Механизм удаления одиночного атомного слоя монокристаллической меди на основе резки:эффект радиуса кромки
Аннотация
Конечная цель механической резки - уменьшить минимальную толщину стружки до одного атомного слоя. В этом исследовании механизм удаления одиночного атомного слоя на основе резки на монокристаллической меди исследуется с помощью серии молекулярно-динамических анализов. Результаты исследования показывают, что при уменьшении глубины резания до атомного масштаба минимальная толщина стружки может быть уменьшена до одного атомного слоя за счет механической резки с использованием инструмента с закругленными краями. Поведение при удалении материала во время удаления одиночного атомного слоя на основе резания демонстрирует четыре характеристики, в том числе образование стружки за счет движения дислокаций, вызываемого напряжением сдвига, упругую деформацию на обрабатываемой поверхности, эффект атомного размера и эффект радиуса режущей кромки. Основываясь на этом понимании, предлагается новая модель резания для изучения поведения удаления материала в процессе удаления одиночного атомного слоя на основе резания, существенно отличающаяся от таковых при наноразрезании и традиционном резании. Полученные результаты обеспечивают теоретическую поддержку исследований и разработок технологий производства в атомном и близком к атомному масштабах.
Введение
Механическая резка, как один из важнейших методов субтрактивной обработки, применялась для изготовления деталей с высоким качеством обработки поверхности [1, 2]. Было проведено большое количество теоретических и экспериментальных исследований, чтобы прояснить механизм удаления подстилающего материала на наномасштабе, чтобы установить и обогатить основную теорию наноразрезания [3,4,5,6]. Результаты исследований вносят значительный вклад в применение нанометрической резки в академических кругах и в промышленности, позволяя изготавливать высокопроизводительные детали, требующие сложной формы и нанометрического качества поверхности [7, 8]. Однако до сих пор нет отчета о механизме удаления материала при резке в атомном и близком к атомному масштабе (ACS), что серьезно ограничивает прогресс в разработке производственных технологий следующего поколения - производство в атомном и близком к атомному масштабе ( ACSM), т. Е. Производство III [9]. Более того, прогрессивное развитие устройств атомарного масштаба также подчеркнуло потребность в различных процессах обработки для достижения ACSM [10].
При обычном резании на макроуровне глубина резания значительно больше, чем радиус режущей кромки, где удаление материала осуществляется за счет образования стружки, вызванного срезанием материала [11,12,13]. При микро / наноразрезании, поскольку глубина резания сравнима или меньше радиуса кромки инструмента, экструзионное стружкообразование постепенно становится преобладающим с уменьшением глубины резания до наномасштаба, что в значительной степени зависит от эффектов радиуса режущей кромки [14,15,16 , 17,18,19]. При резке ACS, поскольку глубина резания дополнительно уменьшается до близкого к атомному масштабу и даже до атомного масштаба, который намного меньше радиуса режущей кромки, эффект радиуса кромки неизбежно повлияет на характеристики съема материала.
Более того, в отличие от обычной резки и микро / нано-резки, при резке ACS глубина резания не только значительно меньше, чем радиус режущей кромки, но также сравнима или даже меньше, чем радиус атомов детали. Практическое поведение при удалении материала будет изменяться при различных соотношениях глубины резания и атомного радиуса заготовки, что признано одним новым эффектом калибровки, то есть эффектом атомного размера [20]. Следовательно, при резке ACS следует учитывать как эффект радиуса режущей кромки, так и эффект размера атома. Однако отчета об этом критически важном вопросе в исследовании технологии резки ACS нет.
По этим причинам в настоящем исследовании влияние размера атомов и радиуса кромки на механизм удаления одиночного атомного слоя на основе резки исследуются с помощью моделирования молекулярной динамики (МД).
Эта статья состоит из следующих разделов. Раздел 2 знакомит с используемой методологией, включая моделирование и протокол, подходящую потенциальную функцию. В разделе 3 представлены результаты анализа и соответствующие обсуждения. В разделе 4 подробно обсуждается механизм удаления одиночного атомного слоя на основе резки под совместным влиянием ультрасовременного эффекта и эффекта атомной проклейки. Выводы исследования приведены в Разделе 5.
Методология
Имитационная модель и протокол
Поскольку глубина резания уменьшается до атомного или близкого к атомному масштабу, действительно сложно экспериментально наблюдать процесс удаления материала на практике. В этом исследовании проводится серия МД-симуляций для анализа механизма удаления одиночного атомного слоя на основе резания с упором на атомный размерный эффект заготовки и эффект радиуса режущей кромки.
На рисунке 1 показаны снимки атомной конфигурации модели алмазно-медной резки, которая состоит из монокристаллической медной заготовки и алмазного режущего инструмента. Моделирование проводится на плоскости (111) монокристалла меди. Размеры заготовки в x - [1–1 0], y - [1 1 -2] и z - Направления [1 1 1] равны 27, 10 и 5 нм соответственно. Во время моделирования методом МД атомы заготовки делятся на атомы пограничного слоя, атомы термостатического слоя и атомы ньютоновского слоя, соответственно, как показано на рис. 1. Два слоя в нижней части заготовки, а именно пограничный слой, остаются фиксированными. по моделированию MD, чтобы исключить возможное смещение положения заготовки, вызванное резанием. Три атомных слоя, прилегающие к пограничному слою, являются атомами слоя термостата. Температуру термостатического слоя поддерживают на уровне 298 К с помощью методов масштабирования скорости. Остальные атомы заготовки принадлежат ньютоновскому слою. В настоящем моделировании передний угол и задний угол режущего инструмента составляют 0 ° и 12 °. Подробные параметры модели приведены в таблице 1. Поскольку резка ACS предпочтительно проводится при более низкой скорости резания, скорость резания 25 м / с в направлении [-1 1 0] используется после учета влияния скорости резания и времени вычислений. стоимость.
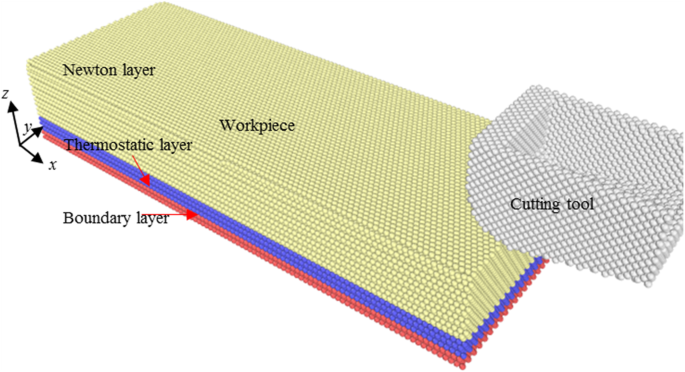
Имитационная модель для алмазной резки
Возможная функция
В системе резки медь-алмаз в основном используются два типа атомов:атомы меди и алмаза. В моделировании МД межатомные взаимодействия должны быть точно описаны, чтобы гарантировать точность вычислений результатов моделирования. Таким образом, разумный выбор потенциальной функции критически важен. В этом исследовании для описания межатомных взаимодействий между атомами меди принята часто используемая потенциальная функция метода погруженного атома (EAM) [21]. Функция Морзе применяется для расчета взаимодействий между атомами меди и атомами алмаза (Cu-C), в основном в зависимости от r.
$$ E ={D} _0 \ left [{e} ^ {- 2 \ alpha \ left (r- {r} _0 \ right)} - 2 {e} ^ {\ alpha \ left (r- {r} _0 \ right)} \ right] $$ (1)где E и D 0 относятся к парной потенциальной энергии и энергии когезии, α представляет собой константу, r 0 - равновесное расстояние, а r расстояние между двумя атомами. Для взаимодействий Cu-C, D 0 составляет 0,087 эв, r 0 составляет 0,205 нм [22], а α составляет 51,40 нм −1 . Для взаимодействий между атомами углерода в режущем инструменте (C-C) значительно более сильная связь между атомами алмаза, чем атомы меди, пренебрежимо мала. Режущий инструмент во время анализа считается жестким.
Определение глубины резания
Глубина резания ( a ) определяется как расстояние между самой верхней точкой поверхности заготовки и самой нижней точкой режущего инструмента. Размер атома детали обычно представлен атомным радиусом ( r w ). Как показано на рис. 2, когда намечено удалить самый верхний первый атомный слой с поверхности заготовки, теоретически максимальная используемая глубина резания может быть получена следующим образом:
$$ {a} _ {\ mathrm {max}} ={r} _w + 0.5 \ ast {d} _ {layer} $$ (2)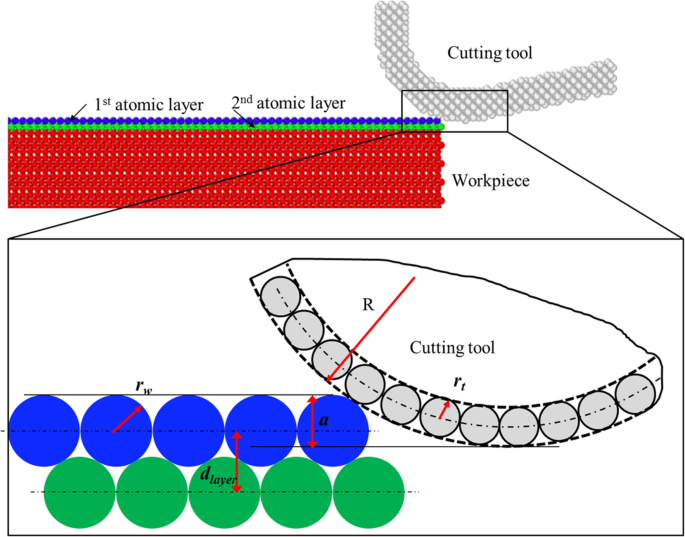
Принципиальная схема определения глубины резания при удалении одиночного атомарного слоя
Здесь d слой представляет собой расстояние между самыми верхними соседними атомными слоями на поверхности заготовки. В этом исследовании весь анализ основан на поверхности (111) монокристаллической медной заготовки; следовательно, r w в формуле. (2) относится к радиусу атомов меди, а именно 1,28 Å. d слой составляет 2,087 Å. Когда a больше чем a макс , самая нижняя точка режущего инструмента войдет в прямой контакт со вторым атомным слоем и может вызвать деформацию материала и даже его удаление. Таким образом, в настоящем исследовании использованная глубина резания меньше a макс (2,32 Å).
Основываясь на выводах, фундаментальный механизм удаления одиночного атомного слоя на основе резки будет значительно изменен при различных комбинациях соотношений a в R и a в r w .
Результаты и обсуждение
Согласно результатам МД, как эффект атомарной проклейки, так и эффект радиуса режущей кромки сильно повлияли на процесс удаления одиночного атомного слоя на основе резания. В следующих разделах, чтобы четко описать эффект атомарного размера и эффект радиуса кромки инструмента, отношение глубины резания ( a ) до атомного радиуса детали ( r w ), a / r w , и глубины резания ( a ) до радиуса кромки ( R ), a / R , работают. Результаты анализа систематически изучаются с точки зрения формирования стружки, образования поверхности, подповерхностной деформации и поведения атомных смещений. Полученные данные позволяют подробно изучить типичные характеристики механизма удаления одиночного атомного слоя на основе резки.
Формирование чипа
Результаты анализа показывают, что из-за эффекта атомарного размера заготовки [20] существует два критических значения отношения глубины резания ( a ) до атомного радиуса детали ( r w ), а именно критическое значение 1 (C 1 ) и критическое значение 2 (C 2 ), который разделил поведение стружкообразования на разные случаи.
- а.
Отношение a / r w меньше критического значения 1 (C 1 ).
На рис. 3 показаны результаты МД моделирования при различном радиусе кромки инструмента на глубине резания около 1,1 Å. Здесь коэффициент глубины резания ( a ) до атомного радиуса детали ( r w ) составляет 0,781.
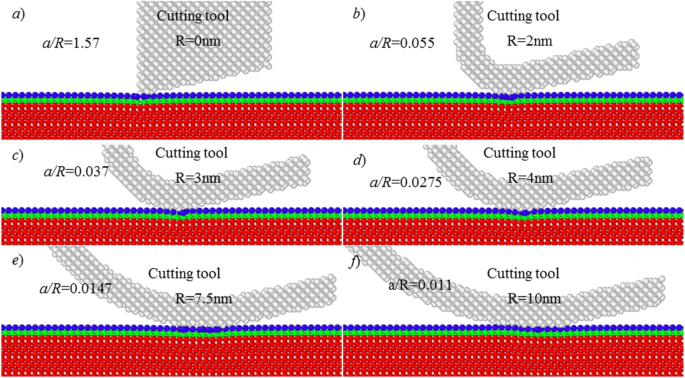
Результаты моделирования при глубине резания 1,1 Å
Несмотря на увеличенный радиус режущей кромки, на каждой обрабатываемой поверхности Cu (111) происходит упругая деформация. В процессе резания не происходит стружкообразования и удаления материала. Исследование показывает, что глубина резания должна быть больше 1,1 Å, чтобы можно было удалить материал с поверхности Cu (111).
- б.
Отношение a / r w больше C1, но меньше критического значения 2 (C 2 ).
Когда глубина резания больше, чем примерно 1,1 Å, а именно, отношение a / r w больше 0,781, происходит съем материала на поверхности заготовки. Как показано на рис. 4, часть материала удаляется с поверхности заготовки, но большее количество атомов в самом верхнем первом слое остается на новой обработанной поверхности, образуя дефекты поверхности. Более того, при увеличении радиуса края до 7,5 нм отношение a / R составляет 0,019. В таком случае часть атомов в первом атомном слое была вдавлена во второй слой и даже в третий атомный слой, как показано на рис. 4e, что следует приписать экструзионному действию режущего инструмента. Это также указывает на то, что эффект радиуса кромки инструмента начинает оказывать влияние на процесс удаления материала, хотя непрерывное удаление материала не может быть достигнуто.
- c.
Отношение a / r w больше C 2 .
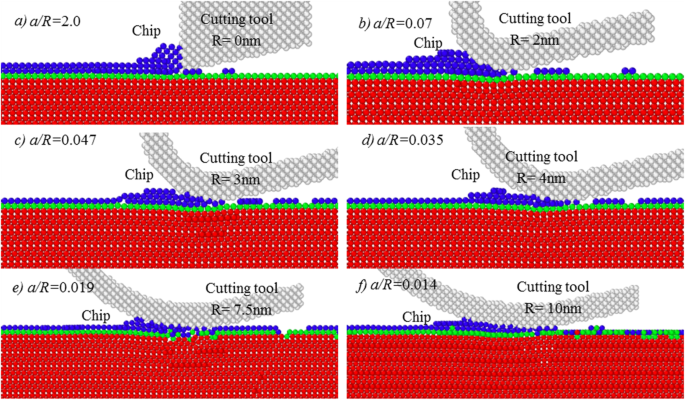
Результаты моделирования при глубине резания 1,4 Å
На рис. 5 показано образование стружки при глубине резания около 2 Å. Здесь отношение a / r w =2 Å / 1,28 Å =1,563. По сравнению с рис. 3, с увеличением глубины резания до 2 Å, атомы в целевом атомном слое могут непрерывно и стабильно удаляться путем формирования чипа. Это указывает на то, что глубина резания была больше минимальной толщины стружки монокристаллической меди, а минимальная толщина стружки могла быть вплоть до одиночного атомного слоя с глубиной резания около 2 Å. После резки материалы в пределах первого атомного слоя были полностью удалены с поверхности заготовки.
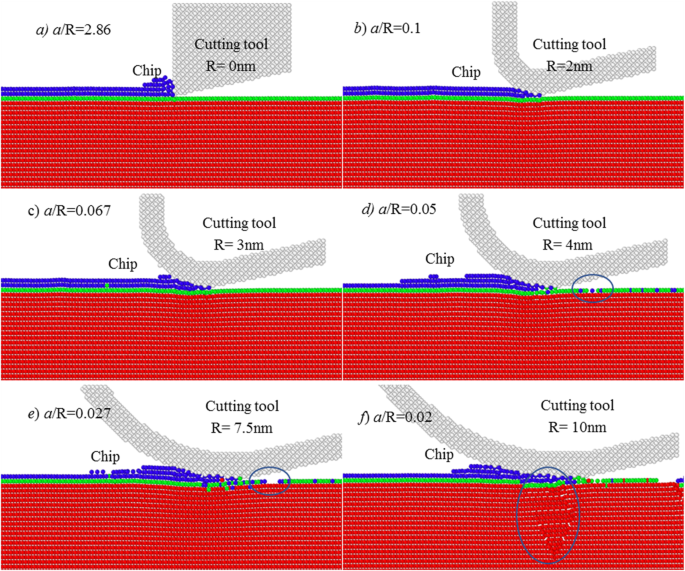
Результаты моделирования резки САУ на глубину резания =2 Å
Однако на рис. 5 также можно заметить, что из-за увеличения отношения a / R очевидно, что атомы в первом атомном слое претерпевают различные процессы удаления, особенно деформацию, вызванную резанием, на обрабатываемой поверхности. При глубине резания 2 Å при использовании острого режущего инструмента, а именно при соотношении a / R составляет 5,70, на обрабатываемой поверхности возникает лишь небольшая деформация. Когда радиус режущей кромки увеличивается до 3 нм, отношение a / R составляет 0,134, очевидно, что амплитуда упругой деформации увеличилась.
Когда радиус кромки инструмента увеличивается до 4 нм, как показано на рис. 5d, многие атомы в целевом первом атомном слое вдавливаются во второй атомный слой, образуя новую обработанную поверхность. При радиусе кромки инструмента около 7,5 нм часть атомов в первом слое диффундирует даже в третий атомный слой. Когда радиус кромки инструмента достигает примерно 10 нм, возникает очевидная упругая и пластическая деформация, которую также можно определить в следующем разделе 3.3.
Следовательно, удаление одиночного атомного слоя на основе резки зависит не только от отношения a / r w , но также отношение a / R . Чтобы добиться удаления одного атомного слоя с помощью механической резки, то есть удаления материала в атомарном масштабе, следует учитывать как эффект размера атома, так и эффект радиуса режущей кромки, что значительно отличается от микро / наноразрезания и традиционной резки в макромасштабе.
Создание поверхности
Одной из целей удаления атомного слоя резанием является получение бездефектной обработанной поверхности с идеальной кристаллической структурой. Влияние атомного размера заготовки на формирование поверхности при резке ACS недавно было изучено [20]. В настоящем исследовании, чтобы четко указать влияние радиуса режущей кромки на формирование поверхности при резке ACS, топография поверхности и состав поверхности новой обработанной поверхности изучаются следующим образом.
Топография поверхности
На рис. 6 показаны топографии обработанной поверхности Cu (111) при различных краевых радиусах. Здесь принята глубина резания 2 Å. Как показано на рис. 6a, b, когда радиус кромки инструмента меньше 3 нм, могут быть получены поверхности Cu (111) с идеальной кристаллической структурой. Что касается дефектов на левой стороне поверхности заготовки, то это связано с деформацией при выходе инструмента из резания. Во время резки на стадии стабилизации на обрабатываемой поверхности не образуется поверхностных дефектов.
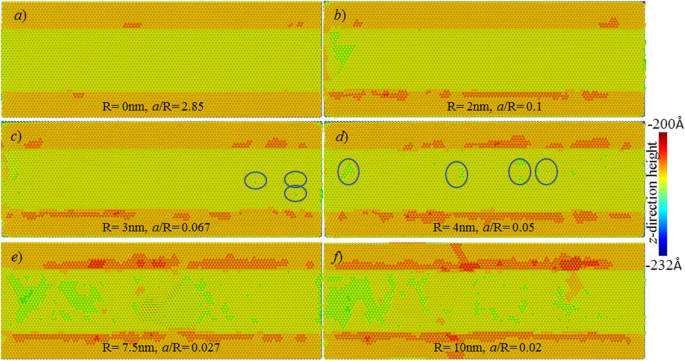
Влияние радиуса кромки инструмента на топографию поверхности. Атомы окрашены в соответствии с их высотой в направлении оси Z
Однако по мере увеличения радиуса кромки инструмента на обрабатываемой поверхности постепенно образуется множество дефектов. При радиусе кромки 4 нм на обработанной поверхности образуется множество дефектов в виде ямок, см. Рис. 6г. Кроме того, когда радиус кромки инструмента равен или превышает 5 нм, образуется большое количество поверхностных дефектов, серьезно ухудшающих качество поверхности. В этом случае с поверхности детали удалено более одного слоя атомов. Следовательно, можно определить, что при глубине резания 2 Å, когда радиус кромки инструмента меньше 3 нм, удаление одиночного атомного слоя может быть достигнуто на поверхности Cu (111). Из-за эффекта радиуса режущей кромки коэффициент глубины резания ( a ) до радиуса кромки ( R ) должен быть больше одного порога, чтобы добиться бездефектной обрабатываемой поверхности за счет удаления одиночного атомного слоя на основе резки. Здесь критическое значение отношения a / R составляет [0,05, 0,067].
Состав поверхности
На рис. 7 показан состав обработанных поверхностей при различных радиусах кромки инструмента и глубине резания 2 Å. Здесь зеленые и синие атомы - это атомы из первого и второго слоев, а красные - атомы под вторым атомным слоем. Как показано на рис. 7a, при использовании острого режущего инструмента отношение a / R составляет 2,85, обрабатываемая поверхность состоит только из атомов первого слоя. Этот результат указывает на то, что целевой первый атомный слой был полностью удален с детали. Более того, это означает, что удаление материала осуществляется послойно, при этом удаляемые материалы поступают только из целевого первого атомного слоя на поверхности заготовки.
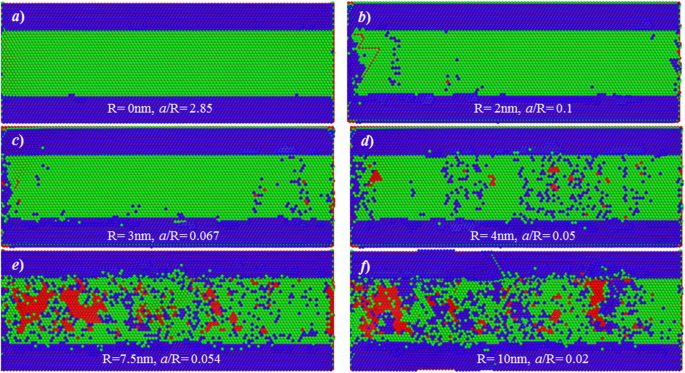
Поверхностный состав обрабатываемых поверхностей. Атомы окрашены в зависимости от номера атомного слоя
Однако, когда радиус кромки инструмента составляет 2 нм и 3 нм, как показано на рис. 7b, c, обработанные поверхности состоят из двух атомных слоев (синего и зеленого). Это указывает на то, что, хотя было достигнуто удаление одного атомного слоя, процесс генерации поверхности включает минимум 2 атомных слоя. Кроме того, когда радиус кромки инструмента больше 4 нм, на обрабатываемой поверхности имеется большое количество атомов первого атомного слоя, что указывает на то, что многие атомы в первом слое были нажаты для создания новой поверхности.
Следовательно, с увеличением радиуса режущей кромки формирование поверхности сильно изменилось. Ниже кратко описаны два типа задействованных механизмов образования поверхности:
- 1.
По слоям :целевой первый атомный слой полностью удаляется для создания новой обработанной поверхности. В процессе резки удаляются только атомы в первом слое.
- 2.
Многослойное удаление :хотя удаление одного атомного слоя могло быть реализовано, атомы в целевом атомном слое претерпевают два типичных поведения смещения. Часть атомов будет сформирована в стружку за счет движения дислокации под действием напряжения сдвига, в то время как другие будут выдавлены в обрабатываемую поверхность под действием режущего инструмента. Процесс удаления материала включает минимум два атомных слоя.
Механизм подповерхностной деформации
При нанорезке происходит упругая и пластическая деформация обрабатываемой поверхности в процессе резки. После того, как режущий инструмент проходит по поверхности заготовки, упругая часть возвращается в исходное положение, а пластически деформированная часть приводит к длительной деформации [1, 2]. Поскольку глубина резания уменьшается до атомных масштабов, при резке в направлении удаления одиночного атомного слоя постулируется, что на обрабатываемой поверхности происходит только упругая деформация. Чтобы убедиться в этом, анализируются состояния подповерхностной деформации заготовки во время и после резки. На рисунке 8 показаны дефектные структуры на поверхности детали при различных радиусах кромки инструмента. Здесь атомы окрашены в соответствии с параметром центросимметрии (CSP), а атомы с CSP меньше 3 опущены, что представляет собой атомы с идеальной FCC-структурой.
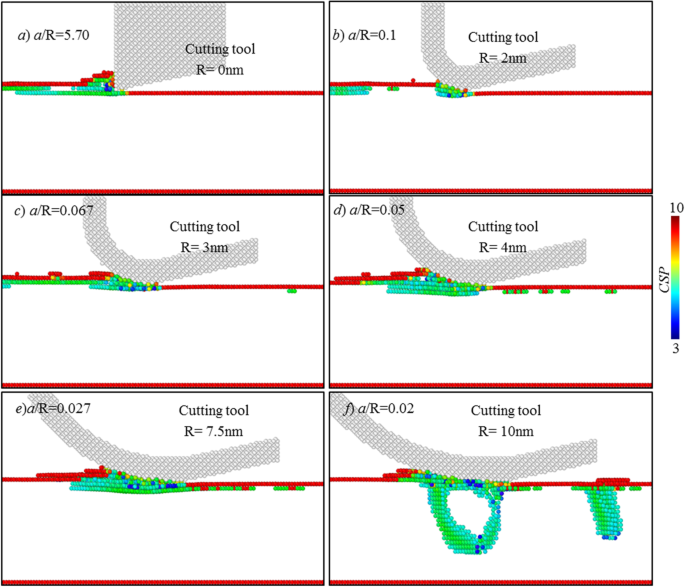
Поверхностный состав обрабатываемых поверхностей. Атомы окрашены в соответствии с их CSP
Когда радиус режущей кромки меньше 4 нм, на обрабатываемой поверхности не образуется подповерхностный дефект. При резке наблюдается только упругая деформация обрабатываемой поверхности.
Как показано на рис. 8, когда радиус режущей кромки равен или больше 4 нм, инициализируются подповерхностные дефекты. Более того, с увеличением радиуса режущей кромки значительно увеличивается количество подповерхностных дефектов. Когда радиус края достигает примерно 10 нм, образуется одна дислокационная петля, которая не может исчезнуть после резки, как показано на рис. 9e. Он четко указывает на пластическую деформацию, происходящую на обрабатываемой поверхности.
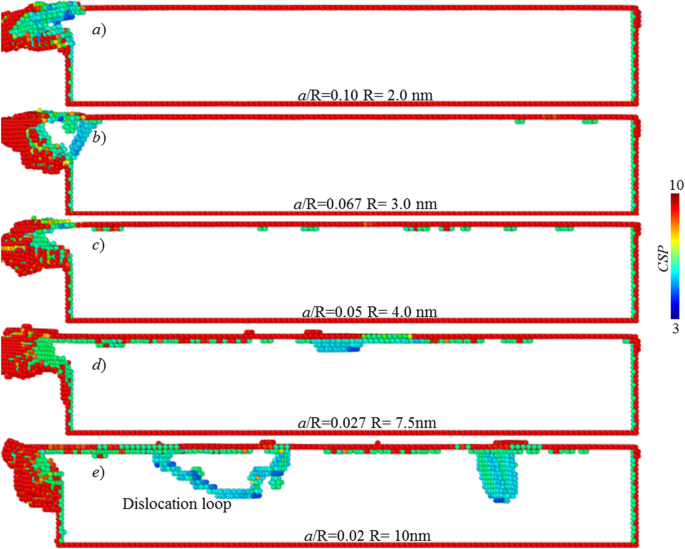
Подповерхностные дефекты на различных радиусах кромки инструмента. Атомы окрашены в соответствии с их CSP
После того, как инструмент пройдет по поверхности заготовки, упруго деформированная часть отскочит назад; таким образом, аннигилируют части подповерхностных дефектов. Как показано на рис. 9a – c, наконец, подповерхностный дефект отсутствует, если радиус кромки инструмента составляет 2 или 3 нм.
Что касается пластически деформированного участка, то он приводит к длительной деформации. Как показано на рис. 9, когда радиус кромки инструмента составляет 7,5 нм, остается небольшое количество подповерхностных дефектов. Когда радиус кромки инструмента составляет 10 нм, дислокационная петля и дефект упаковки, наконец, существуют в подповерхности заготовки.
Основываясь на приведенном выше анализе, можно сделать вывод, что для обеспечения возможности удаления одиночного атомного слоя на основе резки следует избегать пластической деформации и допускать только упругую деформацию на обрабатываемой поверхности. Это считается одной из характерных черт процесса удаления одиночного атомного слоя на основе резки.
Поведение атомарного смещения
Согласно файлам траектории МД, движение дислокации преобладает в процессе удаления одиночного атомного слоя на основе резки. На рисунке 10 показаны результаты моделирования с использованием различных радиусов режущей кромки инструмента. При радиусе кромки 2 нм под действием режущего инструмента только первый атомный слой скользит по направлению резания, образуя стружку, в то время как другие остаются неподвижными. Его можно рассматривать как одно поперечное сечение одной краевой дислокации.
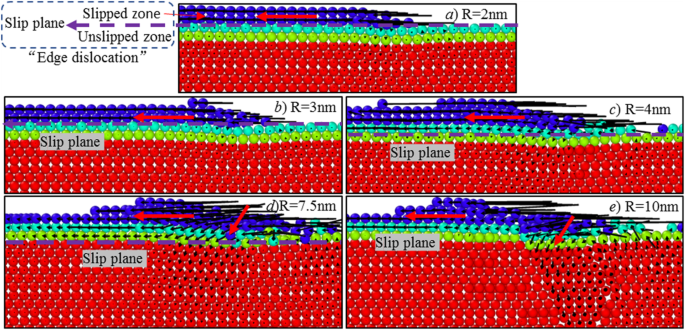
Поведение атомного смещения при различном радиусе режущей кромки
По мере увеличения радиуса кромки инструмента часть материала внутри первого атомного слоя вдавливается в обрабатываемую поверхность, вызывая скольжение атомных слоев ниже первого слоя. Более того, по мере увеличения радиуса кромки инструмента количество атомных слоев, подвергающихся процессу скольжения материала, имеет тенденцию к увеличению. Когда радиус кромки инструмента составляет 4 нм, за исключением первого атомного слоя, второй атомный слой также проводит скольжение материала вдоль направления резания, как показано на рис. 10. Когда радиус кромки инструмента составляет 7,5 нм, по мере продвижения режущего инструмента, три самых верхних атомные слои на поверхности заготовки соскользнули по направлению резания. Кроме того, когда радиус кромки инструмента увеличивается до 10 нм, большое количество материалов было спрессовано с образованием новой обрабатываемой поверхности; на поверхности заготовки происходит пластическая деформация (см. рис. 10e), которую также можно определить на рис. 9.
На рисунке 11 показан процесс скольжения целевого атомного слоя вдоль направления резания. Площадь зоны проскальзывания постоянно увеличивается по мере продвижения режущего инструмента вперед. На расстоянии резки 17,5 нм зона скольжения достигла максимального значения. Впоследствии материалы в зоне скольжения непрерывно формируются в стружку; объем чипа также увеличен.
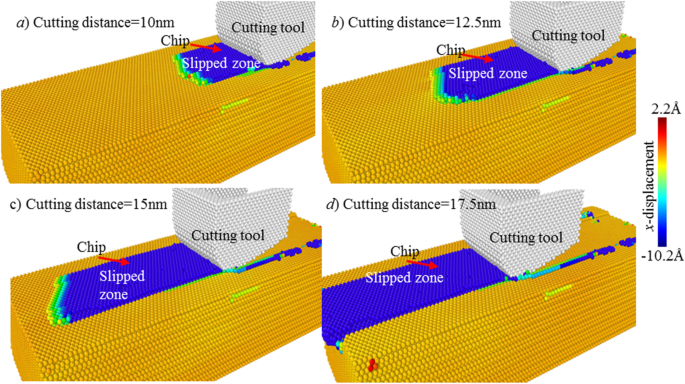
Процесс скольжения целевого атомного слоя при радиусе режущей кромки 2 нм. Атомы окрашены в соответствии со значениями их атомного смещения в направлении x
В целом, согласно анализу в разделах 3.3 и 3.4, по мере увеличения радиуса кромки инструмента как механизм подповерхностной деформации, так и поведение атомного смещения сильно изменились. При разных радиусах кромки инструмента различное количество атомных слоев имеет тенденцию к скольжению вдоль направления резания, в то время как на обрабатываемой поверхности возникают разные режимы деформации, как показано в Таблице 2. Более того, можно обнаружить, что при удалении одного атомного слоя на основе резания Процесс формирования стружки регулируется движением дислокаций, вызванным сдвиговым напряжением, что значительно отличается от стружкообразования при традиционном резании и наноразрезании. Это также можно рассматривать как одну из характерных черт удаления одиночного атомного слоя на основе резания.
Режущая сила
Влияние эффекта радиуса кромки
На рисунке 12 показано влияние радиуса режущей кромки на усредненные силы резания при глубине резания 2 Å. Здесь тангенциальная и нормальная составляющие сил резания, а именно F т и F n , сравниваются. Как показано, для острого режущего инструмента отношение a / R составляет 2,85, а F т 16,4 нН явно меньше, чем F n 23,7 нН. По мере увеличения радиуса кромки инструмента оба значения F т и F n увеличены. Однако F n имеет гораздо большие амплитуды роста, чем F т . Это ясно указывает на то, что по мере увеличения радиуса кромки инструмента нормальная сила резания будет иметь большее влияние на процесс удаления материала в процессе резки ACS. Однако, когда радиус кромки инструмента больше, чем примерно 3 нм, удаление одиночного атомного слоя не может быть достигнуто. Таким образом, большая нормальная сила резания не будет полезна для удаления одиночного атомного слоя на основе резания, и следует предпочтительно использовать более низкую нормальную силу резания.
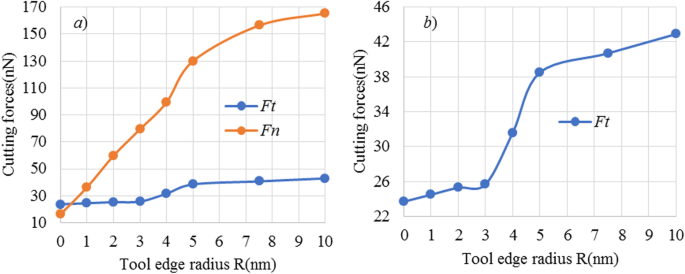
График зависимости сил резания от радиуса режущей кромки при глубине резания 2 Å
Поскольку нормальные силы резания создают напряжение сжатия, обеспечивающее упругую и / или пластическую деформацию обрабатываемой поверхности, тангенциальные силы резания будут создавать напряжение сдвига для образования стружки. Следовательно, можно сделать вывод, что стружкообразование при удалении одиночного атомного слоя на основе резания должно в основном осуществляться за счет тангенциальной силы резания. На рис. 12b также видно, что F т претерпел три вида изменений, которые в дальнейшем приводят к разной топографии поверхности (см. рис. 6), включая следующие:
Когда радиус кромки инструмента меньше примерно 3 нм, а именно, отношение a / R составляет 0,067, F т примерно остается неизменным и всегда меньше 25 нН с увеличением радиуса кромки. В этом случае с поверхности детали удаляется только один атомный слой.
Когда радиус кромки инструмента составляет 3 нм и 5 нм, отношения a / R равны 0,04 и 0,067, а F т очевидно увеличивается примерно до 38,5 нН. Следовательно, с поверхности детали удаляется более одного атомного слоя, но образуется небольшое количество поверхностных дефектов.
Что касается краевого радиуса более 5 нм, F т также постепенно сходится к постоянному значению. В этом случае удаляется более одного атомного слоя. Однако на поверхности и под поверхностью заготовки образуется большое количество поверхностных дефектов.
Можно сделать вывод, что очень низкое тангенциальное усилие резания может позволить удаление одиночного атомного слоя на основе резки при разумном радиусе режущей кромки, таком как 2 нм. В свою очередь, удаление одиночного атомного слоя не могло быть осуществлено, несмотря на большую тангенциальную силу резания.
Влияние эффекта атомарного изменения размера
На рисунке 13 также представлен график зависимости сил резания от глубины резания при радиусе режущей кромки 2 нм. Можно обнаружить, что при радиусе режущей кромки 2 нм по мере увеличения глубины резания как нормальная сила резания, так и тангенциальные силы резания претерпевают трехступенчатые изменения. Наблюдаются явные изменения при глубине резания около 1,1 Å и 1,6 Å. Соответствующее соотношение глубины резания ( a ) до атомного радиуса детали ( r w ) равны 0,055 и 0,080, которые представляют собой два упомянутых выше критических значения a / r w , C 1 и C 2, как показано в разделе 3.1.
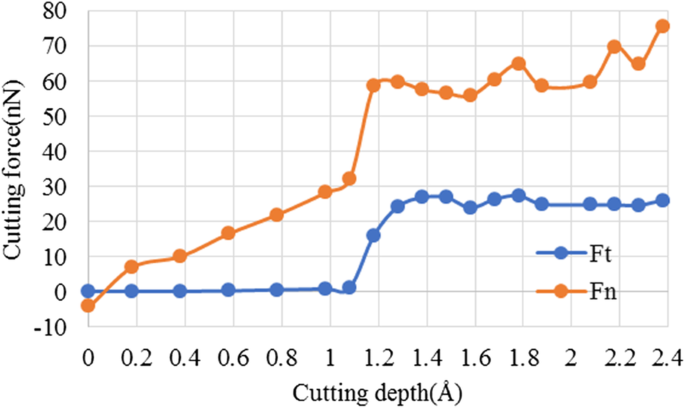
Plot of cutting forces versus cutting depth at edge radius of 2 nm
When cutting depth is smaller than 1.1 Å, namely, the ratio of a/r w is less than 0.055, F т is always 0 nN, while F n is linearly increased to about 32 nN. However, the cutting forces could not enable plastic material deformation and removal on the workpiece surface. Consequently, there is only elastic deformation on workpiece surface, as shown in Fig. 3.
When the cutting depth is larger than 1.1 Å, but smaller than 1.6 Å, the ratio of a/r w is more than 0.055 but less than 0.080. If this case, F т has greatly increased from 0 nN to about 25 Nn, while F n further increased to about 58 nN. The cutting forces are larger enough to enable material removal on workpiece surface. At the cutting depth of 1.4 Å, there is chip formation and material removal on workpiece surface. But the stable and continuous material removal could not be realized and many defects are formed on the processed surface, as shown in Fig. 4.
When the cutting depth is larger than 1.6 Å, both F т и F n are large enough to enable continuous material removal on workpiece surface. Consequently, chip is stably formed over the workpiece surface, and the targeted atomic layer is continuously removed via chip formation, forming a new processed surface, as shown in Fig. 5b and Fig. 6b.
Overall, both cutting-edge radius effect and atomic sizing effect have an influence on cutting force in cutting-based single atomic layer removal process, thereby changing the material removal and surface generation process.
Discussions About Cutting-Based Single Atomic Layer Removal Mechanism
As per above analysis, both atomic sizing effect and cutting-edge radius effect have a great influence on the cutting-based single atomic layer removal mechanism. As summarized in Table 3, depending on the ratio of cutting depth to workpiece atomic radius(a/r w ) and the ratio of cutting depth to edge radius(a/R ), there are minimum 5 typical cases of material deformation and removal behaviours in cutting-based single atomic layer removal process. In this section, the fundamental material deformation and removal mechanism of each case is summarized.
In conventional machining, as cutting depth is significantly larger than the cutting-edge radius, the cutting-edge radius effect can be ignored. As the cutting depth is decreased to nanoscale, which is comparable or lower than the edge radius, the edge radius effect can be no longer ignored. In nanocutting, the material removal process is dominated by the extrusion deformation, which is greatly influenced by cutting-edge radius. As the cutting depth is further decreased to atomic scale, except for cutting-edge radius effect, a new sizing effect, atomic sizing effect [20] has a great influence on material removal.
As shown in Fig. 14, in the cutting-based single atomic layer removal process, there are two portions involving in cutting, i.e., nanometric cutting edge and the lowest cutting tool atoms (B ). Such two portions could be coupled to enable single atomic layer removal. The size of cutting edge, regarded as ‘nano-tool,’ is described by edge radius (R ). The cutting edge is the envelope curve of the outermost atoms in cutting tool. Regarding the lowest atoms, as ‘atomic-tool,’ it is described by workpiece atomic radius (r w ). The cutting-based single atomic layer removal is the results of the coupled actions of nano-tool and atomic-tool on workpiece material.
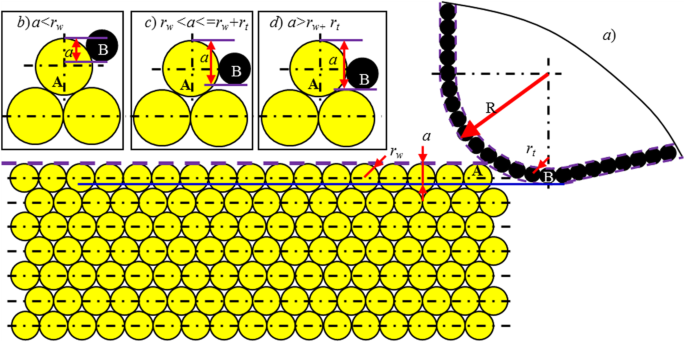
Schematic diagram for cutting-based single atomic layer removal
Firstly, depending on the ratio of cutting depth (a ) to the workpiece atomic radius (r w ), i.e., a/r , there are three kinds of material deformation behaviour in ACS cutting process.
- 1.
The ratio of a/r w is smaller than critical value 1(C1 ).
As shown in Fig. 15, chip formation does not occur, but elastic deformation does occur on the workpiece surface. During cutting process, after workpiece passes the lowest point of cutting tool, the elastically deformed part would recover completely. Consequently, no material deformation and removal occurred on the topmost surface. In such case, the tool edge effect could be ignored. This ratio could be affected by material properties (case 1).
- 2.
The ratio of a/r w is larger than C 1 , but smaller than critical value 2 (C2 ).
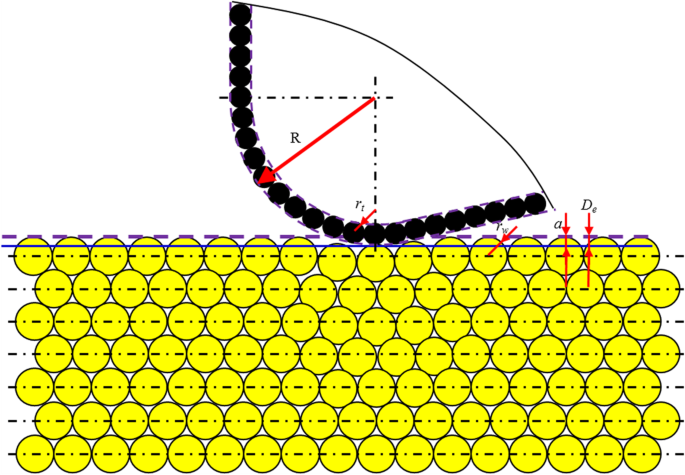
Schematic illustration of cutting-based single atomic layer removal at the ratio of a/rw smaller than C1
As the ratio of the cutting depth to atomic radius (a/r w ) increases to be larger than C1 but smaller than critical value 2(C2 ), there is material removal on the workpiece surface, but it is noncontinuous. In such case, only part of material within targeted atomic layer is formed into chip by shear stress-driven dislocation motion, while others are remained on the workpiece surface. When cutting tool passes over the workpiece surface, the surface quality of the processed surface is seriously deteriorated (case 2) (Fig. 16).
- 3.
The ratio of a/r w is larger than critical value 2 (C2 ).
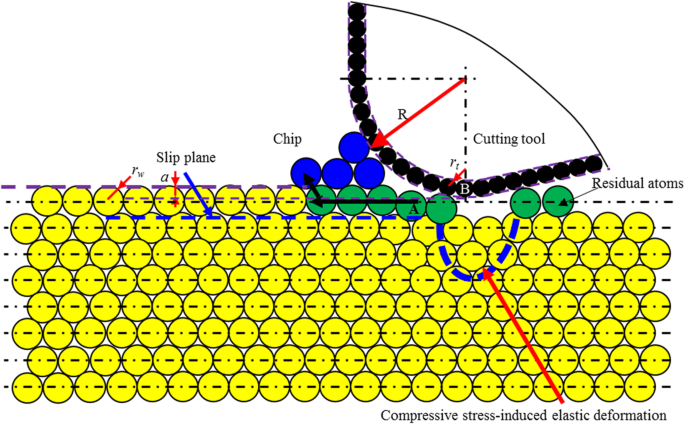
Schematic illustration of cutting-based single atomic layer removal at a/rw larger than C1 and smaller than C2
When the ratio of cutting depth to atomic radius (a/r w ) increases to be larger than critical value, there is a continuous material removal by chip formation during cutting process. In such case, the edge radius effects can no longer be ignored. For ACS cutting process, the maximum cutting depth is subnanometer order. At such extremely low cutting depth, regardless of the nominal rake angle, the effective rake angle is always largely negative. The negative rake face can produce the necessary shear stress to enable chip formation by dislocation motion and the compressive force to enable the elastic and/or plastic deformation on the processed surface.
Depending on the ratio of cutting depth (a ) to tool edge radius (R ), different kinds of elastic and/or plastic deformation process occur on the workpiece surface. There are two threshold values of a/R , namely, threshold value 1 (T 1 ) and threshold value 2 (T 2 ), leading to different material removal processes.
- a.
The ratio of a/R is larger than threshold (T 1 ).
As shown in Fig. 17, there is one atomic slip plane. The workpiece material below this plane would have an elastic deformation. As for the materials above this slip plane, it undergoes a plastic deformation by dislocation motion. A part of materials is also formed into chip by shearing stress-driven dislocation motion, while the other undergoes dislocation slip. After the workpiece passes the lowest point of the cutting tool, the elastically deformed part recovers completely (case 3).
- b.
The ratio of a/R is lower than threshold 1 (T 1 ), but larger than threshold 2 (T 2 ).
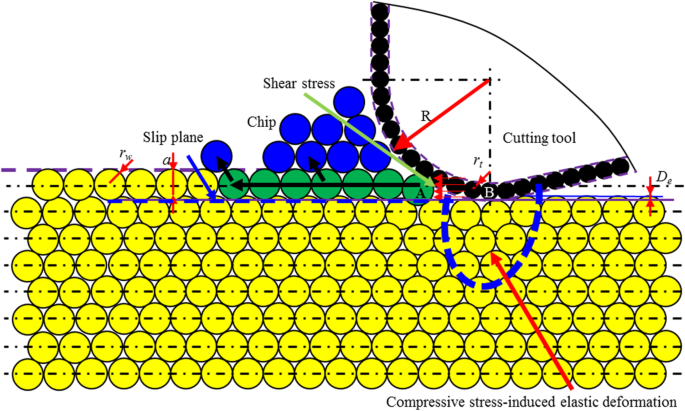
Schematic illustration of cutting-based single atomic layer removal at a/rw larger than C2 and a/R larger than T1
Under the action of cutting edge, minimum two atomic layers undergo dislocation slip, while elastic deformation occurs on the processed surface, as shown in Fig. 18. The cutting edge provides a force to generate the shear stress to enable chip formation by dislocation motion and compressive stress to induce elastic deformation on the processed surface. In such case, part of material within the targeted atomic layer is formed into chip by dislocation motion, while the other is extruded into other atomic layers to form new processed surface. It also drives the slip of other atomic layers on the workpiece surface, leading to the negative dislocation climb. After workpiece material passes the lowest point of the cutting tool, the elastic portion springs back (case 4).
- c.
The ratio of a/R is lower than threshold 2 (T 2 ).
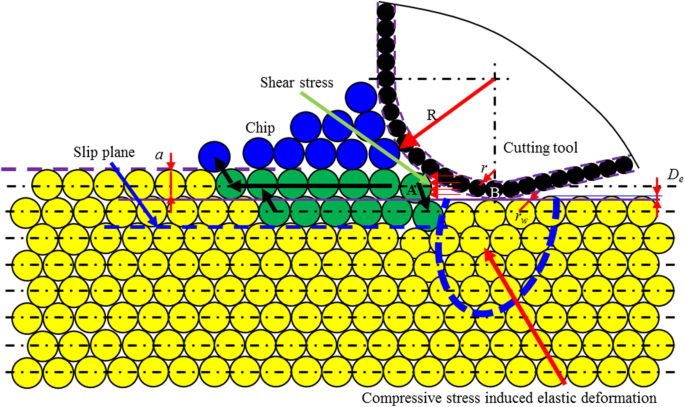
Schematic illustration of cutting-based single atomic layer removal at a/rw larger than C2 , a/R larger than T2 , smaller than T1
As the ratio of a/R decreases to lower than T 2 , there is either no chip formation or extremely small volume of chip formation, but elastic-plastic deformation occurs on the processed surface, as shown in Fig. 19. After workpiece material passes the lowest point of cutting edge, the elastic deformed part springs back. The plastic deformed part (Δ ) leads to lasting deformation. Such ratio is related with material properties, tool geometry and process conditions (case 5).
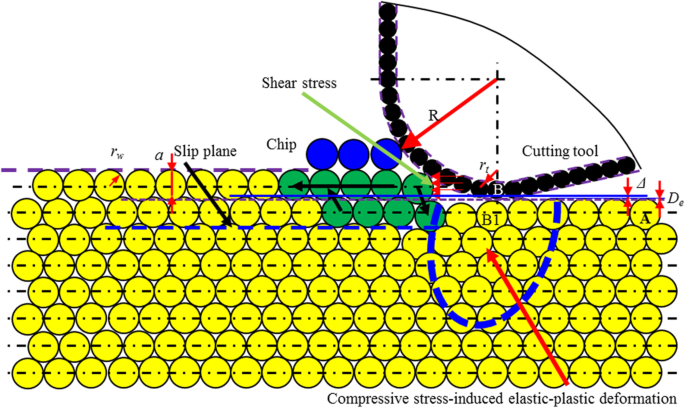
Schematic illustration of cutting-based single atomic layer removal at a/r larger than C2 and a/R lower than T2
Выводы
In the present study, both of atom sizing effect and cutting-edge radius effect are analysed to investigate their influence on chip formation, surface generation, subsurface deformation, and atomic displacement behaviour during the cutting of monocrystalline copper towards single atomic layer removal. The following conclusions can be drawn.
- 1.
A new model is proposed to describe the underlying material deformation and removal mechanism in the cutting-based single atomic layer removal process, which exhibits four characteristics, including chip formation by dislocation motion, elastic deformation occurring on the processed surface, atomic sizing effect, and cutting-edge radius effect.
- 2.
Both of atomic sizing effect and cutting-edge radius effect have a great influence on the material deformation and removal during the cutting process of monocrystalline copper towards single atomic layer removal. With a specific ratio of cutting depth to workpiece atom radius (a/r w ) and that of cutting depth to edge radius (a/R ), cutting-based single atomic layer removal could be achieved on Cu (111) surface.
- 3.
Chip formation is affected by the ratios of a/r w and a/R . There is a chip formation only when the ratio of a/r w is larger than one critical value (C1) and the ratio of a/R is smaller than one threshold value (T1). Moreover, chip formation is mainly dependent on the shear stress-driven dislocation motion, significantly different from the extrusion-dominated chip formation in nanocutting and shearing-dominated chip formation in conventional machining.
- 4.
Single atomic layer removal can be achieved via layer-by-layer removal and multi-layer removal. The former one refers to that the targeted atomic layer could be either fully removed from workpiece surface. The latter one means that the first atomic layer is partly removed while the remaining materials are pressed into other atomic layers, forming a new processed surface.
- 5.
There is only elastic deformation occurring on the processed surface during ACS cutting process, different from the elastic-plastic deformation in nanocutting. It can be regarded as one characteristic feature in ACS cutting.
- 6.
Depending on the combined effect of atom sizing effect and cutting-edge radius effect, there exist five cases of material deformation and removal processes during the cutting-based single atomic layer removal, i.e., no workpiece material is removed (case 1), workpiece materials are non-continuously removed (case 2), a part of materials is formed into chip while others undergoes material slip via dislocation motion (case 3), a part of materials within the targeted atomic layer is formed into chip while others are extruded into other atomic layers to form new processed surface (case 4), and the elastic deformed part springs back, while the plastic deformed part leads to a lasting deformation (case 5).
Доступность данных и материалов
Authors declare that the materials, data, and associated protocols are available to the readers, and all the data used for the analysis are included in this article.
Сокращения
- ACS:
-
Atomic and close-to-atomic scale
- ACSM:
-
Atomic and close-to-atomic scale manufacturing
- MD:
-
Молекулярная динамика
Наноматериалы
- Усовершенствованные технологии осаждения атомного слоя для микро-светодиодов и VCSEL
- Синергетическое фотокаталитически-адсорбционное удаление основного пурпурного эффекта нанокомпозитов AgZnO …
- Иерархические антибактериальные полиамидные 6-ZnO нановолокна, полученные путем осаждения атомных слоев и гид…
- Фотокаталитические свойства порошков TiO2 с покрытием Co3O4, полученных методом плазменного осаждения атомного …
- Настройка уровня Ферми пленок ZnO посредством суперциклического осаждения атомного слоя
- Исследование влияния направления удара на абразивный нанометрический процесс резания с помощью молекулярно…
- Зависимость толщины от межфазных и электрических свойств в атомарном слое, нанесенном на GaN c-плоскости
- Низкотемпературное плазменное осаждение атомного слоя SiO2 с использованием диоксида углерода
- Солнечные элементы с гетеропереходом из кремниевых нанопроволок с пассивирующей пленкой Al2O3, изготовленные …
- Одиночная торцовочная пила по сравнению с двойной торцовочной пилой