Многослойные термопластические ленты, AFP и настой смолы для более демократичных композитов
Novotech (Неаполь, Италия) начиналась как дочернее предприятие Неаполитанского университета «Федерико II» на юге Италии, основанного профессором Леонардо Лечче в 1992 году. «Мы поддерживали авиастроительные компании общего назначения и предоставляли услуги НИОКР по всей Италии», - говорит Лечче. который сейчас является генеральным директором Новотех. «Мы провели структурный анализ деталей самолетов, а также помогли в разработке самолетов».
Компания Novotech, расположенная недалеко от завода Леонардо, который производит композитные секции фюзеляжа для Boeing 787, начала уделять особое внимание композитным материалам в 2014 году. Она приобрела ячейку для автоматической укладки волокна (AFP) у Coriolis Composites (Кевен, Франция) и разработала ее на базе автоклава ( OOA), включая вливание смолы и производство термопластичных композитов, со специальными знаниями в области консолидации на месте с использованием AFP.
Новотех участвовал во многих отраслевых исследовательских проектах, в том числе:
- MESEMA (Магнитоупругие энергетические системы для еще большего количества электрических самолетов)
- САРИСТУ (Интеллектуальные интеллектуальные авиационные конструкции)
- ASAM (Расширенное моделирование механизмов самолета)
- LAMITECH (Инновационные методы испытаний для автоматического наслаивания гибридных композитных материалов)
- ПРОАЛАТЕК (Структурная характеристика и анализ ремонтных решений инновационных оперения из углепластика)
- ЛИЦО (Дружественная обстановка в салоне самолета)
- AIRGREEN 2 - CLEAN SKY 2 (Разработка инновационных концепций и методологий крыла для региональных самолетов следующего поколения)
- ПРОВЕРКА СЕСТРЫ (Исследование и интеграция инновационной системы неразрушающего контроля AFP)
- ТРИНИТИ - CLEAN SKY 2 (баллоны с азотом высокого давления из многослойных термопластов для самолетов)
- НЕХИТЕ - H2020 (Новые гибридные термопластические композитные аэроструктуры, производимые OOA)
«У нас также есть особые отношения с Cytec в Великобритании, занимающейся разработкой новых композитных материалов и процессов», - говорит Лечче. Обратите внимание, что компания Cytec была приобретена компанией Solvay, а место, на которое указывается, - это компания Solvay Composite Materials в Хеаноре, Великобритания - сайт с долгой историей инноваций, включая процесс формирования двойной диафрагмы, недавно протестированный с помощью программы RAPM. «Нашей последней такой деятельностью была разработка процесса термопласта OOA с использованием нового инновационного пресса, который объединяет PEEK (полиэфирэфиркетон) и PEI (полиэфиримид) в новый композитный материал». Этот новый материал, оборудование и процесс теперь были продемонстрированы в стрингере самолета, армированном углеродным волокном (CFRP), сделанном с использованием AFP на месте консолидации и сварки в рамках проекта NHYTE.
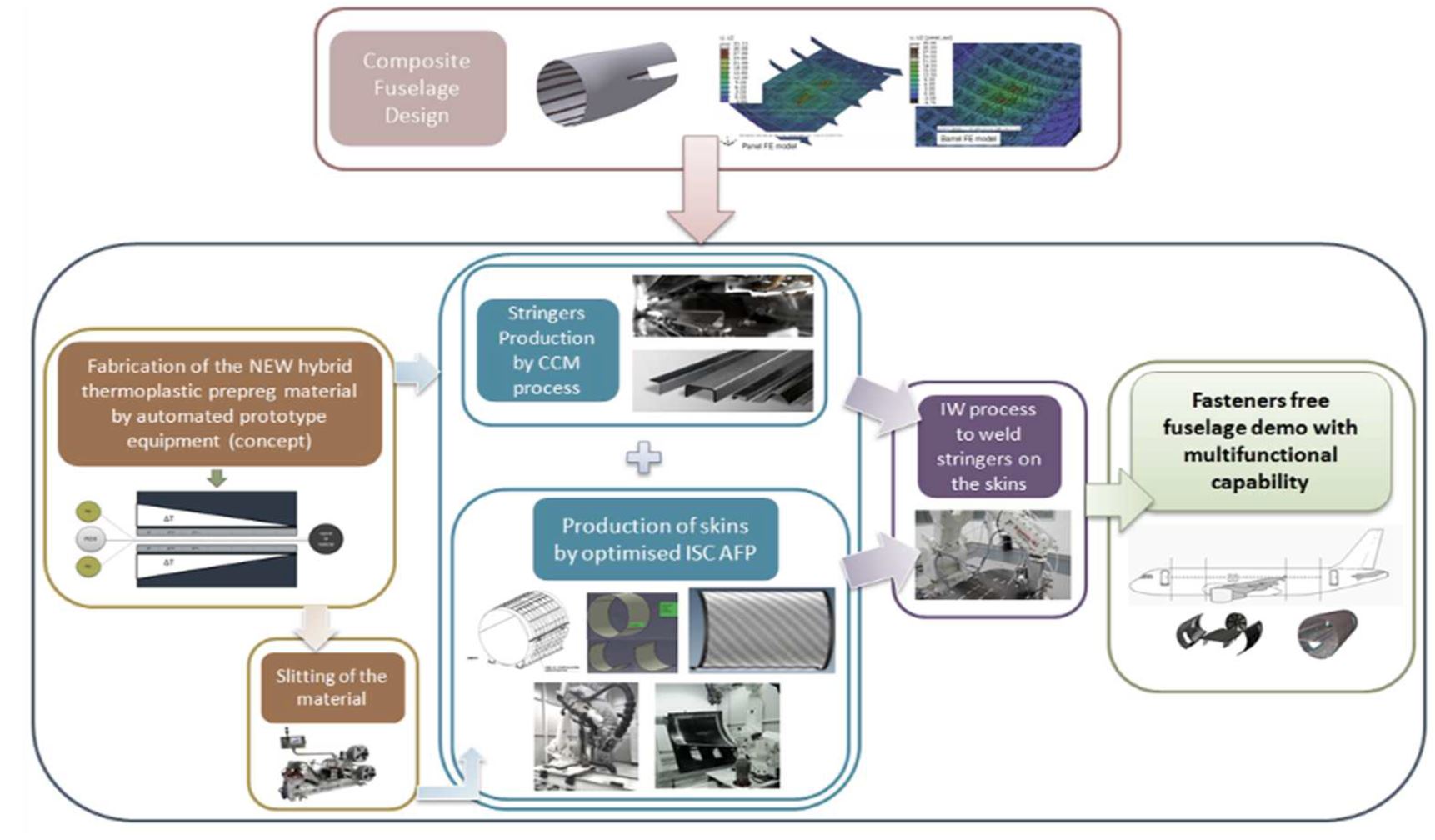
НЕХИТЕ
NHYTE - это исследовательский проект, финансируемый программой Европейской комиссии Horizon 2020, который проводится с мая 2017 года по октябрь 2020 года. «NHYTE использует аморфное соединение для обеспечения устойчивых температурных и технологических условий для термопластичных композитов», - поясняет д-р Марко Бариле, координатор проекта NHYTE. и технический директор Новотех. Это аморфное соединение (см. Диаграмму ниже) - это концепция, запатентованная другим партнером NHYTE, подразделением аэроструктур компании Leonardo (Рим, Италия), которое имеет несколько производственных мощностей на юге Италии.
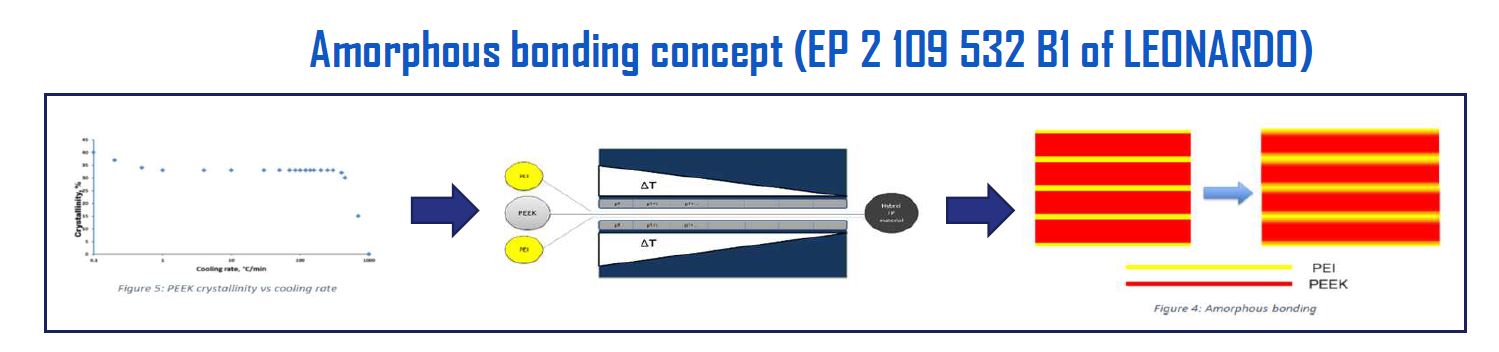
Фото:проект NHYTE
«С материалом, разработанным в NHYTE, мы можем преодолеть текущие ограничения материалов с помощью AFP на месте (ISC) термопластичных композитов (TPC). Вместо того, чтобы обрабатывать полукристаллические полимеры PEEK при температурах чуть ниже 400 градусов C, мы можем нагревать аморфный слой PEI чуть выше 215 градусов температуры стеклования (Tg). Плавление и охлаждение PEI также происходит быстрее, и его не нужно так контролировать по сравнению с PEEK ». Бариль отмечает, что в этой концепции можно использовать и другие аморфные термопласты. PEI был выбран потому, что он хорошо сцепляется с PEEK, материалом, хорошо зарекомендовавшим себя на нескольких демонстраторах аэроструктуры AFP.
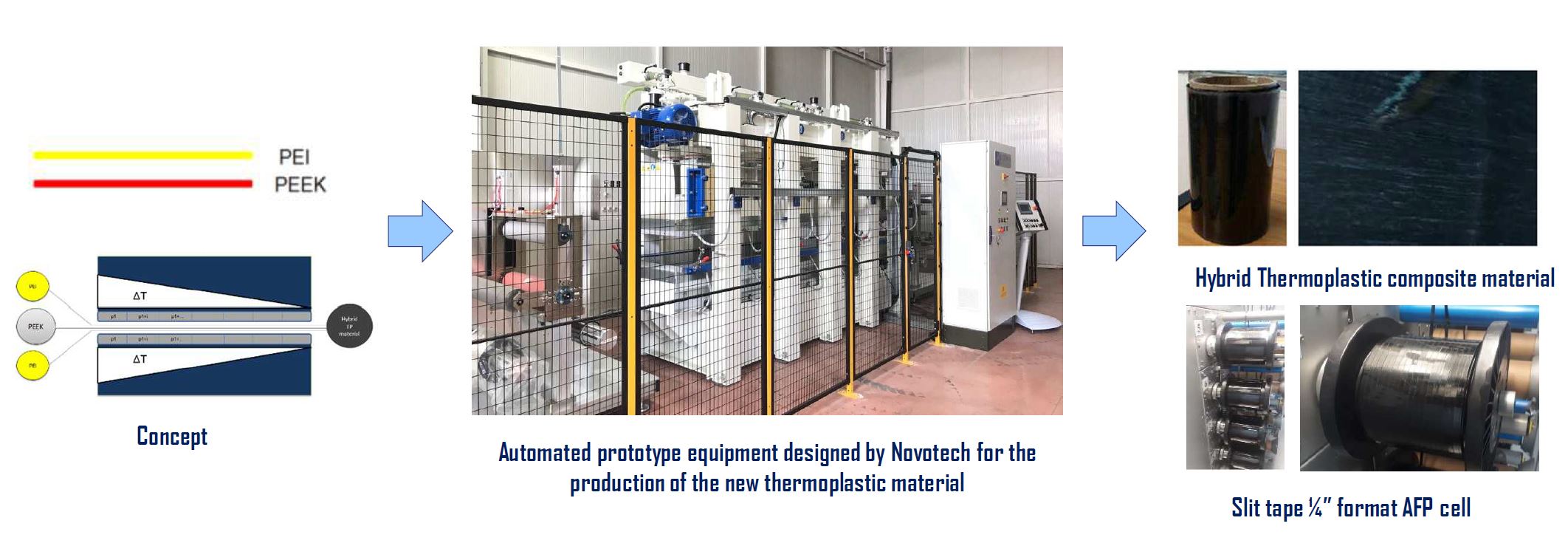
Этот новый материал, разработанный в NHYTE, был произведен в прессе непрерывного действия, разработанном NOVOTECH. Orma Macchine (Бергамо, Италия) поставила корпус пресса, а COMEC Innovative (Кьети, Италия) - модули намотки и разматывания. «Этот пресс может изготавливать непрерывный рулон материала, который мы затем разрезаем на разрезную ленту для использования в машине AFP», - говорит Бариле. Три разных материала входят в пресс слева, как показано на изображении выше. «У нас есть PEI сверху и снизу, а затем PEEK в середине», - объясняет Барил.
Как полукристаллический полимер, PEEK обеспечивает высокие механические свойства, необходимые для первичных структур, в то время как аморфные слои PEI обеспечивают быстрое и простое плавление для склеивания. «Мы контролируем давление и охлаждение материала вдоль плит пресса, начиная с примерно 400 ° C в начале пресса до менее 200 ° C в конце пресса. В результате получается один материал, который представляет собой комбинацию трех входных слоев ».
Этот новый вид термопластической ленты уже уплотняется во время производства, поэтому во время AFP ее нужно только нагреть, чтобы расплавить и уплотнить слои PEI для аморфного связывания. В результате получается ламинат, состоящий из полностью консолидированной ленты из ПЭЭК в ПЭИ и из слоев ПЭИ в ПЭИ, как показано в патенте Леонардо. Этот процесс AFP представляет меньше препятствий по сравнению с текущим AFP ISC с использованием лент из PEEK и PEKK (полиэфирэфиркетон). Как объяснялось в части 2 моей статьи 2018 года по консолидации на месте, текущий AFP ISC требует нагрева ленты и подложки до температуры плавления, размещения ленты на подложке и последующего уплотнения роликом, чтобы процесс охлаждения точно контролировался, что позволяет полукристаллические полимеры для достижения достаточно высокой кристалличности (30-40%) и низких пустот (<3-5%) для структурных свойств.
Критики AFP ISC утверждают, что он слишком медленный - скорость укладки 60-100 мм / с по сравнению с 600-700 мм / с для «двухэтапного» метода, включающего быструю укладку AFP с последующей вторичной стадией в печи или автоклаве для полного закрепить / отжечь термическое напряжение в ламинате. «С нашим материалом вы можете добиться темпа укладки AFP, которые не такие медленные, как при обычном уплотнении на месте, а нагрев, необходимый во время AFP, также может поддерживаться ниже 300 ° C», - говорит Бариле. «Вы можете заполнить пробел в производительности, используя стандартные материалы, которые у нас есть сейчас». Здесь Barile сравнивает AFP ISC термопластичных композитов с термореактивными композитами, используемыми в самолетах Boeing 787 и Airbus A350. «С крупными компонентами, такими как секции фюзеляжа, проблема заключается в доступности при использовании автоклавного отверждения. Термопласты обеспечивают более доступный производственный процесс, но у вас есть высокие температуры и низкие показатели AFP с материалами аэрокосмического качества, доступными в настоящее время на рынке. Наш подход помогает решить эти вопросы. С помощью непрерывного пресса мы можем достичь кристалличности ленты около 30 процентов. Таким образом, у вас есть эта кристалличность в детали и вы работаете только с аморфным слоем во время AFP. Хотя это все еще экспериментальный материал, который можно улучшить, цель проекта NHYTE - создать одноэтапный производственный процесс, который можно использовать в аэрокосмических конструкциях ».
Оптимизация ленты и AFP
«Первые многослойные ленточные материалы были изготовлены здесь, в Новотехе, - говорит Бариле. В этих лентах использовалась незаполненная щелевая пленка Ultem 1000 Sabic (Эр-Рияд, Саудовская Аравия) для PEI и армированная углеродным волокном лента PEEK APC-2 / AS4 от Solvay. Общая толщина составляла ≈0,26 миллиметра, включая слои PEI толщиной 1 или 2 мил (0,001 или 0,002 дюйма). На первом этапе проекта несколько образцов обоих вариантов были испытаны на прочность на межслойный сдвиг (ILSS), чтобы подтвердить процесс производства гибридного термопластического материала. Небольшие купоны также были протестированы партнером NHYTE Applus Laboratories (Барселона, Испания) на предмет полного диапазона механических свойств, включая прочность на растяжение и сжатие, а также модуль упругости, сжатие в открытом стволе (OHC), растяжение в заполненном отверстии, сжатие после удара (CAI), едва видимые ударные повреждения (BVID) и свойства после кондиционирования жидкости.
«У нас не было такого же опыта, как у поставщиков термопластичных композитных лент, поэтому качество материала можно улучшить. Например, объем волокна варьируется от низкого до высокого по толщине, что влияет на свойства ленты и ламината, включая ILSS. Но NHYTE была нацелена на демонстрацию концепции, которую мы и сделали ».
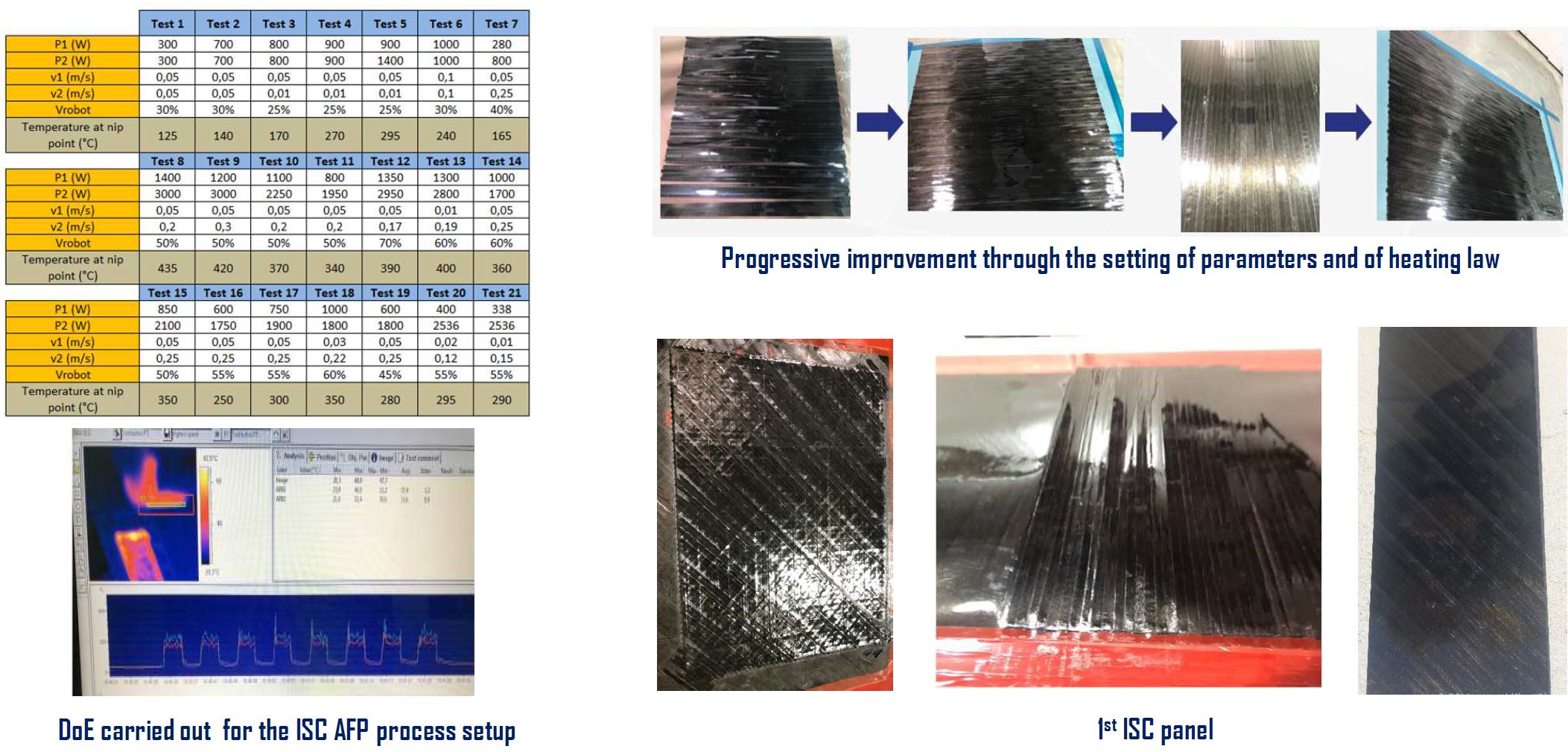
Как видно на изображениях выше, оптимизация процесса AFP для нового материала потребовала значительной экспериментальной работы. «Мы также использовали подход планирования экспериментов (DOE) для оптимизации параметров AFP, а партнер NHYTE Университет Южной Бретани (USB, Лорьян, Франция) разработал инструмент для улучшения нагрузки лазерного нагрева с помощью прогнозирующего численного моделирования». отмечает Бариле.
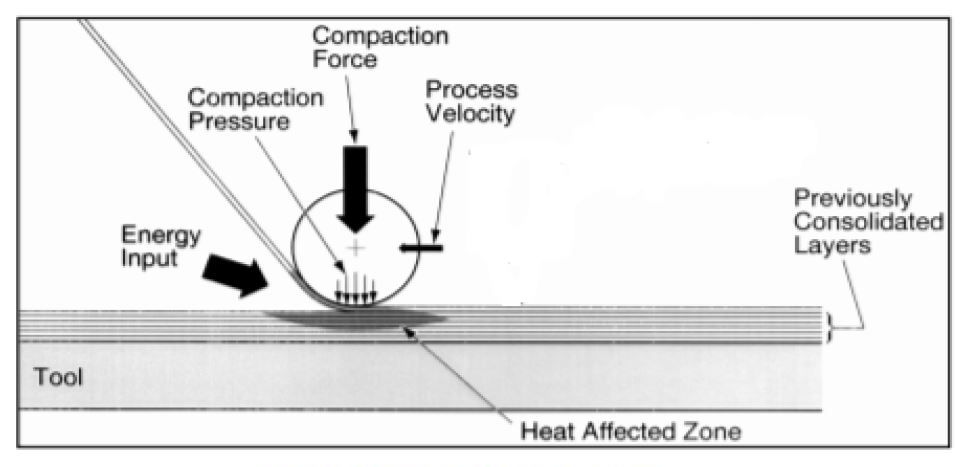
Это моделирование было сначала использовано на ленте APC-2 для проверки качества прогнозирующего инструмента, а затем оно было применено к новому многослойному материалу. Статья по этой работе отправлена для публикации в журнал Composite Structures . . «Вы моделируете теплопроводность в точке контакта», - говорит Бариле. «Затем мы экспериментально проверяем то, что было предсказано при численном моделировании. Это необходимо для определения наилучшего компромисса между скоростью укладки, текучестью расплава полимеров и старением [варкой] композитной пластинки. Это баланс нескольких переменных в процессе консолидации на месте. Смотрим на снижение температуры поступающей ленты на уже наложенную на инструмент ленту. Если вы справитесь с этим изменением температуры, вы сможете уменьшить остаточное напряжение в ламинате. Итак, мы работали над тем, чтобы оценить изменение температуры во время укладки. Вы должны настроить обогрев в соответствии с формой траектории и ориентацией пластинки.
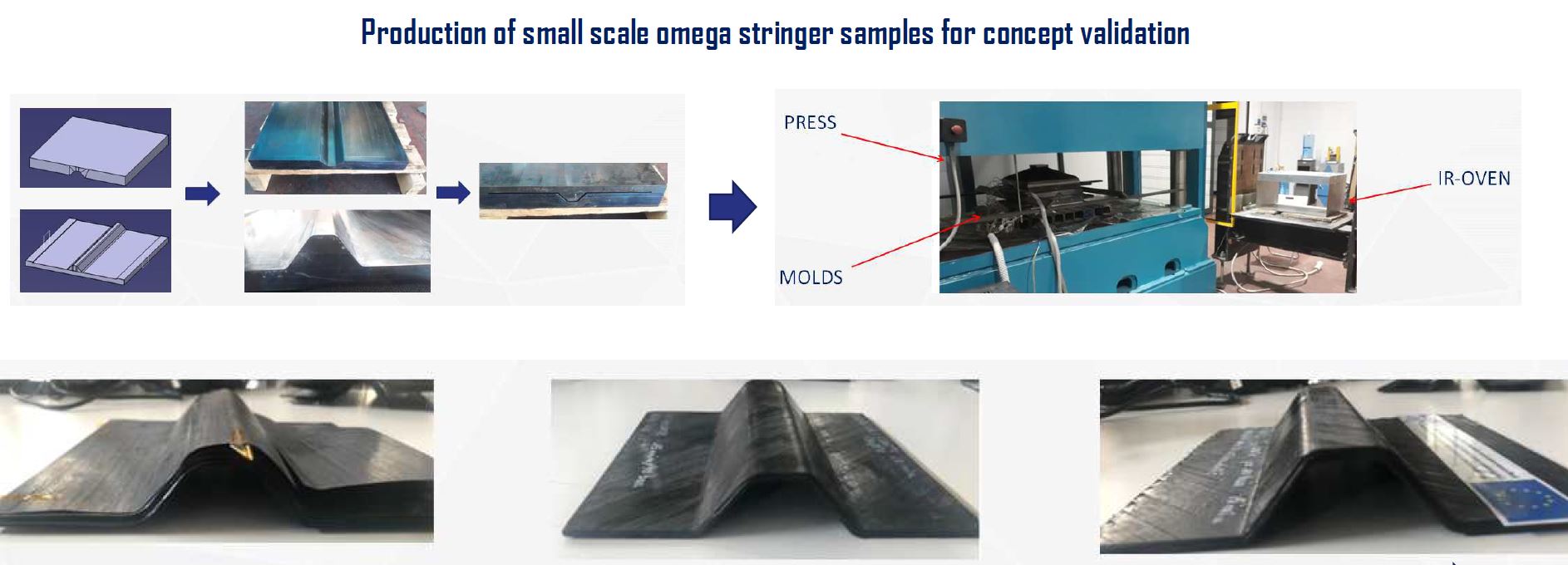
Демонстраторы стрингера и фюзеляжа
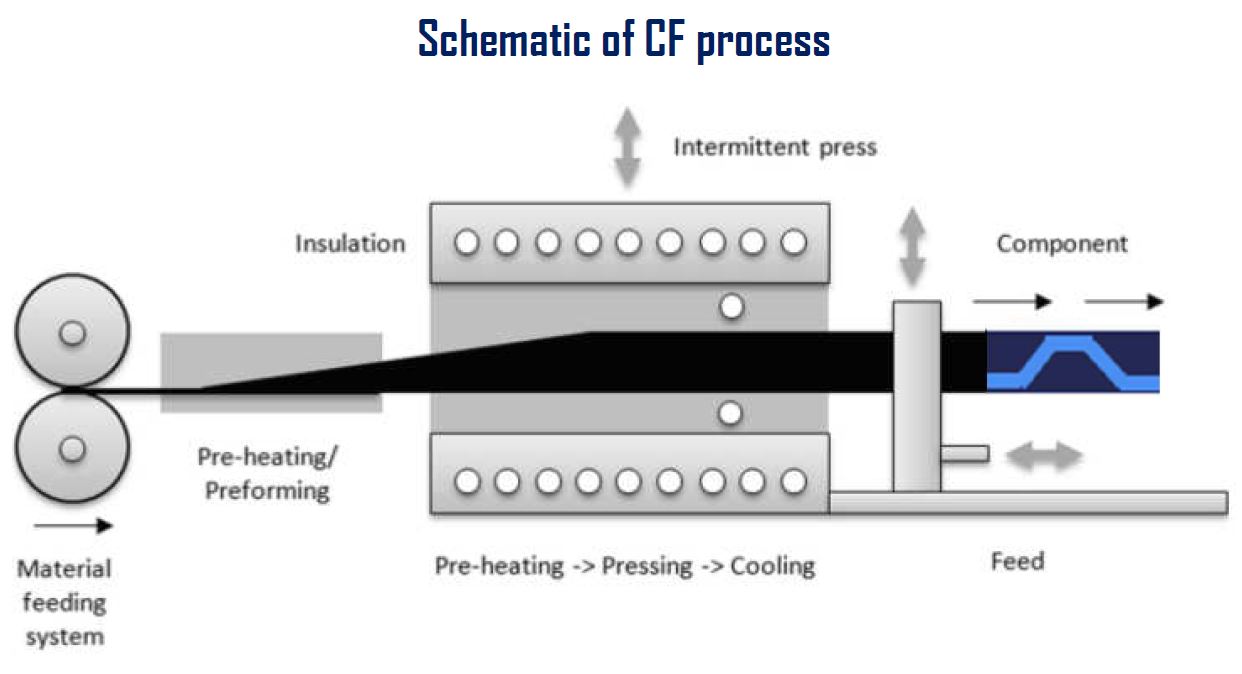
Следующим шагом было изготовление демонстраторов стрингеров, сначала в виде небольших образцов, изготовленных с помощью стационарного пресса, а затем как демонстраторов непрерывного процесса формования стрингеров для проверки того, что потребуется для производства промышленных деталей. Затем эти стрингеры были прикреплены к демонстрационной панели обшивки фюзеляжа AFP с помощью индукционной сварки, разработанной научно-исследовательской организацией CETMA (Бриндизи, Италия).
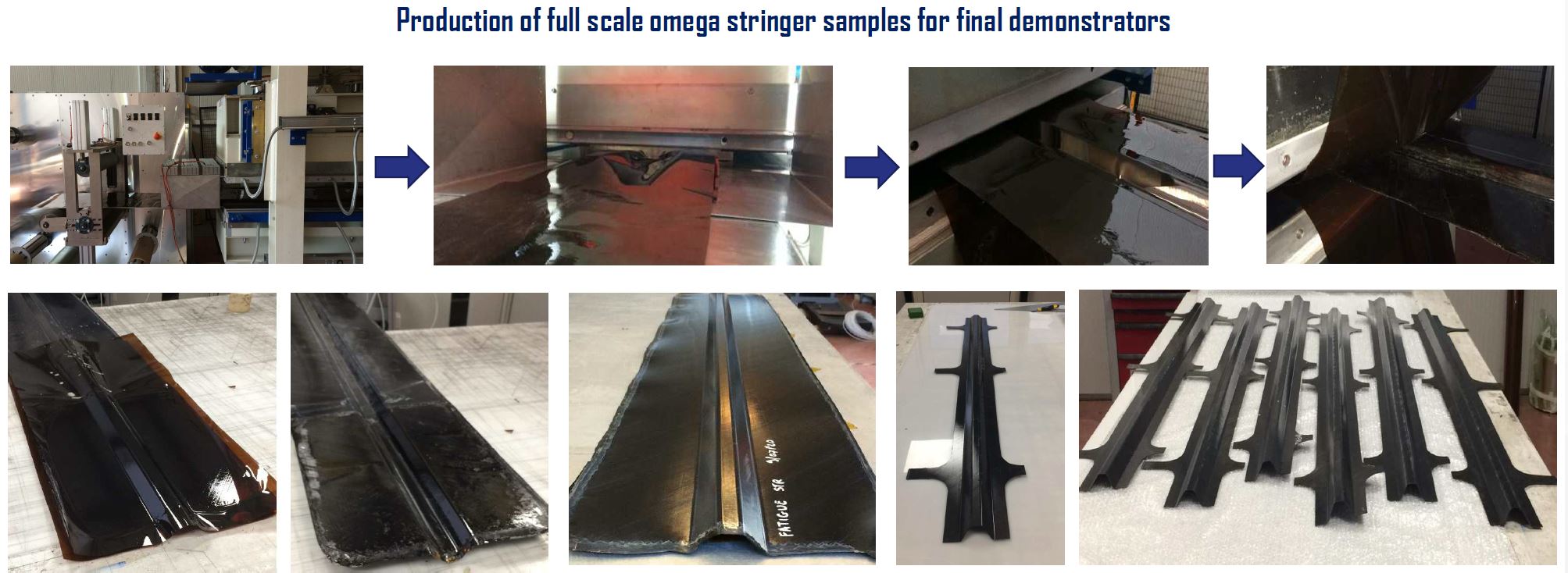
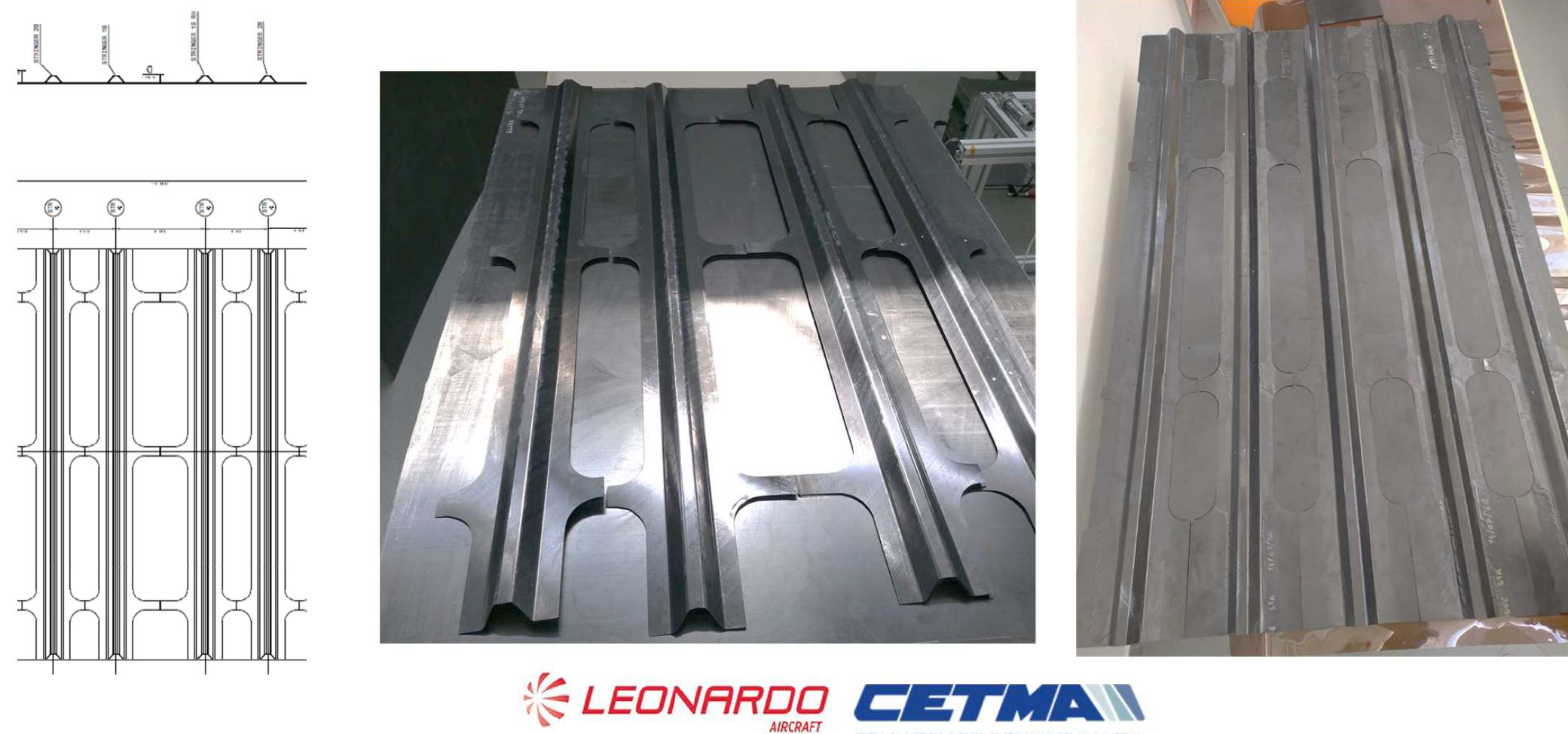
Предлагал ли новый многослойный материал какие-либо преимущества для индукционной сварки? «По сути, он обрабатывал то же самое», - говорит Бариле. «Однако CETMA было непросто определить параметры процесса сварки, потому что в нашем новом материале меньше углеродного волокна по сравнению со стандартными лентами». Затем Applus провела испытания демонстраторов стрингеров и окончательной демонстрации панели фюзеляжа. Партнеры проекта NHYTE Университет Бата (Бат, Великобритания) и компания Leonardo Aircraft также использовали NDI для оценки качества панелей и стрингеров.
«Мы сделали много купонов и мелких деталей, а также большой демонстратор», - отмечает Бариле. «Результаты тестирования Applus очень хороши, учитывая более низкую стоимость производственного процесса по сравнению с тем, что сейчас является стандартом. Наши характеристики прочности и жесткости на 20-25% ниже по сравнению со стандартными термопластичными лентами, доступными в настоящее время, но мы выявили улучшения в процессе, которые должны помочь улучшить это ».
NHYTE завершился 30 октября 2020 года. «Наша идея состоит в том, чтобы продолжить работу над новым проектом, включающим все запланированные нами улучшения», - говорит Бариле. «Мы доказали, как изготавливать материал и как обрабатывать его, используя AFP консолидацию на месте, непрерывную формовку и индукционную сварку. Теперь нам нужно продолжить оптимизацию для индустриализации ». Новотех стремится продолжить работу с тем же консорциумом, но с новыми партнерами.
Примечательно, что Леонардо также работает над улучшением консолидации AFP на месте с помощью индукционной сварки и ленты TPC, которую можно быстро нагревать и охлаждать. Вдобавок обнадеживающие результаты по многослойным композитам PEI / PEEK были только что опубликованы исследователями IMDEA Materials Institute (Мадрид, Испания) и FIDAMC (Мадрид, Испания), последний уже много лет является лидером в консолидации AFP на месте. Дополнительные технические статьи см. В публикациях NHYTE.
Проект SWING
Smart Wing для новой авиации общего назначения (SWING) - это проект, который начался с одобрения Piaggio Aerospace (Вилланова-д’Альбенга, Италия) и софинансируется Министерством экономического развития Италии (MISE). Помимо Novotech, итальянский проектный консорциум включает в себя компанию по развитию технологий Protom (Неаполь) в качестве координатора, Laer Aeronautical Manufacturing (Airola), A. Abete Aerostructures (Nola) и специалиста по аэрокосмическому дизайну ItalSystem (Avellino). Одна из целей SWING - адаптировать автоматизированные процессы изготовления композитов вне автоклава (OOA), включая AFP и инфузию жидкой смолы (LRI), для экономичного и устойчивого производства небольших самолетов с использованием P.180 Avanti переднее крыло в качестве демонстрационной площадки.
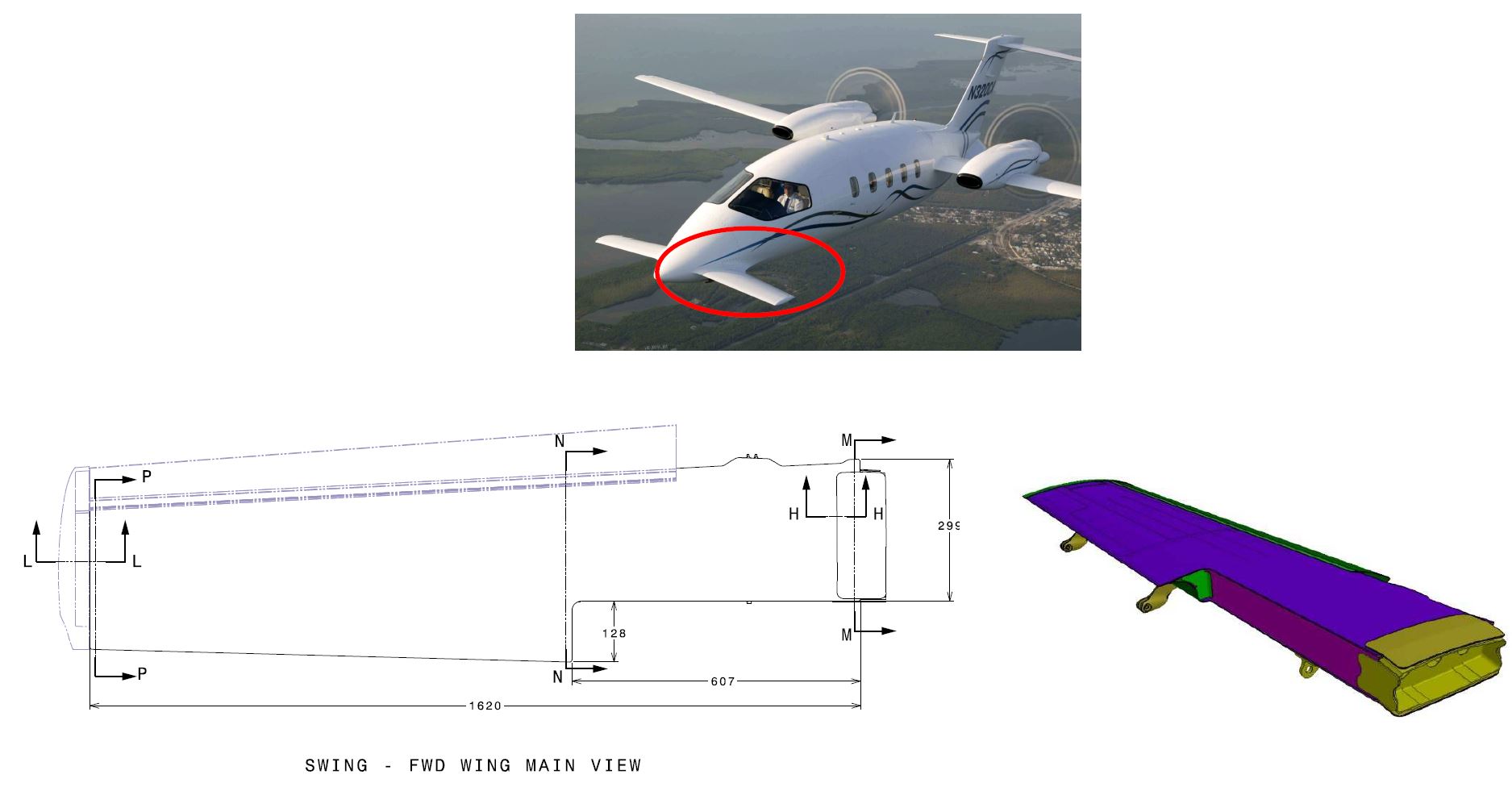
«Идея состоит в том, чтобы сделать переднее крыло P.180 всего из двух основных частей:верхней панели и нижней панели, обе отлитые со встроенными стрингерами и лонжеронами», - говорит Лечче.
«Для нас это началось с нашей работы в качестве квалифицированной лаборатории для Solvay в Великобритании. С 2015 года мы сотрудничаем с новыми материалами и процессами для AFP, LRI и термопластичных композитов. Мы делали сухие преформы, используя ленту из сухого волокна PRISM TX1100 компании Solvay для использования с AFP. Затем эти преформы были пропитаны усиленной эпоксидной смолой Solvay PRISM EP 2400 и отверждены в печи. Мы выполняли эту работу в рамках проекта AIRGREEN 2 для программы экологически чистых региональных самолетов Clean Sky 2, а затем продолжили работу над проектом SWING ». Отметим, что PRISM TX1100 и PRISM EP 2400 прошли квалификацию Объединенной авиастроительной корпорации на производство первого пропитанного смолой крыла для коммерческого самолета - узкофюзеляжного реактивного лайнера «Иркут МС-21» производства компании «Аэрокомпозит».
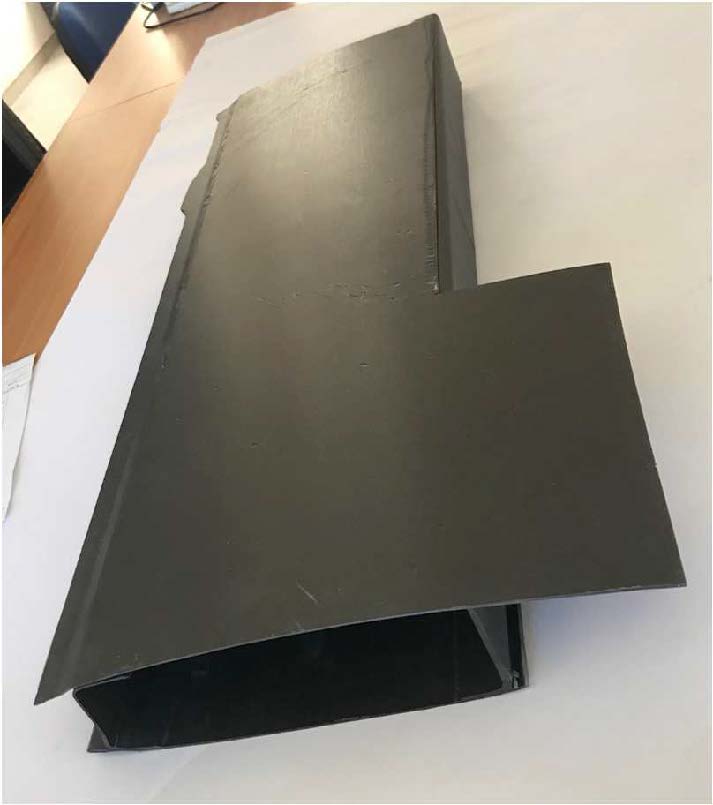
Формованные верхняя и нижняя панели будут соединены с помощью структурного клея, а в следующем году будут проведены статические испытания. «Параллельно мы описываем еще один композит на основе сухой ленты TX1100 и смеси смол от Covestro (Леверкузен, Германия), который может быть валидной альтернативой смолам аэрокосмического качества, в частности, для секторов, где требуется более высокая производительность», - добавляет Бариле. «Эта смола не так эффективна, как эти системы, но она хорошо работает с инфузией и отвечает требованиям к кессону крыла. Если вы хотите снизить стоимость, должен быть какой-то компромисс. Мы надеемся, что эта разработка будет способствовать внедрению технологии AFP в авиацию общего назначения. Его также можно использовать в автомобильном секторе ».
ТРИНИТИ
Новотех также участвует в проекте «Чистое небо 2» TRINITI - резервуары с азотом высокого давления из многослойного термопласта для самолетов, который начался в 2019 году и завершится в 2021 году. Участие Новотеха в этом проекте снова стало результатом разработки итальянской аэрокосмической компании. «Мы работали над проверкой потенциала AFP, используя нашу многослойную ленту при производстве криогенных топливных баков для ракет-носителей, по сравнению с применяемыми в настоящее время процессами намотки нити накала», - объясняет Бариле. «По сути, TRINITI разработает концепцию многослойного материала, аналогичную NHYTE, а затем создаст резервуар, используя уплотнение на месте AFP».
«Преимущество AFP по сравнению с FW, - продолжает он, - состоит в том, что вы можете решить, где вы хотите разместить материал. Вы не ограничены нитью накала, непрерывно наматываемой на деталь. Рассмотрим резервуар, в котором у вас много материала на торцевых крышках, потому что вы не можете разрезать материал во время наматывания нити. При резке и перезапуске волокна / лент в нужном месте с помощью AFP материал используется только там, где это необходимо. Таким образом, вы можете управлять промежутками между лентами, что важно для предотвращения проникновения газа. Чтобы сделать это с намоткой из нити, вам нужно увеличить количество наносимого материала, даже потому, что с AFP вы используете ленту с разрезом, а не буксирную ленту. А при консолидации на месте отпадает необходимость в автоклаве. Мы продемонстрировали, что AFP может быть реальной альтернативой и очень доступной ».
«В настоящее время CETMA проводит испытания на газопроницаемость, чтобы оценить характеристики многослойных материалов в соответствии со спецификациями», - говорит Бариле. Специалисты компании Diehl Aviation (Гильхинг и Дрезден, Германия) представили требования к баллону с азотом длительного хранения высокого давления, используемому в системах пожаротушения самолетов. Эти баки должны выдерживать температуру от -55 ° C до 85 ° C на земле, от -40 ° C до 70 ° C во время полета и давление до 1000 бар.
«Цель состоит в том, чтобы уменьшить вес и уменьшить количество производственных операций», - отмечает он. «Однако стоимость производства с использованием этого метода должна быть определена. Вес снижен за счет отсутствия ненужного материала, но намотка нити - более быстрый процесс по сравнению с AFP ». Другой фактор заключается в том, что резервуары этого типа обычно имеют металлическую или пластиковую облицовку, покрытую углепластиком. Барил говорит, что ТРИНИТИ пытается создать танк без лайнера (Тип V). «Мы избежим газопроницаемости, используя ламинат AFP с низким уровнем пустот. Сейчас мы тестируем в CETMA различные комбинации материалов и готовимся к понижению выбора. Затем мы построим прототип резервуара, но конструкция резервуара зависит от выбранного материала и окончательного процесса. Итак, это то, над чем мы работаем сейчас. Работы по тестированию будут проводиться CTL Composites (Голуэй, Ирландия) ».
ЧАЙКА
Сложный проект SEAGULL стартовал три года назад. «Наша цель - разработать малый гидросамолет нового поколения, который сочетает в себе новую технологию производства композитов, гибридную электрическую силовую установку и автоматизированное складывающееся крыло, которое мы разработали и запатентовали», - поясняет Лечче. «Мы хотели создать самолет с укороченным взлетом и посадкой (STOL), который может конкурировать с самолетами с вертикальным взлетом и посадкой (VTOL), но предлагает большую доступность. Мы считаем, что это может быть личный самолет, управляемый с любой поверхности, и это важная возможность для будущего аэронавтики и мобильности ».
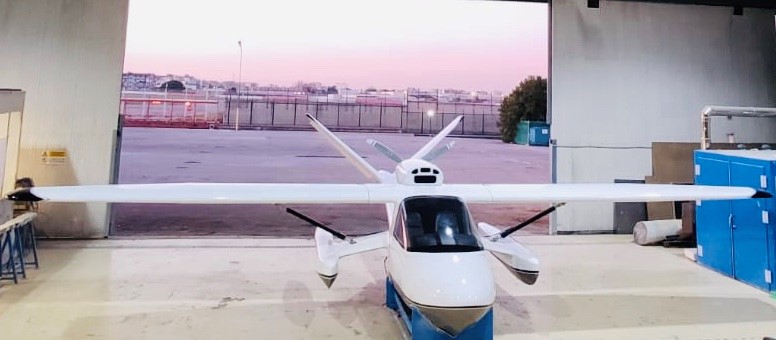
Команда SEAGULL испытала гибридную силовую установку, построила первый прототип в воде и начала испытания в воде в октябре. «После завершения испытаний мы построим летающий прототип в течение следующих нескольких месяцев», - говорит Лечче. «Это очень опытная команда, состоящая из крупных компаний с более чем 50-летним опытом работы в авиации общего назначения».
Летающий прототип SEAGULL будет иметь составные фюзеляж, хвостовое оперение и крыло. «Мы снова будем продвигать применение автоматизированного производства с использованием AFP и инфузии смолы», - говорит Бариле. «Одна из основных проблем с композитами, использующими эти процессы, - это стоимость материалов. В самом деле, мы пытаемся найти также сочетание материала и процесса, более демократичное с точки зрения затрат ».
Смола
- Fraunhofer IPT разрабатывает термопластичные композиты для хранения водорода, лопаток двигателей и т. д.
- Composites Evolution демонстрирует высокоэффективные препреги, новые термопластические ленты UD
- Проектирование для автоматизированного производства композитных материалов для малосерийных авиационных к…
- Термопластические ленты продолжают демонстрировать потенциал для создания композитных аэроструктур
- Перерабатываемые, ремонтируемые и перерабатываемые эпоксидные смолы для композитов
- Карл Майер запускает линию по производству термопластичных UD-лент
- SWM запускает проточную среду Naltex для инфузии смолы
- Двери из термопласта впервые для автомобильных композитов
- Консорциум термопластичных композитов нацелен на крупносерийное производство для автомобильной и аэрокосм…
- Обслуживание мира композитов в Израиле и США