — масло, консистентная смазка или иная смазка
Мы проводим техническое обслуживание, потому что считаем, что надежность оборудования со временем снижается, но мы можем что-то сделать, чтобы восстановить или сохранить первоначальную надежность, которая окупается.
RCM ориентирован на надежность. Его цель состоит в том, чтобы поддерживать присущую конструкции системы или оборудования надежность, признавая, что изменения присущей надежности могут быть достигнуты только за счет изменений конструкции. Мы должны понимать, что оборудование или систему нужно изучать в той ситуации, в которой она работает.
Внедрение бережливого производства
Анализируйте каждый шаг исходного процесса, прежде чем вносить изменения
Основное внимание в бережливом производстве уделяется снижению затрат и увеличению оборота, а также устранению действий, которые не добавляют ценности производственному процессу. По сути, бережливое производство помогает компаниям достичь целевого производства, а также других вещей, внедряя инструменты и методы, которые легко применять и поддерживать. Эти инструменты и методы позволяют сократить и устранить отходы, которые не нужны в производственном процессе.
Инженеры-технологи решили использовать методологию шести сигм DMAIC (проектирование, измерение, анализ, улучшение, контроль) в сочетании с бережливым производством для удовлетворения требований клиентов, связанных с производством труб.
Инженерам-технологам было поручено разработать новую технологическую схему линии по производству труб. Цели проекта включали:
- Улучшенное качество
- Снижение брака
- Доставка до места использования
- Меньшие размеры лотов
- Внедрение системы вытягивания
- Улучшенная обратная связь
- Увеличение производства
- Личная ответственность
- Снижение незавершенного производства
- Гибкость в питании
Прежде чем вносить изменения, команда анализирует каждый этап исходной схемы процесса производства труб.
1. Попытайтесь понять процесс исходного состояния, определить проблемную область, ненужный шаг и не добавленную стоимость.
2. После составления карты процесса команда бережливого производства собрала данные со стенда Совета по проверке материалов (MRB) для измерения и анализа основных типов дефектов. Чтобы лучше понять процесс, команда также изучила время производственного цикла за 20 дней.
В исходном состоянии трубная линия состояла из одного оператора и четырех рабочих, разделенных на две станции большим столом с помощью толкательной системы. Таблица выступала в качестве разделителя между второй и третьей операцией.
Первая обнаруженная проблема заключалась в несбалансированности линии. Первая станция использовалась примерно 70% времени. Операторы на второй станции проводили много времени в ожидании между циклами. Объединив первую и вторую станции, стало очевидным пространство для улучшений в отношении индивидуальной ответственности, контроля оператором запасов и немедленной обратной связи при возникновении проблемы. Эти результаты отражены в исследовании времени и структуре отдела.
Была признана вторая проблема. Из-за технологической схемы производительность не позволяла выполнить производственный график двумя станциями. Поскольку операторы потеряли счет машинным циклам, машины ждали внимания оператора. Операторы также пытались протолкнуть детали через первую станцию — узкое место в процессе — а затем продолжили изготовление деталей на последних двух операциях. Как правило, создаются большие партии незавершенного производства, и проблемы с качеством не обнаруживаются до тех пор, пока не будет произведено большое количество дефектных изделий.
Исходные данные о состоянии были взяты за последние 20 дней до изменения. Команды анализируют каждый шаг в оригинале и вносят изменения. Результаты исследования времени исходного процесса послужили основой для сокращения времени цикла, балансировки линии, разработки с использованием канбанов «точно в срок» и планирования, улучшения качества, уменьшения размера партии и незавершенного производства и улучшения потока. Новые технологические данные были получены через месяц после внедрения. Эта задержка дала операторам станков возможность обучиться и освоить новую систему организации процессов.
С U-образной конструкцией ячейки; Детали отвечают всем требованиям заказчика. Таблица в исходном процессе была удалена, что почти устранило незавершенное производство. С сокращением незавершенного производства и увеличением производства.
Некоторые из концепций, использованных для улучшения процесса, включали полное вовлечение сотрудников (TEI), меньшие размеры партий, планирование, запасы в точках использования и улучшенную планировку. Все сотрудники и руководители отдела были вовлечены во все этапы проекта. Их идеи и предложения были включены в процесс планирования и реализации, чтобы добиться более широкого признания изменений в процессе. Были введены меньшие размеры партий, чтобы свести к минимуму количество произведенных деталей до обнаружения дефектов. Канбаны были введены (в виде стеллажей для обработки материалов) для контроля незавершенного производства и внедрения системы вытягивания. А расположение ячеек уменьшило количество поездок между операциями.
Операторам было разрешено останавливать линию при возникновении проблем. В исходном состоянии операторы все еще продолжали работать с деталями, когда операция была остановлена. Канбан
контроля компоновка устранила возможность сохранения незавершенного производства, требуя от оператора отключения всей линии. Расположение ячеек предоставляет отличные возможности для улучшения связи между операторами о проблемах и корректировках для достижения лучшего качества.
Ежедневно проверяя процесс в исходном состоянии, операторы тратили много времени либо на ожидание погрузочно-разгрузочного персонала, либо на работу с материалами. С U-образной ячейкой доставка к месту использования более удобна для оператора. Оператор размещает ящики с сырьем на шести передвижных роликовых тележках, где его легко достать. Шести коробок хватит на 24 часа.
Для сокращения времени наладки инструменты, необходимые для ремонта и регулировки станка, находятся в ячейке. Винты не стандартизированы; инструменты расположены в порядке возрастания размера, чтобы можно было быстро определить нужный инструмент.
В течение трех месяцев за процессом следили, чтобы убедиться, что он находится под контролем. Сравнение временных проработок исходной и реализованной компоновки показало увеличение производства с 300 до 514 готовых изделий в смену. Новая компоновка устранила двойную обработку между второй и третьей операциями, а также на этапе упаковки. Это также сократило время, упростив цикл всех четырех операций в порядке вытягивающей системы. Спрос клиентов удовлетворялся за две смены, что снижало трудозатраты.
Результаты редизайна следующие:
- Незавершенное производство сократилось на 97 %.
- Производство выросло на 72 %
- Лом сократился на 43 %.
- Использование машин увеличилось на 50 %.
- Использование рабочей силы увеличилось на 25 %.
- Затраты на оплату труда сократились на 33 %.
- Уровень сигмы повышен с 2,6 до 2,8.
This project yielded reduced labor and scrap costs, and allowed the organization to do a better job of making deliveries on time, while allowing a smaller finished-goods inventory. Daily production numbers and single-part cycle time served as a benchmark for monitoring progress towards the goal. Although the sigma level increase , the 43% reduction in defects, 97% reduction in WIP, and production increase of 72% contributed to the project objective.
Implementing lean is a never ending process; this is what continuous improvement is all
о. When you get one aspect of lean implemented, it can always be improved. Don’t get hung up on it, but don’t let things slip back to the starting point. There will always be time to go back and refine some of the processes.
Before Lean Manufacturing was implemented at Nypro Oregon Inc., we would operate using traditional manufacturing. Traditional manufacturing consists of producing all of a given product for the marketplace so as to never let the equipment idle. These goods them need to be warehoused or shipped out to a customer who may not be ready for them. If more is produced than can be sold, the products will be sold at a deep discount (often a loss) or simply scrapped. This can add up to an enormous amount waste. After implementing Lean Manufacturing concepts, our company uses just in time. Just in time refers to producing and delivering good in the amount required when the customer requires it and not before. In lean Manufacturing, the manufacture only produces what the customer wants, when they want it. This often a much more cost effective way of manufacturing when compared to high priced, high volume equipment.
Unit Test:
1. What is 5S?
2. Please Explain each “S” of the 5S.
3. Please Explain Kaizen concept.
4. What is the Pull processing?
5. What is the Poka-yoke?
6. What is the six-sigma DMAIC?
7. What is the objectives for a new process layout of the tube production line?
8. Before making changes, The Manufacturing engineers team do what first?
9. Please lists the results of the redesign.
10. The key to implementing lean new idea or concept is to do what?
CHAPTER ATTRIBUTION INFORMATION
This chapter was derived from the following sources.
- Lean 5S derived from Lean Manufacturing by various authors, CC:BY-SA 3.0.
- Kaizen derived from A Kaizen Based Approach for Cellular Manufacturing System Design:A Case Study by VirginiaTech, CC:BY-SA 4.0.
- Kaizen (image) derived from A Kaizen Based Approach for Cellular Manufacturing System Design:A Case Study by VirginiaTech, CC:BY-SA 4.0.
Промышленные технологии
- Сравнение шести сигм и бережливого производства
- Преимущества автоматизации в бережливом производстве
- 5 блогов по производству и техническому обслуживанию, которые вы должны читать
- 6 областей улучшения, которые анализирует каждый консультант
- 5 необходимых инструментов бережливого производства [Инфографика]
- Что такое бережливое производство? Как оптимизировать с помощью гибкой автоматизации
- Лучшие инструменты бережливого производства, необходимые производителям D2C
- 8 потерь бережливого производства
- Сократите количество отходов за 3 простых шага с помощью бережливого производства
- Как вернуть бережливое производство в нужное русло