Прототип корпуса подушки безопасности подвергает испытанию напечатанные на 3D-принтере композитные материалы
Более века компания Joyson Safety Systems (Оберн-Хиллз, штат Мичиган, США) участвует в разработке, производстве и продаже компонентов безопасности для различных рынков, включая подушки безопасности, ремни безопасности, рулевое колесо и электронику безопасности для автомобилей. промышленность.
Недавно компания провела технико-экономическое обоснование, чтобы изучить возможности использования других существующих материалов и процессов для улучшения таких продуктов, как корпусный контейнер подушки безопасности водителя (DAB), что привело к подтверждению концепции, в которой использовались преимущества аддитивного производства композитов.
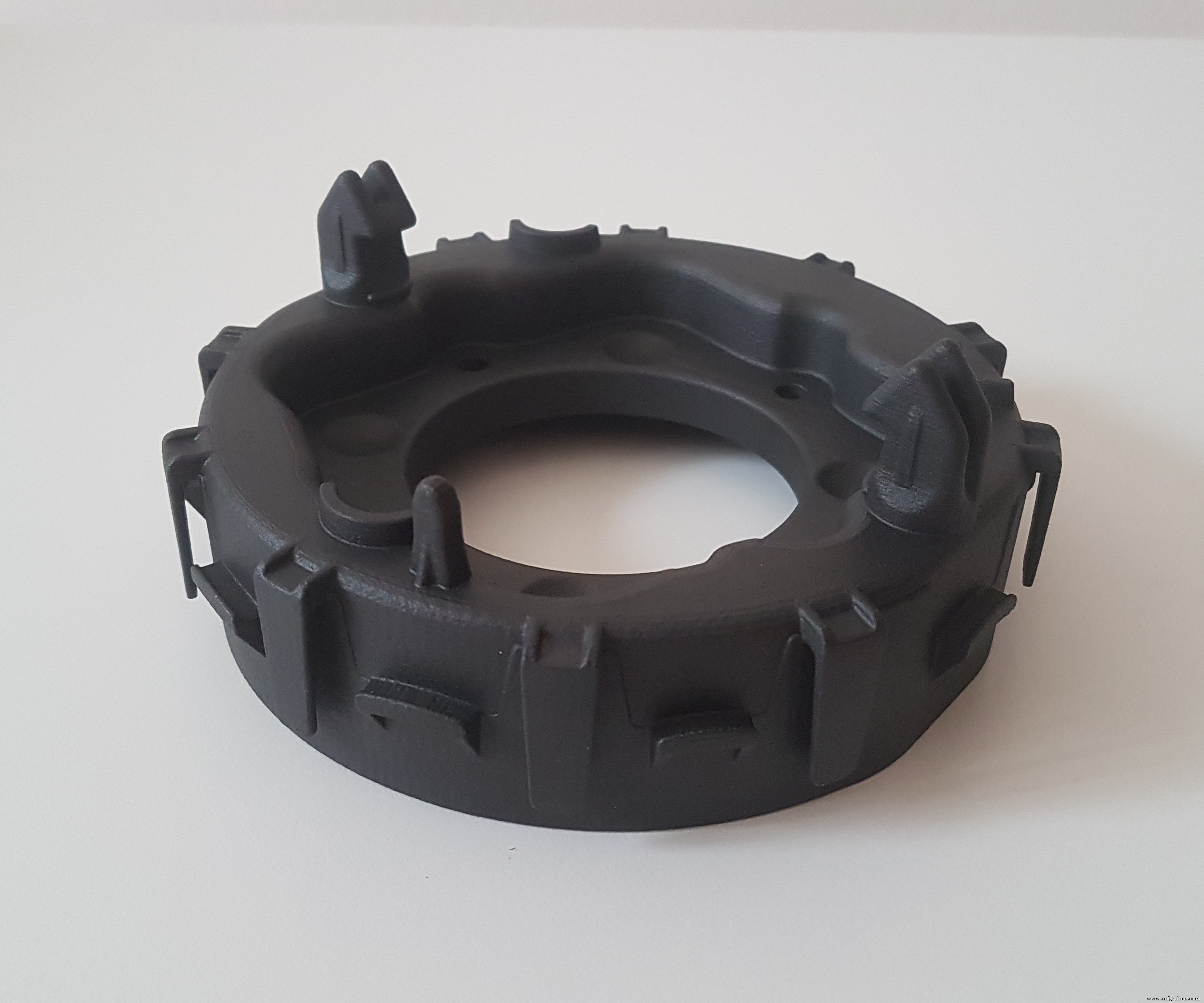
Полная система подушки безопасности состоит из инфлятора, подушки подушки безопасности, крышки и корпуса с точками крепления к рулевому колесу. Сама подушка подушки безопасности расположена в пространстве корпуса и крышки.
Рабочие характеристики корпуса DAB имеют решающее значение. Помимо удержания всей системы подушек безопасности на месте во время движения, эта часть также должна выдерживать силы, прикладываемые к системе подушек безопасности при срабатывании подушки безопасности. Для испытаний материал, из которого изготовлена деталь, должен обладать достаточной прочностью, ударопрочностью и термостойкостью в диапазоне температур от -35 ° C до + 85 ° C.
Оригинальный контейнер был изготовлен с помощью обычного процесса литья под давлением из полиамида (PA), армированного 40% стекловолокна. В рамках технико-экономического обоснования команда Joyson Safety Systems стремилась быстро создать функциональную деталь-прототип в течение нескольких дней, и они хотели найти материал, который демонстрирует механические, термические и эксплуатационные свойства, аналогичные исходным материалам.
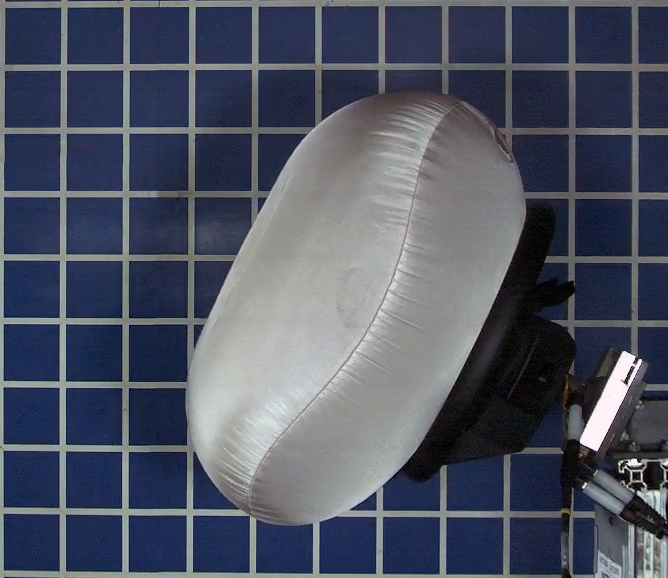
Команда Joyson по инновациям провела анализ рынка, чтобы найти подходящие материалы, и в итоге обратилась в CRP Technology (Модена, Италия) за линейкой высокоэффективных композитных материалов Windform TOP-LINE и собственной услугой 3D-печати.
В частности, команда выбрала углеродное волокно / PA материал Windform SP от CRP, который демонстрирует даже более высокие свойства, чем предыдущие материалы, которые они использовали для этой детали. Детали будут изготавливаться с использованием выбранного аддитивного процесса лазерного спекания (SLS).
Команда смогла быстро изготовить прототип детали и протестировать ее в составе готового модуля подушки безопасности, продемонстрировав высокую прочность и ударопрочность переработанной детали, а также термическую стабильность в диапазоне температур. По сравнению с исходным процессом литья под давлением, новую деталь можно было производить быстрее с использованием SLS и устранять необходимость в дорогостоящих инструментах.
«Эта возможность открыла множество возможностей и возможностей для дальнейшего сотрудничества с CRP Technology», - говорит Самер Зиадех, инженер-разработчик группы основных инженерных материалов Joyson Safety Systems.
волокно
- Ода прототипу
- Вопрос об обслуживании контракта - Часть I
- Разработка легких композитных материалов в медицинской промышленности
- Руководство по пониманию процесса производства композитов
- Какое будущее у композитов в индустрии спортивных товаров?
- Глубокое погружение в применение аэрокосмических композитов
- 3 причины, почему морская промышленность использует преимущества композитов
- 5 советов по поиску лучшего производителя деталей из углеродного волокна
- Nèos International открывает новый штаб-квартиру по производству композитных материалов в Великобритании
- Ценность литья по выплавляемым моделям (часть 2)