Пример использования надежности фармацевтического завода
Специалисты по обслуживанию и надежности могут иметь значение. На большинстве производственных предприятий это означает целенаправленную работу, позволяющую производить больше готовой продукции (будь то безалкогольные напитки, мотоциклы, лампочки, автомобили, кексы, водонагреватели и т. Д.).
На заводе по производству биосинтетического человеческого инсулина (BHI) Eli Lilly в Индианаполисе важнее изменить ситуацию.
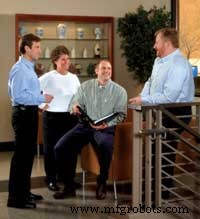
Почти 21 миллион человек в Америке и 200 миллионов человек во всем мире страдают диабетом. Только в США ежегодно диагностируется около 1 миллиона новых случаев. Многим людям с диабетом требуется инсулин для контроля уровня сахара в крови (глюкозы), и растение BHI помогает удовлетворить эту потребность. Этот завод, открытый для производства в 1992 году, производит значительную часть мирового медицинского инсулина. Работа по техническому обслуживанию и обеспечению надежности, повышающая производительность, позволяет компании получать высококачественные, поддерживающие жизнь лекарства в руки тех, кто в них нуждается.
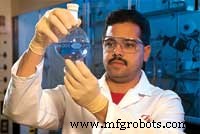
Независимо от того, работаете ли вы в компании, производящей компьютерные чипы или картофельные чипсы, когда вы увеличиваете стоимость для заинтересованных сторон или для экономики, это ни в коем случае нельзя принижать, - говорит Кен Суонк, руководитель группы по техническому обслуживанию и надежности завода. «Неважно, что ты делаешь. Это важно. Однако есть одно явное отличие. Раньше я работал в компании по производству промышленных покрытий. Наши покрытия применялись во всем, от мячей для гольфа до космических шаттлов и хирургических инструментов. Когда я видел конечный продукт, я знал, что являюсь его частью. Но когда ты работаешь в фармацевтической компании. . . это очень много значит на личном уровне.
На выходных я встретил пару, у которой есть маленький сын. Мы поговорили, и я узнал, что у мальчика диабет. Я спросил, есть ли у него тип 1 или тип 2. Отец спросил, откуда вы так много знаете о диабете? Мальчик сказал мне, что он Тип 1. Я посмотрел на него и сказал:«Угадай, чем я зарабатываю на жизнь? Я делаю инсулин. Я работаю в Eli Lilly и делаю Хумулин ». Он сказал:« Спасибо. Мне очень нравится мое лекарство. От этого мне намного легче ».
«Мой отдел отвечает за то, чтобы в этом здании производились лекарства, которые он должен делать каждый раз. Миллионы людей зависят от этого и тянутся к нему каждый день ».
В кампусе компании в Индианаполисе есть
производственные предприятия и корпоративные офисы. сильный>
Рост спроса
Завод BHI большой и технически сложный. В нем размещено более 17 000 единиц оборудования, 13 000 точек ввода / вывода и 600 операционных единиц. Метод обработки для создания молекулы BHI включает несколько этапов центрифугирования, несколько реакций, множество этапов очистки и различные этапы замены растворителя. В результате примерно одна треть операционных единиц классифицируются как операции с высоким риском или критически важные для безопасности.
Несколько лет назад руководители по техническому обслуживанию и надежности решили, что необходимо внести существенные изменения, чтобы максимально использовать время, навыки, ресурсы и возможное влияние на завод. Мощность BHI превышала первоначальную проектную мощность более чем в два раза, а деловой спрос продолжал расти. Технические специалисты были перегружены, усилия по восстановлению часто менялись, чтобы удовлетворить текущие потребности, а важнейшим системам не уделялось должного внимания.
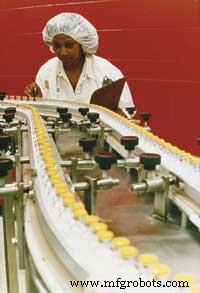
Мы никогда не заботились о том, чтобы наше оборудование работало в надлежащем состоянии », - говорит Суонк. «Но, как и вся остальная фармацевтическая промышленность в то время, мы не уделяли особого внимания нашему оборудованию, за исключением того, что мы всегда хотели получить максимальное время безотказной работы, которое мы могли бы получить, чтобы производить как можно больше лекарств. Но когда вы смотрите на то, чтобы набрать как можно больше килограммов за дверь, мы дошли до того момента, когда вы задаетесь вопросом:«Продолжаем ли мы добавлять объекты или делаем это разумно с точки зрения бизнеса и делаем упор на надежность?» »
Это было то, о чем многие предприятия Eli Lilly размышляли в конце 1990-х годов. Например, технический менеджер BHI Рон Реймер руководил усилиями по увеличению проактивной работы и времени безотказной работы, а также по снижению затрат на техническое обслуживание, находясь в лаборатории компании в Клинтоне (Индиана). В рамках этого проекта, который затем был систематизирован и получил название Proactive Asset Management, он нанял первого инженера по надежности компании.
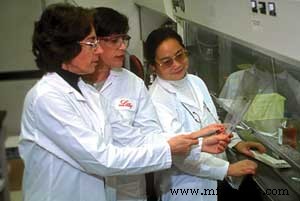
Прямое участие всех основных заинтересованных сторон в обеспечении надежности предприятия
(производство, HSE, контроль качества, финансы, инжиниринг и
менеджмент) помогает обеспечить успех инициативы по
приоритизации надежности.
Усилия BHI по усовершенствованию начались с добавления в 1999 году инженера по надежности и внедрения проектов по техническому обслуживанию, ориентированному на надежность (RCM), и анализа основных причин отказов (RCFA). Эти усилия возросли, когда регулирующие органы, такие как Управление по санитарному надзору за качеством пищевых продуктов и медикаментов и Агентство по охране окружающей среды, начали внимательно изучать техническое обслуживание в фармацевтической промышленности. Послание агентств было простым:техническое обслуживание означает надежность установки; надежность установки равняется надежности продукта; а общая надежность равняется соответствию. «Ненадежным» компаниям грозят штрафные санкции, в том числе прекращение производства.
Важность общения
По словам руководителя группы технического обслуживания и надежности Кена Суонка, коммуникация играет важную роль в успехе инициативы по приоритизации надежности на заводе BHI.
«Общение - одна из самых важных частей моей работы», - говорит он. «Я часто встречаюсь с руководителями производства и объясняю им, что происходит. Я понимаю их приверженность и помогаю им понять, какую ценность это добавляет. Им тоже нужно потратить некоторые ресурсы. Разумеется, надлежащий анализ - это не только наш отдел. Это включает в себя проектирование, техническое обслуживание, надежность, эксплуатацию, технические услуги, временами автоматизацию. Мы тратим много времени на то, чтобы убедиться, что они действительно понимают ценность.
Мне приходится много танцевать и петь, чтобы помочь им понять. Но, судя по всему, бай-ин был хорошим ».
«Именно тогда, я думаю, надежность стала уделять основное внимание, которое она имеет сегодня, - говорит Суонк. оборудование, оно находится в квалифицированном состоянии, оно доступно, когда оно им необходимо, и оно будет работать с заданным уровнем производительности. Очевидно, что мы играем большую роль в этом. Стратегии технического обслуживания, которые мы разработали, направлены на поддержание этого элемента оборудования в квалифицированное состояние. Кроме того, глубина стратегий технического обслуживания учитывает требуемое использование или время безотказной работы. На предприятии есть операции, которые выполняются больше, чем другие, имеют меньшую избыточность, чем другие, или более важны, чем другие. Они требуют большего внимания и более подробного исследования . »
Инициатива по расстановке приоритетов, начатая в начале 2004 года, стала центральной в этой стратегии для обеспечения бесперебойной работы и надежности операционных подразделений, требующих наибольшего внимания.
Как Эли Лилли определяет роли надежности
По словам руководителей службы технической поддержки и надежности Eli Lilly BHI, должностные обязанности и обязанности их инженеров по надежности включают:
- Сведите к минимуму количество отказов оборудования с помощью RCFA, FMEA, анализа RCM, расследований отклонений отведений и т. д.
- Разработайте показатели для оптимизации усилий и ресурсов по обеспечению надежности.
- Собственные планы обслуживания (просмотр / создание / утверждение) для нового и существующего оборудования.
- Реализуйте проекты, ориентированные на надежность, которые влияют на весь поток.
- Сосредоточьте бизнес-методы на обслуживании и надежности, чтобы повысить доступность оборудования.
- Специалисты по надежности наставника.
- Интегрируйтесь с командами диспетчерской для эффективной поддержки их бизнеса.
- Ищите и внедряйте новые технологии для повышения производительности и доступности оборудования.
Функционал и обязанности технических специалистов по надежности включают:
- Поддерживайте инициативы сайта.
- Заполните и обработайте формы ввода данных КСУП.
- Помогите инженерам по надежности с помощью RCFA, интеллектуального анализа данных, FMEA, RCM, отклонений, контроля изменений, полевой проверки, улучшения данных CMMS и т. д. шрифт>
- Специальные проекты - поддержка усилий по обеспечению надежности и т. д.
Сделайте это приоритетом
Суонк пересчитывает приказы о марше, которые в конечном итоге могут привести к повышению надежности.
«Мой начальник в то время сказал:« Подумайте, как мы собираемся сделать объект BHI более надежным ». Нам нужно разобраться с этим », - говорит Суонк. «На самом деле он хотел сказать следующее:« Вам и вашей команде необходимо понять бизнес-потребности предприятия, определить метод, который позволит проложить путь для устранения правильно расставленных пробелов в надежности, продать его бизнесу, выполнить его и сделать это экологично ».
Звучит достаточно просто, по крайней мере, так он думал.
«Мы начали в феврале (2004 г.) и предполагали, что закончим в марте или апреле», - говорит он. «Мы быстро поняли, что это было сложнее и сложнее, чем мы ожидали. К тому же мы хотели сделать все правильно ».
План игры будет заключаться в разработке анализа, который использует существующие данные для определения приоритетов исправления системы как постоянного улучшения, выходящего за рамки ежедневной поддержки отдела. Требования к анализу заключались в следующем:
- он будет брать идентифицированные системы и ранжировать их в соответствии с влиянием на бизнес на основе данных;
- будут представлены все заинтересованные стороны;
- анализ может быть выполнен менее чем за одну человеко-неделю (40 часов).
Эта задача была возложена на плечи отдела проектирования надежности. В состав группы вошли старшие инженеры по надежности Марк Лафевер, Вадим Редчанский и Род Матасовский (ныне на пенсии), а также технические специалисты по надежности Дэвид Дойл, Мэри Энн Даст и Мэтт О’Делл. Они приступили к разработке стратегии содержания анализа.
«Они самые умные. Я был переводчиком от руководства к ребятам в зале », - говорит Суонк. «Они понимали системы данных, и что имело смысл, а что нет».
Группа признала, что для того, чтобы заручиться поддержкой этой инициативы, анализ должен быть основан на фактах и должен напрямую вовлекать и быть значимыми для всех ключевых заинтересованных сторон в области надежности предприятия - производства; здоровье, безопасность и окружающая среда (HSE); контроль качества (QC); финансы; инженерия; и менеджмент. Это должно было быть невероятное достижение баланса.
«Любой может пойти и получить кучу данных», - говорит Лафевер. «Нам нужно было решить, откуда брать данные, как мы собирались их получать, и выяснить, будут ли данные сообщать нам информацию, которая нам нужна для принятия правильных решений».
Таблица 1. Сводка весов для пяти сценариев .
Таблица 2. Пример из анализа чувствительности первого сценария.
После нескольких итераций - и «множества головокружений», - говорит Лафевер - команда завершила анализ, в котором были учтены заинтересованные стороны, используя существующие данные за последние 12 месяцев. Эти данные включают:
1) Часы аварийных работ, приравненные к простою оборудования, для удовлетворения производственных потребностей. Эти данные были получены из компьютеризированной системы управления техническим обслуживанием завода, которая отслеживает все часы, затраченные на каждое рабочее место. Экстренные работы были определены как «работа, которая не может ждать». Хотя это не традиционное измерение времени простоя системы, оно напрямую коррелирует с объемом сбоев, возникающих, когда система не функционирует должным образом.
2) Классификация рисков в соответствии с глобально интегрированным менеджментом безопасности процессов (GIPSM) Lilly для соответствия требованиям HSE. Система классификации имеет четыре возможности:критически важная для безопасности операция, главный фактор риска; высокий риск, связанный со значительным риском для окружающей среды, здоровья и пожара; механическая целостность, определяемая Управлением по охране труда; и никакого риска или «ничего из вышеперечисленного».
3) Количество отклонений от процесса, вызванных отказами оборудования в соответствии с требованиями контроля качества. Это нацелено на отклонения, которые были результатом проблем с надежностью оборудования, а не ошибок оператора или других проблем, не связанных с оборудованием. Количество отклонений учитывалось вместе с уровнем (1, 2 или 3), который определял влияние отклонения на качество продукции.
4) Стоимость реактивных работ для удовлетворения финансов. Это снова было взято из КСУП, которая отслеживает все бюджетные расходы операционных единиц. В эту стоимость включены все детали и рабочая сила, связанные с реактивными работами, выполняемыми в системе.
5) Вклад инженера-технолога для удовлетворения требований инженеров. Инженер-технолог, ответственный за каждую систему, был опрошен по таким темам, как возраст системы, часы потенциального простоя из-за сбоя системы и нормативное влияние.
6) Состояние плана обслуживания системы, также для инженерных нужд. Он был разработан таким образом, чтобы включать четыре уровня:Уровень 1, плановое техническое обслуживание не проводилось, что было признано наиболее серьезным; Уровень 2, профилактическое обслуживание существует в системе; Выполняются уровень 3, периодические квалификационные оценки (PQE), предназначенные для обеспечения того, чтобы система находилась в постоянном состоянии квалификации и пригодна для использования; а на уровне 4 в системе использовался анализ на основе RCM для создания плана обслуживания.
Эти данные позволили провести оценку «критически важного оборудования», в ходе которой были изучены 420 операционных единиц и выявлено то, что потенциально может остановить производство или вызвать инцидент, о котором будет сообщено OSHA или EPA.
«То, как наша структура настроена в нашей КСУП, и то, как мы контролируем нашу базу данных об инцидентах, операционное подразделение было лучшим вариантом», - говорит Лафевер. «Иногда операционная единица - это часть оборудования. В большинстве случаев это основная часть оборудования и многое другое ».
Например, Редчанский говорит, что операционная установка EV1411 (процесс выпаривания) включает «от 50 до 60 единиц оборудования и контрольно-измерительных приборов, таких как клапаны, теплообменники и насосы».
Оценка сократила первоначальный список на 70 процентов, с 420 операционных единиц до 135.
Факты не лгут
Когда дело доходит до определения важности того или иного производственного подразделения, трудно спорить с фактами.
«До того, как мы провели этот анализ, все, о чем говорилось в производстве, было о центрифуге на - передняя часть », - говорит руководитель группы технического обслуживания и надежности Eli Lilly Кен Суонк. «После анализа и демонстрации того, что мы придумали - я указал, что центрифуга заняла 63-е место (в списке из 135 действующих единиц) - они не особо об этом спрашивают.
«Это также заставляет нас смотреть за пределы определения производственного оборудования. Перед анализом люди забыли указать резервуары для отходов, устройства для обработки воздуха и т. Д. Они не подумали о резервуаре 1099 в диспетчерской 2, куда идут все стоки в полу. Смыв проходит через канализацию и попадает в резервуар. Если этот резервуар не работает, мы должны закрыть наши очистные сооружения ».
Меры и вес
Чтобы обеспечить правильную приоритизацию оставшихся 135 единиц, группа решила применить взвешивание к каждому источнику данных и выполнила несколько анализов чувствительности.
«Мы не чувствовали, что шесть критериев одинаково важны, - говорит Суонк. «Мы чувствовали, что безопасность и качество имеют большее влияние, чем, скажем, сумма денег, которые мы тратили на экстренные работы».
Для каждого набора данных была разработана система баллов (от 0 до 3, где ноль означает наименьшее воздействие и серьезность, а 3 - наибольшее воздействие и серьезность), которая применялась к каждому операционному подразделению. Разбивка была следующей:
Часы работы в экстренных случаях (HEW) :менее 15 часов (ноль баллов), от 15 до менее 25 часов (один), от 25 до менее 40 часов (два) и 40 или более часов (три).
Классификация рисков (RC) :нет риска HSE (ноль), система механической целостности (один), процесс с высоким риском (два) и критически важная для безопасности операция (три).
Отклонения (D) :Четыре группировки были составлены с учетом уровней и количества отклонений. Было установлено, что отклонение Уровня 2 было равно трехкратному отклонению Уровня 1, а отклонение Уровня 3 было равно двухкратному отклонению Уровня 2. Таким образом, отклонение Уровня 1 оценивается в одно очко, отклонение Уровня 2 составляет три очка, а отклонение Уровня 3 - шесть очков. Это применялось к каждому отклонению. В результате были получены следующие значения:два или меньше (ноль), больше двух - пять (один), больше пяти - восемь (два) и больше восьми (три).
Стоимость реактивных работ (CRW) :меньше 5000 долларов (ноль), от 5000 до 7 499 долларов (один), от 7500 до 14 999 долларов (два) и 15 000 долларов или больше (три).
Вклад инженера-технолога (PEI) :система минимального воздействия (ноль) и возрастающая до системы максимального воздействия (три).
План обслуживания системы (SSMP) :Анализ RCM выполнен в системе (ноль), PQE выполняется на регулярной основе (один), PM выполнено (два) и плановое обслуживание не выполняется (три).
Оценки были применены к 135 операционным подразделениям. Затем информация была загружена в электронную таблицу, и были применены различные веса, чтобы подчеркнуть важность различных наборов данных. Проект анализа чувствительности включал пять различных сценариев взвешивания, чтобы гарантировать, что одна точка данных не влияет на приоритизацию системы.
Сценарии варьировались от довольно равномерного распределения веса (HEW, HSE, D и SSMP, по 20 процентов каждый; CRW и PEI, по 10 процентов каждый) до исключения двух категорий (HEW, HSE, D и CRW, по 20 процентов каждая; PEI и SSMP, ноль процентов). В последнем сценарии оставшиеся наборы данных были «истинными данными», которые изменялись в соответствии с уровнем надежности, продемонстрированным системой. Сценарии показаны в Таблице 1.
В каждом сценарии анализа чувствительности фактор риска умножался на вес этого конкретного сценария. Продукт каждой категории был суммирован для каждой операционной единицы. В таблице 2 показан пример из первого сценария.
Когда все пять сценариев были выполнены, окончательные баллы для операционных единиц были нанесены на график и исследованы группой надежности. Перед тем, как определить окончательные рейтинги и планы реабилитации, были учтены дополнительные факторы. Было ли заменено данное устройство недавно или замена предусмотрена в плане капитального ремонта? Могут ли планы восстановления для этого блока применяться к другим блокам? Какие функциональные группы необходимы для этого исправления и доступны ли они? Какие меры по исправлению положения были выполнены в прошлом?
«Например, одна из центрифуг вышла в верхней части списка, но мы знали, что другой сайт проводил RCM на очень похожей системе», - говорит Суонк. «Нам не нужно было дублировать усилия».
Окончательный список предлагаемых мероприятий по исправлению положения варьировался в зависимости от подразделения:от углубленного анализа RCM до полного отказа от исправления системы.
На тот момент команда знала, что у них есть всеобъемлющий план.
«Это была тяжелая работа, - говорит Лафевер. «Мы придумывали план трижды - было около 30 - и мы продолжали говорить:« Это недостаточно хорошо ».« Каким образом контроль качества будет относиться к этому? »« Как инженеры-технологи отнесутся к этому? »Мы были очень озадачены. Мы должны были убедиться, что мы рассмотрели все аспекты и все возможные вопросы ».
Свонк добавляет:«Первый удар по этому поводу был такой:« Вау, это даже не близко ». Стало очевидно, почему этого не сделали раньше. Это много работы. Есть также повседневные вещи, которые отвлекают вас от чего-то подобного. Но мы сказали себе, что будем продолжать и делать это ».
В письменной форме
21 сентября 2004 г. Суонк официально представила модель приоритезации руководящей группе предприятия, в которую входят руководитель предприятия и все функциональные менеджеры. Семь месяцев изнурительной работы окупились.
«Не было обмена или дискуссий взад и вперед», - говорит он. «Они были такие:« Это здорово. Продолжить »»
Конечно, кивок головы и махание рукой - это еще не все. Итак, Суонк попросил Лафевер создать отчет, в котором подытожил процесс оценки и подробно описал, как будет проводиться критический анализ оборудования из года в год. Отчет послужит шаблоном для будущих оценок.
«Я сказал руководителям группы подписать его, - говорит Суонк. "Они сделали. Имею это в письменной форме. Никаких колебаний. Это говорит о том, что проведенный нами анализ был действительно сильным ».
28 февраля 2005 г. анализ важнейшего оборудования был формализован и одобрен руководящей группой, а мероприятия по восстановлению наиболее важных производственных единиц завода были включены в бизнес-планы завода на 2005 и 2006 гг.
Шаблон сделал последующие оценки практически безупречными.
«В прошлом году было легко провести анализ», - говорит Лафевер.
План на 2006 год был завершен в мае.
Результаты Remedy
Руководители отделов технического обслуживания и надежности на этом заводе в Eli Lilly заявляют, что в настоящее время они не могут количественно оценить итоговый результат инициативы по приоритизации надежности в долларах и центах.
«К сожалению, мы не всегда видим результаты своей работы год за годом», - говорит Лафевер. «Может быть задержка на год, потому что на проработку системы нужно время».
Но это не значит, что не было никаких преимуществ и результатов.
Редчанский и Дойл говорят, что неизбежна экономия затрат, если просто переоценить, как проводится техническое обслуживание данного актива.
«В ходе анализа мы обнаружили, что тратили значительную сумму денег на пару систем, у которых не было никакой реактивной работы», - говорит Редчанский. «Мы потратили тонну на профилактическое обслуживание. Мы перестарались с личками. Мы изменили способ обслуживания этих систем ».
«Самый большой сдвиг от этого состоит в том, что для некоторых систем люди теперь могут сказать, что на самом деле нормально работать до отказа», - говорит Дойл. «Если это наш диагноз и план для этой конкретной системы, все в порядке. Для нас это совершенно другая философия ».
Суонк говорит, что положительные результаты можно извлечь из уровня производительности завода.
«Тот факт, что мы достигли уровня запасов и то, что наша бизнес-модель движется в сторону повышения производительности, показывает, что мы уже достигли нашей первой важной вехи», - говорит он.
Лафевер считает, что участие в проектах по восстановлению привело к расширению технических знаний и увеличению времени безотказной работы.
«Когда большинство специалистов по обслуживанию и эксплуатации выходят из анализа RCM, их можно классифицировать как экспертов по этой системе», - говорит он. «Все лучше понимают индивидуальные функции групп и то, как они работают вместе, чтобы выполнить свою часть работы по ремонту части оборудования или выявлению проблем с частью оборудования. Само по себе такое взаимодействие, я думаю, сокращает объем возникающих аварийных работ ».
Лучший показатель успеха?
«Это делает наше высшее руководство счастливым, - говорит Дойл.
«И это делает меня счастливым», - говорит Суонк.
Все эти улучшения могут объяснить, почему BHI получила награду Making Medicine Award 2005, которая присуждается заводу Eli Lilly, который «наилучшим образом отвечает потребностям бизнеса и воплощает то, каким должно быть производство в компании».
Другие заводы Lilly принимают к сведению инициативу по приоритизации и изучают возможность принятия. Это привело к повышению прозрачности обслуживания и надежности в масштабах всей компании.
«Частью пользы было корпоративное понимание и осознание ценности, которую добавляет техническое обслуживание», - говорит Реймер. «Это то, чем мы определенно хотим воспользоваться».
Эта команда ежедневно демонстрирует, что профессионалы в области обслуживания и надежности могут иметь значение и действительно имеют значение.
Техническое обслуживание и ремонт оборудования
- Пример использования:приводы и модернизация продольно-перемоточной машины бумажной фабрики
- Поршневой завод использует упреждающий подход к обеспечению надежности и OEE
- Дрю Тройер:Как бизнес-процессы влияют на надежность
- Как надежность предприятия влияет на экономичное внедрение
- Гидроэлектростанция на Гавайях повышает эффективность и надежность
- Саудовская электроэнергетическая компания для повышения надежности электростанции
- Беспроводная система для повышения надежности на электростанции в Неваде
- Повышение доступности - это гораздо больше, чем просто обслуживание
- NV Energy устанавливает беспроводное решение для повышения надежности предприятия
- Пример:решение проблемы с отключением машины