Подключенный контроль
Интернет и облачные вычисления меняют то, как производители используют станки с ЧПУ. Ваш магазин готов к этому?
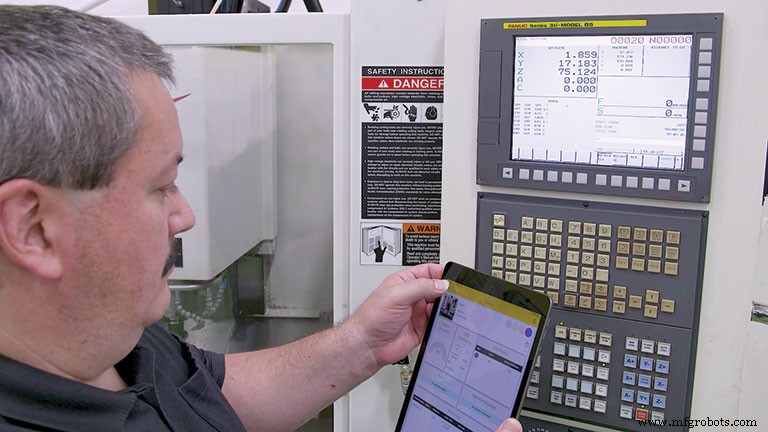
Порты Ethernet впервые начали появляться на токарных станках с ЧПУ и обрабатывающих центрах более 20 лет назад. Стандарт связи станков MTConnect официально дебютировал в США на IMTS 2010 в Чикаго. Вскоре после этого производители заговорили об облачных вычислениях и промышленном Интернете вещей (IIoT). Эти термины стали общепринятыми, когда в 2015 году немецкий экономист Клаус Шваб опубликовал статью, в которой утверждалось, что мир вступил в Четвертую промышленную революцию.
Добро пожаловать в 2021 год. К настоящему времени владельцам механических цехов, программистам ЧПУ и инженерам-технологам должно быть очевидно, что за последние два десятилетия обрабатывающая промышленность значительно изменилась. Станки с ЧПУ намного умнее, чем когда-то, и могут генерировать значительные объемы данных обо всем, что происходит за стеклом. Производственное программное обеспечение также стало умнее, предлагая совместимость и облачные возможности, о которых на рубеже веков можно было только мечтать.
Является ли все это техническое волшебство хорошей вещью или нет, подлежит обсуждению. Кто-то может возразить, что жизнь в цеху уже достаточно сложна — кому нужны большие данные и интеллектуальное оборудование, когда в сутках едва хватает часов, чтобы доставить детали до двери? Другие считают Индустрию 4.0 и все, что с ней связано, четким путем для производителей, и любой, кто ее не примет, скоро вылетит из бизнеса.
Получение FOCAS
Истина лежит где-то посередине. Пол Вебстер, директор FA Engineering в FANUC America Corp. со штаб-квартирой в Рочестер-Хиллз, штат Мичиган, отметил, что станки с ЧПУ были готовы к работе в сети и в Интернете еще до 2000 года. Магазины, решившие игнорировать эту возможность, по-прежнему прекрасно работают, спасибо, и будут продолжать делать это еще долгие годы. И все же мало кто станет спорить с тем, что подключение к станку и улучшенная видимость процессов обработки никогда не бывают плохими и могут иметь значение между прибыльной работой и той, о которой вы так же скоро забудете.
«Мы представили наш FOCAS API (интерфейс прикладного программирования) в начале 90-х годов, а также оптоволоконные порты, а затем порты Ethernet, поэтому подключение ЧПУ уже довольно давно стало простым», — сказал он. «Самым сложным всегда было выяснить, какие данные вам нужны и что вы собираетесь с ними делать, когда они у вас появятся».
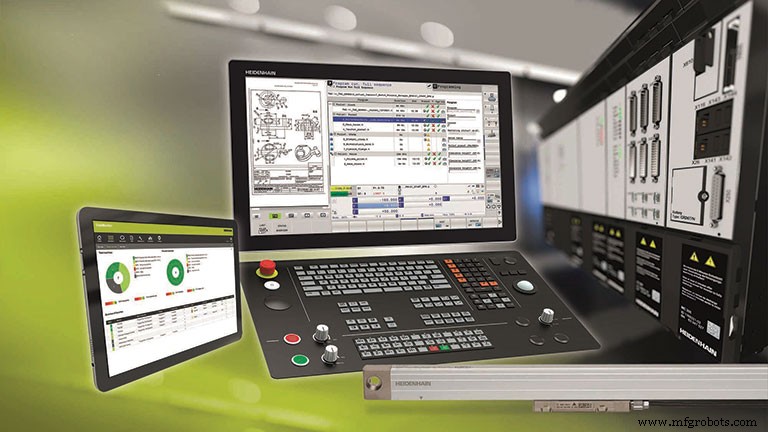
Эти данные включают историю сигналов тревоги, скорость подачи и настройки блокировки шпинделя, температуру серводвигателя и шпинделя, потребляемую мощность, макропеременные и многое другое, и все это может быть получено из станка в непрерывном и автоматическом режиме. Добавьте к этому различные входные данные, предоставляемые оператором — номер задания, статус производства, потребление режущего инструмента и даже информацию о качестве детали — и получить полную картину работы цеха станет не сложнее, чем взглянуть на панель инструментов любого программного обеспечения для мониторинга, собирающего эти данные. .
В случае FANUC это MT-LINKi, независимая от бренда аналитическая платформа, способная одновременно отслеживать более 1000 станков с ЧПУ, а также FASData, программа производственного мониторинга. Аналогичные решения предлагают и другие производители систем управления, а также многие производители станков, поставщики режущего инструмента и сторонние разработчики программного обеспечения. Все они предоставляют средства для сбора, по общему признанию, горы данных и представления их в понятном для людей виде, что дает им возможность реагировать на тенденции и потенциальные проблемы задолго до того, как они смогут негативно повлиять на уровень производства.
Загадка облака
Тогда возникает вопрос, где лучше всего хранить эти данные и где размещать программное обеспечение, используемое для их анализа? Должны ли они оба размещаться в облаке на удаленном хостинге и управляться выделенными специалистами по оборудованию и программному обеспечению? Или более уместна установка «на месте» с использованием всех внутренних ИТ-специалистов, которыми обладает магазин?
Вебстер и другие, опрошенные для этой статьи, в целом согласились с тем, что, хотя первый подход часто является более безопасным и экономичным, многие цеха по-прежнему скептически относятся к программам обработки деталей и производственным данным, покидающим их предприятие. Как и Гисберт Ледвон, директор по развитию бизнеса станков в компании Heidenhain Corp., расположенной в Шаумбурге, штат Иллинойс. Он отметил, что клиенты могут устанавливать программное обеспечение StateMonitor компании в любом месте, но по возможности поощряют установку на месте.
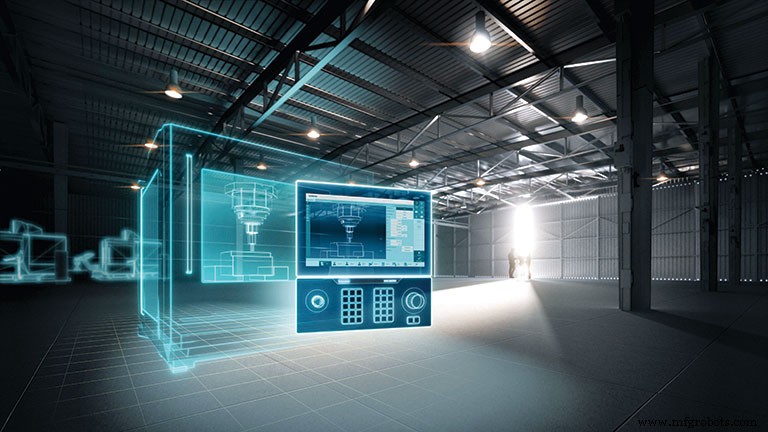
«Наша философия заключается в том, что клиенты должны защищать свою интеллектуальную собственность, а для нас это означает подключение их станков и программных систем к должным образом защищенной корпоративной сети», — сказал он. «Было много случаев, когда магазины были взломаны и вынуждены платить выкуп. Конечно, эти атаки обычно осуществляются через электронную почту, а не через управление станком, но тем не менее это вызывает беспокойство. Вот почему NTMA (Национальная ассоциация инструментальной и механической обработки) начала проводить семинары, показывающие производителям, как они могут защитить себя от подобных киберпреступлений».
Несмотря на это, Ледвон признает, что облако — это технологический тренд, который будет только набирать обороты. Что необходимо для снижения любых сопутствующих рисков, так это хорошие методы ведения ИТ-обслуживания. Установите надежный брандмауэр между сетью магазина и внешним миром. Избегайте прямого подключения ЧПУ к облаку, загружая внешние файлы, программы и исправления на защищенный внутренний сервер, а затем проверяя их с помощью антивирусного программного обеспечения перед распространением. Обучите всех пользователей компьютеров тому, как управлять паролями, обнаруживать вредоносные электронные письма и веб-сайты и защищать корпоративную информацию. Список можно продолжить.
«Учитывая, что управление является нервным центром любого станка, я не думаю, что удобство облачного доступа стоит риска, связанного с Интернетом», — сказал Ледвон. «Однако ничто из этого не мешает производителям внедрять стратегию Индустрии 4.0. Во что бы то ни стало, они должны объединить свои станки в сеть и начать сбор данных для анализа. Это даст им информацию, необходимую для более быстрой настройки станков, сокращения времени цикла, увеличения срока службы инструмента и получения всех других преимуществ, предлагаемых современными системами управления ЧПУ и программными системами».
Родной талант
Еще одним компонентом Индустрии 4.0 является цифровой двойник, который в данном случае относится к виртуальному, но очень точному и всеобъемлющему представлению станка с ЧПУ. По словам Вивека Фуртадо, руководителя отдела цифровых станков Siemens Industry Inc. (Элк-Гроув-Виллидж, Иллинойс), цифровые двойники упрощают проектирование и развертывание станков с ЧПУ, что в конечном итоге повышает эффективность производителей.
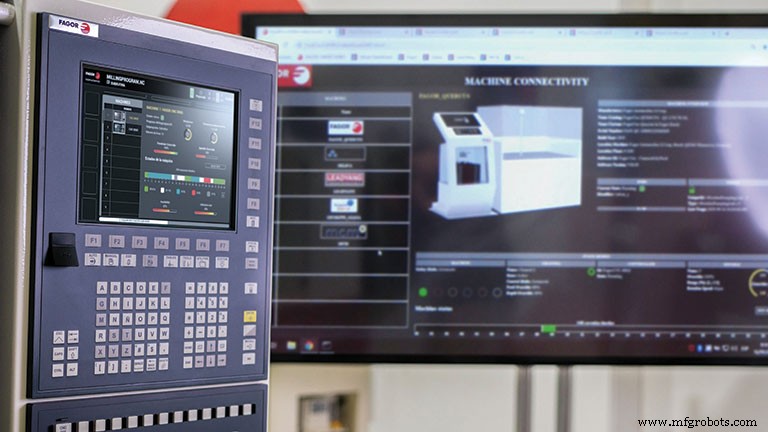
«Наш контроллер SINUMERIK One известен как цифровой, поскольку он был создан с нуля для поддержки цифрового двойника и других передовых технологий», — сказал он. «Это дает производителям станков с ЧПУ возможность создавать виртуальную версию токарного станка или обрабатывающего центра, содержащую все его кинематику и рабочие характеристики. Это значительно сокращает время проектирования и затраты на разработку, а также гарантирует, что продукт будет соответствовать потребностям конечных пользователей».
Контроллеры с поддержкой цифровых двойников служат другим целям. Они ускоряют обучение новых сотрудников и снижают вероятность поломки дорогого станка. Они позволяют сметчикам более точно определять стоимость работ, инженерам разрабатывать оптимизированные производственные процессы, а программистам станков с ЧПУ проверять G-код и выбор режущего инструмента перед отправкой работы в цех. Оказавшись там, они упрощают работу станка благодаря улучшенной графике и удобству использования.
Любой, у кого есть высокотехнологичная CAM-система или программное обеспечение PLM, может сказать, что может выполнить большую часть этого без расширенного управления ЧПУ. И хотя нет никаких сомнений в том, что возможности этих и других программных платформ значительно расширились за последние годы, станки, участвующие в цифровом потоке, предоставляют механическим цехам важный инструмент, улучшающий обмен данными и замыкающий цикл функциональной совместимости.П>
Приспособиться и преодолеть
Помимо цифрового дублирования, Фуртадо предположил, что контроллеры с ЧПУ становятся гораздо более интеллектуальными и удобными для пользователя, с функциями и возможностями, которые узнает любой пользователь смартфона. «Большинство из нас помнят, что когда-то мы использовали наши телефоны, чтобы звонить людям», — сказал он. «Сегодня они позволяют следить за своим здоровьем, искать информацию, делать заказы на продукты и так далее. Более новые поколения контроллеров предлагают аналогичную функциональность. Они могут обрабатывать информацию и подготавливать данные таким образом, чтобы их могли более эффективно использовать операторы-люди или другие системы».
Этот интеллект распространяется и на процесс обработки. Siemens, FANUC и сторонние поставщики решений, такие как Caron Engineering, предлагают возможности адаптивного управления, которые непрерывно отслеживают нагрузки на шпиндель и оси, вибрацию станка и другие подобные факторы, влияющие на срок службы режущего инструмента и качество деталей. Затем эти интеллектуальные системы регулируют параметры обработки в режиме реального времени, оптимизируя съем материала и устраняя потенциальные проблемы.
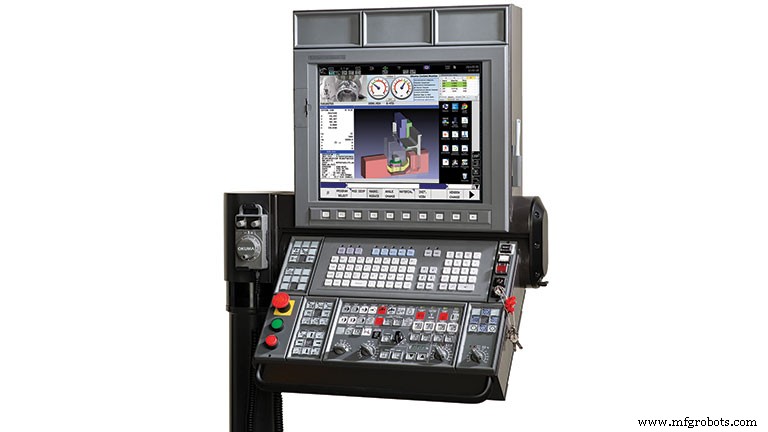
Fagor Automation Corp., Элк-Гроув-Виллидж, штат Иллинойс, является еще одним поставщиком систем управления, стремящимся получить награду «Индустрия 4.0». Харш Бибра, генеральный менеджер Fagor в Северной Америке, объяснил, что его система управления ARFS (адаптивная подача и скорость в реальном времени) делает все это и многое другое, но отметил, что этот тип технологии на основе датчиков также может использоваться для профилактического обслуживания.Р>
«Мы также предлагаем наш пакет подключения i4.0», — сказал он. «Конечно, это позволяет пользователям собирать данные об обработке, а также выполнять такие действия, как отправка предупреждений о состоянии, настройка станка и обновление его прошивки, изменение настроек параметров и т. д. — и все это с мобильного устройства или удаленного компьютера».
Самое узкое место
Бибра видит большие перемены впереди. Помимо более широкого использования датчиков и акселерометров с поддержкой IIoT в станках вместе с более интеллектуальными контроллерами, сами фабрики станут умнее. Искусственный интеллект (ИИ), выходящий далеко за рамки только что упомянутых адаптивных возможностей, станет преобладающим, открывая двери для автоматизированного принятия решений, необходимого для широкомасштабного производства без отключения света.
Все это будет буквально набирать скорость с учетом развития и последующего развертывания сотовых сетей 5G, предположил Бибра. Это не только увеличит пропускную способность Интернета и уменьшит задержку, но, возможно, уменьшит опасения хакеров, упомянутые ранее. «Управление будущего будет оснащено 5G, а генерируемые ими данные можно будет отправлять по беспроводной сети со скоростью до 10 гигабит в секунду (Гбит/с) на так называемые периферийные устройства», — сказал он. «Мы рассчитываем, что через несколько лет эта технология коренным образом изменит способы сбора производителями информации в цехах».
Обратной стороной Индустрии 4.0 является нехватка квалифицированных рабочих, способных разбираться в передовых технологиях и работать с ними. Бибра сказал, что переобучение будет необходимо, поскольку производители становятся более технически подкованными. Однако любые опасения по поводу племенных знаний и потери опыта из-за увольнения сотрудников и выхода на пенсию должны стать древней историей.
Посещение магазина
Джим Космала, вице-президент по проектированию и технологиям Okuma America Corp., Шарлотт, Северная Каролина, объясняет большую часть сегодняшних расширенных возможностей подключения использованием элементов управления на базе ПК. «Многие забывают, что Okuma не только производит станки, но и производит собственные сервосистемы и контроллеры. Они работают под управлением Microsoft Windows и используют чип Intel, оба из которых обеспечивают простоту подключения».
Элементы управления на базе ПК также упрощают установку различных программ на элемент управления — например, в начале пандемии COVID клиенты Okuma могли сотрудничать с другими, используя Microsoft Teams, совместно используя экраны или предоставляя другим удаленное управление по мере необходимости. «В этом вся идея нашего App Store, — сказал Космала. «Пользователи могут загружать и устанавливать все, что им нужно, непосредственно в системе управления OSP, что устраняет необходимость в отдельном ПК. Он представляет собой совершенно новые возможности для совместной работы и взаимодействия».
Одним из таких приложений является Connect Plan от Okuma, которое позволяет пользователям контролировать станки с ЧПУ и собирать рабочие данные. Он работает с большинством станков любой марки или года выпуска, а также с роботами и другими формами автоматизации. Однако, по словам Космалы, Connect Plan использует алгоритм искусственного интеллекта для просмотра доступной информации и выявления тенденций, которые может пропустить человек.
Возьмем менеджера токарного цеха, который после нескольких недель просмотра отчетов по сбору данных и информационных панелей замечает, что определенный токарный станок каждое утро запускается на 10 минут позже, благодаря привычке оператора к кофе, или что температура шпинделя на ближайшем к температуре шлифовальном станке Отдел доставки падает каждый раз, когда они открывают загрузочную дверь. Космала объяснил, что ИИ улавливает эти тенденции гораздо быстрее, чем человек, что дает руководителям возможность быстрее решать потенциальные проблемные области. Более того, эта информация хранится в базе данных, поэтому, когда руководитель покидает компанию, информация не теряется.
«Деминг сказал нам, что без данных вы просто еще один человек со своим мнением», — сказал Космала. «Промышленный Интернет вещей и Индустрия 4.0 предназначены для сбора этих данных и их использования, в конечном итоге превращая их в знания. Это первый шаг для каждого на этом пути. Теперь у нас есть виртуальные конференции и возможность проверять состояние машин или уровень производительности из любого места, а также доступ к удаленным инструментам, которые упрощают автоматизацию. Если вы можете сделать это, не заходя на завод, тем лучше. Все дело в повышении эффективности и времени безотказной работы станка, а оба этих аспекта легче выполнить с помощью современных контроллеров ЧПУ».
Система управления автоматикой
- Что мне делать с данными ?!
- Демократизация Интернета вещей
- Будущее центров обработки данных
- Основы электрических панелей управления
- Машинное обучение в полевых условиях
- Интеграция промышленного Интернета вещей
- Облако в Интернете вещей
- На краю славы:запуск новой эпохи интернет-машин
- Декодер обеспечивает подключенный мониторинг данных каждой машины
- Многочисленные преимущества фабрик, подключенных к интеллектуальному IIoT