Проталкивание конверта с помощью поддонов и роботов
Номенклатура и требования к гибким обрабатывающим модулям растут
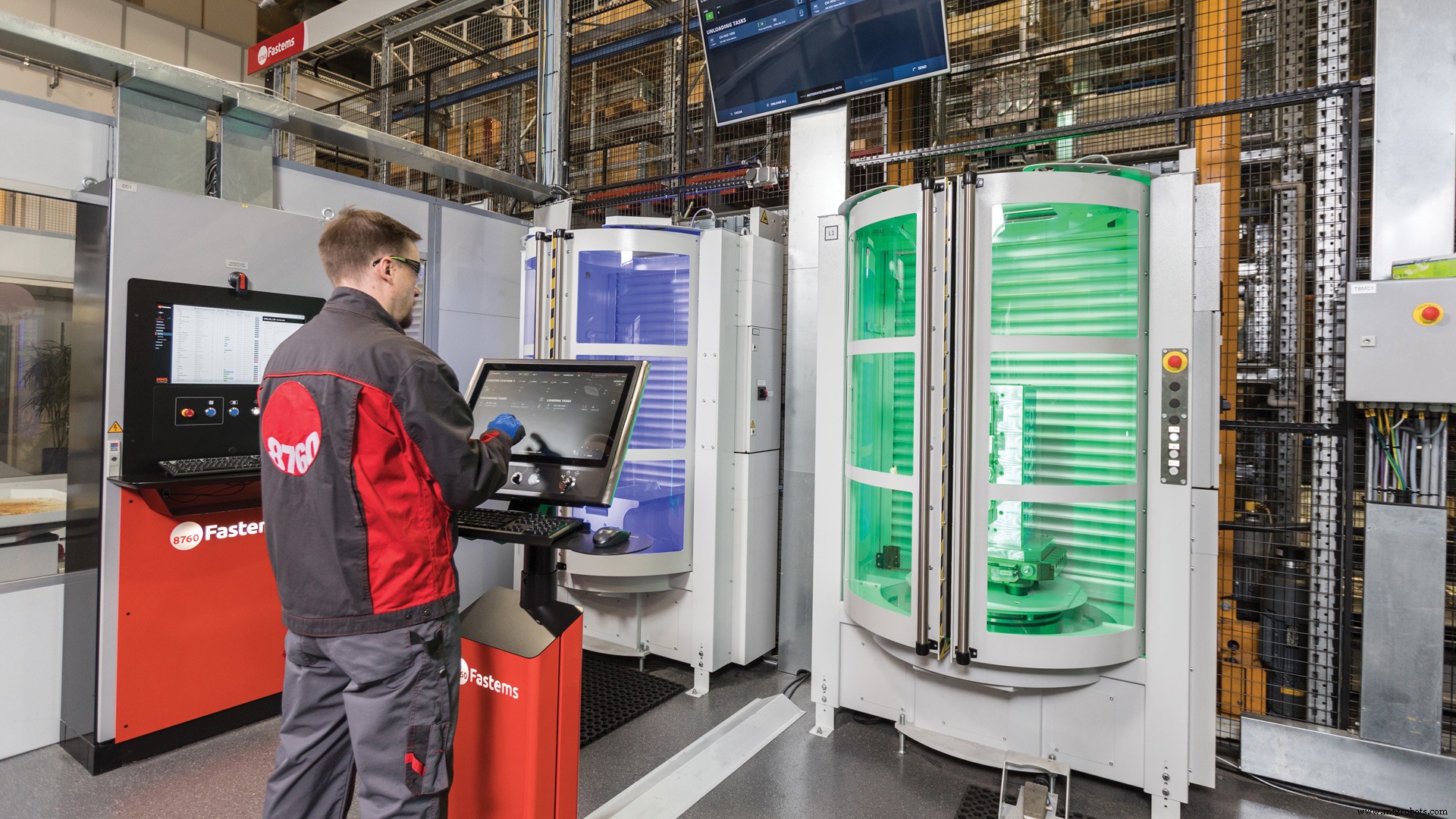
Поскольку автоматизированные производственные процессы продолжают развиваться от «хорошо иметь» к «обязательным» из-за таких проблем, как нехватка квалифицированных рабочих, гибкие конфигурации производственных систем продолжают появляться в новых и интересных формах.
Очевидно, что пандемия COVID-19 побудила производителей ускорить внедрение роботов в паллетные системы. Но это не единственный интригующий ход ФМС за последнее время.
«Гибкие производственные системы сегодня могут означать совсем другие вещи, чем в прошлые годы, — объясняет Зак Спенсер, менеджер по автоматизации компании Methods Machine Tools, базирующейся в Садбери, штат Массачусетс. — В прошлом все привыкли к системам замены поддонов для достижения максимальной гибкости с их машины. Эти пулы поддонов позволяли клиентам устанавливать различные крепления на разные поддоны и запускать свои машины без присмотра.
«Сегодня гибкая автоматизация может принимать разные формы. Это может быть что угодно:от машин на поддонах, роботов, перемещающих поддоны, таких как наши системы автоматизации Plus-K и Plus-K60, до более сложных, но все же простых в использовании систем, таких как гибкие системы технического зрения для установки деталей».
Для тех, кто плохо знаком с игрой автоматизации, Спенсер советует начать с простого.
«Обычно мы рекомендуем начинать с меньшей и менее сложной системы, чтобы они освоились с автоматизацией — привыкните к ней, прежде чем делать огромный скачок. Для нас этот меньший или более интеллектуальный тип системы может означать обслуживание одной машины вместо многих и выполнение одной партии вместо одновременной обработки множества различных типов заготовок».
Решения, большие и малые
Поскольку бизнес по автоматизации поддонов является «сердцем» Fastems, финская компания находится в авангарде новых тенденций в области автоматизации. Пандемия ускорила добавление роботов для загрузки и выгрузки деталей в установках FMS, — говорит Мика Лайтинен, директор по продажам решений в Fastems.
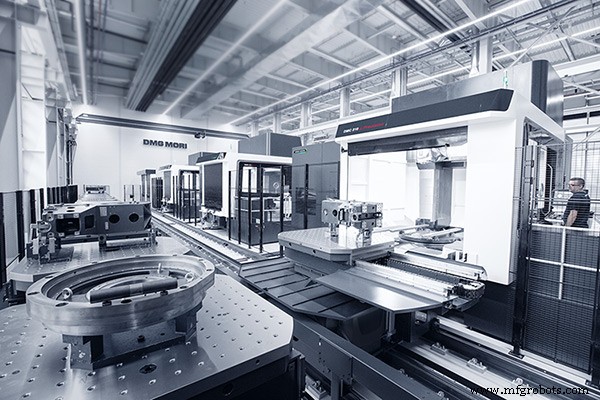
Другие вспомогательные операции все чаще добавляются в одни и те же системы, добавил Кристофер Резни, региональный менеджер Fastems в центральной части США. Например, когда деталь точится или подвергается механической обработке, ее необходимо промывать. Кроме того, детали необходимо проверять — либо по отдельности, либо после 100 циклов. Также могут выполняться операции по удалению заусенцев и автоматической загрузке приспособлений, а подключение к системам автоматического управления транспортными средствами (AGV) обеспечивает поступление материалов в операцию.
Первоначально разработан для горизонтальных обрабатывающих центров. система Fastems FPC (для гибких контейнеров для поддонов) может быть расширена для обслуживания до четырех станков.
«Впервые, по крайней мере в Финляндии, этот блок двигателя будет загружаться и разгружаться автоматически в станке такого типа с использованием AGV», поскольку система была построена без крана-штабелера. AGV перемещает обрабатывающий поддон с места на место для промывки, осмотра, удаления заусенцев и финишной обработки. «У нас также есть задачи по сборке для выполнения определенных операций окончательной обработки. И у нас есть хранилище. Итак, у нас есть все те же элементы, что и на традиционном FMS на базе крана-штабелера, но теперь все на одном уровне из-за веса компонентов.
По словам Лайтинен, использование AGV вместо крана идеально в такой ситуации, учитывая, что время обработки довольно велико — несколько часов, поэтому нет проблем с использованием более медленного погрузочно-разгрузочного транспортного средства для смены поддона.
Среда выполнения и роботы
Независимо от того, являются ли паллетные системы линейными или поворотными, с одной или несколькими машинами, возможности FMS охватывают всю гамму.
В DMG Mori ее LPP, или линейный пул поддонов, и ее более простая RPS, или вращающаяся система поддонов, находят применение в различных конфигурациях.
Для LPP «типичное место для ремонтной мастерской — это от 24 до 36 поддонов, две или три машины и две погрузочные станции», — сказал Джон Макдональд, генеральный менеджер по развитию производственного предприятия DMG MORI в Дэвисе, Калифорния. У нас есть поток материалов на погрузочных станциях и из них, работа стоит в очереди в системе пула поддонов, а машины работают днем и ночью ».
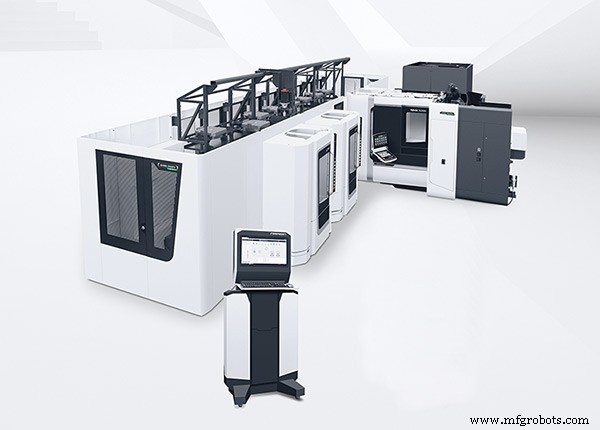
Между тем, RPS — это «система с одной машиной и одной паллетой», — продолжил Макдональд. «Обычно в нем пять поддонов, а мы доходим до 21 поддона. Они отлично подходят для работы в очереди. У вас не так много компонентов, или вы комбинируете его с каким-то быстросменным креплением, чтобы вы могли изменить свою рабочую настройку».
В конечном счете, правильный FMS для данного магазина это тот, который оптимизирует время автономной работы. По его словам, все дело в том, чтобы увеличить количество рабочих часов веретена в день и больше свободного времени, чтобы позволить сотрудникам выполнять другие задачи.
Другая задача ФМС, конечно же, состоит в том, чтобы получить больше работы за дверью. "Клиенты стучатся в мою дверь и говорят:"Вот работа, на которую можно сделать ставку, есть работа, на которую можно сделать ставку". У большинства людей, как я вижу, тяготеет вопрос:"Могу ли я действительно реализовать эту штуку?" Наша частная технология. туры и образовательные мероприятия показывают этим клиентам, как эти инструменты на самом деле работают вместе, чтобы добиться такого времени автономной работы».
Программное обеспечение DMG Mori LPS 4, выпущенное в 2021 году, представляет собой четвертое поколение программного обеспечения компании для управления системами автоматизации. С его помощью производители могут исключить некоторые этапы управления материалами, подключившись напрямую к ERP. Например, если клиент заказывает 500 блоков алюминия 6061 для производства водяных насосов, как объяснил Макдональд, «после того, как вы создали эту работу водяного насоса, ваша ERP-система может направить спрос в систему пула поддонов на то, что она собирается производить дальше. . Мы удалили эту ручную ссылку, когда кто-то вводил данные из ERP в программное обеспечение LPS 4; мы замкнули эту петлю, соединив эти два. Не все клиенты готовы начать использовать этот уровень сегодня, но некоторые из наиболее продуктивных магазинов готовы».
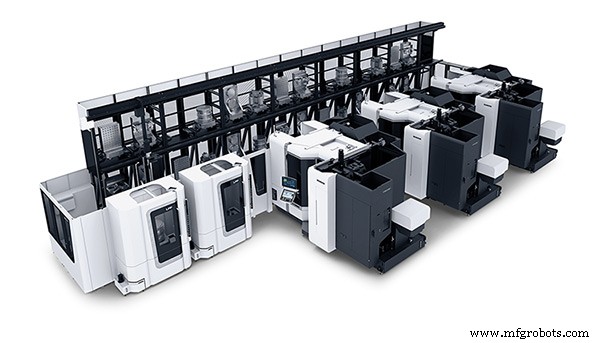
Макдональд отметил, что иллюстрируя возможности своей FMS, компания DMG Mori запускает однометровый LPP с тремя станками в собственном механическом цехе. «В нем есть станция мойки деталей, роботизированная загрузка, гидравлические приспособления и поддоны для материалов. Мы обрабатываем отливки, из которых строятся наши машины, здесь, на нашем заводе в Дэвисе. Оператор загружает отливку на поддон для материала. Почти все эти отливки необходимо поднимать краном; они слишком тяжелы, чтобы их можно было поднять. Они закреплены на поддоне, похожем на поддон вилочного погрузчика. Деталь помещается туда, а затем отправляется на паллетные стеллажи. Поддон с материалом входит в саму загрузку робота, а также в поддон с приспособлениями. Итак, робот берет деталь и загружает ее на приспособление, после чего деталь закрепляется с помощью гидравлического зажима. Затем деталь поступает в обрабатывающий центр.
«После того, как эта операция завершена, она переходит к промывке деталей; деталь очищается для удаления стружки или песка из проклеенных отверстий. У нас есть клиенты, которые пошли еще дальше, где мы интегрировали измерительные машины и ячейки для лазерной маркировки. Кроме того, некоторые клиенты используют LPP в сочетании с нашей централизованной системой управления инструментами, поэтому не только заготовки, но и инструменты в магазине станка заменяются автоматически. Как правило, такие ячейки внедряют OEM-производители».
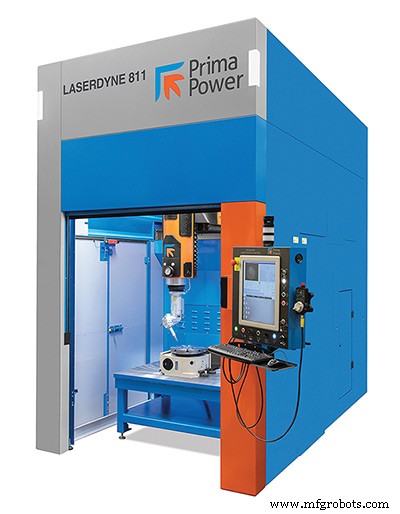
По словам Спенсера, Methods также способствует эволюции от простых систем замены поддонов к роботизированным решениям с элементами управления поддонами.
«Одна очень успешная система, которую мы разработали и внедрили, — это наша система RoboDrill Plus-K, — пояснил Спенсер. «В этой системе используется FANUC RoboDrill с роботом FANUC для обслуживания. Что касается робота, то есть возможность хранить в системе до 60 заготовок одновременно. Эта система имеет функцию управления поддонами, встроенную в систему управления машиной, которая позволяет оператору устанавливать определенные номера программ для различных 60 станций, на которых могут храниться детали. Эта гибкая система также позволяет использовать на станке дополнительные инструменты, что может быть очень полезно при работе с различными типами деталей на 60 различных рабочих станциях».
И мелкосерийное производство с большим ассортиментом не исключено, добавил Спенсер. В таких случаях «обычно мы рекомендуем более жесткое решение. При любой продаже автоматики или станков мы стараемся показать клиенту расчеты рентабельности инвестиций для его магазина, чтобы помочь утвердить продажу оборудования. Мы делаем все, что в наших силах, чтобы окупить возврат инвестиций для клиента в течение 18–20 месяцев». Он добавил, что система Plus-K компании разработана специально для работы с большим ассортиментом и небольшими объемами.
«Мы добились больших успехов в медицинской отрасли благодаря гибким системам. Я думаю, что основная причина этого заключается в потребности медицинской промышленности в многокомпонентных приложениях. Под этим я подразумеваю, что они, как правило, могут запускать небольшие партии — до 10 деталей за раз — прежде чем потребуется изготовить деталь другого типа. Это идеально подходит для более гибкого решения, которое очень легко изменить с одного номера детали на другой».
Он продолжил:«Что касается требований к отслеживанию и отслеживанию, мы предлагаем контроллеры ячеек, которые могут помочь клиентам в отслеживании деталей через системы. Контроллеры ячеек могут отслеживать время безотказной работы оборудования, статусы сигналов тревоги и историю, а также использование машин. Эти системы обычно имеют возможность сканирования QR-кода, штрих-кода или RFID, что позволяет оператору сканировать детали в ячейках и из них во время производства. Эта информация обычно хранится в локальной базе данных ячейки, откуда ее можно скопировать на сервер клиента».
Угол лазера
По словам Доминика Рикарда (Dominic Rickard), менеджера по продажам в Северной Америке компании Prima Power Laserdyne из Бруклин-Парка, штат Миннесота, когда в уравнение входят лазерная резка и сварка, FMS приобретает несколько иное определение.
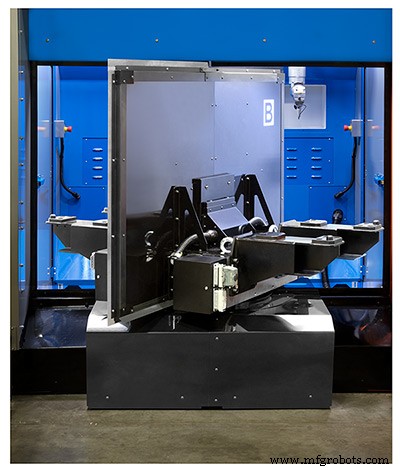
«Гибкая производственная система для 3D-лазерной обработки означает предоставление системы, которая может поддерживать широкий спектр лазерных процессов, например, лазерную сварку, лазерное сверление и 3D-лазерную резку», — пояснил Рикард. «Система должна поддерживать производственные потребности и быть адаптируемой к будущим потребностям бизнеса».
Эта адаптивность будет включать поддержку:
--Низкий объем сегодня и более высокий объем в будущем.
-- Ряд материалов, от мягкой стали, нержавеющей стали и алюминия до специальных материалов. Очень важно переключаться с одного вспомогательного газа на другой с помощью электронного и программного управления.
-- Быстрые переходы от одного производственного процесса к другому – от сварки к резке, к сверлению и наоборот. Например, по его словам, «системы LASERDYNE могут переключаться с 3D-лазерной резки на 3D-сварку за одну-две минуты».
Кроме того, он сообщил, что FMS на основе лазера должна предоставлять информацию о параметрах и процессах в режиме реального времени для систем мониторинга производства/эксплуатации, и эта информация также должна быть записана и сохранена для дальнейшего использования и анализа.
«С нашей точки зрения, размер системы или машины не зависит от гибкости, — сказал Рикард. «Размер системы определяется деталями, которые клиент собирается обрабатывать лазером. Системы LASERDYNE предназначены для обеспечения гибкости производства независимо от того, покупается большая или маленькая система».
По словам Рикарда, последним дополнением Prima Power Laserdyne является система LASERDYNE 811, которая поддерживает философию гибкого производства несколькими способами.
«Во-первых, одна и та же система поддерживает производителя, у которого большой ассортимент деталей и небольшой объем, или производителя, который заказывает системе производство одной детали в течение нескольких лет. Во-вторых, заказчик может интегрировать автоматизацию во время установки системы или в любое время в будущем. Система является модульной и регулируемой. В-третьих, система может быть отдельным оборудованием или составной частью производственной ячейки».
По его словам, система стала благом для одного клиента, субподрядчика автомобильной, пищевой промышленности и рынка товаров для дома. Этот клиент хотел расширить свои возможности обработки и сократить время изготовления различных трехмерных металлических деталей и нескольких цилиндрических деталей. Кроме того, заказчик хотел сократить время переключения креплений деталей.
«Мы предоставили заказчику LASERDYNE 811 с двухпозиционным индексным столом [поворотным столом] для лазерной резки 3D-деталей. Кроме того, мы предоставили общий интерфейс крепления, чтобы оператор мог легко переключать крепления деталей на поворотном столе. Для поддержки цилиндрической детали мы предоставили поворотный стол с тем же интерфейсом крепления детали, чтобы клиент мог легко добавлять и удалять поворотный стол. Добавление поворотного стола аналогично добавлению и удалению крепления детали.
«В результате клиент может выполнять лазерную обработку большого ассортимента SKU и сократить время цикла обработки деталей, что снижает общие затраты, увеличивает производительность завода, сокращает время доставки деталей конечным пользователям и позволяет клиенту оставаться конкурентоспособны без снижения качества».
Рикард объяснил, почему развитие FMS имело решающее значение для успеха его компании.
«По необходимости Prima Power Laserdyne стала пионером в области 3D-лазерной обработки. Чтобы добиться успеха, нам нужно было предлагать гибкие производственные системы. В первые дни бизнеса было очень сложно продать одноразовую машину. Клиенты настаивали на том, что системы должны быть гибкими. FMS — это, так сказать, основная часть нашей ДНК.
«С годами лазерные источники системы начинались с CO2-лазеров, а затем перешли от систем Nd:YAG к волоконным лазерным системам. С каждой сменой источника лазера можно было обрабатывать большее количество материалов. Со временем мы разработали и усовершенствовали наши системы для поддержки сварки, сверления и резки, заменив сопло в конце оптической лазерной цепочки».
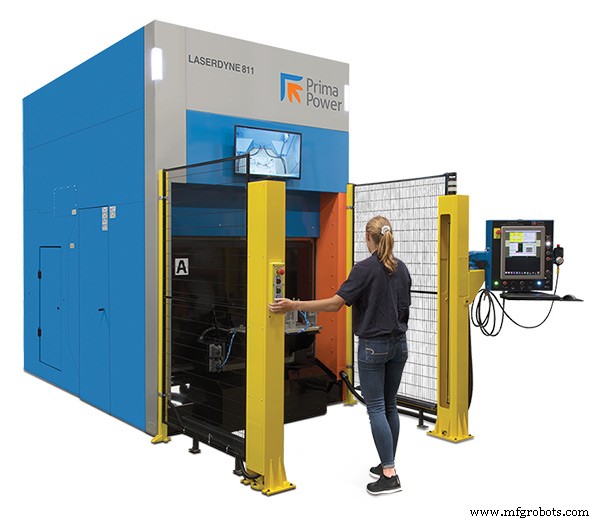
Еще одним изменением стало внедрение компанией SPC и MTConnect в свои системы. «С помощью SPC производитель может записывать все параметры процесса и машины для анализа или ведения учета. С помощью MTConnect производитель может передавать параметры в режиме реального времени, обеспечивая мониторинг процесса в реальном времени. Наконец, система в режиме реального времени контролирует все аспекты машины, включая поимпульсное управление лазером. Управление в реальном времени позволяет контроллеру поддерживать семь или более осей и упрощает интеграцию автоматизации с системами LASERDYNE».
Ultimately, he concluded, “the general manufacturing sector and contract manufacturers are the leading edge when defining and needing FMS. This group of customers needs the ability to adapt their manufacturing processes.
Typically, this group supports a variety of products and customers. The livelihood and success are dependent on how quickly and efficiently they can adapt to the work available with the market. Every market sector has an up and down cycle. If one market sector is down, the speed at which the manufacturer can adapt to the growing market sector can mean the difference between growing the business and going out of business.”
Система управления автоматикой
- Создание роботов с Raspberry Pi и Python
- 13 лучших устройств и систем для умного дома 2019 года
- Роботы, мечтательный бизнес и будущее работы
- Путь 6G начинается с взрыва (и запуска)
- Решение производственных задач с помощью данных и ИИ
- Делавэр:идеальное сочетание человека и ИИ
- Будущее тестирования:автоматизация и коллаборативные роботы
- Изменят ли мир автоматизация и роботы?
- Сочетание ИИ и робототехники с несколькими системами контроля
- Разборка рутинной переработки поддонов