Стратегии гринда:от хорошего к отличному
Как программное обеспечение, автоматизация и достижения в области абразивных материалов ускоряют шлифование деталей и инструментов.
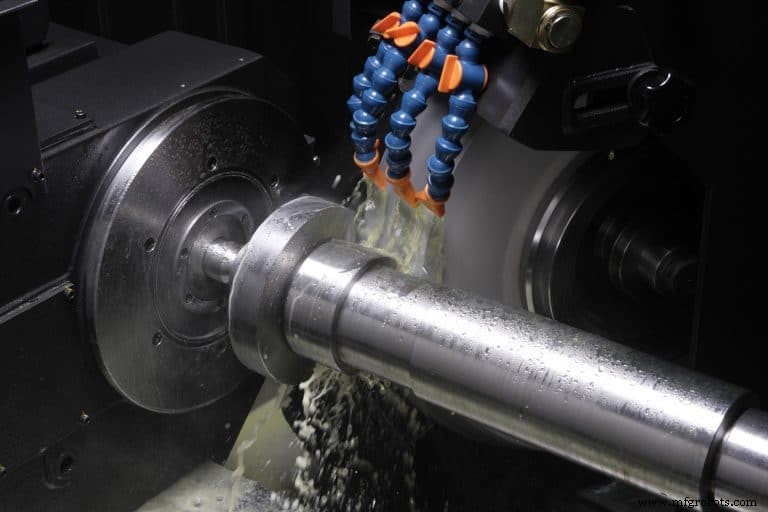
Возможно, ваша компания специализируется на аэрокосмических или медицинских компонентах, и вам необходимо производить изделия сложной геометрии из металлов, которые не поддаются резке традиционными методами механической обработки. Или, может быть, вы работаете или владеете магазином инструментов и фрез и ищете более быстрые и экономичные способы производства сверл, концевых фрез и фасонных инструментов. Какой бы ни была причина и какие бы ни были требования, вам повезло. Как и в случае с большинством технологий металлообработки, шлифование — правильнее называть его абразивной обработкой — за последние годы значительно улучшилось.
Как так? Во-первых, производители шлифовальных кругов разработали новые связки и суперабразивные материалы
, которые однозначно заслуживают звания «супер» и способны удалять больше материала за меньшее время, чем когда-либо прежде. И производители шлифовальных станков поставляют все более функциональное оборудование, достаточно жесткое и мощное, чтобы в полной мере использовать преимущества передовых абразивов, добавляя к своим станкам интеллектуальные функции, такие как автоматизация, удаленный мониторинг и интеллектуальные программные системы.
Проще говоря, шлифование вступило в новую эру производительности и точности деталей; если вы не воспользуетесь этим преимуществом, вы можете упустить значительные возможности для улучшения процессов, повышения качества продукции и увеличения прибыли.
Лучший контроль имеет решающее значение
Основной причиной этого является нехватка квалифицированных машинистов. Это, по словам Шейна Фарранта, национального менеджера по продуктам шлифовальных станков в JTEKT Toyoda Americas Corp., Арлингтон-Хайтс, Иллинойс, который добавил, что облегчение понимания человеко-машинного интерфейса (ЧМИ) является необходимым первым шагом на пути к минимизации последствий менее квалифицированная рабочая сила.
«Более простой и интуитивно понятный ЧМИ — это одно из многих усовершенствований станка, которые мы разработали для нашей линейки универсальных станков для шлифования цилиндрических, распределительных и коленчатых валов, — сказал он. «Это означает удобный для пользователя формат с большей зависимостью от изображений и другой графики, облегчающей настройку и процедуры программирования».
Также был сделан большой толчок к созданию рабочей среды на основе Интернета вещей (IoT). Например, на странице диагностики сенсорного управления Toyoda TOYOPUC отображаются уровни охлаждающей жидкости, вибрация машины, температура масла — все, что может привести к низкому качеству детали или создать производственную проблему, немедленно отправит предупреждение тому, кто несет ответственность за ее устранение. Кроме того, эту информацию можно собирать с системы управления машиной и передавать в сетевую базу данных для исторического анализа.
Еще одной функцией, позволяющей сэкономить время, является автоматическое создание альтернативных программ, которые оператор может вызвать в случае возникновения проблем, связанных с технологическим процессом. Технический директор JTEKT Toyoda Proposal Стив Эрли сказал, что эта опция диалогового управления доступна на вальцешлифовальном станке GE6, который также выиграл от некоторых модификаций литья, двигателей и других компонентов, предназначенных для снижения вибрации и повышения точности станка. это специальное приложение.
По его словам, материалы, используемые для изготовления литиевых батарей, используемых в электромобилях, довольно тонкие, поэтому валки, производящие этот материал, должны быть очень точными, с очень тонкой обработкой поверхности. «Когда оператор настраивает станок, система управления представляет для начала обобщенную программу, а также две альтернативные — одну, более агрессивную для сокращения времени цикла, и более консервативную программу, обеспечивающую лучшее качество поверхности», — сказал Эрли. . «Основываясь на первоначальных результатах, оператор может легко принять решение о переключении на тот набор параметров обработки, который обеспечивает получение наилучшей детали в кратчайшие сроки».
Требуется меньше операций
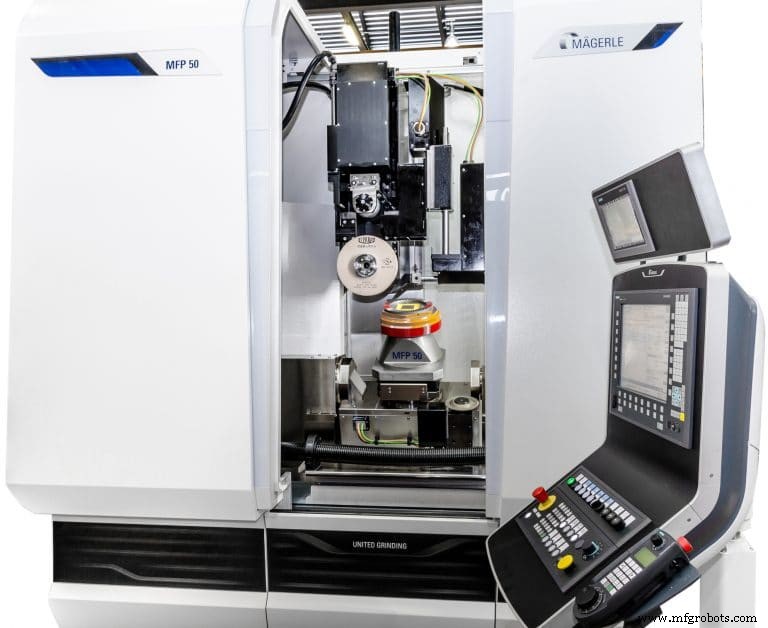
Ларри Маршан, вице-президент профильной группы United Grinding North America Inc., Майамисбург, штат Огайо, согласен с необходимостью простых в использовании элементов управления, особенно по мере того, как шлифовальные станки становятся более функциональными. Но он также сказал, что в производственном сообществе существует огромный призыв к сокращению незавершенного производства и меньшему количеству операций механической обработки, что побудило United Grinding и другие компании принять так называемый подход «сделано за один раз», чтобы сократить время, затрачиваемое оператором. увеличить значение за операцию.
Чтобы поддержать это, United Grinding представила «дополнительные процессы, операции и функции» для профильных шлифовальных станков, которые когда-то были узкоспециальными. «Клиенты хотят повысить ценность обработки одной детали», — сказал Маршан. «Мы наблюдаем большой спрос на станки с автоматической сменой инструмента, что позволяет шлифовать заготовку, а затем использовать дрель или фрезу для окончательной обработки детали. Это устраняет второстепенные операции, сокращает время выполнения заказа и повышает качество».
Означает ли это, что механические мастерские должны обменять свои станки с ЧПУ на универсальный супершлифовальный станок? Нисколько. Точно так же, как многозадачные станки чертовски хорошо справляются с фрезерованием паза или шлифованием шейки, многозадачный шлифовальный станок теперь может выполнять задачи, которые когда-то предназначались для обрабатывающих центров и станков для сверления метчиком — при этом ни один тип станка не может заменить другой. Как заметил Маршан:«Если у вас есть деталь, требующая интенсивного шлифования, вам всегда лучше использовать специальный шлифовальный станок».
По его словам, на это есть несколько причин. Шлифование требует значительно большего количества смазочно-охлаждающей жидкости, чем фрезерные и токарные операции, направленные именно на пересечение заготовки и круга. Привод колеса диаметром в пару футов требует много лошадиных сил, намного больше, чем доступно на среднем станке для изготовления стружки. Наконец, удержание десятых долей и однозначной чистоты поверхности в течение всего дня — это то, в чем преуспевает большинство шлифовальных станков с ЧПУ, потому что они предназначены для оптимизации этих операций. Обрабатывающие центры? Не так много.
Решение сложных задач
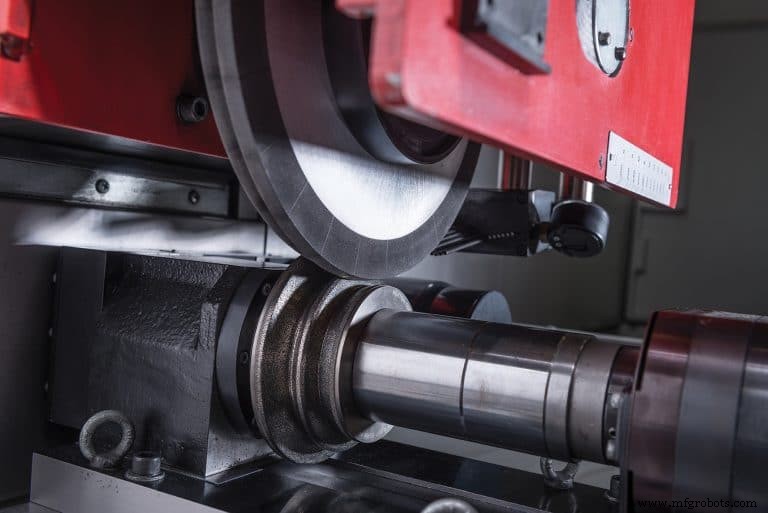
По словам Маршана, эти возможности особенно важны для металлов с высоким содержанием никеля, хрома и кобальта. «Большая часть нашего бизнеса приходится на клиентов, производящих детали из материалов Inconel и Rene, которые — по крайней мере, в закаленном состоянии — почти не поддаются механической обработке. Их единственный вариант — электроэрозионная обработка или шлифование, и благодаря жесткости, мощности и точности современных шлифовальных станков, а также наличию суперабразивов, недоступных до недавнего времени, большинство выбирает последнее».
Одним из ведущих производителей суперабразивов является компания Norton|Saint-Gobain Abrasives, Вустер, Массачусетс. все более эффективной технологии шлифования, превратилась в основной процесс обработки. Однако для достижения наибольшего успеха в этом процессе необходимо применять не менее современные абразивы.
«Традиционные круги с алмазной матрицей на полимерной или металлической связке, как правило, очень плотные, — сказал Барраган. «Быть плотным — это хорошо, потому что это дает вам прочную структуру и помогает обеспечить прочную связь, которая удерживает эту структуру вместе, но это вызывает одно соображение:колесо имеет тенденцию загружаться быстрее, что в долгосрочной перспективе снижает производительность. Гибридные круги Norton Winter Paradigm решают эту проблему».
Говорят, что круги обеспечивают сочетание улучшенного удержания зерна с высоким уровнем пористости, что снижает силы резания. Более высокая пористость также снижает нагрузку — круг шлифует при более низкой температуре, более свободно, с меньшим временем простоя, что в конечном итоге позволяет производить больше деталей в день. В зависимости от используемого абразива круги на гибридной связке эффективно шлифуют твердые сплавы, передовую керамику, закаленные инструментальные стали и жаропрочные сплавы, упомянутые Маршаном из United Grinding.
Однако это нечто большее, чем технология абразивных материалов. Как и станки, к которым они прикреплены, сами колеса становятся умнее, со встроенными RFID-метками для лучшего управления активами, упрощения закупок, отслеживания информации об использовании и зачистке, а также защиты от ошибок оператора.
Norton|Saint-Gobain также не ограничивает свои усилия абразивными продуктами. Его система мониторинга и диагностики процессов 4Sight обеспечивает функциональность IoT, аналогичную той, что обсуждалась ранее, с независимым от бренда мониторингом в режиме реального времени параметров шлифовального станка, таких как нагрузка на шпиндель и использование станка, а также возможностью сохранять данные для анализа тенденций или отправки предупреждений по мере необходимости. . «Это одна из крупнейших инициатив года для нас, и вместе с нашими системами смарт-тегов она служит основой нашего решения для Индустрии 4.0», — сказал Барраган.
На вашем экране:В@дисон
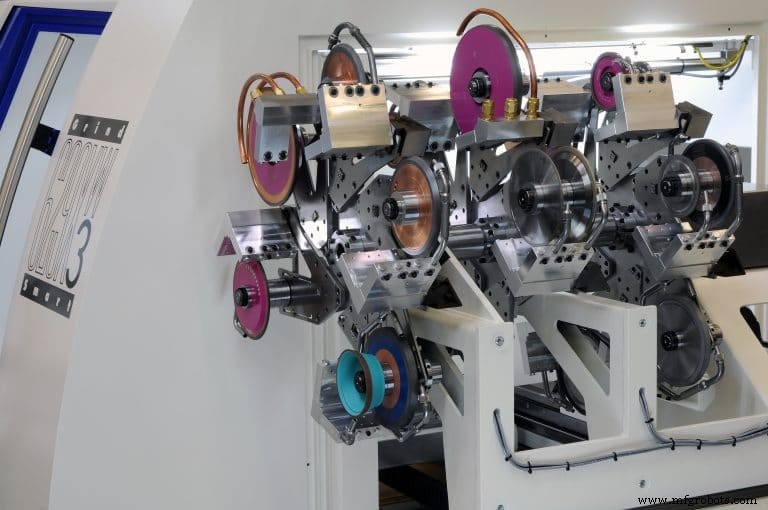
Они не одиноки. Vollmer of America Corp., Карнеги, Пенсильвания, вместе со своей материнской компанией Vollmer Group работает над рядом инструментов и услуг, предназначенных для «цифрового преобразования» шлифовальных операций. Под торговой маркой V@dison они включают в себя экран V@ для улучшенной визуализации параметров станка, проверку V@ для моделирования процесса, ускорение V@ для оптимизации производительности станка в зависимости от обрабатываемой детали и руководство V@ для более последовательного профилактического обслуживания.П>
Фоллмер все еще находится на ранних стадиях этой инициативы, но менеджер по продажам в Северной Америке Шэннон Фокс сказал, что сообществу шлифовщиков все еще доступно множество несложных улучшений. Главным из них является автоматизация. В качестве примера компания Fox указала на роботизированную загрузку деталей и возможности замены круга своего инструмента VGRIND 360 и фрезерно-шлифовального станка. вне производства.
Симуляция — еще один рутинный запрос. Хотя система проверки V@ от Vollmer все еще находится в стадии разработки, Фокс отметил, что программное обеспечение NUMROTOplus, предлагаемое на шлифовальном оборудовании Vollmer и других марок, является зрелой и хорошо принятой альтернативой. «Моделирование становится все более важным, поскольку гриндеры становятся все более способными», — сказал он. «Четверть становится более узкой, геометрия инструмента становится все более сложной, и многие машины, в том числе и наша, позволяют использовать несколько колесных пакетов в одной работе, что вызывает проблемы с помехами. Без симуляции вы рискуете сломать очень дорогой станок».
Видеть — значит верить
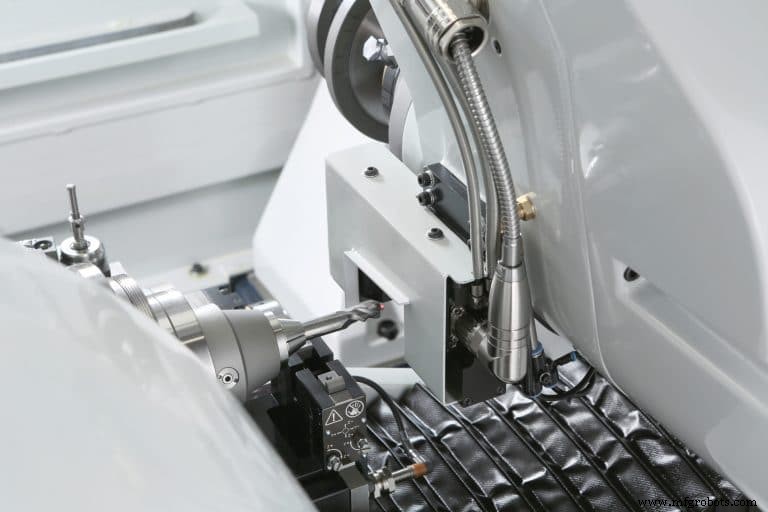
Моделирование важно и по другим причинам. Например, компания ANCA CNC Machines из Мельбурна, Австралия, использует его для прогнозирования дисбаланса инструмента в концевых фрезах с переменным шагом. «Это один из компромиссов с высокопроизводительными фрезами — поскольку расстояние между канавками неравномерное, они по своей природе несбалансированы», — сказал Лукас Хейл, менеджер по глобальному маркетингу. «Чтобы бороться с этим, мы разработали программное обеспечение для моделирования, которое вычисляет дисбаланс и корректирует программу ЧПУ, чтобы компенсировать его, удаляя дополнительный материал в стратегически важных местах. Инструмент выходит из шлифовального станка идеально сбалансированным, что обеспечивает более длительный срок службы инструмента и лучшее качество поверхности обрабатываемой детали».
Хейл согласился с призывом к автоматизации, включая роботизированную обработку деталей и колес, но предложил ряд дополнительных способов повышения производительности. Там, где обычное «залипание» колеса для снятия нагрузки когда-то выполнялось вручную, ANCA автоматизировала его, сократив трудозатраты и увеличив срок службы колеса. Говорят, что программное обеспечение и машины ANCA обеспечивают «значительную простоту использования», сокращая время настройки. А лазерные измерительные системы обеспечивают непрерывную проверку точности и геометрии режущего инструмента с последующим автоматическим смещением или правкой круга для компенсации износа.
И ANCA сделала еще один шаг в этом процессе. Благодаря сотрудничеству с такими компаниями, как Zoller Inc., ведущим поставщиком оборудования для предварительной настройки инструмента, ANCA разработала интерфейс, который поддерживает автоматическую проверку и обратную связь с шлифовальным станком с ЧПУ:робот помещает фрезу в устройство предварительной настройки, которое измеряет его и отправляет результаты. к программной системе, которая настраивает машину по мере необходимости. Это «замыкает цикл», объяснил Хейл, и вместе с интегрированными системами управления заготовками позволяет клиентам «загружать сотни инструментов, нажимать «Пуск» и возвращаться на следующий день к готовым режущим инструментам», — сказал он.
«Базовая конструкция машин также улучшилась за последние пять лет или около того, — продолжил Хейл. «Например, линейные двигатели стали гораздо более распространенными в нашей отрасли. Они не только способствуют повышению качества режущих инструментов и, следовательно, качества деталей, изготавливаемых с их помощью, но и линейные станки перемещаются намного быстрее, чем станки с шарико-винтовой передачей, что сокращает время цикла. А поскольку компоненты машины изнашиваются меньше, срок службы оборудования увеличивается. Вот почему линейные двигатели стали практически стандартным компонентом любого высокоточного высокопроизводительного шлифовального станка».
Первая часть, хорошая часть
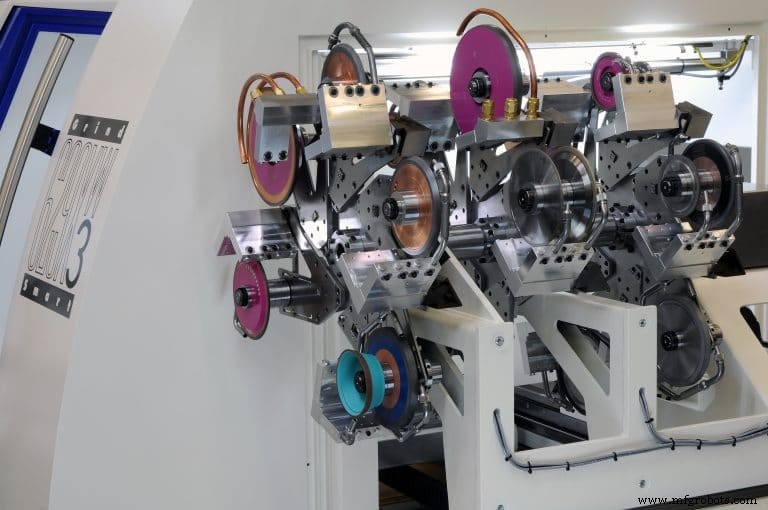
Точно так же, как JTEKT Toyoda решает проблему нехватки квалифицированных механиков с помощью более интуитивно понятного управляющего программного обеспечения, Rollomatic Inc., Манделейн, Иллинойс, работает над тем, чтобы упростить и ускорить настройку станков. Это связано с тем, что большинство производителей инструментов и фрез ничем не отличаются от любой мастерской по резке металла; они сталкиваются с меньшими размерами партий и более короткими сроками выполнения заказов, в результате чего время наладки составляет больший процент от любого производственного цикла. Одна часть решения? Лучшее программное обеспечение.
«На протяжении десятилетий в цехах прожигали по три, четыре, пять заготовок за один установ, постепенно наращивая станок до тех пор, пока не получали хорошую заготовку, — сказал Эрик Шварценбах, президент Rollomatic Inc. — Но с помощью интеллектуального программного обеспечения это вполне возможно. сократить количество бракованных деталей, при этом конечной целью является ноль. Это сокращает не только материальные затраты, но и время на настройку».
Программное обеспечение помогает оператору, создавая трехмерное представление станка, заготовки и шлифовального круга, сказал Шварценбах, устраняя необходимость пробного прогона. Оператор может ускорить анимацию, замедлить ее, отодвинуть или увеличить проблемные области, что поможет ему избежать возможных столкновений между колесным пакетом и заготовкой. А когда анимация завершена и машина фактически изготавливает детали, программное обеспечение устраняет «пустые ходы» и сокращает безопасное расстояние до минимума.
Интеллектуальное программное обеспечение — это здорово, но Шварценбах сразу заметил, что станок и связанные с ним системы одинаково важны. Чем точнее и стабильнее станок, тем легче достичь заданного размера с первой попытки. Кроме того, решающее значение имеют усовершенствованная технология правки кругов, автоматизированные процедуры калибровки, более быстрые средства управления, которые быстрее обрабатывают расчеты, и гибридные колесные связки, которые являются износостойкими, свободными от резки и дольше сохраняют острые углы. Эти факторы играют большую роль в более быстрой настройке и улучшенной способности сделать первую часть хорошей деталью с более коротким временем загрузки.
Как уже упоминалось, автоматическая замена кругов — это еще один прорыв в шлифовании. Шварценбах сказал, что высокоскоростные устройства смены кругов Rollomatic могут заменить пакет кругов за пять секунд, от оправки к оправке, и достичь времени от шлифовки до шлифовки 11 секунд. Однако преимущество выходит за рамки более короткого времени цикла. «Если у вас есть рюкзак с четырьмя колесами, вероятность столкновения выше, чем у рюкзака с одним или двумя колесами. Это усложняет настройку. Так что, если вы можете разделить большой комплект колес и выделить 11–12 секунд на замену колес, то в наши дни это предпочтительный способ».
Система управления автоматикой
- Насколько хорош GCP как выбор карьеры?
- От хорошего к отличному:посмотрите в зеркало
- Стратегии для более надежных компонентов передачи энергии
- Почему заказы на работу заслуживают большей любви со стороны всех нас
- Зачем и когда переходить от световых индикаторов к дисплею HMI
- Как получить больше от инвестиций в самосвалы с шарнирно-сочлененной рамой
- Преимущества использования 5- или 6-дюймового шлифовального круга или лепесткового диска
- EU Automation:лучшие технологические тенденции 2020 года
- 7 стратегий выдающихся менеджеров по безопасности
- Плоское шлифование:больше, чем просто вращение