Обзор приложений:3D-печать для медицинских имплантатов
[Изображение предоставлено Министерством здравоохранения Канады]
Создание более подходящих, долговечных и эффективных костных имплантатов - постоянная задача как ортопедов, так и хирургов. 3D-печать вносит огромный вклад в развитие этой области.
Эта технология позволяет производителям имплантатов создавать имплантаты с расширенными функциональными возможностями и более персонализированными для конкретных потребностей пациента. Кроме того, 3D-печать открывает двери для персонализированных имплантатов, которые могут быть созданы прямо на месте.
На этой неделе мы продолжим серию статей о приложениях для 3D-печати, рассмотрев использование 3D-печати для медицинских имплантатов, а также преимущества и текущие применения этой технологии.
Взгляните на другие приложения, рассматриваемые в этой серии:
3D-печать теплообменников
3D-печать подшипников
3D-печать для производства велосипедов
3D-печать для цифровой стоматологии и производства прозрачных элайнеров
3D-печатные ракеты и будущее производства космических аппаратов
3D-печать для производства обуви
3D-печать электронных компонентов
3D-печать в железнодорожной отрасли
Очки с 3D-печатью
3D-печать для производства готовой продукции
3D-печать для скоб
3D-печать деталей турбин
Как 3D-печать делает гидравлические компоненты более производительными
Как 3D-печать поддерживает инновации в атомной энергетике
Рынок медицинской 3D-печати в 2019 году
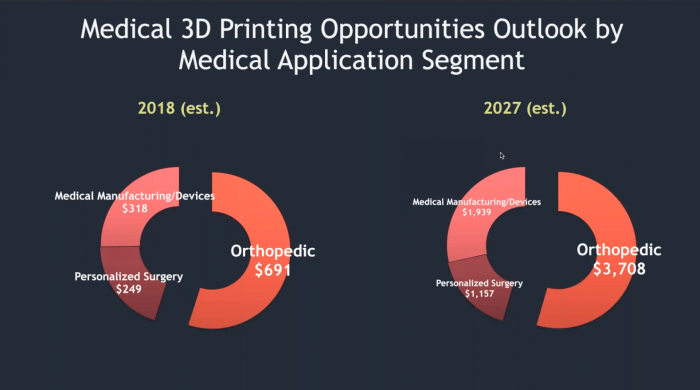
Ортопедические имплантаты - медицинские устройства, используемые хирургическим путем для замены отсутствующего сустава или кости - это лишь одна из возможностей, которые 3D-печать предлагает медицинской промышленности.
Рынок ортопедической 3D-печати оценивался в 691 миллион долларов в 2018 году и, по прогнозам SmarTech Analysis, к 2027 году вырастет до рынка в 3,7 миллиарда долларов.
Хотя производство имплантатов достаточно новое приложение для 3D-печати - впервые оно было использовано примерно в 2007 году - за последнее десятилетие оно быстро росло.
В 2010 году один из первых приверженцев технологии 3D-печати Arcam Electron Beam Melting (EBM) получил первые одобрения FDA для имплантатов, напечатанных на 3D-принтере. Семь лет спустя более 300 3D-принтеров по всему миру производили ортопедические изделия.
Сегодня эта технология используется для создания протезов тазобедренных и коленных суставов, имплантатов для реконструкции черепа и спинных имплантатов. По оценкам, на 2019 год с помощью 3D-печати будет произведено более 600000 имплантатов. К 2027 году это число должно превысить 4 миллиона.
Учитывая такие огромные возможности роста, неудивительно, что все основные производители медицинского оборудования все чаще используют технологию 3D-печати.
Stryker, одна из крупнейших медицинских технологических компаний в мире, недавно выпустила собственные имплантаты, напечатанные на 3D-принтере, в том числе изогнутый задний поясничный кейдж Tritanium TL для задней части позвоночника. Этот полый спинной имплантат получил одобрение FDA в марте 2018 года.
Помимо Stryker, другие известные производители ортопедических устройств, такие как DePuy Synthes, дочерняя компания Johnson &Johnson, и Medtronic вкладывают значительные средства в 3D-печать. Последняя запустила платформу для 3D-печати TiONIC Technology в мае 2018 года с целью создания более сложных конструкций и интегрированных поверхностных технологий для хирургических имплантатов позвоночника.
Помимо признанных производителей медицинского оборудования, за последнее десятилетие появились медицинские стартапы, разрабатывающие собственные подходы к 3D-печатным ортопедическим имплантатам.
Среди них такие компании, как Osseus Fusion Systems, Nexxt Spine, 4WEB Medical и SI-BONE. Некоторые продукты этих компаний уже получили одобрение FDA и успешно используются для лечения пациентов.
Очевидно, что за последнее десятилетие для имплантатов, напечатанных на 3D-принтере, наблюдалась восходящая траектория. Но что именно делает эту технологию такой полезной для медицинских имплантатов?
Преимущества имплантатов, напечатанных на 3D-принтере
Гибкость дизайна
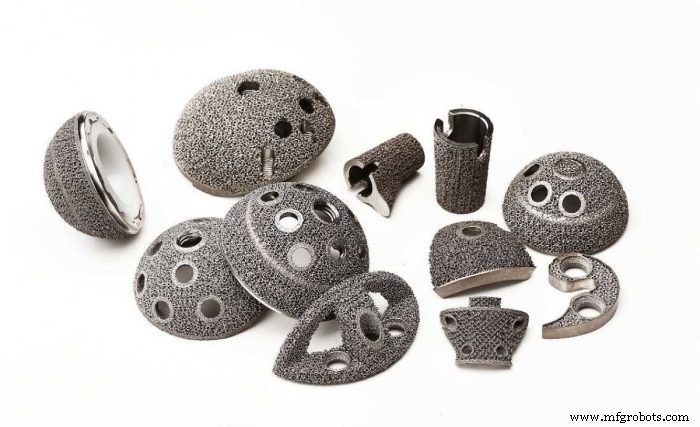
С помощью 3D-печати можно создавать сложные конструкции, которые иначе было бы сложно реализовать с помощью традиционных технологий. Производители имплантатов могут использовать это преимущество для производства имплантатов со сложной конструкцией, таких как трабекулярные структуры.
Трабекулярная кость - это один из двух типов костных тканей человеческого тела. Он имеет губчатую пористую структуру, которую трудно воспроизвести в имплантате. Традиционно производители имплантатов используют специальное покрытие для создания трабекулярной структуры на имплантате. Однако это несет в себе риск расслоения и выхода имплантата из строя.
С другой стороны, с помощью 3D-печати имплантаты с трабекулярной структурой могут изготавливаться напрямую, минуя процесс нанесения покрытия. Что еще более важно, трабекулярная пористая структура, интегрированная в имплантат, напечатанный на 3D-принтере, создает более прочный имплантат с меньшим риском расслоения.
Такую гибкость конструкции обеспечивают технологии 3D-печати металлом, такие как Selective Laser Melting или Electron. Луч плавления. Эти технологии применяют мощный источник энергии, такой как лазер (SLM) или электронный луч (EBM), на тонкий слой биосовместимого порошка, такого как титан.
Повторяя этот процесс на сотнях слоев, можно создать сложный имплант, который будет адаптироваться к структуре кости человека намного эффективнее, чем имплантаты, изготовленные традиционным способом.
Еще одним важным преимуществом пористых имплантатов, напечатанных на 3D-принтере, является улучшенная остеоинтеграция.
Остеоинтеграция - это процесс, который позволяет имплантату стать постоянной частью тела. Пористая трабекулярная структура позволяет кости расти внутри пор, дополнительно укрепляя связь между имплантатом и существующей костью.
Защита от пониженного напряжения
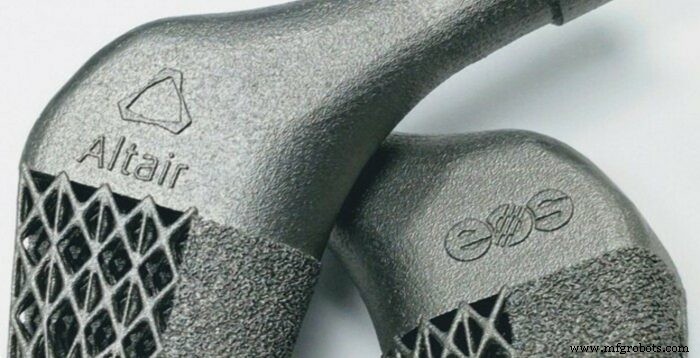
Кроме того, производители медицинского оборудования могут создавать имплантаты, имитирующие жесткость и плотность костей пациента. Помимо улучшения остеоинтеграции, имплантаты, напечатанные на 3D-принтере, могут снизить защиту от стресса и еще больше улучшить физические функции.
Экранирование напряжений - это явление, с помощью которого металлические имплантаты снимают типичные напряжения с кости пациента. В результате уменьшается плотность кости, что приводит к ее ослаблению. Экранирование напряжений может привести к переломам и вывихам. По этой причине создание имплантата как можно ближе к костной ткани пациента является ключом к снижению защиты от напряжения и устранению этих нежелательных эффектов.
В недавнем примере ИТ-компания Altair объединила программное обеспечение для 3D-печати и оптимизации топологии для создания улучшенного имплантата бедренной ножки.
Путем ввода таких параметров, как размер, вес и ожидаемая нагрузка, которую имплант будет нести, было использовано программное обеспечение для оптимизации топологии, чтобы создать новую конструкцию имплантата бедра. Оптимизированная конструкция распределяет напряжение и деформацию более эффективно, чем обычный имплант.
Кроме того, программа оптимизации топологии помогла определить, где материал можно заменить решетчатыми структурами, чтобы сделать имплантат легче.
При испытаниях оптимизированный имплант обеспечил снижение защиты от напряжения на 50,7%. В то же время его предел выносливости увеличился примерно до 10 миллионов циклов. Это означает, что имплантат бедра может выдержать бег трусцой из Лос-Анджелеса в Нью-Йорк и обратно - дважды.
3D-печать имплантатов для конкретных пациентов
В более сложных случаях стандартные имплантаты часто не могут обеспечить необходимую гибкость. В таких случаях может помочь 3D-печать, предлагая возможность настраивать и персонализировать медицинские устройства, включая имплантаты.
Для изготовления имплантата для конкретного пациента производители используют данные, полученные в результате сканирования пациента, такого как компьютерная томография (КТ) или магнитно-резонансная томография (МРТ). Затем данные пациента импортируются в САПР, подготавливаются к производству, 3D-печать и обработка.
Использование индивидуализированного имплантата, напечатанного на 3D-принтере, позволяет сократить время операции и улучшить посадку имплантата.
В настоящее время с помощью 3D-печати можно создавать имплантаты черепа и челюсти на заказ, где эстетические требования так же важны, как и функциональность.
Например, 10-летний китайский мальчик получил имплант челюсти, напечатанный на 3D-принтере, в 2018 году. У него была опухоль в челюсти, которую нельзя было удалить, не вызвав значительного лицевого дефекта.
Хирургическая бригада пришла к выводу, что обычная реконструкция лица слишком опасна для такого молодого пациента. В поисках лучшего решения они обратились к 3D-печати, используя цифровые модели челюсти мальчика для создания идеально адаптированного индивидуального титанового имплантата.
По словам хирургов, имплант челюсти было легко установить, так как он было основано на анатомии пациента. Через три месяца после процедуры имплантация оказалась успешной:челюсть выровнялась, и выросло большое количество тканей.
3 примера имплантатов, напечатанных на 3D-принтере
Имплант бедра, напечатанный на 3D-принтере, позволяет заниматься экстремальным альпинизмом
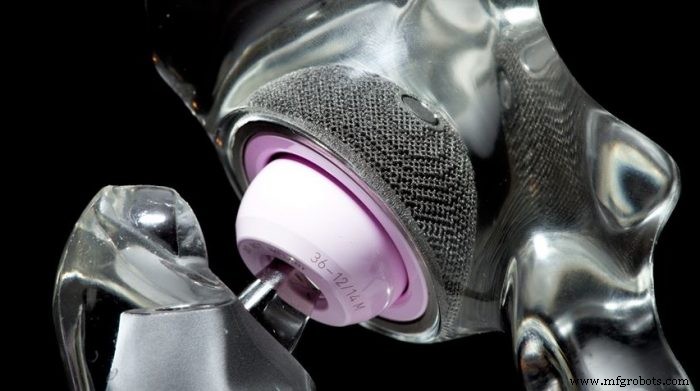
Романо Бенет и его жена Нивес Мерой уже много лет покоряют самые опасные горы мира. В 2017 году альпинистская команда стала первой парой, покорившей все 14 высочайших вершин мира. Однако достичь этого, вероятно, было бы невозможно без помощи 3D-печати.
Бенет страдал от двустороннего аваскулярного некроза, который, по сути, приводит к разрушению кости.
Когда впервые поставили диагноз, Бенет и его жена были на три вершины, не успев пройти кругосветное путешествие по всем 14 горам. Чтобы продолжить путешествие, альпинисту понадобился стабильный имплант, который позволил бы ему быстро восстановиться.
По этой причине хирург Бенета решил использовать имплант, напечатанный на 3D-принтере.
Имплант, известный под торговой маркой чашки Delta Trabecular Titanium (TT), был произведен итальянской компанией, производящей медицинские устройства, Lima Corporate с использованием 3D-принтера Arcam EBM.
Объединив технологию Lima Trabecular Titanium и 3D-печать, стало возможным создавать имплантаты, имитирующие пористую структуру натуральной кости.
Благодаря этой трабекулярной структуре имплантат, напечатанный на 3D-принтере, может выдерживать механические нагрузки во время тяжелых нагрузок. Хирург Бенета, который несколько раз имплантировал чашки TT другим пациентам, полагал, что имплантаты, напечатанные на 3D-принтере, не только обеспечивают большую стабильность и прочность, но и могут прослужить дольше, чем обычные имплантаты.
Когда Бенет получил свой первый имплант, не напечатанный на 3D-принтере, он много месяцев простаивал перед тем, как снова начать лазать. Благодаря имплантату, напечатанному на 3D-принтере, альпинист смог возобновить свою деятельность через два с половиной месяца.
В конечном итоге имплантат, напечатанный на 3D-принтере, сделал свое дело:он позволил Benet быстро восстановиться и успешно завершить его стремление достичь трех последних высотных вершин.
Osseus Fusion Systems:на пути к персонализированным металлическим имплантатам

Osseus Fusion Systems, основанная в 2012 году, является американской компанией, специализирующейся на разработке передовых медицинских продуктов для лечения травм позвоночника.
Чтобы улучшить качество и функциональность своих продуктов, Osseus разработала запатентованную технологию 3D-печати под названием PL3XUS.
Эта технология основана на 3D-печати методом порошкового наплавления, а именно на технологии селективного лазерного плавления (SLM), и позволяет создавать титановые имплантаты с пористостью 80%, оптимизированные для сращивания костей и биологической фиксации (процесса, при котором живая кость прочно прикрепляется к поверхности имплантата).
В августе 2018 года компания Osseus получила разрешение FDA 510 (k) для Aries, своего семейства устройств для межтелового спондилодеза аддитивного производства. Имплантаты семейства Aries призваны помочь хирургам облегчить боль в спине и сократить время восстановления позвоночника.
Ранее в этом году продукт Osseus Aries впервые был применен на практике Джозефом Спайном. центр хирургии позвоночника и сколиоза. Технология PL3XUS позволила спроектировать имплантат с архитектурой, аналогичной архитектуре кости пациента, что облегчило рост кости.
В ближайшие пару лет Osseus планирует выпустить персонализированные устройства на основе компьютерных томографов, рентгеновских снимков и МРТ пациентов.
Следующим шагом компания надеется на то, что дать возможность больницам обеспечить превосходный уход за пациентами и, в конечном итоге, еще больше улучшить результаты хирургических операций для пациентов.
Имплантаты для 3D-печати из высокоэффективных термопластов
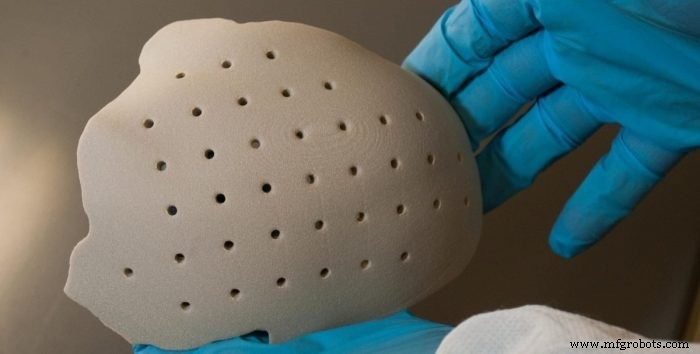
Помимо титана и других биосовместимых металлов, 3D-печать может сочетаться с полимерами, такими как PEEK и PEKK, для изготовления имплантатов. Эти термопласты известны своей высокой прочностью и биосовместимостью, а также обладают рядом преимуществ по сравнению с металлическими имплантатами, такими как более низкая стоимость и прозрачность.
В 2013 году Oxford Performance Materials (OPM) стала первой компанией, получившей разрешение FDA на изготовление черепного имплантата PEKK, напечатанного на 3D-принтере. К 2017 году OPM поставила более 1400 черепных имплантатов и получила разрешения FDA на два других устройства:челюстно-лицевые и спинномозговые имплантаты.
Компания использует технологию селективного лазерного спекания, которая лежит в основе собственной платформы OsteoFab® компании OPM для разработки и производства имплантатов. В одном примере эта платформа позволила разработать, изготовить, протестировать и отправить черепной имплант для конкретного пациента из OPM всего за 3 рабочих дня. Менее чем за неделю хирурги успешно выполнили операцию без каких-либо модификаций резки или сверления для изменения формы имплантата.
3D-печать медицинских имплантатов:эффектно
Биосовместимость, несущая способность и долговечность - основные требования к ортопедическим имплантатам. Трехмерная печать полностью отвечает этим требованиям, одновременно улучшая функциональность и подгонку имплантатов.
Это в первую очередь связано со способностью технологии создавать сложные формы, такие как пористые структуры, которые помогают телу пациента адаптироваться к имплантат быстрее и с меньшим количеством осложнений.
В будущем 3D-печать имплантатов будет развиваться. Одна особенно захватывающая область текущих исследований - это сочетание имплантатов и датчиков, напечатанных на 3D-принтере. Разрабатывая имплантаты с сенсорным питанием, медицинские работники могут потенциально значительно улучшить результаты лечения пациентов.
Встроенные датчики могут собирать такие данные, как температура вокруг имплантата, движения и напряжения, которые испытывает имплантат. Это позволит хирургам своевременно реагировать на любые потенциальные проблемы и адаптировать лечение к потребностям отдельных пациентов.
Компания Renishaw, британский производитель 3D-принтеров по металлу, и Западный университет уже открыли Центр аддитивного дизайна в хирургических решениях (ADEISS) на территории университета. Центр объединяет ученых и клиницистов для разработки новых медицинских устройств, напечатанных на 3D-принтере, подобных описанным выше.
Очевидно, что технология 3D-печати прочно закрепилась в сегменте ортопедии.
Тем не менее, технология должна развиться, чтобы по-настоящему раскрыть свой потенциал для создания имплантатов, изготавливаемых по индивидуальному заказу, на месте оказания помощи.
По общему признанию, только небольшой процент имплантатов в настоящее время изготавливается на заказ с помощью 3D-печати. Несмотря на то, что технология обладает огромным потенциалом, вопросы стандартизации и регулирования еще не решены.
Тем не менее, создание индивидуальных медицинских имплантатов - это то место, где технология может оказать наибольшее влияние и позволить большему количеству людей воспользоваться персонализированным медицинским обслуживанием. Мы полагаем, что в ближайшие годы это направление получит значительный рост.
В следующей статье мы рассмотрим, как 3D-печать может улучшить производство ракет. Следите за обновлениями!
3D печать
- Микротанталовые порошки для медицинского применения
- Обзор приложений:3D-печать для цифровой стоматологии и производство прозрачных выравнивателей
- Обзор приложений:3D-печать для производства велосипедов
- Обзор приложений:3D-печать подшипников
- Обзор приложений:3D-печать для теплообменников
- Обзор приложений:3D-печать в железнодорожной отрасли
- Обзор приложений:5 электронных компонентов, которым может помочь трехмерная печать
- Обзор приложений:3D-печать для обуви
- Обзор приложений:3D-печатные ракеты и будущее производства космических аппаратов
- 10 самых прочных материалов для 3D-печати