Проектирование напечатанной на 3D-принтере турбины Tesla - Часть 2
Введение
Это вторая часть серии из двух частей, в которых подробно описывается дооснащение механически обработанной турбины Tesla деталями Markforged. В первой части мы представили Tesla Turbines, обсудили, какие детали хорошо подходят для 3D-печати, и заменили корпус турбины на деталь Markforged. Теперь мы займемся другим печатным компонентом нашей модернизации турбины:корпусом подшипника.
Корпус подшипника турбины Tesla
Корпус турбины окружает вал в сборе, но не касается его. Вместо этого промежуточная часть, называемая корпусом подшипника, крепится болтами к корпусу турбины и удерживает узел вала с двумя идеально концентрическими подшипниками. Размещая роторы на боковой стороне корпуса подшипника, разработчики оригинальной конструкции позаботились о том, чтобы машинист, вращающий оригинальную деталь, мог легко проверить концентричность отверстий подшипников. Это критически важно. При 24000 об / мин любое смещение роторов турбины могло привести к катастрофическому отказу. В алюминиевом корпусе (в том виде, в котором он был первоначально обработан) допуски для каждой из этих посадок подшипников составляли +0 / -. 0004 ”. Чрезвычайно жесткие допуски обеспечивают хорошую посадку пресс-посадки, не будучи настолько тугой, что препятствуют вращению подшипника. Хотя эта деталь изготавливается на станке Markforged, это гораздо более сложная задача, чем корпус турбины.
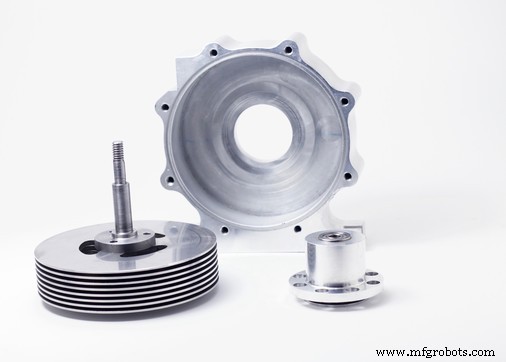
Изменения в конструкции аддитивного производства
Хотя эта часть определенно пригодна для печати, она представляет собой значительно более сложную задачу, чем корпус турбины по нескольким причинам. Во-первых, посадка подшипников должна быть точной и концентрической; однако допуски могут быть немного меньше из-за пониженной твердости поверхности оникса. Это замаскированное благо, поскольку достижение допуска +0 / - 001 ”намного более реалистично, чем то, что требуется для алюминия. Во-вторых, нам нужно было иметь возможность точно печатать как канавки для стопорных колец, так и выступающие фланцы. Оба требовали значительного вспомогательного материала, который можно было удалить из труднодоступных мест, не повредив детали. К счастью, наши отслаивающиеся опоры позволяют легко печатать канавки и фланцы стопорных колец. В-третьих, нам нужно было разместить большое количество волокон в деталях, особенно вокруг подшипников. Если деталь деформируется, любая точность, которую мы достигли с помощью посадки подшипников, будет аннулирована. Деталь достаточно велика, чтобы вместить шесть волоконных колец вокруг каждого подшипника; это достаточная поддержка.
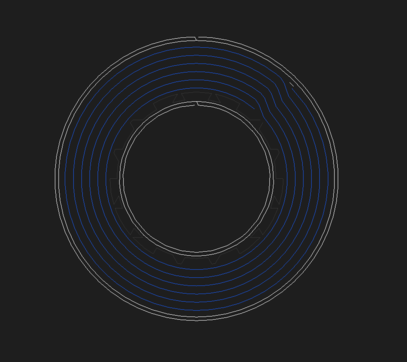
Печать корпуса
Обеспечение жестких допусков возможно на всех наших машинах. Чтобы доказать это, мы решили напечатать две версии корпуса подшипника:одну на Mark Two Enterprise и одну на Mark X с лазерной проверкой размеров.
Второе место
Чтобы напечатать жесткие допуски на Mark Two, мы должны использовать независимо измеренные модульные тесты. Мы подробно рассмотрели модульные тесты в предыдущем сообщении в блоге; они невероятно полезны, позволяя нам печатать с жесткими допусками без конструкции с замкнутым контуром. Для корпуса подшипника мы абстрагируем каждую из двух посадок подшипников на кольца и распечатываем несколько модульных тестов. После каждой распечатки единичного теста мы максимально точно измеряем внутренний диаметр (измерение внутренних трехмерных печатных кругов штангенциркулем может быть довольно трудным) и корректируем размеры нашей детали в САПР. После двух итераций с каждой посадкой подшипника мы включаем каждый новый размер в полную деталь и распечатываем его. Только после измерения и проверки всей детали мы пытаемся вставить оборудование. Если все работает по плану, подшипники плотно прилегают к корпусу, и мы сможем установить корпус подшипника на корпус турбины.
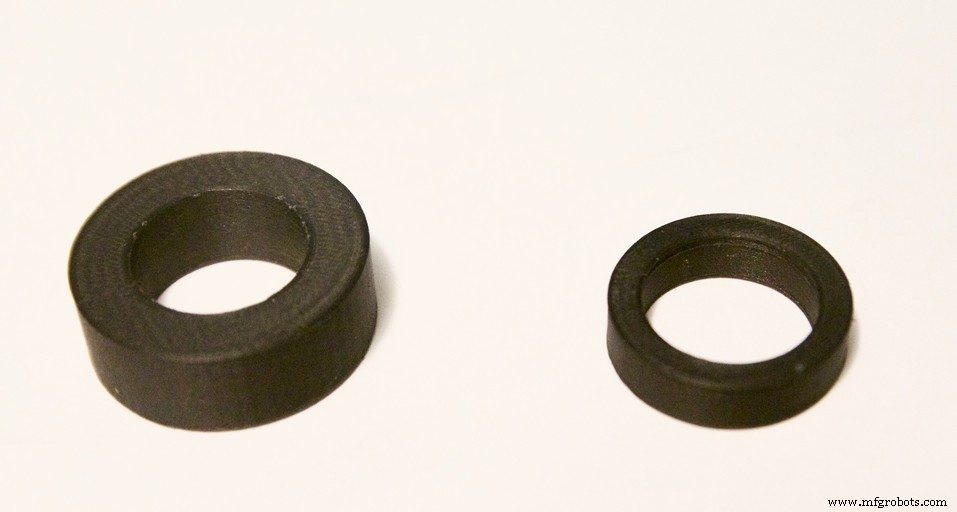
Mark X Housing
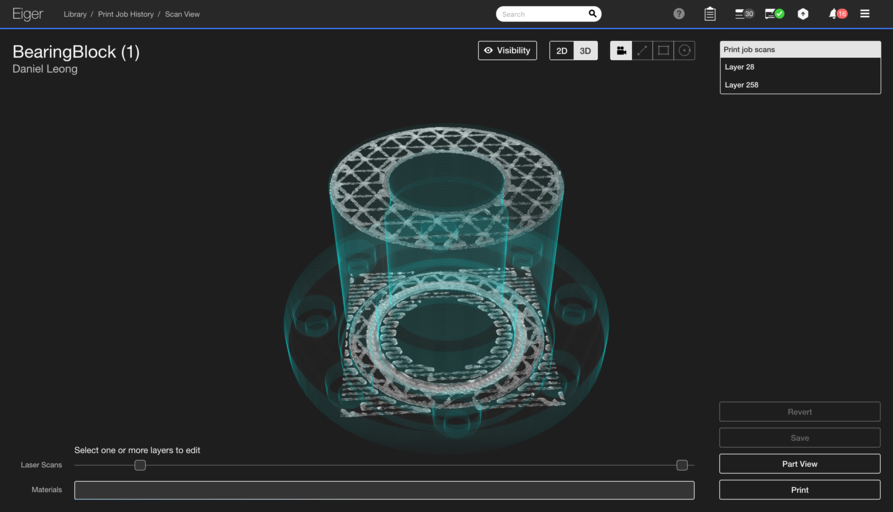
Поскольку обеспечение размеров Mark X по-прежнему подтверждено людьми, мы не можем просто распечатать идеальную деталь. Однако лазерное определение размеров значительно упрощает наш процесс. Вместо использования модульных тестов (которые хоть и хороши, но все же рискуют не проверить допуск, потому что модульный тест с размерами, выходящими за пределы допуска, все еще необходимо воспроизвести), мы печатаем всю деталь с помощью лазерного сканирования на слоях, которые содержат каждый из две критические посадки подшипников. Это позволяет нам проверять посадку каждого подшипника во время печати без использования штангенциркуля. Хотя нам удалось достичь обоих допусков с первой попытки (исключая необходимость повторной печати), отсутствие любого допуска привело бы к простому изменению размеров и повторной печати. Этот рабочий процесс не требует вмешательства пользователя и намного проще, чем использование модульных тестов.
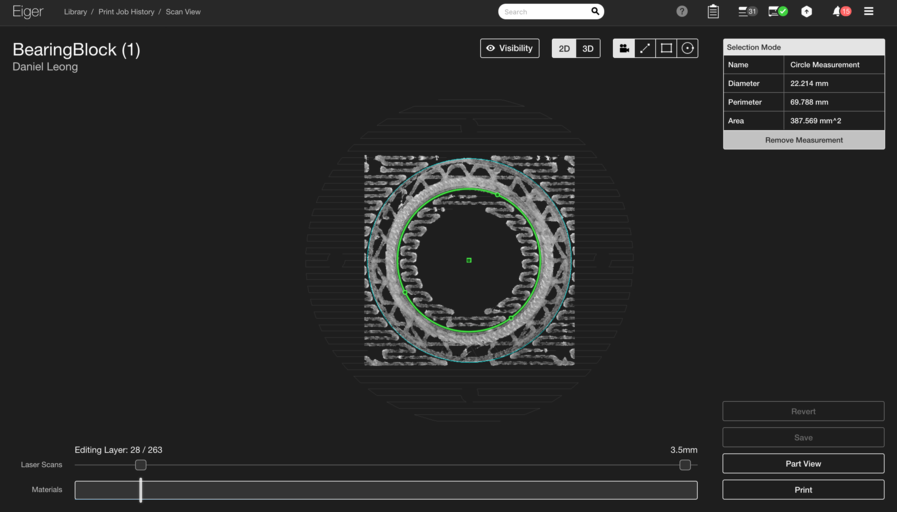
Заключение
Несмотря на свою сложность, корпус подшипника оказался отличным приложением для 3D-печати с жесткими допусками. Мы подтвердили, что можем напечатать функциональную часть с небольшими изменениями дизайна как на Mark Two, так и на Mark X. Более того, корпуса работают взаимозаменяемо; оба позволяют ротору турбины вращаться безупречно.
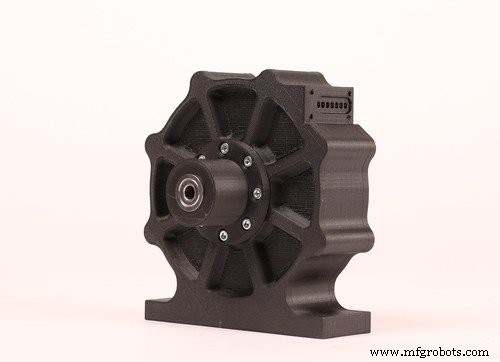
Хотите увидеть больше применений таких машин Markforged? Подпишитесь на нас в Facebook, Twitter, Instagram и Linkedin, чтобы получать больше обновлений!
3D печать
- 10 главных советов, которые следует учитывать при разработке детали FDM
- Приложения для 3D-печати металлом (часть 2)
- Проектирование напечатанной на 3D-принтере турбины Tesla - Часть 1
- Проверка в процессе:улучшение деталей, напечатанных на 3D-принтере
- Часть недели - напечатанный на 3D-принтере амортизатор
- 3D-печатная деталь Markforged:распределитель катушек
- Экстремальные дроны с 3D-печатью
- Точность размеров деталей, напечатанных на 3D-принтере
- Как получить более прочные 3D-печатные детали
- Метод проверки деталей, напечатанных на 3D-принтере (часть 3)