Новый препрег для компрессионного формования в RAPM
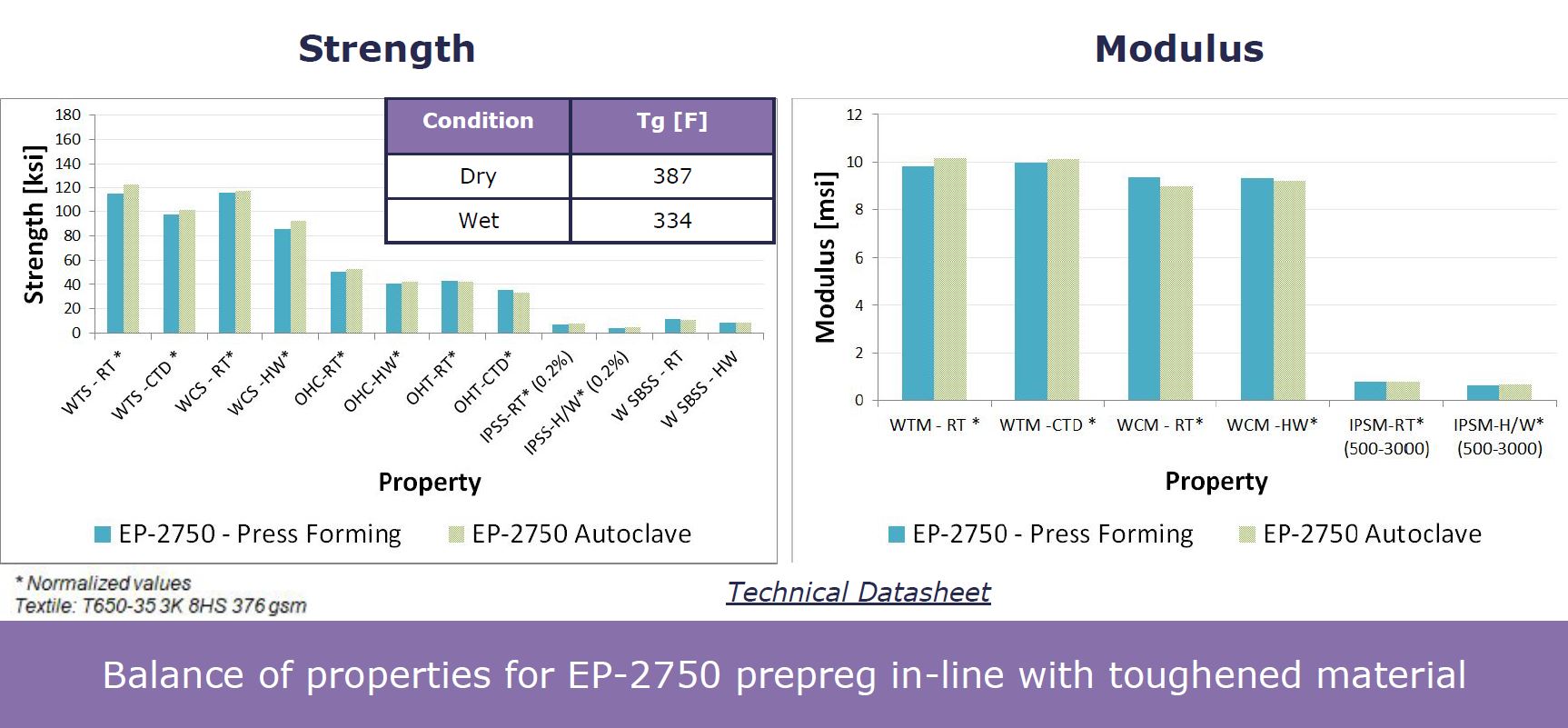
Углеродное волокно / эпоксидный препрег на протяжении десятилетий был основным материалом для аэрокосмических композитов, поскольку он обеспечивает высокие механические свойства и точное содержание смолы / волокна, а также простоту обращения при укладке и отверждении в автоклаве. Однако, поскольку производители самолетов и городской авиамобильности (UAM) исследуют более высокие темпы производства и более низкие затраты, компрессионное формование является привлекательным, сокращая время цикла и повышая эффективность по сравнению с автоклавом. В простейшем случае компрессионное формование включает предварительный нагрев формовочного материала, помещение его в открытую полость инструмента и уплотнение под действием гидравлического давления при температуре, во время которого жидкий термореактивный материал превращается в твердое тело. Затем затвердевшая деталь извлекается для выполнения всех необходимых операций обрезки и отделки.

Комбинация пресс-формования и препрега не только обеспечивает эффективный, высокоскоростной процесс с производительностью и простотой обращения с препрегом, но также позволяет избежать некоторых сложных процессов, связанных с заполнением сухих арматурных материалов жидкой смолой во время таких процессов, как введение смолы и литье с переносом смолы. (RTM). В частности, для небольших авиастроек пресс-формование с использованием препрега обеспечивает время такта менее 30 минут, при этом обеспечивая получение высококачественных деталей со сложной геометрией.
Компания Solvay Composite Materials (Альфаретта, штат Джорджия, США) была ключевым партнером в программе высокопроизводительного производства RApid (RAPM), возглавляемой компанией Boeing Co. (Чикаго, штат Иллинойс, США). RAPM - это «составляющая» часть программы Tailorable Feedstock and Forming (TFF), запущенной Агентством перспективных оборонных исследовательских проектов (DARPA, Арлингтон, Вирджиния, США) в 2015 году. Ее цель - обеспечить быстрое, недорогое и гибкое производство небольших композитных деталей сложной формы и повышение способности композитов конкурировать с обработанным алюминием в оборонных приложениях.
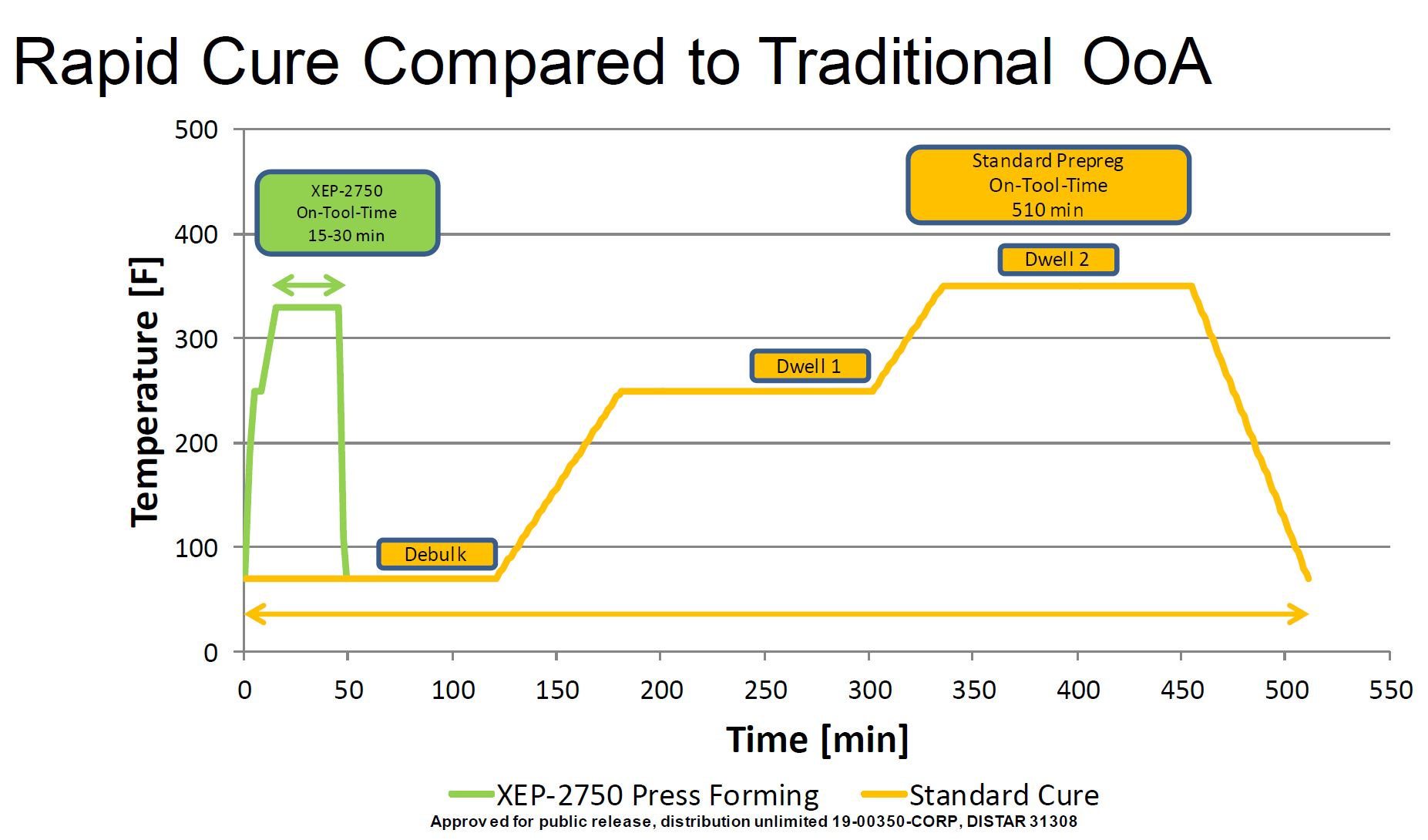
Компания Solvay, долгое время являющаяся поставщиком оборонных приложений для Boeing, также является лидером в разработке новых решений для коммерческой авиакосмической отрасли, таких как эпоксидный препрег CYCOM 5320-1 для использования вне автоклава (OOA), а также для автомобилей, таких как время такта 1 минута, винил-гибридный препрег SolvaLite 730
RAPM стал прекрасной возможностью для Solvay протестировать и усовершенствовать свою экспериментальную систему XEP-2750, которая теперь коммерциализируется как CYCOM EP2750, которая была разработана для объединения производства композитов в аэрокосмической и автомобильной промышленности. В этом блоге - онлайн-боковой панели к майскому обзору 2020 года «Революция парадигмы стоимости композитов, часть 2:формование» - рассматриваются эти разработки, а также используемые процессы компрессионного формования и то, что CYCOM EP2750 предлагает производителям композитов в аэрокосмической и автомобильной промышленности.
Ссылки для этого блога включают:
- «Производство прессов с пружинной рамой для компонентов аэрокосмического производства», Тимоти Дж. Лучини
1
, Алехандро Дж. Родригес
2
, Скотт А. Роджерс
2
, Бюстгальтеры Aurele
3
, Адам Уизолл
3
, Ричард Рассел
3
, Скотт Лукас
2
, Гейл Л. Хан
1
. Материалы конференции SAMPE. Шарлотта, Северная Каролина, 20-23 мая 2019 г.
- «Проблемы геометрии конструктивных деталей в аэрокосмической отрасли для высокоскоростного формования прессованием» от Aurele Bras
1
, Алехандро Дж. Родригес
2
, Ричард Рассел
1
, Тимоти Дж. Лучини
3
, Трэвис Адамс
3
, Адам Уизолл
1
, Скотт А. Роджерс
2
, Скотт Лукас
2
, Гейл Л. Хан
3
. Общество по развитию материалов и технологий - Северная Америка, Материалы конференции SAMPE. Сиэтл, Вашингтон, 4–7 мая 2020 г. Общество по развитию материалов и технологий - Северная Америка.
- «Быстрое высокопроизводительное формование структурного препрега xEP-2750 для формования прессованием» Тимоти Дж. Лучини 1 , Алехандро Дж. Родригес 2 , Скотт А. Роджерс 2 , Бюстгальтеры Aurele 2 , Адам Уизолл 2 , Ричард Рассел 2 , Скотт Лукас 2 , Гейл Л. Хан 1 . SAMPE 2019.
1 The Boeing Company, Сент-Луис, MO 63134, 2 Solvay Composite Materials, Анахайм, Калифорния, США и 3 Композитные материалы Solvay, Хеанор, Великобритания
- Веб-семинар CompositesWorld:«Автомобильные процессы для высокопроизводительного производства аэрокосмических композитов», Алехандро Родригес, Solvay Composite Materials, Анахайм, Калифорния, США.
Материальные и технологические цели
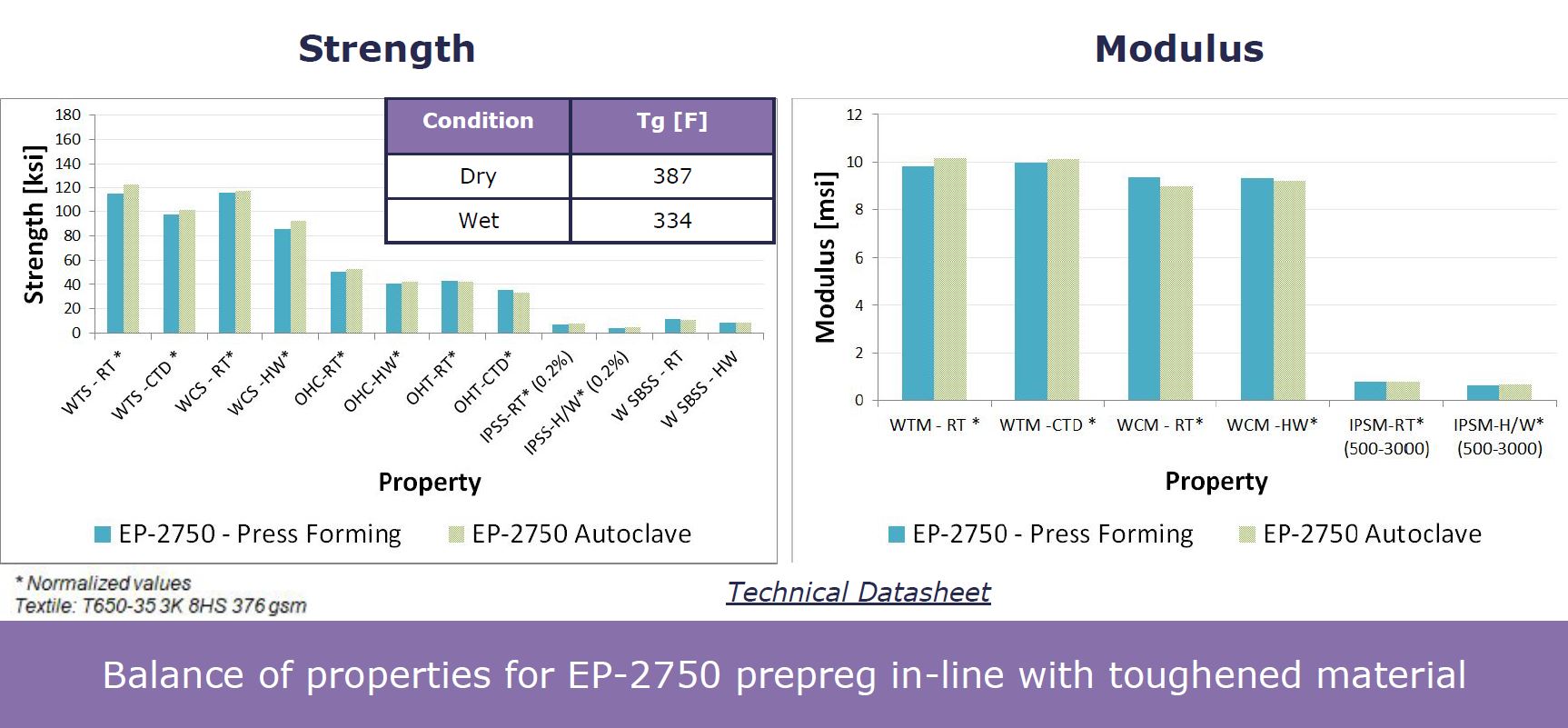
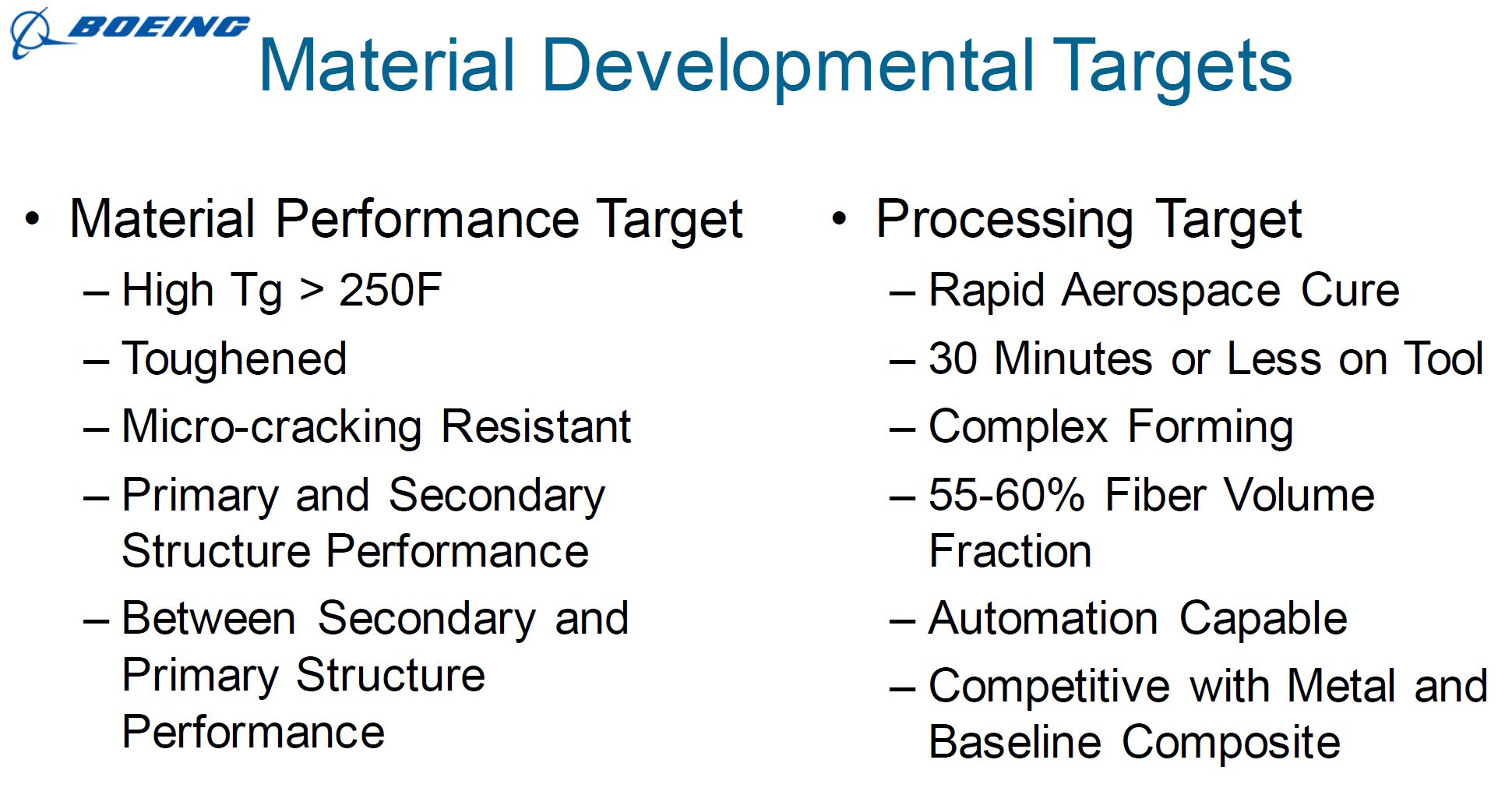
CYCOM EP2750 был разработан для достижения целевых показателей эффективности, установленных Boeing для аэрокосмической упрочненной эпоксидной смолы, демонстрируя баланс температуры стеклования (Tg) до 350 ° F, хорошие свойства надреза - например, сжатие в открытом стволе (OHC) и растяжение в открытом стволе. (OHT) - и стойкость к растворителям. Этот новый класс препрега применим как к первичным, так и к вторичным аэроструктурам и совместим с несколькими армирующими элементами (например, углеродным и стекловолокном).
CYCOM EP2750 также был разработан с возможностью масштабирования производства с использованием автоматизированного манипулирования и компрессионного формования. Это включает время отверждения на инструменте 15-30 минут при 330-370 ° F с 1-часовым пост-отверждением при 350 ° F. Это время такта, составляющее 30 минут или меньше, обеспечивает годовой объем производства 10 000 деталей на инструмент.
Компания Solvay использовала два варианта компрессионного формования во время программы RAPM:формование пружинной рамы и формование двойной диафрагмы (DDF). Оба используют принцип удерживания плоской заготовки и проведения ее через ступень предварительного нагрева в инфракрасном (ИК) диапазоне перед перемещением ее в соответствующую металлическую полость для инструмента. Затем пресс закрывает стальную форму в соответствии с автоматизированной программой и оказывает полное давление на препрег в течение оставшегося времени на инструменте.
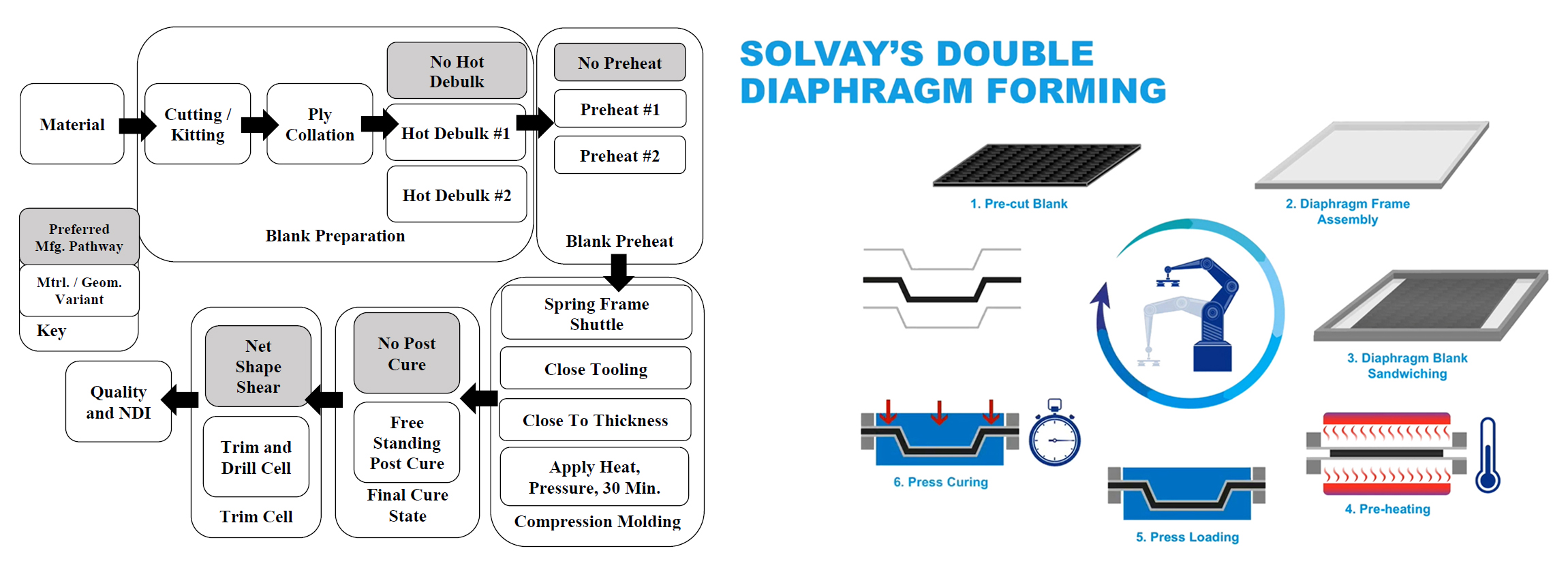
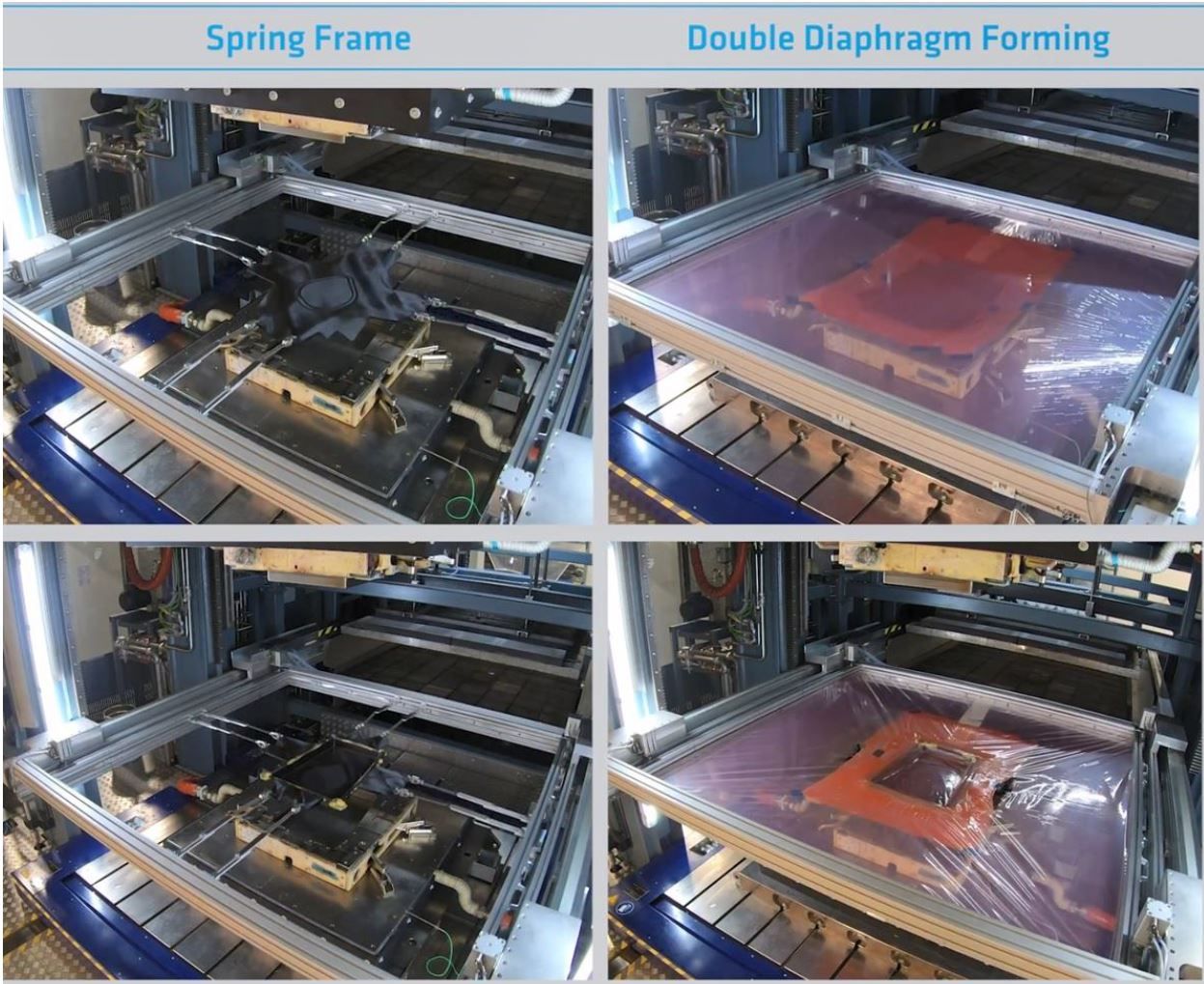
Как в формовании пружинной рамы, так и в DDF используются согласованные металлические инструменты и предлагается метод нагрева и нагрева, исключающий нагрев и охлаждение инструмента, что обеспечивает высокую производительность. Оба были использованы для успешного формования нескольких типов деталей сложной геометрии с подпружиненными шайбами, вертикальными фланцами и вариациями толщины от 3,8 до 8,9 миллиметра. Эти детали были изготовлены в прикладном центре Solvay в Хеаноре, Великобритания.Хотя не доступной во время RAPM, Heanor теперь оснащен полностью автоматизированной линией компрессионного формования от рулона препрега до формованной детали, обеспечивающей время такта от 15 до 60 минут для аэрокосмических деталей, изготовленных из EP2750 и такта. время от 3 минут или меньше для малых и средних деталей с использованием автомобильных препрегов. Solvay видит множество преимуществ в процессе DDF, в том числе:
- Исключение этапа предварительной формовки - из 2D заготовки в 3D-деталь
- Не требуется смазка для пресс-формы или очистка.
- Уменьшение количества вспомогательных материалов (например, сапуна, дренажа, мешка, ленты) по сравнению с автоклавом.
- Улучшенное формование каркаса "покупай и летай" по сравнению с пружинным формованием, поскольку для крепления пружинных зажимов требуется меньше лишнего материала.
Полная или частичная пропитка поддерживает давление
Характеристики EP2750, которые облегчают компрессионное формование, включают его низкую липкость для автоматического захвата и размещения и его полностью пропитанный характер по сравнению с CYCOM 5320-1, который частично пропитан для облегчения кромок, что необходимо для ламинатов без пустот, использующих обработку OOA. Однако при компрессионном формовании используется очень быстрый, принудительный поток смолы из-за приложенного более высокого давления - например, до 350 фунтов на квадратный дюйм (типичный максимум для EP2750) по сравнению с 35 фунтами на квадратный дюйм, обычными для обработки в автоклаве, и 14,7 фунтов на квадратный дюйм при обработке OOA только в вакууме. / P>
Наличие более полностью пропитанного препрега, даже несмотря на то, что содержание смолы лишь немного выше - 40% в CYCOM EP2750 по сравнению с 36% в CYCOM 5320-1 - поддерживает гидростатическое давление во время уплотнения и отверждения в соответствующей металлической полости инструмента, что снижает риск сухие участки, непостоянная толщина затвердевшей детали (CPT), складки и другие дефекты при обеспечении хорошего качества поверхности.
Примечательно, что Solvay разработала запатентованную трансформаторную пленку для увеличения гидростатического давления при использовании препрега CYCOM 5320-1 с низким содержанием смолы. Применяемая для компоновки деталей перед компрессионным формованием, трансформаторная пленка увеличивает содержание смолы и помогает довести CPT до требований при испытаниях формования деталей из RAPM.
Испытания формования деталей из RAPM
Как поясняется в тематической статье CW за май 2020 года, CYCOM EP2750 был одним из основных материалов, испытанных в треке из термореактивного препрега RAPM. Детали Pathfinder, испытанные на начальном этапе производства и разработки, включены
Доступные панели TS-RAPM-001 и -009, выступ TS-RAPM-002 и изогнутый С-образный канал TS-RAPM-003. Детали были спроектированы в Boeing (несколько офисов по всему миру), инструменты были изготовлены в C-Con GmbH (Мюнхен, Германия), детали были изготовлены в Центре приложений Solvay в Хеаноре, Великобритания, а затем были испытаны в Solvay Anaheim, Калифорния, США и Боинг Сент-Луис, Миссури, США
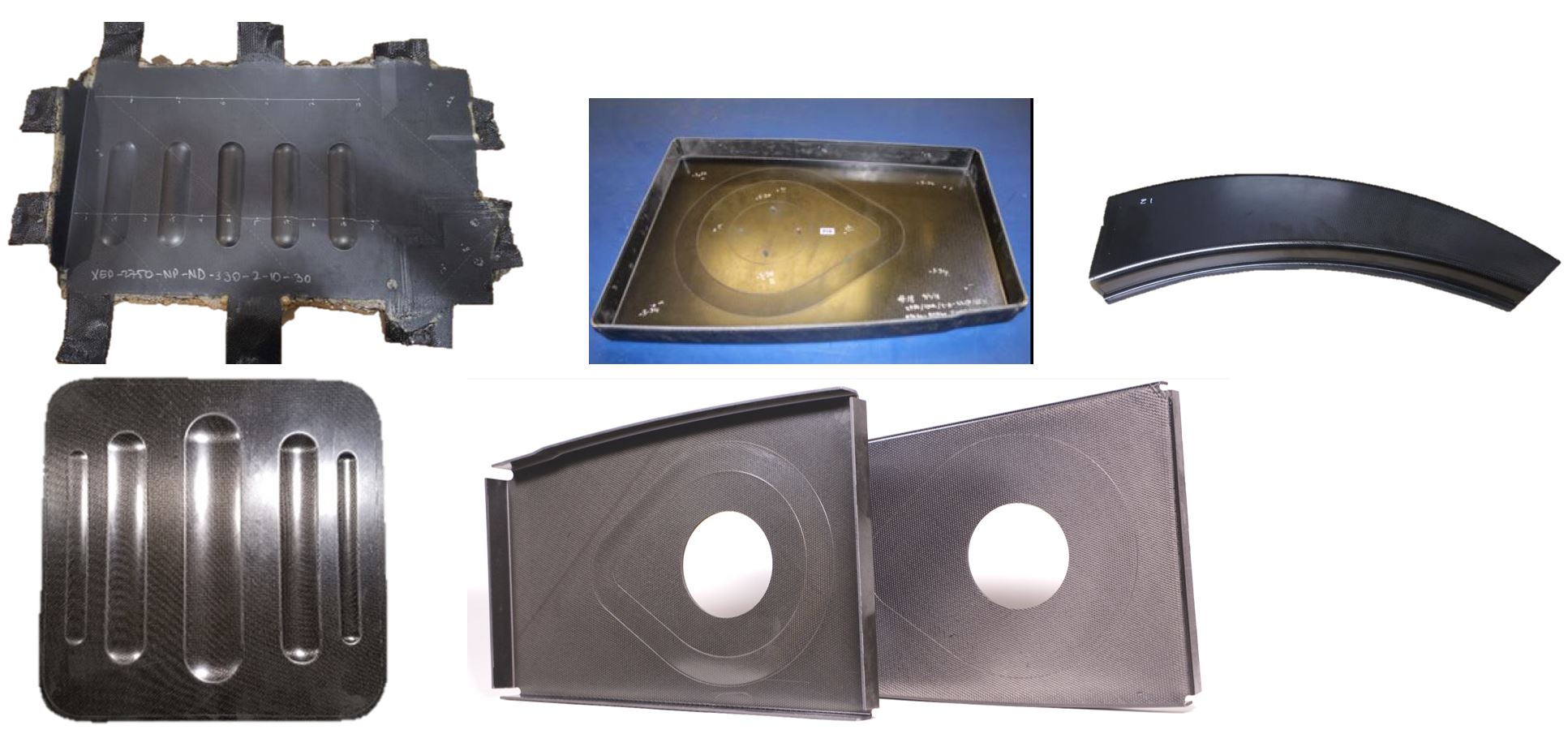
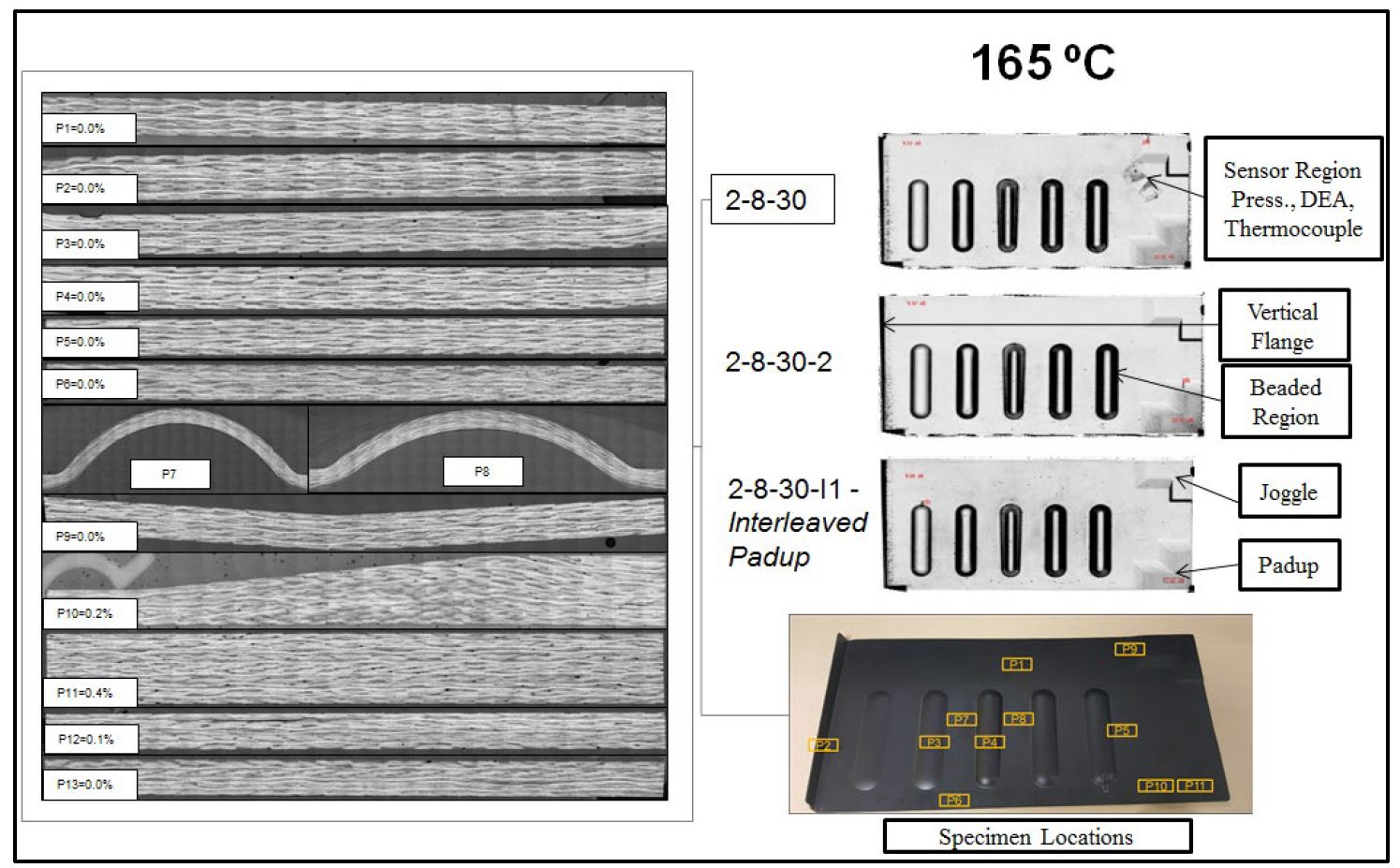

Качество поверхности оценивали с помощью неразрушающего контроля (NDI), и выбранные панели были подвергнуты поперечному сечению на предмет пористости, сдвига короткого пучка, объемной доли волокна, содержания смолы, степени отверждения и температуры стеклования.
Уровни пористости ниже 0,5% были легко достигнуты благодаря высоким давлениям консолидации при компрессионном формовании. Хотя параметры процесса нужно было оптимизировать для каждой отдельной детали, после блокировки процесс оказался повторяемым.
Панно из бисера ТС-РАПМ-009
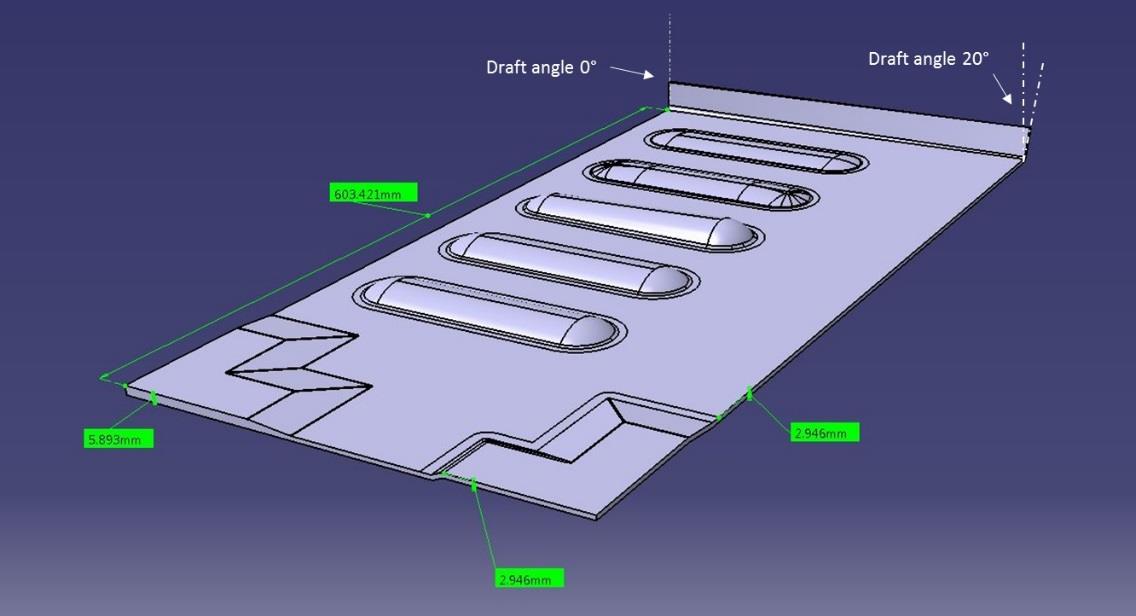
Эта плоская деталь длиной 600 миллиметров имела параллельные борта различной геометрии. Толщина увеличилась с 3 до 6 миллиметров в одном углу (pad-up), в то время как в противоположном углу имелась ступенька постоянной толщины. Противоположный край представлял собой вертикальный фланец с углом наклона, который линейно изменялся от 0 ° до 20 °.
Проскальзывание прижимов
Первоначальные испытания проводились с подкладками, уложенными на поверхность укладки. Однако из-за того, что слои прокладки были расположены около края детали, было возможно, что они выдавятся из детали, что привело к образованию области низкого давления во время отверждения и образования пористости. Решение состояло в том, чтобы чередовать слои прокладки в стопке ламината. Риск соскальзывания и пористости не наблюдался в более поздних частях, где подушки располагались вдали от краев и эффективно блокировались окружающим материалом.
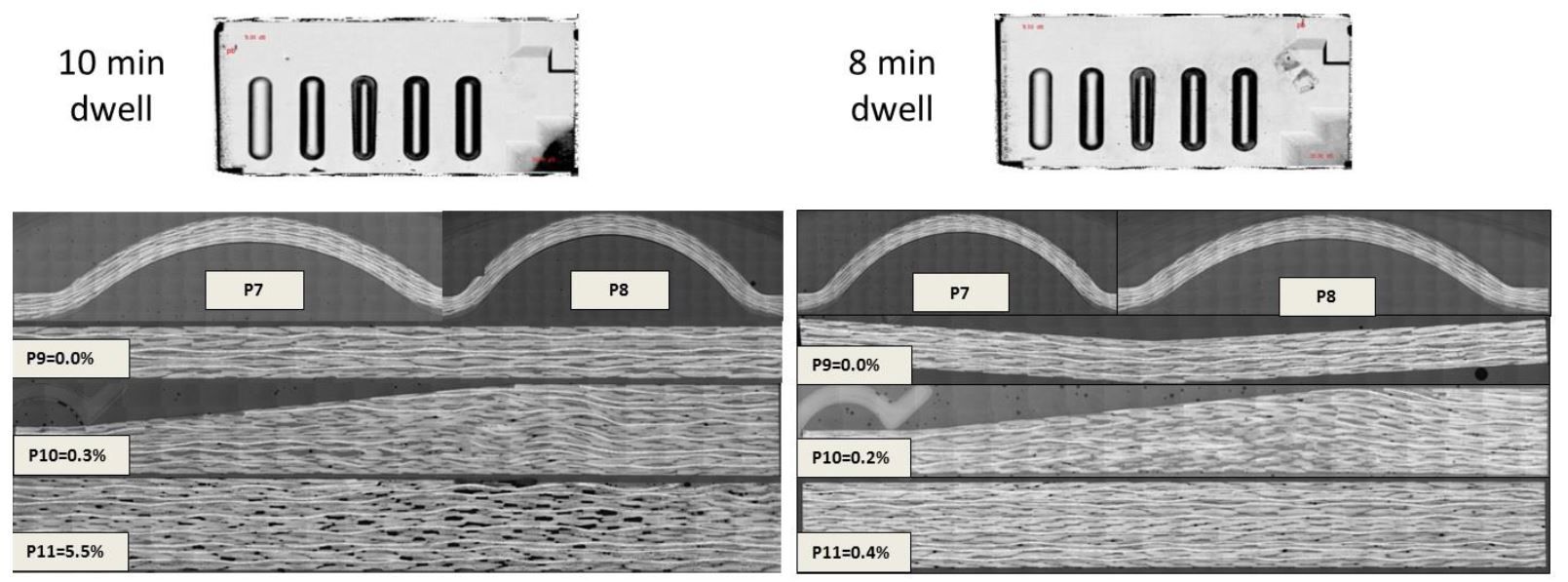
Пористость в зависимости от времени выдержки
Повышенная пористость также наблюдалась, если время выдержки было слишком большим. Панели из бисера, изготовленные с выдержкой в течение 8 минут, имели более низкое содержание пустот, чем панели, изготовленные с выдержкой в течение 10 минут. Это было особенно верно в области дополнения, где содержание пустот составляло 5,5% для 10-минутной выдержки и 0,4% для 8-минутной выдержки. Более короткая выдержка обеспечивает высокий поток смолы, эффективно смачивая волокна и поддерживая давление в полости инструмента за счет отверждения.
Более длительная выдержка позволила снизить поток смолы и давление, особенно в области набивки, из-за ее близости к краю полости инструмента, которая не имела кромки сдвига или уменьшения сечения. Таким образом, давление в полости инструмента уменьшалось на краю детали, особенно в более толстых областях, где поперечное сечение было больше. Отсутствие давления здесь также увеличивало риск соскальзывания слоев подкладки. «При проектировании инструмента уменьшение сечения вокруг полости инструмента поможет создать и поддерживать давление, особенно для деталей различной толщины», - объясняет Гейл Хан, научный сотрудник Boeing и главный исследователь проекта RAPM. «Вам необходимо представить какую-либо форму защемления или уплотнения, чтобы стимулировать состояние гидростатического давления в полости».
Ребро TS-RAPM-002
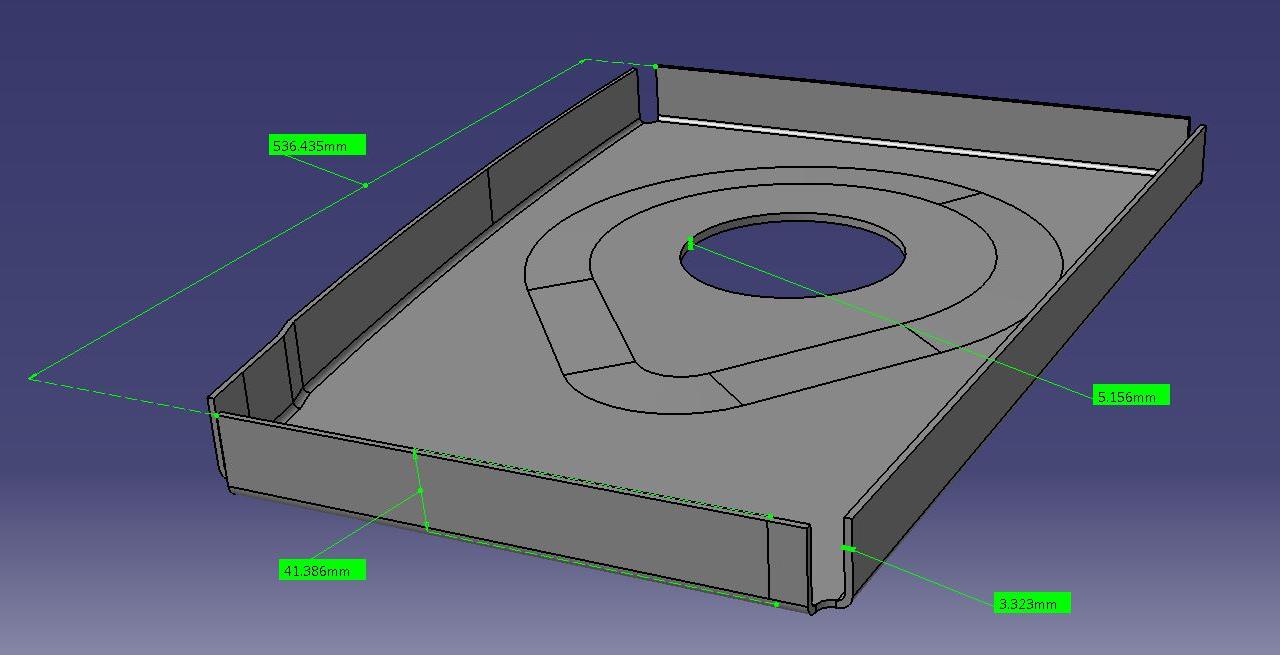
После того, как параметры обработки были установлены для панелей с бортиком TS-RAPM-009, процесс был повторен для выступа TS-RAPM-002, длина которого составляла 540 миллиметров. Толщина выступа в центре увеличилась с 3,3 до 5,2 миллиметра, а глубина вытяжки на окончательно обрезанной части составила 42 миллиметра. Все четыре кромки имели вертикальные фланцы. Обратите внимание, что угол компенсации подпружинения был определен во время испытаний панели с бортиком, а затем был применен к геометрии инструмента выступа. Испытания бортовых панелей также привели к более высокой способности к натяжению и модульному расположению пружин на пружинной раме.
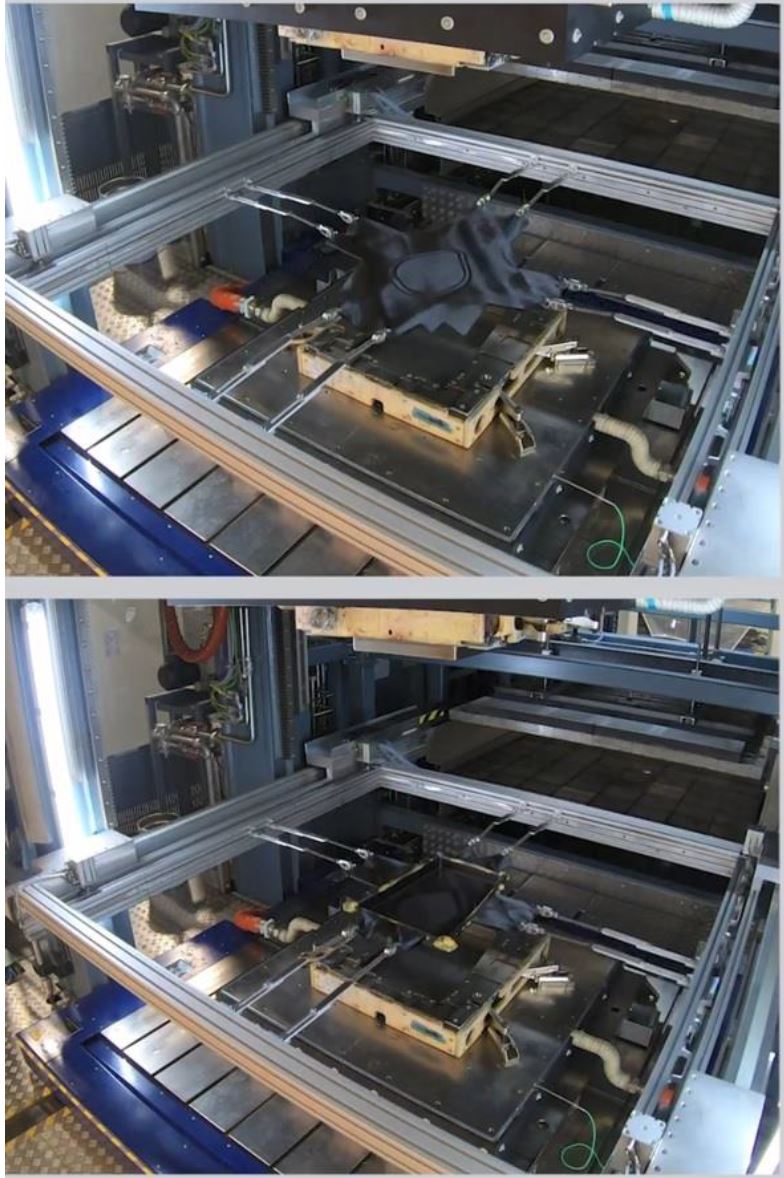
Лишний материал для зажимов
Ребра были изготовлены с использованием как пружинного каркаса, так и DDF. Из-за большой вытяжки ребра требовался излишек материала для крепления зажимов пружинной рамы, но его можно было уменьшить при использовании DDF. Другая проблема заключалась в том, что конструкция инструмента ограничивала пространство для размещения пружинных зажимов в непосредственной близости от полости инструмента.
Варианты CPT
Толщина затвердевшего слоя (CPT) была выше на плоских частях выступа, чем на его вертикальных краях. Было высказано предположение, что геометрия детали удерживала полимер в центральной плоской области, при этом отмечалось, что вертикальные фланцы действовали как полимерное уплотнение. Это способствовало уплотнению и чистовой отделке центральной ровной области. Однако вертикальные фланцы страдали от сильного сдвига во время закрытия инструмента, что вызвало шероховатость поверхности, но не пористость (см. Данные по пористости ниже). CYCOM EP2750, материал с меньшей насыпью, помог смягчить этот эффект - его меньшая толщина уменьшила сдвиг.
Вариации толщины полотна в зависимости от содержания препрега
Исследования качества показали повторяемость ребер с пористостью <0,1% и минимальной складчатостью / волнистостью волокон. Однако, хотя предполагалось, что изменение толщины детали будет минимизировано с помощью согласованной обработки пресс-формы, обзор параметров обработки материала и CPT готовой детали показал, что хотя инструментальный зазор в вертикальных фланцах выступа был фиксированным и постоянным, толщина стенки могла изменяться в зависимости от функции. содержания смолы препрега (менее +/- 2%) и процесса - CPT может варьироваться между фланцами и перегородкой, поскольку смоле позволяется мигрировать внутри полости.
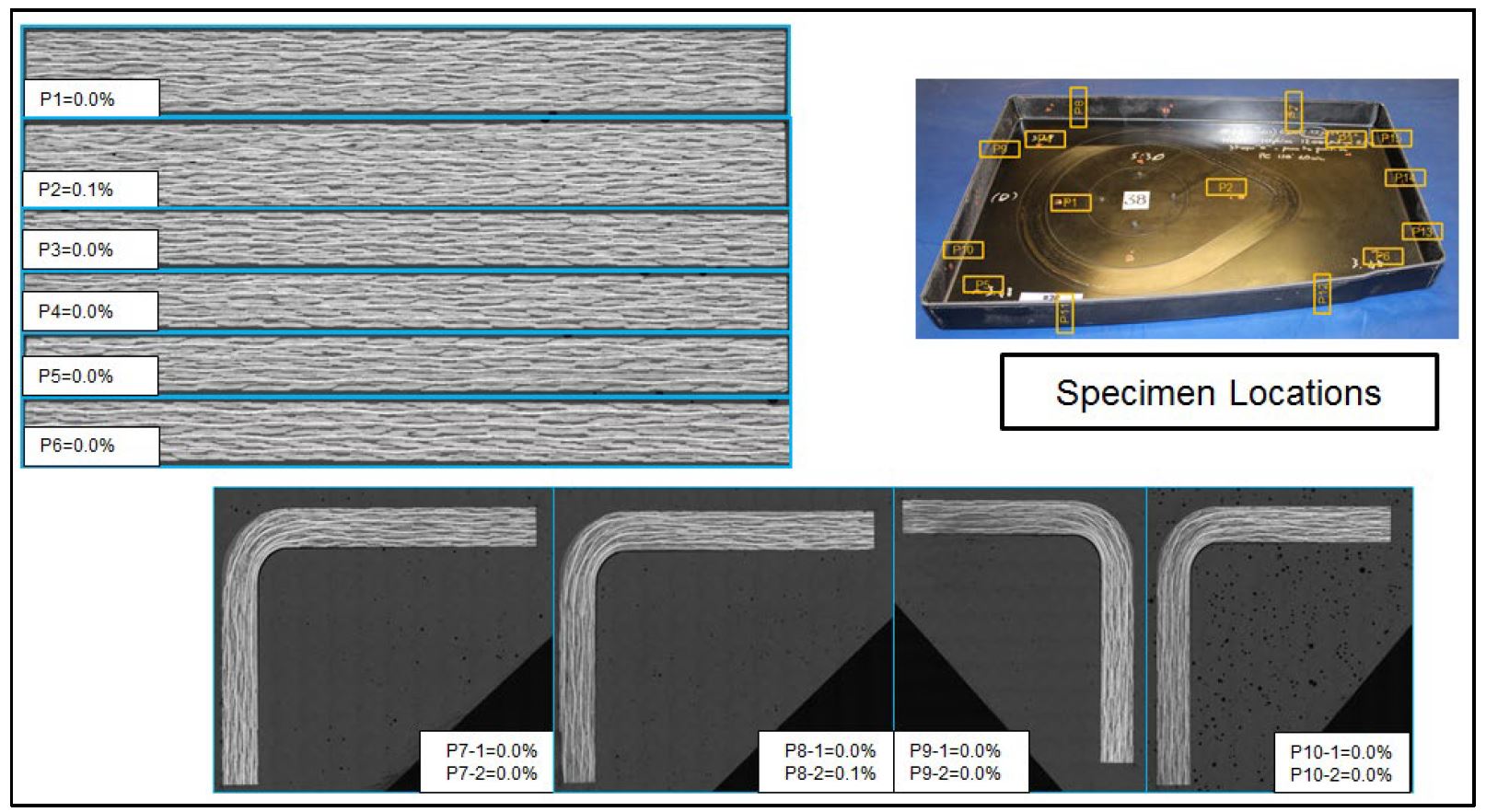
TS-RAPM-003 изогнутый С-образный канал
Эта деталь имела длину 640 миллиметров с U-образным сечением глубиной 40 миллиметров на окончательно обрезанной детали. Внутренний радиус секции был больше, чем внешний радиус, а толщина увеличилась с 6,6 миллиметра в узком участке до 8,8 миллиметра на широком конце. Из-за своей толщины С-образная часть была значительно тяжелее, чем предыдущие части. Поэтому пружинная рама требовала большего количества точек крепления, чем предыдущие детали.
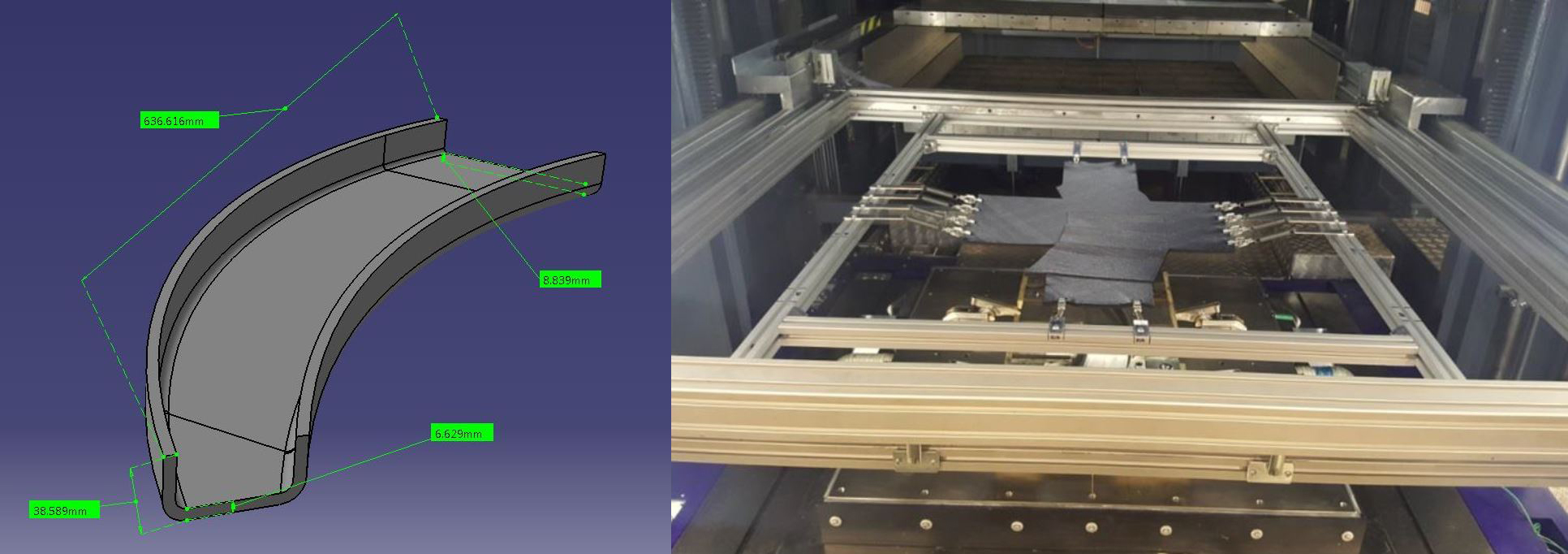
Двойная задержка для поддержания давления в толстых частях
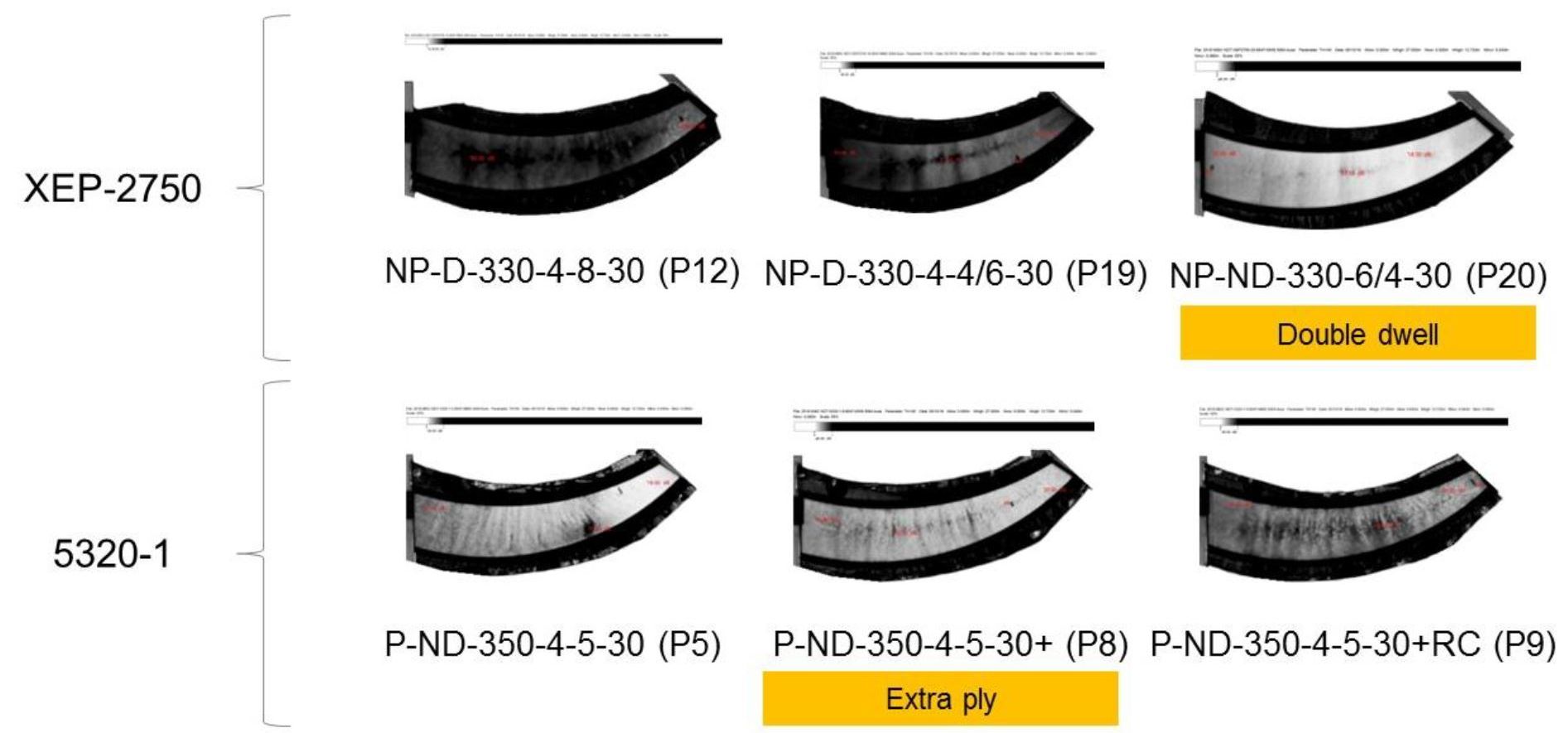
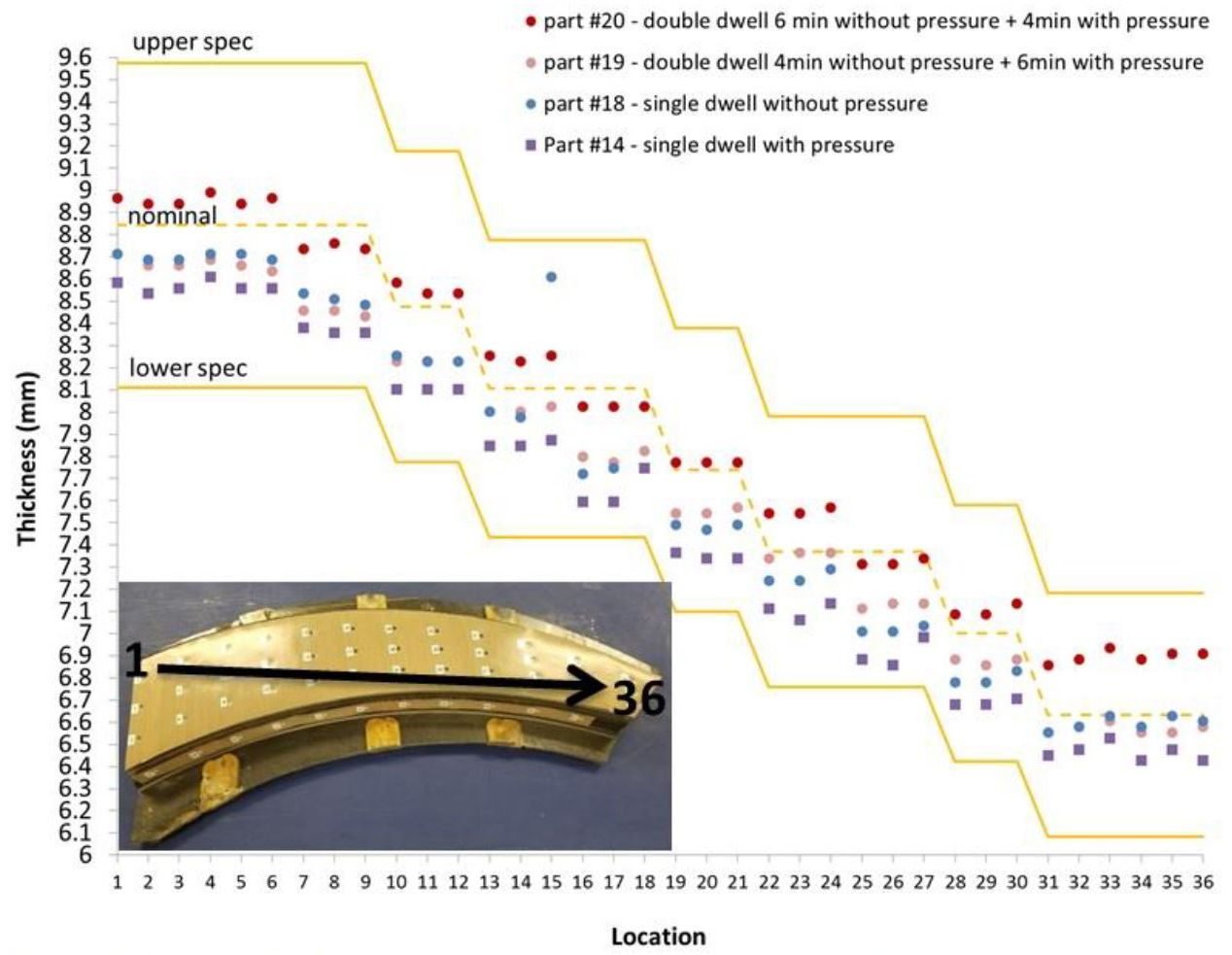
С-сканирование формованных деталей позволяет выявить складки, распространяющиеся от внутреннего радиуса к внешнему радиусу для деталей, изготовленных из предварительно уплотненных заготовок. Серая шкала указывает на то, что морщины также имеют пористость.
Эти морщины и пористость были удалены для деталей из препрега CYCOM EP2750 с помощью «двойной выдержки» . процесс. Он заключается в приложении определенного давления во время выдержки сразу после увеличения вязкости материала. «Это было определено с использованием данных, предоставленных прессой, и инструментов во время разработки процесса», - объясняет Хан. «По сути, есть два этапа постепенного увеличения давления до приложения полного давления. В результате профиль давления во времени имеет форму, аналогичную профилю вязкости смолы. Первоначальная выдержка при объемной толщине используется для увеличения вязкости смолы для предотвращения истончения загрузки материала [заготовки или преформы]. Если заряд имеет значительную толщину, используются две выдержки, чтобы предотвратить потерю давления из-за усадки смолы. Первая задержка находится в промежутке X, а вторая - в промежутке Y, причем Y
На рис. 18 выше показано влияние двойной задержки на толщину части С-образного канала. Согласование давления с вязкостью смолы позволило удерживать большее количество смолы в детали, что смачивало волокна для получения низкой пористости и толщины, необходимой для достижения требуемой номинальной, но сохраняющейся низкой деформации волокна. Однако команда RAPM подчеркнула, что этот процесс двойной выдержки предпочтителен только для более толстых деталей, отметив, что он может вызвать неравномерность CPT в деталях разной толщины.
Обсуждаемые здесь испытания деталей RAPM внесли вклад в высокопроизводительное производство деталей конструкции в аэрокосмической отрасли с использованием формовки препрега под давлением. Извлеченные уроки включают:
RAPM показал, что формование препрега под давлением может производить высококачественные конструкции аэрокосмического качества, сокращая при этом время цикла и трудозатраты. Это позволяет композитам лучше конкурировать в отраслевых исследованиях для аэрокосмических приложений, обеспечивая при этом повышенную экономию веса и улучшенные характеристики компонентов (например, устойчивость к коррозии, растрескиванию, усталости и т. Д.).
Solvay и Boeing вместе работали над усовершенствованием новой системы препрега EP2750, демонстрируя время такта до 20 минут благодаря сочетанию химического состава материалов, препрега, знания процессов и автоматизации.
В дополнение к частям развития производства, описанным выше, RAPM также произвел несколько частей Challenge и Transition, призванных бросить вызов начальные разработки и переход кандидаты с потенциалом победы над обработанным алюминием в оборонных приложениях. К ним относятся:
Результаты и уроки, извлеченные из этих испытаний деталей и других исследований производственных характеристик RAPM, будут опубликованы в 2020/2021 гг.
Solvay также проиллюстрировал, как EP2750 работает с автомобильными деталями, такими как центральная стойка размером 36 на 16 на 2 дюйма и толщиной 0,0725 дюйма, состоящая из 5 слоев углеродного волокна Solvay THORNEL T650-35 со стандартным модулем упругости 3K в корпусе 376 мм. грамм / квадратный метр сатиновой ткани с 8 жгутами. Эта деталь была изготовлена в Solvay Heanor, Великобритания, с использованием DDF. По сравнению со стандартным препрегом в автоклаве комбинация CYCOM EP2750 и DDF обеспечивает сокращение времени цикла на 60% и времени такта на 85% (время между запуском одной детали и следующей детали на производственной линии, т. Е. Время импульса линии) .
Извлеченные уроки RAPM и дальнейшие испытания деталей
Испытания автомобильных запчастей Solvay
Смола
- Компрессионное формование и литье под давлением:в чем разница?
- Компрессионное формование:как это работает
- Компрессионное формование и литье:плюсы и минусы
- Высокоэффективный промывочный агент для выдувных полиолефинов
- ПЭЭК высокой вязкости для литья под давлением и экструзии
- Конвейер, адаптированный для формования преформ
- Третий патент выдан на гибкий термопластический препрег
- Solvay запускает эпоксидный препрег для компрессионного формования авиационных конструкций
- Препрег для аэрокосмической промышленности Toray оптимизирован для вакуумного формования под давлением
- Непрерывные ленты, D-LFT встречаются в новом процессе компрессионного формования