Новый подход к токарной обработке с ЧПУ
High Dynamic Turning в сочетании с инструментальной системой FreeTurn от Ceratizit использует ось B / фрезерный шпиндель токарно-фрезерного центра для выполнения процесса токарной обработки.
Фото предоставлено:Ceratizit
Ceratizit USA, входящая в люксембургскую группу Ceratizit Group, разработала альтернативный подход к токарной обработке, названный High Dynamic Turning (HDT), который в сочетании с динамической инструментальной системой FreeTurn использует фрезерный шпиндель токарно-фрезерного центра с осью B. для выполнения процесса токарной обработки. В отличие от обычного точения пластиной с фиксированным углом подхода к заготовке, это решение обеспечивает 360 градусов свободы подхода инструмента, а точка контакта в станке может изменяться в процессе обработки.
Компания Ceratizit впервые продемонстрировала технологию токарной обработки на открытом мероприятии 2019 года в Ройтте, Австрия, на токарно-фрезерном станке Emco Hyperturn 665 MCplus. По словам доктора Уве Шляйнкофера, руководителя отдела исследований и разработок режущих инструментов Ceratizit Austria, HDT позволяет выполнять все традиционные токарные операции, такие как черновая, чистовая, контурная и торцевая токарная обработка, с помощью всего одного инструмента.
Как работает HDT
Вместо классического статического положения режущей пластины в резцедержателе токарного станка HDT использует фрезерный шпиндель токарно-фрезерного станка с осью B для изменения угла подхода инструмента к заготовке в сочетании с тонкой конструкцией инструментов Ceratizit FreeTurn для минимизации риск столкновения. Благодаря вращению инструмента вокруг собственной продольной оси режущая кромка пластины в действии может быть изменена в любой момент в процессе обработки.
Кроме того, угол въезда свободно регулируется в любой момент в процессе резки. По словам Шлейнкофера, эта концепция позволяет выполнять обработку поднутрений, например, путем изменения угла в плане за один установ. Это не только обеспечивает гибкую обработку различных контуров заготовки, но и оптимальное стружкообразование, более высокие скорости подачи и увеличенный срок службы инструмента, поясняет Шляйнкофер.
Инструмент и оправка
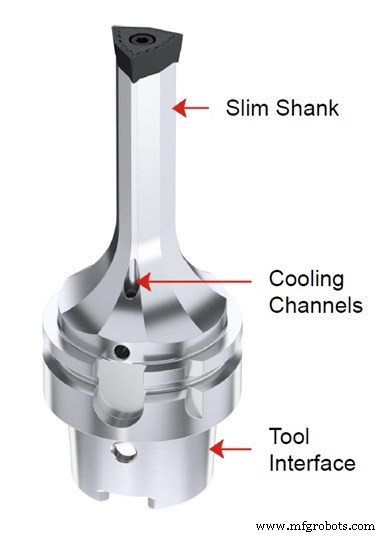
Как следует из названия, в High Dynamic Turning статические токарные инструменты заменяются динамическими, такими как FreeTurn. Определяющей характеристикой инструмента FreeTurn является его простая структура. Резцедержатель с его тонким хвостовиком и осевой концепцией (которая оптимизирует направление сил резания на шпиндель) образует прочный узел. Узкая конструкция позволяет обрабатывать узкие контуры заготовки вплоть до патрона, а охлаждающие каналы обеспечивают подачу СОЖ непосредственно в зону обработки.
В верхней части хвостовика инструмента находится многогранная пластина, которая может состоять из нескольких геометрий режущей кромки с различными свойствами. Это позволяет использовать различные углы в плане, радиусы углов или стружколомы, а также черновые и чистовые операции в одном инструменте. Также доступны различные покрытия и режущие материалы. Таким образом, инструмент можно адаптировать к конкретным требованиям обработки, предлагая преимущество замены нескольких различных инструментов. Это, в свою очередь, приводит к значительной экономии не только в отношении количества инструментов, необходимых для изготовления детали, но и в отношении необходимого количества позиций магазина автоматического устройства смены инструмента (ATC) и смены инструмента.
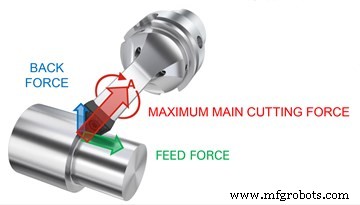
Во время резки исключены вибрации, поскольку основная сила резания направлена в осевом направлении на инструмент в направлении шпинделя.
Чтобы доказать это, Ceratizit продемонстрировал процесс HDT вживую во время дня открытых дверей компании в Ройтте. На станке Emco Hyperturn 665 MCplus были обработаны две разные детали:велосипедная ступица из алюминия AlCuMgPb и вал сцепления из стали 42CrMo4.
Для алюминиевой втулки ротора использовался один инструмент для черновой (1500 об/мин, осевая глубина резания 2 мм) и чистовой обработки (2000 об/мин, осевая глубина резания менее 1 мм). Поскольку угол подхода можно было регулировать во время обработки, все контуры обрабатывались за один установ (даже поднутрения, которые невозможно реализовать при стандартном угле подхода 90 градусов), а воздушные проходы были устранены, поскольку инструмент режет в обоих направлениях, сверху на дно и обратно. По словам Шляйнкофера, по сравнению с обычным точением можно отказаться от четырех инструментов, а время цикла для этой детали сократилось с 2:10 до 1:35 минут.
Стальной вал сцепления был обработан с использованием той же оснастки. Черновую обработку выполняли при скорости резания 200 м/мин и осевой глубине резания от 3 до 5 мм. Чистовую обработку выполняли с той же скоростью резания, но с меньшей глубиной резания на 1-2 мм. Эти параметры обычно могут привести к высоким силам резания, что при обычном точении может привести к вибрации. Тем не менее, Ceratizit утверждает, что, поскольку максимальное основное усилие резания в HDT направлено в осевом направлении к инструменту (в направлении шпинделя — см. изображение ниже), вибрация сводится к минимуму, а усилие удержания инструмента не превышается, что обеспечивает стабильный процесс.П>
Здесь показан стальной вал сцепления (42CrMo4), обработанный с помощью технологии High Dynamic Turning. Поскольку угол подхода инструмента можно регулировать во время обработки, все контуры могут быть обработаны за один установ, включая поднутрения.
Промышленное оборудование
- Определение параметров токарных станков с ЧПУ
- Облегчение токарной обработки с ЧПУ
- Токарный центр с ЧПУ
- Автоматизированный двухшпиндельный токарный центр с ЧПУ
- Быстросменный инструмент с ЧПУ
- Непрерывное включение токарно-фрезерных станков
- Токарные центры с ЧПУ
- Токарный станок с ЧПУ повышает производительность
- Токарный центр с ЧПУ и токарный станок с ЧПУ
- Sandvik представляет новую концепцию токарной обработки