Дефекты литья под давлением:типы, причины и способы их предотвращения
Процесс литья под давлением включает приложение высокого давления к расплавленному металлу, процесс, аналогичный литью пластмасс под давлением. Однако литье под давлением является сложным процессом, и многие факторы могут ухудшить качество отлитых под давлением изделий. Дефекты литья под давлением в настоящее время являются серьезной проблемой из-за отсутствия контроля над сырьем, неадекватного планирования процессов и производства и других факторов.
Следовательно, неспособность правильно устранить эти дефекты литья повлияет на качество конечной продукции. Однако важно отметить, что вы не сможете избежать всех дефектов во время процесса литья под давлением. . В таких случаях дизайнерам может потребоваться изменить конструкцию пресс-формы.
Поэтому в этой статье мы обсудим различные типы дефектов корпуса штампа, подробно описав их причины, решения и способы их предотвращения. Давайте приступим!
Дефект литья под давлением с :типы, Причины <сильный>, сильный> и решение с <сильный>сильный>
Здесь мы рассмотрим различные дефекты литья под давлением и способы их устранения. Эти дефекты часто возникают из-за неправильного заполнения или неадекватной фазы затвердевания и делятся на две основные категории:
Внутренний Дефекты литья под давлением <сильный>сильный>
Эти типы дефектов литья трудно обнаружить, и они ослабляют структурную прочность компонентов. Два основных внутренних дефекта литья:
1. Газовая пористость <сильный>сильный>
Это связано с образованием пузырей в отливке после охлаждения. Вы увидите газовые поры в виде круглых или овальных структур на корпусе деталей для литья под давлением, и они также имеют гладкие, ярко-белые или желтые поверхности.
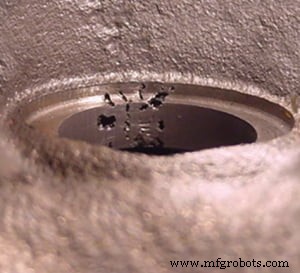
Большинство твердых металлов не могут удерживать большое количество растворенного газа, но жидкие металлы могут. В результате газ в твердом металле образует пустоты или пузыри внутри отливки по мере ее охлаждения. Это часто происходит на этапе затвердевания, и вы можете заметить некоторые отверстия в гипсе. В зависимости от степени пористости газа это может привести к другим типам дефектов и увеличению доли брака.
Причины: <сильный>сильный>
- Выделившийся водород из расплавленных металлических сплавов – Более высокие температуры плавления часто приводят к более высокой растворимости водорода в расплавленных металлических сплавах. Охлаждение и затвердевание при литье под давлением снижает растворимость водорода и высвобождает его из расплавленного металла. В результате возникают газовые поры.
- Участвующие газы в процессе заполнения металлических сплавов – Процесс литья под давлением включает заливку расплавленного металлического сплава в формы с высокой скоростью и давлением. Поэтому турбулентность может возникнуть, если жидкий сплав не может течь стабильно и упорядоченно, что приводит к пористости газа.
- Газы от разделителей для плесени – Смазки для форм обычно разлагаются и выделяют газы при нагревании расплавленным металлическим сплавом. Следовательно, из-за чрезмерного использования разделительных составов для форм может произойти улетучивание газа.
Решения: <сильный>сильный>
- Контролируйте процесс плавления, плавя сырье в вакууме под флюсом или вокруг газа с низкой растворимостью, чтобы предотвратить попадание воздуха в расплавленный металл.
- Убедитесь, что у вас чистый и сухой слиток металлического сплава.
- Используйте различимые параметры литья под давлением, включая скорость впрыска.
- Достаточная длина литника и литника способствует стабильному течению расплавленного сплава и легкому отводу газов.
- Выберите высококачественные смазки для форм и используйте их в разумных количествах.
2. Усадочная пористость <сильный>сильный>
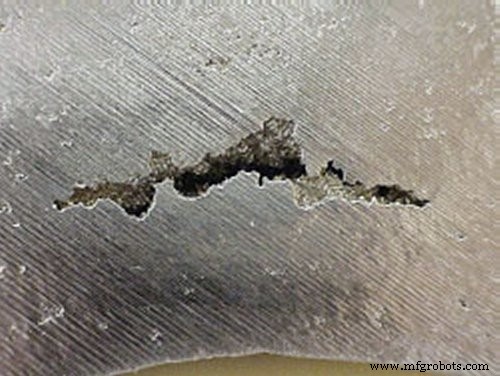
Усадочная пористость образуется в процессе охлаждения и затвердевания литья, а металлические сплавы при охлаждении дают усадку. Следовательно, существует высокая вероятность возникновения этого дефекта без надлежащих мер предосторожности. Однако это становится дефектом, когда неравномерная усадка приводит к искажению формы или образованию дыр в слепке.
Усадочная пористость может проявляться как открытая усадка, коробление и закрытая усадка, влияющая на напряжение металла. Вы увидите этот дефект в виде угловатых краев, и они также могут сопровождаться трещинами или дендритными переломами.
Причины: <сильный>сильный>
- Неразумная конструкция системы охлаждения.
- Плесень открывается слишком рано.
- Использование чрезвычайно высокой температуры заливки.
Решения: <сильный>сильный>
- Улучшить общую структуру литья.
- Измените конструкцию работающей (затворной) системы, включив в нее стояки, обеспечивающие непрерывный поток расплавленного металла.
- Вставьте внутренние охладители, охлаждающие змеевики или ребра для увеличения рассеивания тепла.
- Отрегулируйте температуру литья, чтобы уменьшить общий дефицит объема.
3. Включения <сильный>сильный>
Это отверстия неправильной формы внутри отливки или на ее поверхности. При включениях в металлической отливке присутствуют нежелательные частицы песка, материала, окалины или продукта раскисления. Включения могут влиять на механические функции металлического литья, и их можно идентифицировать с помощью рентгена или УЗК.
Причины: <сильный>сильный>
- Примеси металла из-за неправильной очистки или загрязнения мусором.
- Низкая чистота шихты.
- Взаимодействие металла с окружающей атмосферой или с поверхностью формы.
- Включение слишком большого количества графита в смазки для форм.
Решение ы: <сильный>сильный>
- Убедитесь, что шихта чистая.
- Правильная очистка жидкого металла с тщательным удалением шлаков.
- Правильно очистите полость пресс-формы и ковши.
- Если смазка для пресс-формы содержит графит, обеспечьте равномерное смешивание и перемешивание.
Поверхностный Умереть Кастинг Дефекты <сильный>сильный>
Эти типы дефектов литья часто видны и разрушают поверхность детали и ее эстетические качества. К ним относятся:
1. Трещины <сильный>сильный>
Трещины возникают, когда материал ломается из-за напряжения внутри и снаружи материала. Они выглядят как неправильные или линейные узоры на поверхностях литья под давлением. Первая трещина возникает в процессе охлаждения и затвердевания.
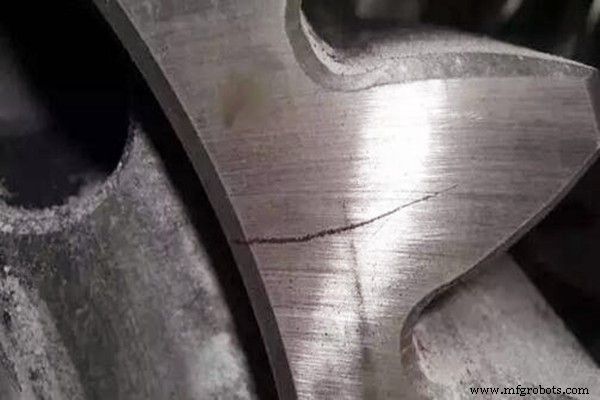
Это происходит из-за того, что материалы с геометрией полости не могут усаживаться в своем естественном состоянии. В результате остаточные напряжения вызывают трещины или деформации формы. Вторая форма трещины возникает из-за внешней силы на компоненте. Силы исходят от фазы резки или пресс-формы во время выброса детали.
Трещины возникают в результате неправильного легирования элементов, содержащихся в литейной массе. Таким образом, вы хотите использовать правильные элементы сплава при плавке. Кроме того, оптимизация структуры компонентов и обеспечение одинаковой толщины стенок предотвратят этот дефект. Сбалансированный выброс деталей для литья под давлением также является хорошим решением для устранения этого дефекта литья.
2. Холодное отключение <сильный>сильный>
Здесь на поверхности слепка имеются неровные линейные линии. Линии узкие и маленькие, с ровными краями, которые могут расширяться под действием внешних сил. Дефекты холодного закрытия при литье под давлением возникают при ненадлежащем сплавлении двух фронтов жидкого металла в полости формы. Следовательно, в компоненте осталось слабое место.
Низкая температура расплава, низкая скорость впрыска, неразумная конструкция литниковой системы и плохая текучесть сплава являются одними из причин холодного закрытия. Визуальные осмотры помогут вам обнаружить этот дефект. Хорошим способом избежать холодного закрытия является повышение температуры литейной формы и расплавленного металла. Вы также можете изменить размер и положение игры, увеличив скорость поршня.
3. Сбои в сети <сильный>сильный>
Сетчатые трещины проявляются в виде волосовидных или сетчатых впадин и выступов на поверхности отлитой под давлением детали. Выступ матрицы расширяется с увеличением времени литья под давлением. Это может произойти из-за грубой полости матрицы, высокой температуры заполнения, неподходящего литейного материала и неправильной термической обработки.
Ваш материал формы для литья под давлением и процесс термообработки должны быть адекватными, чтобы избежать этого дефекта. Кроме того, вы должны обеспечить равномерный и достаточный нагрев пресс-формы для снятия внутреннего напряжения. Тепловой баланс полости штампа должен быть обеспечен надлежащими методами охлаждения. Вам нужен хороший уровень шероховатости для процесса литья под давлением. Поэтому необходимо регулярно полировать полость штампа и литниковую систему.
4. Перетаскивание и пайка <сильный>сильный>
Заедания — это дефекты, возникающие параллельно направлению открытия штампа. Они проявляются в виде полосообразных царапин на поверхности деталей отливки. Пайка возникает из-за ненормального слипания полости матрицы и металлического сплава. Это проявляется как избыток или отсутствие материалов в некоторых областях компонента.
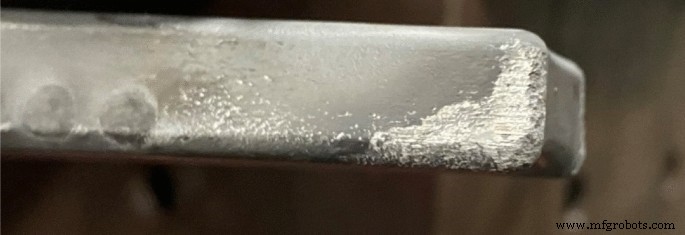
Эти дефекты при литье под давлением вызваны перегревом расплавленного сплава, повреждением поверхности полости формы или недостаточными углами уклона. Эти дефекты также могут быть вызваны неразумным механизмом впрыска и плохим качеством смазки для форм.
Таким образом, было бы лучше использовать высококачественные разделительные составы и оптимизировать механизм выброса. Если на поверхности полости штампа есть повреждения, убедитесь, что вы произвели надлежащий ремонт. Вы также можете отрегулировать направление затвора, чтобы поддерживать сердечники матрицы в правильном состоянии.
5. Мигает <сильный>сильный>
Этот дефект литья под давлением приводит к образованию тонкого металлического листа неправильной формы на отлитой под давлением детали. Некоторые из его причин включают высокую скорость впрыска, высокую температуру подачи, нечистый мусор на поверхности разъема и недостаточное усилие зажима штампа. Поэтому вы должны использовать правильные параметры обработки и обеспечить регулярное техническое обслуживание матрицы, чтобы предотвратить этот дефект.
6. Волдыри с <сильный>сильный>
Литье под давлением включает в себя сжатие воздуха в машине и выброс детали из отливки с помощью вакуумного клапана, перелива или вентиляционного отверстия. Оставшийся внутри воздух будет растворяться в расплавленном металле с равномерным распределением. Турбулентности делают воздух концентрированным, в результате чего образуются полости высокого давления – волдыри.
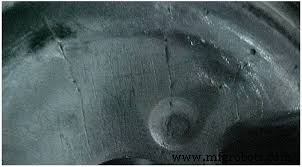
Этот дефект литья под давлением остается скрытым, если температура детали низкая, что снижает прочность детали. В случае, когда температура высокая, вы заметите пузырьки на поверхности. Поэтому параметры литья под давлением должны быть адекватными. Вам также следует оптимизировать систему литников, чтобы обеспечить надлежащую производительность вентиляции.
7. Деформация <сильный>сильный>
Это происходит, когда форма конечной детали не соответствует чертежу. Деформация возникает из-за неправильного удаления затвора, плохой конструкции отливки, преждевременного открытия формы, неадекватных механизмов выталкивания и сопротивления во время выталкивания отливки.
Поэтому вы должны убедиться, что выбрали подходящий механизм удаления ворот. Кроме того, отрегулируйте время открытия пресс-формы, чтобы обеспечить жесткость. Оптимизация конструкций отливок и устранение неблагоприятных факторов извлечения из формы также помогают предотвратить этот дефект.
8. Знаки потока <сильный>сильный>
Это полосы и ненаправленные линии на поверхности детали литья под давлением, отличающиеся по цвету от основы литья. Жидкий металл, попадая в полость, часто образует тонкий неполный слой, который может быть заполнен расплавленным металлом. Эта заливка оставляет следы на компоненте.
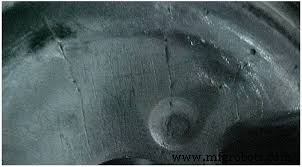
Другими причинами появления следов текучести являются низкая температура пресс-формы, низкое давление заполнения, избыток смазки или смазки для пресс-формы, а также небольшая площадь поперечного сечения. Поэтому вам следует увеличить температуру матрицы, отрегулировать скорость впрыска, площадь поперечного сечения и другие параметры литья.
9. Краткое заполнение <сильный>сильный>
При этом дефекте литья под давлением некоторые материалы могут отсутствовать на поверхности отливки. Это происходит из-за плохой текучести металлического сплава, низкой температуры заполнения, низкого давления впрыска, плохих условий заполнения и чрезмерного использования смазочных материалов.
Хороший способ избежать короткого заполнения — выбрать правильный металлический сплав. Было бы полезно, если бы вы также увеличили температуру штампа и наполнения, а также скорость и давление впрыска. Улучшение конструкции литниковой системы и отвод потока металлической жидкости также поможет предотвратить недолив.
10. Ламинирование с <сильный>сильный>
Ламинирование происходит в результате наложения двух слоев, разделенных в процессе наполнения. Эти дефекты при литье под давлением трудно обнаружить. Они появляются после подготовительных операций, таких как пескоструйная обработка и галтовка.
Удар между отливкой и вставками на этих этапах вызывает подъем слоев цинка. В результате грязь и жидкости могут быть скрыты в середине этих слоев. Скрытые вещества могут проявиться на поверхности во время процессов отделки поверхности. например, гальванизация и покраска, что ухудшает результат.
11. Раковины <сильный>сильный>
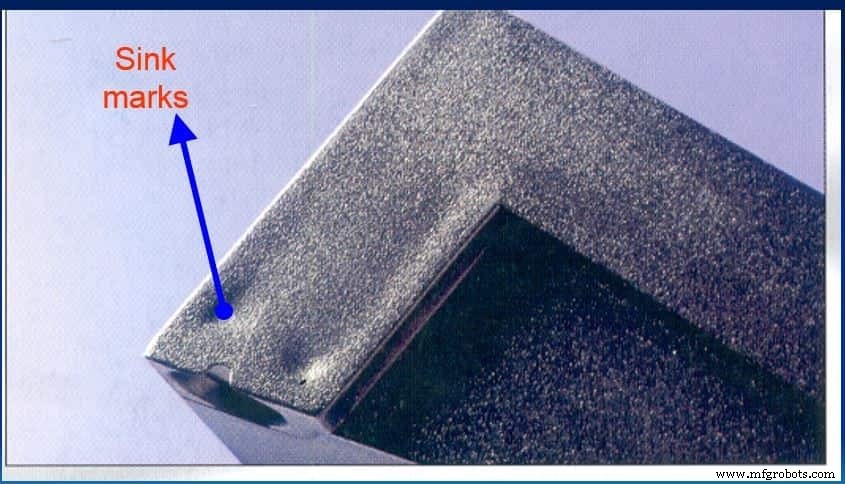
Это углубления на поверхности отливки наряду с толстостенными участками. Провалы возникают из-за низкого давления впрыска, неравномерной толщины стенок отливки, частичного перегрева матрицы и короткого времени выдержки под давлением.
Вы можете обеспечить равномерную толщину стенок за счет оптимизации конструкции отливки. Кроме того, вы можете предотвратить провалы, улучшив вентиляцию полости пресс-формы и увеличив давление впрыска. Увеличение времени удержания давления также является эффективным методом.
Советы по предотвращению Дефекты литья под давлением <сильный>сильный>
Дефекты литья под давлением возникают по разным причинам. Хорошее руководство по дизайну литья будет эффективным. Однако следующие «основные» советы помогут вам избежать этих дефектов:
Эффективная система оценок <сильный>сильный>
Эффективная рейтинговая система подскажет, сокращаете ли вы дефекты или ситуация ухудшается. Рейтинговая система поможет вам узнать, нужны ли вам исправления. Это важно, потому что вы хотите устранить дефект до того, как он достигнет кульминации.
Газовая пористость, усадка и включения являются основными дефектами литья под давлением, которые требуют оценки, чтобы определить их серьезность. Поскольку вы не можете что-то улучшить, не измерив это, вам нужна эффективная система оценок, чтобы избежать этих дефектов.
Правильная толщина стенки <сильный>сильный>
Толщина стенки играет большую роль в дефектах литья, при этом разные стенки приводят к разным результатам. Тонкая стенка заставит металлический сплав замерзнуть, усилив деформацию. Минимальная толщина стенки для магния и алюминия составляет 1,5–2,5 мм, а для цинка — 1,0 мм.
Правильное время заполнения <сильный>сильный>
Время заполнения начинается, когда сплав впервые достигает литника, и заканчивается, когда полость заполнена. Вот руководство по максимальному времени заполнения для большинства кастингов:
Сплав <сильный>сильный> | Тонкая стенка <сильный>сильный> <2 мм <сильный>сильный> | Средняя стена <сильный>сильный> >2 мм <сильный>сильный> |
Алюминий <сильный>сильный> Приблизительно 2 кг <сильный>сильный> | 0,09 секунды | 0,1 секунды |
Цинк <сильный>сильный> Приблизительно 1,4 кг <сильный>сильный> | 0,03 секунды | 0,05 секунды |
Магний <сильный>сильный> Приблизительно 1 кг <сильный>сильный> | 0,02 секунды | 0,03 секунды |
Вы можете предсказать правильное время заполнения, используя расчет PQ2. Расчет предсказывает изменения скоростей ворот и заполняет время, изменяя любой из следующих параметров:
- Площадь ворот
- Размер поршня
- Гидравлическое давление машины
- Настройка скорости плунжера
Правильный поток металла <сильный>сильный>
Ключевым фактором в конструкции ворот является поток металла, который зависит от стандартов проектирования. Эти простые шаги помогут вам использовать правильную схему течения металла:
- Используйте расчет PQ2 для определения размера литника и плунжера, убедитесь, что вы правильно используете время заполнения, скорость литника и давление в полости.
- Затем разделите актерский состав на зоны.
- Разделите ворота так, чтобы каждый журнал заполнялся одновременно.
- Обтекание актерского состава
- Избегайте смешивания дефектов литья.
Правильная температура штампа <сильный>сильный>
Вы должны использовать правильную температуру, чтобы избежать дефектов литья. Низкие температуры охлаждают жидкий металл и могут воздействовать на поверхность, увеличивая затвердевшую часть. Высокий процент твердого металла делает поток жестким и плохо перемешивает. В результате может возникнуть холодная текучесть, что приведет к дефектам.
Работа с РапидДирект в Избегайте Дефекты литья под давлением <сильный>сильный>
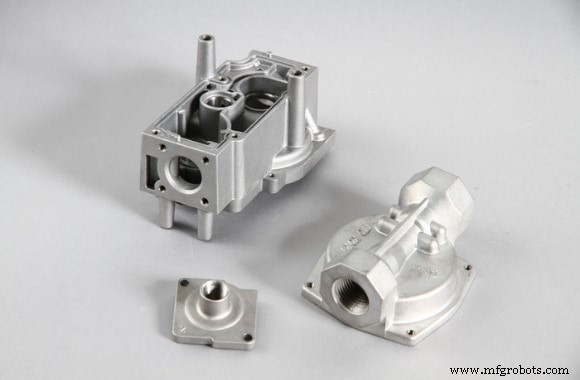
Понимание дефектов литья под давлением и их причин жизненно важно для обеспечения качества деталей. Тем не менее, нужно знать гораздо больше, поэтому лучше всего сотрудничать с экспертом в области литья под давлением. RapidDirect предлагает лучшие услуги по литью под давлением с использованием первоклассных материалов, профессиональных технических специалистов и передовых процессов.
Мы подходим к вашему проекту с целью обеспечения наилучшего качества. Наши механики также постоянно следят за процессом. Таким образом, мы можем убрать неэффективные процессы и использовать только качественные методики. Загрузите файл с дизайном сегодня и получите мгновенную смету.
Часто задаваемые вопросы <сильный>сильный>
Как уменьшить дефекты литья?Вы можете избежать дефектов литья, используя эффективную систему оценок. Использование правильной толщины стенки. температура пресс-формы и схема течения металла также являются эффективными решениями.
Для чего подходит литье под давлением?Процесс литья под давлением популярен для изготовления компонентов в автомобильной промышленности. Дизайнеры и производители также используют этот процесс для изготовления декоративной фурнитуры и других мелких компонентов.
Как удалить пористость в отливках?Хорошая конструкция пресс-формы поможет вам избавиться от газовой пористости. Вы также можете устранить этот дефект, добавив азота в металлический алюминий перед заливкой. Достаточная длина литника и рабочего колеса обеспечит стабильный поток сплава для легкого отвода газов.
Промышленные технологии
- Четыре основных производственных вызова США и способы их преодоления
- 7 Проблемы оцифровки производства - и как их преодолеть
- Семь проблем доставки на последней миле и способы их решения
- Четыре типа кибератак и как их предотвратить
- 4 основных причины отказа ЧРП и способы их предотвращения
- 4 основные причины выхода из строя распределительного устройства и способы их предотвращения
- Дефекты литья:виды, причины и способы устранения
- Как предотвратить дефекты, не связанные со смачиванием
- Основные причины сбоев машины и способы их предотвращения
- Ловушки машинной охраны и как их предотвратить