УЛКОРЕД Процесс
Процесс ULCORED
ULCORED — это процесс прямого восстановления (DR), при котором производится DRI (железо прямого восстановления) в шахтной печи либо из природного газа (NG), либо из восстановительного газа, полученного при газификации угля. Отходящие газы из шахты возвращаются в технологический процесс после улавливания диоксида углерода (CO2), который концентрированным потоком покидает установку DR и направляется на хранение. На этапе прямого восстановления получается твердый продукт, который затем плавится в электродуговой печи (ЭДП). Этот процесс был разработан главным образом в 2006 году группой под руководством компаний LKAB, Voest-alpine и MEFOS.
Цель процесса ULCORED состояла в том, чтобы снизить потребление природного газа, необходимого для производства DRI. Это было достигнуто путем замены традиционной технологии риформинга парциальным окислением (ПОх) ПГ. В сочетании с устройством CCS ULCORED может сократить выбросы CO2 на 70 % по сравнению со средним показателем на маршруте доменной печи.
Концепция процесса ULCORED включает выделение CO2 из технологического газа. Он характеризуется попыткой адаптировать процесс DR на основе газа для минимизации выбросов парниковых газов (ПГ) с использованием технологии улавливания и хранения CO2 (CCS) и в то же время для минимизации использования энергии. Процесс разработан таким образом, чтобы обеспечить извлечение и хранение CO2. Таким образом, процесс также зависит от CCS с аналогичным захватом в процессе.
Процесс основан на использовании переключателя для преобразования газообразного монооксида углерода (CO) из шахты в водород (H2) вместе с устройством удаления CO2. Это открывает новую инновационную эволюцию концепции процесса.
Основные особенности процесса ULCORED DR включают (i) использование кислорода (O2) вместо воздуха, в результате чего образуется отходящий газ, содержащий почти 100 % CO2, который требуется только для сжатия, (ii) существуют возможности для снижения потребности в ПГ на 15-20 %, и (iii) уголь, биомасса, газификация биоотходов и H2 могут использоваться в качестве альтернативы ПГ.
Концепция ULCORED заключается в том, чтобы удовлетворить потребность в сокращении выбросов CO2 с использованием прямого восстановления на основе железной руды и газа для производства DRI. Концепция включает использование 100 % кислорода (O2), POx вместо риформеров, конвертер для производства восстановительного/избыточного газа, не содержащего CO2, и восстанавливающий агент, представляющий собой либо природный газ, либо синтетический газ при газификации угля/биомассы. Вместо ПГ также можно использовать восстановительный газ, полученный при газификации угля.
Процесс аварийного восстановления ULCORED на основе NG
Основными особенностями процесса ULCORED DR на основе природного газа являются (i) отсутствие риформинга, (ii) отсутствие нагревателя и (iii) высокое давление. Из-за высокого давления скорость газа в шахте DR ниже, меньше псевдоожижения и меньше мелких частиц, выходящих из шахты DR. Кроме того, из-за высокого давления требуются меньшие блоки удаления CO2 и POx, а также меньшая потребность в мощности для рециркуляционного компрессора.
Оригинальность концепции заключается в использовании O2 вместо воздуха, что означает отсутствие или низкое содержание азота (N2) в газе. Риформинг осуществляется на установке POx для кондиционирования восстановительного газа (рис. 1). Технология заменяет традиционный риформинг ПГ путем частичного окисления газа для снижения расхода ПГ, необходимого для производства прямого восстановления. Происходит реакция POx:CH4 + 0,5O2 =CO + 2H2 с дельта H =– 8,6 ккал/моль.
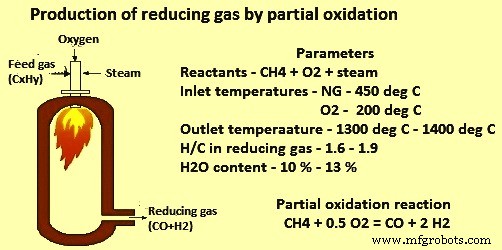
Рис. 1. Снижение образования газа за счет парциального окисления
Пилотная установка для частичного раскисления была испытана в Linde в ходе двух кампаний с горелкой новой конструкции для обогащенного водородом сырьевого газа. Использовался трубчатый реактор с подогретым газом (60 % H2 и 40 % CH4). Выводы пилотных испытаний были следующими:(i) горелка и реактор могут работать без проблем, (ii) может быть получено стабильное пламя без значительного шума, (iii) ожидается, что образование сажи будет ниже 300 мг. /N cum до 460 мг/N cum объема влажного газа, и (iv) из-за атмосферного давления содержание CO2 и CH4 было выше, чем в предварительных расчетах на основе предполагаемого равновесия. Более высокое рабочее давление до 7 кг/кв. см может уменьшить это содержание.
Шахта DR имеет противоточный поток восстановительного газа, впрыскиваемого в фурмы, а железная руда подается холодной сверху. Печь работает при давлении 6 кг/кв. см и температуре около 900°С. Отходящие газы шахты, вероятно, содержат в основном CO, CO2, H2 и H2O.
Отходящие газы шахты, содержащие в основном СО, СО2 и Н2О, проходят через шифтер (одну или две ступени), преобразующий СО в Н2. Использование переключателя водяного газа приводит к высокому содержанию H2 в редукторном валу. Реакция конверсии водяного газа представляет собой CO (г) + H2O (г) <–> CO2 + H2. Почти весь CO в отходящем газе шахты преобразуется в H2, а CO2 удаляется в блоке удаления CO2. Увеличение производства избыточного газа увеличивает потребность в энергии для установки удаления CO2 и производства O2. Расчет правильного уровня избыточного газа является итеративным процессом. По этой причине расчетные уровни избыточного газа будут выше. Ожидается, что предполагаемый избыточный уровень в 2,2 гигакалории на тонну DRI компенсирует дополнительную потребность в энергии. Этого можно добиться за счет перепуска некоторого количества газа непосредственно на переключатель передач. Количество перепускаемого газа определяется на основе свойств восстановительного газа в редукторном валу. В связи с увеличением объемов газа в системе требуются дополнительные инвестиции в блоки переключения и удаления CO2.
В блоке конверсии реакция конверсии СО является экзотермической, и равновесие благоприятствует конверсии СО при высоком отношении пара к газу и низких температурах, при этом на нее не влияет давление. В адиабатической системе достижимое проскальзывание CO определяется температурой на выходе. Конверсия в одном слое катализатора ограничена равновесием, и по мере протекания реакции высокая температура в конечном итоге ограничивает дальнейшую реакцию. Это ограничение может быть преодолено с помощью двухступенчатой системы, состоящей из высокотемпературной конверсии, за которой следует низкотемпературная конверсия с охлаждением между слоями. Низкая рабочая температура обеспечивает наиболее благоприятное термодинамическое равновесие и, следовательно, минимальное проскальзывание CO. Большинство современных заводов H2 имеют системы охлаждения перед низкотемпературным конверсионным реактором, что позволяет работать при температуре, близкой к точке росы технологического газа. Необходимо использовать запас прочности выше точки росы для обеспечения полного испарения капель воды, которые могут образоваться в охладителе.
В зависимости от соотношения паров низкотемпературный конверсионный реактор может работать при температуре до 190°C, не опасаясь конденсации. В этой концепции колошниковый газ проходит высокотемпературный и низкотемпературный конвертер с рекуперацией тепла между ними. Высокотемпературный шифтер преобразует 97,2 % CO, а низкотемпературный шифтер завершает конверсию до 99,5 %. Теплообменник нагревает рециркулирующий газ, и его производительность рассчитывается исходя из установленной разницы температур на горячей стороне 50°С. Избыток тепла в теплообменнике производит пар в паровую сеть через конденсатор/ребойлер.
Блок удаления СО2 используется для удаления СО2 из газа с получением богатого водородом восстановительного газа, который возвращается в процесс. Блок удаления CO2 определяется распределением эффективности удаления CO2, извлечения H2 и N2. Можно использовать два процесса удаления CO2:процесс вакуумной адсорбции при переменном давлении (VPSA) или процесс аминового скруббера. Выбор установки для удаления CO2 (VPSA или амин) зависит от местных требований. Если имеется избыток пара, то энергозатратная отпарка CO2 может производиться с использованием энергии пара на заводе вместо электричества, необходимого для VPSA. Обе технологии имеют свои плюсы и минусы, которые требуют дальнейшего анализа. Обе технологии работают с концепцией ULCORED. Существует также возможность использования адсорбции при переменном давлении (PSA) для удаления CO2 вместо установки VPSA из-за уже имеющегося в процессе высокого давления.
Выбранный тип процесса влияет на блок-схему процесса и макет. Процесс VPSA требует, включая криогенику и сжатие до давления 110 кг/кв.см, 260 кВтч мощности на тонну захваченного CO2. В случае процесса аминового скруббера с высокоэффективными аминами (активированный метилдиэтаноламин, АМДЭА) для полного процесса (амины и сжатие до давления 110 кг/кв. см) требуется около 1,6 тонн пара низкого давления и 160 кВтч энергии на тонну CO2. захвачено.
Часть очищенного газа с высоким содержанием водорода, содержащего N2, отводится из процесса, чтобы противодействовать накоплению N2 в восстановительном газе. Отходящий газ — это ценный газ, который можно использовать для производства пара или обогрева в системе.
Технологическая схема процесса ULCORED на природном газе представлена на рис. 1.
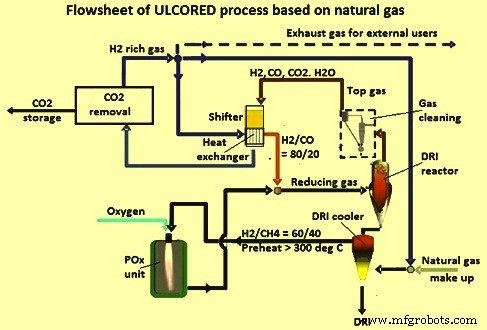
Рис. 2. Технологическая схема процесса ULCORED на основе природного газа
Процесс ULCORED DR, основанный на газификации угля
Наиболее экономичным вариантом с ULCORED является использование угольного газификатора, производящего синтез-газ для установки прямого восстановления и газообразный водород с низким содержанием CO2 для всех пользователей установки. Эта концепция может быть адаптирована как для существующих систем, так и для модернизируемых систем.
Концепция на основе угля основана на производстве восстановительного газа с использованием существующей технологии газификации угля и либо холодной десульфурации (на основе существующей технологии), либо десульфурации горячего газа. Концепция использует O2 вместо воздуха и включает хранение CO2. Высокое содержание H2 в редукторном валу достигается за счет переключения водяного газа. Избыток газа H2 поставляется другим пользователям завода.
Газификация угля является хорошо известным методом и, как ожидается, станет одним из будущих методов преобразования энергии после истощения запасов нефти и газа. Разработано несколько технологий газификации угля. Существуют различия между технологиями, но они, как правило, работают с относительно высокой эффективностью преобразования углерода, обычно превышающей 80 %. Большим преимуществом газификации угля является возможность эффективной очистки синтез-газа (например, от серы, ртути и т. д.) перед использованием.
Так как шахтная печь для производства ПВЖ работает при давлении 6 кг/кв.см, давление газа из газификатора снижается за счет детандерной турбины, которая также рекуперирует мощность (с 30 кг/кв.см до 6 кг/кв.см).Р>
Процесс ULCORED DR можно легко интегрировать с установкой газификации угля, используя преимущества оригинальной концепции процесса. Уголь поставляется на установку газификации угля. Серу удаляют из синтез-газа путем горячей или холодной десульфурации. Чистый синтетический газ смешивается с очищенным рециркуляционным газом, богатым водородом, предварительно нагретым в охладителе прямого восстановления или из теплообменника между высокотемпературным и низкотемпературным конвертерами.
Существует три различных способа интеграции газификатора в процесс ULCORED DR. Газификатор может быть интегрирован либо как холодный синтез-газ, либо таким образом, чтобы использовалась тепловая энергия горячего газа из газификатора. На рис. 3 показаны три различные установки. Возможность производить избыток H2 для системы обеспечивается за счет байпаса очищенного синтез-газа непосредственно в блоки переключения.
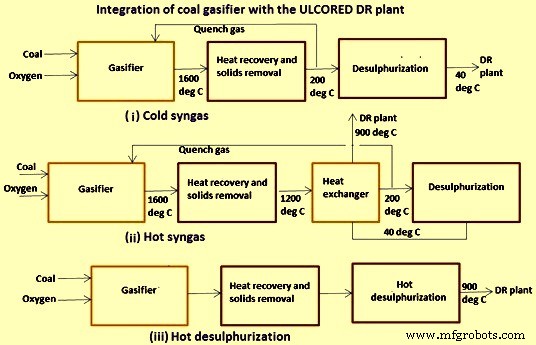
Рис. 3. Интеграция газификатора угля с установкой ULCORED DR
Кислород в основном потребляется в газификаторе угля, а также перед шахтой, в малом АГНКС, что обеспечивает правильную температуру восстановительного газа. Сдвинутый газ — это газ, который должен быть перепущен в конверсионную установку для обеспечения правильного состава восстановительного газа, т. е. увеличения количества H2. Удаленный СО2 представляет собой количество СО2, которое отделяется от основного технологического потока в процессе удаления СО2. Технологическая схема процесса ULCORED на основе угля показана на рис. 4.
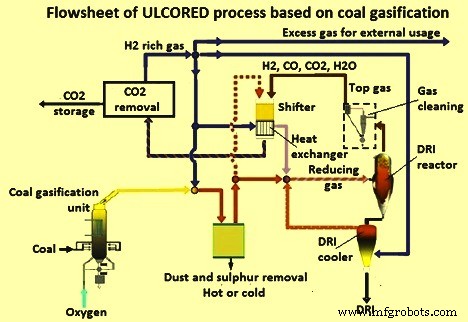
Рис. 4. Технологическая схема процесса ULCORED, основанного на газификации угля
Использование в системе газификатора угля и конвертера позволяет направлять часть синтез-газа непосредственно в конвертор, производя больше газа, чем необходимо для установки прямого восстановления. Эта особенность позволяет производить топливо, обедненное CO2, для сталелитейного завода. Это позволяет иметь один источник CO2 вне системы, что позволяет улавливать и хранить весь CO2, образующийся в системе производства стали.
Текущий статус процесса аварийного восстановления ULCORED
Были завершены углубленные фундаментальные модельные исследования процесса ULCORED DR. Эти модельные исследования включали модели в масштабе окатышей, модели валов и модели процессов с помощью моделирования технологических схем. Модельные исследования помогли в фундаментальном понимании процесса ДР, включая его динамику. Моделирование технологической схемы помогло оптимизировать схему процесса, чтобы она соответствовала процессу ULCORED DR в среде сталелитейного завода. Различные подходы, принятые в ходе исследований по моделированию, дали аналогичные результаты. Эти исследования создали надежную основу для оценки концепции в различных сценариях. Материальный баланс, массовый баланс, энергетический баланс и расчеты выбросов CO2 были выполнены для 1 тонны холодного продукта прямого восстановления с металлизацией 92 % и содержанием углерода 2,76 %.
Одним из интересных вариантов является установка ULCORED DR для производства LRI (менее восстановленного железа) и обычная доменная печь или доменная печь без азота (BF) для производства чугуна (HM) с дополнительной экономией выбросов CO2. LRI является альтернативным выбором вместо DRI, учитывая успешные испытания, проведенные в экспериментальной доменной печи LKAB. Испытание LRI с DR-продуктом, степень металлизации которого снижена до 65 %, дало очень положительный результат в доменной печи с удивительно стабильным состоянием печи и низким расходом кокса, который был ниже 200 кг/т ТМ.
Результатом этих исследований стало то, что процесс ULCORED DR может быть «быстрым решением» для сокращения выбросов CO2 в уже существующих условиях, особенно там, где природный газ относительно дешев. В случае интегрированного металлургического завода с маршрутом доменной печи LRI может быть выбором, учитывая успешные испытания, проведенные на экспериментальной доменной печи LKAB.
Процесс ULCORED DR должен быть сначала испытан в пилотном режиме, шаг, который может использовать возможности печи EDRP (экспериментальная пилотная печь прямого восстановления), которую LKAB планирует построить в ближайшие годы в качестве дополнения к своей экспериментальной доменной печи в Лулео, Швеция. Спецификации EDRP:(i) производство 1 тонны железа в час, (ii) рециркуляция колошникового газа, (iii) диапазон рабочего давления от 0 кг/кв.см до 8 кг/кв.см в шахтной печи, (iv ) расход газа в диапазоне от 1700 Н·м3 до 3100 Н·м3 в час и (v) температура шахтной печи в диапазоне от 900°С до 1050°С.
ULCORED, вероятно, станет кандидатом на модернизацию существующих установок прямого восстановления после того, как ее жизнеспособность будет продемонстрирована в пилотном, а затем и в демонстрационном масштабах, что также займет от 10 до 15 лет или более.
Производственный процесс