Проектирование для автоматизированного производства композитных материалов для малосерийных авиационных конструкций
Производство композитных авиационных конструкций для коммерческих самолетов длится более 50 лет и неуклонно прогрессирует от более мелких деталей до очень крупных основных структур - фюзеляжа, крыльев, оперения, двигателей - разработанных в начале 2000-х годов для Boeing 787 и Airbus A350. Подавляющее большинство этого развития зависело от использования препрегов из углеродного волокна / эпоксидной смолы, отверждаемых в автоклаве, которые сначала укладывались вручную, а затем, в конечном итоге, с помощью автоматической укладки волокон (AFP), автоматической укладки ленты (ATL) и других машинных процессов.
Эти технологии материалов и процессов (M&P) были подходящими для широкофюзеляжных самолетов 787 и A350, скорость сборки которых до пандемии составляла 10-15 единиц в месяц. Однако, поскольку Boeing и Airbus смотрят в будущее и рассматривают возможность применения композитных материалов в основных конструкциях узкофюзеляжных самолетов, которые, как ожидается, будут строиться со скоростью 60-100 в месяц, дизайн и M&P будут отдавать предпочтение высокопроизводительным, нестандартным решениям. -автоклав (OOA), высокоавтоматизированные процессы. Эти процессы включают, среди прочего, литье смолы с переносом (RTM), прессование и вливание жидкой смолы.
Но даже если высокопроизводительное производство будет преобладать в коммерческом авиакосмическом секторе, изготовление композитных авиационных конструкций для низкоскоростных самолеты, в том числе региональные самолеты и программы бизнес-джетов, не только сохранятся, но могут и должны получить выгоду от некоторых из тех же самых затратных, конструктивных и конструкторских инноваций, которые будут использоваться в высокопроизводительных программах.
Учитывая все это, в рамках программы European Clean Sky 2 была запущена программа OPTICOMS - Opti mized Com posite S конструкции для малой авиации. OPTICOMS - это консорциум, возглавляемый производителем аэрокосмической промышленности Israel Aerospace Industries (IAI, Лод, Израиль) с партнерами, которые поставляют инновационные технологии автоматизации, материалы, программное обеспечение, инструменты и оборудование. Цель OPTICOMS - оценить конструкцию кессона крыла, производимую с низкой производительностью, которая отличается автоматизированным производством, интегрированными структурами, отверждением OOA, большим структурным соединением, инновационным производственным и сборочным инструментарием, мониторингом состояния структурных соединений и виртуальным тестированием.
Арнольд Натан, директор по исследованиям и разработкам авиационной группы в IAI и менеджер OPTICOMS, говорит:«Каждый раз, когда мы пытаемся включить автоматизацию в [обсуждение] производства композитов, мы часто слышим, как наши клиенты говорят:« Автоматизация - это хорошо, но только когда у вас большой объем производства ». OPTICOMS был создан, чтобы выяснить, можете ли вы оправдать автоматизацию, когда вы этого не делаете иметь крупносерийное производство. Может ли автоматизация производства композитов быть конкурентоспособной и рентабельной для небольших объемов? »
Дизайн крыльев
OPTICOMS был рожден в результате запроса Clean Sky 2 итальянского производителя самолетов бизнес-класса Piaggio Aerospace (Генуя) на разработку полностью композитного альтернативного крыла для его P180 Avanti бизнес-класс с двумя турбовинтовыми двигателями с девятью пассажирами. Кессон крыла имеет длину 6,8 метра, ширину 0,71 метра у основания и 0,28 метра на вершине. По словам Натана, Piaggio очень хотел оценить альтернативу цельнометаллическому унаследованному кессону крыла - альтернативу с такими же размерами, но с меньшим весом (20%). Кроме того, следует снизить стоимость на 20-30% по сравнению с традиционным производством кессона крыла из композитных материалов. IAI и ее партнеры выиграли контракт и начали работать с Piaggio в 2016 году.
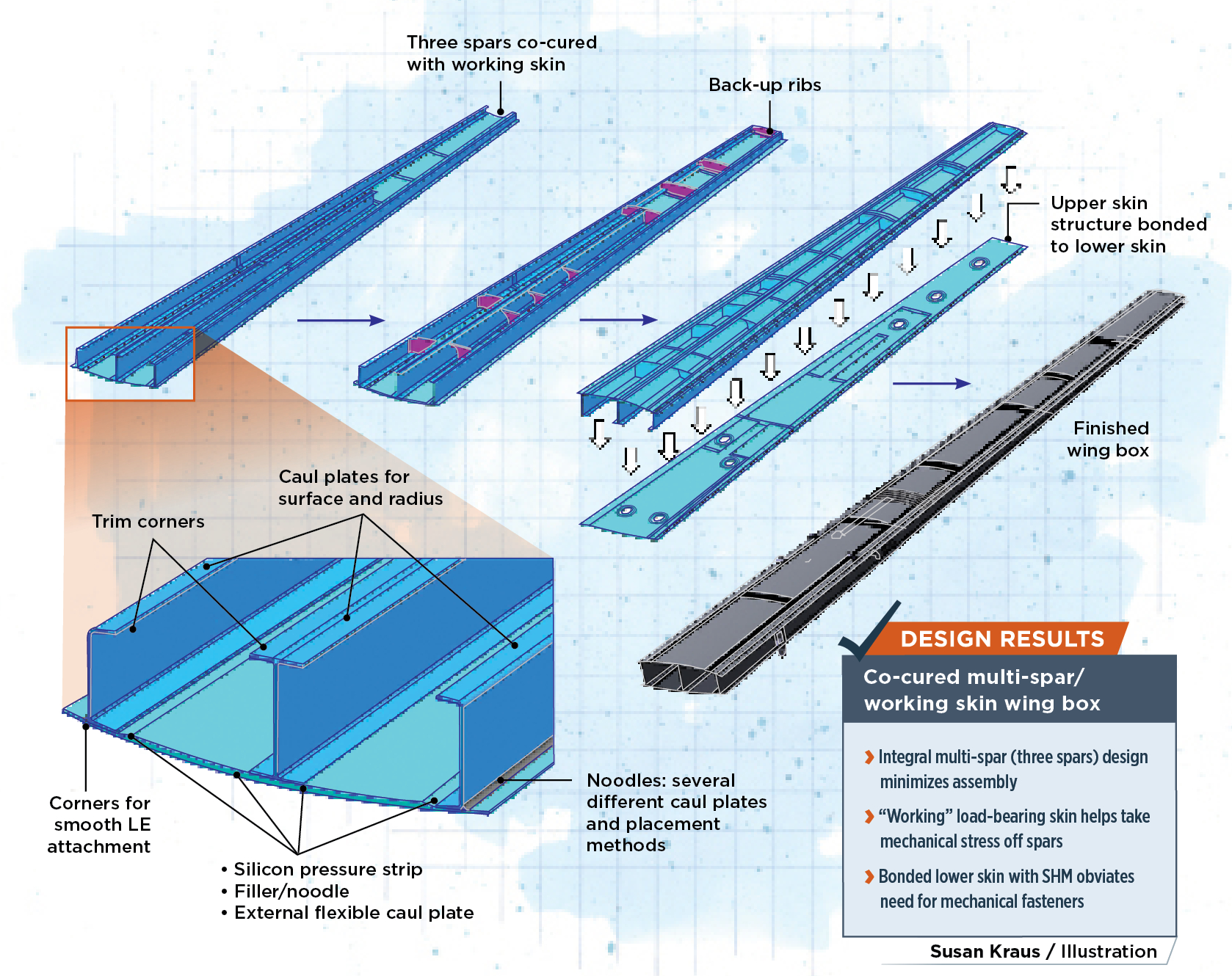
OPTICOMS - это программа, состоящая из нескольких частей, предназначенная для выполнения серии высокодетальных и кропотливо проведенных торговых исследований для оценки и определения оптимальной конструкции крыла, комбинации материалов и процесса изготовления OOA для автоматизированного производства цельнокомпозитного кессона крыла небольшого объема.
IAI и OPTICOMS, говорит Натан, на раннем этапе решили сосредоточиться на трех производственных процессах, предоставляемых тремя партнерами, и оценить их использование:автоматизированный роботизированный захват и укладка сухих и предварительно обработанных тканей, поставляемый Techni-Modul Engineering (TME, Coudes, Франция); автоматизированная укладка волокон (AFP) из сухих и предварительно подготовленных жгутов, поставляемых Coriolis Composites (Queven, Франция); и технология автоматической укладки сухого материала (ADMP), поставленная Danobat (Эльгойбар, Испания). Выбор этих технологий и партнеров будет иметь решающее значение для руководства IAI на протяжении всего исследования многовариантной торговли.
Результаты дизайна
- Интегральная конструкция с несколькими лонжеронами (три лонжерона) минимизирует сборку.
- «Рабочая» несущая обшивка помогает снять механические нагрузки с лонжеронов.
- Склеивание нижней части кожи с помощью SHM устраняет необходимость в механических застежках.
Первым шагом в этом торговом исследовании была оценка дизайна. Эту работу в IAI возглавил Адам Содей, инженер-конструктор по передовым технологиям. Содей говорит, что он и IAI применили чистый подход к конструкции крыла, изучив более 18 концепций для различных архитектур. Дизайн быстро попал в одну из двух категорий. В первом используется «рабочая» обшивка, в которой обшивка кессона крыла становится несущей конструкцией. Во втором - нерабочие обшивки с заряженными лонжеронами. В рамках этих категорий конструкции включают традиционную концепцию нервюр, стрингеров и двух лонжеронов, или, в качестве альтернативы, использование трех лонжеронов, называемых многолонжеронными, без нервюр или стрингеров. В нескольких концепциях также рассматривалось использование конструкции из сэндвич-панелей, создающих полурабочую обшивку.
«Наша мантра заключалась в том, чтобы сократить трудозатраты на производство и сборку», - говорит Содей. «И мы считаем, что если вы сможете разработать более эффективную и более целостную структуру, то вы получите более дешевую и легкую структуру».
Содей говорит, что дизайн сравнивался с рядом показателей, чтобы оценить их способность соответствовать целевым показателям стоимости и веса программы. Эти показатели включают в себя:материальные затраты, сложность конструкции, затраты на изготовление компонентов, затраты на сборку, затраты на неразрушающий контроль (NDT), затраты на инструменты и отсадку, вес, прочность, уровень технологической готовности (TRL), экологические соображения, профиль риска, надежность и надежность. Из них наиболее важными критериями были вес, стоимость изготовления и сборки, сложность конструкции, TRL и профиль риска.
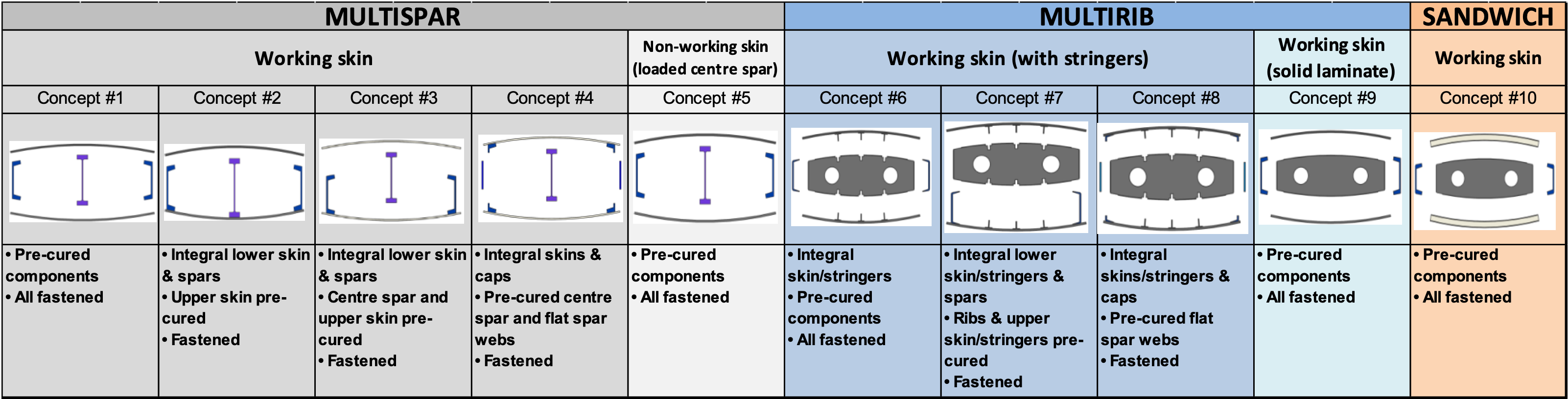
Переход к окончательному дизайну
Данные этой оценки помогли IAI отобрать концепции дизайна до 10 финалистов. Четыре были многолонжеронной / рабочей обшивкой, одна - многолонжеронной / нерабочей обшивкой с нагруженными лонжеронами, четыре - многолонжеронной / рабочей обшивкой со стрингерами, одна - многореберной / рабочей обшивкой без стрингеров и одна - сэндвич-панелями. структура / рабочая обшивка без стрингеров. Каждый дизайн предлагал различные комбинации предварительного отверждения, совместного отверждения, склеивания или механического крепления.
Чтобы получить окончательный дизайн, потребовался еще один раунд торговых исследований с использованием многих из тех же критериев, что и в первом исследовании. Каждому дизайну была присвоена торговая ценность в зависимости от того, насколько хорошо он соответствует критериям. «У нас была большая таблица компромиссов, и каждый вариант дизайна имел свою ценность, и это помогло нам увидеть самый сильный вариант», - говорит Содей.
Содей отмечает, что с самого начала был один дизайн, который неизменно хорошо давал результаты в торговых исследованиях и, похоже, оказался на высоте. Так оно и было. Изнутри получивший название многолонжеронная / рабочая кожа №2, она отличается высоко интегрированной и совместно отвержденной обшивкой верха и тремя лонжеронами. Затем они прикрепляются к нижней обшивке, имеющей панели доступа. Между лонжеронами избирательно расположен ряд «опорных» нервюр, предназначенных для поддержки обшивки, которая принимает на себя большую часть изгибающих нагрузок.
«Самыми подходящими конструкциями, которые мы разработали, - говорит Содей, - были конструкции с несколькими лонжеронами, в которых обшивка становится несущей. Таким образом, лонжероны становятся более простыми и тонкими и не такими тяжелыми, как в традиционных композитных конструкциях крыла. Мы подумали, что, если бы мы могли просто сделать эти лонжероны очень простыми, с постоянным поперечным сечением, это избавило бы от многих головных болей и много отходов ».
Содей говорит, что склеенная интегральная конструкция с несколькими лонжеронами и рабочей обшивкой показала особые перспективы благодаря снижению затрат на сборку, малому весу, простоте автоматизации и общему малому количеству деталей. Однако оставался вопрос:какие материалы и какие производственные процессы лучше всего подходят для воплощения этой конструкции в жизнь?
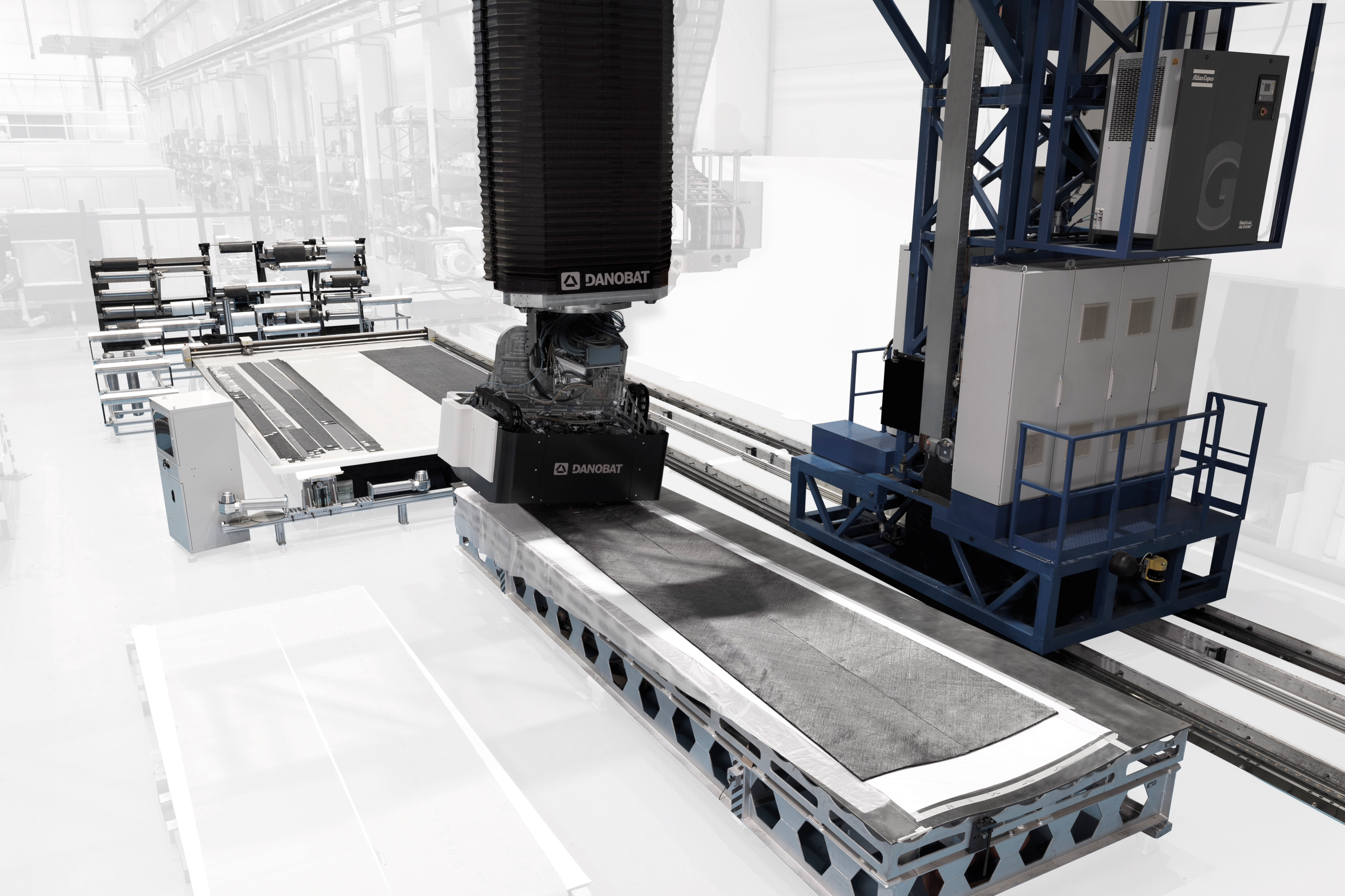
Исследования торговли M&P
Сначала были исследования торговли материалами. Их выполнил в IAI инженер по композитным материалам Янив Юрович. Он говорит, что OPTICOMS приступила к оценке препрегов из углеродного волокна OOA, сухих углеродных волокон (лент и тканей) и смол на основе рекомендаций Piaggio, IAI и технологических партнеров. В результате был составлен список из 35 новых материалов.
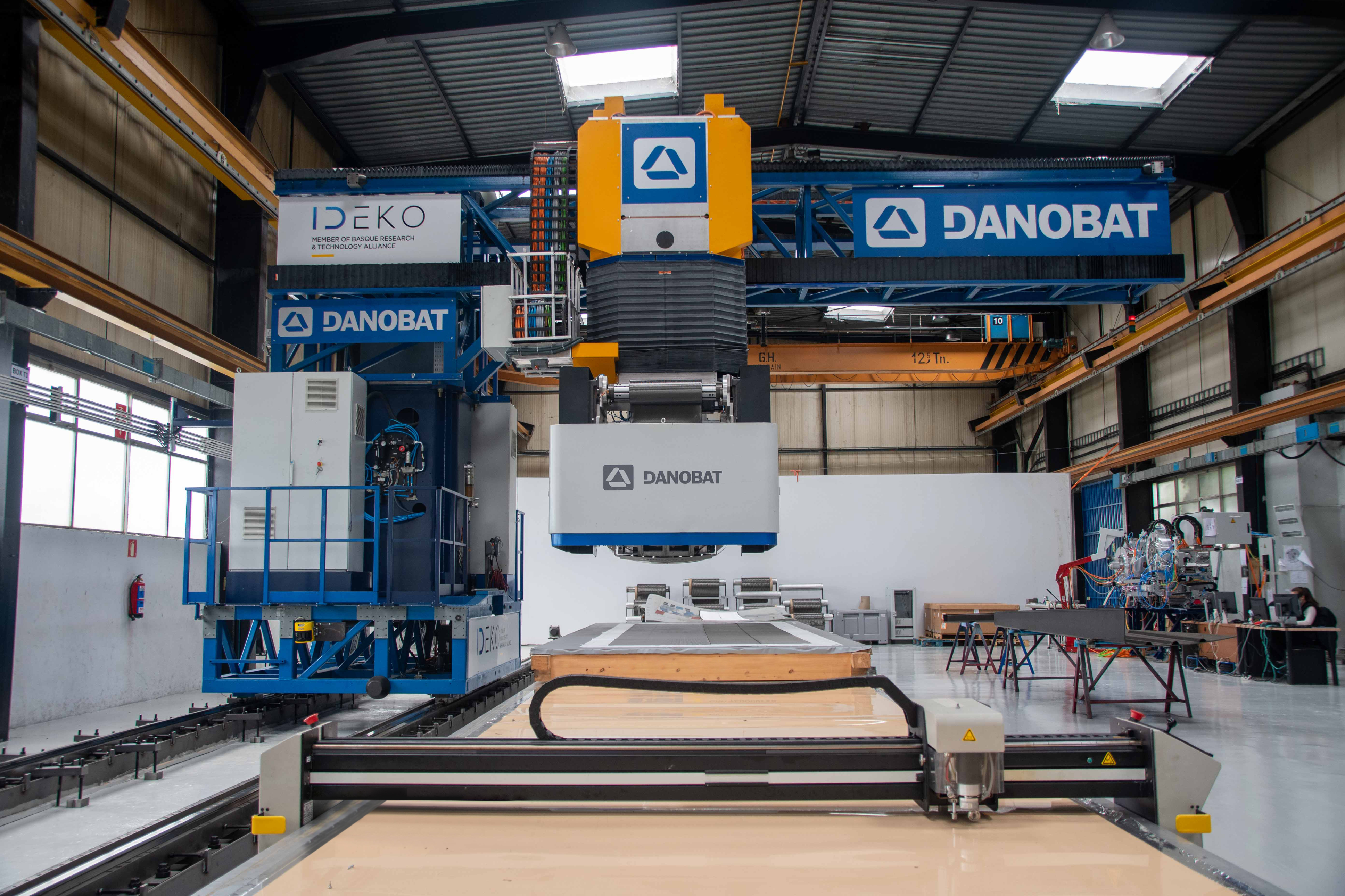
Затем эта первая группа материалов была проверена на основе наиболее важных параметров для проекта OPTICOMS:стоимость, температура стеклования (T g ), вязкость (для инфузии или инъекции) и пригодность для автоматизированных технологий укладки. Эта оценка сократила список материалов с 35 до 20 препрегов, сухих волокон и смол.
Были заказаны образцы каждого из этих 20 материалов; Затем Юрович изготовил купоны и провел механические испытания в рамках следующего понижающего отбора. «Это был действительно большой объем работы, - говорит Юрович. «Это позволило нам принять больше решений и выбрать последние три материала». Эти комбинации волокна / смолы:
- Toray Composites Materials America’s (Такома, Вашингтон, США) 2510 углеродное волокно / эпоксидный препрег.
- Hexcel’s (Стэмфорд, Коннектикут, США) ленты HiTape из углеродного волокна UD для использования с эпоксидной смолой HexFlow RTM6 компании Hexcel.
- Углеродное волокно без обжима (NCF), поставляемое SAERTEX (Saerbeck, Германия), для объединения путем инфузии с упрочненной эпоксидной смолой PRISM EP2400 компании Solvay Composite Materials (Alpharetta, Джорджия, США).
Этот список явно поддерживает использование сухих волокон, что, в свою очередь, способствует использованию инфузии в качестве производственного процесса. Натан говорит, что это отчасти вызвано проблемой управления сроком хранения препрега в условиях малых объемов. «Когда вы говорите о малотиражном производстве, вы действительно не хотите носить с собой много препрега и беспокоиться об управлении сроком годности», - говорит он. «У сухого волокна такой проблемы нет».
Эти три материала также были объединены с одним или несколькими производственными процессами, выбранными для OPTICOMS:препрег Toray совпадает с самовывозом и AFP, Hexcel HiTape / RTM6 совпадает с AFP, а также с подбором и размещением, и SAERTEX NCF совпадает с Pick-and-Place или ADMP.
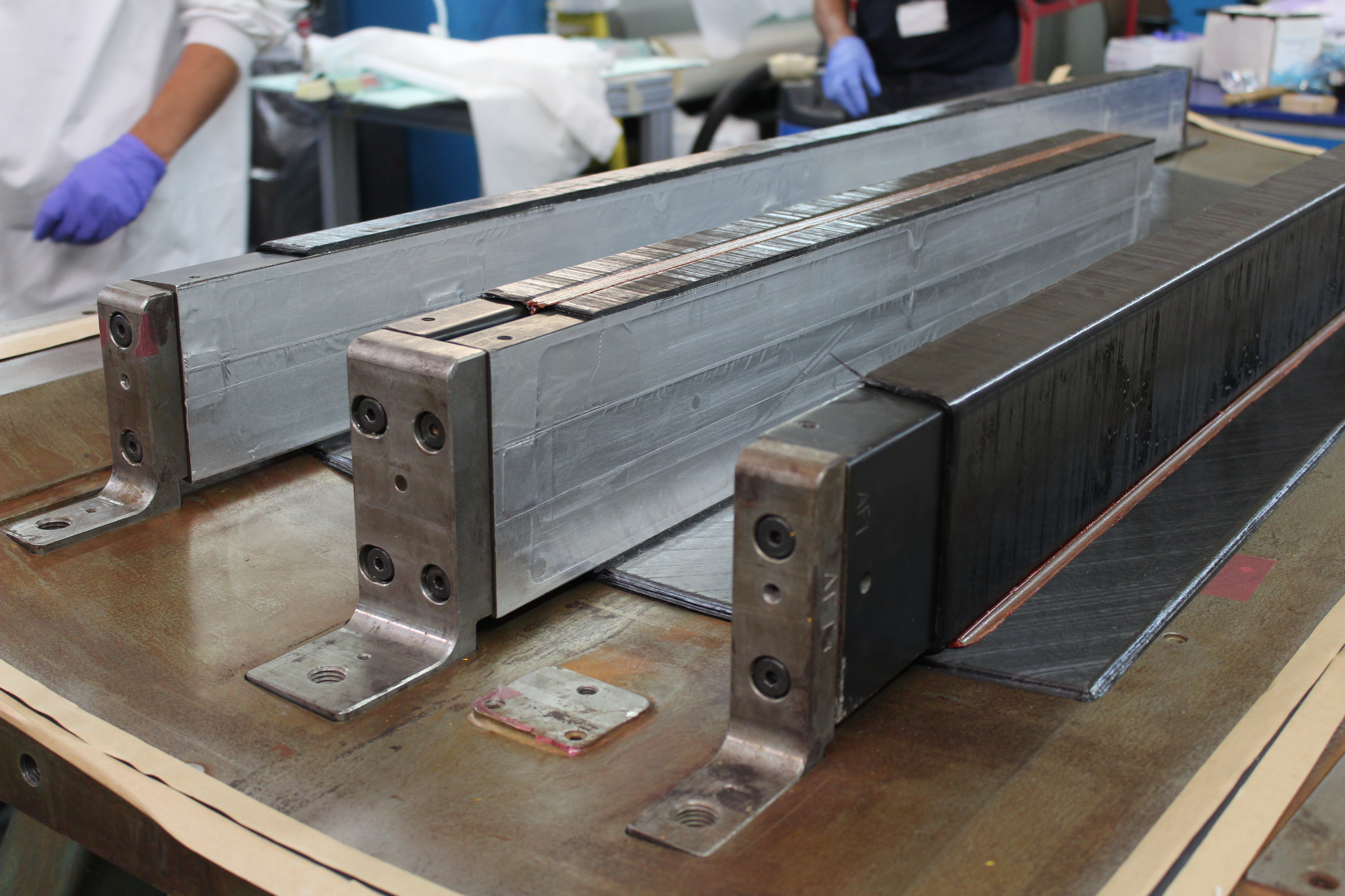
Торговля вокруг автоматизированных производственных процессов - которая лучше всего подходит для того, какой тип детали - все еще осуществляется IAI и OPTICOMS. Однако предварительные результаты, по словам Натана, определенно указывают технологии в определенных направлениях. Например, технология ADMP компании Danobat, первоначально разработанная для быстрой укладки широкой ткани при производстве лопастей ветряных турбин, оказалась столь же эффективной в OPTICOMS. Эта технология получила развитие во время OPTICOMS, и ее надежность и надежность были улучшены, но это все еще менее развитая технология аэрокосмического ремонта по сравнению с AFP.
Напротив, AFP с системой Кориолиса, с ее обширным аэрокосмическим опытом, является зрелой и точной технологией, но имеет более длительное время простоя по сравнению с ADMP и требует относительно частых проверок для выявления аномалий. По словам Натана, Кориолис добился заметного прогресса на протяжении всего проекта OPTICOMS, разработав встроенную проверку простоев в реальном времени для решения этой проблемы. Наконец, технология TME-Pick-and-Place, разработанная для автоматизации переноса обрезанных тканей со стола для раскроя в пресс-форму, оказывается наиболее эффективной для небольших дискретных деталей, таких как опорные ребра в многолонжеронной / рабочей машине. дизайн кожи.
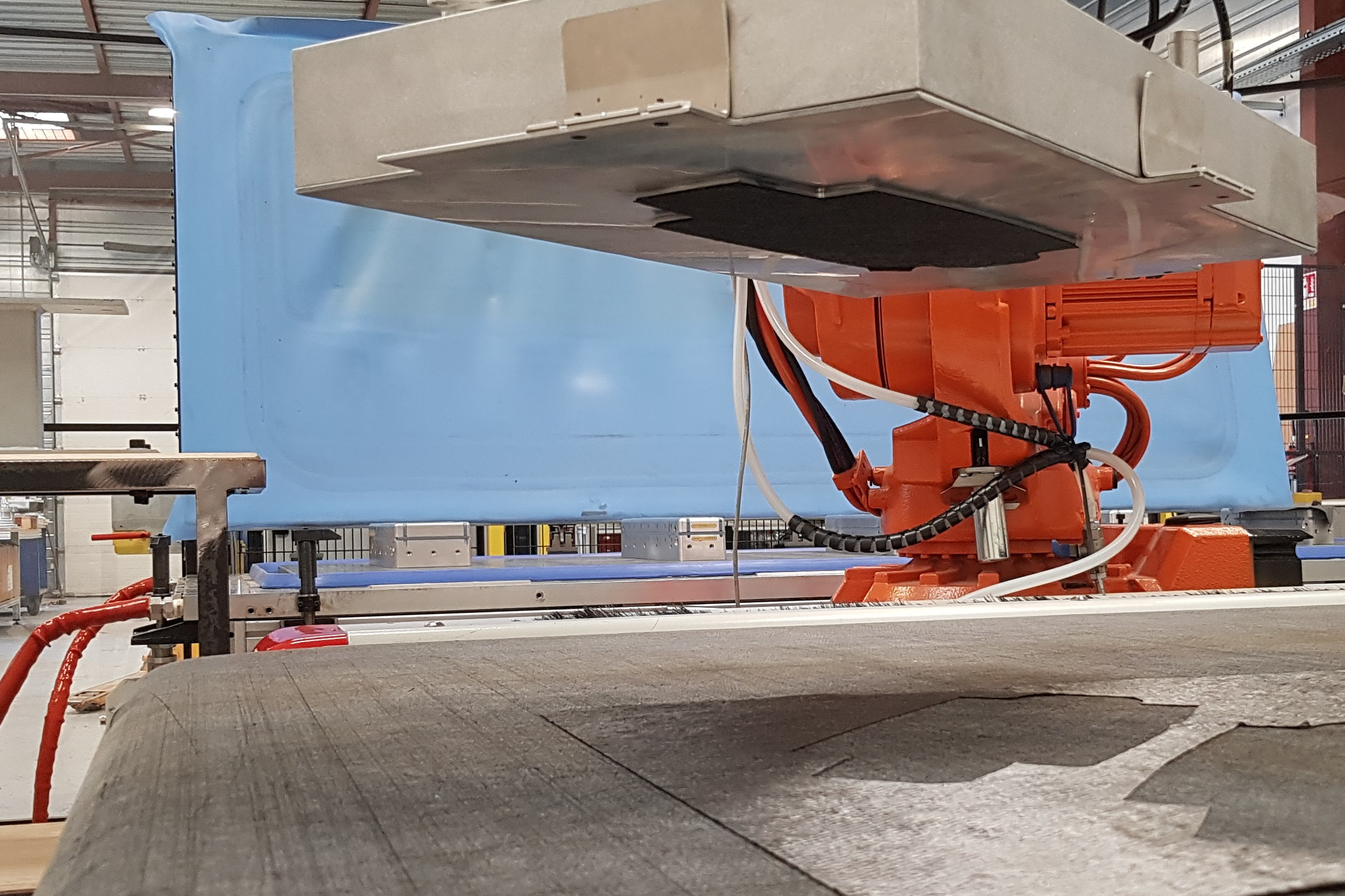
Дальнейшие действия
По словам Натана, OPTICOMS идет по пути к достижению целей автоматизации, снижения затрат и веса, поставленных программой, хотя для оценки производственных процессов и решений по сборке еще предстоит проделать несколько месяцев.
«Это важный момент в отношении OPTICOMS», - поясняет он. «Мы тщательно отбирали дизайн. У нас был сокращенный выбор материала. У нас был сокращенный выбор процессов. Все это требует времени и усилий. Это одна из уникальных сторон проекта ».
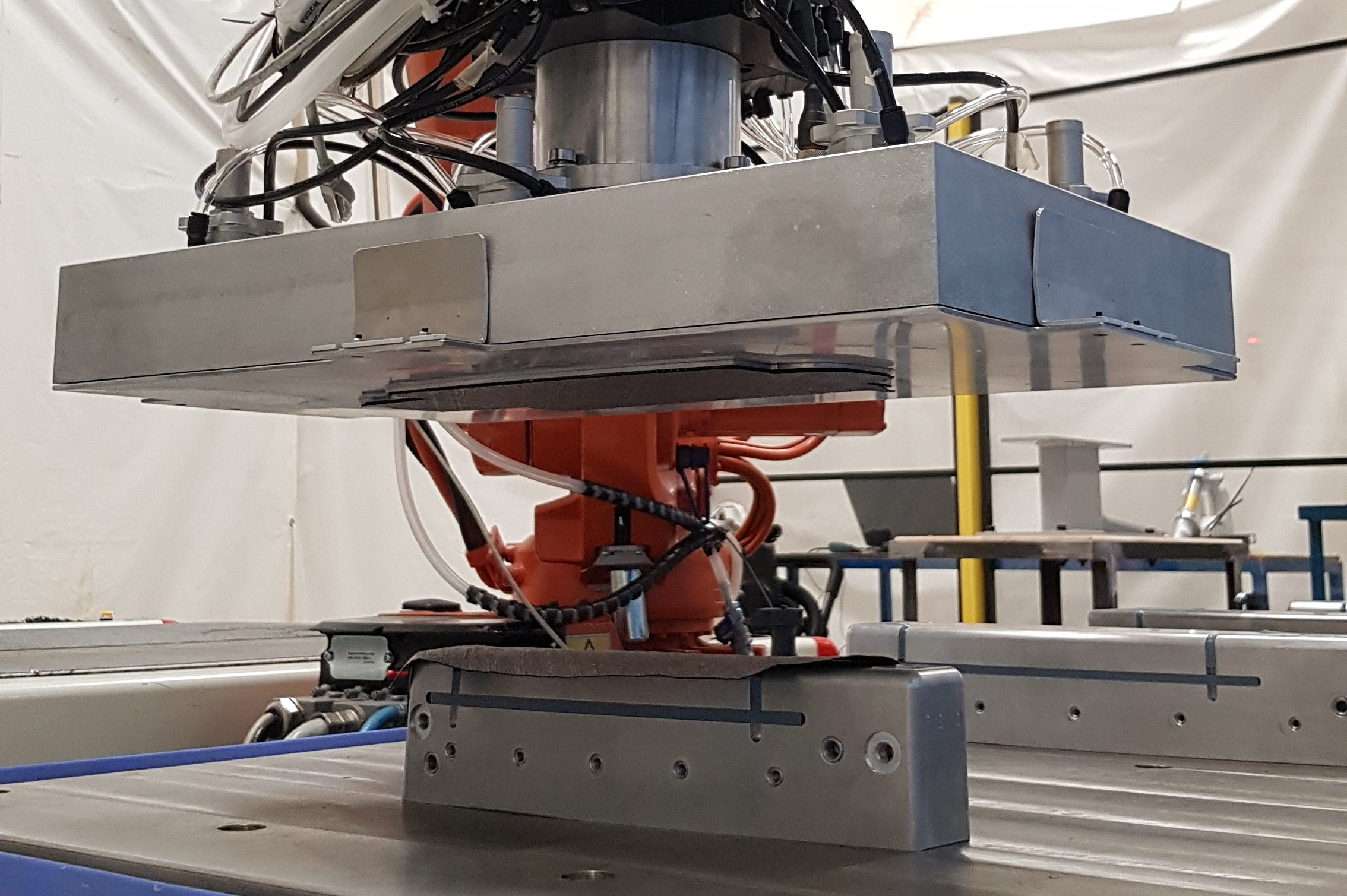
OPTICOMS инициировал три конкурса предложений (CFP) по технологиям и оборудованию для поддержки, обеспечения и улучшения целей проекта. Успешные предложения стали проектами Clean Sky 2, связанными с «материнским» основным партнером OPTICOMS и дополняющими его - все они работают вместе для достижения общей цели.
Первым усилием в этой разработке является FITCoW, цель которого - разработать новую интегрированную систему инструментов из углеродного волокна для совместного отверждения рабочей обшивки и трех лонжеронов. Список целей FITCoW амбициозен:снижение стоимости производимых деталей на 50%, снижение затрат на инструменты на 30% (по сравнению с металлической альтернативой), сокращение времени производства на 20% по сравнению с альтернативами автоклава и OOA, снижение несоответствия CTE на 40% по сравнению с инструментами из инвара. , Сокращение времени нагрева и охлаждения на 20% и сокращение времени проверки на 40% благодаря улучшенным возможностям контроля размеров.
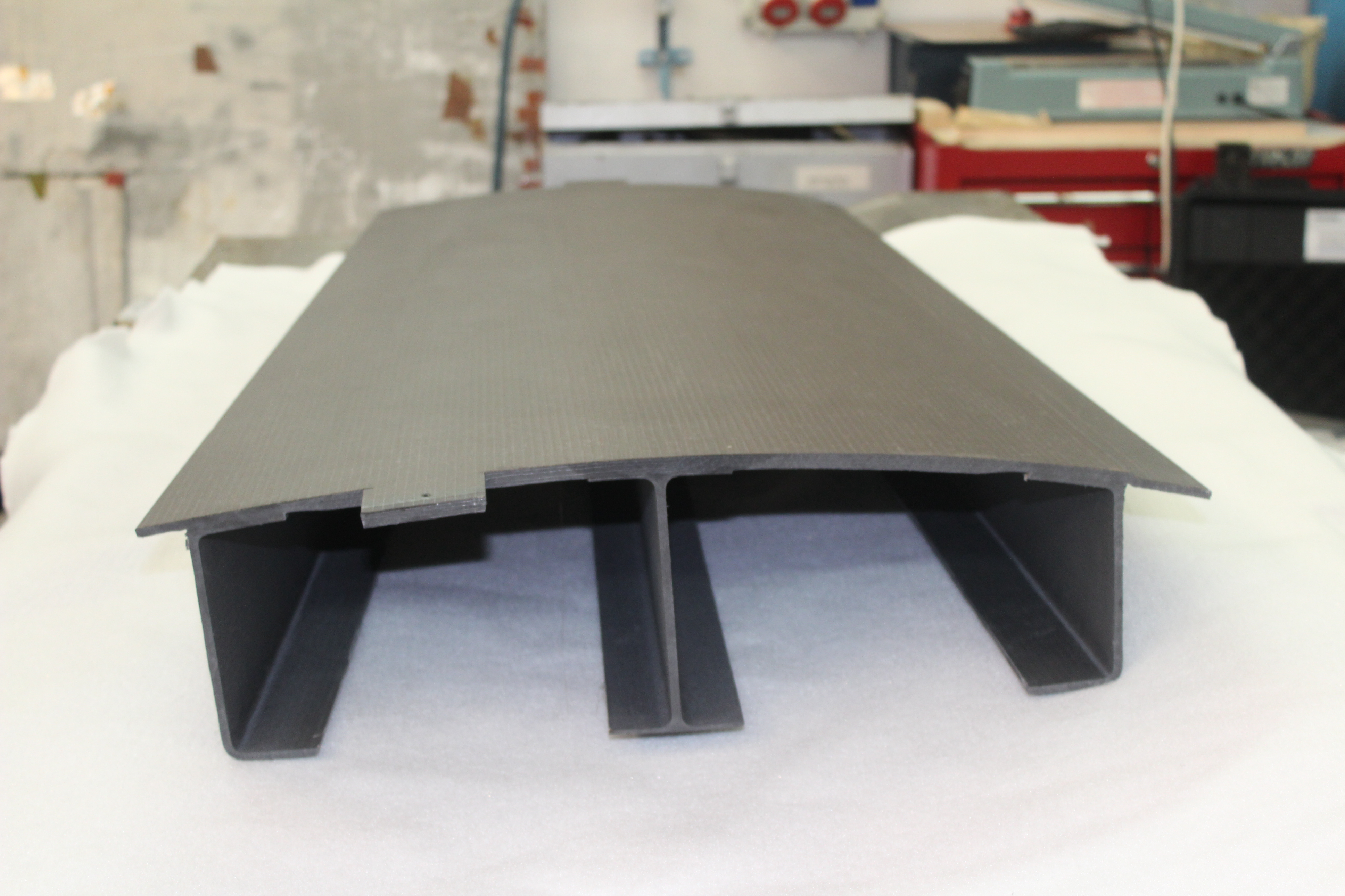
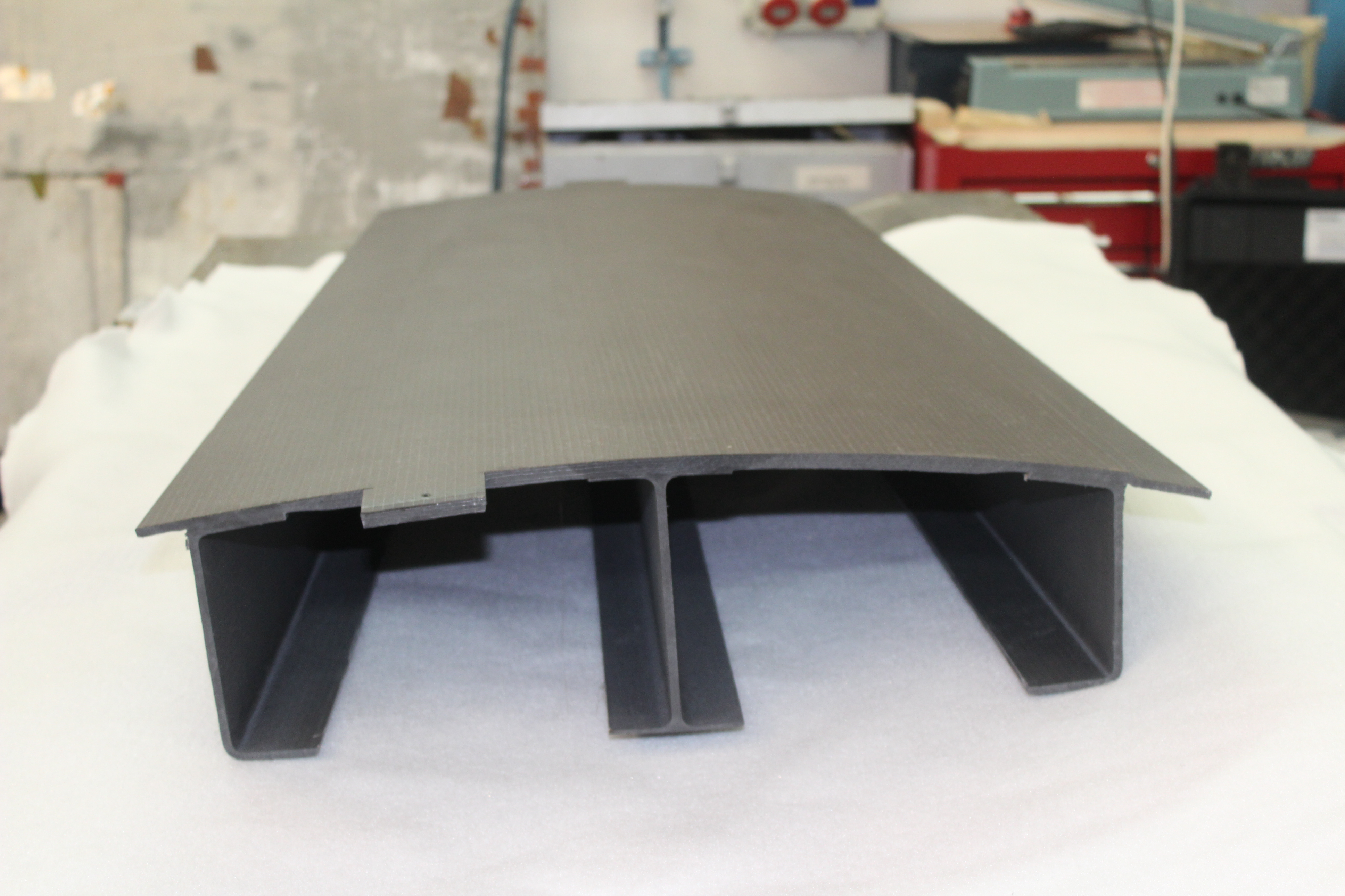
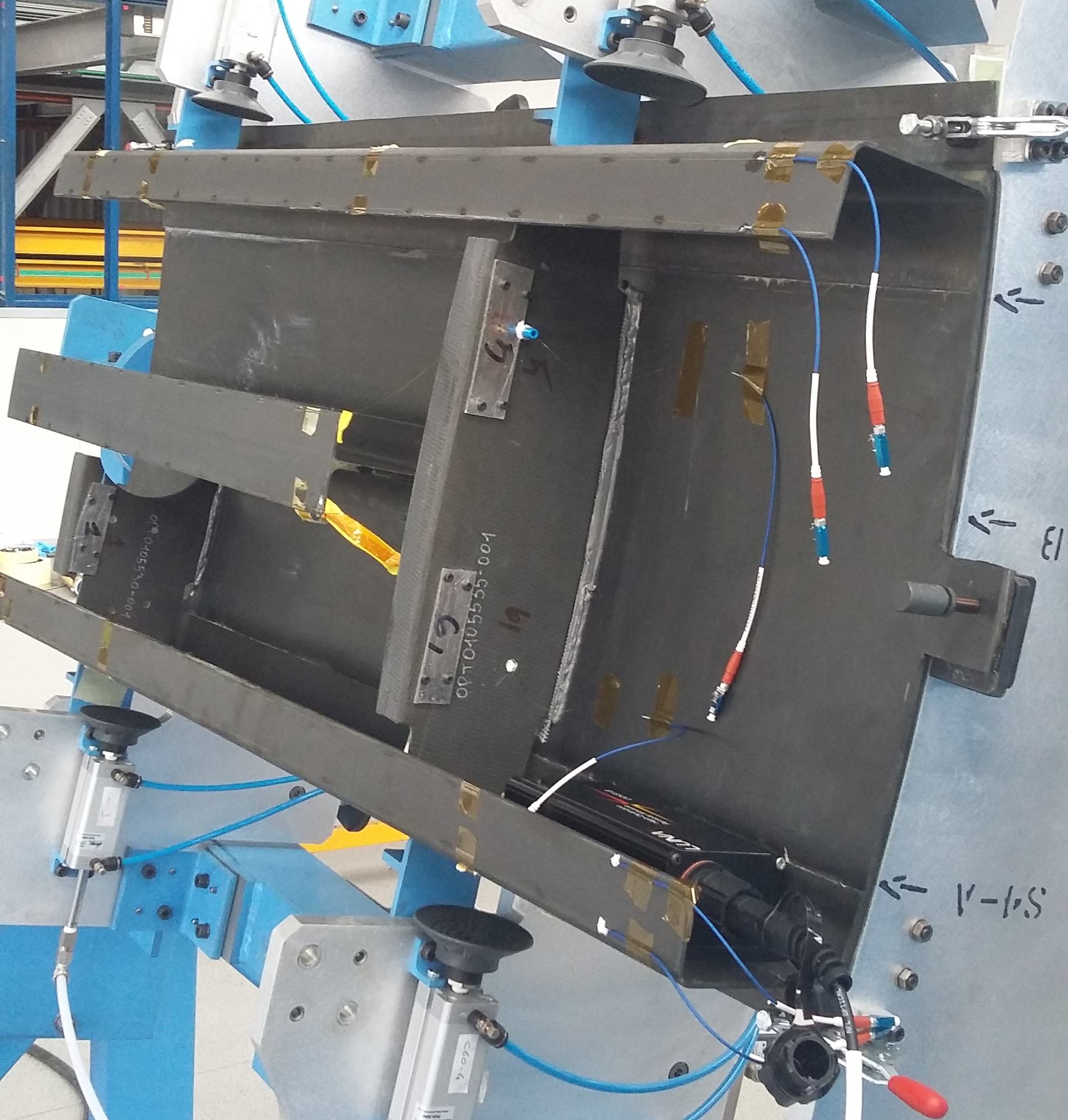
Чтобы связать структуру лонжерона / обшивки с нижней обшивкой, второй CFP привел к другому проекту OPTICOMS под названием WIBOND, чтобы разработать инструмент для сборки склеивания, который размещает клей, прикладывает соответствующее давление и включает оптоволоконные датчики в линию склеивания для обеспечения здоровья конструкции. мониторинг облигации; CW сообщит об этой и других технологиях сборки в отдельной статье, которая будет опубликована в 2022 году.
Третий CFP был инициирован для решения серьезной проблемы остаточных напряжений, вызывающих «пружинение» структуры лонжерона / обшивки. Эти деформации могут отрицательно сказаться на процессе сборки склеивания. Проект ELADINE объединил усилия OPTICOMS по разработке программного обеспечения, которое моделирует и прогнозирует термическую анизотропию, усадку при полимеризации, взаимодействие деталей инструмента, поток смолы и уплотнение, а также градиенты температуры по всей конструкции.
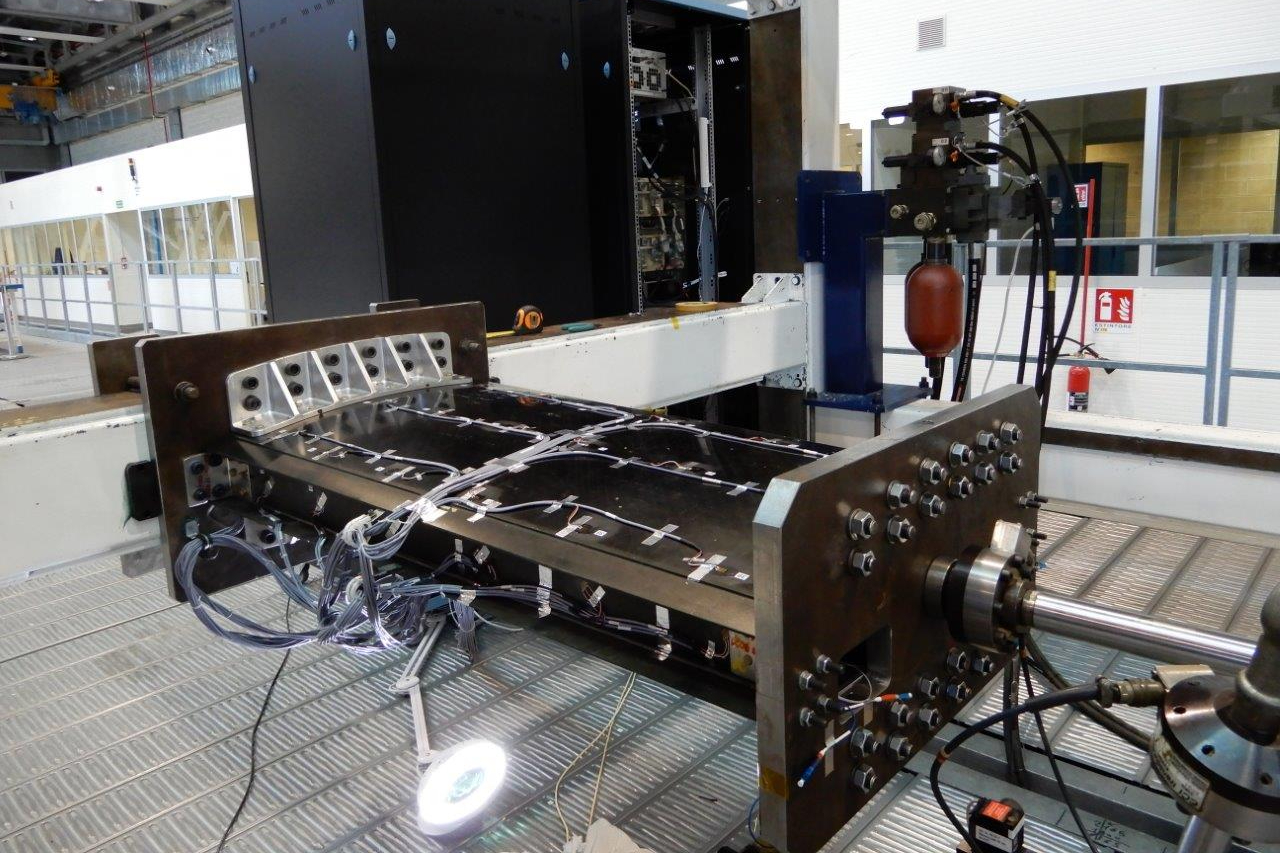
В настоящее время IAI и OPTICOMS уделяют основное внимание доставке ко второму кварталу 2022 года полного 6,8-метрового демонстрационного крыла компании Piaggio для статических и усталостных испытаний. После этого будет проведен анализ общих характеристик крыла и способности конструкции, материалов и процессов соответствовать критериям проекта. После этого будет рекомендация Piaggio о возможных следующих шагах в направлении коммерциализации.
Однако, помимо Piaggio, IAI надеется, что кессон крыла OPTICOMS может найти применение в других самолетах. «Хотя этот проект основан на конкретном самолете, - говорит Содей, - мы постарались сделать его масштабируемым до различной толщины и разных размеров. Мы никогда не упускали из виду тот факт, что эта технология может и должна быть легко адаптируемой ».
Смола
- Сверхлегкие композиты TPE для обуви
- Nexam Chemical, NCC разрабатывают решение для производства высокотемпературных композитов
- Композиты Solvay, выбранные для гоночного катамарана
- Колледж сообщества добавляет гибкость для студентов, изучающих производство композитных материалов
- 4 типичных ошибки, которых следует избегать при проектировании для производства
- Производство печатных плат для 5G
- Удовлетворение большой потребности в автоматизации композитов
- Металлы для многокомпонентного мелкосерийного производства
- Что такое автоматизированное производство?
- Избегайте этих 4 распространенных ошибок при проектировании для производства