Обзор приложений:3D-печатные скобки
Кронштейны, хотя и довольно простые детали, часто используются для 3D-печати. Во-первых, 3D-печать позволяет оптимизировать кронштейн, помогая улучшить производительность детали, а также структуру, в которой используется кронштейн.
В сегодняшнем выпуске «Обзор приложений» мы исследуем ключевые преимущества использования 3D-печати для кронштейнов, а также рассмотрим некоторые интересные приложения в аэрокосмической и автомобильной промышленности.
Взгляните на другие приложения, рассматриваемые в этой серии:
3D-печать теплообменников
3D-печать подшипников
3D-печать для производства велосипедов
3D-печать для цифровой стоматологии и производства прозрачных элайнеров
3D-печать медицинских имплантатов
3D-печатные ракеты и будущее производства космических аппаратов
3D-печать для производства обуви
3D-печать электронных компонентов
3D-печать в железнодорожной отрасли
Очки с 3D-печатью
3D-печать для производства готовой продукции
3D-печать деталей турбин
Как 3D-печать делает гидравлические компоненты более производительными
Как 3D-печать поддерживает инновации в атомной энергетике
Что такое скобка?
Кронштейн - это застежка, предназначенная для удержания вместе двух перпендикулярных частей в сборке и усиления угла.
Кронштейны скрепляют конструкции вокруг нас (например, здания, самолеты и автомобили), в значительной степени определяя прочность, устойчивость и целостность этих структур.
Зачем использовать 3D-печать для скобок?
Кронштейны - довольно простые компоненты в изготовлении традиционными методами. Однако с появлением 3D-печати инженеры теперь могут исследовать новые способы оптимизации конструкции кронштейнов.
Это в значительной степени возможно благодаря способности 3D-печати создавать сложные геометрические формы, которые были бы либо невозможны, либо недешевы и трудоемки при использовании традиционных средств производства.
Основными преимуществами кронштейнов, напечатанных на 3D-принтере, являются:
Более быстрое изготовление
Производство сложных металлических кронштейнов обычно требует настройки нескольких станков и может занять много часов. С другой стороны, 3D-печать может предложить более быстрое решение. Одна из причин заключается в том, что внутри 3D-принтера можно разместить несколько деталей, что позволяет одновременно производить несколько кронштейнов на одной машине.
Для кронштейна, который ранее был отлит под давлением, экономия времени еще больше, поскольку 3D-печать сокращает время изготовления пресс-формы.
Удаленная сборка
Некоторые кронштейны состоят из нескольких частей, что может увеличить время, необходимое для сборки кронштейна. 3D-печать позволяет спроектировать и изготовить кронштейн как единое целое, что требует меньше труда и времени для сборки кронштейна. 3D-печать кронштейна как единой детали также, вероятно, увеличит общую прочность детали.
В одном из примеров Philips использовала 3D-печать для изготовления обновленного кронштейна, который удерживает лампы на месте на производственной линии. Деталь часто ломалась, одна или две выходили из строя каждую неделю, в основном из-за многократного воздействия высоких температур, в сочетании со структурой с линиями сварных швов от четырехсекционного кронштейна.
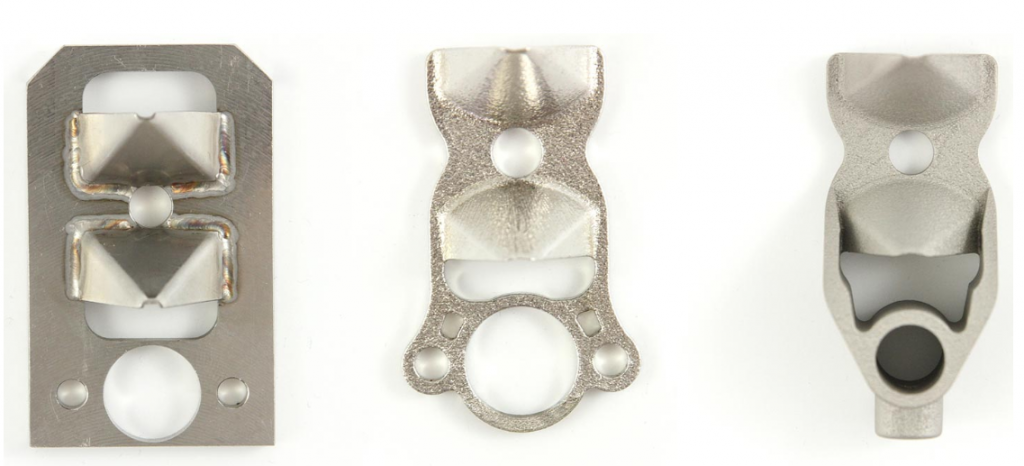
Компания Philips смогла преобразовать металлическую деталь в кронштейн с единой структурой, сократив трудоемкую сборку детали и полностью удалив точки давления в линии сварки. За первые три месяца использования обновленная скоба ни разу не сломалась.
Снижение отходов материала
В процессе 3D-печати кронштейна, поскольку один компонент часто использует меньше материала, таким образом создается более легкий кронштейн.
Эта экономия веса приводит к сокращению расхода материала и, в некоторых случаях, может улучшить производительность системы, в которой используется кронштейн.
В качестве примера возьмем двигатели GEnx от GE. В двигателях использовались кронштейны, изготовленные традиционными методами, такими как фрезерование. Это означает, что детали были вырезаны из большого куска металла, и более половины его оказалось отходами.
Команда, работающая над кронштейнами, поняла, что с помощью 3D-печати детали они смогут сократить до 90 процентов отходов.
Команда также внесла небольшие улучшения в конструкцию, благодаря которым вес кронштейна уменьшился на 10%. По словам команды, «когда дело доходит до полета, важна каждая унция». Это означает, что уменьшение веса компонента может повлиять на уровень расхода топлива самолета, снизить его и, следовательно, сделать самолет более эффективным.
В другом примере инженеры Ford недавно напечатали на 3D-принтере пластиковый кронштейн электрического стояночного тормоза для Ford Mustang Shelby GT500, который на 60 процентов легче, чем ранее штампованная стальная версия.
Возможность замены металла на пластик или композит
В некоторых случаях с помощью 3D-печати можно изготавливать кронштейны из пластика, а не из металла. Пластиковые кронштейны могут лучше подходить для таких приложений, как потребительские товары с ограниченным сроком службы или продукты с чувствительными электронными компонентами, где металлические кронштейны не работают.
Один из примеров - производитель устройств связи, Boyce Технологии. Компания использовала 3D-печать для создания пластиковых деталей для тотемов NYC Transit. Каждая из этих систем имеет зеленый акриловый колпачок наверху, на котором находится светодиодная лента для освещения, а также чувствительный антенный прибор.
Чтобы предотвратить нарушение сигнала антенны, их не должно быть. металлический материал перед ним. Это означает, что компании пришлось изготавливать кронштейны для светодиодной ленты и корпус для антенны из пластика. У команды Бойса было очень мало времени на проектирование, проектирование и производство, что сделало 3D-печать подходящим решением.
Используя систему BigRep Studio, Бойс смог создать прототип изогнутых монтажных кронштейнов для светодиодных ламп для освещения крышки, а затем сразу приступить к производству этих деталей на той же платформе.
3D-печать этих кронштейнов позволила изготавливать их быстрее и с меньшими затратами, чем литье под давлением или механическая обработка, а также соответствовать требованиям отсутствия металла над антенной.
Еще примеры кронштейнов, напечатанных на 3D-принтере
Аэрокосмическая промышленность
Титановые кронштейны для Boeing 787, напечатанные на 3D-принтере
Аэрокосмические кронштейны из титановых сплавов, напечатанные на 3D-принтере, становятся все более распространенными в конструкции самолетов. Одним из примеров является скоба для защелки люка доступа для Boeing 787, установленная Spirit AeroSystems.
Фурнитура дверной защелки, которая ранее подвергалась механической обработке, теперь напечатана на 3D-принтере компанией Norsk Titanium с использованием собственной технологии Rapid Plasma Deposition (RPD). Название описывает процесс:плазменная дуга позволяет контролировать осаждение титана с высокой скоростью наращивания. Сообщается, что эта технология в 50-100 раз быстрее, чем системы на основе порошка, и использует на 25-50 процентов меньше титана, чем процессы ковки.
Ключевой причиной перехода на 3D-печать титаном является возможность сокращения производства Стоимость. Титан стоит дорого, и при обработке детали из блока титана большая часть этого дорогостоящего материала тратится впустую. Вторая проблема - это большое количество машинного времени и затрат на режущий инструмент, которые уходят на механическую обработку металла, что увеличивает стоимость производства.
Благодаря 3D-печати кронштейна Spirit может существенно снизить эти расходы, одновременно сокращая время вывода на рынок новых деталей как минимум на 60%.
Компания Liebherr-Aerospace напечатала 3D-кронштейны для Airbus
Другой пример из аэрокосмической промышленности:компания Liebherr-Aerospace начала 3D-печать кронштейнов передней стойки шасси для Airbus A350 XWB.
Эти кронштейны будут первыми в истории квалифицированными. Титановые детали, напечатанные на 3D-принтере, внедрены в систему Airbus.
В отличие от Spirit AeroSystems, компания Liebherr смогла модернизировать деталь, чтобы снизить вес на 29 процентов. Использование 3D-печати также помогло увеличить жесткость компонента на 100%.
В 2019 году компания Liebherr-Aerospace достигла ключевой вехи:Федеральное управление гражданской авиации Германии дало компании зеленый свет на производство компонентов с использованием AM. С тех пор компания Liebherr начала 3D-печать титановых серийных деталей, включая кронштейны.
Автомобильная промышленность
Кронштейн для крыши, оптимизированный и напечатанный на 3D-принтере BMW
В 2018 году BMW выпустила свой культовый автомобиль i8 Roadster с отмеченным наградами металлическим кронштейном для крыши, напечатанным на 3D-принтере.
Кронштейн для крыши - небольшой компонент, который помогает складывать и раскладывать верхнюю часть автомобиля, потребовалась новая конструкция, чтобы максимизировать производительность механизма складывания крыши. Для достижения этой цели инженеры BMW объединили 3D-печать с программным обеспечением для оптимизации топологии.
Используя программное обеспечение, инженеры смогли ввести такие параметры, как вес, размер компонента и нагрузка, которую он будет принимать. Затем программа создала проект, который оптимизировал распределение материала детали.
Дизайн, созданный командой инженеров, невозможно было отлить. Команда обнаружила, что единственный способ реализовать этот дизайн - это 3D-печать металлом.
Благодаря технологии селективной лазерной плавки (SLM) инженеры создали металлический кронштейн для крыши, который в 10 раз жестче и на 44% легче, чем традиционный вариант.
Облегченные скобы Bugatti
На автомобилях Bugatti также есть несколько кронштейнов, напечатанных на 3D-принтере. Один из них - титановый кронштейн спойлера, изготовленный в сотрудничестве с Fraunhofer IAPT. Считается, что этот спойлер улучшает аэродинамический дизайн автомобилей Bugatti.
Еще одним партнером в проекте кронштейна спойлера была компания Siemens, которая помогла оптимизировать кронштейн для производства. В итоге последняя часть продемонстрировала предел прочности на разрыв 1250 МПа, плотность материала более 99,7% и снижение веса на 53%.
3D-печать также использовалась для изобретения небольшого Кронштейн мотора со встроенным водяным охлаждением для суперкара Bugatti Chiron. Деталь служит активным теплозащитным экраном, значительно снижая теплоотдачу двигателя. Инновационный компонент, напечатанный на AlSi10Mg на 3D-принтере SLM280 Twin от SLM Solutions, был установлен во всех серийных автомобилях с момента выпуска первого Bugatti Chiron.
Кронштейны, напечатанные на 3D-принтере:небольшие компоненты с огромными возможностями
Кронштейны - это небольшие и довольно обыденные детали, которые было трудно оптимизировать в прошлом, когда инженеры были ограничены традиционными методами производства. Сегодня инженеры могут разработать оптимизированные кронштейны и воплотить эти конструкции в жизнь с помощью 3D-печати.
Благодаря этой технологии кронштейны можно сделать легче, но при этом более жесткими и прочными. Приведенные выше примеры также демонстрируют, что с помощью 3D-печати можно увеличить срок службы компонента и общую производительность.
Очевидно, что до массовой 3D-печати скобок еще далеко. Тем не менее, специализированные приложения, такие как кронштейны для самолетов и кронштейны, производимые небольшими объемами, останутся хорошей нишей для технологий в будущем.
3D печать
- Сварка и склейка пластиковых деталей, напечатанных на 3D-принтере
- Изучение 3D-печати Polyjet
- Что такое биопечать?
- Обзор приложений:3D-печать для медицинских имплантатов
- Обзор приложений:3D-печать для цифровой стоматологии и производство прозрачных выравнивателей
- Обзор приложений:3D-печать для производства велосипедов
- Обзор приложений:3D-печать подшипников
- Обзор приложений:3D-печать для теплообменников
- COVID-19 привлек внимание к трехмерной печати
- Применение 3D-печати в автомобильной промышленности