Объединение пластмасс и композитов для деталей класса A без инструментов
Производство композитных деталей с отделкой класса А не является Святым Граалем - существует множество компаний, которые делают это на регулярной основе. Однако при этом с использованием настоя смолы без дорогие инструменты или гелькоуты и из расчета одна деталь в час? Что ж, это что-то уникальное.
От пластика к композитам
Plastics Unlimited была основана 25 лет назад Терри и Нэнси Киффер, - объясняет их сын Дакота Киффер, директор по продажам и маркетингу компании. «Они были фермерами в Айове и начали искать новую и развивающуюся отрасль, - объясняет он. - Они думали, что пластмасса лучше, чем сварка или обработка дерева, и не хотели конкурировать со своими соседями. Они посмотрели на литье под давлением, ротационное формование и переработку пластмасс, но затем наткнулись на термоформование и действительно поняли это ». (При термоформовании используются тепло и вакуум / давление для формования листов термопласта в фасонные детали.)
Затем родители Киффера связались с компанией, производящей детали из армированного стекловолокном пластика (FRP). «Они увидели, насколько прочен стеклопластик, но также и то, что для этого требовался долгий, многоэтапный процесс, примерно четыре часа на каждую деталь, поэтому в день производилось только две детали», - продолжает он. «По сравнению с нашим производством пластмасс, они считали, что это слишком медленно. Мы обрабатывали детали каждые 2-6 минут - может быть, даже производили 5-6 деталей за один раз - то есть тысячи деталей в день ». Чтобы восполнить этот пробел, отцу Киффера пришла в голову идея использовать термоформованный пластиковый корпус в качестве инструмента . .
Результатом является процесс производства композитных деталей без использования инструментов, который Plastics Unlimited называет разработанным композитом без инструментов (TEC). «Удаляет гелькоут и этапы освобождения инструмента », - говорит Киффер. «Кроме того, при термоформовании вы можете осмотреть поверхность класса А и убедиться, что она идеальна». Другими словами, поверхность класса A не скрывается под композитным ламинатом. «Все, что было необходимо, - это один инструмент для термоформования, и этот процесс по-прежнему имел смысл для наших клиентов по производству пластиковых деталей».
Запатентованный композитный процесс
Киффер отмечает, что композит объединяет два материала, чтобы сделать материал лучше, чем любой из компонентов по отдельности. «Мы комбинируем два разных типа материалов и два разных процесса, чтобы сделать продукт лучше». В частности, продукт, состоящий из пластика, смолы и стекловолокна, предлагает уникальное сочетание преимуществ. «Пластмассы обладают гораздо более высокими ударными характеристиками, чем гелькоуты», - объясняет он. «Также на пластике можно напечатать любую текстуру или рисунок, например, камуфляж. Пластик также обеспечивает большую глубину изображения без последующей полировки, что исключает вторичные операции финишной обработки ».
Между тем, по сравнению с распылением рубленого волокна в процессе открытого формования, эта запатентованная технология обеспечивает более высокое содержание волокна, более высокое качество и отсутствие / отсутствие летучих органических соединений (ЛОС). Он указывает, что распыление измельченного волокна на пластмассы для ванн и спа не запатентовано. «Мы всегда используем вакуумную инфузию, чтобы сделать FRP частью продукта», - говорит Киффер, добавляя, что «наши детали имеют гладкую поверхность, поэтому мы больше похожи на легкую RTM с герметичными пластинами. Мы всегда выходим на новый уровень. Клиенты обращаются к нам с проблемой, и мы стараемся найти решение, отвечающее их потребностям. Мы очень изобретательны и запатентовали наши новые разработки ».
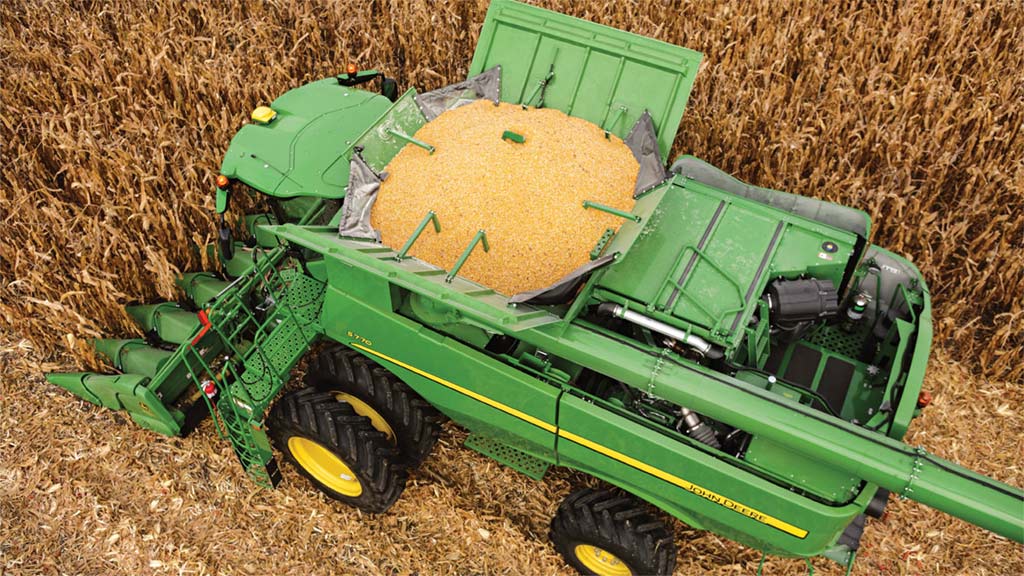
Примеры деталей
Одной из деталей, которые Plastics Unlimited производит с использованием этого процесса, является удлинитель зернового бункера для комбайнов John Deere, производимый Deere &Company (Молайн, Иллинойс). «Это самая верхняя часть комбайна, открытая, где находится зерно», - поясняет Киффер. «По сравнению с оригинальным стальным резервуаром наш более прочный. Мы делаем его с гладкой отделкой внутри и зеленым цветом John Deere снаружи с черными вставками по углам. Это самый большой из доступных удлинителей зернового бункера, который можно складывать. Это более разработанный продукт по сравнению с нашими конкурентами, с добавлением пеноматериала и ребер для увеличения жесткости ». Также требуется некоторая стальная арматура, которая, по словам Киффера, на самом деле отливается «без вторичного склеивания».
Такое сочетание материалов и процесса придает готовой детали большую прочность. «У нас есть видео, где на эти места падают бетонные блоки», - говорит Киффер. По его словам, при формовании стальных приспособлений прочность на вырыв может быть в 4-5 раз выше, чем при вторичном склеивании с использованием стандартных промышленных клеев на основе метилметакрилата.
Plastics Unlimited может производить до 2500 таких деталей в месяц, при этом размеры некоторых панелей составляют 5 на 7 футов. «Это потребовало бы дорогостоящих инструментов, если бы не было сделано с использованием нашего метода», - говорит Киффер, отмечая, что TEC можно использовать для довольно больших деталей - до 8 футов на 11 футов. «Наши детали могут иметь большую форму и геометрию, чем сталь. Это важно для наших клиентов, потому что позволяет им отличаться с помощью стиля. Наша стойкость к ультрафиолету также лучше, чем у большинства гелькоутов ».
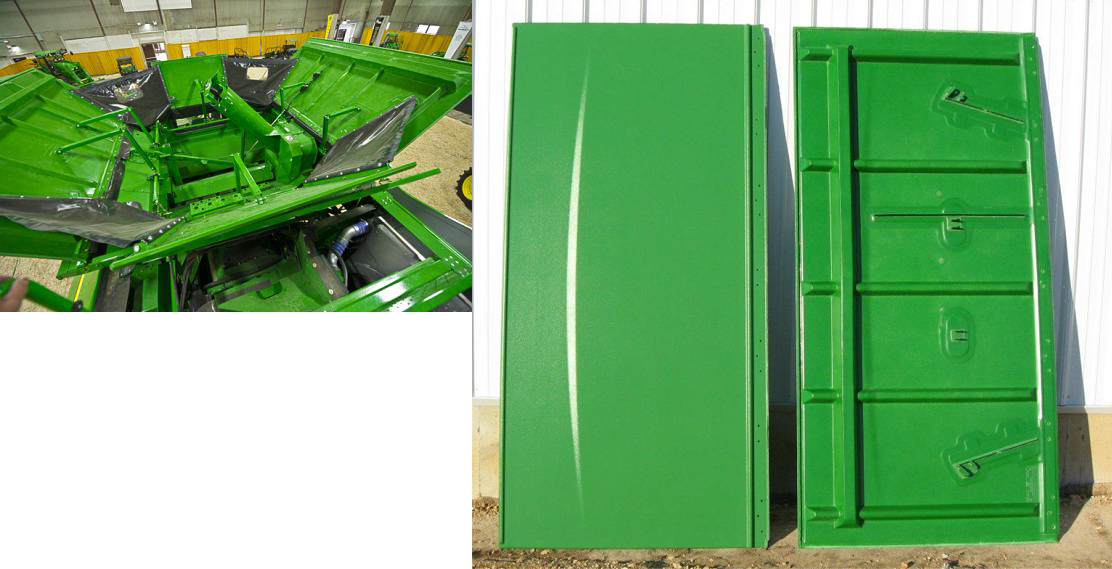
Plastics Unlimited поставляет запчасти для ряда компаний, включая телескопические подъемники Harley-Davidson и Gehl. «Мы также производим мягкие на ощупь детали, которые выглядят и ощущаются как кожа», - говорит Киффер. Компания также производила компоненты для грузовиков для Navistar и запчасти для жилых автофургонов для Winnebago. «Мы предпочитаем массовое производство от 100 000 деталей в год до нескольких сотен».
Киффер признает, что инжекция длинных волокон (LFI) и литье под давлением смолы (RIM) являются конкурентными процессами, «но детали не такие конструктивные, как то, что мы делаем. Например, зерновой бункер комбайна вмещает 400 бушелей, на которые действует сила 10 тонн. Детали RIM, которые не сильно армированы, просто не выдерживают таких нагрузок, а инструменты RIM очень дороги ».
Продолжение разработки
«Мы много работаем над исследованиями и разработками с нашими клиентами, - говорит Киффер. «Мы исследуем различные смолы, пенопласт, ламинат, слои армирования и отделки, а затем показываем им прототипы, чтобы они могли очень быстро провести испытания. Мы постараемся сделать деталь более технологичной, ища способы снизить стоимость и улучшить производительность, а также удовлетворить различные эксплуатационные требования, такие как экстремальные высокие и низкие температуры и удары ».
Plastics Unlimited имеет 100 000 квадратных футов производственных площадей и 75 сотрудников, включая команду из трех инженеров. Его 5-осевой станок с ЧПУ Thermwood позволяет производить инструменты внутри компании, а также быстро создавать прототипы, что важно для клиентов, поскольку они стремятся сократить сроки разработки.
«Мы также работаем с компаниями общественного транспорта и авиакосмической отрасли», - продолжает он. «Многие интерьеры в метро в настоящее время сделаны из стеклопластика с гелькоутом и алюминиевой структурой за ним. Им нужен легкий вес, а также косметическая обработка поверхности. Мы рассматриваем широкий спектр приложений, включая медицину, электротехнику и строительство ».
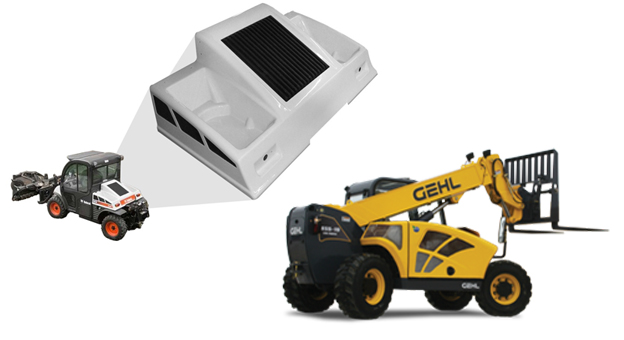
Компания также занимается термоформовкой пластмасс, армированных углеродным волокном (CFRP). «Мы создали материалы Tepex и Polystrand и работаем над различными разработками с медицинским заказчиком», - говорит Киффер. «Мы можем использовать высококачественные пластмассовые материалы, такие как Kydex, а затем использовать CF / эпоксидную смолу для аэрокосмической промышленности или такие материалы, как полиуретан, поликарбонат и ABS, которые обеспечивают красивую внешнюю отделку и являются экономически эффективными. За этими последними пластиками мы можем использовать полиэфир, винилэфир, армированный стекловолокном или эпоксидный ламинат ».
По словам Киффера, Plastics Unlimited работает на стыке пластиков, металлов и композитов. «Наши детали обычно на 30-40 процентов легче стали. Но мы находим, что рынку по-прежнему нужно немного просвещать, что такое композиты и на что они способны ». Тем не менее, компания видит большой потенциал для будущего роста. «Не все материалы работают вместе, и особенно не все смолы совместимы со всеми пластиками», - отмечает он. «За эти годы мы провели так много тестирования и разработки, что очень хорошо понимаем ландшафт и возможности. Мы обладаем уникальным опытом и предлагаем уникальный набор возможных решений ».
Смола
- Kubernetes в Azure:инструменты и советы для достижения успеха
- Шаблоны программирования и инструменты для облачных вычислений
- TPE «Smooth-Touch» для новых требований к конструкции упаковки и деталей
- Детали руки робота для автоматизации выбора и размещения
- Настройка ультразвуковых датчиков для оптимизации и контроля процесса композитов
- Перерабатываемые, ремонтируемые и перерабатываемые эпоксидные смолы для композитов
- Партнер Victrex и Bond для 3D-печати деталей из PAEK
- 20 основных сварочных инструментов и оборудования для начинающих
- Процессы отделки деталей и компонентов
- ЕЖЕДНЕВНОЕ И ПЕРИОДИЧЕСКОЕ ОБСЛУЖИВАНИЕ КОНВЕЙЕРОВ И ЧАСТЕЙ